
книги / Совершенствование метода вибродиагностики технического состояния элементов дорожных конструкций и кольцевых стендов
..pdf
где Aη = µτη = 2η(1Eτ+ν) .
Значения функций U, V и W вычисляются по приведенным формулам.
Для представления в виде, удобном для программирования, записываются следующие расчетные соотношения, а также меняются обозначения величин:
U2(X, Z) = A(D1 – BD0(X, Z)) + 2U1(X, Z) – U0(X, Z), (2.21) W2(X, Z) = A(D5 – BD4(X, Z)) + 2U1(X, Z) – U0(X, Z),
где вместо u(t − τ), u и u(t + τ) записано U0(X, Z), U1(X, Z) и U2(X, Z) соответственно, вместо U, W, U(t – τ), W(t – τ) записано D1, D5, D0, D4, коэффициент А = 1 + Aη, коэффициент
В = |
|
|
Aη |
. |
1 |
|
|||
|
+ A |
|||
|
|
|
η |
Коэффициенты А и В зависят от коэффициента вязкости материалов конструкции. Экспериментально установлено [8], что для реологических свойств материалов дорожной конструкции с покрытием из асфальтобетона вязкоупругие свойства битума являются определяющими. Поэтому для экспериментального определения вязкоупругих характеристик битума на кафедре СДМ ПНИПУ проведено исследование по оригинальной методике.
Для определения механических характеристик дорожных материалов (в частности битума) использовался стенд, принципиальная схема которого приведена на рис. 2.2–2.6. Стенд представляет собой массивное основание с вертикально расположенной опорой, на которой испытываемый образец – стальная балка с размерами 200 × 20 × 2 прямоугольного сечения с нанесенным слоем исследуемого материала подвергается изгибным колебаниям при комнатной температуре.
Стенд состоит из основания 3 и опоры 4. На опоре устанавливается исследуемый образец с покрытием, представляющим
81

Рис. 2.2. Схема установки и соединения аппаратуры для исследования колебаний двухслойной балки: 1 – металлическая балка; 2 – исследуемый материал (битум); 3 – основание; 4 – опора; 5 – вибратор; 6 – тензодатчик; 7 – звуковой генератор низкой частоты; 8 – тензостанция; 9 – мост сопротивлений Р33; 10 – осцилограф НО-41У; 11 – источник питания ВСА-5К; 12 – компенсационный тензодатчик
2ПКБ-20-200В
Рис. 2.3. Общий вид лабораторной установки: 1 – звуковой генератор низкой частоты; 2 – тензостанция; 3 – металлическая балка со слоем битума; 4 – осцилограф; 5 – блок питания
82
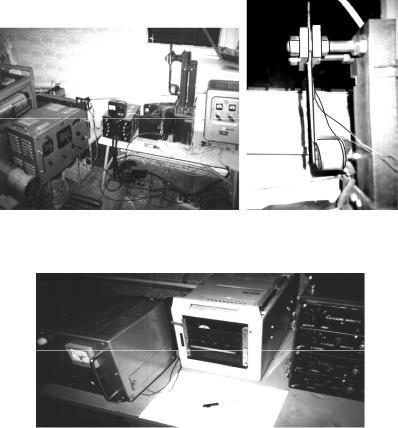
Рис. 2.4. Экспериментальная установка |
Рис. 2.5. Балка и вибратор |
Рис. 2.6. Осциллограф и гальванометр
собой металлическую балку 1 и слой демпфирующего материала 2, а также вибратор 5. Вибратор подключен к выходным клеммам звукового генератора. Вблизи защемления на металлической балке установлен тензодатчик 6, соединенный по полумостовой схеме с компенсационным датчиком 12. Сигнал с датчика деформаций поступает на тензоусилитель 8, а затем через согласующее устройство 9 – на осциллограф 10 с источником питания 11.
83
Частота возбуждения от генератора 7 подается на электромагнитный силовозбудитель 5. Образец испытывает изгибные колебания, при которых изменяется деформация поверхности образца, регистрируемая тензодатчиком 6. Сигнал от тензодатчика через тензостанцию 8 и согласующее сопротивление 9 подается на шлейфовый осцилограф 10 типа НО-41У, на экране которого видна амплитуда сигнала, пропорциональная уровню деформаций образца около опорного захвата.
Испытаниям подвергалась стальная балка с нанесенным на нее слоем битума. Проведено три эксперимента с различной толщиной слоя битума. Каждый эксперимент состоял из двух частей. На первом этапе исследовались вынужденные колебания балки. Она с помощью генератора колебаний низкой частоты вводилась в режим резонанса, в результате чего фиксировалась максимальная амплитуда и частота резонанса. На основании полученных данных были построены графики кривых резонанса. Затем балка вводилась в режим свободных колебаний путем отклонения ее свободного конца на расстояние, соответствующее максимальной амплитуде при резонансе. Замеряя время затухания колебаний, мы определили коэффициент затухания и логарифмический декремент.
