
- •Введение
- •ЧАСТЬ ПЕРВАЯ
- •1. СОСТАВЛЕНИЕ КИНЕМАТИЧЕСКОЙ ТЕХНОЛОГИЧЕСКОЙ CХЕМЫ И КАРТЫ МАШИНЫ
- •1.1. Общие положения
- •1.1.1. Технологический процесс и его схема
- •1.1.2. Структура машин
- •1.2. Составление технологической схемы и карты макаронного пресса
- •1.2.1. Описание технологического процесса получения сырых короткорезаных макаронных изделий на прессе
- •1.2.2. Технологические и вспомогательные операции технологического процесса получения сырых макаронных изделий
- •Таблица 1
- •1.3. Составление структурной и кинематической схем макаронного пресса
- •2. СОВМЕЩЕНИЕ ДВИЖЕНИЙ РАБОЧИХ ОРГАНОВ МАШИН ЦИКЛИЧЕСКОГО ДЕЙСТВИЯ
- •2.1. Общие положения
- •2.2. Задание и его выполнение
- •3.1. Общие положения
- •3.2. Задание и его выполнение
- •3.2.1. Расчет объемного дозатора барабанного типа
- •3.2.2. Расчет тарельчатого дозатора
- •4.1. Общие положения
- •4.1.1. Расчет шнековых смесителей
- •4.2. Задание и его выполнение
- •4.2.1. Расчет барабанного смесителя
- •4.2.2. Расчет шнекового смесителя
- •5. РАСЧЕТ И КОНСТРУИРОВАНИЕ ШНЕКОВ ПРЕССОВ ПЛАСТИЧЕСКИХ ПРОДУКТОВ
- •5.1. Общие положения
- •5.2. Задание и его выполнение
- •ЧАСТЬ ВТОРАЯ
- •6.1.Общие положения
- •6.1.2. Машины с вращающимися ситами
- •6.1.3. Просеивающие машины с неподвижными ситами
- •6.2. Задание и его выполнение
- •6.2.2. Расчет пирамидального бурата
- •6.2.3. Расчет просеивающих машин с неподвижными ситами
- •7. ОПРЕДЕЛЕНИЕ ПАРАМЕТРОВ ВОЗДУШНЫХ СЕПАРАТОРОВ
- •7.1. Общие положения
- •7.2. Задание и его выполнение
- •8 .ОПРЕДЕЛЕНИЕ ПАРАМЕТРОВ МАГНИТНЫХ СЕПАРАТОРОВ
- •8.1. Общие положения
- •8.2. Задание и его выполнение
- •9. РАСЧЕТ ПАРАМЕТРОВ РАБОЧИХ ОРГАНОВ ТРИЕРОВ
- •9.1. Общие положения
- •9.1.1. Цилиндрические триеры
- •9.1.2. Дисковые триеры
- •9.2. Задание и его выполнение
- •9.2.1. Расчет цилиндрического триера
- •9.2.2. Расчет дискового триера
- •10. РАСЧЕТ ОСНОВНЫХ ПАРАМЕТРОВ ОБОЕЧНЫХ МАШИН
- •10.1. Общие положения
- •10.2. Задание и его выполнение
- •Конструктивно принимаем диаметр цилиндра обоечной машины D равным 0,5 м (500 мм).
