
книги / Сварка трубопроводов
..pdf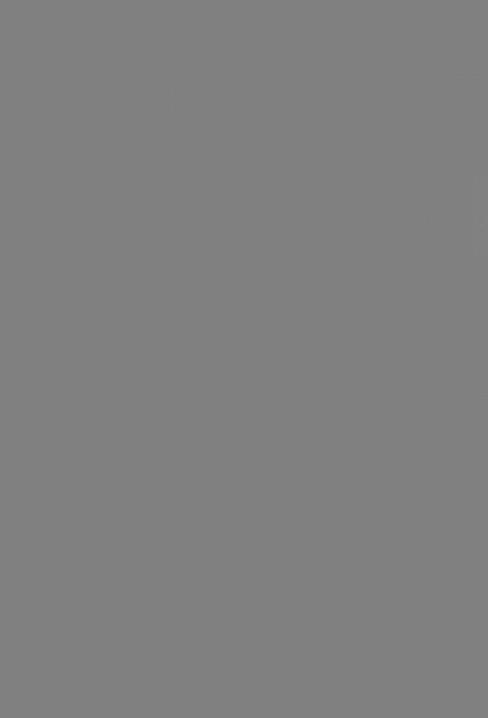
ченной линии реза. При этом краска и масло выгорают, а окалина отстает от металла. Затем поверхность металла зачищают металли
ческой щеткой.
Процесс резки начинают с нагревания металла. Подогреваю щее пламя резака направляют на край разрезаемого металла и на гревают до температуры воспламенения его в кислороде, практи чески составляющей температуру плавления. Затем пускают струю режущего кислорода и перемещают резак вдоль линии раз реза. Кислород сжигает верхние нагретые слои металла. Теплота, выделяющаяся при сгорании, нагревает нижележащие слои металла до температуры воспламенения и поддерживает непре рывность процесса резки.
Резку металла большой толщины выполняют следующим образом. Мундштук резака вначале устанавливают перпендику лярно поверхности разрезаемого металла так, чтобы струя подо гревающего пламени, а затем и режущего кислорода располага лась вдоль вертикальной грани разрезаемого металла. После про грева металла до температуры воспламенения пускают струю ре жущего кислорода. Перемещение резака вдоль линии резания начинают после того, как в начале этой линии металл будет проре зан на всю его толщину. Чтобы не допустить отставания резки в нижних слоях металла, в конце процесса следует постепенно замедлить скорость перемещения резака и увеличивать наклон мундштука резака до 10—15 ° в сторону, обратную его движению. Рекомендуется начинать процесс резки с нижней кромки. Предва рительный подогрев до 300 —400 °С позволяет производить резку с повышенной скоростью. Скорость перемещения резака должна соответствовать скорости горения металла. Если скорость переме щения резака установлена правильно, то поток искр и шлака выле тает из разреза прямо вниз, а кромки получаются чистыми, без на теков и подплавлений. При большой скорости перемещения реза ка поток искр отстает от него, металл в нижней кромке не успева ет сгореть и сквозное прорезание прекращается. При малой скорости сноп искр опережает резак, кромки разреза оплавляют ся и покрываются натеками.
Давление режущего кислорода устанавливают в зависимости от толщины разрезаемого металла и чистоты кислорода. Чем выше чистота кислорода, тем меньше его давление и расход.
Ширина и чистота разреза зависят от способа резки и толщи
ны разрезаемого металла. Машинная резка дает более чистые кромки и меньшую ширину разреза, чем ручная резка. Чем боль ше толщина металла, тем больше ширина разреза.
Процесс резки вызывает изменение структуры, химического состава и механических свойств металла. При резке низкоуглеро дистой стали тепловое влияние процесса на ее структуру незначи тельно. Наряду с участками перлита появляется неравновесная со ставляющая сорбита, что даже несколько улучшает механические качества металла.
2.2.4. Газыг применяемые при сварке и резке
Кислород при атмосферном давлении и обычной температуре — это газ без цвета и запаха, несколько тяжелее воз духа. При атмосферном давлении и температуре 20 °С масса 1м3 кислорода равна 1,33 кг. Сгорание горючих газов или паров горю чих жидкостей в чистом кислороде происходит очень интенсивно, в зоне горения развивается высокая температура [11].
