
книги / Научно-исследовательская работа магистров по технологии машиностроения
..pdf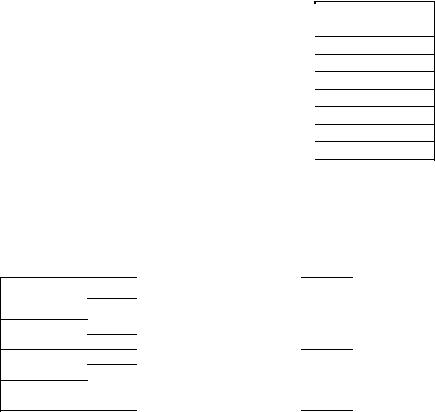
Условия испытаний: обрабатываемый материал – сталь 45, инструмент – проходной резец, оснащенный пластиной из твердого сплава Т15К6, геометрические параметры инструмента выбраны согласно нормативам следующим образом: γ = 10º; α = 8º; α1 = 8º;
φ = 45°; φ1 = 45°; λ = 0°; rв = 0,5 мм.
Матрица планирования представлена в табл. 2. Преобразование независимых переменных Хi к безразмерным
переменным хi проводится с помощью известного уравнения преобразования. В каждой точке факторного пространства опыт повторялся по три раза.
Таблица 2
Матрица планирования независимых переменных в полном факторном эксперименте 23
|
x1, ° |
x2, ° |
x3, ° |
1 |
– |
– |
– |
2 |
+ |
– |
– |
3 |
– |
+ |
– |
4 |
+ |
+ |
– |
5 |
– |
– |
+ |
6 |
+ |
– |
+ |
7 |
– |
+ |
+ |
8 |
+ |
+ |
+ |
Результаты испытаний представлены в виде таблицы на примере исследования влияния режимов резания на виброскорость (табл. 3).
Точкиυплана
1
2
3
Таблица 3 Результаты исследования виброскорости, мм/с.
y1 |
y2 |
y3 |
yv |
2 |
ˆ |
ˆ |
2 |
|
|
|
|
|
sv |
yv |
( yv – yv ) |
|
|
ln y1 |
ln y2 |
ln y3 |
ln yv |
|
||||
|
|
|
|
|||||
0,55 |
0,58 |
0,56 |
0,56 |
0,00073 |
–0,560 |
0,000193 |
||
–0,60 |
–0,54 |
–0,58 |
–0,57 |
|||||
|
|
|
|
|||||
0,65 |
0,70 |
0,68 |
0,68 |
0,00140 |
–0,400 |
0,000089 |
||
–0,43 |
–0,36 |
–0,39 |
–0,39 |
|||||
|
|
|
|
|||||
0,70 |
0,71 |
0,67 |
0,69 |
0,00091 |
–0,356 |
0,000105 |
||
–0,36 |
–0,34 |
–0,40 |
–0,37 |
|||||
|
|
|
|
171

|
|
|
|
|
|
Окончание |
табл. |
3 |
||
|
|
|
|
|
|
|
|
|
|
|
Точки планаυ |
y1 |
y2 |
y3 |
|
yv |
2 |
ˆ |
|
ˆ |
2 |
|
|
|
|
|
sv |
yv |
|
( yv – yv ) |
|
|
ln y1 |
ln y2 |
ln y3 |
|
ln yv |
|
|
||||
|
|
|
|
|
|
|
|
|||
4 |
0,58 |
0,60 |
0,62 |
|
0,60 |
0,00111 |
–0,516 |
|
0,00027 |
|
–0,54 |
–0,51 |
–0,48 |
|
–0,51 |
|
|
||||
|
|
|
|
|
|
|
||||
5 |
0,59 |
0,57 |
0,61 |
|
0,59 |
0,00115 |
–0,518 |
|
0,000093 |
|
–0,53 |
–0,56 |
–0,49 |
|
–0,53 |
|
|||||
|
|
|
|
|
|
|
||||
6 |
0,69 |
0,72 |
0,70 |
|
0,70 |
0,00047 |
–0,358 |
|
0,000037 |
|
–0,37 |
–0,33 |
–0,36 |
|
–0,35 |
|
|||||
|
|
|
|
|
|
|
||||
7 |
0,75 |
0,80 |
0,76 |
|
0,77 |
0,00116 |
–0,246 |
|
0,000236 |
|
–0,29 |
–0,22 |
–0,27 |
|
–0,26 |
|
|||||
|
|
|
|
|
|
|
||||
8 |
0,70 |
0,6 |
0,67 |
|
0,67 |
0,00139 |
–0,406 |
|
0,000110 |
|
–0,36 |
–0,43 |
–0,40 |
|
–0,40 |
|
|||||
|
|
|
|
|
|
|
||||
|
|
ln y |
= –0,42 Σs2 |
