
книги из ГПНТБ / Полухин П.И. Прокатка и термическая обработка железнодорожных рельсов
.pdf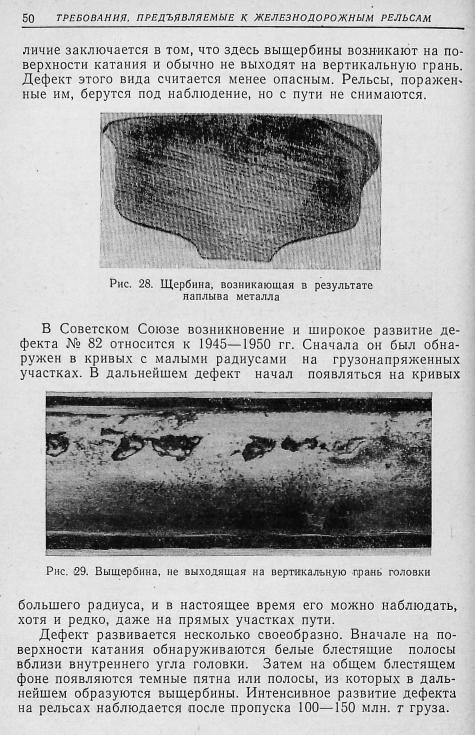
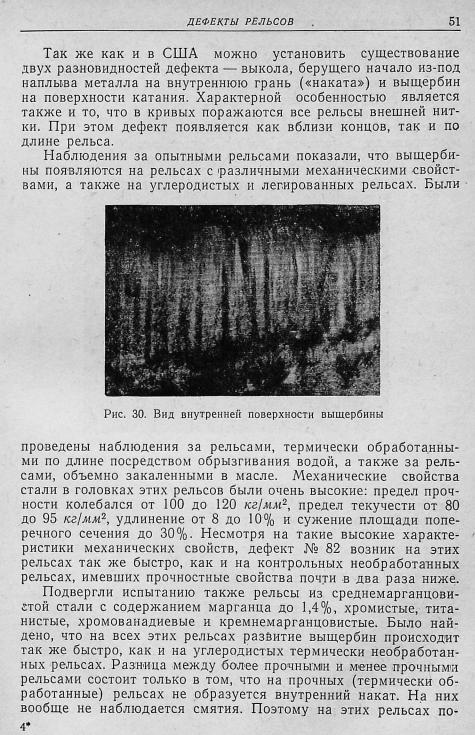
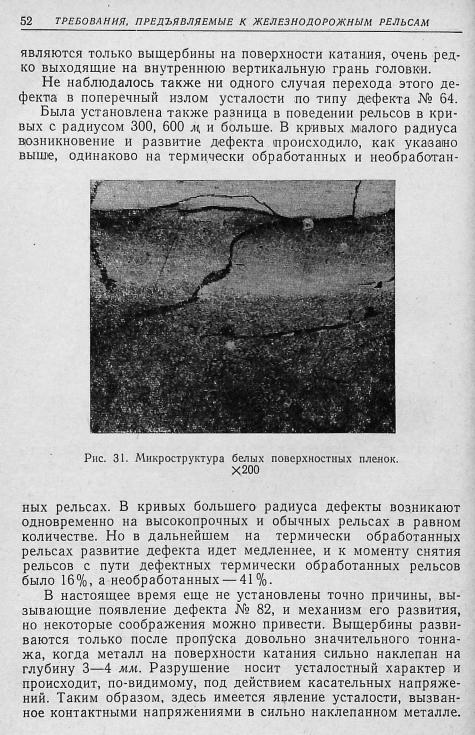
ДЕФЕКТЫ РЕЛЬСОВ |
53 |
В начальной стадии развития дефекта на поверхности ката ния образуются белые пленки. Микроструктура этих пленок по казана на рис. 31. Как видно из этой микрофотографии, на по верхности катания лежит собственно белая пленка, толщиной 0,03—0,05 мм. Твердость этой пленки около 600 НВ\ микро структура представляет собой смесь мартенсита и коагулиро ванных карбидов. Под белой пленкой лежит переходный слой также повышенной твердости, в структуре которого наблюдает ся смесь сорбита и троостита. Еще глубже лежит основной металл.
