
книги из ГПНТБ / Иванов И.А. Технология легких бетонов на искусственных пористых заполнителях учеб. пособие
.pdfтовляют на станке конструкции ВНИИЖелезобетопа в вертикальном положении, виброуплотнением с пригрузом. Как показал опыт работы заводов в Минске и
Куйбышеве, из легких бетонов можно |
изготовлять на |
|
порные трубы, рассчитанные на контрольное |
давление |
|
до 15—20 ат. |
|
|
Впервые аглопоритожелезобетонмые |
напорные трубы |
|
методом центрифугирования по технологии, |
разрабо |
танной под руководством И. Н. Ахвердова в |
Институте |
||||
строительства и архитектуры |
Госстроя БССР, |
были из |
|||
готовлены |
в 1965 г. |
|
|
|
|
Опори |
линии электропередачи |
(НЭП) — конструк |
|||
ции, несущие провода и грозозащитные тросы |
воздуш |
||||
ных линий |
электропередачи. |
Железобетонные |
центри |
||
фугированные опоры могут |
быть |
одностоечной |
и пор |
тальной конструкции. Их изготовляют в виде унифици рованных стоек диаметром 560 мм и длиной 22 м, из которых собирают портальные опоры. Центрифугиро вание позволяет получать полые круглого сечения опо ры из жестких легкобетонных смесей, при этом достига ется равномерное уплотнение смеси по всей длине изделия. Вследствие повышенной плотности бетона ар матура в опорах ЛЭП не корродирует, хотя опоры эксплуатируются в тяжелых условиях (подвергаются воздействию блуждающих токов, попеременному замо раживанию и оттаиванию и т. д.). Опоры ЛЭП изготов ляют из керамзитобетона марок 400—500 с применени ем стержневой арматуры из низколегированных сталей
диаметром 12—14 мм. Стоимость |
таких опор на 11 — |
15% ниже, чем опор из тяжелых |
бетонов, а транспорт |
ные расходы меньше на 20—30%. |
|
Конструкции для транспортного строительства
Применение легких бетонов взамен тяжелых весьма эффективно в автодорожных мостах разных.систем, где постоянная нагрузка от массы большепролетных конст рукций достигает 70—80% всей расчетной нагрузки.
По данным И. Г. Иванова-Дятлова, применение лег ких бетонов в пролетных строениях мостов снижает массу конструкций до 30%. В результате этого значитель но снижаются транспортные и монтажные расходы. В ряде случаев рационально сооружать из легких бето нов проезжую часть металлических мостов.
30
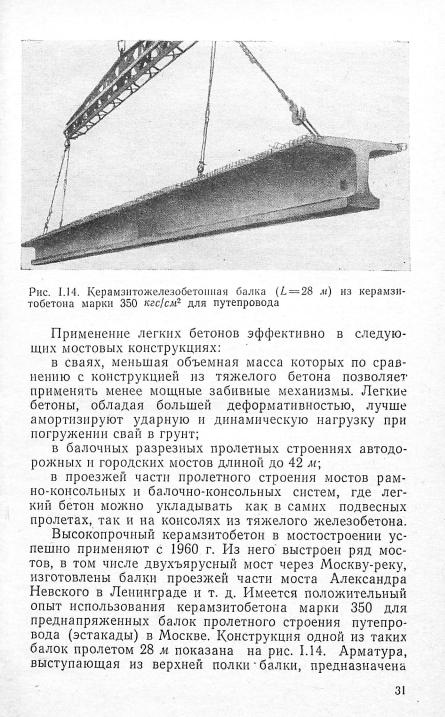
для замонолнчнвання проезжен части эстакады. В Бе лорусской ССР успешно ведется строительство ряда мостов п путепроводов из аглопорптобетоиа марок 250—400. Применение аглопорптобетоиа позволило сни зить общую массу пролетного строения па 25% " сэконо мить 12% высокопрочной арматуры.
