
книги / Специальные плазменные технологии
..pdfрят две дуги – прямого и косвенного действия, первая из которых обеспечивает плавление основного металла, вторая – плавление присадочной проволоки.
По виду применяемого присадочного материала известные способы плазменной наплавки можно разделить на три основные группы: наплавка проволокой или прутками, наплавка по неподвижной присадке, уложенной или каким-либо образом закрепленной на наплавляемой поверхности, наплавка порошком.
В подавляющем большинстве случаев плазменную наплавку выполняют механизированным способом. Нередко процесс наплавки полностью автоматизирован. Лишь в некоторых случаях наплавку производят вручную с использованием в качестве присадки прутков и порошков.
1.3.1. Плазменная наплавка проволокой (прутками)
Плазменная наплавка с присадкой проволоки или прутков отличается наибольшим разнообразием схем включения плазмотрона, присадочного материала и изделия в цепь дуги, которые определяют характер распределения тепловой мощности дуги между присадочным и основным металлами. Наплавку с присадкой одной проволоки выполняют тремя основными способами (рис. 3):
♦плазменной струей с токоведущей присадочной прово-
локой;
♦плазменной дугой прямой или обратной полярности
сэлектрически нейтральной присадочной проволокой;
♦комбинированной (двойной) плазменной дугой прямой или обратной полярности с токоведущей присадочной проволокой.
11
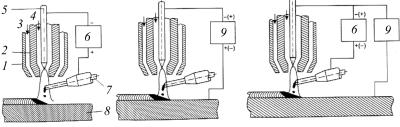
а |
б |
в |
Рис. 3. Схемы плазменной наплавки с присадкой одной проволоки:
а– плазменной струей с токоведущей присадочной проволокой;
б– плазменной дугой с нейтральной присадочной проволокой; в – двойной дугой; 1 – защитное сопло; 2 – плазмообразующее
сопло; 3 – защитный газ; 4 – плазмообразующий газ; 5 – электрод; 6 – источник питания косвенной дуги; 7 – проволока; 8 – изделие; 9 – источник питания дуги прямого действия
Наплавка плазменной струей с токоведущей присадоч-
ной проволокой. Наплавку выполняют постоянным током прямой полярности (рис. 3, а). Дуга горит между вольфрамовым электродом-катодом и присадочной проволокой, подаваемой сбоку под прямым углом к оси плазмотрона
Между катодом и соплом плазмотрона постоянно горит также слаботочная (15–25 А) дежурная дуга, которая поляризует промежуток электрод–проволока и тем самым обеспечивает надежное возбуждение и устойчивое горение рабочей дуги. Вследствие магнитного дутья струя плазмы, генерируемая дугой элек- трод–присадочная проволока, отклоняется от оси плазмотрона по ходу подачи проволоки. Для компенсации этого отклонения плазмотрон устанавливают под углом 50–60° к поверхности изделия так, чтобы струя плазмы была направлена на сварочную ванну примерно под прямым углом к наплавляемой поверхности. Основной металл нагревается за счет теплового воздействия струи плазмы и теплоты переносимого каплями присадочного металла. Эффективная тепловая мощность такого источника на-
12

грева зависит не только от силы тока дуги электрод–проволока, но и от расстояния между проволокой и поверхностью основного металла (рис. 4). Сохраняя силу тока и, следовательно, скорость плавления присадочной проволоки неизменными за счет расстояния между проволокой и поверхностью основного металла, можно в довольно широких пределах изменять мощность, расходуемую на нагрев основного металла.
а |
б |
Рис. 4. Изменение эффективности тепловой мощности q плазменной струи (а) и плазменной струи с присадочным материалом (б)
в зависимости от силы тока Iпр и расстояния от проволоки до изделия h. Присадочная проволока 10Х18Н10Т, диаметр 1,6 мм
Благодаря этому при наплавке плазменной струей можно регулировать тепловые и диффузионные процессы на границе сплавления, определяющие глубину проплавления основного металла и его содержание в наплавленном слое, протяженность, состав и свойства зоны сплавления, а также другие характеристики наплавленных слоев.
