
книги / Сопротивление материалов деформированию и разрушению. Ч. 1
.pdfРис. 3.8. |
Схема нагружения нижней поверхности крыла транспортного самолета: |
1 — набор |
высоты; 2 — крейсерский полет; 8 — снижение; 4 — наземные нагрузки |
зана на рис. 3.9 [28]. Кривая А относится к крейсерскому полету на высоте 6100 м с последующим быстрым снижением, В — к набору высоты в крейсерском полете с 6100 до 9150 м с последующим более медленным снижением. Из рис. 3.9 видно, что, например, для режима В при увеличении продолжительности полета с 2 до 10 ч срок безопасной эксплуатации в часах возрастает более чем в 2,5 раза.
Т а б л и ц а |
3.3. |
Амплитудные и частотные отношения составляющих нагрузок |
||||
|
|
|
|
|
Возможные отношения |
|
Изделие, элемент конструкций |
амплитуд |
частот |
||||
|
|
|
|
|
||
Фюзеляжи, |
подвески |
рулей, |
элероин, |
0,03...0,5 |
1,5...5000 |
|
стабилизаторы |
в самолетах |
|
||||
Элементы энергетических установок |
0,03...0,5 |
100... 1000 |
||||
Гидротурбины |
|
|
|
0,1...0,5 |
2,5... 150 |
|
Шпиндели блюмингов и прокатных станов |
0,01...0,5 |
15...30 |
||||
Режущие цепи врубовых |
машин |
|
0,1...0,5 |
15...20 |
||
Подкрановые |
балки |
|
|
0,01...0,25 |
10.. .1000 |
|
Металлоконструкции радио- и телевизи |
|
|
||||
онных мачт |
|
|
|
железо |
0,1...0,5 |
1,5... 150 |
Главные балки и раскосы форм |
|
|
||||
бетонных мостов |
|
|
0,05...0,25 |
30...100 |
Важной проблемой применительно к обеспечению прочности высокоскоростных самолетов, которая весьма^ актуальна и для космической техники, является аэроди намический нагрев деталей. На рис. 3.10 показана зависимость максимальных тем ператур, достигаемых при длительном полете в нижних слоях атмосферы [138]. Неко торые данные по этому вопросу приведены ранее (см. рис. 2.14). При этом следует учитывать, что современные конструкции аппаратов с людьми на борту совершают
Ттах; К
Продоткителоность зтааа полета,ч
Рис. 3.9. Зависимость срока эксплуатации самолета от продолжительности полета
Рис. 3.10. Максимальные температуры, достигаемые при длительном полете в ниж них слоях стратосферы
полеты при скоростях до четырех звуковых скоростей. Баллистическая ракета вхо дит в плотные слои атмосферы со скоростью, превышающей звуковую в 20 раз. Если бы вся потенциальная энергия такой баллистической ракеты превращалась в тепло, то его количество было бы в 20 раз больше величины, необходимой для полного ис парения ракеты [138].
Обеспечение работоспособности этих конструкций требует использования мате риалов со специальными свойствами, в частности теплозащитных материалов, неко торые свойства которых были приведены в табл. 2.69.
3.3. Газотурбинные двигатели
Газотурбинные двигатели, особенно авиационные,— типичный при мер высоконапряженных конструкций большой ответственности, получившие широ кое распространение в технике. Особенностью газотурбинных двигателей является стремление к реализации в них максимально высоких рабочих температур. Рост температуры перед турбиной обеспечивает снижение массы двигателей и повышение их мощности и экономичности. Наблюдается непрерывная тенденция роста темпера туры газа перед турбиной. Так, в 1955 г. она составляла 1150... 1200 К, в 1965 г.— 1300...1400 К, в 1975 г — 1420...1530 К, в 1980 г.— 1600...1650 К [178]. Поданным работы [92], рост температуры газа перед турбиной будет продолжаться.
Одновременно наблюдается рост давлений в компрессоре: если в 1955 г. он со ставлял 1,0...1,1 МПа, то в 1970 г.— 2,3...2,5 МПа, в 1975 г.— 2,5...3,0 МПа, в 1980 г.— 3,7...3,5 МПа, в настоящее время рассматривается возможность создания двигателей с давлением до 4 МПа.
