
книги / Процессы обработки заготовок. Методы механической обработки поверхностей деталей машин
.pdf4.4.4. Черновое шлифование
Черновое шлифование осуществляют при скорости вращения круга порядка 30 м/с, продольной подаче от 10 до 30 м/мин
иглубине шлифования 0,02–0,04 мм.
Вкачестве СОЖ используют эмульсию или 4 %-ный водный содовый раствор.
При черновом шлифовании достигается точность обработки
7–9-го квалитета и шероховатость поверхности Ra = 1,25–2,5 мкм. Припуск составляет порядка 0,7 мм.
4.4.5. Чистовое шлифование
Чистовое шлифование осуществляют при скорости вращения круга порядка 30 м/с, продольной подаче от 10 до 30 м/мин и глубине шлифования (0,01–0,02) мм. В качестве СОЖ используют эмульсию или 4 %-ный водный содовый раствор. При этом достигается точность обработки 5–6-го квалитета и шероховатость поверхности Ra = 0,32–1,25 мкм.
Припуск составляет порядка 0,3 мм.
4.4.6. Тонкое (отделочное) шлифование
Тонкое шлифование осуществляют при скорости вращения круга порядка 30–35 м/с, продольной подаче от 8 до 12 м/мин
иглубине шлифования 0,005–0,01 мм с выхаживающим проходом без врезания (глубина шлифования равна нулю). В качестве СОЖ используют эмульсию или 4 %-ный водный содовый раствор. При этом достигается точность обработки 3–4-го квалитета
ишероховатость поверхности Ra = 0,08–0,32 мкм. Припуск составляет порядка 0,05 мм.
4.5. ПРИТИРКА (ДОВОДКА) ПЛОСКИХ ПОВЕРХНОСТЕЙ
Притирка – отделочная операция, которую выполняют свободным абразивом или пастами с помощью плоских притиров путем прижима с определенным усилием обрабатываемой
91
поверхности заготовки к плоской поверхности притира и перемещения заготовки относительно притира, при которой снимается тончайший слой металла – до 0,02 мм.
Целью притирки является получение плотного, или герметичного разъемного и подвижного соединения. Точность притирки до 0,002 мм.
Доводка служит для получения не только требуемых форм
ишероховатости поверхности, но и заданных размеров с допуском по 3-му квалитету точности.
Плоские поверхности притирают после чистового шлифования, хонингования, фрезерования, протягивания, шабрения.
Относительное перемещение заготовки и притира должно обеспечивать движение зерен абразива по новым, не повторяющимся траекториям.
Притиры изготавливают из чугуна или бронзы и на их поверхность наносят абразивную суспензию (микропорошок с машинным маслом). В качестве абразивов достаточно часто
используют окись хрома (Cr2O3), крокус (порошок (Fe2O3) окиси железа) и венскую известь (порошок углекислого кальция с примесью магния и железа).
По твердости, режущим свойствам и производительности окись хрома стоит на первом месте. Наиболее чистую поверхность обеспечивает венская известь. В качестве смазывающего материала используют смесь машинного масла с керосином.
При использовании венской извести применяют спирт, а при использовании крокуса – вазелин.
Для доводочных работ широко используют пасты ГОИ (государственного оптического института).
Пасты ГОИ содержат термически обработанную (прокаленную) окись хрома, жиры и органические поверхностно-активные кислоты (олеиновую или стеариновую).
Пасты ГОИ делятся на грубые (40 мкм), средние (16 мкм)
итонкие (7 мкм и менее). Цифры указывают толщину снятого слоя со стальной закаленной плитки при 100 возвратно-поступа- тельных движениях притира.
92
Существует ручная и машинная притирка (доводка). Ручная доводка подразделяется на предварительную,
среднюю, чистовую, отделочную и зеркальную.
Предварительная ручная доводка обеспечивает точность
5–7-го квалитета и шероховатость поверхности Ra = 0,32–1,25 мкм. Припуск от 0,015 до 0,025 мм.
