
книги из ГПНТБ / Салтыков, А. В. Основы современной технологии автомобильных шин
.pdfголовку, в пространство, заполненное резиновой смесью. Обрезиненная проволока выходит из головки через прорезь изолирующей планки, имеющей форму наружных габаритов обрезиненной ленты. Прорезь сдерживает выпрессовку резины и пропускает только не обходимое для обрезинивания количество. Поскольку червяк шприц-машины работает непрерывно (независимо от работы про тягивающего станка), головка снабжена отверстием для выпрессовки избытка резины. Выпрессованный резиновый шнур возвра
щают на разогревательные вальцы и смешивают со свежей резиной. Иногда его прямо пускают в шприц-машину. Конструкция направляющей и изоли рующей планок зависит от вида обрезиниваемого материала (плетенка, уточная или безуточная ленты, оди ночная проволока). Температура рези новой смеси в головке должна быть около 60—70°С. Вначале головку подогревают паром, а затем охлаж дают вйдой, как и ' корпус шприцмашины.
На рис. 8.37 показано сечение пле тенки, правильно и неправильно обре зиненной.
Из головки шприц-машины обрезиненная проволока поступает на про тягивающий станок (рис. 8.36, 12), ко торый одновременно является охлади тельным приспособлением (барабаны протягивающего станка охлаждаются водой). Для улучшения охлаждения
дополнительно применяется маленькая охладительная ванна с ме таллическим валком Для нанесения воды на обрезиненную про волоку; сверху проволоки вращается обрезиненный валик, отжи мающий избыток влаги.
Частично охлажденная проволока далее поступает на компен сатор 13, действующий как склад, соединяющий процесс непрерыв ного обрезинивания проволоки с периодическим процессом намотки колец. С верхнего шкива проволока сходит на направляющий блок и подается на кольцеделательный станок. Кроме того, на компенса торе резиновая изоляция дополнительно охлаждается.
Изготовление колец. В настоящее время в отечественной про мышленности и за рубежом применяются несколько типов кольцеделательных станков.
П о л у а в т о м а т и ч е с к и й с т а н о к для колец больших размеров модели АКД-2А (рис. 8.38,6). Этот станок широко при меняется в отечественной промышленности. На нем выпускают крылья диаметром от 730 до 1100 мм. Станок автоматически на матывает заранее установленное количество витков (8—20) на
276
шаблон и останавливается. После этого кольцо обрубается пнев- матическим ножом и конец проволоки подается для заправки на шаблон, замок шаблона открывается и кольцо снимается. Произ водительность станка — 0,62—2,8 шт/мин. Станок может устанав ливаться в агрегат вместе с компенсатором.
За рубежом для изготовления колец больших размеров при меняется станок типа «Беннер 46», имеющий такую же произво дительность, как и станок АКД-2А. Для колец малых и средних размеров в отечественной промышленности применяется кольцеделательный автоматический станок АКД-1А (рис. 8.38,а). На станке изготавливаются кольца диаметром 381—622 мм. Станок наматывает на шаблон от 2—8 витков, обеспечивая длину стыка в кольце от 75 до 200 мм. Обрезиненная проволока автоматически наматывается в кольцо на шаблоне; конец проволоки автомати чески захватывается, кольцо обрубается и сбрасывается с шаб лона. Для колец определенного размера требуется свой шаблон, имеющий приспособление (сменные звенья) для регулировки длины окружности в малых пределах. Иногда вместо сменных звеньев для раздвигания шаблона применяется микрометриче ский винт. Скорость намотки проволоки— 120 м/мин; производи тельность станка — 7—20 колец/мин. Из зарубежных станков ука занного типа известен автоматический станок FSW.
Общий вид агрегата для изготовления колец показан на рис. 8.36. Обычно в агрегате устанавливают два кольцеделательных станка.
М н о г о р у ч ь е в ы е к о л ь ц е д е л а т е л ь н ы е а г р е г а т ы , (рис. 8.39). Вышеописанный процесс производства колец (из пряди проволоки в один ручей) в последнее время начинают заменять многоручьевыми установками, которые работают аналогично с тем исключением, что в шприц-машину и далее на кольцеделательные станки одновременно поступает параллельно несколько (от 2 до
4)ручьев проволочной ленты.
Многоручьевой кольцеделательный агрегат имеет шпулярник
для проволоки вместимостью на 24 катушки. Диаметр червяка шприц-машины обычно составляет 90—120 мм. Протягивающий ба рабан, ролики, направляющие на всех станках агрегата, а также шаблон и нож имеют большую ширину, рассчитанную на разме щение 2—4 параллельных прядей проволоки. В два ручья пропус кается 9—12-прядная лента, в три — 7—8-прядная, в четыре — до 6 прядей.
