
книги / Мониторинг состояния цементобетонных дорожных конструкций
..pdf
а б
Рис. 2.9. Испытание образцов бетона: а – кернов; б – призм размером 10×10×40 см
Призменная прочность, модуль упругости и коэффициент Пуассона определялись по ГОСТ 24452–80, измерение продольных и поперечных деформаций осуществлялось вплоть до разрушения образцов или до уров-
ня нагрузки 0,9–0,95 Rb, что позволило определить Rcrc0 , Rcrcγ , γ. Продольные деформации измерялись на базе 200 мм индикаторами
часового типа с ценой деления 0,001 мм, а поперечные – тензорезисторами базой 50 мм прибором ИДЦ-1.
Границы микротрещинообразования бетона определялись по методике О.Я. Берга. Нижняя граница микротрещинообразования Rcrc0 определя-
лась величиной напряжений осевого сжатия, при которой начиналось увеличение значения дифференциального коэффициента поперечной деформации µ1 = ∆εn/∆ε от постоянного значения или уменьшение величины приращения внешнего объёма образца ∆Q = ∆ℓ – 2∆εn (∆ε и ∆εn – приращения соответственно продольной и поперечной деформации образцов на данной ступени нагрузки).
Верхняя условная граница образования микротрещин Rcrcγ определя-
лась величиной напряжений осевого сжатия, при которой дифференциальный коэффициент поперечной деформации достигал наибольшей теоретической возможной для твердого тела величины µ1 = 0,5, а приращение внешнего объема образца при нагружении достигало значения ∆Q = 0.
Коэффициент упругости бетона γ определялся как отношение упругой части продольной деформации бетона к его полной деформации на соответствующих ступенях нагружения. В настоящей работе значение коэффициента γ определялось при уровне напряжения σ = 0,85Rb.
81
Морозостойкость определялась по ГОСТ 10060–87, а водонепроницаемость и водопоглощение (W) – по ГОСТ 12730.5–84 и 12730.0–84, 12730.3–78.
Определение гигроскопической влажности, содержания гидратной воды в цементе, исследование коррозиестойкости и водостойкости, диф- ференциально-термический, ренгенографический и петрографический анализ проведены совместно с институтом БелДорНИИ. При этом определение гигроскопической влажности производилось в соответствии с НД, для термоанализа пользовались фоторегистрирующим пирометром Курнакова ФПК-55 с платино-платино-родиевыми термопарами, а рентгенограммы снимались на рентгеновской установке Дрон-2,0 с медной трубкой. Режим трубки: Кν = 32, mA = 20, интенсивность 2000 исп/с, скорость съемки – 2° в минуту.
Реплики для электронной микроскопии были сняты с цементного камня и исследованы методом одноступенчатых Pt/С. Полученные реплики свежих сколов просматривали в электронном микроскопе УЭМВ-100В при увеличении V 9500 р. Увеличение на фотобумаге 10 000 р.
Моделирование, климатических условий осуществлялось повторением циклов, включающих в себя нагрев образцов в сушильном шкафу до температуры 95 °С, выдерживание при этой температуре в течение 4–5 ч,
остывание до температуры 20–5 °С в течение 5–6 |
ч и повторный на- |
грев [17]. |
|
Исследование влияния условий твердения на коррозионную стой- |
|
кость производилось на цементно-песчаных |
балочках размером |
20×20×100 мм. Для обеспечения сопоставимости результатов применялся Вольский песок. Условия предварительного твердения и последовательность проведения эксперимента приведены на рис. 2.4. В качестве агрессивной среды применяли 3 % раствор Na2SO4 и для сравнения – водопроводную воду. Установление скорости и глубины процесса гидратации, возникновения новообразований и проникновения агрессивных
ионов SO24− в глубь образцов проводили при помощи рентгенографиче-
ского, дифференциально-термического и химического анализа.
