
книги / Технология термического производства. Способы наноструктурирования материалов
.pdf51
|
|
Таблица 2.8 |
|
Состав соляных ванн, применяемых при закалке |
|
||
|
|
|
|
Состав в процентах |
Температуры |
Рабочая |
|
плавления, °С |
температура, °С |
||
|
|||
NaNO3 |
308 |
320–550 |
|
KaNO3 |
334 |
350–550 |
|
NaNO2 |
284 |
325–550 |
|
KNO2 |
387 |
– |
|
45NaNO3 + 55KNO3 |
220 |
230–550 |
|
45NaNO2 + 55KNO3 |
137 |
155–550 |
|
50NaNO3 + 50KNO2 |
143 |
160–550 |
|
50NaNO2 + 50KNO3 |
225 |
280–550 |
|
50NaNO3 + 50KNO3 |
220 |
280–550 |
|
25KNO3 + 75NaNO3 |
240 |
380–540 |
|
50NaNO3 + 50NaNO2 |
205 |
260–600 |
|
25NaNOa + 25NaNO3 + 50KNO3 |
175 |
205–600 |
|
NaOH |
328 |
350–700 |
|
KaOH |
360 |
400–650 |
|
75NaOH + 25NaNO3 |
280 |
420–540 |
|
35NaOH + 65KOH |
155 |
– |
|
20NaOH + 80KOH с добавкой 6H2O |
130 |
150–250 |
51
Окончание табл. 2.8
52
Состав в процентах |
Температуры |
Рабочая |
|
плавления, °С |
температура, °С |
||
|
|||
37NaOH + 63KOH |
160 |
180–350 |
|
40NaOH + 35Na2CO3 + 25KCl (или NaCl) |
– |
500–600 |
|
60NaOH + 40NaCl |
450 |
500–700 |
|
45NaNO3 + 27,5NaNO2 +27,5KNO3 |
120 |
240–260 |
|
53KNO3 + 40NaNO3 + 7NaNO3 c добавкой 2–3,5H2O |
100 |
110–125 |
|
95NaNO3 + 5Na2CO3 |
304 |
380–520 |
|
38KOH + 22NaOH – f 20NaNO3 + 15NaNO2 + 5Na3PO |
150 |
160–360 |
|
70NaOH + 15NaNO3 + 10NaNO2 + 5Na3PO4 |
250 |
280–600 |
|
60NaOH + 15NaNO3 + 15NaNO2 + 10Na3PO4 |
280 |
300–500 |
|
40NaOH + 30NaNO3 + 25NaNO2 + 5Na3PO4 |
280 |
300–500 |
|
Карналлит |
440 |
450–600 |
|
93Карналита + 7NaCl |
410 |
450–600 |
|
93Карналита + 7сильвинита |
390 |
450–600 |
52
Расплавы щелочей действуют раздражающе на кожу, поэтому предъявляются повышенные требования к вентиляции, спецодежде и другим санитарно-гигиеническим условиям труда.
Охлаждение в средах, изменяющих агрегатное состояние
К данным средам относят низкокипящие жидкости – воду, водные растворы солей и щелочей, масло. При закалке в этих средах различают три периода: 1) период пленочного кипения, когда скорость охлаждения сравнительно невелика; 2) период пузырькового кипения, наступающий при полном разрушении паровой пленки (рубашки), которое наблюдается при охлаждении поверхности до температуры ниже критической – в этот период происходит быстрый отвод тепла; 3) период конвективного теплообмена, который отвечает температурам ниже температуры кипения охлаждающей жидкости – теплоотвод в этот период происходит с наименьшей скоростью.
Охлаждение в воде и водных растворах
Схематически особенности такого охлаждения показаны на рис. 2.20, 2.21 [13].
Кривая охлаждения поверхности железного образца (см. рис. 2.21), получена экспериментально. На участке 1–2 кривой за очень короткое время, исчисляемое долями секунды, происходит быстрое охлаждение за счет отбора тепла, затрачиваемого на образование паровой пленки. Величина первичного падения, как показывают опыты, зависит от свойств жидкости и, в частности, от значения тепла парообразования, температуры и вязкости, а также от характеристики охлаждаемого изделия: температуры, величины удельной поверхности, формы, а также тепловых характеристик металла.
