
книги / Основы экспериментальной механики разрушения
..pdf«губ среза», занимают часть поверх ности разрушения, соизмеримую с зо ной прямого излома. Губы среза мо гут быть расположены как по одну сторону от плоскости прямого излома (показано штриховой линией), так и по разные.
Наблюдаемая картина обусловлена тем, что при данных толщинах t в
центральной части образца реализуется объемное напряженное состояние и создаются условия, близкие к плоской деформации,, а по краям сохраняется плоское напряженное состояние. Тре щина нормального отрыва распространяется на некоторое рас стояние по центральной части сечения, образуя своеобразный туннель в образце. На диаграмме нагрузка-смещение при этом часто появляется скачок, обусловленный приостановкой роста пли даже уменьшением нагрузки. Дальнейшего продвижения «туннельной» трещины не происходит из-за тормозящего влия ния краевых зон (губ среза), разрушение которых происходит косым изломом при более высоких нагрузках. На диаграмме нагрузка-смещение начинает наблюдаться рост нагрузки и ис кривление самой диаграммы вследствие изменения податливос ти образца. Схематически «забегание вперед» фронта трещины по центральной части сечения показано на рис. 5.3. Направле ние роста трещины на рисунке показано стрелкой.
С увеличением толщины образца t в пределах области В доля кристаллического излома увеличивается, а влияние и от носительная доля губ среза уменьшаются. Это приводит к по
степенному падению измеряемых |
значений трещиностойкости |
||
Кс Для ряда сталей низкой и средней |
прочности некоторых |
||
алюминиевых сплавов это падение описывается |
эмпирической |
||
зависимостью |
|
|
|
№ .Y = ! + U |
^ î j V |
* . |
(5.1) |
справедливой в области В при условии f^(K id o t)2.
При достаточно большой толщине t*, когда влияние губ сре за становится пренебрежимо малым, разрушение практически всего сечения образца происходит прямым изломом путем рас пространения трещины нормального отрыва в условиях плоской деформации. Трещииостойкость Кс в этот момент достигает сво его минимального значения, равного Къ, и перестает зависеть от толщины образца (область С на рис. 5.1). Таким образом, вязкость разрушения Кхс является константой материала, в то время как Кс из-за зависимости от t следует сопровождать указанием толщины, к которой Кс относится.
Условия, когда толщина образца обеспечивает измерение Kic (условия плоской деформации), принято записывать в виде
m ( K iJ < h ) 2, |
(5.2) |
•где р — эмпирический коэффициент, равный, как установлено, ‘2,5 для малоуглеродистых и низколегированных сталей, алюми ниевых и титановых сплавов. Для аустенитных сталей (5 = 5, а
.для такого хрупкого материала, как чугун, — (5= 0,6. Значение
.(3=2,5 является наиболее употребительным в эксперименталь ной механике разрушения.
Практическое использование формулы (5.1) затруднено тем, что величина Kic заранее неизвестна. Поэтому приходится про водить измерения при некотором начальном значении t. Если результат измерений не удовлетворяет (5.2), то измерение по вторяют с увеличенной толщиной образца и т. д. Предвари тельный выбор t может быть произведен в соответствии с табл. 5.2 по известным пределу текучести и модулю упругости.