= 0,00832 Σ = 0,000889 |
|
|
||||
|
|
|
|
v |
|
|
|
|
|
|
Вычислялись коэффициенты регрессии и дисперсия параметра оптимизации (средняя арифметическая из дисперсий всех n различных вариантов опытов):
|
n |
|
|
s2 y |
sv2 |
0,00104. |
|
v 1 |
|||
n |
|||
|
|
Дисперсия коэффициентов регрессии
s2 bi s2nry 0,000043 , s bi 0,00658.
Проверка значимости коэффициентов bi проведена с помощью критерия Стьюдента. Значимыми оказались коэффициенты b1, b3, b23.
В результате линейная математическая модель этой зависимости будет выглядеть так:
yˆ 0,42 0,08х1 0,039х3 0,017х23.
После потенцирования получена cтепенная математическая модель влияния режимов резания на виброскорость:
B |
V 0,08 |
S0,04 0,03ln t t0,14 |
мм/с |
|
e0,65 |
||
|
|
|
172

Проверка адекватности полученной модели проведена по критерию Фишера.
Для этого рассчитано фактическое значение критерия:
s2
F 2 ад 0,8548. s y
Табличное значение Fкр [1] составило 3,24.
Так как Fкр > F, то уравнение адекватно.
Аналогичным образом получены и проверены остальные математические модели физических параметров процесса резания:
для составляющих силы резания
|
P e4,134 |
A; P e4,134 |
A; |
P e4,134 |
A, |
|
|
z |
x |
|
y |
|
|
где A |
S0,797 0,096ln t |
t0,698 |
|
|
|
|
|
; |
|
|
|
||
V 0,076 0,063ln S 0,027ln t 0,025ln S ln t |
|
|
|
для температуры резания
T e5,24 V 0,17 0,09ln S 0,07ln t S0,53 t0,51 С;
для шума резания
|
Ш e3,2 |
V 0,03 S0,01 t1,63 Дб; |
|
|
для мощности резания: |
|
|
||
M |
e3,6 |
V 0,496 0,117ln S 0,187 ln t 0,058ln S ln t |
Вт. |
|
|
S |
0,301 0,116ln t t0,267 |
||
|
|
|
Затем по полученным математическим моделям построены графики этих зависимостей.
При анализе всех полученных зависимостей выяснилось, что наиболее значимыми являются зависимости параметров шума и вибрации резания от режимов резания (рис. 2–7). Изменение составляющих сил резания, температуры и мощности резания от режимов резания оказались менее значимыми и в дальнейшей работе не анализировались.
173
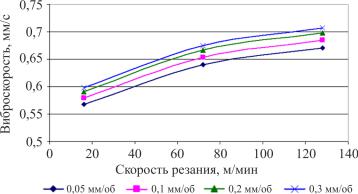
Рис. 2. График зависимости вибрации (виброскорости) от скорости резания при различных подачах при глубине резания 0,7 мм
На графике зависимости (рис. 2) видно, что при увеличении скорости резания с 16 до 128 м/мин при постоянной подаче 0,05 мм/об и глубине резания 0,7 мм происходит рост параметра виброскорости от 0,56 до 0,67 мм/с. При увеличении подачи до 0,3 мм/об значения виброскорости увеличиваются от 0,61 до 0,71 мм/с соответственно.