Наряду с этим устанавливали рост и снижение прочностных характеристик раствора образцов в зависимости от условий и времени предварительного твердения. Коэффициент стойкости (КС) вычисляли как отношение величины средней прочности раствора образцов после определённого срока выдерживания их в агрессивной среде к величине его
82

прочности после твердения в водопроводной воде в течение того же срока. Валовое содержание гипса определяли по общепринятой методике [27, 31, 85]. Определение Са(ОН)2 в образцах, твердевших в воде и растворе Na2SO4, проводили спиртово-глицератным способом.
Статическая обработка экспериментальных данных проводилась по методикам, представленным в работах [56, 68, 141]. Наряду с оценкой влияния добавки ПЯ-01 на стойкость бетонов в условиях воздействия климата проводилось исследование влияния добавки ПЯ-01 на свойства бетоноконструкций и на потребительские свойства конструкций, испытывающих воздействие климатической среды Урала и Западной Сибири. В качестве таких конструкций выбраны предварительно напряжённые дорожные плиты (ПДН), изготовленные ООО «Строительный комплекс Звёздный» на производственных площадках строительных организаций города Перми по проекту Киевского филиала института Союздорпроект (типовые проекты 503-0-042).
Оценка качества плит ПДН производилась по фактическим показателям трещиностойкости, получаемым в результате статических испытаний в соответствии с требованиями проекта и ГОСТ 8829–94.
Плиты испытывались статическим нагружением по схеме, предусмотренной проектом – двумя сосредоточенными силами, приложенными в средней части пролёта на расстоянии 1,5 м от опоры (рис. 2.10) или на консольной части плит (рис. 2.11).
Рис. 2.10. Определение трещиностойкости нижней зоны плит ПДН
83

Рис. 2.11. Определение трещиностойкости верхней зоны плит ПДН
Загружение плит осуществлялось через два деревянных бруска сечением 10×10 см железобетонными плитами размерами 1×1×0,08 м, масса которых позволяла обеспечивать требования ГОСТа по величине нагрузки на всех этапах загружения.
Величины контрольных нагрузок принимались по проекту с введением поправки на величину контрольной нагрузки по трещиностойкости с учётом усадки и ползучести. Загружение конструкций производилось ступенями по 10 % от контрольной нагрузки с 10-минутной выдержкой на ступени, вплоть до 80% контрольной нагрузки по трещиностойкости, после чего величина ступени нагружения снижалась до 5 %, а время выдержки увеличивалось до 15–20 минут. При достижении контрольной нагрузки конструкции выдерживались не менее 2 часов. Образование и раскрытие трещин фиксировалось лупами и микроскопом МПВ-2.
Изучение возможности использования плёнкообразующего препарата К-9 для повышения стойкости бетонов в условиях воздействия климата осуществлялось по двум направлениям: посредством создания плёнки на поверхности образцов и изделий, свободных от опалубки, до прогрева их в термоформах и в виде вторичной защиты пропаренных в камерах ямного типа образцов и изделий.
В первом случае образцы прогревались на специальной установке, обеспечивающей нагрев днища форм. Верхняя поверхность образцов контактировала с внешней средой и покрывалась плёнкообразующим препаратом в один или два слоя. Для сопоставления часть образцов оставалась не покрытой, часть покрывалась лакэтинолем в один или два слоя.
84
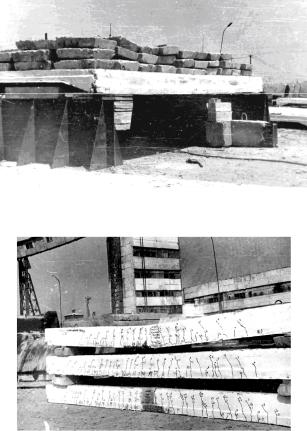
Температура бетона замерялась в центре образцов и варьировалась от 80 до 135 °С, скорость подъёма температуры менялась от 20 до 60 °С в час, время прогрева составило 8 часов, остывание естественное.
Образцы испытывались в холодном состоянии через 10–12 часов после отключения подогрева, часть образцов испытана в возрасте 28 суток и 3 месяцев. Определение эффекта от применении плёнкообразующего препарата К-9 на изделиях, прогреваемых в термоформах, осуществлялось на сваях и лотках.
