
книги из ГПНТБ / Басов, А. И. Механическое оборудование обогатительных фабрик и заводов тяжелых цветных металлов учебник
.pdfХарактеристика трубы (рис. |
17) следующая: |
|
Внутренний диаметр, |
м м ......................... |
630 |
Длина,, м ........................................................ |
|
93 |
Шаг спирали, мм ...................................... |
|
500 |
Скорость вращения, |
об/мин . . . . |
14—24 |
Производительность по огарку, м3/ч |
30—60 |
|
Общая мощность двигателей, кВт |
18 |
|
Так как материал в трубе перекатывается, |
а не скользит (как |
|
в шнеках), труба практически не истирается, спираль работает без |
||
замены 5—6 лет. |
|
|
Транспортирующая винтовая труба отличается простой и весьма |
||
надежной конструкцией, тихим, спокойным ходом; проста в обслужи- |
Рис. 18. Загрузочное устройство винтовой трубы
вании и не требует сложного ремонта; при хорошо работающей вен тиляции — отличается надежной герметичностью, что очень важно при транспортировке горячих, пыле- и газовыделяющих материалов, таких, как огарок; позволяет осуществлять загрузку одновременно в нескольких пунктах. В условиях работы на горячем цинковом огарке с температурой 600—700° С труба позволяет охлаждать его до температуры примерно 100° С, необходимой для дальнейшей пере
4 0
работки огарка. Для интенсивного охлаждения трубы по всей ее длине устанавливают водяные брызгала (форсунки).
Недостатки винтовой трубы — громоздкость и металлоемкость конструкции; наличие нескольких приводных механизмов, обуслов ливающих повышенный удельный расход энергии; влаговыделение при охлаждении брызгалами.
§ 7. Вибрационные конвейеры
Перемещение материала в вибрационном конвейере происходит внутри трубы (желоба), которая совершает большое число колеба ний (до 3000 в минуту) с малой амплитудой (0,5—3,0 мм).
Приводы вибрационных конвейеров бывают механические и элек тромагнитные. В механическом приводе колебания создаются криво шипно-эксцентриковым механизмом, в электромагнитном — элек тромагнитом, якорь которого жестко соединен с трубой конвейера. При прохождении тока вибрации якоря передаются трубе. Имеются конструкции конвейеров с инерционными вибраторами. В них вибра ции создаются вращением неуравновешенных масс.
Для достижения спокойной работы конвейера, устранения вибра ций, вредно влияющих на фундамент и несущие конструкции здания, применяют конвейеры двухтрубные уравновешенные (рис. 19) с ме ханическим приводом. Транспортирующие трубы 6 и 8 расположены одна над другой и соединены коромыслами 4 и плоскими рессорами 5. Концы рессор жестко соединены с трубами коробками 3. Соединение
коромысел с трубами — шарнирное с резиновыми втулками, сни жающими влияние вибраций. При температурном изменении длины труб ползуны 11 могут перемещаться в направляющих 7, установ ленных на стойке 9 рамы 10. Эксцентриковый вал 13 расположен на нижней трубе и крепится хомутами 12. Эксцентриковый вал полу
чает вращение от электродвигателя через ременную передачу и через шатун 1 и седло 2 приводит в движение транспортирующие
трубы. Движение труб происходит попеременно: когда одна дви жется вперед, другая отходит назад. Таким образом создается урав новешенная работа конвейера.
При движении трубы вперед материал перемещается вместе с ней, а при обратном ходе материал остается на месте, а труба как бы уходит из-под него.
Каждую трубу собирают из нескольких секций длиной около 4000 мм, соединяемых фланцами и точеными болтами. Соединения должны обеспечить, кроме прочности, точность установки секций, соосность их. Также тщательно приваривают фланцы к трубам.
каждую секцию труб подвешивают на четырех коромыслах и восьми рессорах. Рессоры изготовляют из кремнистой пружинящей стали марки 60С2 или 55С2. Применение стеклопластика позволило в несколько раз повысить стойкость рессор.