Таким образом увеличение виброскорости в диапазоне скоростей резания от 16 до 128 м/мин составляет 15–20 %. При увеличении глубины резания t от 0,5 до 1,5 мм и скорости резания V от 16 до 128 м/мин величина виброскорости усиливается на 10–12 % (рис. 3).
В результате анализа зависимости шума резания от режимов резания установлено, что при увеличении подачи (рис. 4) с 0,05 до 0,3 мм/об и постоянной глубине резания 0,5 мм шум резания увеличивается незначительно, с 8,35 до 8,51 Дб при скорости резания 16 м/мин, т.е. на 3 %. С увеличением скорости резания от 16 до 128 м/мин шум резания увеличивается на 7–10 %. При увеличении глубины резания (рис. 5) с 0,5 до 1,5 мм и постоянной подаче 0,3 мм/об шум резания резко увеличивается, с 9 до 51 Дб, т.е. в 4,5 раз, при скорости резания 16 м/мин. При скорости резания 128 м/мин с увеличением глубины резания шум резания увеличивается с 9,5 до 54 Дб, т.е. в 5,1 раза.
174
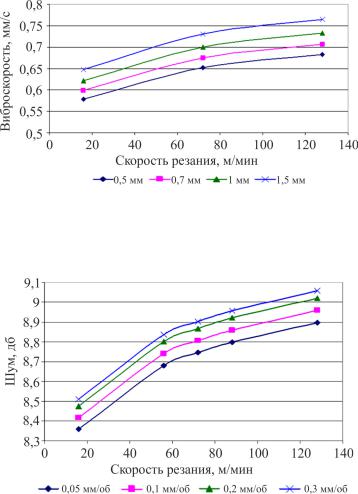
Для комплексной оценки влияния режимов резания – скорости, подачи и глубины резания на шум и вибрацию резания полученные зависимости представлены в виде поверхностей отклика (см. рис. 6, 7).
Рис. 3. График зависимости виброскорости от скорости резания при различных глубинах резания при подаче 0,3 мм/об.
Рис. 4. График зависимости шума резания от скорости резания при различной подаче при глубине резания 0,5 мм
175

Рис. 5. График зависимости шума резания от скорости резания при различной глубине резания при подаче 0,3 мм/об.
Рис. 6. Поверхность отклика – зависимость виброскорости от скорости резания и от глубины резания при постоянной подаче S = 0,3 мм/об.
176
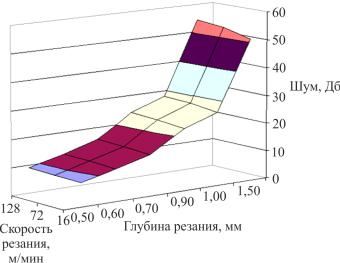
Рис. 7. Поверхностьотклика– зависимостьакустическогошума отскоростирезанияиот глубинырезанияприпостоянной подачеS = 0,3 мм/об.
На данных графиках можно определить значения шума и вибрации при любом сочетании параметров режимов резания – скорости, подачи и глубины резания.
Анализируя полученные зависимости виброскорости и шума резания от режимов резания можно сделать вывод, что на изменение шума и вибрации резания оказывает существенное влияние увеличение глубины резания. Увеличение подачи и скорости резания оказывают меньшее влияние.
Выводы
1.В результате сравнительного анализа установлено, что наиболее значимыми физическими параметрами процесса резания из рассмотренных являются параметры вибрации и шума резания. Эти параметры могут служить основными объективными показателями состояния процесса резания на металлорежущих станках с ЧПУ.
2.Увеличение скорости резания в диапазоне от 16 до 128 м/мин вызывает увеличение параметров вибрации при подаче 0,05 и глубине
177
резания 0,7 мм на 11 %, шум резания при подаче 0,05 и глубине резания 0,5 мм возрастает, соответственно, на 15 %.
