
книги / Термическая обработка и волочение высокопрочной проволоки
..pdfв Для проволоки диам. 5 мм тМин можно найти по форму ле (2):
тмин = 30 4- 5D2 = 30 + 5*52 = 155 сек.
г. Диаметр 5,0 мм больше условного критического (2,0 мм). Следовательно, максимальная скорость патентирования опреде лится по формуле (19):
î-макс = — == -7 # -60 = 5,75 м/мин.
ТМИИ
д.Для проволоки диам. 2,0 мм Тмин также находим по фор муле (2):
тми11 = 30 + 5D2 = 30 + 5*22 = 50 сек.
е. Диаметр 2 мм равен условному критическому. Следова тельно, максимальную скорость патентирования следует вычис лить по формуле (21):
*макс = J * - = Ь . = |
J1 Ë .. 60 = |
ijf® .60 = 17,8 M/MUH. |
Тмин |
50 |
15 |
ж. Для проволоки диам. 1,6 мм тМИц найдем по формуле (2): Тми,, = 30 4- 5D2 = 30 4- 5 -1,62 = 42,8 сек.
з. Диам. 1,6 мм меньше условного критического (2,0 мм). Следовательно, максимальная скорость патентирования опреде лится по формуле (20):
г>макс = — = 4 |
г ‘60 = 17,8 м/мин. |
Тр |
15 |
П р и м е р / 2. Определить длину патент.ир01вочной ванны, ес ли длина нагревательной печи равна 11 ж, а агрегат предназна чен для патентирования проволоки диам. 1 мм и толще.
а. Исходу из сформулированного выше принципа выбора со отношения длин печи и ванны, в качестве условного критиче ского диаметра примем диаметр не более 1 мм.
б. Примем DK.у = 1 MMj тогда по формуле (2)
тми,1 = 30-f-5DK.y = 304-5*1 |
= |
35 сек. |
||
в. Зная, что хpj= 15 сек., из соотношения |
(11) находим |
|||
|
30 + 5 D " , |
|
|
|
" - ■ г - |
15 |
* - % |
= 2-33- |
|
LD |
|
|
|
|
г. Приняв La = 0,95 L'n = 10,5 м, определим |
||||
|
10 ,5 |
л с |
|
|
L, = -2 ,3 3 |
—’4,5 /(. |
|
|
|
д. Полная длина ванны |
|
|
|
|
L B = La |
4 ,5 = 4,75 м. |
0 ,9 5 |
0 ,9 5 |
ВЛИЯНИЕ СТРУКТУРЫ МЕТАЛЛА И ВЕЛИЧИНЫ ЕГО ЗЕРНА ПЕРЕД ПАТЕНТИРОВАНИЕМ НА ИЗМЕНЕНИЕ СВОЙСТВ ПРОВОЛОКИ
1.ВЛИЯНИЕ НОРМАЛИЗАЦИИ, ПРОВЕДЕННОЙ ПЕРЕД ПАТЕНТИРОВАНИЕМ, НА СВОЙСТВА ПРОВОЛОКИ
Опираясь на принцип ориентационного и размерного соответ ствия при фазовых превращениях, происходящих в твердых те лах, В. Д. Садовский, К. А. Малышев и Б. Г. Сазонов [55] уста новили, что крупное зерно, образовавшееся после высокотемпе ратурного на.грева, уничтожается при повторном нагреве лишь при температурах, значительно превышающих критическую точ ку Ас3.
Это положение, работа В. Я. Зубова о влиянии величины зер на на свойства проволоки [10], а также установленная в работах автора [56—60] взаимосвязь между приростом предела прочно сти и изменением пластичности послужили теоретическими пред посылками для исследования влияния нормализации, т. е. вели чины зерна перед патентированием, на изменение свойств прово локи.
Серия экспериментов была проведена на стали марки У9А, имеющей химический состав: 0,86% С; 0,23% Мп, 0,24% Si; 0,020% S; 0,020% Р; 0,07% Сг; 0,11% Ni; 0,10% Си.
