
книги из ГПНТБ / Полухин П.И. Прокатка и термическая обработка железнодорожных рельсов
.pdfО ПЕРСПЕКТИВАХ ТЕРМИЧЕСКОЙ ОБРАБОТКИ РЕЛЬСОВ |
395 |
Среднемарганцовистые рельсы не были подвергнуты объем ной закалке. Возможно, что вследствие повышенной прокаливае мое™ стали при объемной закалке получились бы интересные результаты. Поверхностная закалка среднемарганцовистых рельсов вряд ли может быть рекомендована.
11.О перспективах термической обработки рельсов
Кнастоящему времени имеется уже значительное число ис следований по термической обработке рельсов. Все методы тер мической обработки рельсов можно разбить на две большие группы: 1) поверхностной закалки и 2) объемной закалки.
Поверхностную закалку рельсов в различных ее вариантах исследовали как в Советском Союзе, так и за границей, причем раньше, чем объемную закалку. Начало исследования объемной закалки относится к пятидесятым годам. По многим причинам поверхностная закалка и до настоящего времени привлекает осо бенное внимание исследователей. Главной из них является не обоснованная боязнь хрупкости объемно закаленных рельсов.
Несмотря на то, что во всех опытах эти рельсы имели более вы сокие механические свойства по сравнению с необработанными, понятие «закаленный» рельс вызывало представление о хрупкой стали со структурой мартенсита. Это отразилось в технических условиях на поставку рельсов с закаленными концами и рельсов, обработанных по всей длине. Толщина закаленного слоя по макроструктуре не должна была превышать 4—6 мм, а зона за каленного металла должна заканчиваться у верхних закругле ний головки рельсов. Этим подчеркивалось желание сохранить большую часть сечения необработанной, т. е. якобы более пла стичной по сравнению с сорбитной термически обработанной зо ной. Несостоятельность подобных представлений ясна. Такие требования со стороны Министерства путей сообщения надолго задержали систематическое изучение закалки рельсов.
Кроме этого, методы поверхностной закалки проще, чем ме тоды объемной закалки. Долгое время считали рельсы дешевой некондиционной «торговой» продукцией, которую экономически нецелесообразно подвергать полной термической обработке, на пример, закалке с отпуском.
И, наконец, не было изучено напряженное состояние рельса под нагрузкой колес. Недостаточно были изучены концентрация напряжений на входящих углах (выкружки под головкой) и в шейке, а также поперечные изгибающие моменты в подошве, приводившие к раскрытию волосовин и т. д.
Многие авторитетные исследователи до настоящего времени считают, что рельс достаточно прочен и нужно только упроч нить поверхность катания его против смятия, истирания и обра
396 ТЕРМИЧЕСКАЯ ОБРАБОТКА РЕЛЬСОВ
зования выщербин. Нам кажется, что такой взгляд основан на недоразумении. Если в настоящее время положение с большин ством дефектов, кроме1явлений контактной усталости, является более или менее благополучным, то происходит это только пото му, что сильно возросли вес 1 пог. м рельса, толщина шейки и подошвы и значительно повысилось в стали содержание угле рода.
Однако опыты по термической обработке легированных рель сов показывают, что, для того чтобы получить удовлетворитель ные свойства обработанного слоя, необходимо снижать содер жание углерода в рельсовой стали. В результате этого, при по верхностной обработке головки резко снизится прочность шейки и подошвы и неизбежно возникнут дефекты седьмой и четвертой групп.
Следует отметить, что необработанная сталь работает зимой при температурах ниже порога хладноломкости. Кроме того, в легированных рельсах сравнительно жесткая закалка поверх ности путем обрызгивания водой вызовет чрезмерно высокие на пряжения и в закаленной зоне. В углеродистых рельсах необра ботанный металл шейки и подошвы окажется неработоспособ ным в пути при возрастании нагрузки на ось скоростей движе ния и грузонапряженности дорог.
Наблюдения за службой в пути термически обработанных рельсов показали, что поверхностно закаленные рельсы не сво бодны от дефектов второй, шестой и седьмой групп. Они пора жаются дефектами этих групп даже в большей степени, чем не обработанные рельсы. Это понятно, так как металл рельса в ме стах возникновения этих дефектов совершенно не упрочнен, а остаточные напряжения выше, чем в необработанном рельсе.
Объемная закалка всего сечения рельса будет необходимой хотя бы потому, что, возможно, будут применять рельсы мень шего веса. Так как механические свойства стали в обработан ном состоянии практически одинаковы при всех методах закал ки, то не видно никакого смысла в том, чтобы оставить боль шую часть сечения рельса необработанной и не использовать то повышение прочностных свойств и пластичности стали, которые обеспечивает термическая обработка.