3.Увеличение подачи от 0,05 до 0,3 мм/об вызывает увеличение шума с 7 до 10 %, вибрации с 15 до 20 %.
4.Увеличение глубины резания от 0,5 до 1,5 мм вызывает увеличение шума в 4,8 раза и вибрации от 10 до 12 %.
Заключение
Результаты проведенных исследований позволяют утверждать, что разработанный компьютерный диагностический центр можно эффективно и достоверно использовать для проведения более глубоких научных исследований процессов резания и шлифования, разработки системы адаптивного управления режимами резания по мере износа инструмента, разработки ускоренных методов назначения оптимальных режимов резания, для объективного выбора наиболее рациональной марки инструментального материала, вида и метода применяемого износостойкого покрытия инструмента и др.
Порядок выполнения лабораторной работы
1.Изучить методический материал по теории и актуальности проблемы диагностики процесса резания.
2.Ознакомиться с основными физическими явлениями и их параметрами, происходящими в процессе резания
3.Изучить методику проведения работы, устройство датчиков
иизмерительной аппаратуры.
4.Установить необходимые датчики для измерения силы резания, температуры резания, шума и вибрации, мощности резания.
5.Подключить аппаратуру диагностического центра «Камертон» и персональный компьютер.
6.Установить заготовку в патрон токарного станка и токарный резец в резцедержатель, надежно закрепить.
7.Составить план трехфакторного эксперимента по указанию преподавателя и учебного мастера.
8.Установить режимы резания согласно плану эксперимента.
178
9.Провести запись исследуемых параметров резания при различных комбинациях скорости резания, подачи и глубины резания.
10.Провести обработку полученных данных с использованием метода планирования экспериментов.
11.Сделать выводы по результатам работы.
12.Написать отчет о проделанной работе с выводами.
13.Ответить на вопросы по теме лабораторной работы.
14.Получить зачет.
Вопросы к зачету
1.В чем состоит актуальность проблемы диагностики процесса резания?
2.Каковы основные физические явления, происходящие в процессе резания?
3.Причины появления физических параметров.
4.Основные параметры физических явлений.
5.Как влияют условия резания на изменение физических параметров в зоне резания?
6.Как измеряется вибрация при резании?
7.Как измеряется шум резания?
8.Как измеряется температура резания?
9.Как измеряются составляющие силы резания?
10.Как можно использовать результаты данных исследований на практике?
179
Лабораторная работа № 8 ИССЛЕДОВАНИЕ ТОЧНОСТИ И НАСТРОЕННОСТИ
ТЕХНОЛОГИЧЕСКИХ ПРОЦЕССОВ ИЗГОТОВЛЕНИЯ ДЕТАЛЕЙ
Цели работы
1.Изучить методы анализа точности изготовления деталей и настроенности технологических процессов.
2.Овладеть навыками проведения измерений и расчетов при исследовании точности и настроенности ТП экспериментальностатистическим методом.
4.Исследовать точностьи настроенность ТП обработкирезанием.
5.Получить навыки оформления операционной карты контроля.
Теоретическая часть
Статистическая обработка результатов измерений
Процесс измерения всегда представляет собой сравнение измеряемой величины с эталоном. Эталоном является некоторая другая величина (такой же размерности), принимаемая за единицу измерения. Сравнение редко осуществляется непосредственным наложением эталона на исследуемый объект, чаще используется какой-либо прибор.
Измерение физической величины не может быть выполнено абсолютно точно. Любое измерение дает приближенный результат, иначе говоря, содержит погрешность измерения. Погрешностью измерения называется разность между истинным значением измеряемой величины X и результатом измерения xi.
x = X – xi. |
(1) |
Абсолютная точность – понятие идеальное, а в реальных технических изделиях на их функционирование влияет слишком большое число всевозможных факторов, и интерес, как правило, представляет не точное значение, а диапазон изменения значения измеряемой величины. Таким образом, технические науки довольствуются приближенными результатами измерения. Но при этом необходимо
180