Катанку диаметром 6,2 мм подвергали термической обработ ке по четырем вариантам.
I в а р и а н т : патентирование при длине печи 10 м, длине ванны 3,5 м, температуре 'нагрева 950 °С, температуре охлажда
ющей |
среды (селитры) 430 °С |
и |
скорости патентирования |
3 м/мин. |
|
|
|
II |
в а р и а н т : нормализация |
при |
температуре печи 1050°С |
и продолжительности пребывания проволоки в печи 7 мин.; да лее патентирование по режиму I варианта.
III в а р и а н т : нормализация при температуре печи 1050°С и продолжительности пребывания проволоки в печи 15 мин.; да лее патентирование по режиму I варианта.
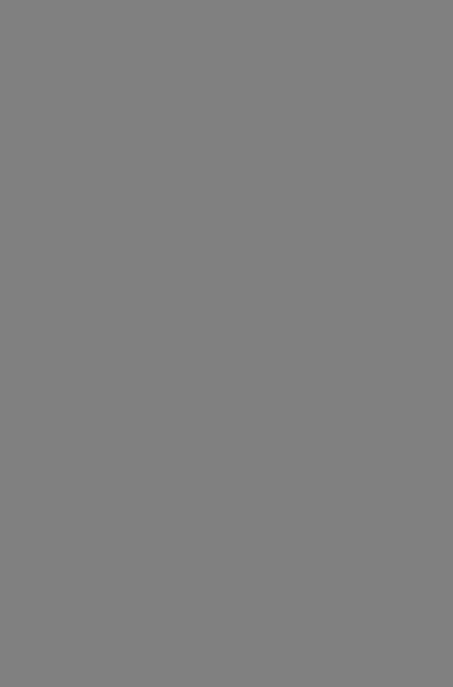
Для того чтобы установить влияние нормализации перед патентированием на изменение свойств проволоки при более жест ких условиях деформации, патентированную заготовку без пред варительной нормализации (I вариант) '.и предварительно нор мализованную (III вариант) подвергали волочению с диам. 6,2 мм на диам. 2,8 мм с -частными обжатиями 23%, т. е. минуя одну волоку, по приведенному же выше маршруту.
|
|
|
|
Т а б л и ц а |
б |
|
Механические свойства стали У9А диам. 6,2 |
мм |
|
||
|
Состояние материала |
Предел |
проч Относительное |
||
|
ности, кг/мм* сужение, |
% |
|||
«Сырая» катанка . |
...................... |
94 |
13 |
|
|
После |
патентирования |
130 |
21 |
|
|
Нормализованная заготовка (1050 °С, 7 мин.) |
98 |
17 |
|
||
После |
патентирования .............................. |
132 |
25 |
|
|
Нормализованная заготовка |
(1050 °С, 15 мин.) |
97 |
19 |
|
|
После |
патентирования |
................. |
127 |
22 |
|
Нормализованная заготовка (950 °С, 40 мин.) |
97 |
20 |
|
||
После |
патентирования |
|
130 |
23 |
|
Проволока диам. 2,8 мм, протянутая с частными обжатиями 12 и 23%, а также проволока диам. 1,6 мм, волоченная с частны ми обжатиями 12%, была проверена на предел прочности, отно сительное сужение, числа перегибов и числа скручиваний.
На рис. 19 и 20 даны результаты испытаний. Анализ экспери ментальных данных, приведенных на этих рисунках, показывает, что нормализация заготовки перед патентированием значитель но повышает пластические свойства проволоки после волочения.
Из рис. 19 видно, что благодаря применению нормализации при 1050 °С в течение 15 мин. перед патентированием пластиче ские свойства проволоки диам. 2,8 мм, волоченной с частными обжатиями 12% (суммарное обжатие Q = 80%), значительно повысились: относительное сужение — с 48 до 55%, число переги бов—на 28,5%. При суммарном обжатии около 80% и частных
обжатиях 23% относительное сужение |
повысилось с 42 до |
49%, а число .перегибов на 46%. |
|
Таким образом, при волочении с большими частными обжа |
|
тиями применение высокотемпературной |
нормализации перед |
патентированием еще более эффективно повышает пластические свойства проволоки, чем при малых частных обжатиях.
