
книги / Особенности получения наноструктурированных ионно-плазменных плёнок с заданными свойствами
..pdfстали при обработке аустенитной стали 12Х18Н10Т в 1,7 раза и повысить качество обработанной поверхности (табл. 7).
Выявлено, что для ионно-плазменных методов, в частности электродугового испарения, свойствены неравновесные условия и высокая анизотропия скоростей формирования по различным направлениям. Пленки, полученные данным методом, имеют много разновидностей структур, характеризуемых размером поликристаллической фазы, фазовым составом и морфологией поверхности.
Определено, что на ориентирование оси (111) текстуры пленок ZrN оказывает влияние положение подложки относительно потока пленкообразующих частиц. На скорость осаждения и строение поликристаллической фазы пленок ZrN влияют: состав газовой смеси и парциальное давление ее активной составляющей, положение подложки относительно потока пленкообразующих частиц, дистанция подложка – источник плазмы, состояние (подвижная или неподвижная) подложки и ее размеры.
Установлены технологические параметры, оказывающие непосредственное влияние на фазовый состав и свойства пленок ZrN, получаемых методом электродугового испарения. К таким параметрам относятся: температура подложки, температура конденсации, ток дуги, напряжение смещения на подложке, давление газовой смеси, соотношение реакционного и инертного газа газовой смеси, дистанция подложка–источник плазмы.
Проведение технологического процесса в соответствии с оптимальными технологическими параметрами позволило получить износостойкие пленки ZrN, позволяющие в сложных технологических условиях обрабатывать такие сложные материалы, как аустенитные стали, повысить стойкость инструмента из быстрорежущей стали в 1,7 раза и улучшить качество обработанной поверхности.
Увеличение сопротивляемости инструментального материала адгезионному изнашиванию при осаждении пленки ZrN
61
Таблица 7
Результаты промышленных испытаний [110]
|
Тип |
Диа- |
Материал |
Скорость |
Ско- |
Обрабаты- |
Мате- |
Коли- |
Количе- |
Время |
Ско- |
Струж- |
|
инст- |
метр, |
инстру- |
шпин- |
рость |
ваемый |
риал |
чество |
ство от- |
обработ- |
рость |
ка |
|
румен- |
мм |
мента |
деля, |
подачи, |
материал |
пленки |
обра- |
верстий |
ки, мин |
обра- |
|
|
та |
|
|
об/мин |
об/мин |
|
|
ботки |
|
|
ботки, |
|
|
|
|
|
|
|
|
|
|
|
|
мин |
|
62 |
|
|
|
|
|
|
|
|
|
|
|
Элемен- |
|
|
|
|
|
|
|
|
|
|
|
тарная, |
|
|
|
|
|
|
|
|
– |
4 кл. |
max 60 |
10 |
6 |
|
|
|
|
|
|
|
|
рваные |
|||||
|
|
|
|
|
|
|
|
|
|
|
|
|
|
Сверло |
8 |
Р6М5 |
500 |
100* |
12Х18Н10Т |
|
|
|
|
|
края |
|
|
|
|
|
|
|
||||||
|
Zr–ZrN |
6 кл. |
300 |
30 |
10 |
Сливная |
||||||
|
|
|
|
|
|
|
||||||
|
|
|
|
|
|
|
|
|
|
|
|
|
* Вертикально-фрезерный станок модели 6Р13.
обусловлено снижением склонности структур быстрорежущей стали к взаимодействию с обрабатываемым материалом за счет появления на его поверхности промежуточного тела (пленки), имеющего более устойчивые электронные конфигурации типа s2p6, а также повышением уровня энергетического порога, при котором не возможна адгезия инструментального материала с обрабатываемым из-за снижения касательных напряжений
итемператур.