- •11. РАСЧЕТ ОСНОВНЫХ ПАРАМЕТРОВ РАБОЧИХ ОРГАНОВ ВАЛЬЦОВЫХ УСТРОЙСТВ
- •11.1. Общие положения
- •11.2. Задание и его выполнение
- •12. РАСЧЕТ ПАРАМЕТРОВ РАБОЧИХ ОРГАНОВ МОЛОТКОВЫХ ДРОБИЛОК
- •12.1. Общие положения
- •12.2. Задание и его выполнение
- •Литература
- •ПРИЛОЖЕНИЯ
- •Приложение 19
Окончание таблицы 7
1 |
2 |
3 |
4 |
5 |
6 |
7 |
5 |
300 |
Мука в/с |
28 |
|
30 |
40 |
Мука 1 с |
|
32 |
|
|
||
|
|
|
|
|
||
6 |
650 |
Мука в/с |
26 |
|
28 |
90 |
Мука 1 с |
|
33 |
|
|
||
|
|
|
|
|
||
7 |
800 |
Мука 2 с |
24 |
|
26 |
100 |
Мука 1 с |
|
30 |
|
|
||
|
|
|
|
|
||
8 |
350 |
Мука 2 с |
22 |
|
26 |
40 |
Мука 1 с |
|
30 |
|
|
||
|
|
|
|
|
||
9 |
750 |
Мука в/с |
30 |
|
28 |
120 |
Мука 2 с |
|
24 |
|
|
||
|
|
|
|
|
||
10 |
200 |
Мука в/с |
31 |
|
30 |
30 |
Мука 2 с |
|
28 |
|
|
||
|
|
|
|
|
5. РАСЧЕТ И КОНСТРУИРОВАНИЕ ШНЕКОВ ПРЕССОВ ПЛАСТИЧЕСКИХ ПРОДУКТОВ
5.1. Общие положения
Шнеки (специальные винты) широко применяются в различного рода шнековых устройствах: питателях, дозаторах и прессах. Каждое такое устройство представляет собой цилиндрический кожух, внутри которого расположен один или два шнека. Кожух имеет приемный бункер и специальным образом оформленное выходное отверстие (матрица, сопло, мундштук). При наличии двух шнеков им придают встречное вращательное движение. Каждое устройство снабжено приводом.
По конструкции шнеки подразделяются на сплошные и лопастные, которые могут выполняться с правильной прямой и косой винтовыми поверхностями, с переменным аксиальным и радиальным шагом.
Из опыта работы многих шнековых устройств известно, что под действием винтовой поверхности шнека транспортируемый материал движется не параллельно его оси, а винтообразно с переменной скоростью в осевом и радиальном направлениях в зависимости от расстояния частиц материалов до оси шнека, от коэффициента трения и величины противодавления [8].
Так как углы подъема винтовых линий (рис.23) правильной винтовой поверхности шнека изменяются, увеличиваясь от периферии к центру шнека, то осевое перемещение частиц материала, расположенных в радиальном направлении, будет неодинаковым.
71
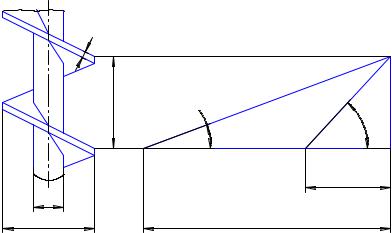
Для практических расчетов достаточно принимать αср среднее арифметическое значение углов подъема винтовых линий на периферии αD и у
вала αd шнека, которое определяется по формулам: |
|
|
||||||
αср = 0,5(αD +αd ) . |
|
|
(80) |
|||||
Здесь |
|
H |
|
|
H |
|
|
|
αD = arctg |
|
; |
αd = arctg |
, |
(81) |
|||
π D |
π d |
|||||||
|
|
|
|
|
||||
где Н – шаг витков шнека, м; |
|
|
|
|
|
|||
D и d – диаметры шнека и вала шнека в м. |
|
|
|
|||||
Снижение перемещения частиц продукта в осевом направлении |
||||||||
можно учесть коэффициентом отставания k o |
, который вычисляется по |
|||||||
формуле: |
|
|
|
|
|
|
|
|
ko |
=1 − (cos2 αср − 0,5 f sin 2αср ) , |
(82) |
где f = tgϕ – коэффициент трения (ϕ – угол трения).
Диаметр вала шнека должен быть больше предельного, определяемого из условия по формуле:
d |
|
≥ |
H |
tgϕ . |
(83) |
|
пр |
π |
|||||
|
|
|
|
δ
H
A
d D
B
α d |
α D |
|
|
|
πd C |
|
πD |
Рис.23. К определению параметров шнека
Производительность шнекового устройства определяется произведением полезно заполненного одношагового межвиткового объема в пределах плоского угла в один радиан на угловую скорость вращения шнека, которую можно определить из формулы:
Q = 0,127 (D2 − d 2 )(H −δ)(1 − ko ) ρ ψ ω , |
(84) |
где δ – толщина витка шнека в осевом направлении по наружному диаметру, м;
ρ – плотность материала, кг/м3;
72
ψ– коэффициент заполнения межвиткового пространства;
ω– угловая скорость вращения шнека, с–1.
