
книги / Промышленные роботы. Ч. 2
.pdf
Рис. 2.10. Кран-манипулятор с новой АСМ |
Рис. 2.11. Кран-манипулятор |
|
фирмы Effer |
Новая АСМ включает в себя уже существующую систему ограничения нагрузки фирмы Atlas. Специальная программа позволяет изменять характеристики крана в соответствии с индивидуальными потребностями пользователя, регулировать его скорость и грузоподъемность, изменяя производительность гидросистемы (рис. 2.10).
В ответ на требования EN 12999 компания Effer разработала прибор DMU (Data Monitoring Unit – блок контроля показаний), непрерывно контролирующий нагрузку и вылет стрелы крана-манипулятора (рис. 2.11) и не позволяющий превышать безопасные пределы грузоподъемности. Если нагрузка приближается к предельной, DMU предупредит оператора звуковым и световым сигналами. Если нагрузка превышает допустимый предел, ограничитель блокирует рычаг подъема и не дает поднять груз выше. Система позволяет лишь опустить груз либо вернуть стрелу в положение допустимой нагрузки. На кранах определенного типоразмера и на шасси отдельных типов система позволяет работать и в случае, когда стрела располагается над кабиной и капотом машины, автоматически снижая в этом опасном положении допустимую нагрузку. Система также постоянно проверяет, находится ли крановая платформа в горизонтальном положении. Контроль осуществляется восемь раз в секунду, а регистратор процесса фиксирует все данные по циклам подъема и все случаи перегрузки. Записанные данные при необходимости можно использовать.
Большинство моделей кранов-манипуляторов серийно оснащают дистанционным управлением, позволяющим оператору работать, находясь на безопасном расстоянии от машины. Дистанционное управление осуществляется по радио или кабелю, кроме того, имеется пульт управления на крановой надстройке. Каждый кран-манипулятор оснащен этими тремя системами управления, чтобы обеспечивались безопасность и удобство оператора в любых условиях (рис. 2.12).
21

Поставив все функции крана-манипулятора под контроль электронной системы управления FX и автоматического динамического управления, можно значительно увеличить производительность крана. FX – интеллектуальная электронная система, которая не только обеспечивает постоянство характеристик и полный контроль над краном, но и амортизирует динамические нагрузки, что позволяет поднимать больше, работая на безопасном пределе заложенных в конструкцию крана возможностей. Поскольку инерционные нагрузки контролируются лучше, то напряжения в конструкции крана уменьшаются, в результате надежность и срок службы крана-манипулятора увеличиваются.
Компания HMF в 2008 г. расширила модельный ряд и выпустила три новых крана-манипулятора (рис. 2.13). Самая малая модель ряда – Handy-330 с грузовым моментом 29,4 кН·м (3 тс·м). Специалисты HMF утверждают, что использовали в конструкции Handy-330 принципы конструкции кранов большего типоразмера. Стрела крана оснащена тремя телескопируемыми секциями, которые обеспечивают вылет до 7,1 м. Собственная масса крана-манипулято- ра всего 500 кг, он предназначен для установки на самые легкие коммерческие автомобили. Две дру-
гие модели Odin и Thor сгрузовым моментом соответственно 509,6 и 705,6 кН·м (52 и 72 тс·м) серийно оборудуются многими полезными
устройствами, такими как встро- Рис. 2.13. Кран-манипулятор модели Handy-330 енное в систему дистанционное управление. Стрелы обоих крановманипуляторов могут иметь до восьми секций с вылетом 20,31 и 20,46 м. Шестисекционная модель Thor оборудуется удлинителем, с которым высота подъема и вылет стрелы составляют 35 м.