9.ИССЛЕДОВАНИЕ СТРУКТУРЫ И СВОЙСТВ
НАНОСТРУКТУРИРОВАННЫХ ПЛЕНОК ZRN, ФОРМИРУЕМЫХ МЕТОДОМ МАГНЕТРОННОГО РАСПЫЛЕНИЯ
Ионно-плазменные методы характеризуются направленностью потока пленкообразующих кластеров и неравновесными условиями, что, в зависимости от условий проведения процесса, приводит к различному структурному состоянию формируемых пленок [121]. Осаждение наноструктурированных ионноплазменных пленок с улучшенными эксплуатационными характеристиками возможно на модернизированном вакуумном оборудовании, а детальная информация может быть получена с использованием микроскопии высокого разрешения, анализа состава и дефектности пленок с помощью различных методов: РФЭС, РФА, электронной оже-спектроскопии (ЭОС), сканирующей и просвечивающей электронной микроскопии (СЭМ и ПЭМ), спектроскопии обратного резерфордовского рассеяния (СОРР), электронного микрозондового анализа (ЭМА), спектроскопии аннигиляции позитронов (САП), вторичной ионной масс-спектроскопии (ВИМС), сканирующей туннельной и атом- но-силовой микроскопии (СТМ, АСМ), локальной дифракции электронов (ЛДЭ) и др. [122]. За последние десятилетия исследователи добились значительного повышения надежности изделий с упрочняющими и защитными пленками. В результате исследований были выяснены и устранены многие факторы,
63
ухудшающие потенциальные возможности пленок. Проблема получения наноструктурированных пленок различного назначения практически решена, однако проблема стабилизации свойств указанных пленок находится на стадии совершенствования. Управление структурой, фазовым составом и механическими свойствами формируемых ионно-плазменных пленок возможно при оптимизации технологических параметров процесса осаждения, установлении корреляционных связей последних со структурой и свойствами формируемых пленок.
Целью данного этапа работы является исследование влияния соотношения реакционного и инертного газов в газовой смеси на механические свойства, фазовый состав, морфологические особенности и структурные характеристики пленок на основе ZrN, формируемых методом магнетронного распыления.
9.1. Методика проведения эксперимента
Пленки на основе ZrN формировали на автоматизированной установке УРМ3.279.048 электродугового испарения и магнетронного распыления с двух магнетронов с мишенями из циркония марки Э110, работающих от источников постоянного тока, на подготовленной поверхности тестовых образцов из нержавеющей стали 12Х18Н10Т. Перед технологическим процессом формирования пленки поверхность тестовых образцов подвергали ионной очистке, в процессе которой максимальная температура поверхности (Tmax) соответствовала 651 К. Температуру поверхности конденсации в процессе осаждения пленки поддерживали с помощью резистивного нагревателя, установленного в центральной части вакуумной камеры и контролировали с помощью инфракрасного бесконтактного пирометра «Термикс». Для увеличения адгезионной прочности пленки ZrN осаждали подслой из циркония, после осаждения которого температура поверхности образца не превышала 613 К (Tmax). Морфологические особенности сформированных пленок исследовали на автоэмиссионном электронном микроскопе Ultra-55. Рент-
64
геноструктурный и рентгенофазовый анализы пленок ZrN проводили с помощью рентгеновского дифрактометра Shimadzu XRD-6000 в Cu Кα-излучении. Микротвердость композиции пленка–подложка измеряли микротвердомером ПМТ-3 при нагрузке на индентер 0,5 Н. Пленки на основе ZrN формировали при различном соотношении реакционного и инертного газов в газовой смеси. Технологические параметры процесса магнетронного распыления приведены в табл. 8, структурные характеристики и механические свойства сформированных пленок на основе ZrN – в табл. 9.