Технический кислород добывают из атмосферного воздуха, который подвергают обработке в воздухоразделительных уста новках, где он очищается от пыли, углекислоты и осушается от влаги. Перерабатываемый в установке воздух сжимается комп рессором до высокого давления и охлаждается в теплообменни ках до сжижения. Жидкий воздух разделяют на кислород и азот. Процесс разделения происходит вследствие того, что температура кипения жидкого азота ниже температуры жидкого кислорода на 13 °С. Азот оказывается более легкокипящим газом и испаряет ся первым, поэтому его отводят из воздухоразделительной уста новки в атмосферу. Жидкий чистый кислород накапливается в воздухоразделительном аппарате. При испарении кислорода им заполняют баллоны под давлением, создаваемым с помощью ком прессора. Технический кислород транспортируют в стальных бал лонах (см. рис. 2.8) согласно требованиям ГОСТ 949 —73 или в ав тореципиентах под давлением (15 ± 0,5) МПа (150 ± 5 кгс/см2) или (20 ± 1,0) МПа (200 ± 10 кгс/см2) при 20 °С. При наполнении бал лонов, их хранении и транспортировании в интервале температур от минус 50 °С до плюс 30 °С давление газа в баллоне должно соот ветствовать приведенному в табл. 2.3.
Таблица 2.3
Давление кислорода в баллоне в зависимости от температуры окружающего воздуха
|
Давление газа |
Допустимое |
Температу в баллоне, МПа |
отклонение, |
|
ра газа, °С |
(кгс/см2) |
МПа (кгс/см2) |
15 МПа (150 кгс/см2) при 20 °С
Давление газа, |
Допустимое |
в баллоне, МПа |
отклонение, |
(кгс/см2) |
МПа (кгс/см2) |
20 МПа (200 кгс/см2) при 20 °С
-50 |
9,3 (93) |
|
12,3 |
(123) |
|
-40 |
10,2 (102) |
|
13,2 |
(132) |
|
-30 |
11,1 (111) |
|
14,6(146) |
|
|
-20 |
11,9(119) |
|
15,8 |
(158) |
+ 1,0(10) |
-10 |
12,7 (127) |
± 0,5 (5) |
16,9 |
(169) |
|
0 |
13,5 (135) |
|
17,9(179) |
|
|
+ 10 |
14,3(143) |
|
19,0(190) |
|
|
+ 20 |
15,0(150) |
|
20,0 |
(200) |
|
+ 30 |
15,7 (157) |
|
21,0 |
(210) |
|
Ацетилен (С2Н2) является химическим соединением углерода с водородом. Это бесцветный горючий газ, имеющий резкий ха рактерный запах. Длительное вдыхание ацетилена вызывает голо вокружение, тошноту, а иногда и сильное общее отравление. Аце тилен легче воздуха: 1м3 ацетилена при 20 °С и атмосферном дав лении имеет массу 1,09 кг. Ацетилен является взрывоопасным га зом. Температура самовоспламенения ацетилена лежит в преде лах от 240 до 630 °С и зависит от давления и присутствия в ацетиле не различных примесей. При атмосферном давлении смесь ацети лена с воздухом взрывается при содержании в ней ацетилена 2,2 % и более, а в смеси с кислородом при содержании — 2,8 % и более. Взрыв ацетилено-воздушной или ацетилено-кислородной смеси может произойти от искры, пламени или сильного местного нагре ва. Поэтому обращение с карбидом кальция и с ацетиленом требу ет осторожности и строгого соблюдения правил техники безопас ности.
В промышленности ацетилен получают: при разложении жид ких горючих веществ, таких как нефть, керосин; воздействием электродугового разряда.
Промышленный ацетилен закачивают в баллоны (рис. 2.9), где
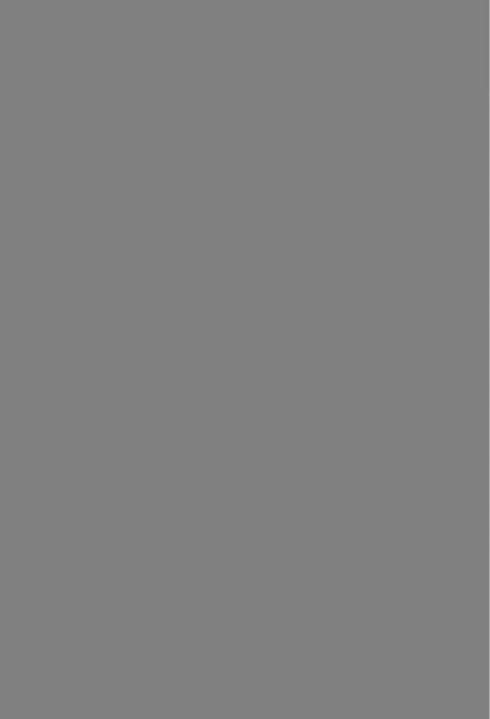
давление в наполненном баллоне не должно превышать 1,9 МПа (19 кгс/см2) при 20 °С. Для сохранности наполнительной массы нельзя отбирать ацетилен из баллона со скоростью более 1700дм3/ч.