Реализация высоких рабочих температур в газотурбинных двигателях обеспе чивается созданием высокотемпературных материалов, некоторые из которых были рассмотрены в предыдущей главе, применением жаростойких и жаропрочных по крытий и использованием эффективных систем охлаждения лопаток первых ступеней турбины, которые подвергаются воздействию наиболее высоких температур. Стрем ление к реализации максимально высоких температур и особенности эксплуатации двигателей, особенно малоресурсных двигателей специального назначения, приво дит к большим скоростям нагрева и охлаждения и в связи с этим — к существен ным термическим напряжениям. В качестве примера на рис. 3.11 показано измене ние температуры на нестационарных режимах работы в диске и рабочей лопатке авиа ционного газотурбинного двигателя [64]. Из рисунка следует, что скорости возрас тания температуры лопаток и дисков могут составлять 177...250 град/мин. Как по казано в работах [37, 105, 153, 154], в период запуска в дисках транспортных ГТД температура обода достигает 973 К в течении 2...3 мин, температура кромок лопа ток — 1173... 1273 К за десятки секунд. Такие режимы нагрева, а также реализуемые в этоэд случае режимы охлаждения деталей гораздо более жесткие, чем, например, в эле ментах стационарного энергетического оборудования, обеспечение прочности и дол говечности деталей в этих условиях требует больших усилий. Реализация высоких температур приводит к целому ряду проблем, нуждающихся в решении,— таких, как сернистая коррозия, охрупчивание материала в процессе длительного воздействия
Рис. 3.11. Изменение температуры на нестационарных режимах в диске (а) и рабо чей лопатке (б):
I — взлет; I I — сброс газа; II I — приемистость; О — обод диска; С •»- ступица диска; К — кромка лопатки; Ц — центральная часть сечения лопатки
высоких температур и химически активных сред, термоциклическая прочность «го рячих» деталей, надежность жаростойких и износоустойчивых покрытий, прочность контактных поверхностей и т. д. Свойства некоторых материалов, используемых для изготовления ГТД, допустимые для них рабочие температуры и детали, которые из готавливаются из них, были приведены в табл. 2.5.
Другая группа вопросов обеспечения прочности газотурбинных двигателей связана с обеспечением вибрационной прочности. В связи с большими скоростями газовых потоков, высокими удельными мощностями, ограниченной жесткостью деталей, большими давлениями в компрессоре детали ГТД, особенно авиационных, подтверждены вибрациям, которые могут привести к усталостным разрушениям. Эта проблема актуальна для вентиляторных лопаток, лопаток компрессора, дисков турбины и компрессора, корпусов оболочек и т. д.
В условиях вибрации резко возрастает вероятность усталостных разрушений и возникает необходимость учёта влияния на прочность и долговечность всех факто ров, роль которых существенна при усталости.
Третья группа вопросов связана с обеспечением высокой надежности и доста точно большого (10 000...20 000 ч) ресурса двигателей. Проблема обеспечения проч ности двигателя большого ресурса требует обеспечения на заданный ресурс всего комплекса характеристик: пределов длительной прочности, ползучести и релаксации напряжений; сопротивления повторно-статической нагрузке или малоцнкловон усталости; термоциклической прочности; непрерывно изменяющихся в процессе наработки (характеристик) высокочастотной усталости (особенножаропрочных и цвет ных сплавов); сопротивления материала охрупчиванию; стабильности состояния по верхностного слоя под действием износа, коррозии, эрозии, выгорания легирующих элементов; стабильности структурного и фазового состава материала; чувствитель ности материала к технологическим методам упрочнения; умеренного рассеяния механических свойств; сохранения посадок в сопрягаемых деталях; сопротивления износу и фреттинг-коррозии контактируемых пар [178].
Для деталей авиационных газотурбинных двигателей, возможно, в большей степени, чем для деталей других конструкций, характерно одновременное воздей ствие на них различных повреждающих факторов. В табл. 3.4 по данным работы [64] приведены основные детали газотурбинных двигателей и факторы, определя ющие их ресурс. Из таблицы видно, что большинство деталей одновременно под вергается воздействию различных повреждающих факторов. Это еще раз подчерки вает необходимость разработки методов, позволяющих при расчетах на прочность и долговечность учитывать взаимодействие повреждающих факторов.
Анализ отказов авиационного газотурбинного двигателя в процессе его стендо вой отработки выполнен в работе [63]. Результаты этого анализа приведены на рис. 3.12 [56, 63], откуда следует, что в процессе стендовой доводки авиационног® газотурбинного двигателя наиболее часто встречаются отказы, связанные с проч
ностью, причем наиболее часто встречаются поломки, инициированные переменными нагрузками.