|
|
Т а б л и ц а |
5.2 |
|
|
|
ВЫБОР ПРЕДВАРИТЕЛЬНОЙ ТОЛЩИНЫ |
||
|
|
ОБРАЗЦА ПРИ ИСПЫТАНИЯХ |
|
|
|
|
НА ВЯЗКОСТЬ РАЗРУШЕНИЯ |
|
|
|
|
|
(°т/Е) *0-2 |
/, ММ |
|
|
|
0,50 и менее |
100 |
|
|
|
0,50—0,57 |
75 |
|
|
|
0,57-0,62 |
63 |
|
|
|
0,62—0,65 |
50 |
Рис. 5.4. Зависимость |
тре- |
0,65-0,71 |
38 |
|
щнностойкостн |
металличе |
0,71—0,80 |
25 |
|
ского образца |
от радиуса |
0,80—0,95 |
12 |
|
кривизны в основании |
на |
0,95 и более |
6 |
чального надреза
Как уже отмечалось, при испытаниях на трещиностойкость используются образцы с начальной трещиной. Применение об разцов с узкими надрезами, сделанными искусственно с по мощью режущего инструмента, приводит к недопустимо боль шим погрешностям в измерениях. В качестве иллюстрации на рис. 5.4 построена зависимость Кс от радиуса р в основании на чального надреза, полученная в серии специальных испытаний. Можно видеть резкое падение величины Кс с уменьшением р. -Лишь при чрезвычайно острых надрезах (при р порядка нес кольких сотых или даже тысячных долей мм) Кс принимает по стоянное значение.
Практически начальная трещина создается путем усталост ного нагружения образца с инициирующим надрезом в режиме циклического растяжения. При этом максимальное напряже ние цикла не должно быть большим, чтобы не повлиять на ре
зультаты последующих измерений. Рекомендуется на основании •экспериментальных данных соблюдать условие Отах<0,5от.
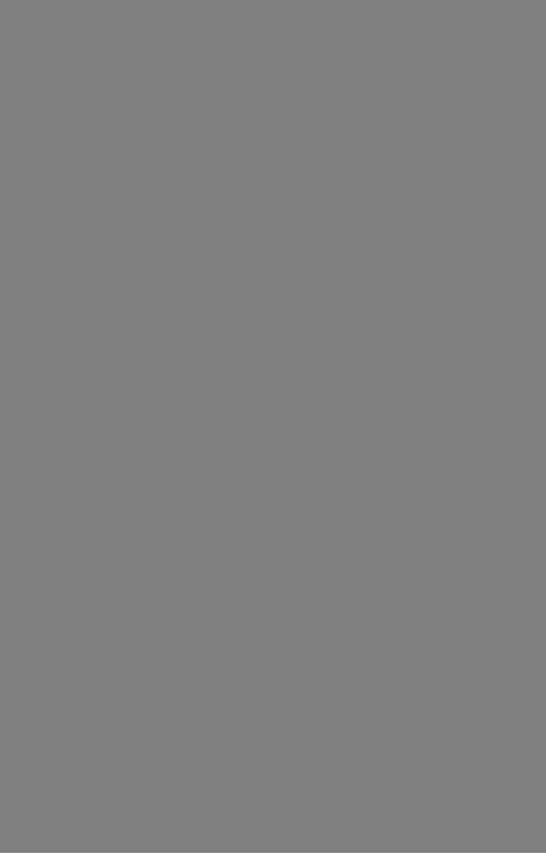
Рис. 5.6. Типы диаграмм нагрузка—смещение
Разрушение образца в этом случае носит смешанный характер частично прямым, частично косым изломом. Момент образова ния «туннельной» трещины обычно сопровождается характер ным треском и легко выявляется в процессе испытания.
На диаграммах типа III максимальная нагрузка, соответст вующая моменту разрушения образца, не попадает в интервал, ограниченный 5%-ной секущей, но максимальное смещение от носительно невелико.
Диаграммы типа IV относятся к образцам, разрушение кото рых происходит на ниспадающей ветви графика при нагрузках, меньших максимальной Рс и больших смещениях.
Классификация диаграмм нагрузка — смещение с помощью 5%-ной секущей, имеющая полуэмпирическое обоснование, соз дает определенные удобства при определении расчетной нагруз ки P Q, п о которой вычисляется в соответствии с формулой типа (2.46) условное значение критического коэффициента интенсив ности напряжений K Q.
Для диаграмм типа I расчетная нагрузка принимается рав ной разрушающей PQ= P C. Для диаграмм типа II в качестве PQ используется максимальная нагрузка в области скачка. На диаграммах типа III и IV PQ определяется точкой пересечения 5%-ной секущей с экспериментальной кривой. Если же удается зафиксировать момент начала докритического роста трещины (точка О на диаграмме типа IV), то принимают PQ— P0.
