
книги / Основы сварочных работ при сооружении магистральных трубопроводов
..pdf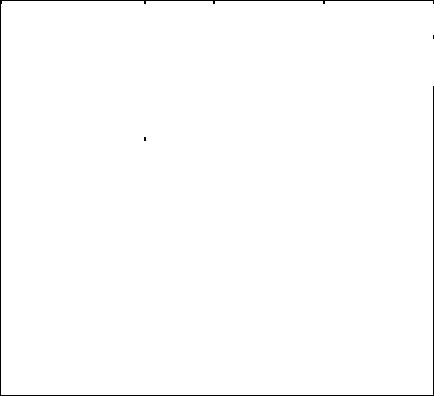
Окончание табл. 3
Корень шва |
|
«Горячий» |
Заполняющие |
Облицовочный |
|
проход |
слои |
слой |
|
|
|
|||
РДС электродом с ос- |
|
– |
Механизированная |
сварка порошко- |
новным покрытием |
|
|
вой самозащитной проволокой (типа |
|
|
|
|
Innershield) |
|
|
|
|
|
|
РДС электродом с целлюлозным |
Механизированная |
сварка порошко- |
||
покрытием |
|
|
вой самозащитной проволокой (типа |
|
|
|
|
Innershield) |
|
|
|
|
|
|
РДС |
|
– |
Автоматическая сварка в среде СО2 |
|
|
||||
РДС |
|
– |
Автоматическая сварка порошковой |
|
|
|
|
проволокой с принудительным фор- |
|
|
|
|
мированием шва |
|
Механизированная |
|
– |
РДС электродом с основным покры- |
|
сварка в среде СО2 ме- |
|
|
тием |
|
тодом STT |
|
|
|
|
Механизированная |
|
– |
Механизированная |
сварка порошко- |
сварка в среде СО2 ме- |
|
|
вой самозащитной проволокой (типа |
|
тодом STT |
|
|
Innershield) |
|
Механизированная |
|
– |
Автоматическая односторонняя свар- |
|
сварка в среде СО2 ме- |
|
|
ка порошковой проволокой в среде |
|
тодом STT |
|
|
СО2 |
|
Автоматическая сварка CRC-Evans AW – двухсторонняя сварка тонкой электродной проволокой сплошного сечения в среде СО2
7.СВАРОЧНЫЕ МАТЕРИАЛЫ
7.1.Назначение сварочных материалов
При дуговых способах сварки неразъемное сварное соединение получается путем расплавления кромок свариваемых деталей либо кромок и дополнительного присадочного металла с образованием общей сварочной ванны и последующей кристаллизацией этой ванны после прекращения действия источника нагрева. Металл образо-
41
вавшегося сварного шва должен обладать необходимыми свойствами − отсутствием дефектов, равнопрочностью с основным металлом и другими свойствами, определяемыми условиями его работы. Этого можно достичь легированием сварочной ванны с помощью присадочного металла, покрытия, флюса и применением специальных методов защиты зоны сварки (защитные газы, вакуум).
Присадочный металл и другие вещества, используемые при сварке плавлением с целью получения неразъемного соединения, удовлетворяющего определенным требованиям, называются сварочными материалами. К сварочным материалам относят сварочную проволоку, присадочные прутки, порошковую проволоку, плавящиеся покрытые электроды, неплавящиеся электроды, флюсы, защитные газы и металлические порошки.
Дополнительный металл в виде сварочной проволоки, прутков или стержней обычно требуется для получения шва с необходимыми геометрическими размерами, так как в большинстве случаев расплавление только кромок основного металла не обеспечивает выпуклости шва, заполнения зазора и разделки кромок (если она есть). Если дополнительный металл в процессе сварки включен в сварочную цепь, он называется электродным, а если не включен − приса-
дочным.
Дополнительный металл в виде проволоки и электродных стержней и дополнительные средства в виде электродного покрытия, флюса, защитного газа, сердечника порошковой проволоки и др. обеспечивают в комплексе газовую, шлаковую или комбинированную газошлаковую защиту зоны сварки окружающего воздуха, стабилизацию горения дуги, раскисление и легирование металла шва, очистку его от вредных примесей и газов, правильное формирование шва, предотвращают образование в нем сварочных дефектов.
