
книги / Химия и технология баллиститных порохов, твердых ракетных и специальных топлив. Т. 2 Технология
.pdfсмеси от нитропродукта — позволило за счет увеличения фак тора разделения в 3000 — 4000 раз сократить технологический цикл и загрузку зданий взрывоопасным продуктом в десятки и сотни раз.
Конечно, гетерогенный процесс нитрования аморфно-кри сталлического капиллярно-пористого полимера с высокой энергией межмакромолекулярного взаимодействия, связанный с неоднократным движением нитрующих и стабилизирующих растворов по капиллярам и в межкапиллярном объеме поли мера, несоизмеримо сложнее и длительнее аналогичного по химизму процесса этерификации глицерина.
Тем не менее, применение физических методов ускорения процессов могло бы существенно сократить технологический цикл и превратить условно непрерывный процесс в непрерыв ный на всех фазах производства.
На рис. 41 предложен один из возможных вариантов не прерывного процесса с ускорением операции этерификации УЗ и СВЧ-генераторами, отделения кислот и стабилизации — принудительным отжимом и вакуумированием в шнековых прессах типа СПА-300 (с ускорением операции диффузии УЗ и СВЧ-генераторами).
Реализация такого процесса в производстве позволит не только сократить технологический цикл до нескольких часов, но и за счет воздействия на структуру полимера гидродинами ческих, кавитационных режимов и СВЧ-излучения в значи тельной мере нивелировать ее неоднообразие и исключить не обходимость формирования многотоннажных общих партий.
101
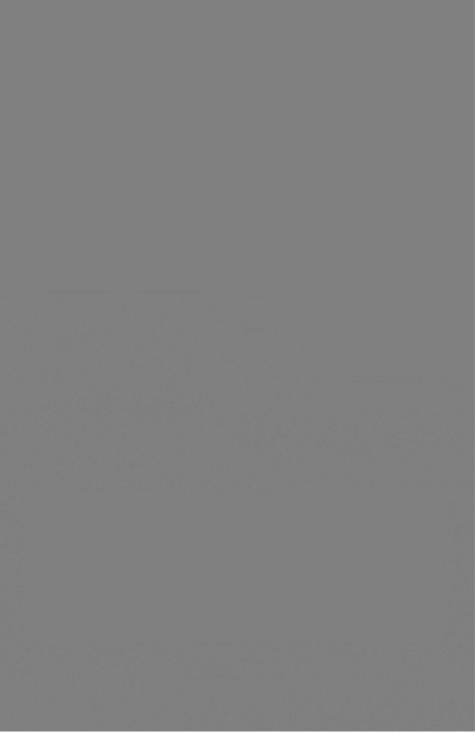
Преимущества данного метода с точки зрения безопасно сти очевидны.
В СССР, начиная с 30-х годов прошлого века, изготовле ние баллиститных порохов производилось по периодической схеме. Пороховая масса готовилась в варочном котле (мета тель Броунса) путем последовательного ввода всех компонен тов и смешения в водной среде при температуре 45...50°С (рис. 43).
Нитрат глицерина готовился по способу Натана и после проверки химической стойкости самотеком подавался сначала в общий, затем в локальный распределитель, откуда расходо вался по мере надобности в мастерскую «варки».
Подготовка и дозировка остальных компонентов пороховой массы производилась кустарным способом, что не обеспечива ло постоянства химического состава.
Коллоксилин через сито вручную протирался в большой ларь, в котором путем перелопачивания усреднялась его влаж ность, и готовилась усредненная партия сырья. После опреде ления влажности коллоксилин на сухой вес дозировался в ме татель. Остальные компоненты также вручную развешивались на обычных весах.
При таком способе производства длительность собственно операции «варки» (смешивания под водой около 250 кг мас сы) с отжимом продолжалась около трех часов.
Рис. 43. Периодическая схема изготовления пороховой массы в водной среде:
1 — общий распределитель; 2 — локальный распределитель; 3 — сито; 4 — ларь; 5 — мешатель; 6 — отжимная центрифуга; 7 — разрыхлитель ное (протирочное) устройство
1 0 3
Режим «варки» на примере порохов НФ и НФ-2 был сле дующим:
—загрузка в котел — 265 кг массы;
—модуль (вода: масса) — 7,5;
—число оборотов мешалок в котлах Броунса — 180/90 об/мин;
—температура варки — 45...50°С;
—загрузка коллоксилина вручную — 5 мин;
—перемешивание массы — 5 мин;
—инжектирование ДБФ — 15 мин;
—перемешивание — 10 мин;
—заливка НГЦ самотеком — 30 мин;
—перемешивание — 10 мин;
—инжектирование вазелина — 5 мин;
—перемешивание — 5 мин;
—охлаждение до 25°С — 60 мин;
—выгрузка массы в центрифугу — 30 мин;
Итого длительность одного цикла — 175 мин. «Сваренная» и протертая пороховая масса для усреднения
химического состава перелопачивалась в специальных ларях, вмещающих одну смесь массой около 4 тонн. Затем пороховая масса подвергалась химическому анализу, который проводился в течение 8... 10 часов. В случае получения неудовлетворитель ных результатов смесь подвергалась вторичному перелопачива нию и повторному анализу. При повторном неудовлетвори тельном анализе смесь поступала на исправление.