При заданной производительности по уравнению (84) можно определить диаметры шнека или угловую скорость вращения шнека.
Если формуемый или прессуемый материал является пластичновязким и обладает адгезией, то в качестве коэффициента трения берется коэффициент внутреннего трения, определяемый из условия связи частиц между собой при сдвиге слоев материала.
Шаг винтовой линии шнека выбирается равным H=(0,7—0,8)·D. Для получения максимальной производительности шнекового
устройства необходимо принимать небольшие значения углов подъема винтовых линий шнека не менее 10°. В противном случае может произойти отрыв материала от внутренней поверхности корпуса устройства.
Для снижения опасности проворачивания материала на внутренней поверхности корпуса устройства устанавливают ребра или делают углубления, располагая их в продольном или слегка винтовом направлении, кроме того, должно выполняться следующее условие:
Fк > Fш,
где Fк – площадь внутренней цилиндрической поверхности корпуса шнекового устройства и Fш – площадь одной стороны поверхности шнекового витка на длине одного шага шнека, которые
определяем по формулам: |
|
|
|
|||
|
|
1 |
Fк =π D (H −δ) , |
D + 2 L |
|
(85) |
F = |
|
(π D L −π d l + H 2 ln |
) , |
(86) |
||
4 |
π |
|
||||
ш |
|
d + 2 l |
|
|||
|
|
|
|
|
|
где l и L – развертки винтовых линий, соответствующие диаметрам вала и шнека, м.
Крутящий момент Mкр (Н·м) на валу шнека и осевое усилие S (Н)
можно определить по методике К. П. Гуськова [9] из формул: |
|
M кр = 0,131 n pmax (D3 − d 3 ) tgαср , |
(87) |
S = 0,393 n (D2 − d 2 ) pmax , |
(88) |
где n – число рабочих шагов шнека; |
|
pmax – максимальное давление прессования, МН/м2 . |
|
Зная крутящий момент на валу шнека и осевое усилие, находят соответствующие им нормальное и касательное напряжения по формулам:
σсж |
= |
S |
|
, |
(89) |
||
F |
|||||||
|
|
|
|
|
|||
τ = |
|
Mкр |
, |
(90) |
|||
|
Wр |
||||||
|
|
|
|
73
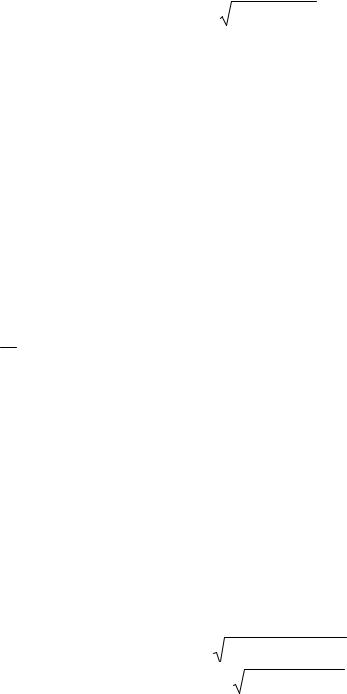
где F – площадь поперечного сечения вала шнека, м2 ;
Wр – полярный момент сопротивления поперечного сечения вала шнека, м3.
Эквивалентное напряжение по теории наибольших касательных напряжений определяют по формуле:
σэ = σсж2 + 4 τ 2 . |
(91) |
Последний виток шнека, выходящий в прессовую камеру, находится под действием максимального давления. Этот виток следует рассчитать на прочность.
С небольшим допущением один виток можно уподобить кольцевой пластинке, защемленной по внутреннему контуру в теле вала шнека. В этом случае наибольший изгибающий момент на внутреннем контуре такой пластинки [5], выполненной из стали, определяем по формуле:
Mи = |
pmax D2 |
|
1,9 − 0,7 a−4 −1,2 a−2 −5,2 ln a |
. |
(92) |
||
32 |
|
|
|
||||
|
|
1,3 + 0,7 a−2 |
|
||||
А наибольшее напряжение (оно же и эквивалентное) определяем по |
|||||||
формуле: |
|
|
|
6 Mи |
|
|
|
|
|
|
σи = ± |
, |
(93) |
||
|
|
|
|
||||
|
|
|
|
δ 2 |
|
где a = Dd — отношение диаметров, величина которого практически лежит
в пределах от 1,8 до 3.
