
книги / Неформованные огнеупоры. Т. 1 Общие вопросы технологии
.pdfобщем виде на рис. 6.30 для керамических суспензий, твердеющих по концентраци онному механизму.
За оптимальный следует принимать такой интервал Ср в котором еще сохраняются низкая пористость и высокая прочность вяжущего (кривые /, 2), но реологические показатели (кривые 7,5) уже имеют существенно пониженные значения. Этот интер вал Сухарактеризуется высокой седиментационной устойчивостью, удовлетворитель ной проницаемостью и довольно высокой скоростью формования. Для более тонко дисперсных суспензий, отличающихся вследствие этого постоянством пористости и прочности вяжущего в большем интервале Су(кривые 7', 8*), Су целесообразно смес тить в область меньших Сг
Кроме концентрации, важным фактором является температура суспензии при ее введении в заполнитель. Как показано в главе 4, повышение температуры концентри рованных керамических суспензий до 60-70 °С может резко уменьшать аномалию их вязкости, что существенно для технологии керамобетона, так как позволяет приме нять суспензии с большей Су .
Ниже на примере кварцевого керамобетона показаны как основные технологичес кие параметры, так и свойства литых бетонов, полученных как в СЖФК заполнителя, так и полученных по обычной технологии (“плавающий” каркас заполнителя ПК).
Применительно к кварцевой керамике, формуемой шликерным литьем, актуальность технологии керамобетона состоит еще и в возможности существенного ускорения процесса формования. Обусловлено это тем фактом, что вследствие низкой пористос ти, продолжительность набора толстостенных отливок может достигать нескольких суток [6.34].
В исследованиях [6.22] для получения кварцевого керамобетона применяли порис тый заполнитель (бой сухих или обожженных изделий из кварцевой керамики). В ка честве вяжущего применяли водные суспензии кварцевого стекла (содержание час тиц размером до 5 мкм 25-35 %, содержание частиц более 63 мкм 5-10 %; плотность суспензии изменяли в пределах 1,60-1,88 г/см3 путем разбавления дистиллированной водой). Заполнитель характеризовался ситовым размером 2-5; 5-7; 7-10; 10-15; 1520 мм. Формование образцов вели в гипсовых (активных) формах: кубы с ребром 5 и 7 см, балки — 4х4х 16 см.
Изучены два основных способа получения керамобетона с жесткофиксированным (ЖФК) и плавающим каркасом (ПК). Принципиальные схемы получения керамобетонов с различными структурами показаны на рис. 6.26,6.27. Принципы структурообразования керамобетонов должны выбираться с учетом типа заполнителя и вида изде лий. Способ структурообразования за счет обезвоживания керамических суспензий пористыми заполнителями может найти широкое распространение в том случае, если заполнители обладают удовлетворительными капиллярными свойствами. Учитывая, что используемый заполнитель (бой обожженной кварцевой керамики) обладает по
ристостью 10—12 %, а его коэффициент упаковки |
(в случае монофракционного |
|
состава) — 0,50-0,55, коэффициент влагоемкости каркаса |
весьма низок и при оп |
ределенном разбавлении суспензии в каркасе заполнителя оказывается недостаточно объема пор для процесса структурообразования керамобетона. В связи с этим наблю дается большая разница в продолжительности формования материала в активных и
неактивных формах. Например, если в активных (гипсовых) формах струюурообразование кубов с ребром 7 см осуществляется за 1,5-3 ч, то в неактивных — за 8-16 ч.
Для выбора оптимальных технологических параметров структурообразования керамобегона варьировали структурой, составом и ситовым размером заполнителя, плот ностью суспензии. Изучено влияние смачивания заполнителя.
Формование керамобетона с ПК изучали на бое необожженной кварцевой керамики и на обожженном заполнителе. В этом случае заполнитель вводили в суспензию с расчетом его объемного содержания Су = 0,35-0,40, после чего формовали образцы. Свойства такого керамобетона после сушки (/ = 105-110 °С) и обжига приведены в табл. 6.4.