Исходные данные, расчет и результаты эксперимента: Материал балки – Ст.3
Размеры балки: длина l = 200 мм, ширина h = 0 мм, толщина δ = 2,5 мм.
Исследуемый материал – битум БНД 40/60. Температура воздуха в лаборатории +20 °С.
Эксперимент № 1 Исследовалась чистая балка без слоя битума.
1) Частота резонанса fрез = 44 Гц. Максимальная амплитуда колебаний 12 мм.
Кривая резонанса № 1 показана на рис. 2.7.
84

Рис. 2.7. Кривая резонанса № 1
2) Время затухания колебаний балки составило 12,5 с. Имеем закон изменения амплитуды по времени:
А = А0е–nt,
где А0 – максимальная амплитуда; е – экспонента; n – коэффициент затухания; t – момент времени.
Для определения коэффициента затухания n на языке Quick Basic v4.5 была написана программа расчета цикла изменения амплитуды от ее максимального значения до нуля. Ре-
зультаты расчета: период колебаний Т = |
1 |
= |
1 |
= 0,02272 с; |
|
fрез |
44 |
||||
|
|
|
коэффициент затухания n = 1,39; декремент колебаний δ = nТ = = 1,39 · 0,02272 = 0,03158.
Эксперимент № 2 На балку нанесен слой битума толщиной 2,5 мм.
1) Частота резонанса fрез = 39 Гц. Максимальная амплитуда колебаний 12 мм.
Кривая резонанса № 2 показана на рис. 2.8.
85

Рис. 2.8. Кривая резонанса № 2
2) Время затухания колебаний балки составило 3 с.
Период колебаний Т = 1 = 1 = 0,02564 с, коэффици-
fрез 39
ент затухания n = 5,8; декремент колебаний δ = nТ = = 5,8 · 0,02564 = 0,1487.
Эксперимент № 3 На балку нанесен слой битума толщиной 5 мм.
1) Частота резонанса fрез = 38,5 Гц. Максимальная амплитуда колебаний 12 мм. Кривая резонанса № 3 показана на рис. 2.9.
Рис. 2.9. Кривая резонанса № 3
86

2) Время затухания колебаний балки составило 1,125 с;
1 1
период колебаний Т = fрез = 38,5 = 0,02597 с; коэффициент
затухания n = 15,7; декремент колебаний δ = nТ = 15,7 · 0,02597 = = 0,408.
Из графиков резонансных кривых видно, что ширина резонансного пика уменьшается с увеличением толщины слоя битума, а также происходит смещение кривой в сторону более низких частот, т.е. заметно явление вибродемпфирования всей системы.
При свободных колебаниях η= πωδЕ , где η – вязкость ма-
териала, МПа·с; ω – частота колебаний, с–1; Е – модуль упругости, МПа.
Как видно из формулы для определения вязкости материала покрытия, необходимо знать его модуль упругости. На основании проведенных опытов можно определить модули упругости методом свободных колебаний.
Уравнение свободных колебаний балочки с покрытием можно представить в форме
|
|
|
(α+ jβ) |
∂4ξ |
+ q |
∂2ξ |
= 0, |
(2.22) |
|
|
|
|
∂x4 |
∂t2 |
|||||
|
|
|
|
|
|
|
|||
где q = |
γ1h1 + γ2h2 |
; |
γ1 и γ2 – удельные веса материала покрытия |
||||||
g |
|||||||||
|
|
|
|
|
|
|
|
истальной балочки; g = 9,81 м/с2;
α= 13 (E1ϕ+ E2ψ),
β= 13 E1ϕη,
ψ= h23 −3h22δ+3h2 ,
87
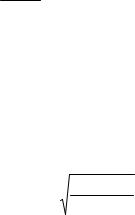
ϕ = h13 +3h12δ+3h1δ,
где δ – расстояние от плоскости контакта стальной балочки и покрытия до нейтральной плоскости; E1 и h1 – действительная часть комплексного модуля материала покрытия и толщина слоя покрытия; E2, h2 – динамический модуль материала основы из металла и толщина металлической балочки; η – коэффициент потерь материала покрытия; ξ – прогиб балочки.
Решение уравнения принимаем в виде
ξ(x,t) = ξ(x)e( jω−n)t .
После подстановки получим
(α+ jβ) ∂4∂ξx(4x) = q(ω2 −n2 + j2ωn)ξ(x).