Операция переработки (рис. 44) осуществлялась путем многократного вальцевания массы на горизонтальных вальцах (около 25...30 прокаток в течение 50...60 мин), затем калиб рующего вальцевания на вертикальных вальцах и последующе го прессования на гидравлических прессах.
Вся работа производилась вручную, в условиях высокой пожароопасности и токсичности (в рабочей зоне Снгц — до 100 мг/м3 при ПДК = 0,02 мг/м3).
Особенно тяжелые условия труда были при вальцевании на горизонтальных вальцах — последовательные загрузки массы сверху и прием полотна снизу с горячего стола и повторение этих операций до 30 на одну вальцовку (~ 20 кг).
Вышеописанный технологический процесс смешения ком понентов пороховой массы в воде с последующим ее отжимом на центрифуге и усреднением путем перелопачивания в ларе, решивший вопрос безопасности нобелевского метода, обладал
104
Рис. 44. Периодическая схема переработки пороховой массы:
1 — горизонтальные вальцы; 2 — вертикальные вальцы; 3 — гидравлический пресс
рядом существенных недостатков, среди которых наиболее важными были следующие:
—недостаточное однообразие пороховой массы по хими ческому составу вследствие неточного дозирования и неудов летворительного метода перемешивания (перелопачиванием);
—недостаточная глубина пластификации («созревания») вследствие грубого диспергирования компонентов в водной среде, неинтенсивного перемешивания и малого времени со зревания массы (в суспензии или в отжатом виде);
—длительность технологических операций, высокие тру дозатраты при практически отсутствии механизации.
В СССР в 30—40-х годы большой группой исследователей во главе с А. С. Бакаевым были проведены фундаментальные исследования процессов, протекающих при варке пороховой массы — диспергирования, смешения, смачивания, капилляр ной пропитке и т. д., — позволившие модернизировать произ водство сначала в периодическом, полунепрерывном, а затем и в непрерывном вариантах [17, 39, 40].
На основе теории смачивания Ребиндера [38] были иссле дованы поверхностные явления на границе НЦ — жидкость — жидкость и определены закономерности пропитывания кол локсилина водой, нитроглицерином, диэтиленгликольдинитратом, вазелиновым маслом, дибутилфталатом и др.
Установлено, что наибольшей скоростью пропитывания об ладают вазелиновое масло, ДБФ, НГЦ и ДЭГДН. Скорость пропитывания водой значительно меньше.
3.2Непрерывная технология «варки»
3.2.1Физико-химические процессы пластификации при «варке»
пороховой массы
Недостатки технологического процесса, представленного выше на рис. 43, приводящие к неоднообразию химического состава продукции и громадным затратам ручного труда, дик товали необходимость усовершенствования технологии и, пре жде всего, в направлении исследования механизма взаимодей ствия всех компонентов в водной среде, а также механизации ручных операций.
Работами ОБ-59 [39] в 39—40 гг. было установлено, что причинами макронеоднородности пороховой массы (разброс химического состава по объему массы) является плохое пере-
106
мешивание при перелопачивании в ларе и недостаточно каче ственное смешение в варочном «котле».
В связи с этим вместо ларя был введен в технологический процесс смеситель большой емкости, в котором при интен сивном смешении готовилась общая партия пороховой массы.
Для повышения качества смешения в котле вместо лопаст ной мешалки было предложено использование турбинной, а ввод пластификаторов вместо раздельного — в виде заранее приготовленного однородного раствора (рис. 45).
При рассмотрении взаимодействия полимера с пластифи каторами авторы [40, 41] исследуют широкий круг вопросов от диспергирования компонентов в воде до диффузии низко молекулярных пластификаторов в межмакромолекулярном объеме полимера.
Особый акцент во всем процессе пластификации делается на операциях смачивания НЦ жидкими компонентами и набу хания волокон НЦ за счет капиллярной пропитки и диффузии пластификаторов.