Соответственные детали газотурбинного двигателя, например диски, подверга ются сложному комплексу силовых и тепловых воздействий, имеют сложную гео метрическую форму, их материал подвергается сложному процессу механической и термической обработки, вносящему определенную технологическую наследствен ность в свойства материала. Все это приводит к большому многообразию возможных разрушений. Анализ таких разрушений выполнен в работе [27], результаты кото рого приведены в табл. 3.5. Откуда следует, что к разрушению дисков приводят самые разнообразные факторы: высокие статические напряжения при высоких тем пературах, и механическая и термическая усталость, высокие термические напря жения, наличие технологических дефектов и т. д. Существенное влияние на проч ность ряда деталей ГТД, в первую очередь компрессорных лопаток, могут оказы вать эксплуатационные дефекты типа забоин [105]. В ряде случаев возникновение
Т а б л и ц а |
3.4. Детали |
АГТД |
и факторы, определяющие |
их ресурс |
|
|||
|
|
|
|
Длитель |
Выносли |
Повтор |
Термо |
Износ и |
|
Деталь |
|
контакт |
|||||
|
|
ная проч |
вость |
ное на |
стойкость |
ная вынос |
||
|
|
|
|
ность |
|
гружение |
|
ливость |
Лопатки турбины |
|
|
|
|
|
|
|
|
рабочие |
|
|
|
+ |
+ |
+ |
+ |
|
сопловые |
лопаток |
тур |
+ |
+ |
+ |
+ |
|
|
Замки крепления |
|
|
|
|
|
|||
бины |
|
|
|
~т~ |
+ |
+ |
+ |
+ |
Диски турбины |
компрессора |
+ |
+ |
+ |
|
|||
Рабочие лопатки |
|
+ |
+ |
|
|
|||
Направляющие аппараты |
ком |
|
|
|
|
|
||
прессора |
|
лопаток |
ком |
+ |
+ |
4* |
|
|
Замки крепления |
|
|
|
|
|
|||
прессора |
|
|
|
+ |
•+ |
+ |
|
+ |
Диски компрессора, валы |
|
+ |
+ |
|
+ |
|||
Шестерни шлицы, |
подшипники |
+ |
+ |
+ |
|
+ |
||
Опоры |
|
|
|
+ |
+ |
|
|
|
Корпус |
|
|
|
|
|
|
|
|
компрессора |
|
|
+ |
+ |
+ |
+ |
|
|
турбины |
и камеры сгорания |
+ |
+ |
+ |
|
|||
Оболочки |
|
|
|
+ |
+ |
+ |
|
|
Реверс |
|
|
|
|
+ |
|
+ |
|
Трубки и агрегаты |
|
|
+ . |
|
|
+ |
забоин на лопатках компрессора носит массовый характер и приводит к необходи мости снятия двигателей с эксплуатации. В работе [105] приведены данные, что по этой причине снимается с эксплуатации до 30 % двигателей.
Для судовых газовых турбин прочность компрессорных лопаток в значительной степени зависит от попадания в воздушный тракт солей морской воды. Примеры экс плуатационных дефектов, встречающихся на лопатках турбины и компрессора ГТД приведены на рис. 3.13 [179]. Для турбинных лопаток, эксплуатирующихся в усло виях обтекания высокотемпературным газовым потоком, на ранней стадии характер но возникновение локальных мест химической неоднородности поверхностных слоев, которые в дальнейшем являются источником трещин термической и механической усталости (рис. 3.13, а). На этом рисунке 1—3 — слои с различным химическим составом. Размер h, показанный на рисунке, после 5000 ч эксплуатации для сплава ЭИ 826 составил 0,8 мм, а после 20 000 ч эксплуатации — 2 мм.
На рис. 3.13, б показаны коррозионные язвы, наблюдающиеся в компрессорных лопатках первой и второй ступеней из стали 1Х12Н2ВМФ судовой турбины. Для 8000и 16 000 ч эксплуатации средние значения h соответственно равны 0,3 и 0,9 мм.