Таким образом, следует ожидать, что в условиях эксплуата ции рельсы, обработанные по всему сечению, будут работать лучше, чем рельсы с поверхностной закалкой.
Рассмотрим затруднения, встречающиеся при выполнении термической обработки и особенно вопрос о напряжениях, воз никающих в рельсах. При поверхностной закалке водой, хотя бы даже при прерывистой закалке, появляются значительные на пряжения первого рода, вызывающие большое искривление рельсов. Как в опытах на заводе А, так и в практике работы за
О ПЕРСПЕКТИВАХ ТЕРМИЧЕСКОЙ ОБРАБОТКИ РЕЛЬСОВ |
397 |
вода Г стрела изгиба (подошва вогнута) обработанных рельсов достигает до 0,5 м. .
Значительные местные напряжения возникают также около всевозможных концентратов напряжений. Так, что на заводе Г нельзя было закаливать рельсы с просверленными болтовыми отверстиями, так как около них образуются трещины. В опытах на заводе А также приходилось закрывать отверстия специаль ными болтами с. гайками. На заводе Г на переднем торце рельса в закалочной машине образовывались трещины, которые в даль нейшем удаляли посредством фрезерования специально остав ленного припуска.
Все это свидетельствует о высоких напряжениях в рельсах. Это понятно, так как глубина проникновения термического воз действия велика. Она достигает 25—30 мм от поверхности ката ния. Большой объем металла, уменьшающий .свою длину при первоначальном охлаждении и увеличивающий ее при переходе к бездиффузионным превращениям, способен вызвать большие напряжения вовсем объеме рельсов.
Как показали опыты на заводе Г, полная объемная закалка рельсов в воде невозможна, так как приводит к разрушению их по шейке. Закалка в масле вызывает значительно меньшие на пряжения. При изготовлении опытных партий рельсов, закален ных в масле, хотя и наблюдалось непостоянное и. иногда боль шое коробление, но ни в одном случае не было'обнаружено тре щин в рельсах.
Однако практическое проведение закалки в масле вызывает сомнения вследствие больших масштабов масляного хозяйства, потребного при обработке рельсовой продукции современного крупного завода. Первые примерные расчеты показали, что ко личество масла в системе должно быть около 500—600 т. Для этого нужны маслоохладительные установки, запасные емкости и пр. Все это требует больших площадей, усложняет схему об работки рельсов. В условиях действующих заводов не удается разместить все необходимое оборудование и правильно органи зовать поток рельсов.
Поэтому следует считать, что наиболее целесообразной бу дет закалка рельсов обрызгиванием пароводяной или водовоз душной смесью. В опытах Сибирского института металлов при правильном подборе количества воды для охлаждения отдель ных частей профиля-рельс при закалке оставался прямым. Ис кривление рельсовначинается только при отпуске, причем ве личина этого искривления незначительна.
Таким образом, наиболее перспективной, на наш взгляд, язляется закалка в роликовых машинах типа завода Г, но с об рызгиванием частей рельса мелкой водовоздушной смесью. Количество воды должно быть рассчитано, исходя из площади
398 |
ТЕРМИЧЕСКАЯ ОБРАБОТКА РЕЛЬСОВ |
поперечного сечения рельсов и скорости охлаждения отдельных элементов профиля. Такой способ охлаждения рельсов необхо димо тщательно'изучить для выбора правильных условий про цесса. При проектировании и постройке рельсотермических це хов на заводах необходимо предусмотреть возможность осу ществления такой объемной закалки. Это требование является обязательным.
12.Термическая обработка рельсов на отечественных заводах
До 1960 г. только на заводе Г построена промышленная ус тановка для поверхностной закалки рельсов по всей длине. Схема расположения оборудования показана на рис. 196. От
Рис. 196. Схема расположения оборудования для закалки рельсов на заводе Г:
1 — роликовая печь; 2 — шлеппера для выдачи рельсов; 3 — кантова тель; 4 — закалочная машина; 5 — машина для горячей гибки рельсов;
5 — холодильник
пил рельсы поступают по рольгангу к печи охлажденными до 200—300°. Рельсы набирают партиями по 6—8 шт. и направляют
впечь (ем. рис. 179). В печи рельсы нагреваются до 800—850°,
азатем выдаются по одной штуке из печи через щелевое окно
вбоковой стенке.
Нагретый рельс движется по рольгангу, попадает в канто ватель, где кантуется головкой вниз, и в таком положении за дается в закалочную машину. Закалочная машина (рис. 197) имеет общую длину 21,98 м и состоит из 22 клетей, из них 11с приводными роликами и 11 с холостыми. Продвигаясь в маши не, рельсы проходят над закалочными аппаратами, расположен ными между клетями.