Т а б л и.ц а 6.4
Характеристика исходных материалов и свойства кварцевого керамобетона с плавающим каркасом заполнителя
Заполнитель из |
Размер |
|
Свойства керамобетона с плавающим каркасом |
|
||||
частиц |
|
|
|
После обжига при 1200 °С |
||||
боя кварцевой |
Исходного после сушки при 100 °С |
|||||||
заполни- |
||||||||
керамики |
|
|
|
|
|
|
||
теля, мм |
у, г/см3 |
Лн,% |
Осж, МПа |
У, г/см3 |
Ян, % |
а Сж, МПа |
||
|
||||||||
|
|
|||||||
Обожженной |
10-15 |
1,88 |
14,8 |
7,0 |
2,01 |
9,0 |
28,0 |
|
|
7-10 |
1,87 |
15,4 |
10,0 |
1,92 |
11,1 |
37,0 |
|
|
5 -7 |
1,87 |
15,4 |
8,4 |
1,91 |
9,6 |
57,2 |
|
|
2 -5 |
1,87 |
15,4 |
9,6 |
1,97 |
11,6 |
52,0 |
|
Необожженной |
10-15 |
1,82 |
17,4 |
5,6 |
1,92 |
12,4 |
36,4 |
|
|
7 -10 |
1,85 |
16,2 |
6,4 |
1,96 |
11,7 |
53,1 |
|
|
5 -7 |
1,82 |
17,5 |
6,0 |
1,94 |
10,9 |
58,0 |
|
|
2 -5 |
1,85 |
16,5 |
2,8 |
1,97 |
11,1 |
95,0 |
Т а б л и ц а 6.5
Характеристика исходных материалов и свойства керамобетона с ЖФК заполнителя
|
|
|
|
Свойства кварцевого керамобетона с |
|||||
|
|
Размер |
Коэффи |
жесткофиксированным каркасом |
|
||||
|
Заполнитель из |
Исходного после |
После обжига при |
||||||
Метод введения |
частиц |
циент |
|||||||
боя кварцевой |
|||||||||
суспензии |
заполни |
упаковки |
сушки при 100 °С |
1200 °С |
|
|
|||
керамики |
|
|
|||||||
|
теля, мм |
каркаса |
|
|
|
|
|
||
|
|
|
|
|
|
Ос*. |
|||
|
|
|
|
у, г/см3 |
а » , МПа |
у, г/см3 |
|
||
|
|
|
|
МПа |
|||||
|
|
|
|
|
|
|
Гравитационный |
Обожженной |
10-15 |
0,60 |
1,85 |
6,0 |
1,93 |
25,6 |
То же |
|
7-10 |
0,54 |
1,83 |
8,0 |
1,94 |
31,4 |
|
|
5-7 |
0,54 |
1,88 |
12,8 |
1,99 |
52,6 |
|
|
2-5 |
0,53 |
1,86 |
13,2 |
1,94 |
60,0 |
|
Необож |
10-15 |
0,58 |
1,85 |
4,8 |
1.95 |
16,8 |
|
женной |
|
|
|
|
|
|
_ и_ |
|
7-10 |
0,58 |
1,88 |
11,0 |
2,01 |
59,0 |
|
5 -7 |
— |
1,85 |
9,2 |
1,92 |
52,5 |
|
- н - |
|
2-5 |
— |
1,79 |
7,2 |
1,83 |
32,5 |
Гравнтационный |
Обожженной |
7-10 |
0,64 |
1,87 |
8,0 |
1,89 |
46,0 |
с внброутряской |
|
|
|
|
|
|
|
Максимальные прочностные свойства в случае обожженного заполнителя достига ются при ситовом размере й* = 5+7 мм, на необожженном заполнителе — при й* = = 2+5 мм, хотя и при значении О ' = 5+7 мм и й* = 7+10 мм достигнут предел прочно сти при сжатии сг^, равный 53,1-58,0 МПа. Меньшие значения ст^ в случае использо вания крупного обожженного заполнителя объясняются повышенными напряжения ми, возникающими за счет разности усадок при спекании заполнителя и вяжущей сус пензии.
Аналогичные свойства проявляются и у керамобетона с ЖФК (табл. 6.5).