Средняя ручная доводка обеспечивает точность 4–5-го квалитета и шероховатость поверхности Ra = 0,16–0,32 мкм.
Припуск 0,01–0,015 мм.
Чистовая ручная доводка обеспечивает точность 4-го квалитета и шероховатость поверхности Ra = 0,04–0,16 мкм. Припуск
0,005–0,01 мм.
Отделочная ручная доводка обеспечивает точность 3–4-го квалитета и шероховатость поверхности Ra = 0,01–0,04 мкм.
Припуск 0,0025–0,005 мм.
Зеркальная ручная доводка обеспечивает точность 3-го квалитета и шероховатость поверхности Ra < 0,01 мкм. Припуск от 0,001 до 0,0025 мм.
При ручной доводке существенную, если не основную, роль играет квалификация рабочего и культура производства в целом.
Машинная притирка (доводка) плоских поверхностей осуществляется на специальных плоско-доводочных станках с использованием плоских, как правило, чугунных притиров и специальных приспособлений.
Существуют станки для односторонней плоской доводки и станки для одновременной доводки двух параллельных плоскостей заготовки, установленной между двумя плоскими притирами.
При односторонней доводке на рабочую поверхность притира наносят пасту ГОИ соответствующей зернистости. Затем к поверхности притира посредством специального прижимного устройства заготовку или заготовки, установленные в кассете, прижимают к рабочей поверхности притира. Кассете с заготовками сообщают медленное (от 2 до 5 об/мин) вращение (ось кассеты перпендикулярна рабочей плоскости притира и не совпадает с центром притира). Притиру сообщают рабочее движение
93
в горизонтальной плоскости по заданной траектории (круговой, конхоидной, циклоидной или растровой – в виде фигуры Лиссажу с большим периодом возврата) со скоростью 15–40 м/мин. Усилие прижима заготовки 0,05–0,3 МПа.
Притирка (доводка) на станках, движение притира которых осуществляется по круговой, конхоидной или циклоидальной траектории, обеспечивает точность деталей 5–6-го квалитета с шероховатостью поверхности Ra = 0,08–0,32 мкм. Использование станков, у которых притир совершает рабочее движение по растровой траектории (абразивные зерна каждый раз проходят по новой траектории, не повторяя траекторию движения предыдущего зерна), позволяет достичь точности 3–4-го квалитета и шероховатости поверхности Ra = 0,04–0,16 мкм.
Припуск для предварительной машинной притирки равен
0,010–0,025 мм, а для окончательной – 0,005–0,010 мм.
4.6. ПОЛИРОВАНИЕ ПЛОСКИХ ПОВЕРХНОСТЕЙ
Полирование – это отделочная операция обработки поверхности полировальными кругами (войлочными, матерчатыми, джутовыми, лепестковыми и др.) и лентами. Припуск под полировку не оставляют.
На рабочей поверхности полировальных кругов при помощи специальных клеев закрепляют абразивные зерна.
В качестве абразивной составляющей достаточно часто используют окись хрома (Cr2O3), крокус (порошок (Fe2O3) окиси железа) или венскую известь (порошок углекислого кальция с примесью магния и железа). По твердости, режущим свойствам и производительности окись хрома стоит на первом месте. Наиболее чистую поверхность обеспечивает венская известь.
Целью полирования является снижение шероховатости поверхности.
Полирование не исправляет дефекты формы и размеров, полученные на предыдущих операциях.
94
Режимы полирования назначают из условия прочности полировальных кругов на разрыв, удержания абразива на рабочей поверхности полировального круга и обеспечения условий сохранения режущих свойств абразивных зерен. Полирование осуществляют при помощи шлифовальных (электрических или пневматических) машинок, а также на плоскошлифовальных и полировальных станках.
Шероховатость поверхности достигает Ra = 0,04–0,32 мкм.
4.7. ШАБРЕНИЕ ПЛОСКИХ ПОВЕРХНОСТЕЙ
Шабрением называется операция по снятию (соскабливанию) с поверхности заготовки очень тонких слоев металла специальным режущим инструментом – шабером.