Вычисленное по найденной расчетной нагрузке P Q значение K Q принимается равным Kic при выполнении условий коррект ности измерений. Эти условия обеспечивают применимость кон цепции квазихрупкого разрушения и обычно используются в ви де трех независимых пар соотношений (проверка производится по любой паре) :
1) Рс/Р<з<\Л, I и *>р(К<г/от)2;
ill
2) |
P C/ P Q^ 1,1, |
фтах<1,5%; |
3) |
PC/PQ^ 1,1, |
(5.3) |
Vc/VQ^ 1,2. |
Здесь p — коэффициент, входящий в формулу (5.2), <pmax — на ибольшее относительное утонение образца в месте разрушения.
Если хотя бы одно из условий выбранной пары не выполня ется, то при необходимости определения вязкости разрушения
К\с следует увеличить толщину образца, приняв ее, |
например, |
|
равной P(/C(?/G T ) 2, и |
повторить измерения. |
экспери |
В случае, когда |
определять Ки в дополнительном |
менте не требуется, находят трещиностойкость Кс, соответствую щую материалу данной толщины. При этом вместо P Q за рас четную нагрузку принимается Pc (для диаграммы типа IV—Ро) и вводится поправка Ирвина на пластичность гр. Расчет ведет ся методом последовательных приближений. Вначале вычисля ется величина
К'с = К (Р с, h ) .
где /0 — начальная длина трещины.
Затем находится условная длина трещины l' = l0 + (K'c)V
Далее вычисляется второе приближение
к- « р , . 'О.
по которому находится I", и т. д. Расчет прекращается, когда разность между результатами двух последовательных вычис лений трещиностойкости окажется не более 2%. При этом для обеспечения приемлемой точности определения Кс необходимо проследить, чтобы длина пластической зоны гр не была больше 0,2 /о. Кроме того, требуется проверка выполнения общего ус ловия применимости понятий линейной механики разрушения
ос^0,8стт, |
(5-4) |
где ас — номинальное напряжение по сечению-нетто при нагруз ке Рс-
Еще одним обстоятельством, усложняющим определение Кс, является необходимость измерения докритического подрастания трещины, которое может быть значительным при малой толщи не образца. В расчетах должна использоваться длина трещины в критической точке, найденная с учетом увеличения исходной длины на участке докритического роста. При измерении Kic данная коррекция не вводится из-за ее малости, обусловленной большой толщиной образца.
При известных Кхс и Кс можно найти критические значения других характеристик трещиностойкости G, Ô и J простым пере счетом по приводившимся ранее формулам.
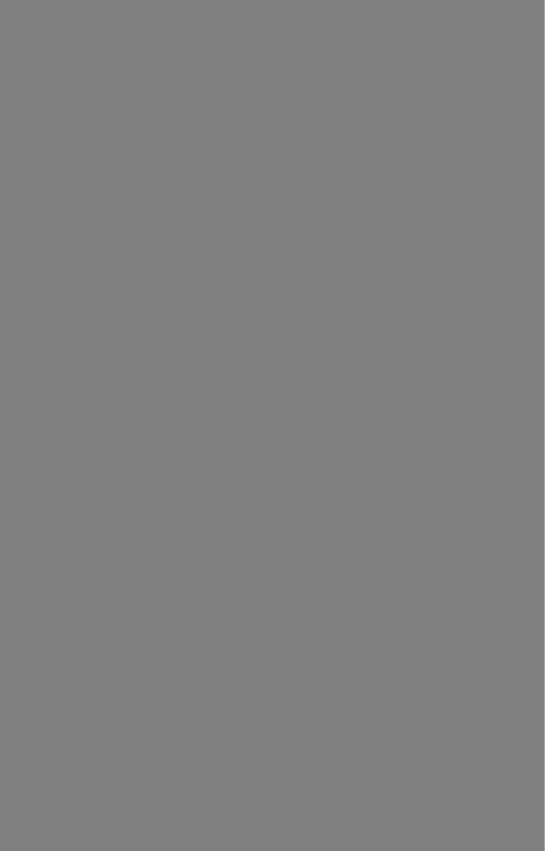
жения с увеличением продолжительности его действия. Времен ные эффекты являются также причиной наблюдаемого в экспе рименте медленного роста трещин при постоянной или даже убывающей нагрузке. Медленный рост предшествует достиже нию критического состояния, т. е. началу быстрого роста трещи ны в динамическом режиме.