53
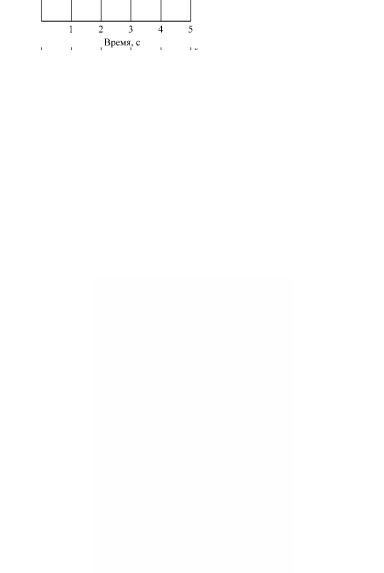
|
|
|
|
|
|
|
|
|
|
|
|
|
|
|
|
|
|
|
|
|
|
|
|
|
|
|
|
|
|
а |
|
б |
Рис. 2.20. Охлаждение в средах, изменяющих агрегатное состояние (схема): а – кривая охлаждения; б – характер изменения скорости охлаждения образца и коэффициента теплоотдачи среды; I – стадия пленочного кипении; II – стадия пузырчатого кипения; III – стадия конвективного теплообмена; tI–II – температура перехода от пленочного к пузырчатому кипению; tII–III – температура перехода от
пузырчатого кипения к стадии конвективного теплообмена
Рис. 2.21. Кривая охлаждения поверхности 20-миллиметрового сферического железного образца в воде при 20 °С. Скорость циркуляции воды 25 см/с
54
Величина первичного падения температур металлического образца в различных средах дана в табл. 2.9.
Таблица 2.9
Границы первичного падения температур поверхностей металлических образцов в низкокипящих средах
|
Температура в точке 2 (см. рис. 2.21), °С |
||||
Материал |
|
|
|
Масло |
|
5% водный |
Вода |
Вода |
индустри- |
||
и размер образца, мм |
|||||
раствор NaOH |
20 °С |
80 °С |
альное |
||
|
|
|
|
50 °С |
|
Железный образец D25 |
300 |
330 |
550 |
500 |
|
Железный образец D190 |
350 |
400 |
– |
550 |
|
Серебряный образец D20 |
– |
420 |
600 |
570 |
Участок 2–3 соответствует стадии пленочного кипения. Здесь паровая пленка имеет максимальную толщину и характеризуется высокой устойчивостью. Участок кривой 3–4 соответствует стадии пузырчатого кипения, участок 4–5 – стадии конвективного теплообмена.
Наиболее характерным для более точных кривых охлаждения металлической поверхности в воде является расположение максимумов скорости охлаждения в области низких температур. Максимально быстрое охлаждение внутренних объемов толстых изделий в отличие от их поверхностей наблюдается при высоких температурах. Уровень температуры будет тем выше, чем дальше от поверхности изделия расположен охлаждаемый объем.
Из рис. 2.22 видно, что в то время как на поверхности изделия в начале охлаждения температура снижается с большой скоростью, в середине ее охлаждение еще не начинается. Только после того как на поверхности температура сильно снизится, начинается снижение температуры центра. В период когда на поверхности охлаждение идет с макси-
55
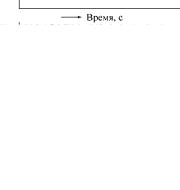
|
|
|
мальной скоростью, скорость |
||
|
|
|
|||
|
|
|
охлаждения в центре изделия |
||
|
|
|
незначительна. После сниже- |
||
|
|
|
ния температуры и скорости |
||
|
|
|
|||
|
|
|
охлаждения |
поверхности |
|
|
|
|
|||
|
|
|
центр изделия, еще имеющий |
||
|
|
|
высокую температуру, начи- |
||
|
|
|
нает охлаждаться с макси- |
||
|
|
|
|||
|
|
|
мальной скоростью. |
|
|
|
|
|
|
||
|
|
|
Таким |
образом, |
начало |
|
|
|
и самый процесс охлаждения |
||
Рис. 2.22. Кривые охлаждения |
поверхности |
намного |
опере- |
||
жают начало и процесс охла- |
|||||
поверхности и внутренних объ- |
ждения внутренних объемов |
||||
емов стального цилиндра в воде |
изделий. Это опережение тем |
||||
|
(схема) |
больше, чем больше эти объ- |
|||
|
|
|
емы удалены от поверхности охлаждения (см. рис. 2.22) или чем больше толщина изделия. В холодной воде центр большинства изделий наиболее интенсивно охлаждается тогда, когда температура поверхности достигает 150–250 °С, а в масле наиболее интенсивное охлаждение центра соответствует температуре поверхности 250–450 °С.
Учитывая, что поверхность охлаждаемых изделий в воде и масле достигает указанных температур за время, не превышающее 2–3 с, можно сделать вывод, что эвакуация основных количеств тепла из закаливаемых изделий большого сечения осуществляется тогда, когда их поверхность имеет температуру ниже 400–450 °С (рис. 2.23). Вследствие этого при закалке изделий среднего и большого размеров наибольшее значение имеет охлаждающая способность жидкости в нижнем интервале температур ниже 450 °С. Для мелких изделий, в которых не создается значительной разности температур поверхности и центральных зон, на результаты закалки оказывает влияние охлаждающая способность жидко-
56
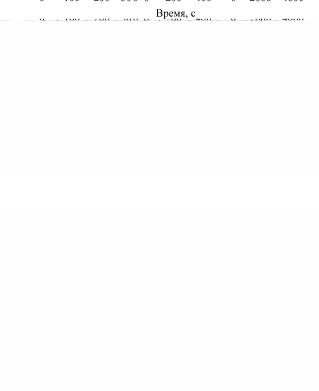
сти в более широком интервале – от 700 до 200 °С; при этом особенно сильно влияет охлаждающая способность в верхней части данного интервала.