Сельскохозяйственное |
строительство |
|
|
|
||
Применение конструкции |
и изделии |
из |
легкого |
бе |
||
тона открывает широкие возможности для |
повышения |
|||||
сборности |
в сельскохозяйственном строительстве. При |
|||||
возведении |
жилых домов и |
производственных зданий |
||||
успешно используют керамзптобетонные |
крупные |
бло |
||||
ки и стеновые панели |
вместо кирпичной |
кладки. |
При |
значительной рассредоточенное™ сельских строек объем
грузоперевозок |
этих |
конструктивных |
элементов на |
|||||||
5 млн.. т меньше, чем кирпича, |
а ежегодная |
потребность |
||||||||
в рабочей силе меньше на 12 тыс. человек. |
|
|
||||||||
ЦНИИЭПсельстрой |
рекомендует изготовлять из ке- |
|||||||||
рамзитобетона |
марки |
50, |
с |
объемной |
массой 900— |
|||||
1100 кг\мъ |
двухслойные |
конструкции |
стеновых |
панелей. |
||||||
Благодаря |
применению |
защитного |
слоя |
|
из |
плотного |
||||
бетона толщиной |
3—5 |
см срок службы |
их в |
условиях |
||||||
агрессивной среды |
возрастает. |
|
|
|
|
|
||||
Из бетона |
на |
пористых |
заполнителях |
изготовляют |
каркасы и плиты покрытия животноводческих помеще
ний. Продолжительность |
возведения |
животноводческих |
||
помещений |
сокращается |
на 10%, |
а |
трудоемкость ра |
бот—на 25%. |
|
|
|
|
Наряду |
с керамзитобетоном |
успешно применяют |
аглопоритобетон для производства аналогичных конст рукций. Предприятия, изготовляющие аглопорит, рабо тают на сырье, которое достаточно распространено. Это позволяет расположить их в непосредственной бли-. зости от объектов сельскохозяйственного строительства.
3. Легкобетонные изделия и конструкции, применяемые за рубежом
За рубежом изготовляют аналогичные пористые за полнители, что и в Советском Союзе, по известные под различными фирменными названиями. Так, на основе зол ТЭС в Англии выпускают зольный гравий, извест-
32
ный под фирменным названием «лайтаг». Его исполь зуют в легких бетонах различного назначения. Из та ких бетонов, например, выполнены конструкции здания аэровокзала Лондонского аэропорта, крупнопанельного административного 17-этажного здания «Кольерс Вуд». Относительно низкий коэффициент теплопроводности бетона на зольном гравии позволил принять толщину стен 23 см.
В течение многих лет в США и Англии из легких бетонов изготовляют пустотелые стеновые камни. Про изводство это считается весьма рентабельным. Напри мер, в Англии объем ежегодно выпускаемых стеновых камней примерно равен объему стен, возводимых из кирпича.
Из материалов I Междун а родного конгресса по лег ким бетонам в Лондоне в 1968 г. известны интересные примеры эффективного использования легких бетонов за рубежом. Так, в США при строительстве железнодо рожной линии через залив Сан-Франциско успешно применяли полые легкобетонные сваи длиной 37 м. Из легкого бетона изготовляют преднапряженные конст рукции большого пролета (балки таврового сечения
пролетом до 30 м, шириной 2,5 м, высотой |
1,5 |
м). Для |
|||
перекрытий и покрытий |
большепролетных |
производст |
|||
венных и общественных зданий в США |
используют |
||||
плиты коробчатого сечения, известные |
под |
названием |
|||
«динакор», их длина достигает 30 м, а высота |
изменя |
||||
ется в зависимости от пролета от 20 до 61 |
см, |
ширина |
|||
2,4 м. |
|
|
|
|
|
Легкие бетоны успешно применяют в дорожных по |
|||||
крытиях, а также |
при |
строительстве |
взлетно-посадоч |
||
ных аэродромных |
полос. Они долговечнее, чем покрытия |
из тяжелого бетона, поскольку имеют более высокую трещиностойкость и лучше выдерживают действие вы сокотемпературных газов.
Зарубежный опыт показывает, что большой экономи ческий эффект может быть получен в результате при менения легких бетонов при строительстве высотных зданий. В Венгерской Народной Республике возводят многоэтажные здания, монолитные стены которых вы полняют в подвижной опалубке из легкого бетона. В Сиднее (Австралия) выстроено жилое здание «Парк Реджис» высотой 140,6 м. В этом здании около 90% объема всех конструкций выполнено из легких бетонов.