Характерно, что для заполнителя с одинаковым /)зс, показатели |
примерно адек |
ватны для сравниваемых технологий керамобетона. |
|
В рассматриваемой технологии с применением ЖФК заполнителя весьма важную роль играют плотность и равномерность его упаковки. Из табл. 6.5 видно, что приме нение предварительного виброуплотнения ЖФК заполнителя ф = 7+10 мм) позволи ло повысить его с 0,54 до 0,64 и увеличить исходный предел прочности при сжатии кварцевого керамобетона в 1,45 раза (с 31,4 до 46,0 МПа).
Следует отметить, что для керамобетонов, получаемых по технологии ЖФК, в оп ределенных случаях характерен дефект их структуры, названный “сухим контактом” [6.24]. Он состоит в том, что в участках плотного расположения зерен заполнителя отсутствует прослойка вяжущего. Этот дефект устраняется в технологии керамобето нов с “плавающим” каркасом заполнителя [6.20].
В ряде случаев эффективным является также способ, промежуточный между техно логиями керамобетонов с “плавающим” каркасом заполнителя и жесткофиксирован ным. Этот способ применяется в промышленных объемах при формовании донной части глуходонных керамобетонных сталеразливочных стаканов [6.19]. В таком керамобетоне объемная доля заполнителя (1-10 мм) достигает 70 %, а пористость, как правило, не превышает 9 %. При определенных условиях [6.2,6.37] на основе кварце вого стекла получены мелкозернистые материалы пористостью 4-7 %.
Технология 1п$ИСа$Р в производстве низкоцементных бетонов. По оценкам ряда зарубежных специалистов считается, что в области технологии производства и при менения низко- и сверхнизкоцементных огнеупорных бетонов наиболее значимым до стижением последних лет является разработка технологии 1пй1Саз1®, запатентованная фирмой “А1соа” (Европа) [6.26-6.28, 6.37]. Указанный патент США [6.25] заявлен в 1998 г. и опубликован в декабре 2000 г. В ряде публикаций, например, [6.28], эта тех нология названа “революционно новой”. Сообщается, что ТпГйСаз!® 1есЬпо1о§у (тех нология заливки каркаса фракционированного заполнителя) предназначена как для выполнения монолитных футеровок, так и для изготовления крупных фасонных огне упоров (блоков). Согласно публикациям [6.26], схема процесса показана на рис. 6.31.
По этой технологии форму или опалубку заполняют сухим фракционированным ломом конвертерных огнеупоров (18-22 мм) или зернистым табулярным глиноземом (6-12 мм). Каркас заполнителя, характеризующегося К 58-60 %, заливают (пропи тывают) мелкозернистым сверхнизкоцементным саморастекающимся бетоном (1пШ(га(юп Саз1аЫе) влажностью 9-9,5 % с максимальным размером заполнителя ^ пвx = = 1 мм. Вводимый в каркас заполнителя гидратационно твердеющий мелкозернистый бетон (матричная система) имеет сложный (преимущественно трехкомпонентный) состав и занимает 40-42 % от общего объема сформировавшегося бетона. Согласно
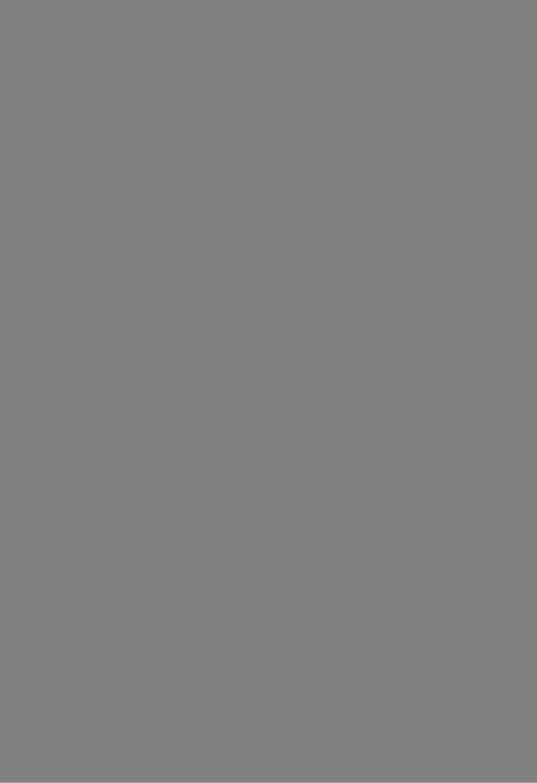
че 0,25 мм должно составлять 55-85 %. Это идеально соответствует вышерассмот ренным характеристикам порошков, применяемых для матричного бетона. Это же можно отметить применительно к соотношению дисперсности вяжущей (матричной) системы и заполнителя. Еще ранее [6.21] было установлено, что “минимальный раз мер частиц зернистого каркаса должен быть примерно на порядок больше макси мальногоразмера частиц в шликере ”.Для рассмотренных случаев получения 1пШСа$1- бетонов соотношение й т]пзаполнителя к й тмвяжущего для фракционированного лома огнеупоров составляет 18 (близко к рис. 6.29, б), а для зернистого табулярного глино зема — 6 (близко к рис. 6.29, в). В технологии керамобетонов успешно опробованы различные варианты рассмотренного принципа: для изготовления монолитных футеровок, в процессах “намоноличивания” и бетонирования в скользящей опалубке, при изготовлении фасонных огнеупоров и высокоточных керамических изделий [6.1,6.20].