Таблица 8 Технологические параметры процесса магнетронного распыления
Параметр |
|
Номер опыта |
|
||
1 |
2 |
3 |
4 |
||
|
|||||
|
|
|
|
|
|
Дистанция магнетрон–подложка L, мм |
120 |
120 |
120 |
120 |
|
Соотношение газов в газовой смеси N2/Ar, |
30/70 |
35/65 |
40/60 |
50/50 |
|
% |
|
|
|
|
|
Давление в вакуумной камере р, Па |
1,0 |
1,0 |
1,0 |
1,0 |
|
Напряжение смещения на подложке Uсм, В |
80 |
80 |
80 |
80 |
|
Напряжение на магнетроне Uм, В |
450 |
450 |
430 |
440 |
|
Ток на магнетроне Iм, А |
4,7 |
4,4 |
4,7 |
4,5 |
|
Мощность магнетронной системы N, кВт |
2,12 |
1,98 |
2,02 |
1,98 |
|
Максимальная температура поверхности |
621 |
622 |
624 |
629 |
|
конденсации Tmax, К |
|
|
|
|
|
Микротвердость композиции пленка–под- |
11,0 |
11,0 |
12,0 |
6,0 |
|
ложка Нµ, ГПа |
|
|
|
|
65
Таблица 9
Структурные характеристики пленок на основе ZrN, сформированных магнетронным распылением
|
Характеристика |
|
Номер опыта |
|
||
|
1 |
2 |
3 |
4 |
||
|
|
|||||
|
Соотношение газов в газовой |
30/70 |
35/65 |
40/60 |
50/50 |
|
|
смеси N2/Ar, % |
|
|
|
|
|
|
Фазовый состав: |
|
|
|
|
|
|
ZrN |
0,310 |
0,590 |
0,601 |
0,495 |
|
66 |
ZrN0,28 |
0,690 |
0,410 |
0,399 |
0,505 |
|
|
|
|
|
|
||
dZrN/dZrNтабл, нм |
0,2698/0,2673 |
0,2679/0,2673 |
0,2679/0,2673 |
0,2679/0,2673 |
||
|
||||||
|
dZrN0,28/dZrN0,28табл, нм |
0,2619/0,2588 |
0,2603/0,2588 |
0,2614/0,2588 |
0,2600/0,2588 |
|
|
IZrN/IZrN0,28 |
0,19 |
1,25 |
1,83 |
0,83 |
|
|
maxI111/IΣ |
0,108 |
0,417 |
0,456 |
0,405 |
|
|
maxI002/IΣ |
0,564 |
0,328 |
0,246 |
0,453 |
Примечание: dZrN/dZrNтабл – межплоскостное расстояние ZrN; IZrN/IZrN0,28 – отношение интенсивностей всех рефлексов кубической ZrN и гексагональной ZrN0,28 фазы; maxI111/IΣ и maxI002/IΣ – отношение максимальных интенсивностей рефлексов (111) и (002) к суммарной интенсивности рефлексов всех фаз ZrN.
66
9.2.Влияние соотношения реакционного и инертного газов
всмеси на температуру поверхности конденсации,
фазовый состав, структуру и свойства наноструктурированных пленок на основе ZrN
С использованием рентгенофазового анализа полученных дифрактограмм (рис. 20) установлено, что поликристаллическая составляющая пленки представлена двумя фазами: ZrN с кубической решеткой типа NaCl с параметром а = 0,463 нм и фазы ZrN0,28 с гексагональной решеткой типа Mg с параметрами а = 0,322 нм и с = 0,518 нм. На рис. 21 представлен сравнительный спектр фрагментов дифрактограмм полученных образцов пленок.
Выявлено, что изменение процентного соотношения азота и аргона в газовой смеси не влияет на фазовый состав пленки. Зерна кубической фазы ZrN имеют преимущественную кристаллографическую ориентировку (111), гексагональной фазы ZrN0,28 – (002). При сравнении соотношения интенсивностей рефлексов фаз (111)ZrN (угол 2θ ≈ 33,45°) и (002)ZrN0,28 (угол 2θ ≈
≈ 34,3°) на дифрактограмме рис. 20, б и объемных долей фаз в пленках (табл. 9) установлено, что при соотношении газов N2/Ar = 40/60 % формируется пленка с наибольшим количеством стехиометрической кубической фазы ZrN; максимальной относительной долей в пленке зерен, ориентированных в направлении (111), и минимальной – в направлении (002); наибольшей микротвердостью композиции пленка–подложка
12 ГПа.