Причиной появления этих закаленных пленок является мгно венный нагрев поверхности катания при неизбежном проскаль зывании колес при вписывании колесных пар в кривые. При радиусе 300 м это проскальзывание составляет около 3%. На прямых участках пути такое проскальзывание может возникнуть
вследствие разных диаметров |
колес одной и |
той |
же ко |
лесной пары, причем разность |
диаметров достигает |
иногда |
|
10—12 мм,- |
|
вследствие |
|
Мгновенно нагретая тонкая пленка закаливается |
очень быстрого отвода тепла внутрь головки рельса. Закалоч ное происхождение этих пленок хорошо иллюстрируется рис. 32. На нем дана микрофотография такой же пленки, как и на рис. 31, но после отпуска при 600°. Как видно, белая пленка ис чезла, и структура основного металла полностью восстано вилась.
Более детальное изучение этого вопроса показало, что явле ния закалки поверхности широко распространены и вызываются трением, ударами, кратковременным прохождением электриче ского тока через контактную поверхность, обработкой током вы сокой частоты, автогенной горелкой и т. д.
Мартенситные пленки, будучи хрупкими, изрезаны трещина ми, распространяющимися также и на переходный слой (см. рис. 31). Трещины пересекают почти под прямым углом закален ный слой, а в основном металле меняют свое направление и идут параллельно поверхности катания.
Эти трещины могут быть очень эффективными концентрато рами напряжений.
Пока материал не наклепан, трещины не проникают в глубь металла. Мартенситные пленки под действием колес растрески ваются и отделяются от поверхности рельсов, вызывая шелуше ние. Но можно предположить, что когда металл, лежащий под пленкой, будет достаточно наклепан и охрупчен, то трещины бу дут углубляться внутрь металла и соединяться с внутренними трещинами, возникшими в результате наклепа (см. рис. 9). Та кой механизм хорошо объясняет все особенности образования дефекта № 82.
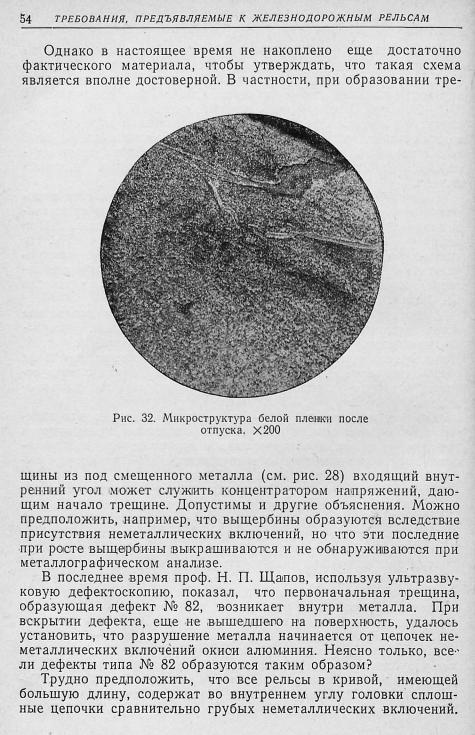
ДЕ ФЕ КТ Ы РЕЛЬСОВ |
55 |
Когда рельсы (высокоуглеродистые или термически обрабо танные) не имеют наката металла на внутреннюю вертикальную грань головки, то отпадает и концентратор напряжений в виде входящего угла под грибовидным наплывом металла. Но выщер бины на поверхности катания образуются очень быстро. Следо вательно, здесь действует иной концентратор напряжений.
Опыт шлифования рельсов на американских железных доро гах также не подтвердил гипотезу концентрации напряжений во входящем углу. На шлифованных рельсах дефекты типа «fla-
Рис. 33. Схема испытания образца рельса для получения дефекта № 82
king» образовывались так же интенсивно, как и на необработан ных рельсах.
Таким образом, причины, вызывающие начало разрушения, еще не ясны. Известны попытки исследователей воспроизвести дефект № 82 в лабораторных условиях. Для этого на машинах
сподвижной нагрузкой устанавливали специальную «люльку»,
вкоторой закрепляли образец (рис. 33). Периодически после определенного числа циклов нагрузки образец поворачивался вместе с люлькой на небольшой угол относительно продольной оси. Такие периодические повороты способствовали более энер гичному смещению металла в боковом направлении и образова нию грибовидного наплыва на одну из вертикальных граней го ловки. В дальнейшем образовывалась трещина по типу рис. 28 или даже расслоение головки (рис. 34).