7.2. Сварочная проволока и прутки
Наиболее часто в качестве добавочного металла используют сварочную проволоку. При механизированной сварке плавлением ее
42
используют в виде непрерывного плавящегося электрода, при ручной сварке − в виде электродных стержней и присадочных прутков.
Состав и технические требования к проволоке и пруткам, предназначенным для сварки плавлением, регламентируются следующими государственными стандартами:
ГОСТ 2246–70. Проволока стальная сварочная. ГОСТ 10543–82. Проволока стальная наплавочная.
ГОСТ 7871–75. Проволока сварочная из алюминия и алюминиевых сплавов.
ГОСТ 16130–85. Проволока и прутки из меди и сплавов на медной основе сварочные.
Другие виды сварочной проволоки и прутков, применяемые при сварке и наплавке, выпускаются по специальным техническим условиям или по стандартам, не предусматривающим их специальное назначение для сварки.
Ниже приведены краткие сведения о сварочной проволоке и прутках из вышеперечисленных ГОСТов.
Стальная сварочная проволока (ГОСТ 2246–70). Стандарт рас-
пространяется на холоднотянутую гладкую проволоку из низкоуглеродистой нелегированной стали, поставляемую в мотках или бухтах массой до 80 кг.
Стандартом предусмотрено 77 марок сварочной проволоки разного химического состава; выпускается шесть марок низкоуглеродистой проволоки (Св-08, Св-08А, Св-08АА, СВ-08ГА, Св-10ГА
иСВ-10Г2), 30 марок легированной проволоки (Св-08ГС, Св-12ГС, Св-08Г2С, Св-10ГН, Св-08ГСМТ, Св-15ГСТЮЦА, Св-20ГСТЮА
идр.), 41 марка высоколегированной проволоки (Св-12Х11НМФ,
Св-12Х13, Св-10Х17Т и др.).
Обозначение марок проволоки состоит из сочетания букв и цифр. Буквы «Св» обозначают сварочную проволоку, следующие за ними первые две цифры показывают содержание углерода в сотых
долях процента, а цифры после букв − содержание данного элемента в процентах. Если после буквы нет цифры, значит данного элемента содержится менее 1 %. В остальном маркировка сварочной проволо-
43
ки подобна маркировке сталей. Наличие на конце марки букв «А» или «АА» свидетельствует, что эта проволока изготовлена из более высококачественной стали и содержание в ней вредных примесей серы и фосфора уменьшено.
Условные обозначения легирующих элементов следующие: С − кремний; Н − никель; М − молибден; Т − титан; Ю − алюминий;
Ц− цирконий; Г − марганец; Х − хром; Ф − ванадий; Р − бор;
Б− ниобий; В − вольфрам; Д − медь.
Влегированной стали легирующих элементов содержится от
2,5 до 10 %, в высоколегированной − более 10 %.
По требованию потребителя сварочную проволоку изготовляют из стали, выплавленной электрошлаковым (Ш), или вакуумно-дуго- вым (ВД) переплавом, или в вакуумно-индукционных печах (ВИ).
Взависимости от назначения стальную сварочную проволоку подразделяют на проволоку для сварки (наплавки) и проволоку для изготовления электродов (Э). Это обусловлено более жесткими требованиями к проволоке для изготовления электродов.
По виду поверхности низкоуглеродистую и легированную проволоку подразделяют на неомедненную и омедненную (О). Омеднение делается для улучшения контакта при подводе тока к движущейся проволоке в сварочном автомате или полуавтомате и для уменьшения износа мундштука и тянущих роликов механизма подачи проволоки.
Вусловном обозначении сварочной проволоки указывают диаметр и марку проволоки, приведенные выше индексы, характеризующие способ выплавки стали, назначение и вид поверхности проволоки, а также стандарт.
Примеры условного обозначения проволоки:
1. Проволока сварочная диаметром 3 мм, марка Св-08А, предназначенная для сварки (наплавки), с неомедненной поверхностью – проволока 3 Св-08А ГОСТ 2246–70.