Шнеки могут изготовляться литыми, точеными, сварными и паяными. В индивидуальном производстве чаще всего шнеки изготовляются сварными, причем винтовая поверхность (перо) шнека составляется из отдельных элементов — вырезанных и выгнутых разомкнутых колец.
Для изготовления шнека диаметром D с заданным диаметром вала d и шагом H необходимо изготовить кольца с наружным диаметром Do ,
внутренним диаметром do и разомкнутыми на угол выреза αo |
(рис. 24). |
||
Вначале определяют ширину b винтовой поверхности и длины |
|||
винтовых линий l и L в пределах одного шага шнека по формулам: |
|||
b = 0,5 (D − d) ; |
(94) |
||
l = H 2 + (π \ d)2 ; |
(95) |
||
L = H 2 + (π d)2 . |
(96) |
||
Затем определяют угол выреза по формуле: |
|
||
αo = 2 π − |
L −l |
. |
(97) |
|
|||
|
b |
|
74
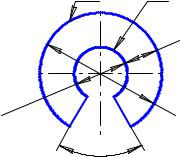
Ll b
d
o
D
o
α î
Рис.24. Схема кольца заготовки витка шнека
И, наконец, диаметры кольца определяем по формулам: |
|
||||||||||||
D |
= |
|
2 L |
|
; |
d |
|
= |
|
2 l |
|
. |
(98) |
2 |
|
|
|
2 |
|
|
|||||||
o |
|
π −αo |
|
o |
|
π −αo |
|
||||||
|
|
|
|
|
|
|
|
|
|
|
|
||
Кольца можно изготовлять |
с |
углом |
|
выреза |
αо=0. Таких |
колец- |
заготовок для выполнения шнека заданной длины надо меньше, чем колец
с углом αо |
> 0, так как одно такое кольцо образует винтовую поверхность |
|||||||||||||||
на длине шнека, определяемой по формуле: |
|
|
|
|
||||||||||||
|
|
|
|
|
|
1 |
|
|
|
|
|
α |
o |
|
|
|
|
|
|
|
|
H |
= H |
|
+ |
|
|
|
|
|
(99) |
||
|
|
|
|
|
|
|
|
|
|
|
||||||
|
|
|
|
|
|
1 |
|
|
|
|
|
. |
||||
|
|
|
|
|
|
|
|
|
|
2π −αo |
|
|||||
|
Из формулы видно, что образуемая длина шнека несколько больше |
|||||||||||||||
шага шнека. |
|
|
|
|
|
|
|
|
|
|
|
|||||
|
Мощность на валу шнека N (кВт) определяем по формуле: |
|
||||||||||||||
|
|
|
|
|
N = 215 P n tgα |
ср |
(R3 |
− R3 ), |
(100) |
|||||||
|
|
|
|
|
|
|
|
|
|
|
|
|
1 |
|
||
где |
P |
– давление прессования, МПа; |
|
|
|
|
|
|||||||||
|
R = |
D |
– наружный радиус шнека, м; |
|
|
|
|
|
|
|||||||
|
2 |
|
|
|
|
|
|
|
||||||||
|
|
|
|
|
|
|
|
|
|
|
|
|
|
|
||
|
R = |
d |
|
– радиус вала шнека, м; |
|
|
|
|
|
|
|
|
|
|||
|
|
|
|
|
|
|
|
|
|
|
||||||
|
1 |
2 |
|
|
|
|
|
|
|
|
|
|
|
|
|
|
|
|
|
– частота вращения шнека, мин–1. |
|
|
|
||||||||||
|
|
n |
|
|
|
Для разработки кинематической схемы привода шнека необходимо рассчитать общее передаточное число, которое определяем по формуле:
i = |
nдв. |
. |
(101) |
|
|||
|
n |
|
|
Общее передаточное число привода является произведением всех |
|||
передаточных чисел привода и определяется по формуле: |
|
||
i = i1 ... in . |
(102) |
Общий коэффициент полезного действия является произведением всех КПД передач привода и определяется по формуле:
75