При резке металла используют пропан. Пропан — это горю чий газ, который получают при добыче природных газов или при переработке нефти. Обычно получают не чистый пропан, а с при месью бутана до 5 —30 %. Такая смесь именуется пропан-бутано- вой. Для сварочных работ пропан-бутановая смесь доставляется потребителю в сжиженном состоянии в специальных баллонах (см. рис. 2.9). Переход смеси из жидкого состояния в газообразное происходит самопроизвольно в верхней части баллона из-за мень шей удельной массы газа по сравнению со сжиженной смесью. Технический пропан тяжелее воздуха и имеет неприятный специ фический запах.
Характеристики газовых баллонов представлены в табл. 2.4.
|
|
|
Таблица 2.4 |
|
Сводная таблица характеристик газовых баллонов |
||||
Характеристика |
Кислород |
Ацетилен |
Пропан |
|
баллона |
||||
|
|
|
||
Размеры, мм: |
|
|
|
|
высота |
1370 |
1370 |
950 |
|
диаметр |
219 |
219 |
309 |
|
Масса без газа, кг |
67 |
83 |
35 |
|
Давлениегаза, МПа |
15 |
2 |
1,6 |
|
Состояние газа |
Сжатый |
Растворенный |
Сжиженный |
|
Емкость, дм3 |
40 |
40 |
50 |
|
Количество газа |
6 м3 |
5,32 м3 |
24 кг |
2.2.5. Машинная кислородная резка
Механизированную резку производят газореза тельными машинами "Орбита-2м, "Спутник-3" [1, 24].
Перед резкой следует удалить из трубы на участке длиной не менее 0 ,5 - 1,0 м снег и грязь, так как наличие влаги ухудшает ка чество реза и структуру металла кромки. Разрезаемый участок трубы шириной 50—100 мм по периметру необходимо тщательно
зачистить механической или ручной проволочной щеткой. На по верхности трубы не должно быть слоя праймера, следов изоляции, окалины, ржавчины, пыли, масляных и жировых загрязнений. Резка неочищенного металла приводит к значительному сниже нию производительности процесса, ухудшению качества поверх ности реза.
Скорость резки и давление кислорода должны соответство вать табл. 2.5.
Таблица 2.5
Режимы машинной резки
Режимы машинной резки при применении Толщина ацетилена пропана металла, Скорость Давление Давление Скорость Давление Расход
ммрезки, кислорода, горючего резки, кислорода, горючего
|
мм/мин |
МПа |
газа, МПа |
мм/мин |
МПа |
газа, л/м |
|
5 -10 |
600-400 |
0,35 |
-0,4 0,04-0,045 |
500-400 |
0,4-0,45. |
25-35 |
|
10-20 |
500-400 |
0,4 |
-0,5 |
0,04-0,045 |
400-300 |
0,45-0,55 |
35-45 |
20-30 |
400-350 |
0,5 |
-0,7 |
0,045-0,05 |
300-350 |
0,55-0,75 |
45-55 |
Резку начинают прожиганием в теле трубы отверстия следую щим образом: резак подводят к месту пробивки отверстия, зажи гают горючую смесь резака, разогревают место пробивки до тем пературы воспламенения в струе кислорода и постоянно включа ют подачу режущего кислорода.
После пробивки отверстия включают привод перемещения резака по периметру трубы. Резку труб производят по замкнутому периметру трубы, начиная с нижнего положения.
В процессе резки необходимо следить за соблюдением выб ранного режима, т. е. сохранять неизменными состав смеси, рас стояние между мундштуком резака и металлом, скорость резки, давление газов.
Шероховатость кромки реза не должна превышать 0,16
и0,32 мм при толщине разрезаемого металла соответственно 5—15
и16 —30 мм.
Перед сваркой после машинной газокислородной резки необ ходимо тщательно удалить с кромки реза грат и окалину.