Для уравновешивания системы необходимо иметь одинаковые массы верхней и нижней труб, одинаковую равномерную загрузку их транспортируемым материалом, а также одинаковые длины верх-
41
13 |
1 |
2 |
3 |
4 |
5 |
6 |
них и нижних плеч коромысел. Двухтрубный конвейер загружают через загрузочное устройство специальной конструкции: загрузоч ный и разгрузочный патрубки разделены вертикальной перегородкой для деления поступающего материала на равные части. Конвейер можно загружать в разных точках по его длине. Загрузочное устрой ство в этом случае закрепляют на трубе хомутами. Колеблющиеся загрузочные патрубки соединяют с неподвижными конструкциями (бункерами, течками) гибкими патрубками (рукавами) из прочной ткани или резины. Не допускается установка конвейера под боль шими бункерами без промежуточной воронки или питателя, так как давление вертикального столба материала, находящегося в бункере, не позволит осуществить движение системы.
Достоинства двухтрубных конвейеров следующие: герметичность конструкции, что позволяет применять их для транспортирования горячих газовыделяющих материалов (агломерата оборотного, огарка и др.); малый расход электроэнергии; уравновешенность колеблю щихся масс; удвоенная производительность против однотрубного; возможность достичь длины до 100 м в одном агрегате с одним при водом; незначительный износ труб вследствие отсутствия скользя щего трения между трубой и материалом.
К недостаткам этих конвейеров относятся невозможность транс портировки влажных липких и пылевидных материалов; резкое па дение производительности при работе на подъем материала, поэтому наибольший угол их наклона не превышает 5°.
Горизонтальные двухтрубные виброконвейеры конструкции ВНИИцветмета используются для транспортировки оборотного агло мерата, имеющего температуру около 400—500° С.
В цветной металлургии применяют виброконвейеры с электро магнитным приводом конструкции института «Механобр» (рис. 20). Транспортирующая труба 1 конвейера подвешена на пружинных амортизаторах 6. Колебания трубе передаются электромагнитными вибраторами 4, жестко закрепленными на ней кронштейнами и хому тами 3 под углом 20° к продольной оси трубы.
Конвейер собирают из нескольких секций длиной примерно по 15 м. Соединение секций — телескопическое. На каждой секции установлено несколько одновременно работающих электровибра торов, примерно через 2,5—3 м. Загрузка осуществляется через от верстие 5, а выгрузка материала через отверстие 2.
Труба и вибратор соединены между собой через упругую си стему — пакет плоских стальных пружин-рессор 7. Для создания значительных усилий, интенсивно действующих на транспортирую щую трубу, необходимо одновременное синхронное действие всех установленных электровибраторов. В этом случае с наступлением резонанса небольшие возмущающие силы каждого вибратора пре образуются в необходимые для колебания системы усилия.
Эти конвейеры герметичны, труба подвергается очень малому истиранию транспортируемым материалом, не имеют вращающихся частей. Однако для нормальной работы требуются тщательное из готовление и наладка вибраторов, обеспечивающие устойчивую син
43
h
2500___________ ________ ^ _____________________________ Ш .
хронность действия всех вибра торов. К их недостаткам сле дует отнести наличие несколь ких приводов-вибраторов срав нительно с малостойкими сталь ными рессорами. Как и двух трубные, эти конвейеры не пригодны для работы на влаж ных, липких и пылевидных материалах.
Производительность кон вейеров с электромагнитными вибраторами конструкции Механобра составляет от 50 до 650 т/ч при мощности каждого вибратора от 0,5 до 8 кВт, ам плитуде колебаний 0,62—■1,25 мм и частоте колебаний 3000 в ми нуту. По такому же принципу работают вибропитатели (см.
стр. 48).