Конструкция закалочного аппарата показана на рис. 197. Вода из отверстий закалочного аппарата омывает поверхность катания рельса и небольшую часть боковых вертикальных гра-
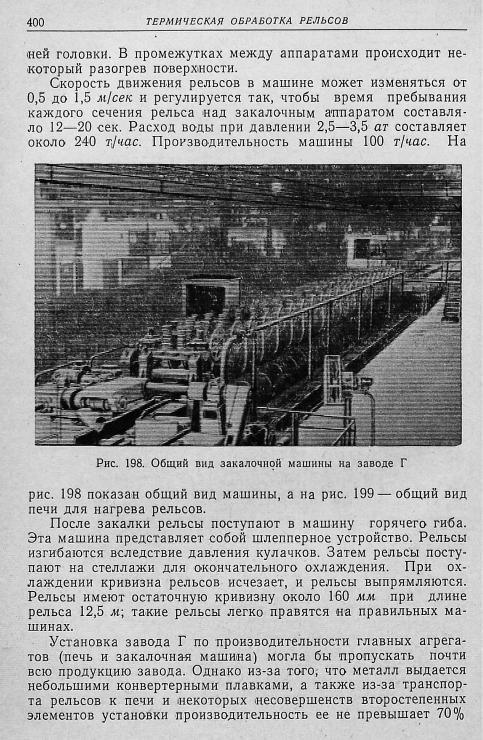
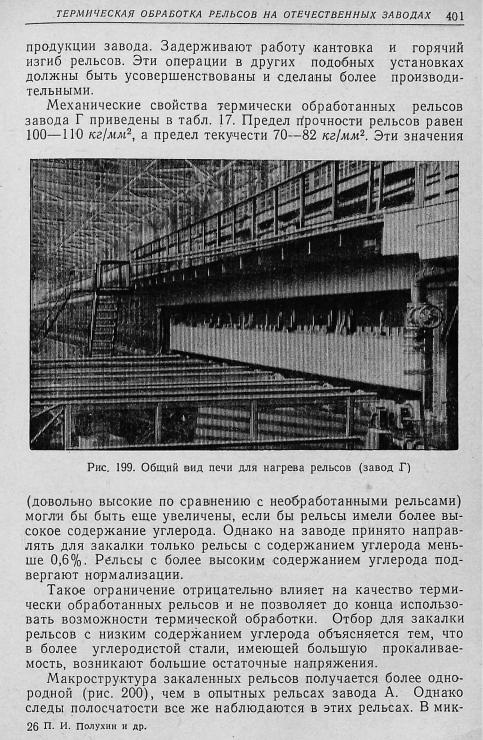
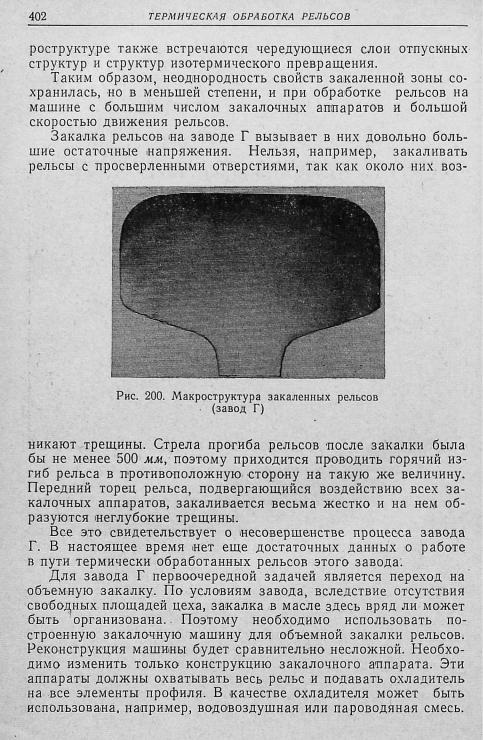
4 0 4 |
т е р м и ч е с к а я о б ра б о тк а р е л ь с о в |
и являются короткими проходными печами с верхним и нижним расположением горелок. Горелки представляют собой удлинен ные коробки . со многими отверстиями, направляющими пламя
Рис. 201. Установка для скоростного нагрева рельсов на заводе В
так, чтобы оно не попадало непосредственно в нагреваемый рельс. В каждой секции имеется шесть верхних и шесть нижних горелок, причем верхние горелки более мощные. В дымоходе каждой секции установлен рекуператор. Как показали опыты, рельс нагревается до закалочной температуры, проходя десять секций за десять минут.