днг нгц
Рис. 45. Схема смешения компонентов пороховой массы с предварительной подготовкой раствора пластификаторов:
1 — смеситель с турбинной мешалкой; 2 — аппарат для приготовления растворителей; 3 — смеситель общих партий; 4 — центрифуга
1 0 7
Несмотря на различное определение понятия «смачивание» все авторы, рассматривая это явление, исходят из представле ния о том, что поверхность раздела фаз всегда является источ ником силового поля вследствие некомпенсированности моле кулярных сил в междуфазном поверхностном слое. Ребиндер П. А. [42] считает, что «мерой напряженности такого молеку лярного силового поля является междуфазное поверхностное натяжение».
Смачиваемость твердого тела жидкостью характеризуется растекаемостью жидкости под действием равнодействующей силы / (рис. 46), равной
/ = <723-013-0,2 cos© -Ти, |
(3.1) |
где (для рассматриваемого случая вода — НЦ — пластифика тор) а2з — поверхностное натяжение на границе НЦ — вода; ап — поверхностное натяжение на границе НЦ — пластифи катор; Ст|2 — поверхностное натяжение на границе пластифи катор — вода; тц — сила трения по площади, препятствующая растеканию.
Краевой угол © находится из условия / = 0 (прекращения растекания):
cos0 = —3~ ° 13 —— . |
(3.2) |
<*!•> <Г|, |
|
3
Рис. 46. Силы, определяющие смачиваемость твердого тела:
1 — пластификатор; 2 — вода; 3 — НЦ; от12 — поверхностное натяжение на границе пластификатор — вода; ст,3 —
поверхностное натяжение |
на границе |
НЦ — пластификатор; ст2з |
по- |
верхностное |
натяжение на |
границе НЦ — вода |
|
108
Величиной тц можно пренебречь как незначительной, и то
гда
В —cos© = — —— . |
(3.3) |
СТ1 |
|
Эту величину принимаем как меру смачивания.
В случае смачивания на границе твердого тела и двух несмешивающихся антиполярных жидкостей, названного П. А. Ребиндером [38] избирательным смачиванием, обе жид кости вдоль периметра смачивания конкурируют в борьбе за поверхность твердого тела. При этом твердое тело всегда луч ше смачивается жидкостью, имеющей по отношению к нему меньшую разность полярностей (меньшую поверхностную энергию стжид_тв т). Существенное влияние на смачивание ока зывает адсорбция поверхностно-активных веществ (ПАВ) на смачиваемой твердой поверхности. Как правило, ПВА улучша ют' смачиваемость.
При смачивании твердых пористых тел, особенно тел с развитой капиллярно-пористой структурой (как НЦ), необ ходимо учитывать явление капиллярности (рис. 47). При сма чивании стенок искривление поверхности с образованием во гнутого мениска приводит к изменению нормального давления
I П
Рис. 47. Явление капиллярности: I — жидкость смачивает стенки капил
ляра; II — жидкость не смачивает стенок капилляра
109
(уменьшения). Жидкость, не смачивающая стенок, образует выпуклый мениск с увеличением давления.
Капиллярное же давление
^a = A(Pi “ Рг)?. |
(3-4) |
где Ра = Р— Р'\ рь р2 — плотность жидкости и ее насыщенного пара; h — капиллярное поднятие.
С другой стороны: |
|
2ст., cos© |
(3.5) |
1рrr = — М-------J |
где г0 — радиус капилляра.
При смачивании стенок капилляра жидкостью:
2 ст|2 C O S ©
(3.6)
JeCPi “ Pг ) я '
При несмачивании наблюдается опускание жидкости в ка пилляре с плоским уровнем на эту же высоту А.
Поскольку капиллярное давление зависит от радиуса ка пилляра, то, очевидно, малые капилляры заполняются быст рее, чем капилляры большего диаметра. Это явление рассмат ривалось нами ранее при исследовании структуры капилляр но-пористой системы нитратов целлюлозы.
Поверхностное натяжение с повышением температуры ли
нейно |
падает |
[42]: |
|
|
|
ст7.=сг0(1-у7’), |
(3.7) |
где у= |
const. |
|
|
Следовательно, смачивание с повышением температуры улучшается.
Таким образом, при модернизации технологического про цесса производства пороховой массы были выявлены важные закономерности пластификации НЦ и определены стадии процесса:
—избирательное смачивание поверхности НЦ пластифи каторами в водной среде;
—сорбция пластификаторов капиллярно-пористой систе мой полимера;
—диффузия молекул пластификатора в межмакромолекулярной структуре полимера.
На каждой стадии выявлены основные технологические факторы, определяющие скорость и глубину процесса, но