Это испытание очень длительное и требует высокой прочно сти машин, так что в течение года можно испытать небольшое число образцов. На этих машинах испытывали рельсовые об разцы углеродистой стали термически необработанные, норма лизованные, закаленные в масле, а также рельсовые образцы легированных сталей. В табл. 8 приведены некоторые резуль таты этих испытаний. Стойкость рельсов оценивалась числом циклов нагрузки, выдержанных образцом до появления трещи
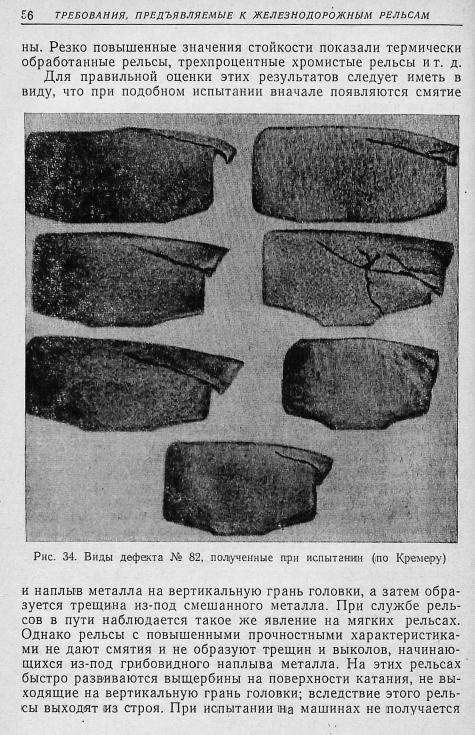
Таблица 8
СТОЙКОСТЬ РАЗЛИЧНЫХ РЕЛЬСОВ ПРОТИВ ОБРАЗОВАНИЯ ДЕФЕКТА № 82 ПРИ ИСПЫТАНИЯХ НА МАШИНЕ С ПОДВИЖНОЙ НАГРУЗКОЙ, РАВНОЙ 22,7 m
|
|
|
|
|
|
|
|
|
|
|
|
|
а |
|
|
|
|
|
|
|
|
|
|
|
|
|
о _ |
|
|
|
Химический состав стали, %. |
|
|
Механические свойства |
Ч Or |
||||||
|
|
|
|
|
х ^ я |
||||||||
|
|
|
|
|
|
|
|
Твер- |
|
|
|
|
= - Я |
Рельсы |
|
|
|
|
|
|
|
|
|
|
|
tf 5 « |
|
|
|
|
|
|
|
|
дость |
|
|
|
|
„ “ а |
|
|
|
|
|
|
|
|
|
ИВ |
|
|
|
|
8 >»>* |
|
|
С |
Мп |
Si |
Сг |
N1 |
Мо |
СТ$ |
°ь |
5, % |
Ф. % |
Лайм |
|
|
|
|
«я |
||||||||||
|
|
|
|
|
|
|
|
|
кг/мм* |
кг/мм2 |
|
|
D* я o.s |
Углеродистые, с пламенной закалкой по |
0 ,77 |
0 ,9 0 |
0,20 |
|
|
|
338 |
|
|
|
|
0,682 |
|
верхности ....................................................... |
|
_ |
|
|
|
|
|
|
|||||
|
|
|
|
|
|
|
|
|
|
|
|
|
|
Кремнистые ....................................................... |
|
0 ,7 5 |
0 ,7 5 |
0 ,45 |
— |
— |
— |
288 |
— |
■— |
— |
— |
0 ,7 2 0 |
М едистые........................................................... |
|
0,71 |
0 ,8 0 |
— |
— |
— |
— |
273 |
5 2 ,6 |
9 5 ,5 |
7 ,5 |
16,6 |
0,8 1 3 |
Кремнемолибденовые....................................... |
|
0 ,7 3 |
0 ,8 9 |
1,96 |
— |
— |
0 ,4 9 |
351 |
8 3 ,9 |
102,3 |
2 , 3 |
9 ,3 |
0,820 |
Обычные .......................................................... |
|
0 ,7 6 |
0,81 |
0 ,1 4 |
— |
— |
— |
267 |
5 0,0 |
9 5,0 |
8 ,0 |
14,0 |
0,9 5 5 |
Закаленные с прокатного |
нагрева . . . . |
— |
— |
— |
— |
— |
— |
335 |
— |
— |
— |
— |
0 ,9 9 4 |
Марганцовистые, термически обработанные |
0 ,5 9 |
1,36 |
0 ,1 4 |
— |
— |
— |
372 |
8 0 ,2 |
114,0 |
8 ,5 |
2 5 ,5 |
1,127 |
|
Молибденовые................................................... |