Пленка с минимальной микротвердостью 6 ГПа и минимальной толщиной (так как выше интенсивность пика подложки α–Fe (2θ ≈ 44,7°)) формируется при соотношении газов N2/Ar = 50/50 %, примерно в одинаковых объемных долях фаз стехиометрического и нестехиометрического нитрида циркония в пленках, оптимальном соответствии среднего размера зерен табличным значениям, но при минимальной относительной доле
67

|
|
|
|
|
|
|
|
а |
б |
68
|
|
|
|
|
|
в |
г |
Рис. 20. Рентгеновские дифрактограммы (Cu Кα-излучение) пленок на основе ZrN, полученных при раз-
личном соотношении газов в газовой смеси N2/Ar, %: а – 30/70 = 0,43; б – 35/65 = 0,54; в – 40/60 = 0,67; г – 50/50 = 1,00
68
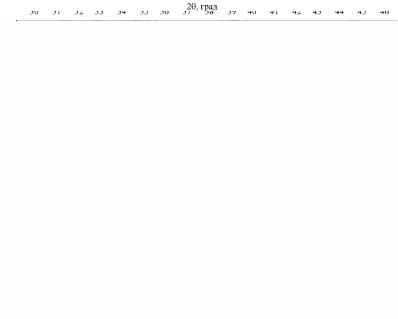
Рис. 21. Сравнительный спектр фрагментов дифрактограмм образцов пленок на основе ZrN, полученных магнетронным распылением при различном соотношении подаваемых газов аргона и азота N2/Ar, %:
30/70 = 0,43; 35/65 = 0,54; 40/60 = 0,67; 50/50 = 1,00
в пленке зерен, ориентированных в направлении (111), и максимальной – в направлении (002). Толщина пленки наибольшая при подаче 30 % N2. Можно заключить, что пленки будут формироваться в направлении (111) при соотношении газов N2/Ar = = 40/60 % и в направлении (002) – при N2/Ar = 50/50 % с са-
мой низкой энергией в случае, если определяющим фактором процесса формирования пленки является поверхностная энер-
гия [123].
Для изучения условий сохранения роста зерен в направлении преимущественной кристаллографической ориентации определяли температуру поверхности конденсации в процессе осаждения пленки пирометрическим способом (рис. 22). Уста-
69
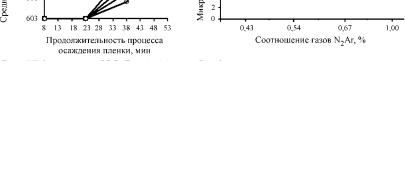
новлено, что температура поверхности конденсации с увеличением продолжительности процесса осаждения пленки при всех соотношениях газов не только поддерживается постоянной, но и незначительно увеличивается примерно на 40 К. Поэтому можно утверждать, что подвижности атомов на поверхности подложки достаточно, чтобы обеспечить сохранение преимущественного ориентирования зерен в процессе формирования пленки и степени ее текстурированности. Микротвердость же композиции пленка–подложка при созданных технологических условиях в большей степени зависит от содержания азота в газовой смеси. На рис. 22 приведены зависимости температуры поверхности конденсации и микротвердости композиции пленка–подложка от продолжительности процесса осаждения пленки.
|
|
|
|
|
|
а |
б |
Рис. 22. Зависимости температуры поверхности конденсации от продолжительности процесса магнетронного распыления (а) и микротвердости композиции пленка–подложка от соотношения газов N2/Ar га-
зовой смеси, % (б): 30/70 = 0,43; 35/65 = 0,54; 40/60 = 0,67; 50/50 = 1,00
Морфологические исследования сформированных пленок показали, что на поверхности сплошной пленки при всех соотношениях газов формируются структурные образования в виде
70