
книги из ГПНТБ / Белоусов Н.Н. Термическая обработка отливок из алюминиевых сплавов (стенограмма лекции, прочитанной в ЛДНТП на занятии семинара ленинградских литейщиков)
.pdf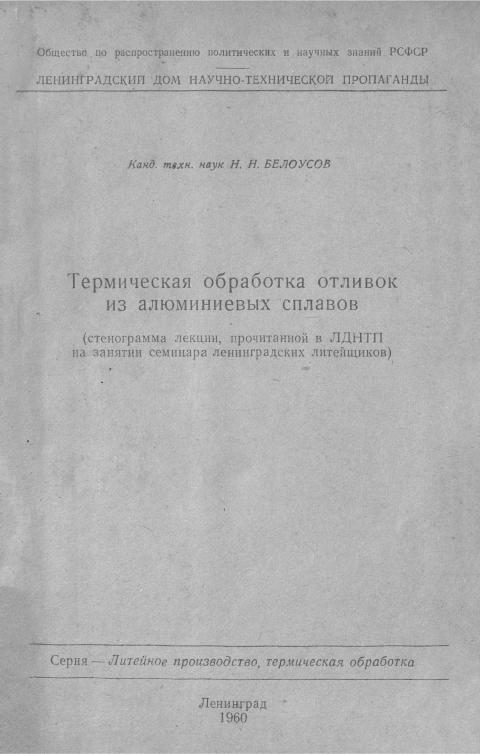
-**4waav«0aifl> -*
|
roc ny w |
j |
'. |
. АУЧН»-Т = Хг - ~*Я |
|
j |
БИБЛИОТЕКА ОСО* |
Ai
Ш 63
ВВЕДЕНИЕ
В последние годы в народном .хозяйстве нашей страны все более широкое применение получают алюминиевые сплавы. Семи летним планом предусмотрено увеличение производства алюминия
в2,8—3 раза, что будет обеспечено главным образом за счет ввода
встрой новых мощных электростанций, развития производства
глинозема прогрессивными методами и др. Среди алюминиевых сплавов большую группу составляют литейные сплавы.
Для получения требуемых показателей механических свойств многие литейные алюминиевые сплавы подвергаются термической
обработке, которая имеет ряд важных особенностей по сравнению с термической обработкой деформируемых сплавов. Эти особен ности, связанные с составом и строением литых сплавов, еще недо статочно исследованы и поэтому термическая обработка относится к одной из наименее разработанных и изученных областей техно логии производства отливок из алюминиевых сплавов. Литератур
ные данные по этому вопросу весьма разноречивы.
ГОСТ 2685—44 содержал указания по режимам термической обработки включенных в него сплавов, однако в ГОСТ 2685—53 эти рекомендации отсутствуют. На разных заводах, зачастую для одних и тех же литейных алюминиевых сплавов, устанавливаются пазличные режимы термической обработки. На многих заводах
применяются чрезмерно длительные выдержки при нагреве отливок под закалку, что приводит к нерациональному расходованию электроэнергии и удлиняет цикл производства литых деталей.
В последние годы в СССР изысканы новые композиции высоко прочных и коррозионноустойчивых литейных алюминиевых спла вов, не вошедшие в ГОСТ 2685—53. Среди них, по нашему мне нию., наиболее перспективными являются сплавы АЛЮ [1], АЛ8-У (АЛ8 улучшенный) и АМг7Л. Последний разработан специально для литья под давлением.
Эти новые сплавы подвергаются термической обработке по специальным режимам.
Автором в течение ряда лет проводились систематические исследования по установлению оптимальных режимов закалки и искусственного старения литейных алюминиевых сплавов несколь
3
ких марок. Эти исследования закончились разработкой ускорен ных режимов термической обработки отливок, успешно опробован ных и внедренных на ряде заводов [2].
В настоящей работе содержатся некоторые общие сведения о теории и практике термической обработки литейных алюминие вых сплавов, а также основные результаты исследований автора
вэтой области.
Всвязи с отсутствием в технической литературе исчерпываю
щих данных о процессах естественного и искусственного старения высокопрочных литейных алюминиево-магниевых сплавов (из-за
малой изученности процессов), в брошюре приводятся некоторые
результаты исследований автора по этому вопросу.