3 И. Л. Иванов
Г л а в а II
МАТЕРИАЛЫ ДЛЯ ИЗГОТОВЛЕНИЯ ИЗДЕЛИИ ИЗ ЛЕГКОГО БЕТОНА
1. Основные виды искусственных пористых заполнителей
Заполнитель занимает |
в |
бетоне до 80% |
его объема. |
Получение легкого бетона |
с оптимальными |
свойствами |
|
существенно зависит от вида |
применяемого |
искусствен |
ного пористого заполнителя (см. схему). Свойства запол нителя определяются прежде всего его объемной насып
ной массой. |
Установлены следующие |
марки |
пористого |
||||
заполнителя |
по объемной |
массе (в кг/м3): |
50, |
100, |
150, |
||
200, 250, 300, 350, 400, 450, 500, 600, 700, 800, |
900 и |
1000. |
|||||
Для песка принята |
дополнительная |
марка |
1200 |
кг/м3. |
|||
По химическому |
составу |
пористые |
заполнители |
раз |
деляют на кислые и основные. Они могут иметь различ ное соотношение стекловидной и кристаллической фаз. Слагающее их вещество может находиться почти цели ком в стекловидной фазе (кислые гранулированные до менные шлаки, керамзит из хорошо вспучиваемых глин) или же иметь преимущественно кристаллическую струк туру (некоторые карбонатные заполнители). Такие за полнители, как аглопорит, в равной мере содержат стек ловидную и кристаллическую фазу.
Искусственные пористые заполнители подразделяют ся на мелкие и крупные: к мелким относятся сыпучие материалы (песок) объемной насыпной массой (в вы сушенном состоянии) не более 1200 кг/м3 при крупности зерен до 5 мм, к крупным — зерна от 5 до 40 мм при объ
емной массе не более 1000 |
кг/м3. |
|
|
|
|
|
||
Крупные заполнители для легкого бетона применяют |
||||||||
пористые, мелкие же |
могут быть |
в |
некоторых |
случаях |
||||
плотными. Так, для конструктивных легких бетонов, |
от |
|||||||
которых требуется не только повышенная |
прочность, |
но |
||||||
и возможно меньшая |
деформативность, |
рекомендуется |
||||||
в качестве мелкого заполнителя кварцевый песок. |
|
|||||||
Естественные |
заполнители получают |
из природного |
||||||
пористого камня |
с применением |
механических |
методов |
|||||
переработки (дробления, |
рассева). |
Искусственные |
за |
полнители изготовляют как из минерального сырья, представляющего собой преимущественно осадочные по-
34
Заполнители д л я легких бетонов
Природные |
Искусственные |
Вулканическо го происхож дения: вулканиче ские шлаки; пемза; туфы
Перлит
вспучен ный, песок, щебень
Осадочного проис хождения:
пористые известняки и ракушечники; пески кварцевополевошпатовые; пески известняковые
Глинистый
еланей.
керамзит,
дробленый
песок
|
|
И з плотного сырья |
|
И з |
рыхло |
Из |
расплавов |
|
|
|
|
|
|
го |
сырья |
|
|
|
Естест |
Побочных |
|
|
Металлурги |
|||
|
венного |
продуктов |
|
|
ческие шлаки |
|||
|
|
|
промыш |
|
|
|
|
|
|
|
|
ленности |
|
|
|
|
|
|
|
|
|
|
|
|
Гранулирован |
|
|
|
|
Шлаки |
Шлаки |
|
|
ный шлак |
|
|
|
|
Естественного |
|
||||
|
|
|
отвальные |
топливные |
|
|||
|
|
|
металлур |
(котель |
|
|
|
|
|
|
|
гические: |
ные): |
|
|
|
|
|
|
|
щебень, |
щебень, |
|
|
|
|
|
|
|
песок |
песок |
|
|
|
|
|
|
|
|
|
Глины |
|
Суглинки |
Шлаковая |
Шунгнт |
|
Трепел, |
|
|
|
|
пемза, |
|
|
опока |
|
I |
|
|
щебень, |
||
|
|
|
|
|
Керамзит, |
|
Аглопорит, |
п есок |
|
|
трепель - |
|
|
|
|||
шунгнзит |
|
керамзитовый |
щебень, |
|
||||
ный |
гравий |
|
|
|||||
|
|
|
песок |
|
песок |
|
||
|
|
|
|
|
|
|
роды (реже вулканического происхождения), так и из побочных продуктов металлургической, энергетической; промышленности. Производство их предусматривает при менение более сложных технологических процессов: спе кания, вспучивания н порнзацпи нагретой или расплав ленной массы. Такие заполнители в зависимости от формы зерен п характера их поверхности могут быть гравиевидные п щебневпдные, с закрытой п открытой пористостью.
