
книги / Современные и перспективные термолитические процессы глубокой переработки нефтяного сырья
..pdfДанная схема получила широкое распространение и внедряется на всех совре менных УЗК, но она имеет ряд недостатков:
—организация сброса предохранительных клапанов в абсорбер Е-52 обусловливает наличие большой поверхности конденсаторов-холодильников по верху абсорбера (ВХ-51), аналогичной для верха основной фракционирующей колонны К-1, пос кольку при сбросе ППК поверхность охлаждения необходимо рассчитывать на полную производительность установки. Учитывая, что сброс ППЖ происходит крайне редко (по опыту, раз в несколько лет), то значительная часть оборудования будет простаивать;
— подача продуктов с низа абсорбера на верх в качестве абсорбента приводит к уносу высококипящих продуктов и частичек кокса с верха абсорбера в систе му охлаждения, что приводит в выходу из строя конденсаторов-холодильников из-за «забивания» внутренней поверхности трубок высококипящими продуктами пропарки и охлаждения, имеющими положительную температуру застывания. Первая закрытая система прогрева камер, пропарки и охлаждения кокса НПЗ
России была внедрена на НПЗ г. Перми по технологии «Foster Wheeler».
В 2008 г. на ООО «Ново-Уфимский НПЗ» внедрена и успешно эксплуатируется закрытая система по технологии УГНТУ. Схема была внедрена на УЗК 21-10/300 ОАО «НУНПЗ» в 2007 г. и эксплуатируется в настоящее время. Для вновь строящей ся УЗК на ОАО «Уфанефтехим» разработана схема улавливания продуктов пропарки и охлаждения кокса.
Узел улавливания продуктов прогрева, пропарки и охлаждения кокса ОАО «Уфанефтехим». Продукты пропарки и охлаждения подаются в нижнюю часть абсорбера К-104 (рис. 3.25). В линию подачи продуктов пропарки и охлаждения подается тяжелый газойль коксования с температурой 200-250 °С для исключения конденсации воды и разрушения эмульсии. В эту же линию подаются дистиллятные продукты прогрева камер из емкости прогрева.
Сверху абсорбера при температуре 150 °С выводятся пары воды, дистиллятные продукты прогрева камер, пропарки и охлаждения кокса, которые после охлаждения в конденсаторе-холодильнике поступают в сепаратор, где происходит разделение на газ, жидкие нефтепродукты и воду. Газ из сепаратора направляется на очистку МЭА, жидкие нефтепродукты направляются в емкость орошения основной ректификаци онной колонны.
Отделившаяся вода направляется на узел очистки кислой воды.
Подача продуктов охлаждения из коксовой камеры в абсорбер производится до температуры 150 °С. При снижении температуры ниже 150 °С продукты охлаждения поступают, минуя абсорбер, через конденсатор-холодильник в сепаратор.
Из кубовой части абсорбера выводятся уловленные продукты прогрева, пропарки и охлаждения и тяжелого газойля коксования, которые через холодильник подаются на 3-ю тарелку абсорбера в качестве орошения, а балансовое количество через холо дильник направляется в шлемовые трубопроводы камер коксования. В эту же линию подаются жидкие продукты из емкости прогрева камер коксования. Учитывая, что количество паровой фазы в верхней части абсорбера достаточно велико, а также для исключения уноса тяжелых высококипящих фракций в конденсатор-холодиль ник и сепаратор предусматривается подача тяжелого газойля на верхнюю тарелку.
151
При этом две верхние тарелки абсорбера выполняют роль отбойников для тяжелых высоковязких продуктов, поступающих по линии рециркуляции с низа абсорбера на 3-ю тарелку.
Рисунок 3.25 — Принципиальная технологическая схема блока улавливания
продуктов пропарки и охлаждения
Тяжелый газойль, поступающий на верхнюю тарелку, конденсирует и смывает высококипящие компоненты с 1 и 2-й тарелки. Температура подаваемого в абсорбер тяжелого газойля регулируется путем изменения расходов газойля, подаваемого на смешение, выводимого до и после холодильника.
Для исключения возможности забивания трубок конденсатора-холодильника тяжелыми высоковязкими продуктами пропарки и охлаждения кокса и повышени ем надежности его работы производится поочередная промывка одной из секций конденсатора-холодильника (всего шесть секций), предварительно отключенной от парового потока продуктов пропарки и охлаждения. Остальные секции работают
вобычном режиме.
Вкачестве промывочного агента используется тяжелый газойль коксования, тем пература которого регулируется смешением потоков тяжелого газойля до и после холодильника. После промывки тяжелый газойль направляется либо в линию подачи кулинга в шлема камер коксования, либо в линию возврата ЦО в основную ректи фикационную колонну.