Практические рекомендации по некоторым вопросам техноло гии термической обработки отливок имеют целью помочь производ ственникам предотвратить пороки литых деталей из алюминиевых сплавов, обусловленные недоброкачественнойтермической обра боткой.
1. ОБЩИЕ СВЕДЕНИЯ О ТЕОРИИ И ПРАКТИКЕ ТЕРМИЧЕСКОЙ ОБРАБОТКИ ЛИТЕЙНЫХ АЛЮМИНИЕВЫХ СПЛАВОВ
Принципиальная возможность получения эффекта от термиче ской обработки алюминиевых сплавов определяется характером диаграмм состояния этих сплавов, а именно наличием области твердых алюминиевых растворов, концентрация которых увели чивается с повышением температуры.
Характерным примером в этом отношении является диаграмм;!
состояния алюминий — медь в ее начальной области, относящейся к высокой концентрации алюминия (рис. 1).
Диаграммы состояния двойных сплавов алюминий — кремний
(рис. 2) и алюминий — магний (рис. 3) также свидетельствуют
.о принципиальной возможности термической обработки этих спла
вов. Однако эффект от закалки и старения двойных алюминиевокремниевых сплавов практически ничтожен. Увеличение показате лей механическйх свойств относительно богатых кремнием сплавов (силуминов) после их термической обработки достигается в основ ном за счет процессов образования так называемого простого
упрочнителя — силицида магния (MgaSi) при добазке к силумину
магния (рис. 4), |
а также упрочнителя более сложного химического |
состава — фазы |
W — при добавке к силумину магния совместно |
с медью. |
|
Термически обрабатываемые силумины, в состав которых вхо дят вышеуказанные фазы-упрочнители, обычно называются спе циальными силуминами.
Типичная микроструктура модифицированного силумина до эвтектического состава (сплав марки АЛ4, см. табл. !) изобра
4
жена на рис, 5, а литого в кокиль сплава АЛ9 — на рис. 6. Под влиянием термической обработки (закалки и старения) микрэ-