Рис. ;ill\ Схема откатов авиационного газотурбинного двигателя в процессе его стендовой доводки
КУС,ан,МДж/м*
Рис. 3.15. Зависимость предела текучести и предела прочности (а) и ударной вязкости (б) стали 15Х2МФА от облучения
там активной зоны. Управление и регулировка активной зоны осуществляются через верхний блок с приводами и блок защитных труб. Нагретый в активной зоне тепло носитель поступает через выходные патрубки корпуса реактора по главным цирку ляционным трубопроводам диаметром 500—800 мм одной из петель (число которых составляет от 4 до 8) в парогенераторы (рис. 3.14). Скорость циркуляции теплоноси теля составляет 3—5 м/с. Образующийся в парогенераторах пар под давлением 30— 65 кГ/см3 (3—6,5 МПа) поступает в турбогенераторы. Температура питательной во ды в парогенераторах составляет 463...473 К [129]. Корпуса атомных реакторов из готавливаются из теплоустойчивой и радиационностойкой перлитной никель — хром — молибден — ванадиевой стали (15Х2МФА) с антикоррозионной аустенитной наплавкой. Главные циркуляционные трубопроводы изготавливают из аустени тной нержавеющей стали или из перлитной теплостойкой стали с антикоррозион ной плакировкой.
В отличие от обычных сосудов высокого давления, корпуса реакторов подверга ются воздействию мощного нейтронного и у-излучения, вызывающего значительныеизменения свойств металла. Наиболее неблагоприятны из них потеря пластичности и увеличение склонности стали к хрупким разрушениям. В связи с этим вопрос ра диационной стойкости материала корпуса реактора с точки зрения его длительной работоспособности приобретает первостепенное значение.
На рис. 3.15, а приведены данные, характеризующие изменение некоторых ме ханических свойств стали 15Х2МФА в зависимости от накопленной дозы нейтронно го облучения (флюенса) при температуре облучения 543...563 К. Из рисунка вид но, что в процессе облучения резко увеличиваются значения а02 и о в, умень
шается отношение ов/о02 которое характеризует запас пластичности материала.
|
На рис. 3.15, б приведены температурные зависимости ударной |
вязкости ста |
||
ли 15Х2МФА до облучения |
(7) и после различных доз нейтронного облучения (2 — |
|||
Ф = |
1,2 • 1020 н/см2, Тобл = |
573...623 К, 3 — Ф = 9,1 . 1020 н/см3, Тобл * |
533... |
|
543 |
К). |
|
снижает |
тем |
|
Как видно из этого рисунка, нейтронное облучение существенно |
пературу перехода в хрупкое состояние. Охрупчивание материала характерно иетолько для условий нейтронного облучения, но, хотя и в меньшей степени, и для других условий длительного высокотемпературного нагружения, как это показано на рис. 2.21.
Помимо статических нагрузок детали реактора подвергаются циклическим на грузкам. Спектр этих нагрузок определяется [129] программными и аварийными, пусками и остановами с числом повторений 100...500; гидроиспытаниями повышен
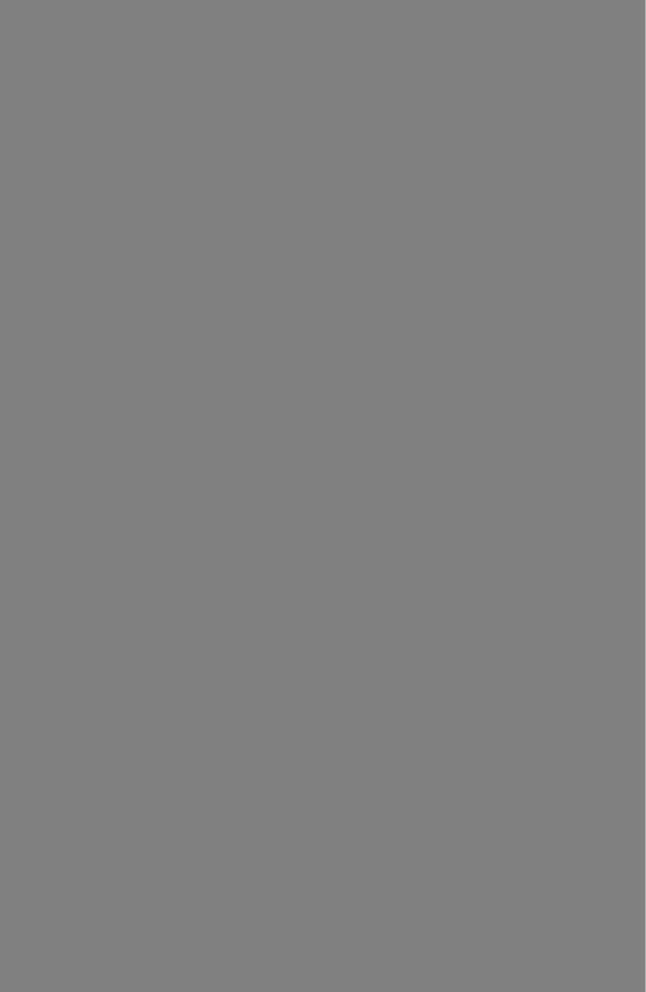
вых котлов, теплообменников и других такие трещины весьма характерны. Обра щает на себя внимание высокий процент врожденных трещин, по-видимому, техно логического происхождения (29 %). Этот вывод согласуется со следующим наблюде нием: около 64% общего числа отказов паровых котлов приходится на отказы котлов
со сроком службы до 10 лет (для анализа были взяты данные по котлам, |