Производительность агрегата повышается во столько раз, сколько ручьев выпускается на нем, то есть в 2—4 раза. Так, на пример, двухручьевой агрегат выпускает до 400 колец/ч диаметром
730 мм.
Многоручьевые агрегаты ввиду высокой производительности найдут широкое применение в промышленности.
Для обеспечения заданной прочности кольца должны выпус каться с нахлестом. Для плетенки и уточной ленты нахлест дол жен составлять 40—80 мм, для безуточной ленты — 80—120 мм.
277
9Ц5
Рис. 8.38. Кольцеделательный станок:
а — станок АКД-1 А; б — станок АКД-2А: |
ролик; 6 —станина' |
л механизм захвата проволоки; 2 — шаблон; 3 — механизм подачи проволоки; 4 — режущий механизм; 5 — направляющий |
|
7 —привод; 8 — кольцеловитель. |
1 |
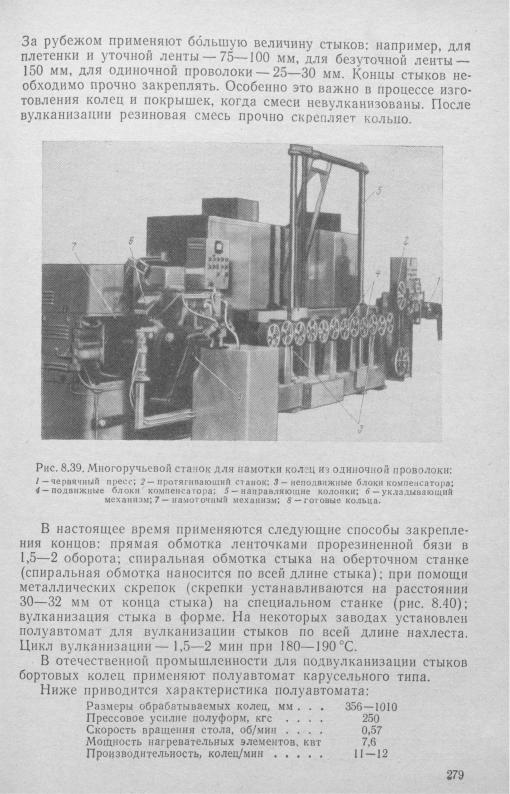
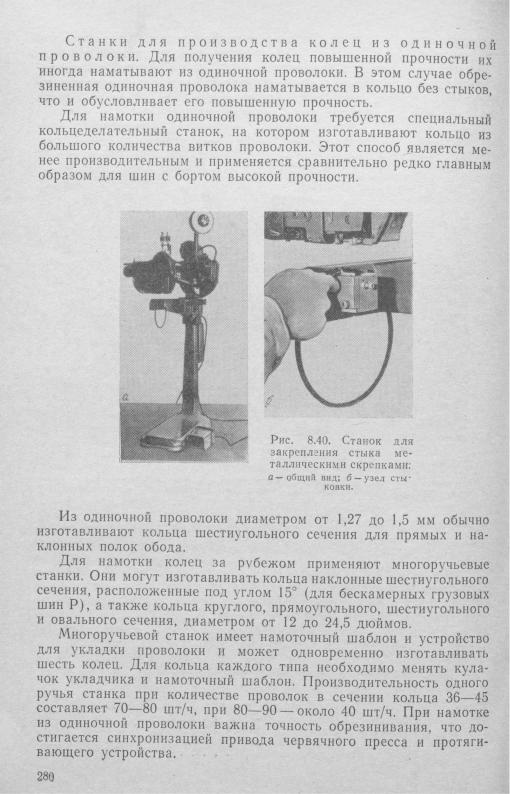
За последние годы наметилась тенденция применять витые кольца, главным образом, в производстве колец для легковых по крышек. Применение витых колец позволяет уменьшить массу кольца на 50% и облегчить монтаж шин на обод. В отечествен ной промышленности витые кольца изготавливают из проволоки диаметром 1 мм методом навивки.