По кромкам после машинной газокислородной резки разре шается выполнять ручную дуговую сварку электродами с основ ным видом покрытия, автоматическую сварку под флюсом по руч ной подварке и двустороннюю.
Сварку электродами с покрытием целлюлозного вида разре шается выполнять только после механической обработки кромок реза или зачистки их шлиф-машинками.
Резка труб при отрицательных температурах окружающего воздуха может сопровождаться появлением трещин в кромке реза. Во избежание образования трещин и получения более пла стичного металла у линии реза в зависимости от состава стали, толщины металла, режима резки необходимо применять предва рительный подогрев.
Для механизированной воздушно-плазменной резки труб при строительстве магистральных трубопроводов предназначена уста новка "Орбита ПЛ-1" [2].
Для выполнения резки контейнер с установкой необходимо расположить на расстоянии не менее 1,5 —2 м от разрезаемой трубы.
На обрабатываемую трубу монтируют направляющий пояс (рис. 2.10), соответствующий ее диаметру. Для обеспечения точно сти резки необходимо произвести тщательную выверку установки направляющего пояса. Ходовую часть машины "Орбита" монтиру ют на направляющий пояс.
Поверхность трубы в месте, где начинается рез и где должно произойти возбуждение основной дуги, очищают от окалины, гря зи, масла, ржавчины, краски, а полость трубы — от грязи, снега и др. При резке изолированных труб место начала реза необходи мо очистить от изоляции, после чего в этом месте зачистить поверх ность трубы до металлического блеска.
Плазмотрон закрепляют в державке суппорта ходовой части машины "Орбита" Расстояние между плазмотроном и поверхно стью разрезаемой трубы должно быть 10—15 мм, а его положение не должно изменяться в процессе резки.
Угол наклона плазмотрона к образующей трубы должен соот ветствовать требуемому углу скоса кромок.
Шланги, кабель, ведущие от источника питания к плазмотро ну, располагают таким образом, чтобы в процессе движения ма шины вокруг трубы они не мешали работе плазмотрона.
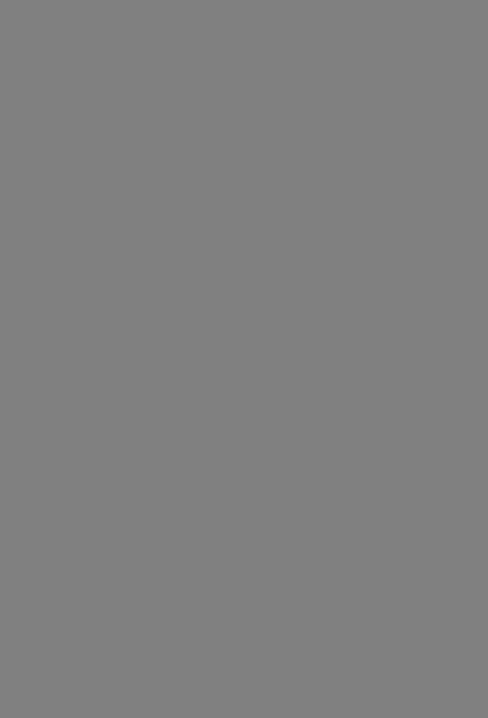
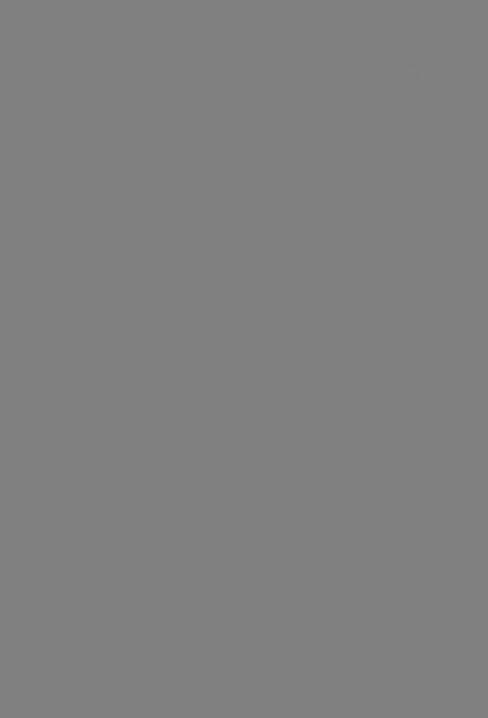