§ 8. Элеваторы
Для перемещения сыпучих материалов в вертикальной плоскости или под крутым уг лом (65—70° и выше)1 приме няют элеваторы. В зависимости от тягового органа элеваторы разделяются на ленточные и цепные. Грузонесущим органом элеваторов служит ковш.
Ленточный вертикальный элеватор (рис. 21) состоит из бесконечной прорезиненной лен ты 1 с закрепленными на ней ковшами 2, огибающей привод ной 3 и натяжной 10 цилиндри
ческие барабаны. Приводную станцию элеваторов, состоящую обычно из электродвигателя и редуктора (иногда ременной передачи), устанавливают всег да на верху элеватора на само стоятельной жесткой сварной раме.
Натяжное’устройство 7 нахо-. Q, дится на нижнем конце элевато-
44
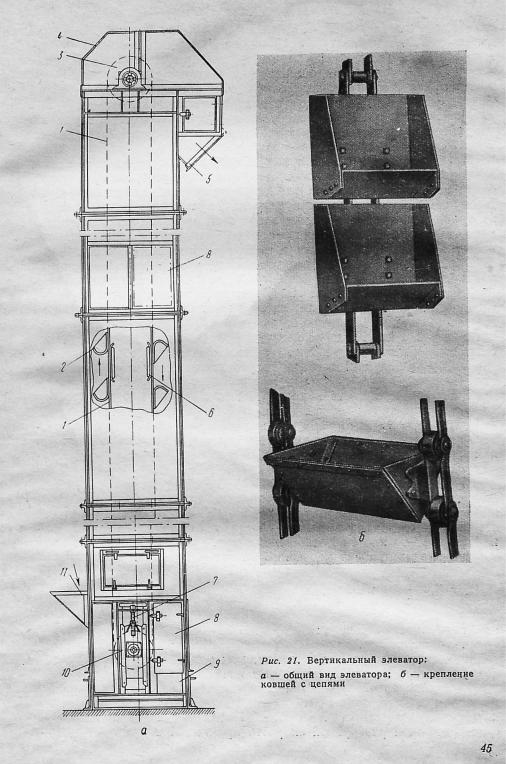
ра. Натяжения ленты и цепей регулируют обычно винтами. Кожух 4
является несущей конструкцией, воспринимающей нагрузку от на тяжения тяговых органов, усилие зачерпывания материала, динами ческую нагрузку и собственный вес. Поэтому изготавливают его жестким, прочным н плотным из листовой стали толщиной 2—5 мм. Отдельные его секции соединяют болтами и прокладками.
Материал в элеватор поступает через загрузочный |
карман 11 |
в зумпф 9, а выгружается через наклонное отверстие |
5 в головке |
элеватора.
При транспортировании сухих, легкосыпучих, порошкообразных н мелкокусковатых материалов, допускающих зачерпывание ковшей без значительного сопротивления, применяют ленточные элеваторы. В случае транспортирования тяжелых, кусковатых и абразивных материалов используют цепные элеваторы, при этом материал насы пают в ковши. Практически же материал одновременно зачерпы вается в ковши и насыпается в них из загрузочной воронки.
Ковши быстроходных элеваторов (преимущественно ленточных) разгружаются под действием центробежной силы при прохождении их через приводной барабан. В элеваторах, транспортирующих тяжелые влажные материалы, разгрузка осуществляется самотеком. Для ее-улучшения обратную ветвь ковшовой цепи отклоняют допол нительными отклоняющими звездочками, шинами или роликовыми батареями. Состояние рабочих органов проверяют через смотровые дверки 8. В больших элеваторах устанавливают специальные на правляющие 6.
В зависимости от транспортируемого материала ковши бывают глубокие и мелкие. Глубокие ковши с пологим наклоном верхней кромки (около 25° к горизонту) устанавливают в элеваторах, транс портирующих сухие легкосыпучие материалы; мелкие ковши с углом наклона кромки около 45° применяют при перемещении плохосыпу чих слеживающихся материалов.