|
0 ,7 5 |
0 ,7 9 |
— |
— |
' — |
0 ,3 4 |
314 |
7 4 ,7 |
111,1 |
8 ,0 |
3 1 ,0 |
1,187 |
Марганцовистые, термически необрабо |
|
|
|
_ |
_ |
|
|
|
|
|
|
|
|
танные ........................................................... |
|
0 ,5 9 |
1,36 |
0 ,1 4 |
. |
262 |
4 8 ,5 |
8 9 ,3 |
11,0 |
3 2 ,5 |
1,221 |
||
Марганцовомолибдеиовые, термически не |
|
|
|
|
_ |
|
|
|
|
|
|
|
|
обработанные ............................................... |
|
0 ,6 0 |
1,35 |
0 ,1 2 |
— |
0 ,3 7 |
265 |
6 4 ,0 |
8 7,5 |
10,0 |
3 4 ,3 |
1,250 |
|
Английские, сорбитизированные по методу |
0 ,5 6 |
1,14 |
0 ,1 5 |
— |
— |
|
235 |
4 5,0 |
8 6,0 |
10,8 |
2 8 ,3 |
1,557 |
|
Занберга ....................................................... |
|
— |
|||||||||||
|
|
|
|
|
|
|
|
|
|
|
|
|
|
Легированные, термически обработанные |
0 ,2 4 |
1,28 |
0 ,20 |
0 ,6 4 |
0 ,5 7 |
0 ,3 4 |
331 103,0 |
113,0 |
10,8 |
6 4 ,7 |
2,742 |
||
X ром и сты е....................................................... |
|
0,31 |
0 ,6 6 |
0 ,32 |
3 ,1 3 |
— |
— |
374 |
9 1 ,2 |
121,0 |
9 , 5 |
3 5 ,3 |
3,136 |
Углеродистые, термически |
обработанные |
0 ,7 8 |
0 ,8 6 |
— |
— |
— |
— |
360 |
8 5 ,5 |
126,5 |
7 ,6 |
3 5 ,2 |
3,425 |
П р и м е ч а н и е . В медистых рельсах содержится 1,11% Си.
58 ТРЕБОВАНИЯ, ПР ЕДЪ ЯВ ЛЯ ЕМЫЕ К ЖЕ Л ЕЗ Н ОД ОР ОЖ Н ЫМ РЕЛЬСАМ
выщербин на поверхности катания, и поэтому может сложиться неправильное представление о действительной стойкости раз личных рельсов в пути. Очевидно, что способ испытания должен быть изменен таким образом, чтобы можно было получить обе эти разновидности дефекта № 82. Без этого оценка работоспо собности рельсов будет всегда односторонней.
По данным табл. 7, рельсы Р-43 снимаются с пути из-за де фекта № 82 в очень небольшом количестве. Сложилось мнение, что это объясняется некоторыми особенностями профиля рель сов Р-43, химическим составом стали этих рельсов и благоприят ным сочетанием механических свойств. Однако следует при знать такое мнение недостаточно обоснованным. Профиль рель сов Р-43 ничем принципиально не отличается от профиля Р-50 и даже по абсолютным размерам близок к нему. Содержание уг лерода в рельсах Р-43 ниже, чем в рельсах Р-50 и Р-65.