Как видно из рис. 20, проволока диам. 1,6 мм из заготовки, обработанной по I варианту (без нормализации перед патенти рованием), оказалась хрупкой: относительное сужение состави ло у ней 2—6% (среднее значение 3,7%), а числа перегибов в
54
Рис.'19. Зависимость свойств проволоки диам. 2,8 мм, про
тянутой |
с суммарным |
об |
||||
жатием |
Q — 80%, |
от режи |
||||
ма нормализации |
заготовки |
|||||
перед |
патентированием |
|||||
(сплошная |
линия — при |
|||||
частных |
обжатиях |
|
12%; |
|||
пунктир — при частных |
об |
|||||
I |
жатиях 23% ): |
|
||||
— без |
нормализации: .// — |
|||||
с |
нормализацией |
при |
1050 °С |
|||
н |
выдержке 7 мин.: |
/// |
— с |
|||
нормализацией |
при |
|
1050 °С и |
|||
выдержке |
15 |
мни.; |
IV |
— с |
||
нормализацией |
при |
|
940 °С и |
|||
|
выдержке |
4U |
мин. |
|
л . -
Ü а ,,
Гермичеот обработка |
|
|||
Рис. |
20. |
Зависимость |
||
свойств |
проволоки диам. |
|||
1,6 мм, протянутой |
с |
|||
суммарным |
от |
обжатием |
||
Q = 93,5%, |
режима |
|||
нормализации |
заготовки |
|||
перед |
патентированием |
|||
(обозначения, |
как |
на |
||
|
рис. |
19) |
|
пяти случаях из десяти равнялись нулю. Среднее значение чисел перегибов равнялось 4,1 (рис. 20). При суммарном обжатии около 93,5% благодаря высокотемпературной нормализации перед патентированием относительное сужение проволоки диам.
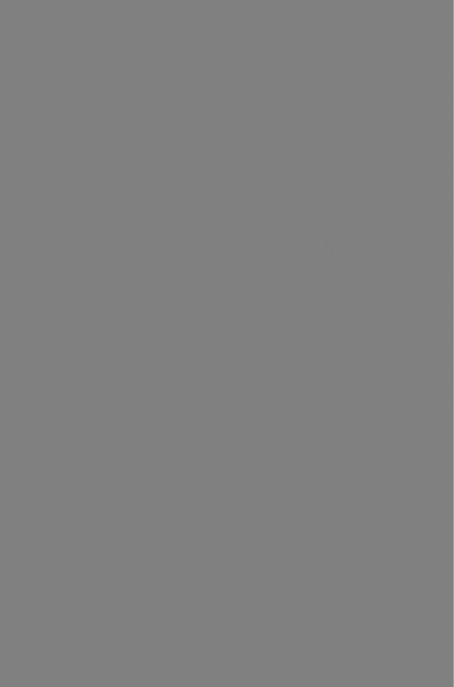
пературной нормализации заготовки перед патентированием создает блатоприятные предпосылки для интенсификации про цесса волочения.
Исследованиями автора [56^-60] установлено, что при обжа тий до 80% в. патентованной стали У8А наблюдается более интенсивный подъем пластических свойств, чем в стали с пони женным содержанием углерода. Это дало основание полагать о возможности использования для производства высокопрочной проволоки заэвтектоидных сталей, например У12А, не применяе мых до сих пор (в* настоящее время при производстве высоко прочной проволоки ограничиваются применением стали У9А).
Первой операцией по подготовке катанки к дальнейшему во лочению в этом случае является отжиг на зернистый перлит для устранения цементитной сетки, отсутствие которой является обя зательным условием для получения высоких свойств проволоки после волочения.