Во втором случае раствор плёнкообразующего препарата К-9 наносился на поверхность образцов и изделий через 4 часа после их тепловлажностной обработки. Эффект от использования плёнкообразующего препарата в качестве вторичной защиты определялся посредством исследования физико-механических свойств и петрографического анализа образцов бетона и потребительских свойств плит ПГ.
Рис. 2.12. Схема испытания плит ПГ
Рис. 2.13. Плиты ПГ после испытаний
85
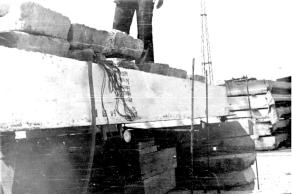
Рис. 2.14. Схема расстановки приборов при испытании плит ПГ
Оценка качества предварительно напряжённых плит ПГ размером 3×6 м производилась по фактическим показателям прочности жёсткости и трещиностойкости плит.
Для сопоставления результатов испытывались плиты, не покрытые плёнкообразующим препаратом К-9, покрытые плёнкообразующим препаратом и плиты, изготовленные из бетонных смесей, пластифицированных добавкой ПЯ-01 и покрытые препаратом К-9.
Схема испытаний плит соответствовала требованиям проекта и представлена на рис. 2.12, плиты после испытаний – на рис. 2.13, схема расстановки приборов – на рис. 2.14.
Выводы по главе 2
1.Разработана и предложена структурно-логическая схема проведения исследований.
2.Выбраны исходные материалы, составы бетонов и технологии изготовления образцов и изделий. Определены характеристики свойств для описания состояний бетонов.
3.Разработаны мероприятия по уменьшению экспериментального шума и повышению надёжности и достоверности получаемых результатов.
4.Разработана схема проведения экспериментальной части работы, направленная на получение ряда последовательных состояний бетонов
иобеспечивающая возможность сопоставления состояний бетонов с добавкой ПЯ-01 и без неё, пропаренных и непропаренных, твердевших под воздействием климата и в нормальных условиях.
86
Глава 3
ВЛИЯНИЕ КЛИМАТИЧЕСКИХ ФАКТОРОВ НА ОСНОВНЫЕ ХАРАКТЕРИСТИКИ СВОЙСТВ И СТРУКТУРЫ ЦЕМЕНТНОГО БЕТОНА
3.1. Прочностные свойства цементобетона
Приведенные для соответствующих возрастов результаты определения кубиковой и призменной прочностей представлены в табл. 3.1.
Таблица 3.1
Усредненные значения кубиковой и призменной прочностей бетона в различных возрастах
|
|
|
|
Значения прочностей бетона, МПа |
|
|||
|
Возраст |
|
1-го состава |
|
2-го состава |
|||
|
непропаренного |
пропаренного |
пропаренного |
|||||
|
|
|
||||||
|
|
|
R |
Rb |
R |
Rb |
R |
Rb |
3 |
суток |
22,5/19,5 |
16,0/11,0 |
37,5/35,0 |
18,0/16,0 |
30,0/27,5 |
20,0/16,0 |
|
14 |
суток |
32,0/27,5 |
25,0/21,0 |
42,5/40,0 |
39,0/37,0 |
45,5/38,5 |
31,5/34,0 |
|
28 |
суток |
28,0/35,5 |
17,5/26,0 |
40,0/43,0 |
37,0/39,0 |
34,5/44,5 |
29,5/36,5 |
|
3 |
месяца |
24,0/49,0 |
17,5/35,5 |
35,0/52,5 |
31,0/44,0 |
27,5/54,5 |
25,0/41,0 |
|
6 |
месяцев |
37,5/56,0 |
23,5/41,5 |
42,0/60,0 |
36,5/47,0 |
35,5/61,5 |
28,5/45,0 |
|
9 |
месяцев |
42,0/60,0 |
32,0/44,5 |
45,0/63,5 |
39,5/47,5 |
37,5/66,5 |
35,5/46,5 |
|
12 |
месяцев |
42,5/61,5 |
35,0/46,0 |
42,5/65,0 |
41,0/47,5 |
41,0/67,5 |
39,0/47,5 |
|
18 |
месяцев |
62,0/63,0 |
34,0/47,5 |
51,5/65,0 |
37,5/47,5 |
50,0/67,5 |
37,5/46,0 |
Примечание. Перед чертой приведены значения характеристик прочностей бетонов, твердевших в условиях воздействия климата, за чертой – в нормальных.