6.1.6. Центробежное формование из литых бетонов
Метод центробежного литья в производстве огнеупоров был развит в технологии кварцевых сталеразливочных изделий [6.2,6.19]. На начальной стадии развития и при менения этого способа формования сталеразливочных огнеупоров (стаканы, теплоза щитные трубы, ролики печей для отжига стали) для формования применяли ВКВС плавленого кварца плотностью 1,88-1,89 г/см3 с содержанием частиц крупнее 63 мкм 5-8 %. По сравнению со шликерно-литыми огнеупорами, такой способ имеет суще ственно меньшую продолжительность формования (15-20 мин против 10-20 ч). Од нако по структуре и свойствам материала центробежно-формованные отливки, по срав нению со шликерно-литыми из аналогичных суспензий, характеризовались следую щими недостатками:
•повышенной пористостью (17-20 % против 12-14 %);
•существенным расслоением зернового состава отливки по толщине и неравномер ной структурой,
•значительным перепадом пористости отливки по толщине;
•более крупнопористым строением материала вследствие того, что значительная доля высокодисперсных (<5 мкм) частиц, содержащихся в исходной суспензии, уда ляется со сливом после окончания формования.
Как следует из рис. 6.32, а, разница в пористости между образцами из внутреннего
инаружного слоя отливки достигает 9 % (при температуре обжига 1050 °С).
При повышении температуры обжига опытных образцов до 1100°С и выше, в них
наблюдается усадка, которая имеет существенно отличные значения для материала наружного и внутреннего слоя (рис. 6.32, б). Поэтому температура термообработки центробежно-формованных изделий с рассмотренными параметрами ограничена ве личиной начальной усадки.
С целью существенного улучшения структуры и качества центробежно-формованных изделий в дальнейшем была повышена плотность исходных ВКВС до 1,91-1,93 г/см3 с одновременным увеличением содержания как крупной (>63 мкм) фракции (до 15-20 %), так и мелкой (<1 мкм).
Дальнейшее повышение качества и стойкости кварцевых стаканов связано с распрос транением принципов технологии керамобетона применительно к процессу центробеж-
Рис. 6.32. Влияние температуры обжига / на открытую пористость Я (а) и линейную усадку Д/ (б) образцов из наружного (/), среднего(2) ивнутреннего (5) слоя (потолщинестенки) стаканов центро бежного формования
ного формования изделий. Для производства прямоточных стаканов за счет оптимиза ции исходного зернового состава и режимов формования представилась возможность реализовать технологию, позволившую получить равномерную по толщине структуру материала при содержании крупной фракции (0,063-1 мм) в пределах 55-60 %. Такой среднезернистый керамобетон, полученный на основе формовочных смесей с зерно вым составом, соответствующим области 3 на рис. 6.30, характеризуется пористостью 10-12 % и вместе с тем тонкокапиллярной структурой, определяющей повышенную стойкость к службе. В последующем процесс центробежного литья успешно опробован применительно к керамобетонам муллитокорундового состава [6.3, 6.5].