152
Продукты пропарки и охлаждения поступают в нижнюю часть абсо |
Р б е р а g -9 |
под тарелки (рис. 3.26). |
Рисунок. 3.26 — Схема улавливания продуктов пропарки
иохлаждения кокса УЗК 21-300 ОАО «НУНПЗ»
Вабсорбере 10 клапанных тарелок.
На верхнюю тарелку абсорбера Е-9 подается тяжелый газойль коксования в сме си с продуктами пропарки и охлаждения, поступающими с низа абсорбера. Про дукты пропарки и охлаждения в смеси с тяжелым газойлем подаются в абсорбер после воздушного холодильника АВО-8 . Для исключения попадания воды в про дукты пропарки и охлаждения температура верха Е-9 поддерживается на уровне 130-140 °С подачей необходимого количества тяжелого газойля, минуя АВО-8 .
Уловленные продукты пропарки и охлаждения выводятся вместе с тяжелым га зойлем.
С верха абсорбера продукты прогрева и охлаждения вместе с водяным паром поступают в конденсатор воздушного охлаждения КВО-5, из которого поступают с теплообменник-доохладитель Т-5, после которого подаются в сепаратор С-1.
Из сепаратора С-1 с низа конденсированная вода сбрасывается в канализацию, продукты пропарки и охлаждения откачиваются с установки. С верха сепаратора отводится газ на факел.
При достижении температуры продуктов охлаждения, поступающих из коксовой камеры, ниже 150-160 °С поток в абсорбер Е-9 закрывается и продукты охлаждения напрямую направляются в КВО-5 и далее через Т-5 в сепаратор С-1.
Прогрев коксовых камер проводят в колонне К-2. Продукты прогрева насосом Н-7а подают или в линию тяжелого газойля на входе в АВО-8 , или в линию вывода котельного топлива.
Дистиллятные продукты прогрева направляются в К-1.
153
3.7. Совершенствование системы гидроудаления кокса на УЗК
Извлечение образовавшегося кокса из коксовых камер занимает значительное место в процессе производства и обработки кокса. Состояние системы выгрузки кокса наряду с качеством сырья и технологическими параметрами процесса кок сования определяет продолжительность цикла коксования и производительность установки.
На первых установках ЗК (до середины 30-х гг. XX в.) извлечение кокса из камер производилось механическим способом, используя различные шарошки и долота, что приводило, даже при относительно небольших размерах коксовых камер, к ис пользованию в основном ручного труда, и продолжительность удаления и зачистки камеры составляла до 35 ч [30].
Внастоящее время извлечение кокса из реакционных камер УЗК осуществляется исключительно гидравлическим способом.
Способ гидравлического удаления заключается в воздействии высоконапорных водяных струй на массив кокса с разрушением его при воздействии струй и вынос отколотых кусков кокса в подкамерное пространство.
Схема гидроудаления кокса на всех установках идентична. Вода под высоким давлением (до 25 МПа) и большим расходом (до 250 м3 /ч) подается центробежным насосом по полой штанге к гидрорезаку, находящемуся на ее нижнем конце и вве денному в коксовую камеру. Верхний конец штанги соединен с механизмами, обес печивающими поступление в нее воды, возможность перемещения по высоте камеры
ивращение. Гидрорезак снабжен струеформирующими соплами, поступающая из которых вода за счет аккумулированного запаса энергии производит разрушение кокса.
Сначала в коксовом массиве производится формирование сквозного отверстия по центру камеры струями воды, направленными вниз. После формирования вер тикального сквозного отверстия горизонтальными струями воды производится гид роразрушение кокса до полного освобождения камеры. На рис. 3.27 представлена принципиальная схема гидроудаления кокса из коксовых камер.
Гидравлический резак /, в котором производится формирование разрушающей водяной струи, является одним из главных механизмов системы гидроудаления, обес печивающих производительность выгрузки и ее продолжительность. Гидравличес кие резаки создавались специально для применения на установках ЗК.
Вотличие от гидрорезаков механизмы, обеспечивающие перемещение его внутри коксовой камеры, в основном заимствованы из бурового машиностроения [62]. Это ро торы 2 обеспечивающие вращение штанги 3 с гидрорезаком, гибкий буровой рукав 4, позволяющий перемещать штангу с гидрорезаком в вертикальном направлении, вер тлюг 5 для соединения гибкого рукава с вращающейся штангой, многоскоростная лебедка 6 для перемещения штанги с гидрорезаком в вертикальном направлении. Для подачи большого количества воды с высоким давлением используются мощные центробежные насосы 7.
Это оборудование обеспечивает подачу воды высокого давления к соплам гидро резака, плавное вращение и вертикальное перемещение его внутри коксовой камеры для осуществления гидроудаления кокса по заданной технологии.