Поскольку временные эффекты, как установлено, сильно за висят от уровня напряжения (часто по экспоненциальному за кону), то можно предположить, что они сконцентрированы в не которой окрестности вершины трещины, вне которой полимер деформируется упруго. Если допустить далее, что размер ука занной окрестности мал по сравнению с длиной трещины и ха рактерным размером тела и что рост трещины происходит до статочно медленно, то можно за характеристику трещиностойкости принять критическое значение коэффициента интенсив ности напряжений в функции единственного аргумента — скоро сти роста трещины. Сделанные предположения позволяют пред ставить силовой критерий (2.45) в применении к росту трещин в полимерных материалах в следующей форме:
K = Kc(V), |
i= dlldt, |
(5.5) |
где К с ( ' 1 ) является материальной |
функцией, |
определяемой эк |
спериментально в опытах с различными скоростями деформиро вания. Для ряда полимерных систем установлена допустимость
степенной аппроксимации функции KC(Q-
В простейших случаях критерий (5.5) можно разрешить от носительно dljdt:
dl/df=f(K). (5.6)
Сравнение последнего выражения с (4.2) и (4.3) демонстри рует формальную эквивалентность способов описания роста тре щин в полимерах и роста усталостных трещин, хотя лежащие в их основе физические процессы различны.
Если рассматривать полимер как линейно вязкоупругую сре ду, что часто делается, то можно непосредственно ввести фактор времени в соотношения механики разрушения, заменив соглас но принципу Вальтерра упругие постоянные на их операторные эквиваленты. Указанный принцип справедлив в применении к монотонно растущим трещинам.
Рассмотрим в качестве иллюстрации данного подхода вязкоупругий аналог трещины Гриффитса на основе энергетического критерия (3.30).
Поскольку для трещины Гриффитса /<>=1 из-за отсутствия пластической зоны в вершине, то критерий (3.30) упрощается:
ô
о
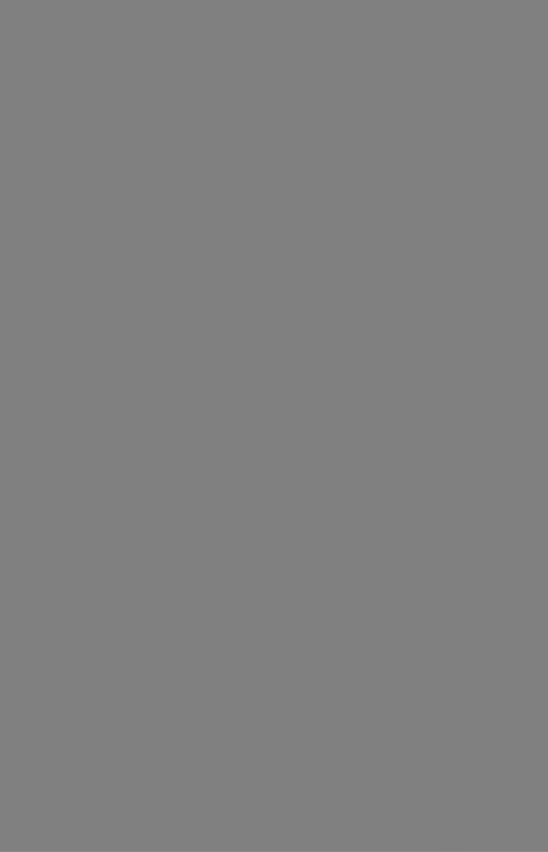
правильнее следует называть полукристаллическим, поскольку полная кристаллизация полимерной среды принципиально не достижима из-за наличия неупорядоченных участков макромо лекул, их концов и дефектов иного происхождения. Примерами аморфных термопластов являются органическое стекло (поли метилметакрилат — ПММА), полистирол (ПС), поликарбонат (ПК), поливинилхлорид (ПВХ). К типичным представителям полукристаллических термопластов можно отнести полиэтилен (ПЭ), полипропилен (ПП), лавсан (полиэтилентерефталат — ПЭТФ).