Исходные формовочные системы для центробежного формования этих керамобетонов характеризуются высоким (массовая доля 50-65 %) содержанием огнеупорного заполнителя с 7 )^ = 1-5-5 мм. В процессе формования, сопровождающегося “сжатием” системы (уплотнение средних и крупных частиц с переходом в “слив” части высоко дисперсных), содержание заполнителя в отформованном материале повышается до 65-80 % с соответствующим уменьшением содержания тонкодисперсной (матричной) составляющей, частично удаляемой со сливом.
В качестве характерного примера, иллюстрирующего особенности центробежного способа формования, на рис. 6.33 сопоставлены интегральные кривые зернового рас пределения исходной формовочной системы и сформованного материала при изго товлении стакана-коллектора на основе муллитокорундового керамобетона (толщина изделия 45 мм).
Исходная формовочная система содержит 40 % тонкодисперсной составляющей, вводимой посредством ВКВС муллита с добавкой 8Ю2 и 60 % сложного (муллит + корунд) полидисперсного (0,063-5,0 мм) заполнителя. Смесь этого состава, характе ризующаяся Сг = 0,84 и влажностью около 5 %, после формования при незначитель ных (3-4 м/с) величинах окружной скорости вращения позволяет получить высоко плотный (пористость 13-14 %) материал, который имеет более крупный зерновой со став. По сравнению с исходным составом содержание тонкодисперсной составляю щей (<63 мкм) понижается до 22 % с соответствующим ростом содержания заполни теля до 78 %.
Рис. 6.33. Интегральные кривые зернового распре делениятвердой фазы исходной муллитокорундовой керамобетонной смеси (7) и сформованного из нее центробежным методом изделия (2): р — содержа
ние фракций; ^ — диаметр частиц
По сравнению с центробежным формованием материалов на основе ВКВС [6.2,6.19] применительно к формованию изделий из керамобетонных смесей процесс характе ризуется целым рядом преимуществ. Прежде всего, благодаря предельному концент рированию исходной формовочной системы представляется возможным резко пони зить коэффициент избытка смеси при формовании (с 10-20 до 5-8 %). Если в первом случае отмечается существенное различие плотности материала по толщине (за счет сегрегации частиц по крупности), то во втором оно практически отсутствует. И если в сливе центробежного формования кварцевой керамики из ВКВС значение7 )^ не пре вышает 5-10 мкм, то при формовании из керамобетонных смесей, несмотря на значи тельно (в 2-3 раза) меньший избыток системы, Отахсоставляет 50-100 мкм.
Проведены сопоставительные исследования метода центробежного формования с методами вибролитья и вибропрессования [6.5]. Данные по влиянию температуры тер мообработки на пористость и прочность этих керамобетонов показаны на рис. 6.34.
Методами вибролитья при влажности 4,5 и 4,8 % были сформованы керамобетоны из смеси как исходного состава (см. рис. 6.33, кривая 7), так и характерного для керамобетона центробежного формования (см. рис. 6.33, кривая 2). Вибролитые керамобе тоны характеризуются исходной пористостью 16-17 %, которая незначительно (на 0,5— 1,0 %) повышается после термообработки. Предел прочности при сжатии их в исход ном состоянии 5-11 МПа, но резко возрастает уже при относительно низкотемпера турной термообработке.
Рис. 6.34. Влияние температуры термообработки I наПт и оея муллитокорундовых керамобетонов:
7 — зерновой состав соответствует кривой 2 на рис. 6.33, влажность 4,8 %, вибролитье; 2 — зерно вой состав соответствует кривой 7 на рис. 6.33, влажность 4,5 %, вибролитье; 3 — зерновой состав
соответствует кривой 7 на рис. 6.33, добавка 25 % корундового заполнителя крупностью 5-10 мм, влажность 3,2 %, вибропрессование при давлении пригруза 0,1 МПа
В случае дополнительного введения в исходную формовочную систему (см. рис. 6.33, кривая /) крупной фракции элекгрокорунда (5-10 мм) в количестве 25 % при виброп рессовании представилось возможным понизить влажность смеси до 3,2-3,4 % с од новременным уменьшением исходной пористости вибропрессованного керамобетона до 14,5 %. При этом существенно (до 15 МПа) увеличился предел прочности при сжа тии как исходного, так и термообработанного при 1000-1200 °С керамобетона. При веденные на рис. 6.34 данные свидетельствуют о том, что керамобетоны не уступают или превосходят по свойствам известные НЦОБ соответствующего состава. Это сви детельствует об эффективности технологии керамобетонов.