Рис. 1. Диаграмма состояния сплавов системы А1—Си.
Рис. 2. Диаграмма состояния сплавов системы А1—Si.
структура силуминов не подвергается существенным изменениям:
после длительного нагрева под закалку наблюдается лишь неко торая коагуляция и сфероидизация зерен кремния (рис. 7).
5
Рис. 3. Диаграмма состояния сплавов системы А1—Mg.
Рис. 4. Диаграмма состояния .
псевдобинарных сплавов системы
Al—MgoSi.
Мимический
сплава | |
|
Марка |
Mg |
|
|
|
|
|
|
|
|
|
|
Таблица 1 |
|
состав |
алюминиевых _литейных сплавов |
ГОСТ 2685—53), применительно к отливкам, из вторых |
|
|||||||
|
составлены рекомендации о режимах |
термической' обработки |
|
|
|
|
||||
|
|
|
|
|
|
Химический с |
о с |
т а в, в % |
|
|
Основные компоненты |
|
|
Примесей не |
бол е е__________ ______ |
||||||
|
|
|
|
Ее |
|
|
|
|
Сумма учи- |
|
|
|
|
прочие компо ненты |
|
|
Ni |
Ti |
ТЫКЯРМЫТ |
||
|
|
|
3 к |
Д |
Si Мп Си Zn Sn |
|||||
|
|
|
3 |
Д |
||||||
51 |
Мп |
Сп |
|
|
Mg |
эимесей |
к
|
|
|
|
|
|
|
N1 |
Ос- |
|
|
|
|
|
|
|
|
|
|
|
|
|
|
|
АЛ1 |
1,25-1,75 |
|
— |
■ — |
3,75—4,5 |
2,251,75- |
таль- |
|
0,8 |
0,8 |
— — 0,7 — — |
0,3 |
— |
— |
— |
1,5 |
1,5 |
— |
|||||
|
ное |
|
|||||||||||||||||||||
АЛ2 |
— |
10,0-13,0 |
— |
— |
|
|
■ |
0,8 |
1,0- |
1,5 |
— |
— |
0,5 |
0,8 |
0,3 |
— |
— |
— |
2,2 |
2,3 |
2,8 |
||
АЛЗ |
0,2-0,8 |
4,0—6,0 |
0,2—0,8 |
1,5-3,5 |
|
— |
» |
|
1,0 |
1,2 |
1,5 |
— |
— |
— |
— |
0,3 |
0,01 |
— |
— |
1,3 |
1,5 |
1.8 |
|
АЛЗВ |
0,2—0,8 |
4,0 |
6,0 |
0,2-0,8 |
1,5-3,5 |
|
— |
» |
|
1,1 |
1,3 |
1,5 |
— |
— — |
— |
0,5 |
— |
0,5 |
— 2,0 2,1 |
2,3 |
|||
АЛ4 |
0,17—0,3i |
8,0 - 10,5 |
0,25 - 0,5 |
— |
|
— |
п |
0,6 |
0,9 |
1.2 |
— |
— |
— |
0,3 |
0,3 |
0,01 |
— 0,15 |
1,1 |
1,4 |
1,7 |
|||
АЛ4В |
0,2- 0,1 |
8,0-11,о |
0,2—0,5 |
—. ■ |
|
— |
я |
0,9 |