Так как энергия плазменной струи передается основному металлу не непосредственно, а через слой жидкого присадочного металла, то наплавку плазменной струей с токоведущей проволокой можно рассматривать как своеобразную заливку поверхности изделия перегретым присадочным металлом.
Ю.Л. Красулин и М.Х. Шоршоров получили следующую формулу для определения глубины проплавления основного металла:
13

H = 2 |
аtk |
T |
|
||
ln |
в |
|
, |
||
|
|||||
|
|
Tc |
|
где H – глубина проплавления основного металла, см; а – коэффициент температуропроводности основного металла, см2/с; tk – длительность контактирования жидкой и твердой фаз, т.е. время пребывания наплавляемого металла в жидком состоянии на поверхности раздела, с; Tв – средняя температура жидкого металла (сварочной ванны), °С; Tс – температура солидуса основного металла, °С.
Из этой формулы следует, что для получения малой глубины проплавления необходимо уменьшать перегрев металла сварочной ванны и длительность его контактирования с твердым основным металлом (при этом подразумевается отсутствие иных источников теплоты, кроме перегретого присадочного металла).
При наплавке плазменной струей металлов и сплавов более легкоплавких, чем основной металл, последний практически не расплавляется, а при наплавке материалов с близкими теплофизическими свойствами его проплавление незначительно, при этом обеспечивается высокая прочность соединения наплавленного и основного металлов. Усталостная прочность биметаллических деталей, наплавленных этим способом, значительно выше, чем при дуговой наплавке, что связано с отсутствием или меньшей толщиной хрупких кристаллизационных и диффузионных прослоек в зоне сплавления.
На качество наплавки плазменной струей сильное влияние оказывает подготовка поверхности изделия и присадочной проволоки под наплавку. Перед наплавкой проволоку обычно подвергают химической очистке (травлению), а поверхность обрабатывают и обезжиривают.
Рекомендуемые режимы: ток порядка 150–210А, расход плазмообразующего газа – 2,5–3 л/мин, защитного – 16–20 л/мин;
14
оптимальное расстояние от торца плазмотрона до проволоки равно 5–8 мм; скорость наплавки составляет 3–12 м/ч.
Наплавка плазменной струей нашла практическое применение в судовом машиностроении для нанесения антифрикционных и коррозионно-стойких сплавов.
Наплавка плазменной дугой с нейтральной присадочной проволокой (рис. 3, б). С точки зрения нагрева основного металла плазменная дуга является более эффективным и более локальным тепловым источником, чем плазменная струя. При наплавке плазменной дугой эффективный КПД нагрева основного металла составляет 50–75 %, а при использовании плазменной струи КПД – 20–45 %. При помощи плазменной дуги можно наплавлять массивные изделия и выполнять прецизионную наплавку весьма мелких деталей, что практически не осуществимо с помощью плазменной струи. Кроме того, плазменная дуга обратной полярности благодаря эффекту катодной очистки дает возможность использовать для наплавки сплавы, легированные алюминием, титаном и другими элементами, образующими трудновосстанавливаемые тугоплавкие оксиды, а также наплавлять детали из алюминиевых сплавов. То обстоятельство, что присадочная проволока электрически нейтральна, снижает интенсивность ее плавления, но в ряде случаев дает некоторые технологические и металлургические преимущества: благодаря меньшему перегреву капель уменьшается разбрызгивание при наплавке порошковой проволокой, предупреждается чрезмерное растворение карбидных зерен при наплавке композиционных сплавов, снижается угар легко испаряющихся легирующих элементов и т.д. При использовании этого способа плавление присадочного материала происходит за счет теплоты, получаемой от столба дуги путем конвективного и лучистого теплообмена. Следовательно, присадочная проволока может плавиться на различном расстоянии от оси дуги, начиная от точки ввода ее в столб дуги и кончая точкой выхода из него. В первом случае скорость плавления проволоки минимальна, во втором – максимальна для данного режима горения дуги.