154
Важнейшим показателем процесса гидроудаления является производительность, которая должна обеспечивать освобождение камеры за регламентное время. Произ водительность гидроудаления можно увеличить за счет сокращения числа необходи мых для обрушения кокса проходок струи путем выбора оптимального соотношения между давлением и диаметром струи, механической прочностью кокса, скоростью нарезки щелей в коксовом массиве.
Рисунок 3.27 — Принципиальная схема гидроудаления кокса из коксовых камер:
1 — |
коксовая камера; 2 — |
гидрорезак; 3 — штанга; 4 — ротор вращения штанги с гидрорезаком; |
5 — |
вертлюг; 6 — буровой |
рукав; 7 — лебедка поднятия-опускания штанги с гидрорезаком; 8 — |
|
высоконапорный насос гидрорезки; 9 — подпорная емкость |
Гидрорезаки по назначению подразделяют на разделенные и комбинированные. На первых УЗК использовались раздельные резаки. Один резак использовался для бурения центрального отверстия в коксовом массиве — гидродолото. В этом ре заке имеются 2-3 ствола, направленных вниз вертикально и под некоторым углом (рис. 3.28). Такая конструкция обеспечивает образование вертикальной скважины по оси коксовой камеры размером 0 ,5-0, 8 м.
Для разрушения основного массива кокса применяют резак, имеющий сопла, направленные горизонтально или под некоторым углом (рис. 3.29).
Основным недостатком раздельных гидрорезаков является то, что для их замены процесс гидроудаления прерывается.
155
Рисунок 3.28 — Резак для пробуривания центрального отверстия
В России и странах СНГ все установки оснащены комбинированными гидро резаками, которые совмещают возможность пробуривания центральной скважины и резки основного массива кокса [63]. На рис. 3.30 представлен наиболее распро страненный гидрорезак ГРУ-ЗР, состоящий из корпуса 7, в нижней части которого расположены бурильные сопла 2 для пробуривания вертикального отвода. В верхней части корпуса расположен узел переключения 3, позволяющий переключать поток воды к режущим соплам 4 для резки основного массива кокса. Переключение сопел с бурения вертикального ствола на резку производится вручную. Для этого водяной насос останавливают или переводят на циркуляцию, а резак выводят из камеры.
156
Рисунок 3.30 — Комбинированный резак гидроудаления кокса:
1 — корпус; 2 — сопла бурильные; 3 — узел переключения; 4 — сопла режущие
При выгрузке кокса из камер диаметром до 5,5 м используются резаки типа ГРУ-ЗР-170, рассчитанные на давление до 17,0 МПа. Подача воды осуществляет ся центробежными насосами типа ПЭ-270х150, с электродвигателями мощностью 2000 кВт.
Для коксовых камер Ш7 м используют гидрорезаки ГРУ-ЗР-250 с возможнос тью эксплуатации при давлении до 25,0 МПа. Фактическое давление на гидрорезаке составляет 23,0 МПа. Используемый насос типа АПЭ-380 с электродвигателем до 3000 кВт.
Для подачи воды от гибкого рукава к штанге с резаком используется в основном вертлюги ВБНМ-75, а для вращения штанги с гидрорезаком — роторы Р360-Ш15.
Сварные штанги на всех установках заменены на цельнотянутые квадратного сечения.
На ряде установок для поднятия и вращения штанги с гидрорезаком используют гидроприводы, что позволяет обеспечить бесступенчатое плавное регулирование скоростей в оптимальном диапазоне.
На зарубежных установках для поднятия и опускания штанги также используют многоскоростную лебедку, а вращение штанги осуществляется принципиально подругому. Для этого разработан специальный вращатель, установленный на верхнем конце штанги, совмещающий в себе функции вертлюга и ротора. В качестве привода вращателя используется сжатый воздух.
За рубежом для гидроудаления используют как раздельные гидрорезаки, так и комбинированные. В последние годы разработаны конструкции гидрорезаков [64], позволяющих осуществлять переключение с режима бурения на режим резки дис танционно. Один из вариантов гидрорезака представлен на рис. 3.31.