1,2 |
1,5 — — — 1,0 |
0,5 |
— |
0,3 |
— |
2,6 |
2,8 |
3,0 |
||||||
АЛ5 |
0,35-0,6 |
4.5 |
5,5 |
— |
1,0-1,5 |
|
— |
я |
0,6 |
1,0 |
1,5 |
— |
— |
0,5 |
— |
0,3 |
0,1 |
-г- |
Ti |
1,0 |
1,3 |
1,7 |
|
|
|
|
|
|
|
— |
|
— |
|
0,20 |
|
2,0 |
— |
||||||||||
АЛ6 |
'■— |
4,5 |
6,0 |
— |
2,0—3,0 |
|
— |
я |
|
1,1 |
1,4 |
— |
0,1 |
— |
0,3 |
0,3 |
— . — |
1,8 |
|||||
|
|
|
|
|
|||||||||||||||||||
АЛ7 |
— |
|
— |
— |
4,0-5,0 |
|
— |
я |
|
1,0 |
1,0 |
■—• |
0,1-3 |
1,2 |
— |
— |
0.3 |
— |
— |
— |
2,2 |
2,2 |
• — |
|
|
|
— |
||||||||||||||||||||
АЛ7В |
— |
|
— |
— |
3,0 5,0 |
|
— |
» |
|
1,1 |
1,3 |
— 0,03 |
1,5 |
0,5 |
— |
0,5 |
— |
0,3 |
4,0 |
4,2 |
—• |
||
|
|
|
-Ti |
||||||||||||||||||||
АЛ8 |
9,5 11,5 |
|
—... |
— |
— |
. |
— |
я |
0,3 |
0,3 |
— |
— |
0,3 |
0,1 |
0,3 |
0,1 |
— |
— |
1,1 |
1,1 |
— |
||
|
|
|
|
|
|
|
|
|
|
|
|
|
|
|
|
|
|
|
|
0,7 |
|
|
|
|
|
|
|
|
|
|
|
|
|
|
|
|
|
|
|
|
|
|
|
Be |
|
|
|
|
|
|
|
|
|
|
|
|
|
|
|
|
|
|
|
|
|
|
|
0,07 |
|
|
|
АЛО |
0,2—0,4 |
6,0-8,0 |
— |
— |
|
— |
я |
0,6 |
1,0 |
1,5 |
— |
— |
0,5 |
0,2 |
0,3 |
0,01 |
— |
— |
1,0 |
1,4 |
1,9 |
||
АЛ9В 0,2—0,5 6,0-8,0 |
—• |
— ■ |
|
— |
я |
|
1,1 |
1,2 |
— |
— |
— |
0,6 |
1,5 |
0,5 |
— 0,3 — 3,7 3,8 |
— |
|||||||
АЛ12 |
— |
— |
— |
9,0-11,0 |
|
— |
• |
|
1,0 |
1,2 |
— |
— |
1,0 |
— |
— |
0,5 |
— |
0,5 |
— |
2,8 |
3,0 |
—• |
|
|
В обозначениях марок буква «В» указывает, что отливки изготовляются из вторичных литейных алю |
|
|||||||||||||||||||||
|
миниевых |
сплавов в |
чушках |
по ГОСТ |
1583—53. |
В |
графах |
содержания |
примеси |
железа буквы |
указывают |
|
|||||||||||
|
способ литья: |
3 — в |
землю, |
К ■— в кокиль, |
Д — под |
давлением. |
|
|
|
|
|
|
|
|
|
|
|
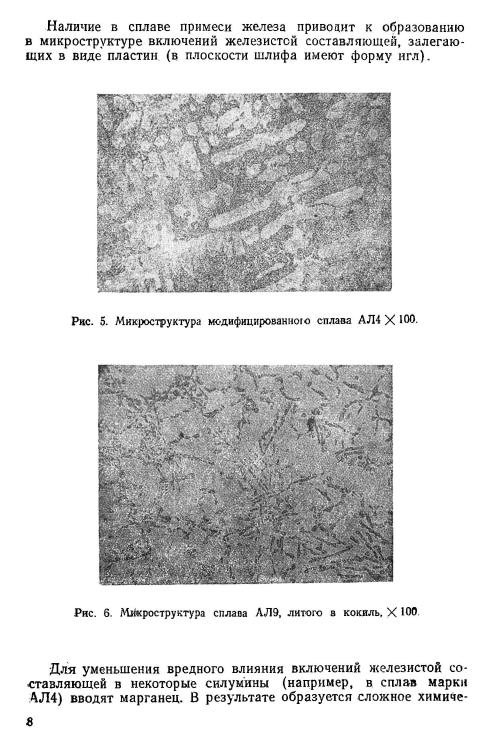
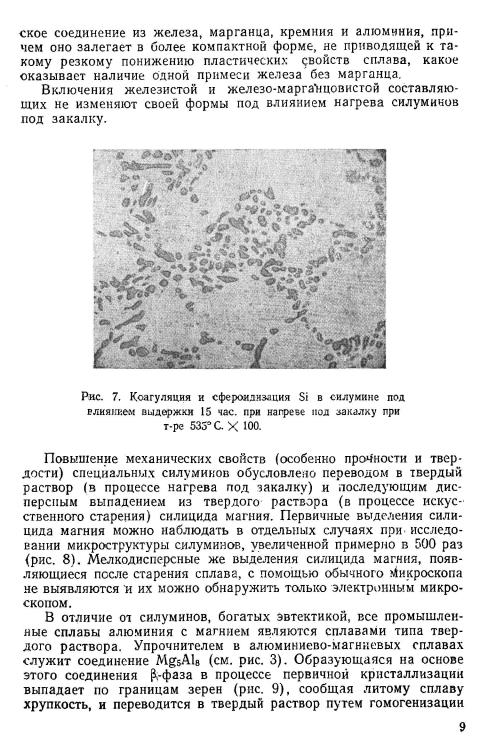
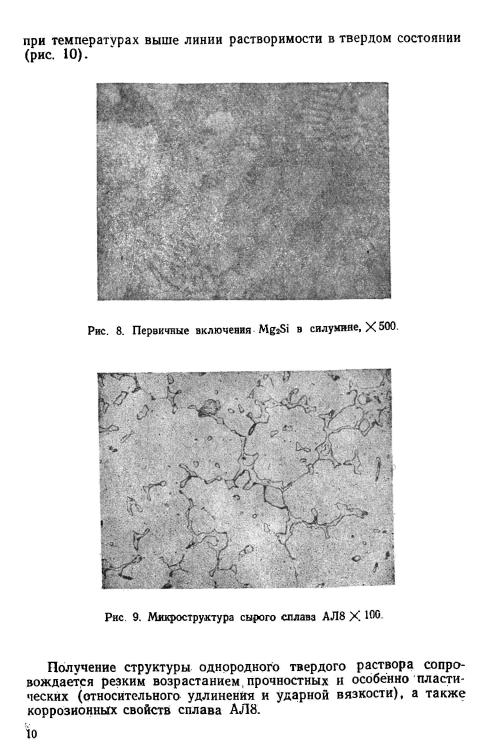