Уже второй год компания HMF участвует в совместном проекте с фирмой OTR Tyres, крупнейшим в Европе производителем шин для землеройной техники. Партнеры разработали специальный так называемый гибридный кранманипулятор для погрузки шин. Он состоит из основания и колонны, взятых от
22
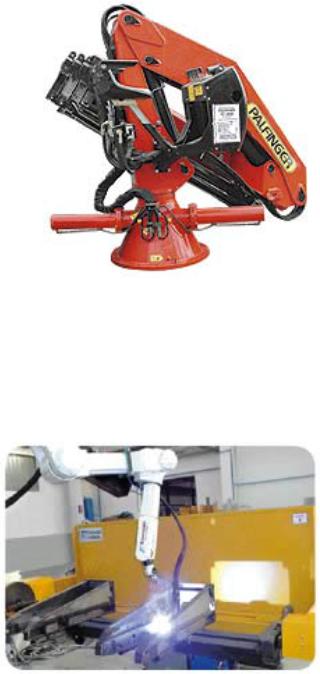
модели HMF-2000. Внутренняя секция стрелы и удлинитель позаимствованы от модели 1720-Т, наружная секция и удлинитель – от модели FJ9. Этот кранманипулятор оборудован гидравлическими выносными опорами, дистанционным радиоуправлением с восьмью функциями и электронной системой выравнивания машины.
На выставке английских коммерческих автомобилей (SED) были представлены новые краны-манипуляторы компании Cormach, выпущенные в 2008 г. Модель 22500Е ASC грузоподъемностью 9,3 т оснащена одной – шестью телескопируемыми секциями с гидроприводом. Радиус рабочей зоны – 5,72...15,84 м.
Модификацию с четырьмя телескопируе- |
|
||||
мыми секциями с гидроприводом по заказу |
|
||||
комплектуют удлинителем с двумя, тремя и |
|
||||
четырьмя секциями, и тогда радиус рабочей |
|
||||
зоны увеличивается до 21,72 м. |
|
|
|||
Одной из последних разработок фирмы |
|
||||
Hiab является кран-манипулятор Partek |
|
||||
Cargotec с грузовым моментом 147 кН·м |
|
||||
(15 |
тс·м) |
– модель XS |
144 |
HI-PRO |
|
(рис. 2.14). Ее оснастили системой дистан- |
|
||||
ционного |
радиоуправления |
CombiDrive |
Рис. 2.14. Кран-манипулятор фирмы |
||
5000, |
дополненной современной |
системой |
Hiab |
ограничения поворота крана.
2.2.2. Роботы, выполняющие обработку деталей и заготовок
Хотя роботы, выполняющие обработку изделий с помощью различных инструментов, и нашли пока менее широкое применение, чем аналогичное оборудование для транспортировки деталей и заготовок, они продемонстрировали свою эффективность при решении многих задач.
Сварка. Эта операция чаще всего выполняется с помощью роботов (рис. 2.15), предназначенных для манипулирования инструментом. Роботы могут осуществлять два вида сварки: точечную контактную и дуговую.
23
В обоих случаях робот удерживает сварочный пистолет, который пропускает ток через две соединяемые металлические детали.
Всоответствии с управляющей программой сварочный пистолет может перемещаться, практически не отклоняясь от заданной траектории. И если программа отлажена хорошо, сварочный пистолет прокладывает шов с очень высокой точностью.
Впоследние годы быстро развивается автоматизация дуговой сварки (сварки плавлением) с применением промышленных роботов. Сваркой плавлением можно соединять практически все используемые для изготовления конструкций металлы и сплавы любой толщины. Этот процесс связан с сильным шумом, большими температурами, действием дыма и интенсивного света (искрение); автоматизация позволяет избежать этих вредных воздействий на человека,
атакже обеспечивает высокое качество швов, большую стабильность и скорость работы.