Цель шабрения – обеспечение плотного прилегания сопрягаемых поверхностей и герметичности (непроницаемости) подвижных соединений.
Шабрением обрабатывают прямолинейные поверхности, например, направляющие станин прецизионных станков.
Для получения поверхности высокого качества последовательно выполняют черновое, получистовое и чистовое шабрения.
Шабрение широко применяется в станкостроении и инструментальном производстве, как окончательный процесс обработки незакаленных поверхностей.
Широкое применение шабрения объясняется особыми качествами полученной шабрением поверхности, которые состоят
вследующем:
–в отличие от шлифованной или полученной притиркой абразивами поверхности шаброванная поверхность более износостойка, потому что не имеет шаржированных в ее поры остатков абразивных зерен, ускоряющих процесс износа;
–шаброванная поверхность лучше смачивается и дольше сохраняет смазывающие вещества благодаря наличию так называемой разбивки этой поверхности, что также повышает ее износостойкость и снижает величину коэффициента трения;
95
– шаброванная поверхность позволяет использовать самый простой и наиболее доступный метод оценки ее качества по числу пятен прилегания на единицу площади.
Шабрение можно выполнять вручную или механическим способом.
Первый способ требует большой затраты времени при высокой квалификации исполнителя, но обеспечивает высокую точность и качество обработанной поверхности.
Второй способ осуществляется с помощью специальных станков, на которых шабер получает возвратно-поступательное движение. При этом способе требуется меньше времени, однако качество обработки оставляет желать лучшего.
Ручным шабрением за один проход шабера снимают слой металла толщиной от 0,005 до 0,07 мм и достигают отклонение от плоскостности 0,003–0,01 мм. Количество пятен на один квадратный дюйм шабренной поверхности составляет более 30.
Припуск под шабрение составляет в зависимости от размера плоскости от 0,1 до 0,5 мм.
96
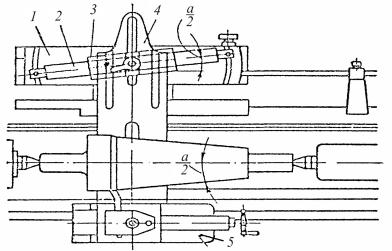
5. МЕТОДЫ ОБРАБОТКИ КОНУСНЫХ ПОВЕРХНОСТЕЙ
5.1. ОБРАБОТКА НАРУЖНЫХ КОНУСНЫХ ПОВЕРХНОСТЕЙ
Обработка наружных конусных поверхностей с образующей достаточно большой протяженности производится точением на станках токарной группы тремя методами:
–точением с помощью конусных линеек;
–точением методом настройки кинематических цепей;
–точением при смещенном заднем центре.
Обработка конуса по конусной линейке (рис. 5.1) осуществляется следующим образом.
Рис. 5.1. Схема обработки конуса на токарном станке с помощью конусной линейки
97
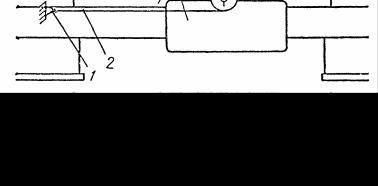
На кронштейне 1 установлена линейка 2, которая может быть повернута на заданный угол (равный половине угла α при вершине обтачиваемого конуса). По конусной линейке 2 перемещается ползун 3, связанный с поперечной кареткой 5 жесткой тягой 4. Поперечная каретка освобождена от винта поперечного суппорта. При движении продольной каретки 5 по направляющим станины станка ползун 3, перемещаясь по линейке 2, через тягу 4 заставляет поперечную каретку вместе с резцом следовать по направлению конусной линейки 2 под заданным углом α/2.
Отсутствие конусных линеек на токарных станках не препятствует обработке конусов.