2. Проволока сварочная диаметром 2,5 мм, марка Св-08ХГСМФА, предназначенная для изготовления электродов, из стали, выплавлен-
44
ной в вакуумно-индукционной печи, с омедненной поверхностью – проволока 2,5 Св-08ХГСМФА-ВИ-Э-О ГОСТ 2246–70.
Втехнических требованиях ГОСТа приведена таблица химического состава проволок и изложены требования к их размерам.
Проволока выпускается следующих диаметров: 0,3; 0,5; 0,8; 1,0; 1,2; 1,4; 1,6; 2,0; 2,5; 3,0; 4,0; 5,0; 6,0; 8,0; 10,0; 12,0 мм.
Встандарте указаны правила приемки, методы испытаний, требования к упаковке, маркировке, транспортированию и хранению проволоки.
Каждый моток или бухту проволоки снабжают металлической биркой, на которой указано наименование завода-изготовителя, условное обозначение проволоки, номер партии, клеймо технического контроля. Каждая партия проволоки сопровождается сертификатом, содержащим основные технические данные.
Стальная проволока для наплавки (ГОСТ 10543–82). Выпуска-
ется 30 марок наплавочной проволоки, которые разделены на три
группы: углеродистые − 9 марок (Нп-25, Нп-50 и др.); легированные − 11 марок (Нп-40Г, Нп-30ХГСА и др.); высоколегированные −
10 марок (Нп-20Х14, Нп-30Х10Г10Т и др.).
Цифры и буквы, стоящие после индекса Нп (наплавочная), показывают примерный химический состав наплавочной проволоки так же, как и у сварочной проволоки по ГОСТ 2246–70. Отличие заключается лишь в том, что цифра после буквы (содержание легирующего элемента в процентах) не ставится при содержании элемента менее 2 %.
Стальную наплавочную проволоку выпускают следующих диа-
метров: 0,3; 0,5; 0,8; 1,0; 1,2; 1,4; 1,6; 1,8; 2,0; 2,5; 3,0; 4,0; 5,0; 6,0; 6,5; 8,0 мм.
Пример условного обозначения проволоки наплавочной из стали марки 30ХГСА диаметром 3 мм: проволока 3Нп-30ХГСА ГОСТ 10543–82.
Как и в стандарте на сварочную проволоку, в ГОСТ 10543–82 приведены таблица химического состава наплавочных проволок, требования к размерам, правила приемки, испытаний и т.п. Допол-
45
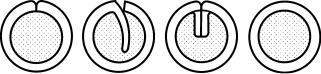
нительно дано справочное примечание, в котором указаны твердость и примерное назначение металла, наплавленного проволоками конкретных марок, например, проволока марки Нп-Г13А предназначена для наплавки железнодорожных крестовин, зубов ковшей экскаваторов и т.п., наплавленный ею металл имеет твердость
220–280 HRC.
Наряду с металлической проволокой сплошного сечения в сварке применяется порошковая проволока, представляющая собой непрерывную трубку (часто сложного внутреннего сечения), заполненную порошкообразным наполнителем − шихтой (рис. 24).
Рис. 24. Виды внутреннего сечения порошковой проволоки
Оболочку порошковой проволоки изготовляют из стальной (чаще низкоуглеродистой) ленты толщиной 0,2–0,5 мм. Наполнитель представляет собой смесь порошков из газо- и шлакообразующих компонентов, а также легирующих компонентов, обеспечивающих защиту зоны сварки и требуемые свойства сварного шва.
Классификация, сортамент и технические требования на порошковую проволоку для сварки углеродистых и низколегированных сталей регламентируются ГОСТ 26271–84.
Стандарт устанавливает изготовление проволоки 15 диаметров. По условиям применения проволока подразделяется на газозащитную (ПГ), применяемую для сварки в углекислом газе и газовых смесях, и самозащитную (ПС) для сварки без дополнительной защиты. По гарантируемому пределу текучести наплавленного металла
сварочная порошковая проволока может быть 9 типов.