Ниже приведена характеристика кольцеделательного станка:
Диаметр выпускаемых колец, м м |
.................................. |
330—482,6 |
||
Диаметр сечения, м м ........................... |
• ........................... |
3—10 |
||
Шаг витка, м м ..................................................................... |
|
|
60—200 |
|
Скорость навивки, |
м /м и н .................................................. |
|
10—30 |
|
Количество |
шпуль с проволокой, ш т ..................................... |
2 |
||
Производительность станка, ш т / ч |
........................................ |
80 |
||
Низкая производительность станков для производства витых ко |
||||
лец тормозит их применение в шинном производстве. |
||||
Обертка колец. В целях улучшения монолитности кольца и ад |
||||
гезии его с тканевыми деталями кольцо обертывают текстильной |
||||
ленточкой из |
ткани |
квадратного |
переплетения, |
закроенной под |
углом 45°. Обычно применяют хлопковую ткань, промазанную ре |
||||
зиной на фрикционном каландре с двух сторон. Иногда на вну |
||||
треннюю (обращенную к кольцу) |
часть ткани накладывают тонкий |
|||
слой резиновой смеси. Это увеличивает силу сцепления ткани с ре |
||||
зиной кольца и уменьшает опасность расслоения борта в процессе |
||||
вулканизации. Обертку рекомендуют применять при .безуточных |
||||
проволочных лентах, а также для тех шин, где применяется напол |
||||
нительный шнур или требуется повышенная монолитность кольца. |
||||
Существуют два способа наложения оберточной ленточки на |
||||
кольца: прямая и спиральная обертки. |
|
|||
Прямая обертка, вдоль окружности кольца текстильной про |
||||
резиненной ленточкой, закроенной под углом 45°, осуществляется |
||||
на станках, показанных на рис. 8.41. При обертке таким способом |
||||
края ткани соединяются внахлест. На станках обертывают кольца |
||||
диаметром от 8 до 40 дюймов. Станок имеет систему направляю |
||||
щих приспособлений, обертывающих кольцо тканью, и прикаты |
||||
вающие ролики, плотно прикатывающие ткань к поверхности |
||||
кольца. На этих станках можно накладывать наполнительный |
||||
шнур, помещаемый под обертку. Ткань в оберточный станок может |
||||
подаваться на катушках, устанавливаемых в питатели, или транс |
||||
портерами после продольно-резательной машины прямым потоком. |
||||
Оберточные станки подобной конструкции имеют производитель |
||||
ность 750—800 колец в смену. Для повышения производительно |
||||
сти труда на оберточную ленточку иногда на каландре наклады |
||||
вают резиновую ленточку*, служащую для заполнения крыла. |
||||
Прямая обертка в настоящее время считается недостаточно |
||||
качественной для придания монолитности. |
|
* Обычно накладывают ленточку из тряпичной смеси (с добавкой из отходов корда).
281
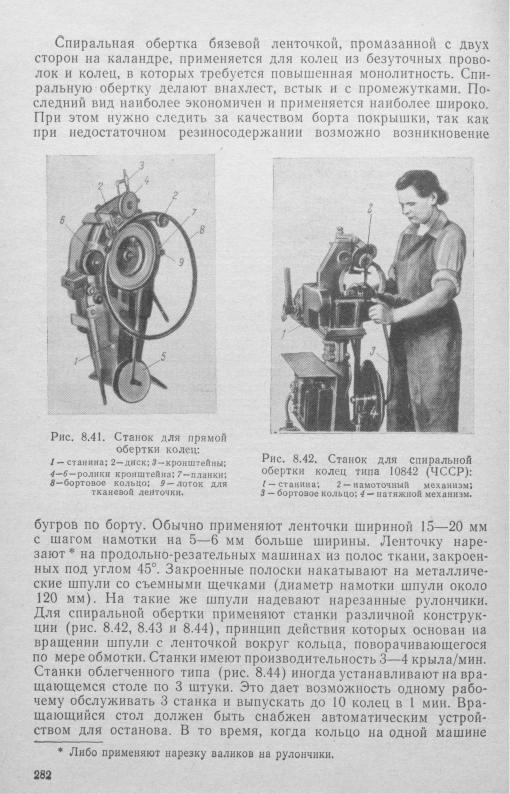
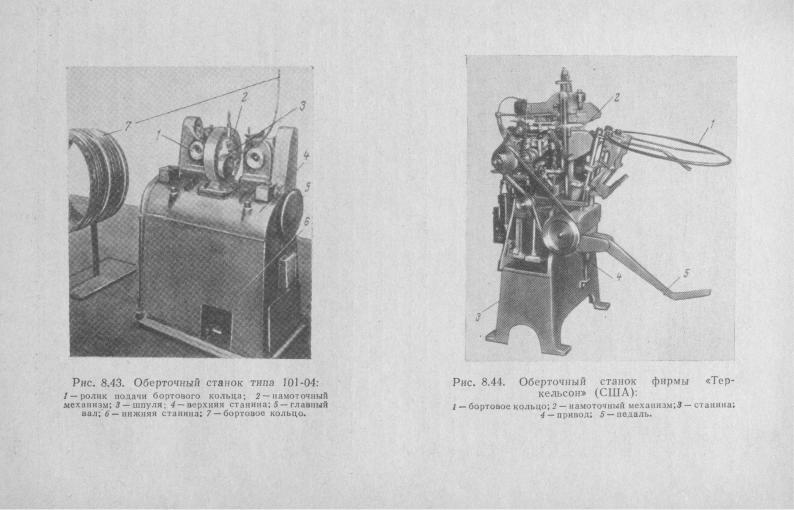
изготовлено, другие станки продолжают работать. Рабочий снимает обернутое кольцо, вставляет очередное проволочное кольцо в ста нок и, нажимая педаль, включает стол в движение.