а
б
Рис. 2.23. Температура поверхности (1), центра (2) и температурные перепады (3) сферических стальных образцов диаметром 25,4 мм (а) и 189,7 мм (б) охлаждаемых в воде, масле и воздухе
Рассмотрим подробней охлаждение в воде и водных растворах. Вода является дешевым и широко распространенным охладителем, применяемым при закалке изделий. Обладая достаточно высокой скоростью охлаждения в интервале
57
температур перлитного превращения (650–550 °С), вода позволяет получать необходимую твердость и прокаливаемость крупногабаритных изделий. Однако большая скорость охлаждения в интервале температур мартенситного превращения вызывает возникновение значительных напряжений в закаливаемых изделиях и, как следствие, деформации и трещинообразование.
Примеси в воде по-разному влияют на охлаждающую способность. Добавка поваренной соли и едких щелочей в количестве 5–10 % заметно повышает охлаждающую способность воды; 5–7%-ный водный раствор марганцевого калия уменьшает скорость охлаждения в интервале температур мартенситного превращения (дает среднюю скорость охлаждения между чистой водой и маслом). Главным и важным отличием охлаждающей способности растворов по сравнению с водой является резкое повышение скорости охлаждения при высоких температурах, что связанно с разрушением паровой пленки.
Ввиду этого прокаливаемость сталей в растворах солей и щелочей, как видно из рис. 2.24, выше, чем в воде. Кроме того, устранение паровой пленки в результате добавки соли сильно повышает равномерность охлаждения, а также тепловые напряжения и во многих случаях снижает суммарные растягивающие напряжения, которые вызывают образование закалочных трещин.
Подобно добавкам поваренной соли на охлаждающую способность воды действуют и добавки других солей, хорошо растворимых в воде (соды, сернокислого натрия, хлористого кальция).
С повышением температуры воды и водных растворов соли теплота испарения их снижается, что приводит к существенному изменению их охлаждающей способности.
Обычно для закалки используется вода с температурой 15–30 °С. Однако слои воды, соприкасающиеся с охлаждаемой
58
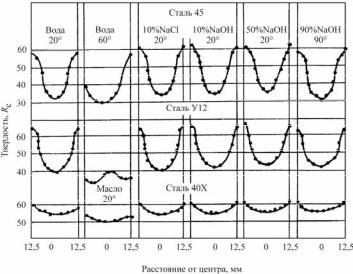
Рис. 2.24. Прокаливаемость цилиндрических образцов диаметром 25 мм в воде, водных растворах соли и щелочи
поверхностью изделия, всегда бывают сильно перегреты, вплоть до 100 °С. Наличие на изделии отверстий, как сквозных, так и особенно глухих, грубых следов механической обработки, больших горизонтальных поверхностей препятствуют отводу перегретой воды от охлаждаемой поверхности, и охлаждение изделия или отдельных частей его происходит, как в подогретой воде. При таких условиях толщина паровой пленки резко увеличивается, область пузырчатого кипения становится более узкой, скорость охлаждения в перлитном интервале распада аустенита резко снижается, а в области температур, соответствующих мартенситному превращению, остаются высокими. Таким образом, при закалке в горячей воде тепловые напряжения снижаются, а структурные получаются высокими, что способствует образованию закалочных трещин. Следовательно, во избежание закалочных трещин нельзя допускать нагрева воды выше температуры 30–40 °С,
59
что обеспечивается активной циркуляцией воды в закалочном баке.
Резкая зависимость охлаждающей способности воды от температуры является большим ее недостатком как закалочной среды. Добавки соли в воду несколько снижают зависимость ее охлаждающей способности от температуры. Так, небольшой подогрев 10%-го раствора соли приводит к снижению высоких скоростей охлаждения в средней области температур и выравниванию охлаждения в разных условиях. Более концентрированный, 20%-ный, раствор соли при нагреве значительно сильнее снижает скорости охлаждения при низких температурах, чем при высоких. Такое распределение скоростей более благоприятно и, следовательно, предупреждает образование трещин при закалке. Однако такой раствор имеет повышенную вязкость, вследствие чего он охлаждает недостаточно равномерно.
Наиболее высокой и равномерной охлаждающей способностью отличаются холодные 5–15%-ные растворы соли, которые хорошо зарекомендовали себя на практике. Такие изделия, как эталонные пластинки для прессов Бринеля и приборов Роквелла, к которым предъявляются повышенные требования в отношении равномерности их твердости на поверхности, обычно подвергаются закалке в соляных растворах.
Однородность температур в закалочном баке обеспечивают достаточностью его объема и циркуляцией охлаждающей жидкости. Циркуляция жидкости оказывает значительное влияние как на скорость охлаждения, так и на равномерность охлаждения всей поверхности изделия, уровень получаемой твердости, наличие мягких пятен, коробление, трещинообразование и т.д.
Желательно, чтобы направление циркуляции совпадало с направлением тепловых потоков, т.е. снизу вверх. Для обеспечения качественного охлаждения необходимо правильно
60