В зависимости от содержания углерода, серы и фосфора в наплавленном металле порошковая проволока подразделяется на категории А, В, С.
46
По гарантируемой минимальной ударной вязкости наплавленного металла при определенной температуре испытаний проволока имеет 9 уровней.
В соответствии с допустимыми пространственными положениями сварки и условиями формирования сварного шва проволока подразделяется: для нижнего положения (Н); для нижнего и горизонтального (Г); для нижнего, горизонтального и вертикального (В); для горизонтального с использованием принудительного формирования (ГП); для вертикального с использованием принудительного формирования (ВГ); для всех пространственных положений с использованием принудительного формирования (УП).
С учетом указанной классификации регламентируется следующая буквенно-цифровая структура условного обозначения сварочных порошковых проволок: марка; диаметр (мм); условия применения; тип; категория по химическому составу; уровень по ударной вязкости; допустимое положение сварки; обозначение стандарта. Обозначение марки проволоки должно начинаться индексом ПП (порошковая проволока), после которого через дефис приводится название марки, принятое разработчиком. Например, порошковые проволоки, разработанные в Институте электросварки им. Е.О. Патона НАН Украины, имеют маркировку ПП-АН… с последующим числом. Названия марок проволок, разработанных до введения ГОСТ 26271-84, носят произвольный характер − ПП-2ДСК,
ЭПС-15/2, СП-1, ППВ-5 и т.п.
Пример условного обозначения порошковой проволоки марки ПП-АН3 диаметром 3 мм, самозащитной (ПС), по величине предела текучести металла шва типа 44, по химическому составу наплавленного металла категории А, обеспечивающей ударную вязкость металла шва не ниже 35 Дж/см2 при температуре –20 °С (2), для сварки в нижнем положении (Н) – ПП-АН3 3,0 ПС44-А2Н
ГОСТ 26271–84.
Учитывая возможность возникновения неблагоприятных сани- тарно-гигиенических условий при изготовлении и сварке порошковой проволокой, ГОСТ 26271–84, кроме обычных разделов «Техни-
47
ческие требования», «Правила приемки», «Методы испытаний» и другие, содержит раздел «Требования безопасности и охраны природы».
7.3. Покрытые электроды для ручной дуговой сварки и наплавки
Покрытыми электродами сваривают различные стали, чугуны, многие цветные металлы и сплавы, но основной объем ручной дуговой сварки приходится на стали. В связи с этим общие требования к электродам для сварки и наплавки сталей регламентированы государственными стандартами. Электроды для сварки чугуна и цветных металлов не стандартизованы и выпускаются в соответствии с техническими условиями.
В настоящее время в России действуют четыре ГОСТа на электроды:
ГОСТ 9466–75. Электроды покрытые металлические для ручной дуговой сварки сталей и наплавки. Классификация, размеры и общие технические требования;
ГОСТ 9467–75. Электроды покрытые металлические для ручной дуговой сварки конструкционных и теплоустойчивых сталей. Типы.
ГОСТ 10052–75. Электроды покрытые металлические для ручной дуговой сварки высоколегированных сталей с особыми свойствами. Типы.
ГОСТ 10051–75. Электроды покрытые металлические для ручной дуговой наплавки поверхностных слоев с особыми свойствами. Типы.
7.3.1. Классификация покрытых электродов
По назначению электроды подразделяются:
У − для сварки углеродистых и низколегированных конструкционных сталей с временным сопротивлением разрыву до 60 кгс/мм2;
48
Л − для сварки легированных конструкционных сталей с временным сопротивлением разрыву свыше 60 кгс/мм2;
Т− для сварки легированных теплоустойчивых сталей;
В− для сварки высоколегированных сталей с особыми свойст-
вами;
Н − для наплавки поверхностных слоев с особыми свойствами. Подразделение электродов на типы регламентировано
ГОСТ 9467–75, ГОСТ 10051–75 и ГОСТ 10052–75.
На марки электроды разделяют по техническим условиям и паспортам. Каждому типу электрода могут соответствовать несколько марок.
