
ЛАБЫ ПО ТКМ
.pdf
2 ОБЩИЕ СВОЙСТВА МИНЕРАЛЬНОГО ПОРОШКА Минеральный порошок представляет собой продукт тонкого из-
мельчения известняков, доломитов, доломитизированных известняков. Минеральный порошок должен быть сухим и рыхлым. Активированный минеральный порошок должен быть однородным по цвету. Материалы, используемые для приготовления минерального порошка, должны быть чистыми, не содержащими загрязняющих и глинистых примесей в количестве более 5% по массе.
Минеральный порошок должен соответствовать требованиям ГОСТ 16557 «Порошок минеральный для асфальтобетонных смесей». Технические условия. Испытание минерального порошка осуществляется по ГОСТ 12784-78 «Порошок минеральный для асфальтобетонных смесей». Методы испытания.
2.1 ОПРЕДЕЛЕНИЕ ЗЕРНОВОГО СОСТАВА ПОРОШКА Аппаратура:
1.Набор сит с сетками № 1,25; 063; 0315; 014; 0071 по ГОСТ 3584-73.
2.Весы лабораторные рычажные по ГОСТ 19491-74.
3.Шкаф сушильный по ГОСТ 7365—55.
4.Эксикатор по ГОСТ 6371-73.
5.Чашка фарфоровая диаметром 10 — 20 см по ГОСТ 9147-73.
6.Пестик с резиновым наконечником.
7.Сосуд емкостью 6 — 10 л.
8.Вода дистиллированная со смачивателем.
Производство определения Пробу активированного порошка массой 100 г отбирают из средней
пробы в воздушно-сухом состоянии, а 100 г неактивированного порошка — из средней пробы, высушенной до постоянной массы при температуре 105 — 110 °С в течение 5 ч и охлажденной в эксикаторе до комнатной температуры.
Пробу минерального порошка помещают в фарфоровую чашку, носик которой снизу смазан вазелином, заливают небольшим количеством воды (с добавкой смачивателя или без смачивателя) и растирают в течение 2 —3 мин пестиком с резиновым наконечником.
Воду со взвешенными в ней частицами сливают на сито с сеткой № 0071, установленное над сосудом. Затем пробу порошка вновь заливают водой, растирают и воду снова сливают.
21
Последовательное растирание частиц и сливание мутной воды продолжают до тех пор, пока вода не станет прозрачной. После промывки попавшие на сито частицы минерального порошка крупнее 0,071 мм переносят в фарфоровую чашку с остатком. Оставшуюся в чашке воду осторожно сливают, а затем чашку ставят в сушильный шкаф для высушивания остатка пробы порошка при температуре 105 — 110 °С до постоянной массы.
Промывание и растирание минерального порошка непосредственно на сите не допускается.
По разности массы взятой пробы и массы остатка устанавливают массу частиц мельче 0,071 мм, прошедших через сито в процессе промывки порошка. Затем остаток пробы порошка просеивают через набор сит, начиная с сита с наибольшим диаметром отверстий, кончая ситом с сеткой № 0071.
Перед окончанием просеивания каждое сито вручную интенсивно встряхивают над листом бумаги в течение 1 мин. Просеивание считают законченным, если количество частиц, прошедших сита с отверстиями размерами 1,25 и 0,63 мм, не превышает 0,05 г, а прошедших сита с отверстиями размерами 0,315; 0,14 и 0,071 мм — 0,02 г.
Остаток на каждом сите взвешивают и определяют частные остатки в процентах по отношению к массе просеиваемой пробы (точность определения 0,1 %).
Общую массу частиц размером 0,071 мм в процентах определяют сложением масс частиц, прошедших данное сито в процессе промывки порошка и при сухом рассеве пробы, оставшейся после промывки.
За результат испытания принимают среднее арифметическое двух определений.
Расхождение между результатами параллельных определений на каждом сите не должно быть более 2 % (от общей массы пробы). Общая потеря порошка при рассеве не должна превышать 2 % от взятой пробы.