Данное уравнение эквивалентно двум уравнениям:
|
∂ |
4 |
ξ(4x) |
|
|
α |
|
−qω2ξ(x) = 0, |
|||
|
|
∂x |
|
||
|
∂4ξ(x) |
|
|||
β |
|
||||
∂x |
4 |
−2ωnqξ(x) = 0. |
|||
|
|
|
(2.23)
(2.24)
(2.25)
Решая систему уравнений, можем записать собственную частоту изгибных колебаний в форме
ω= (kl)2 E1ϕ+ E2ψ |
, |
(2.26) |
3ql4 |
|
|
где l – длина балочки; (kl)4 = 3,52.
Действительная часть модуля материала покрытия определяется из уравнения. После преобразований запишем
|
|
|
E2 |
+ рЕ +с = 0, |
|
||
|
|
|
1 |
|
1 |
|
|
p = |
(kl)4 |
(4E2h13h2 +4E2h1h23 +6E2h12h22 )−12ω2l4qh1 |
, |
||||
|
|
|
h4 |
(kl)4 |
|||
где |
|
|
|
(2.27) |
|||
|
|
|
1 |
|
|
||
|
|
|
|
|
|
|
|
|
|
c = |
(kl)4 E2h4 −12ω2l4qE h |
|
|||
|
|
|
2 2 |
2 2 |
. |
|
|
|
|
|
h4 |
|
|
||
|
|
|
|
(kl)4 |
|
||
|
|
|
|
1 |
|
|
|
88
Для вычисления модуля упругости была составлена программа на языке Quick Basic, в которой, задавая частоту основного резонанса, получаем действительную часть динамического модуля упругости покрытия.
Так, для эксперимента №2 при f = 39 Гц Е = = 1,397731 · 1010 Па= 1,39 · 104 МПа.
Для эксперимента № 3 при f = 38,5 Гц Е = 2,32844 · 109 Па = = 2,32 · 103 МПа.
Согласно теории Фойгта для свободных колебаний, логарифмический декремент имеет вид
δ = |
πηω, |
(2.28) |
||
|
|
Е |
|
|
откуда найдем динамическую вязкость |
|
|||
η= |
δЕ |
, |
(2.29) |
|
|
||||
|
|
πω |
|
|
Тогда можем найти значение вязкости покрытия: |
||||
– для эксперимента 2 η= |
0,1487 13900 |
= 2,685 МПа·с; |
||
|
|
3,1415 245 |
|
|
– для эксперимента 3 η= |
0,408 2320 |
=1,245 МПа·с. |
||
|
3,1415 241,9 |
|
Как видно из приведенных ранее уравнений, значение вязкости материала покрытия зависит от многих параметров колебательной системы. Механизм зависимости статического модуля упругости и вязкости материала покрытия от толщины его слоя нами на сегодняшний день до конца не изучен и представляет собой отдельную тему, но на основании проведенной работы можем утверждать, что нам удалось найти искомые характеристики битума. Более точные значения можно получить, ужесточая условия эксперимента: применение балки равного сопротивления изгибу, исключения влияния заделки и т.д. Но в данной постановке эксперимента условно будем считать, что средний модуль упругости данного материала имеет значение
89
Ебит = |
Е2 + Е3 |
= |
13900 +2320 |
=8110 МПа, |
|
2 |
2 |
||||
|
|
|
среднее значение динамической вязкости битума
ηбит = |
η2 +η3 |
= |
2,685 +1,245 |
=1,965 МПа·с. |
|
2 |
|
2 |
|
Сравнение полученных значений модуля упругости и вязкости битума с характеристиками конструкционных материалов, опубликованными Акустическим институтом АН РФ, показывает, что результаты нашего эксперимента вполне соответствуют реальным значениям.
Для расчетов механических характеристик дорожной конструкции автором использовался частный случай описанного метода, основанный на двухмерной модели дороги, которая представляет собой поперечное сечение. В плоскости этого сечения рассматривалась нагрузка на дорогу (задается начальным перемещением узлов сетки) и снимался сигнал отклика в виде колебаний узлов сетки.
При использовании описанной в математической модели конструкции автомобильной дороги, основанной на методе конечных разностей, возникла необходимость располагать виброхарактеристикой отклика дороги после проезда по ней автомобильного транспорта. Таким образом, источником колебаний может являться движущийся автомобиль, остаточный колебательный процесс регистрируется с помощью датчика виброперемещения, который находится в одной плоскости сечения с нагрузкой. Данные по колебаниям поверхности являются эталонными в процессе расчета. Величина виброперемещения поверхности дороги в момент проезда автотранспорта используется в качестве начального условия для расчета прочности конструкции.
Для получения виброхарактеристики процесса колебания автором было проведено экспериментальное исследование поведения поверхности дороги при проезде автотранспорта. По-
90