Для выяснения влияния содержания углерода в рельсовой стали на развитие дефекта № 82 были изготовлены сначала опытные партии малоуглеродистых рельсов с содержанием уг лерода 0,64—0,70%. Наблюдения за работой этих рельсов в пути не обнаружили никаких преимуществ малоуглеродистых рельсов. Они показали сильное смятие, особенно на участках с
затяжными подъемами пути. Вместе с тем |
развитие дефекта |
№ 82 на этих рельсах происходило так же |
интенсивно, как и |
на обычных. |
|
Результаты опыта были настолько убедительны, что прокат ка малоуглеродистых тяжелых рельсов была прекращена. Та ким образом, никаких особенностей в свойствах рельсов Р-43,
которые могли бы объяснить малое |
поражение |
их |
дефектом |
|
№ 82, не было обнаружено. |
объяснение стойкости |
рельсов |
||
Было предложено другое |
||||
Р-43. Как правило, при замене |
рельсов Р-43 рельсами Р-50 или |
|||
Р-65 изменяется и характер верхнего |
строения |
пути. |
Обычно |
песчаный балласт заменяется щебеночным, увеличивается число шпал на 1 км пути. Кроме этого, рельсы Р-50 и, особенно Р-65, имеют больший момент инерции поперечного сечения, чем рель сы Р-43. В результате всех этих изменений жесткость пути воз растает, и соответственно растет стёпень динамического воздей ствия подвижного состава на рельсы. Удары становятся более жесткими. Контактные напряжения на поверхности контакта колеса с рельсом практически не зависят от момента инерции профиля рельсов. Они определяются только нагрузкой и вели чиной контактной площадки. Последняя при прогибах рель сов резко возрастает, и поэтому на более слабых рельсах Р-43 и мягком песчаном основании контактные напряжения меньше. В результате этого меньше и повреждения рельсов. Такое пред положение заслуживает внимательного изучения. Возможно,
ДЕ ФЕ КТ Ы РЕЛЬСОВ |
59 |
что уменьшение жесткости пути значительно снизит |
изъятие |
рельсов по дефекту № 82, При этом, конечно, имеется |
в виду |
не возврат к песчаному балласту и рельсам малого веса, а соз дание новых конструкций крепления рельсов к шпалам, вклю чающих упругие амортизирующие элементы, способные смяг чить жесткость ударов неподрессоренных масс о рельсы.
Однако главная причина малого изъятия рельсов Р-43 по де фекту № 82 состоит в другом. Как указывалось выше, этот де фект начинает интенсивно развиваться после пропуска 120— 150 млн. тгруза. Но гораздо раньше на рельсах Р-43 возникают другие дефекты. Очень большое количество рельсов Р-43 сни мается с пути из-за дефектов 1, 3, 6, 7-й групп. Таким образом, рельсы выходят из строя еще до того, как на них начал бы раз виваться дефект № 82. При этом следует иметь в виду, что об щий съем с пути рельсов Р-43 во много раз превышает съем бо лее тяжелых рельсов, и поэтому применение легких рельсов не облегчит положение на железных дорогах, а, наоборот, сделает невозможной эксплуатацию пути.
Из сказанного вытекают следующие возможности борьбы с дефектом № 82, распространение которого на железных доро гах Советского Союза в настоящее время создает трудности для транспорта. Прежде всего необходима реконструкция особенно трудных участков пути с кривыми радиусом меньше 600 м. За тем нужно ввести обязательную смазку внешних рельсов в кри вых посредством путевых лубрикаторов. Необходима разработ ка новых систем крепления пути с упругими амортизаторами.
Рельсовая сталь при высоких прочностных характеристиках должна обладать определенным запасом пластичности. По мнению некоторых специалистов, здесь необходимы стали, ко торые при прочности порядка 140—150 кг/мм2 обеспечивали бы при разрыве удлинение 10—12% и сужение площади попереч ного сечения около 30%. Ясно, что разработка такой стали и особенно внедрение ее в производство представляют исключи тельные трудности, и вряд ли эта задача может быть решена до тех пор, пока на рельсопрокатных заводах не будут построены цехи полной термической обработки рельсов.
Введение термической обработки углеродистых рельсов бу дет способствовать исчезновению той разновидности дефекта № 82, образованию которой предшествуют смятие и наплыв ме талла на боковую вертикальную грань головки. Это наиболее опасный вид дефекта вследствие склонности его к переходу 'в поперечные изломы типа дефекта № 64.
На прямых участках пути выщербины на поверхности катания или исчезнут совсем, или будут крайне редким явлением, а на кривых радиусом 600 м и больше количество выщербин будет в 3—4 раза меньше, чем наблюдается сейчас на необработанных