По всей видимости, показатели свойств керамобетонов, полученных центробежным формованием, будут выше, чем виброформованных. Это следует из того, что методом центробежного формования из крупнозернистых формовочных систем можно полу чить наиболее плотные керамобетоны (пористость 13-14 % против 14,5-17 % для виб роформованных). Последнее обусловлено специфическими особенностями метода. Если при применении вибролитья и вибропрессования в сформованном керамобетоне, как правило, содержатся макропоры (захваченный воздух), то в материале, сфор мованном центробежным методом, этот тип пор отсутствует. Кроме того, при центро бежном методе формования концентрация твердой фазы в вяжущем (матрице) может быть повышена по сравнению со значением Су исходной суспензии. В виброформо ванных керамобетонах указанный эффект “сжатия” вяжущей фазы (матрицы бетона) не достигается.
6.1.7. О структурообразовании литых бетонов
при частичном обезвоживании
Большой практический интерес к производству и применению саморастекающихся НЦОБ и СНЦОБ вызван, прежде всего, тем фактом, что последние являются очень удобными применительно к ремонту износившейся футеровки. В практике металлур гического производства, например, для ремонта желобов доменных печей и сталераз ливочных ковшей, распространена следующая технология ремонтов. После локаль ного износа монолитной огнеупорной футеровки (например, в шлаковом поясе) пос леднюю подвергают подготовке (очистке от металла, шлака и т.д.), затем вставляют шаблон. Зазор между последним и изношенной футеровкой заливают литым бетоном. При этом поверхность очищенного (“старого”) бетона является достаточно пористой и неспеченной. Вследствие этого после заливки “свежего” бетона на контактной по верхности происходит его структурообразование за счет частичного обезвоживания на пористой подложке. Если в случае применения НЦОБ и СНЦОБ этот фактор структурообразования является дополнительным (вспомогательным), то в случае керамо бетонов — основным. В связи с изложенным, ниже на примере ВКВС рассмотрены общие закономерности структурообразования при частичном обезвоживании. Они яв ляются общими для любых водных дисперсных систем (суспензий и масс).
Ранее было показано [6.2,6.38], что в зависимости от области применения ВКВС их первичное структурообразование (переход из текучего состояния в твердое) осуще ствляется посредством или частичного обезвоживания за счет пористой формы (при шликерном литье), пористого заполнителя (при формовании керамобетонов), другой
пористой подложки (например, огнеупора) или кладки (при использовании ВКВС в качестве наливных масс, мертеля, огнеупорного покрытия), или отжатая части жид кости (при центробежном формовании). В работе [6.38] на примере ВКВС кислого и кислотно-амфотерного составов впервые обобщено влияние основных факторов, оп ределяющих механизм их структурообразования. Независимо от вида пористой под ложки и типа ВКВС физическая сущность механизма структурообразования состоит в частичном обезвоживании системы до состояния, соответствующего критической концентрации. Движущей силой процесса является эффективное давление пористой подложки, определяемое ее капиллярным давлением и активной пористостью.
Переход ВКВС, характеризующейся исходной концентрацией С^ в состояние СУкр сопровождается концентрированием системы. Величину уменьшения объема при этом предложено характеризовать коэффициентом усадки К = (СИкр/Ск) -1 . По мере повы шения относительной концентрации ВКВС показатель К понижается. Показатель при структурообразовании является важнейшим из факторов, так как фактически ха рактеризует отношение объема жидкости, поглощенной пористой подложкой (фильт рат) к объему образовавшейся при этом массы. Следует отметить, что в процессах фильтрования для характеристики аналогичной взаимосвязи принят обратный пока затель — отношение объема осадка к объему фильтрата.