Ширину ковша принимают на 25— 150 мм меньше ширины ленты. При ширине ковша до 250 мм устанавливают одну цепь, при более широких ковшах — две цепи (рис. 21, б). Ковши крепят к ленте
обычно заклепками, а к цепям — болтами или заклепками с приме нением уголков или специальных звеньев.
Производительность ковшового элеватора
Q= 3,6 м3/ч,
где i — емкость ковша, л;
а— шаг ковша, м;
v— скорость движения ковша, м/с; Ф — коэффициент наполнения ковша.
При транспортировке тяжелых абразивных материалов скорость движения ковшей принимают в пределах 0,4— 0,6 м/с; при транс портировке легкосыпучих материалов быстроходными элеваторами с центробежной разгрузкой скорость принимают в пределах 1,25—
46
4 м/с, а для плохбсыпучих пылевидных й влажных материалов
0,8—2 м/с.
Достоинства элеваторов — малая площадь, занимаемая элева торной установкой; высокая степень герметичности; возможность подачи материала на высоту до 60 м при производительности одного агрегата до 500 м3/ч. Их недостатки — непригодность для транспорти ровки влажных глинистых материалов; чувствительность к пере грузкам, поэтому для нормальной работы необходимо соблюдать равномерность подачи материала; большое число шарниров в цепях и сравнительно быстрый их износ при транспортировке абразивных материалов, что приводит к повышенным эксплуатационным рас ходам их на ремонт и замену.
Для повышения износостойкости цепей, работающих на абразив ных материалах, звенья, ролики и пальцы изготовляют из легиро ванных сталей и подвергают термической обработке. Рабочие по верхности ковшей и звездочек наплавляют износостойкими мате риалами. Изношенные ковши необходимо своевременно заменять. Неравномерный износ звеньев и пальцев может привести к перекосам цепей и их обрыву. Следует внимательно и регулярно осуществлять натяжение цепей и не допускать подпрессования материала в зумп фах. Соединения секций и стенки кожуха должны быть плотными, чтобы избежать загазованности и запыленности окружающей атмо сферы.
Для предотвращения самопроизвольного обратного движения ковшовой ленты или цепи устанавливают стопорные устройства: бесшумные храповые и роликовые механизмы, электромагнитные тормоза, а для предохранения от повреждений при случайных обры вах — специальные предохранительные устройства (ловители и др.).
§ 9. Питатели
Для обеспечения нормальной работы оборудования (дробилок, мельниц, металлургических печей и др.) подача перерабатываемого материала (руды, концентрата, шихтовых материалов и др.) должна быть равномерной. Поэтому устанавливают специальные механизмыпитатели, размещаемые под бункерами для питания конвейеров, транспортирующих материал к технологическим агрегатам, или перед этими агрегатами.
Существует большое число конструкций питателей для сыпучих материалов, отличающихся в основном конструктивным исполне нием рабочих органов. Наиболее распространены ленточные, пла стинчатые, тарельчатые, лотковые, винтовые и вибрационные пита
тели (рис. 22).
Ленточный питатель (рис. 22, а) представляет собой ленточный
конвейер малого размера. Он также состоит из бесконечной проре зиненной ленты, охватывающей приводной и натяжной барабаны. Рабочая ветвь ленты и нижняя ветвь (длинных питателей) поддержи ваются роликами 6. По бокам ленты устанавливают борта, предотвра
щающие просыпание материала. На нижней кромке бортов закреп
47
ляют уплотнительные резиновые пластины. Для стыковки ленты применяют вулканизацию или используют металлические изделия. Натяжное устройство — винтовое.