Роботы, применяемые для автоматизации дуговой сварки, представляют собой универсальные перепрограммируемые манипуляторы. Система управления сварочным роботом должна обеспечивать быструю настройку параметров управления для заданной траектории движения сварочной горелки. Траектория может быть задана аналитически функцией перемещения горелки во времени или множеством точек, полученных экспериментально. Во время сварки оператор должен иметь возможность подкорректировать траекторию, чтобы обеспечить точность позиционирования не более необходимой (±0,1 мм). Также необходимо учитывать типы материалов свариваемых изделий и их толщину, от которых будет зависеть скорость перемещения головки сварочной горелки. Если скорость перемещения горелки будет отличаться от заданной, то даже при нулевой ошибке позиционирования не будет обеспечено высокое качество швов, так как при меньшей скорости края свариваемых материалов расплавятся недостаточно, а при большей переплавятся.
Основной проблемой управления дуговой сваркой является проблема точного позиционирования, т.е. точного отслеживания заданной траектории в пространстве и во времени, при непрерывном контурном управлении для выполнения относительно сложных манипуляционных задач. Основными факторами, порождающими эту проблему, являются существенная нелинейность динамической и кинематической модели, динамическая взаимосвязь между отдельными системами, а также незапланированные факторы: изменение программы траектории или неожиданное изменение полезной нагрузки.
24
Большинство ранее применявшихся методов управления либо не учитывали изменение динамики во времени, либо были настолько сложны и громоздки в вычислительном отношении, что требовали очень большого количества вычислений на каждом шаге за короткий промежуток времени. В первом случае не обеспечивались заданные требования к динамическому регулированию, а во втором были необходимы очень мощные и дорогие контроллеры.
Для устранения проблем нелинейностей дифференциальных уравнений применяется линеаризация динамической модели. Однако линеаризация с помощью классических методов с использованием разложения нелинейных дифференциальных уравнений в ряд Тейлора в окрестности рабочей точки требует перенастройки параметров управления при изменении рабочей точки.
Для устранения этих проблем применяют новый общий метод компенсации взаимосвязей и нелинейностей дифференциальных уравнений динамики с использованием диффеоморфного преобразования и теории алгебры Ли. Данный подход основан на идее получения «внешней линеаризации» сложной нелинейной системы с использованием диффеоморфного преобразования координат и нелинейной обратной связи по состоянию. Этот метод позволяет обеспечить поблочную развязку выхода; построение конструктивного алгоритма нахождения нелинейной обратной связи для подсистем, в которых число выходов может быть меньше числа входов или равно ему; развязку выходов нелинейной обратной связью с точки зрения состояния системы. Для обеспечения устойчивости системы управления нелинейная обратная связь соединяется с контроллером оптимальной коррекции ошибок.
Преимуществом этого метода является то, что не требуется перенастройки параметров управления, поскольку линеаризация проводится не в конкретной точке, а на целом подмножестве нелинейных плоскостей.
Большинство роботов для точечной сварки применяется в автомобильной промышленности. При сборке автомобиля необходимо выполнить огромное количество операций точечной сварки, чтобы надлежащим образом соединить между собой различные детали кузова, например боковины, крышу и капот. На современных конвейерах эти детали вначале соединяются временно несколькими прихваточными сварными соединениями. Далее кузов перемещается по конвейеру мимо группы роботов, каждый из которых осуществляет сварку в строго определенных местах (рис. 2.16). Поскольку все кузова монтируются
25

на одной производственной линии, для получения высококачественных соединений просто требуется, чтобы робот каждый раз повторял заданную последовательность перемещений.
Рис. 2.16. Робот для сварки кузова автомобиля
При очевидных преимуществах такого использования роботов существует ряд серьезных технических проблем. Запрограммировать робот весьма непросто. Необходимо не только задать точный маршрут движения манипулятора, но и подготовить инструкции, в соответствии с которыми регулируется напряжение и сила тока в каждой точке маршрута. А эти параметры могут меняться, например, в зависимости от толщины свариваемого материала или от того, какую форму имеет прокладываемый шов – прямую или криволинейную.