Из этих данных следует, что результатом воздействия климатической среды на прочностные свойства бетонов является увеличение прочности в начальный период до 14 суток и уменьшение в более зрелом возрасте по сравнению с бетонами нормального твердения, что согласуется с результатами других исследователей [104, 132, 146] .
Понижение прочности прекращается в возрасте примерно 90 суток, после чего начинается повышение, интенсивность которого зависит от
87
состава бетона и минимальна для бетонов с добавкой пластификатора ПЯ-01. Спады прочности совпадают в дальнейшем с сезонными изменениями температуры и влажности.
Анализ значений прочностных характеристик с помощью критерия согласия Вилкоксона показывает, что в одном случае, а именно, при со-
поставлении бетонов непропаренных и пропаренных, |
u − |
|
n1n2 |
|
оказалось |
||||
2 |
|||||||||
|
|
|
|
|
|
|
|||
больше соответствующего табличного значения: |
|
u − |
n1n2 |
|
= |56 – 32| = |
||||
|
|
||||||||
|
|
||||||||
|
|
|
|
2 |
|
|
|
|
|
= 24 > 19, где u – полное число инверсий, M = |
n1n2 |
|
– математическое |
||||||
2 |
|
||||||||
|
|
|
|
|
|
|
ожидание.
Следовательно, гипотеза Н0 отбрасывается и делается вывод о неслучайности различия прочностей, значения которых принадлежат к различным генеральным выборкам, то есть пропарка бетона привела к статистически значимому изменению чувствительности к воздействию климата. Сопоставление бетонов непропаренных с пропаренными, пласти-
фицированными добавкой ПЯ-01: |
u − |
n1n2 |
|
= |36 – 24,5| = 11,5 < 16,5 – |
|
||||
|
2 |
|
|
подтвердило нуль-гипотезу H0.
Следовательно, введение добавки привело к повышению чувствительности к воздействию климатической среды, и различие стало статистически незначимым.
В ряде исследований установлены зависимости, связывающие между собой призменную и кубиковую прочности бетонов:
О. Граф |
Rb = (0,85 – 0,81·10–3R)R, |
(3.1) |
Д. Эмпергер |
Rb = (0,80 – 0,23·10–3R)R, |
(3.2) |
A.A. Гвоздев |
Rt = R (1300+R)/(1450+3R), |
(3.3) |
M.H. Малько |
Rb = 1,1(R – 100), |
(3.4) |
Г.Н. Писанко |
Rb = 0,787R, |
(3.5) |
В.Н. Пунагин |
Rb = R/(1,8 – 10–3R), |
(3.6) |
В действующих нормах принято |
Rbn = (0,77 – 0,001B)В |
(3.7) |
Сопоставление значений призменных прочностей, вычисленных по вышеприведенным зависимостям, с экспериментальными для бетонов естественного твердения приведено в табл. 3.2.