Во вторую группу общей классификации входят каучуки и каучукоподобные материалы природного и искусственного про исхождения, способные к большим упругим деформациям. Осно ву их структурного строения составляют, трехмерные сетки с от носительно редкими точками сшивки. Материалы этой группы здесь не рассматриваются.
Третью группу составляют жесткие высокосшитые полимер ные системы, температура плавления которых выше температу ры термической деструкции, так что они разрушаются при на гревании без существенного размягчения. Представителями дан ной группы являются эпоксидная и полиэфирная смолы, полу чившие широкое распространение в качестве матричных мате риалов в композитах.
Приведенные сведения о структурном строении и классифи кации полимеров предельно схематичны. Структурное строение реальных полимерных материалов отличается сложной иерар хией надмолекулярных образований *.
В зоне высоких напряжений перед вершиной трещины в по лимерах могут развиваться пластические деформации по ме ханизмам, лишь в деталях отличающимся от механизмов плас тического течения металлов. Полосы сдвига, например, особен но часто наблюдаются в кристаллических термопластах. Однако в большинстве случаев определяющую роль играет специфичес кий механизм деформирования, получивший название крейзинга (крейзообразования).
Крезы (трещины серебра, волосяные трещины) образуются под действием растягивающих напряжений перед вершиной трещины. Вначале из-за микронеоднородности поля напряжений возникают микропустоты (рис. 5.7), перемычки материала меж-
.ду которыми получают возможность вытягиваться в микрошей ке, образуя фибриллы (тяжи). Процесс вытяжки фибрилл ста билизируется эффектами ориентационного упрочнения. Сформи ровавшееся трещиноподобное образование (крейз) обладает ус тойчивостью и способностью выдерживать значительные на грузки. Рост основной трещины происходит путем последова тельного разрыва скрепляющих поверхности крейза фибрилл.
* См.: Б а р т е н е в Г. М., 3 е л е и е в 10. В. Физика и механика полимеров.
— М.: Высшая школа, 1983. — 391 с.
На рис. 5.8 представлена получившая распространение мо дель образования крейзов, называемая моделью «менисковой неустойчивости» из-за своей формальной аналогий с явлением потери устойчивости в тонком слое жидкости при разведении двух жестких плоскостей.
На рис. 5.9 приведены результаты измерений профиля кон цевой зоны трещины в ПММА. Продольный размер области крейзинга гр во много раз превосходит поперечный ôi (масшта
Рис. 5.7. Начальная стадия образования крейзов
и2, мкм
-20 0 |
20 |
40 |
|
Рис. 5.8. Образование крейзов |
|
|
|
Xj, мкм |
|
по модели «менисковой |
неус |
б е . 5.9. Профиль |
концевой |
зоны |
трещины |
тойчивости» |
|
тончивости» |
|
||||
в ПММА. Точки — эксперимент, |
сплош |
|
|
||
ная линия — расчет |
|
|
|
||
бы по осям Xi и х2 различны), т. е. возникает ситуация, |
пол |
||||
ностью согласующаяся |
с моделью |
Леонова—Панасюка—Даг- |
дейла. Хорошее согласие этой модели с экспериментом подтвер ждается расчетом, как следует из выполненного на рис. 5.9 построения. Некоторое отклонение экспериментальных точек от расчетного профиля на свободных поверхностях трещин обус ловлено влиянием слоя, образованного разорванными концами фибрилл. Расчет проводился по формуле, являющейся более удобной для данного случая модификацией формулы (3.13)
где TJ *■ У i —Xi/Гр .
120