прослужив |
шим до 40 лет). |
|
Весьма подробно разрушения корпусов сосудов высокого давления, в том числе |
|
корпусов атомных реакторов, проанализированы в работе [48], где дана |
следующая |
классификация повреждений сосудов высокого давления: образование |
неглубоких |
трещин и трещин, приводящих к потере герметичности сосуда; хрупкое разрушение
сосуда |
связано с |
|
быстрым |
распространением трещин. Разрушения |
первых |
двух |
|||
Т а б л и ц а |
3.8. |
|
|
|
|
< |
|
|
|
Обобщенные данные по образованию трещин в барабанах |
|
||||||||
паровых котлов |
|
|
|
|
|
|
|
||
|
|
|
|
|
|
Тип котла |
|
|
|
|
Характеристика |
ТГМ-94 |
БКЗ-210 |
ТГМ-84 |
ПК-10 |
||||
|
|
|
|
|
|||||
.Наибольший |
срок |
службы, |
|
|
|
|
|||
тыс. |
ч. |
|
|
пусков |
50 |
52 |
44 |
105 |
|
Наибольшее число |
160 |
155 |
152 |
1010 |
|
||||
Рабочее давление, |
|
МПа |
15,5 |
15,5 |
15,5 |
11,0 |
|||
Предел |
текучести |
|
при рабо |
|
|
|
|
||
чей температуре, МПа |
260 |
260 |
270 |
190 |
|
||||
Максимальные условные на |
|
|
|
|
|||||
пряжения |
в зоне разруше |
|
|
|
|
||||
ния, |
МПа |
|
|
|
420...440 |
420... 440 |
420...440 |
250...270 |
|
Число |
поврежденных бара |
|
|
|
|
||||
банов, %- |
|
|
|
46,7 |
53,0 |
70 |
81,7 |
||
общее |
|
|
|
||||||
в том числе с трещина |
13,3 |
33,4 |
51,3 |
75,7 |
|||||
ми |
более 0,5 |
мм |
|||||||
групп возникают, как правило, в зонах концентрации напряжений и связаны с |
цик |
лическим характером нагружения конструкции. Обобщенные сведения по нагруженности и режиму эксплуатации барабанов паровых котлов и числу поврежденных барабанов, встречающихся в практике, приведены в табл. 3.8 [48]. Повреждения в этом случае характеризуются главным образом трещинами у отверстий и шту церов.
Следует отметить значительную роль сварки в возникновении повреждений со судов давления. В соответствии с результатами анализа, выполненного в работе [198],
для 132 случаев эксплуатационных повреждений сосудов давления |
89 % этих слу |
чаев связаны с образованием трещин вблизи сварных швов в узлах |
присоединения |
к корпусу сосуда патрубков и других элементов. Из них семь случаев закончились хрупким разрушением сосуда. В работе [198] также сделан вывод, что сварные швы и зоны термического влияния сварки — наиболее вероятные места разрушения со судов давления за счет существования в этих районах необнаруженных технологи ческих дефектов. Причем наиболее вероятный период проявления скрытого дефек та — первые два-три года работы конструкции, а затем даже при длительной экс плуатации (до 30 лет) вероятность разрушения от технологических дефектов очень мала.
Существующие методы контроля дефектов в крупногабаритных конструкциях, к сожалению, не дают возможности полностью выявить трещины малых размеров. На рис. 3.16 построены гистограммы и распределения производственных дефектов в корпусах атомных реакторов [48]. Стрелкой указана граница чувствительности дефектоскопов; 1—3 — соответственно реакторы ВВЭР-440 с учетом гидропрессовки,
ВВЭР-440 и ВВЭР-1000 на стадии изготовления. |
как |
Анализ повреждений сосудов высокого давления, работающих в составе |
|
обычных, так и атомных энергетических установок (табл. 3.9), выполненный в |
ра- |
» |
|