В процессе производства искусственных заполнителей можно изменять их пористость, прочность и другие свой
ства. |
Учитывая эти |
преимущества, легкие бетоны полу |
|||||||||||
чают |
|
в |
основном |
па |
искусственных |
заполнителях. |
|||||||
К 1975 |
г. объем |
применяемых в |
строительстве |
искусст |
|||||||||
венных |
заполнителей |
|
будет |
в 8 раз |
превышать |
добычу |
|||||||
естественных |
пористых |
заполнителей. |
|
|
|
||||||||
Известны четыре основных метода поризации сырья |
|||||||||||||
при его термической |
обработке: |
|
|
|
|
||||||||
1) |
предварительное |
вспенивание |
исходной |
шихты; |
|||||||||
2) |
выгорание |
органических |
добавок |
пли примесей; |
|||||||||
3) |
вспучивание исходной |
шихты в |
пиропластическом |
||||||||||
состоянии |
газообразными |
продуктами; |
|
|
|||||||||
4) |
вспучивание расплава газо- и парообразными про |
||||||||||||
дуктами. |
|
|
|
|
|
|
|
|
|
|
|
||
Несколько |
обособленное |
положение |
занимает агло |
||||||||||
мерация, |
при |
которой |
порпзацня |
достигается в |
резуль |
тате одновременного действия ряда процессов: выгора ния топлива, испарения влаги, контактного спекания отдельных зерен и лишь частично вспучивания.
Керамзит
Сырьем для производства керамзита служат глинис тые породы, которые должны обладать следующими ос новными свойствами:
1) способностью хорошо вспучиваться в процессе об жига; коэффициент вспучивания Къ =—— {V1{ — объем
вспученной гранулы керамзита; Vc — объем сухой сыр цовой гранулы до обжига) должен быть не менее 2;
2) легкоплавкостью, позволяющей вести обжиг ке рамзита при температуре, не превышающей 1250° С. При нагревании гранул в печи значительная часть наиболее мелких глинистых частиц переходит в расплав. Глинис тое сырье, находящееся в пиропластическом состоянии.
36
должно иметь оптимальную вязкость в том интервале температур, когда наиболее интенсивно выделяются га зообразные продукты. Именно в этот момент в результа те сгорания органических примесей, разложения карбо натов и водосодержащих минералов, а также восстанов
ления окислов железа происходит вспучивание; |
|
|||||
3) определенным интервалом температур между нача |
||||||
лом оплавления |
гранул |
и температурой, при |
которой |
|||
получается |
керамзит |
с |
объемной |
массой |
гранул |
|
0,95 г]смг. |
Этот |
интервал |
вспучивания |
должен |
быть не |
менее 50° С. Если это условие будет соблюдаться, то да же при неизбежных отклонениях температуры обжига от оптимальной не произойдет спекание гранул или ава рия печи.
Сырье, удовлетворяющее всем названным требовани ям, встречается относительно редко. Для улучшения его свойств широко применяют некоторые твердые и жидкие добавки (пиритиые огарки, золы ТЭС от сжигания ка менного угля, соляровое масло, сульфитно-спиртовую бражку и др.).
В основу современной технологии производства ке рамзита положены результаты исследований, которые проводились Н. А. Поповым, С. П. Онацким, В. В. Ере менко, И. А. Гервидсом, А. В. Жуковым, Г. И. Книгпной, Л. К. Петровым, И. Я- Слободяником и др.
Применяют три способа производства керамзита: су хой, мокрый и пластический. Сухой способ используют при наличии плотного глинистого сырья. Глинистые сланцы после дробления и рассева можно сразу на правлять в печь. По мокрому способу глиняную пульпу насосами подают в шламбассейн, а затем в печь. Испа рение большого количества влаги вызывает повышенный расход топлива, поэтому данный способ целесообразно применять при использовании слабо вспучивающегося сырья, в котором необходимо равномерное распределе ние соответствующих добавок. Однако при этом способе трудно добиться высокого коэффициента вспучивания, малой объемной массы и требуемой однородности ке рамзита; форма зерен получается неправильная.