Использование настроенных кинематических цепей позволяет посредством несложного приспособления обрабатывать конусы. Для этого достаточно (рис. 5.2) установить на винт
Рис. 5.2. Схема обработки конуса методом настроенной кинематической цепи
суппорта 7 поперечной подачи вместо маховика барабанчик 5 и, прикрепив к его поверхности гибкий металлический трос 2, навить один конец троса на поверхность барабанчика 5; другой конец троса 2 необходимо закрепить в неподвижном упоре 1.
При продольном перемещении слева направо суппорта 4 продольной подачи винта (от ходового винта) барабанчик 5 благодаря натяжению троса 2 начнет поворачиваться и вращать
98
ходовой винт поперечной подачи. Резец 6 будет обрабатывать на заготовке 3 наружный конус с заданным углом (каждому углу конуса будет соответствовать барабанчик строго определенного диаметра). Погрешность выполнения угла конуса будет зависеть от соотношения диаметров барабанчика 5 и троса 2. Чем больше эта величина, тем точнее выполнение угла конуса.
Для обеспечения принудительного движения резца 6 при перемещении суппорта 4 в обоих направлениях (слева направо
исправа налево) необходимо к наружной цилиндрической поверхности барабанчика 5 прикрепить два металлических троса 2, свободные концы которых присоединить к станине станка.
Конец одного троса 2 необходимо присоединить к станине станка слева от суппорта 4 (как показано на рис. 5.2), а конец другого троса – справа от суппорта 4 (на рис. 5.2 не показано).
Конусы с малым углом при вершине (до 10–12°) на заготовках, имеющих центровые отверстия и установленных в центрах (передний и задний) станка, можно обрабатывать точением при смещении заднего центра станка в горизонтальном направлении.
Обработка конусов с большим углом при вершине (более 12°)
иотносительно малой протяженностью образующей (до 250 мм) производится точением на токарных станках за счет поворота верхних салазок поперечного суппорта с резцедержателем и закрепленным в нем резцом на заданный угол, равный половине угла при вершине обрабатываемого конуса.
Продольная подача в направлении, параллельном образующей конуса, обеспечивается перемещением верхних салазок.
Обработку конусов с протяженностью менее 50 мм можно обеспечить применением широких резцов с передним углом в плане, равном половине угла при вершине обтачиваемого конуса. При этом резцу сообщают перемещение на врезание поперечным суппортом станка.
Кроме того, обработку наружных конусных поверхностей с любыми углами при вершине обтачиваемого конуса любой протяженности можно производить на токарных станках с ЧПУ.
99
Обработку наружных конусных поверхностей, к которым предъявляются повышенные требования по точности и шероховатости поверхности, можно производить на круглошлифовальных станках.
Шлифование длинных конусов с малым углом при вершине (до 12°) производят в центрах методом продольной подачи периферий или торцом шлифовального круга при повороте стола станка на заданный угол, равный половине угла при вершине шлифуемого конуса.
Шлифование коротких конусов (протяженность конуса менее высоты шлифовального круга) производят в центрах периферией шлифовального круга методом врезания при повороте шпиндельной бабки (оси шлифовального круга) на угол, равный половине угла при вершине шлифуемого конуса.
Для обработки конусной поверхности на станках, ось шпинделя шлифовального круга которых параллельна оси центров, рабочую поверхность шлифовального круга необходимо править под углом, равным половине угла при вершине шлифуемого конуса, и шлифование производить методом врезания.
При особо высоких требованиях к чистоте обработки конусной поверхности ее можно подвергнуть суперфинишу или полированию.
5.2. ОБРАБОТКА ВНУТРЕННИХ КОНУСНЫХ ПОВЕРХНОСТЕЙ
Обработка внутренних конусных поверхностей (конических отверстий) производится точением на станках токарной группы, зенкерованием и развертыванием на токарных и сверлильных станках, шлифованием на внутришлифовальных станках и притиркой на доводочных станках.
Обработка конусных отверстий относительно большого диаметра (более 100 мм) с протяженностью образующей до 500 мм в основном производится растачиванием на токарных станках за счет поворота верхних салазок поперечного суппорта с резце-
100