Катанка из стали У12А была подвергнута отжигу на зернис тый цементит в цеховых условиях по режиму: нагрев до 760 °С за 4 часа 30 мин., выдержка при 760° С в течение 13 час., охлаж дение с печью до 680 °С продолжительностью в 4 часа, выдержка при 680 °С в течение 4 час., охлаждение с печью до 550 °С и за мочка в воде.
Микроструктура этой стали после отжига приведена на рис. 21, а*. Дальнейшую обработку стали У12А осуществляли по
III варианту, т. е. производили нормализацию (1050°С, 15 мин.)
ипатентирование. Такая термическая обработка обеспечила са мое высокое качество проволоки после ее волочения (табл. 7).
|
|
|
|
Т а б л и ц а 7 |
|
|
Механические свойства заготовки из стали У12А и |
|
|||
|
протянутой |
из нее проволоки |
|
|
|
|
(средние значения из пяти испытаний) |
|
|
||
Диаметр |
|
Предел |
Относи |
Число |
Число |
Состояние металла |
тельное |
||||
проволоки |
прочности |
сужение, |
перегибов |
скручива |
|
мм |
|
кг/мм2 |
% |
|
ний |
|
|
|
|
|
|
6,2 |
После нормализации |
115 |
11 |
— |
— |
|
(1050 °С, 15 мин.) |
|
|
|
|
6,2 |
После нормализации |
147 |
17 |
— |
— |
2,8 |
и патентирования |
219 |
46,5 |
11,5 |
29 |
После деформации |
|||||
1,6 |
с обжатием 80% |
294 |
42,7 |
14,9 |
25 |
После деформации |
собжатием 93,5%
*При более быстром охлаждении катанки из заэвтектой|дной стали не посредственно после прокатки, например в горячен воде, также можно по лучить структуру без цементитной сетки.
При металлографическом исследовании микроструктуры нор мализованных и патёнтированных заготовок из стали У12А цементитной сетки не обнаружено (рис.'21, б и в).
После травления, которое не вызвало растрескивания метал ла в кислоте, и подготовки поверхности заготовка из стали У12А была подвергнута волочению с частными обжатиями 12% по приведенному выше маршруту.
Волочение стали У12А не вызывало затруднений: дрожания проволоки и обрывов не было, процесс практически не отличал ся от волочения стали У9А.
Полученную проволоку диам. 2,8 и 1,6 мм подвергали испы таниям на определение предела прочности, относительного су жения, чисел перегибов и чисел скручиваний.
Сопоставление результатов испытания проволок из сталей У12А (табл. 7) и У9А (рис. 19 и 20) свидетельствует о высоких свойствах проволоки из стали У12А.
Проволока диам. 1,6 мм из стали У12А имеет явные преиму щества по сравнению с такой же проволокой из стали У9А, об работанной по I варианту— без нормализации перед патентированием (см. рис. 20 и табл. 7).
Для сопоставления свойств проволоки из стали У12А и из стали У9А, прошедшей термообработку по III варианту (норма лизация при 1050 °С в течение 15 мин. и патентирование), металл
подвергали дальнейшему волочению с диам. |
1,6 мм: У12А — по |
|||||
маршруту 1,6—1,5—1,4 мм |
(Q = 95%); У9А — по |
маршруту |
||||
1,6—1,5—1,4—1,3—1,2 мм (Q = 96%). |
пределе |
прочности 294— |
||||
Проволока |
из стали |
У9А |
при |
|||
298 кг/мм2 |
оказалась |
хрупкой |
(относительное |
сужение |
10,5—13,5%, число перегибов 1—10), а проволока из стали У12А при пределе прочности 310—319 кг/мм2 показала достаточно вы сокиеотносительное сужение (35—36%) и число перегибов (15—18).
Это свидетельствует о преимуществе проволоки из стали У12А по сравнению с проволокой из стали У9А также в случае термической обработки этих сталей по III варианту.
Применением высокотемпературной нормализации заготовок перед патентированием из стали марки У12А была изготовлена также проволока других диаметров с очень высокими свойства ми, например, диам. 0,3 мм с пределом прочности 384 кг/мм2 и отношением разрушающего усилия Руз с узлом к максималь ному разрушающему усилию Р без узла 56,3%.