15
При наплавке плазменной дугой обратной полярности действует иной, чем при традиционных способах наплавки, механизм сплавления основного и присадочного металлов. Под действием дуги обратной полярности впереди фронта сварочной ванны возникает «зона запотевания», представляющая собой частично оплавленный хорошо смачиваемый участок поверхности основного металла. Небольшая часть наплавляемого металла растекается по этой зоне и образует тонкую (около 10 мкм) пленку, на которую затем натекает остальной присадочный металл. Основной металл при этом практически не расплавляется. Доля его в наплавленном слое составляет всего 0,1 %. Характерные детали, наплавляемые этим способом, – клапаны и седла клапанов двигателей внутреннего сгорания, детали трубопроводной арматуры для воды, пара и газа, ножи для резки металла, прокатные валки, штампы и др.
Наплавка двойной плазменной дугой с токоведущей при-
садочной проволокой. Схема процесса приведена на рис. 3, в. Его отличительной особенностью является наличие двух дуг прямой или обратной полярности, питаемых, как правило, от автономных источников. Одна из них горит между электродом плазмотрона и изделием, другая – между электродом и присадочной проволокой. Плавление присадочного материала происходит за счет теплоты, получаемой им путем теплообмена с плазмой столба дуги электрод–изделие, и теплоты, выделяющейся в активном пятне дуги электрод–проволока. Интенсивность плавления зависит от силы тока обеих дуг, полярности, диаметра и места плавления присадочной проволоки и некоторых других факторов. По производительности этот способ значительно превосходит наплавку плазменной дугой с нейтральной присадкой, обеспечивая при этом во многих случаях меньшее проплавление основного металла. Практическое применение находит наплавка двойной плазменной дугой обратной полярности. Режимы наплавки: ток дуги (электрод–изделие, электрод–проволока) составляет 100–220 А; скорость наплавки в зависимости от размеров изделия и размаха
16
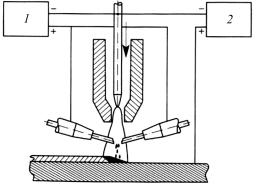
колебаний плазмотрона составляет 2–10 м/ч; расход плазмообразующего газа – 2–3,5 л/мин, защитного – 15–20 л/мин. Наплавляемые изделия – преимущественно детали судового машиностроения, в частности поршни диаметром 60–160 мм; восстановление поршней двигателей внутреннего сгорания и других деталей из алюминиевых сплавов.
Наплавка комбинированной плазменной дугой с присад-
кой двух проволок. Благодаря применению двух присадочных проволок (рис. 5), подаваемых в столб плазменной дуги прямого действия навстречу друг другу, компенсируется их магнитное дутье и повышается производительность наплавки до 30 кг/ч и более. Зону наплавки защищают от воздуха насадки довольно больших размеров (230×120 мм). Защитный газ – аргон или смесь аргона с водородом; плазмообразующий газ – аргон или аргоно-гелиевая смесь.
Рис. 5. Схема плазменнойнаплавки сприсадкой двух проволок: 1 – источник питаниядугиэлектрод–проволока; 2 – источникпитаниядугиэлектрод–изделие
Мундштуки для подачи проволоки снабжены керамическими направляющими, что позволяет работать с малым вылетом проволок и обеспечивает точное направление их в столб плазменной дуги. Процесс наплавки стабилен и не чувствителен
17

кколебаниям длины дугового промежутка. Практическое применение, хотя и в небольшом объеме, этот способ нашел в атомном и химическом машиностроении.
Плазменная наплавка горячими проволоками. Характер-
ной особенностью этого способа наплавки является подогрев за счет Джоулевой теплоты присадочных проволок, подключенных
кавтономному источнику питания (рис. 6). Две присадочные проволоки, обычно диаметром 1,6 или 2,4 мм, подаются с постоянной скоростью в сварочную ванну, создаваемую мощной плазменной дугой прямого действия. Проволоки расположены V-образно под углом 30° друг к другу и включены последовательно через сварочную ванну в цепь источника переменного тока с жесткой внешней характеристикой. Ток, проходящий через проволоки, создает магнитное поле, которое стремится отклонить плазменную дугу. При последовательном включении и V-образном расположении проволок их магнитные поля в основном компенсируют друг друга. Это наряду с применением для нагрева проволок переменного тока позволяет практически полностью устранить влияние магнитного дутья на дугу и обеспечить ее пространственную стабилизацию.