Намотанные на шпули ленточки подают к стенкам транспор терами. На спирально-оберточных станках производят также изо ляцию резиновой ленточкой витых бортовых колец. Эту операцию, обычно, проводят одновременно с оберткой бязью.
Наложение крыльевой ленты. После обертки крыльев проводят операцию флипперования — наложение крыльевой ленты. Флиппер представляет собой ленту из ткани полотняного переплетения или прорезиненного корда. Обычно применяется вискозный сверхпроч ный корд структуры 5,45/1/2 или полиамидный корд. Применение корда дает возможность усилить монолитность борта. Лента за кроена под углом 45° и размещается вокруг кольца так, чтобы края ее накладывались ступеньками и лента образовала «ворот ник». Часто одновременно с флипперованием накладывают резино вый наполнительный шнур. Иногда применяют несколько крылье вых лент. Эти ленты обычно заранее дублируются друг с другом и в таком виде накладывают на кольца. Необходимо края лент рас полагать ступеньками величиной 10—15 мм, с тем, чтобы обра зовать плавный переход от толстого борта к тонкой гибкой бо ковине.
Для предотвращения перетирания корда кромки крыльевой ленты обкладывают резиновой ленточкой. Необходимость в этой операции отпадает, если толщина обкладки корда достаточна.
Ширина воротника определяется контуром заплечика бараба на и конструкцией покрышки. Иногда крыльевые ленты вообще не применяют и заменяют их слоями корда, завертывая их на крыло и под крыло. Накладку крыльевых лент (флиппера) произ водят на специальных флипперовальных станках (рис. 8.45). Ниже приводится характеристика крыльевых станков, выпускаемых отечественной промышленностью:
|
|
Станок СКФ*3 |
Станок СКФ-4 |
|
|
для грузовых |
для легковых |
Габариты кольца, мм |
|
покрышек |
покрышек |
|
|
|
|
внутренний диаметр ................... |
381-530 |
300-530 |
|
ш ирина........................................... |
8 -1 6 |
8 -1 5 |
|
высота .......................................... |
6 -1 8 |
6 -1 8 |
|
Ширина крыльевой ленты, мм . . . |
70—140 |
70-140 |
|
Скорость прикатки, м / с ................... |
0,59 |
0,74 |
|
Мощность электродвигателя, |
кВт . . |
- 1,1 |
0,6 |
Производительность станка, |
шт/ч |
100 |
170 |
Изготавливаются также крыльевые станки СКФ-5 для колец диаметром 600—860 мм и станки СКФ-6 для колец диаметром 1000—1100 мм. Станки всех типов снабжаются специальными пи тателями.
За рубежом флипперовальные станки выпускаются для колец диаметром от 10 до 15 дюймов, от 16 до 24 и от 24 до 40 дюймов.
Для того, чтобы облегчить поворот материала крыла вокруг кольца при формовании (экспендировании) покрышки, собранной
284
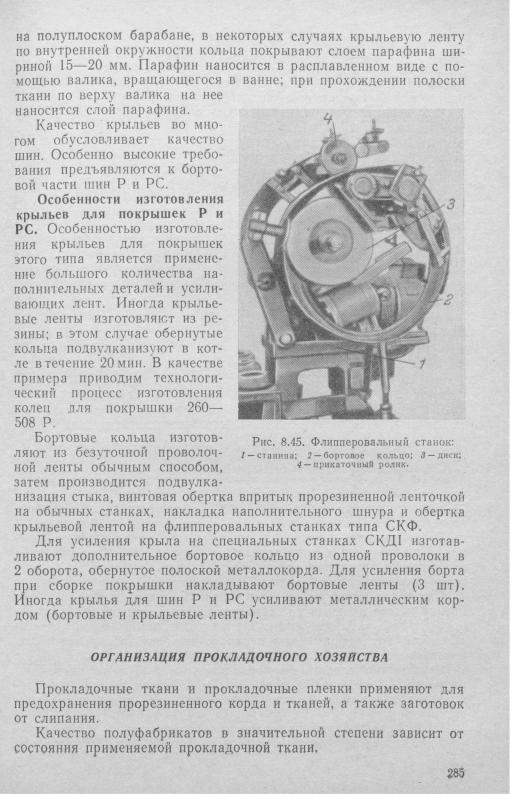