Рис. 22. Схемы |
питателей |
для сыпучих материалов: |
а — ленточный: |
б — пластинчатый; в — тарельчатый; г — вибрационный; д — лотковый |
|
качающийся; е — цепной; |
ж — барабанно-лбпастный; 3 — винтовой; и — лопастный; 1 — |
бункер; 2 — шиберная заслонка; 3 — натяжной барабан; 4 — лента; 5 — кожух; 6 — ролик;
7 — приводной барабан; 8 — пластины (полотно); 9, |
10 — приводная 4-натяжная звездочка; |
|||||
11 |
— винт; |
12 — диск; |
13 — нож; |
14 — желоб; |
15 — электровибратор; 16 — подвеска; |
|
17 |
— опорный ролик; 18 — лоток; 19 — шатун; 20 — кривошип; 21 — барабан; |
22 — вал; |
||||
23 |
— рама; |
24 — цепь; |
25 — лоток; |
26 — корпус; |
27 — барабан; 28 — вал; |
29 — винт; |
30 |
—лопасть; 31 — щель бункера; 32 — ленточный |
конвейер; 33 — барабан |
|
Скорость движения ленты составляет 0,05—0,4 м/с. Для подачи тяжелых, вязких и плохосыпучих материалов скорость снижают. В этом случае в приводе предусматривают храповой механизм, по
48
зволяющий получить большое передаточное отношение. Наиболее распространен привод от электродвигателя через один или два ре
дуктора.
Питатели устанавливают горизонтально или с уклоном в сторону подачи до 10°. Производительность питателя подсчитывают по фор
муле |
|
(19) |
Q = 3,6Bhvyk т/ч, |
|
|
где В — ширина ленты между бортами, м; |
||
/г — толщина слоя |
материала на ленте, м; |
|
v — скорость движения ленты, |
м/с; |
|
у — объемная масса материала, |
кг/м3; |
|
k — коэффициент |
заполнения |
ленты материалом, рав |
ный 0,7—0,8. |
|
|
Производительность питателя можно регулировать, изменяя ско рость движения ленты или положение регулировочной заслонки 2.
Наиболее просто регулировать скорость ленты питателей с храповым механизмом, для этого достаточно изменить радиус кривошипа
(см. рис. 23).
Питатели бывают стационарные и передвижные. Последние уста навливают под бункерами с несколькими выпускными отверстиями для подачи материала на сборный ленточный конвейер.
Для разгрузки ленты от давления вертикального столба мате риала, находящегося в бункере, предусматривают наклон стенки под углом 45—50°, что позволяет плавно опускать материал на ленту. Питатели, работающие на пылящих материалах, должны быть укрыты плотным кожухом.
Область применения ленточных питателей — подача мелкокусковатых, сухих и влажных материалов. Широкое использование их обусловлено простотой конструкции, малым расходом электро энергии, спокойной устойчивой работой, малой собственной массой и сравнительно малыми эксплуатационными расходами.
Основные параметры питателей — ширина ленты и расстояние между осями барабанов. Техническая характеристика питателей приведена в табл. 1.
ТАБЛИЦА |
1 |
|
|
|
|
|
ТЕХНИЧЕСКАЯ ХАРАКТЕРИСТИКА ЛЕНТОЧНЫХ ПИТАТЕЛЕЙ |
|
|||||
Ширина |
Расстоя |
Диаметр |
Скорость |
Производи |
Мощность |
Масса без |
ние |
электро |
|||||
ленты, |
между |
барабана, |
ленты, м/с |
тельность, |
двигателя, |
двигателя, |
мм |
барабана |
мм |
|
м8/ч |
кВт |
кг |
|
ми, мм |
|
|
|
|
|
250 |
800 |
320 |
0,02—0,035 |
_ |
1 |
172 |
400 |
865 |
320 |
0,05—0,43 |
5,4—46,5 |
1,8 |
327 |
400 |
2200 |
320 |
0,018—0,262 |
4—20 |
1,8 |
750 |
400 |
3200 |
320 |
0,018—0,262 |
4—20 |
1,5—2,5 |
820 |
500 |
1500 |
320 |
— |
7,2—62 |
1,8 |
510 |
800 |
2000 |
500 |
0 ,035-0,2 |
17— 175 |
4,0 |
1500 |
4 А. И . Басов |
49 |