Рис. 6. Схема горячей наплавки горячими проволоками: 1 – источник постоянного тока для питания плазменной дуги; 2 – источник переменного тока для подогрева проволок; 3 – присадочные проволоки
18
Силу тока, скорость подачи проволок и расстояние от токоподводящих мундштуков до поверхности сварочной ванны, т.е. длину нагреваемых участков проволок, выбирают такими, чтобы проволоки нагревались проходящим через них током почти до температуры плавления. В результате резко повышается производительность наплавки. Проволоки плавятся в сварочной ванне без образования дуги. Характерная особенность плазменной наплавки горячими проволоками – малое тепловложение в основной металл и, следовательно, небольшая доля основного металла в наплавленном и минимальная зона термического влияния.
Типичные режимы: ток дуги порядка 500–600 А, ток в проволоках – 400–550 А; плазмообразующий газ – гелиево-аргоновая смесь, содержащая 50–75 % гелия, расход 22–40 л/мин; защитный газ (Ar) – 30–40 л/мин.
Наплавляемые детали – фланцы крупных сосудов высокого давления, трубные доски теплообменников, детали химических аппаратов, элементы корпусов реакторов и оборудования первого контура атомных электростанций.
Плазменная наплавка плавящимся электродом. Способ плазменной наплавки (сварки) плавящимся электродом от обычной дуговой наплавки (сварки) отличается тем, что конец проволочного электрода и дуга, горящая между проволокой и изделием, окружены аксиальным потоком плазмы, создаваемым плазменной дугой прямого или косвенного действия. Благодаря этому значительно возрастает скорость плавления электродной проволоки, повышается стабильность дуги, улучшаются характер переноса электродного металла (практически полностью устраняется разбрызгивание) и формирование сварных швов (наплавленных валиков). В зависимости от способа генерирования плазмы рассматриваемый процесс имеет несколько разновидностей (рис. 7). Процесс наплавки по схеме (рис. 7, а) начинают с возбуждения плазменной дуги между расположенным эксцентрично относительно сопла неплавящимся электродом и изделием. Дуга между электродной проволокой, подаваемой по оси
19
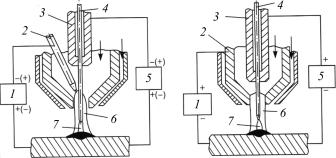
горелки, и изделием возбуждается спонтанно, без короткого замыкания дугового промежутка и горит стабильно при изменении скорости подачи проволоки в очень широком диапазоне. Сварку и наплавку по этой схеме можно вести как на прямой, так и на обратной полярности. При обратной полярности резко возрастает тепловая нагрузка на неплавящийся электрод, что ограничивает силу тока плазменной дуги. Для повышения допустимой силы тока плазменной дуги используют в качестве неплавящегося электрода сопло (рис. 7, б).
а |
б |
Рис. 7. Схема плазменнойнаплавки плавящимсяэлектродом: а– с плавящимсяэлектродом плазменнойдуги; б – стоковедущим соплом; 1 – источник питания плазменнойдуги; 2 – вольфрамовый иливодоохлаждаемый медныйэлектрод; 3 – мундштук;
4 – электродная проволока; 5 – источникпитаниядуги плавящегося электрода; 6 – плазменнаядуга; 7 – дуга плавящегося электрода
При этом упрощается конструкция плазмотрона, уменьшаются его габариты. Процесс начинают с возбуждения путем короткого замыкания дуги плавящегося электрода, после чего в течение 0,1 с самопроизвольно возникает стабильная плазменная дуга между соплом и изделием. Под воздействием магнитного поля, существующего вокруг электродной проволоки, активное пятно дуги располагается на стенке канала сопла. В за-
20