Также необходимо сконструировать фиксаторы, удерживающие детали в процессе сварки таким образом, чтобы сварка осуществлялась при высокой точности позиционирования. Когда сварочный пистолет держит человек, он способен учитывать незначительные смещения заготовки и сдвинуть инструмент, чтобы выполнить шов в заданном месте. Робот же не способен принимать подобные решения. Если фиксаторы допускают перекос или смещение, то существует вероятность того, что сварные швы будут расположены с отклонением. Кроме того, фиксатор должен быть таким, чтобы манипулятор имел доступ к детали с разных сторон.
Следующая проблема касается допусков на изготавливаемые детали. Человек принимает во внимание неизбежные отклонения в размерах, но роботу по-
26
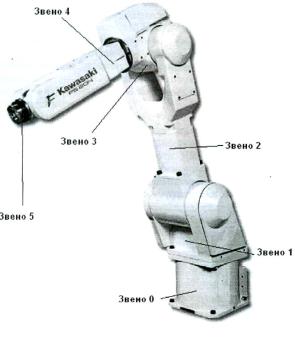
добная коррекция не под силу. Таким образом, когда сварка осуществляется с помощью автоматики, допуски на детали, изготавливаемые на других участках предприятия, должны быть минимальными.
Воздействие, которое роботы оказывают на другие этапы производственного процесса, осуществляется по принципу домино.
Робот Kawasaki F-серии применяется для автоматизации дуговой сварки и представляет собой универсальный перепрограммируемый манипулятор, система управления которым обеспечивает быструю настройку параметров управления для заданной траектории движения сварочной горелки. Оператор данного робота во время сварки может подкорректировать траекторию, чтобы обеспе-
чить точность позиционирования не более необходимой ( ±0,1 мм) (рис. 2.17). Манипуляционная система робота Kawasaki F-серии и его двигательные возможности определяются видом и расположением кинематических пар. Выбор варианта кинематической схемы манипуляционной системы определяется конкретными условиями техпроцесса. Эта схема должна обеспечивать достаточную степень универсальности функционирования робота с учетом операций, которые ему предстоит выполнять во внешней среде. Для выполнения транспортных операций без ориентации объекта достаточно сочетания трех ки-
нематических пар.
Планирование траектории движения манипулятора робота Kawasaki F-серии осуществляется с помощью алгоритмов управления планированием. Эти алгоритмы управления рассматриваются как нелинейные алгоритмы разделения командного движения по степеням подвижности манипулятора.
Манипулятор состоит из пяти кинематических пар (КП): четырех вращательных S1, S2, S4, S5 и одной поступательной S2. Он снабжен рабочим органом, представляющим собой электрод для дуговой сварки заготовок, движущихся по конвейеру. Кинематические пары образуют разомкнутую (есть звенья, входящие в одну КП) простую пространственную (звенья движутся в разных плоскостях) кинематическую цепь.
27

Большинство роботов Kawasaki F-серии для дуговой и точечной сварки применяется в автомобильной промышленности при сборке автомобилей.
Сверление. Как правило, операцию сверления осуществляют на станке. При использовании робота в его захватном приспособлении закрепляется рабочий инструмент, который перемещается над поверхностью обрабатываемой детали, высверливая отверстия в нужных местах. Преимущество подобной процедуры проявляется в тех случаях, когда приходится работать с крупногабаритными и массивными деталями или проделывать большое число отверстий.
Операции сверления играют значительную роль в производстве самолетов. Они предшествуют клепке, при которой в отверстия вставляются миниатюрные зажимные детали, скрепляющие между собой два листа металла. В деталях самолетов необходимо проделывать сотни, а то и тысячи отверстий под заклепки, и вполне естественно, что такую операцию поручили роботу.
Например, одна английская компания изготавливает детали механизма бомбосбрасывания, предназначенного для истребителя «Торнадо». Механизм представляет собой цилиндрическую конструкцию длиной примерно 6 м, к которой требуется приклепать кожух из восьми металлических панелей. В кожухе необходимо просверлить около 3000 отверстий под заклепки. Проблема заключалась в том, как добиться, чтобы робот, оснащенный высокоскоростной сверлильной головкой, проделывал отверстия точно в заданных местах.