Электроды подразделяют по толщине покрытия в зависимости от отношения диаметра электрода (D) к диаметру стального стержня (d):
М − с тонким покрытием (D/d ≤ 1,20);
С − со средним покрытием (1,20 < D/d ≤ 1,45); Д − с толстым покрытием (1,45 < D/d ≤ 1,80); Г − с особо толстым покрытием (D/d > 1,80).
В зависимости от требований к точности изготовления электродов, состоянию поверхности покрытия, сплошности выполненного данными электродами металла шва и содержания серы и фосфора в наплавленном металле электроды делятся на группы 1, 2 и 3.
По видам покрытия электроды подразделяют: А − с кислым покрытием; Б − с основным покрытием; Ц − с целлюлозным покрытием; Р − с рутиловым покрытием; П − с покрытием прочих видов. При покрытии смешанного вида используют соответствующее двойное условное обозначение. При наличии в составе покрытия железного порошка в количестве более 20 % к обозначению вида покрытия добавляют букву Ж.
По допустимым пространственным положениям сварки или наплавки электроды подразделяют: 1 − для всех положений; 2 − для всех положений, кроме вертикального сверху вниз; 3 − для нижнего, горизонтального на вертикальной плоскости и вертикального снизу вверх; 4 − для нижнего и верхнего в лодочку.
49
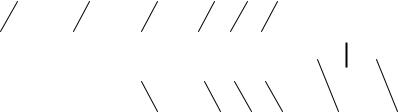
Условное обозначение. Все вышеперечисленные элементы классификации электродов должны быть указаны в условном обозначении. Структура условного обозначения приведена на рис. 25.
1 2 3 4 5 6
|
|
|
|
|
|
|
|
|
|
|
|
|
|
|
|
|
|
|
|
|
|
|
|
|
|
|
|
|
|
|
|
|
|
|
|
|
|
|
|
|
|
|
|
|
|
|
|
|
|
|
|
|
|
|
|
|
|
|
|
|
|
|
|
|
|
|
|
|
|
|
|
, |
|
|
|
|
|
|
|
|
|
|
|
|
|
|
|
|
|
|
|
|
|
|
|
|
|
|
|
|
|
|
|
|
|
|
|
|
|
|
|
|
|
|
|
|
|
|
|
|
|
|
|
|
|
|
|
|
|
|
Е |
|
|
|
|
|
|
|
|
|
|
|
|
|
|
|
|
||
|
|
|
|
|
|
|
|
|
|
|
|
|
|
|
||||||||||
|
|
|
|
|
|
|
|
|
|
|
|
|
|
|
|
|
|
|
|
|
|
|
|
|
7 |
|
|
|
|
8 |
9 |
10 |
11 |
|
12 |
Рис. 25. Структура условного обозначения электродов: 1 − тип; 2 − марка; 3 − диаметр, мм; 4 − назначение электродов; 5 − толщина покрытия; 6 − группа электродов по качеству изготовления; 7 − группа индексов, указывающих характеристики наплавленного металла и металла шва по ГОСТ 9467–75, ГОСТ 10051–75 или ГОСТ 10052–75; 8 − вид покрытия; 9 − допустимые пространственные положения сварки или наплавки; 10 − род применяемого при сварке или наплавке тока, полярность постоянного тока и номинальное напряжение холостого хода источника питания сварочной дуги переменного тока частотой 50 Гц; 11 − стандарт, регламентирующий классификацию электродов и общие технические условия
(ГОСТ 9467–75); 12 − обозначение стандарта на типы электродов
Для электродов марок, не относящихся к типам по ГОСТ 9467–75, ГОСТ 10051–75 и ГОСТ 10052–75, тип электрода в условном обозначении не приводят (поз. 1 на рис. 25), а вместо стандарта на типы электродов указывают технические условия на электроды конкретной марки (поз. 12 на рис. 25). В условном обозначении электродов для сварки углеродистых и низколегированных сталей с временным сопротивлением разрыву до 60 кгс/мм2 после буквы Е тире не ставят. Приведенное на рис. 25 условное обозначение должно быть указано на этикетках или маркировке коробок, пачек и ящиков с электродами. В документации на электроды их условное обозначение
50