Рассматриваемые вопросы механизма структурообразования в значительной степе ни разработаны применительно к процессу шликерного литья керамических материа лов. Образование (набор) слоя массы (отливки) на пористой форме в дальнейшем рас сматривается по аналогии с процессами фильтрации как образование несжимаемого осадка на несжимаемой (форма) перегородке при фильтровании с постоянной разно стью давлений Д/?. Исходя из положений теории фильтрации, зависимость скорости
образования набранной массы описывается уравнением |
|
*мЯф*ф |
(6.10) |
т Рлцг ПфКф+Км |
|
где Н— толщина набранной массы; /?ф, # ф, # ф — капиллярное давление, проницае мость и пористость формы соответственно; Ки— проницаемость набранной массы; Л,,,— вязкость жидкой фазы суспензии; Р — фактор, определяемый концентрацией системы и пористостью осадка.
Анализ влияния различных характеристик ВКВС на кинетику их структурообразования, проведенный в работе [6.38], дал основание несколько расширить число факто ров, определяющих кинетику процесса. Так, к основным факторам отнесены такие характеристики ВКВС, как их седиментационная устойчивость, концентрация колло идного компонента, среднеповерхностный диаметр частиц. Основные факторы урав нения (6.10) могут быть выражены объемными фазовыми характеристиками. Так, фак тор р, характеризующий взаимосвязь между Суи Лотл, можно определить в виде соот ношения: Р = пу= Си/СКкр.
Несмотря на многообразие влияющих факторов, временная зависимость толщины слоя набранной массы при шликерном литье или при других случаях структурообра зования ВКВС может быть выражена отношением: Н= А?г|/2, где К — константа скоро
сти набора массы (мм*мин,/2), которая комплексно учитывает все факторы, определя ющие скорость струюгурообразования.
При структурообразовании ВКВС наиболее значимым параметром является гидро динамическое сопротивление слоя осадка (или набранной массы). Ранее [6.34, с. 117] была предложена методика по определению коэффициента фильтрации Кф воды через предварительно набранный на пористой форме слой массы. По аналогии с законом Дарси принимается, что Кфявляется в то же время и коэффициентом пропорциональ ности, характеризующим гидравлическую проводимость набранной массы при набо ре последующих ее слоев. Этот показатель для случая структурообразования ВКВС является аналогом сопротивления слоя осадка в процессах фильтрации [6.38].
Как и в случае процессов фильтрования при постоянном давлении и меняющейся скорости процесса [6.38], кривая роста слоя набранной массы, как это следует из рис. 6.35, является параболой.
Существенное замедление процесса во времени определяется соответствующей за висимостью коэффициента Кф, резкое понижение которого отмечается уже при тол щине набранной массы в 1-2 мм. В связи с этим, если продолжительность набора слоя массы толщиной 4 мм на начальной стадии составляет ~1 ч, то для увеличения к
на 4 мм на конечной стадии (с 22 до 26 мм) требуется >7 ч. |
|
Очевидно, что существует взаимосвязь между показателями Кфи |
соответствую |
щей системы и средней скоростью набора массы в любом из узких промежутков вре мени литья. С учетом того, что К’ показывает объемную долю фильтрата по отноше нию к объему набранной массы, а ЛГф = (у/х)/Р (где V— объем отфильтрованной воды за время т на поверхности Г, мм/мин), показатель Л(Дт) = ЛТф (Л^/100)"1мм/мин.
Так, для т = 14-ь19 ч при К * = 0,00015 мм/мин Л(т) = 0,00015 (20/100)"1мм/мин, что совпадает с экспериментальными данными рис. 6.35.
Закономерности понижения Кфпо мере роста к в существенной степени обусловле ны падением статического давления жидкости в осадке Дрос и пористой форме Дрф. По некоторым литературным данным, при атмосферном давлении гипсовые формы обла дают капиллярным давлением 0,1-0,2 МПа.
Значительное влияние на кинетику процесса структурообразования оказывают гид родинамические характеристики и всасывающая способность пористой подложки. Как
Рис. 635. Зависимостьтолщиныслоянабранноймассы к (У) икоэффициентаеефильтрации/Гф(2) от продолжительности процесса(а), атакжеК отЛ (б)дляслучаяшликерного литья из ВКВС кварце вогостекла (Ск= 0,73; Пт —12,5 %; = 20 %) в гипсовые формы