Наиболее распространен пластический способ. Он предусматривает многоступенчатую переработку рыхло го глинистого сырья, в которое в ряде случаев вводят добавки. Подготовленная масса направляется для фор мования сырцовых гранул, которые перед обжигом про-
37
Рис. |
I I . 1. |
Кривая обжига |
керам |
|
зита |
во |
вращающейся печи |
(по |
|
данным |
С. |
П. Онацкого) |
|
ходят сушку в сушильном барабане. В некоторых случа ях процесс сушки может быть совмещен с обжигом во вращающейся печи. Допустимая влажность гранул при подаче их в печь принимается около 20%.
Все три рассмотренных способа различаются лишь подготовкой сырья. Основным технологическим процес сом производства керамзита является его обжиг во вра щающихся печах. При этом весьма важно правильно на значить температурный режим обжига, обеспечивающий необходимую степень вспучивания гранул и максималь ную производительность печей.
Поскольку процесс газовыделения должен совпадать по времени с пиропластпческим размягчением гранул, наиболее интенсивное вспучивание происходит при быст ром подъеме температуры. Однако быстро нагреть гра нулы до температуры вспучивания возможно лишь при соответствующей их подготовке, т.е. предварительной сушке и подогреве. На этих этапах чрезмерно ускорять процесс нецелесообразно. При быстром нагревании мо гут развиваться большие температурные деформации и даже разрушаться гранулы.
Гранулы рекомендуется нагревать постепенно до тем пературы 200—600° С, а затем быстро поднимать темпе ратуру примерно до 1200° С. Теоретическая температура горения топлива во вращающейся печи составляет око ло 2000° С, ее снижение до 1200—1300° С достигается по дачей воздуха с избытком против теоретического в 2 ра за и более. Оптимальный режим обжига гранул во вра щающейся печи, по данным С. П. Онацкого, показан на рис. I I . 1.
Для производства керамзита применяют вращающие ся печи размером 2,5X40 м. В комплекте с соответству ющим оборудованием для подготовки шихты и формовки гранул указанная технологическая линия имеет произво-
38
дительность 100 тыс. м3 в год. В настоящее время уже создано оборудование, включая печь новой конструкции 3,5X75 м, для технологической линии производительно' стыо 200 тыс. м3 в год.
Особо легкий керамзитовый гравий1 получают мето дом опудривания сырцовых гранул перед обжигом по рошком огнеупорного материала. Опудривание и окатку сырцовых гранул можно производить в сушильном бара бане. Нанесение огнеупорного порошка на поверхность гранул позволяет повысить температуру их обжига, что
интенсифицирует процесс вспучивания |
(табл. |
II.1). |
Т а б л и ц а ПЛ. Характеристика керамзитового |
гравия, |
полученного |
без опудривания и с опудриванием сырцовых гранул |
|
|
(по данным НИИКерамзита) |
|
|
Объемная масса |
|
||
в кг/м* |
фракции |
s |
|
Гранулы |
|
||
|
Прочие |
||
20—40 мм |
10—20 мм |
||
|
О)
i ? цили кгс/с
вв
>атура вания
V§
С- 1 ш Я
й"
Без |
опудривания . . |
240 |
246 |
8—14 |
1120 |
4,5 |
С |
опудриванием . . |
104 |
140 |
3 - 8 |
1200 |
10 |
На прочность, долговечность и, главное, однородность легкого бетона большое влияние оказывает режим ох лаждения керамзита. Это влияние тем заметнее, чем крупнее гранулы и выше их пористость. В процессе бы строго охлаждения в зернах керамзита усиливаются ос таточные напряжения. Первоначально напряженное со стояние гранул отражается на ряде свойств керамзита: ползучести, морозостойкости, прочности. По данным Пензенского инженерно-строительного института, в ре зультате резкого охлаждения керамзита и появления в нем микротрещин могут снизиться прочность бетона на раскалывание, изгиб и призменная прочность, т.е. те по казатели, которые в наибольшей степени зависят от прочности заполнителя на разрыв. Нельзя допускать резкого охлаждения керазмнта, если он применяется для бетона, который будет эксплуатироваться в агрессив-
1 Технология производства особо легкого керамзитового гравия разработана Куйбышевским НИИКерамзитом.
39