88
|
|
|
|
|
|
|
|
|
|
|
Таблица 3.2 |
|
|
|
Сопоставление теоретических и экспериментальных значений призменной прочности |
|
|||||||
|
|
|
|
|
|
|
|
|
|
|
|
|
Возраст |
|
|
Значения (МПа) и погрешность (%) вычисленного по зависимости |
|
||||||
|
|
3,1 |
3,2 |
3,3 |
3,4 |
3,5 |
3,6 |
|
3,7 |
||
|
|
|
|
|
|||||||
|
|
|
|
|
|
|
|
|
|
|
|
3 |
суток |
|
14,0/–12,5 |
16,9/+5,6 |
16,2/+1,25 |
13,8/–13,75 |
17,7/+10,6 |
15,9/–0,6 |
|
16,8/+5,0 |
|
14 |
суток |
|
18,9/–24,4 |
23,4/–6,4 |
21,5/–14,0 |
24,2/–3,2 |
25,2/+0,9 |
23,7/–5,2 |
|
23,8/–4,8 |
|
28 |
суток |
|
17,4/–0,57 |
20,7/+18,5 |
19,3/+10,3 |
21,0/+20,0 |
22,0/+25,7 |
20,6/+17,7 |
|
20,7/+18,3 |
|
3 |
месяца |
|
15,6/–10,8 |
17,8/+1,7 |
17,1/–2,3 |
15,4/–12,0 |
18,8/+7,45 |
17,2/–1,71 |
|
17,9/+2,28 |
|
6 |
месяцев |
|
20,6/–12,4 |
26,6/+13,2 |
24,5/+3,8 |
30,3/+28,9 |
29,6/+25,9 |
29,8/+26,9 |
|
26,4/+12,3 |
|
9 |
месяцев |
|
21,4/–33,1 |
29,4/–8,1 |
26,6/–16,8 |
35,2/+10,0 |
33,0/+3,12 |
34,6/+8,1 |
|
30,6/–4,38 |
|
12 |
месяцев |
|
21,2/–39,4 |
29,8/–14,8 |
27,0/–22,9 |
35,8/+2,28 |
33,4/–4,58 |
35,0/0,00 |
|
31,0/–11,4 |
|
18 |
месяцев |
|
22,4/–34,2 |
35,4/+4,1 |
31,4/–10,6 |
46,2/+35,8 |
40,9/+20,3 |
46,6/+37,0 |
|
37,4/+10,0 |
Примечание. Перед чертой приведены значения Rb в МПа, за чертой – погрешность в %.
89
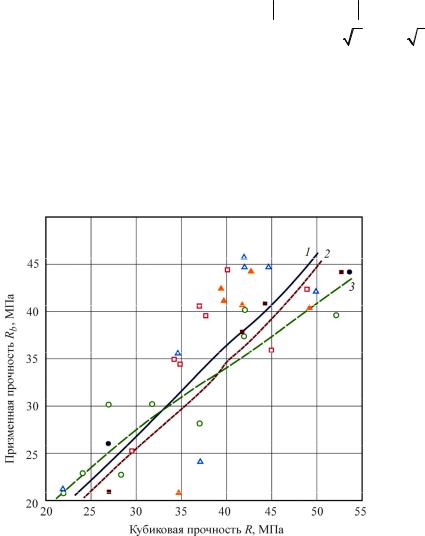
Последовательное применение критерия согласия Колмогорова к выборкам значений Rb, вычисленных по вышеприведенным зависимостям, показало, что только зависимость, предложенная В.Н. Пунагиным, пригодна для описания зависимости Rb от R. D = sup F(x) −F(X ) при сопос-
тавлении с экспериментальными данными дало λ = Dn n = 0,01 8 = = 0,284 <1,36 , где 1,36 – табличное значение D.
Следовательно, различие статистически незначимо.
Обработка экспериментальных данных показала, что несколько измененная зависимость В.Н. Пунагина Rb = R(1,8 – 0,013R) дает лучшую сходимость, причем в таком виде она пригодна и для пропаренных бетонов в возрасте от 14 суток до 1 года. Соотношение кубиковой и призменной прочностей представлено на рис. 3.1.
Рис 3.1. Соотношение кубиковой и призменной прочностей бетона: 1 – формула
Rb = R/(1,8 – 0,013R); 2 – формула Rb = R/(1,8 – 0,01R); 3 – формула Rb = = (0,77 – 0,001B)B. ○ – непропаренный бетон в условиях воздействия климата; ∆ – пропаренный бетон в условиях воздействия климата; □ – пропаренный бетон с добавкой ПЯ-01 в условиях воздействия климата; ● – непропаренный бетон, твердевший в нормальных условиях; ▲ – пропаренный бетон, твердевший в нормальных условиях; – пропаренный бетон добавкой ПЯ-01, твердевший
в нормальных условиях
90