Таким образом, при использовании заэвтектоидной стали У12А и применении высокотемпературной нормализации загото вок перед патентированием получается проволока с очень высо кими прочностными и пластическими свойствами, а также чис лами перегибов и скручиваний.
Высокотемпературный нагрев и продолжительная выдержка обеспечивают получение крупного зерна в нормализованной за-
58
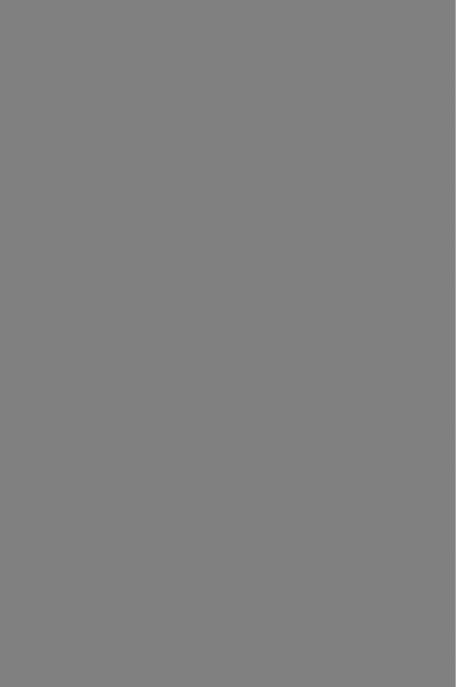
Более дисперсная и равномерная структура «и крупнозерни стое строение патентированного металла, предварительно под вергнутого высокотемпературной нормализации, и обеспечивают высокие свойства проволоки после волочения.
Описанный механизм перекристаллизации не согласуется с представлениями, происходящими при нагреве и охлаждении стали, излагаемыми в учебниках и монографиях по металлове дению, но находится в полном соответствии с принципом ориен тационного и размерного соответствия фазовых превращений
а-ь-у [55].
В микроструктуре заготовок, обработанных по III варианту (нормализация при 1050°С в течение 15 мин. и патентирование), более ярко выражено перистое строение (рис. 18, в) и при этом получены наиболее высокие свойства проволоки (см. рис. 19 и 20). Наименее ярко выражена перистость в структуре стали, обработанной по I варианту, т. е. без нормализации перед патентированием (рис. 18,а). Здесь свойства проволоки низкие (см. рис. 19 и 20).
Так как III вариант термической обработки обеспечил наи более высокие свойства проволоки, можно полагать, что микро
структура патентированной заготовки с ярко выраженной перистостыо наиболее благоприятна.
Аналогичная закономерность изменения структуры и свойств получена автором и на проволоке других диаметров из стали
У8А и У12А [62].
2. ВЫСОКОТЕМПЕРАТУРНЫЙ НАГРЕВ ЗАГОТОВОК ПРИ ПАТЕНТИРОВАНИИ — СПОСОБ ПОВЫШЕНИЯ МЕХАНИЧЕСКИХ СВОЙСТВ ПРОВОЛОКИ ПОСЛЕ ВОЛОЧЕНИЯ
При изучении влияния нормализации перед патентированием на изменение свойств проволоки оба вида термической обработ ки производили раздельно, в две операции.
Для проверки возможности замены высокотемпературной нормализации высокотемпературным нагревом непосредственно на патентировочной печи, т. е. для проверки возможности совме щения двух операций, была запатентирована проволока тонких размеров из сталей У9А и У12А при необычных режимах на грева,
В первом случае на одном из заводов на агрегате с печью длиной 13 м и ванной длиной 4,5 м запатентировали проволоку диам. 1,8 м из стали У9А (0,92% С) по режиму, указанному в табл. 8.
Во втором случае на другом заводе была запатентирована проволока диам. 1,8 мм из стали У9А (0,94% С) и диам. 1,4 мм из стали У12А (1,15% С и 1,17% С). Длина печи 16 м, длина ванны 5 м. Режим патентирования приведен в табл. 9.