Инженеры пришли к выводу, что данную проблему можно решить следующим образом: рабочий просверливает ряд эталонных отверстий (примерно через 1 м друг от друга) вдоль панелей, которые размещаются надлежащим образом поверх цилиндрической конструкции.
Манипулятор с закрепленным в его зажиме сенсорным зондом (не сверлом) (рис. 2.18) перемещается над поверхностью заготовки, посылая в память робота данные о местонахождении эталонных отверстий. Затем робот рассчитывает точные координаты остальных отверстий, исходя из этих базовых точек. Завершив операцию сверления, робот удаляет оставшиеся в отверстиях крошечные части-
Рис. 2.18. Робот для операции цы металла специальным инструментом.
сверления
28
Бесконтактная обработка заготовок. Из-за малой жесткости и недоста-
точной твердости роботы не могут проводить обработку твердых материалов резаньем. Поэтому инженеры изучают бесконтактные методы обработки материалов, подобных металлу или пластику. К таким методам, в частности, относится обработка лазером. В рабочем органе робота закреплен прибор, который направляет высокоэнергетическое когерентное излучение лазера (для чего нередко используется волокно-оптическая система передачи) на обрабатываемую заготовку. Лазер может с высокой точностью резать пластины из металла, в частности из стали. Робот перемещает рабочий орган над обрабатываемым листовым материалом по траектории, определяемой программой. Программой же регулируется интенсивность светового луча в соответствии с толщиной нарезаемого материала.
Другой бесконтактный метод резанья основан на использовании струи жидкости. Такой подход впервые применила компания «Дженерал моторс». На ее заводе в г. Адриане установлена система с 10 роботами, изготавливающая пластмассовые детали нефтеналивных цистерн. Восемь из десяти роботов направляют водяные струи под высоким давлением на перемещаемые конвейером пластмассовые листы. Эти струи прорезают в исходном материале ряд отверстий и щелей, а также удаляют лишние элементы пластмассовых прессованных деталей. По утверждению представителей компании «Дженерал моторс», подобная роботизированная система весьма экономична, так как исключает износ инструмента и позволяет повысить качество операций резанья. Поскольку система управляется программой, которая находится в памяти центрального компьютера, для контроля и обслуживания всех 10 роботов требуется только два оператора.
Нанесение различных составов на поверхность. На большинстве пред-
приятий после таких операций, как резанье, производится обработка поверхности только что изготовленных деталей (чаще всего окраска) (рис. 2.19). Это еще один тип производственных операций, которые способен выполнять робот, если его оснастить пульверизатором. В память робота закладывается программа, обеспечивающая выполнение определенной многократно повторяемой последовательности перемещений. Одновременно программа регулирует скорость разбрызгивания краски. В результате на поверхности окрашиваемой детали образуется равномерное покрытие, причем нередко робот обеспечивает более высокое качество окраски, чем человек, которому свойственна неточность движений.
29

Рис. 2.19. Робот для окраски изделий
Среди других процедур обработки поверхности можно отметить напыление антикоррозийных жидкостей на листы металла для защиты их от химического или физического воздействия окружающей среды, а также нанесение клеевых составов на поверхность деталей, подлежащих соединению.
Автомобилестроительные компании исследовали возможность применения последней операции на этапе окончательной «подгонки» готовых узлов, в частности при монтаже таких элементов, как хромовые вкладыши на кузове автомобиля. При выполнении подобных операций робот (рис. 2.20) помещают в оболочку, которая защищает его от попадания клея и других связующих веществ. Его также можно «обучить» тому, чтобы он время от времени самостоятельно очищался, погружая захватное приспособление в очищающую жидкость.
Рис. 2.20. Робот для нанесения клеевых составов
Чистовая обработка. Самая «непопулярная» операция в механообработке, которая трудно поддается автоматизации, – это удаление заусенцев, посторонних частиц и зачистка.
30