157
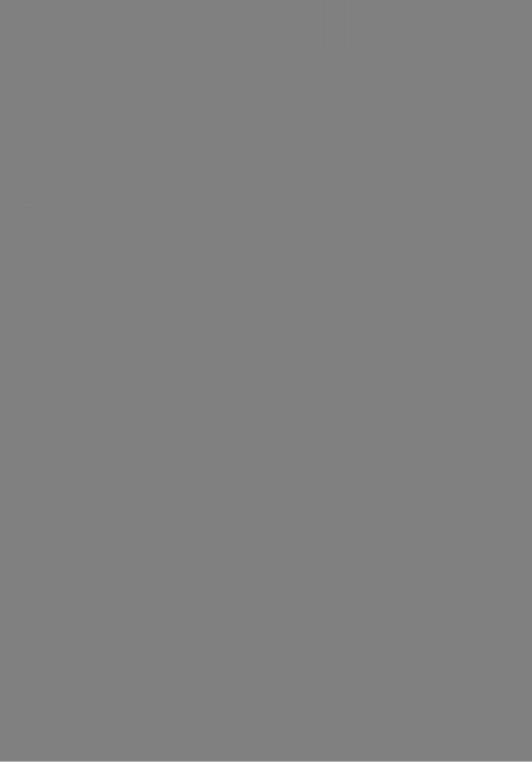
либо по окончании выгрузки и предварительного обезвоживания. В соответствии с этим системы транспорта разделяются на два типа [63]:
—работающие одновременно с гидровыгрузкой кокса (системы с «жесткой» свя зью);
—осуществляющие транспорт кокса независимо от гидровыгрузки и после пред варительного обезвоживания (системы с разрывом).
На установках с «жесткой» связью между гидроудалением и транспортом предъ
являются повышенные требования к оборудованию, т. к. выход из строя одного из узлов системы транспорта приводит к прекращению гидроудаления, что приводит к нарушению цикла работы камер, снижению производительности и даже оста новке.
Основными достоинствами систем с «жесткой» связью являются компактность, хорошая чистота рассева кокса на фракции крупности, меньшая загрязненность тер ритории.
Основными недостатками являются необходимость большого запаса по произво дительности и мощности из-за неравномерной скорости выгрузки кокса.
Системы транспорта с «жесткой» связью между гидроудалением и транспортом кокса разделяются:
—выгрузка из камер производится после дробления на ленту транспортера, имею щего отверстия в днище для отвода воды и подающего кокс системой транспор теров на склад;
—выгрузка кокса из камер после дробления непосредственно в вагоны-хопперы, имеющие отверстия для стока воды и мелких фракций кокса в лоток между рель сами. После заполнения коксом одного вагона-хоппера под камеру подается сле дующий. Выгруженный кокс в вагонах подается на склад [65];
—полностью закрытая система выгрузки и последующего транспорта кокса — са мотечная и с шламовым насосом [6 6 ].
Полностью закрытые системы выгрузки кокса применяются для удовлетворения требований к чистоте окружающей среды и для предотвращения загрязнения кокса в районах, где бывают песчаные бури и высока вероятность озоления полученного кокса, в особенности специальных марок.
Всамотечных системах (рис. 3.32) коксовая камера расположена над емкостью для приема и осушки кокса. Между коксовой камерой и приемной емкостью распо ложена дробилка, и дробленый кокс вместе с водой гидрорезки поступает в закры тую емкость. Вода из емкости удаляется при помощи дренажных устройств, и после дренирования воды кокс выгружается на закрытую конвейерную систему и подается на склад кокса. Самотечная закрытая система выгрузки кокса требует очень высоких расположений коксовых камер.
Взакрытых системах со шламовым насосом (рис. 3.33) коксовая камера распо
ложена на одном уровне с емкостью для осушки, а кокс после дробления вместе с водой выгружается в закрытый шлюз, куда подается дополнительное количество воды. Из шлюза кокс с водой поступает на прием шламового насоса и подается в верх нюю часть емкости для осушки кокса. Из емкости осушки вода поступает в шлюз самотеком. Кокс после предварительной осушки из емкости поступает на закрытый конвейер, подающий кокс на склад для хранения.
159
Рисунок 3.32 — Закрытая система выгрузки в обезвоживающий бункер:
1 — коксовая камера; 2 — дробилка; 3 — бункер обезвоживающий; 4 — шламовый насос; 5 — конвейер подачи кокса на склад; 6 — емкость грязной воды; 7 — емкость высоконапорного насоса гидроудаления
Закрытые системы используют на предприятиях, расположение которых не до пускает загрязнения окружающей среды (например, вблизи городов) и при получе нии коксов специального назначения (игольчатого, например), где предъявляются жесткие требования к загрязнению кокса.
Системы с «разрывом», в которых транспортирование кокса на склад осущест вляется независимо от системы гидроудаления, разделяются на системы, произво дящие выгрузку на бетонную площадку, расположенную на нулевой отметке и на системы, производящие выгрузку в прикамерную яму-накопитель, на дне которой смонтирован коллектор сбора и отведения воды. Выгрузка кокса в вагоны-хопперы и полностью закрытая система выгрузки и транспорта с использованием обезвожи вающих емкостей, в которые кокс поступает непосредственно из коксовых камер, имеются только на зарубежных установках замедленного коксования.
160