2.2 ОПРЕДЕЛЕНИЕ ПЛОТНОСТИ НЕАКТИВИРОВАННОГО ПОРОШКА
Аппаратура:
1.Мерная колба вместимостью 250 см3 или пикнометр
2.Технические или аналитические весы
3.Вакуум - прибор
4.Безводный керосин
22
5.Сито с отверстиями 1,25 и 0,14 мм
6.Фарфоровая чашка
Производство определения
Берут 200г минерального порошка просеивают через сито с отверстиями 1,25 мм, высушивают до постоянной массы из высушенного минерального порошка берут две навески по 70 г, если плотность определяют в мерных колбах вместимостью 250см3 , или по 10 г, если определяют в пикнометре вместимостью 100см3.
В мерную колбу или пикнометр высыпают навески, наливают примерно на 2/3 ее объема безводный керосин, ставят на один час под вакуум , затем заполняют керосином до черты на шейке колбы или пикнометра ( по низу мениска) выдерживают 30 мин при температуре 200 С и, если уровень керосина изменился, то его снова доводят до черты на шейке и взвешивают.
Плотность минерального порошка (г/см 3)определяют по формуле:
ρп = m2 ρk / m2 + m3 - m4 , |
( 1 ) |
Где m2 - масса сухого минерального порошка, г; ρк - плотность керосина при 200С, г/см3;
m 3- масса колбы с керосином при 200 С;
m 4- масса колбы с минеральным порошком и керосином, г. Плотность керосина определяется по формуле:
ρк = m-m1/V , |
( 2 ) |
Где m- масса колбы с керосином при 20+2оС, г; m 1- масса сухой колбы, г;
V - объем колбы см3 .
2.3 ОПРЕДЕЛЕНИЕ СРЕДНЕЙ ПЛОТНОСТИ ПОРОШКА
Аппаратура:
1.Форма для определения средней плотности
2.Поддон
3.Гидравлический пресс
4.Технические весы
23
5.Сито № 1,25
6.Сушильный шкаф
Подготовка к испытанию и проведение испытания 1кг минерального порошка высушивают при 105 - 1100 С и про-
сеивают через сито № 1,25 мм. Берут 300г порошка и постепенно высыпают в форму, установленную на поддон.
В форме порошок распределяют ножом, прижимают вкладышем и уплотняют на гидравлическом прессе, выдерживают ее 3 минуты. После нагрузку снимают и форму вместе с вкладышем ставят на чистый лист бумаги. Затем вкладыш и верхнюю часть формы снимают и минеральный порошок в нижней ( рабочей) части формы срезают ножом.
Излишек минерального порошка взвешивают, а среднюю плотность минерального порошка определяют по формуле:
ρ0 = m - m1 /V, |
( 3 ) |
Где m - первоначальная масса минерального порошка, г; m1 - масса остатка от первоначальной навески, г;
V - объем формы (100 см3 ).
2.4 ОПРЕДЕЛЕНИЕ ПОРИСТОСТИ ПОРОШКА Пористость минерального порошка определяют по формуле:
Υпор= (1- ρ0 / ρп ) *100 |
(4 ) |
Где ρ0 - средняя плотность порошка, г/см3; ρп - плотность минерального порошка, г/см3 .
2.5 ОПРДЕЛЕНИЕ КОЭФФИЦИЕНТА ГИДРОФИЛЬНОСТИ ПОРОШКА Аппаратура:
1.Фарфоровые чашки
2.Цилиндр
3.Палочки с резиновыми наконечниками
24
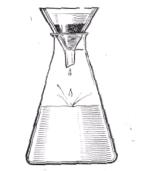
Производство определения
Берут две навески порошка по 5 г (+ 0,01г) и каждую высыпают в фарфоровую чашку. В одну чашку с порошком наливают воду, а в другую - очищенный керосин. Затем порошок в каждой чашке растирают пестиком в течение 5 мин и, смывая в одном случае водой, а в другом керосином, выливают в градуированные цилиндры емкостью по 50 см3.
Уровень воды и керосина в цилиндрах должен быть равен 50 см3 . После того как при спокойном состоянии цилиндров оседание частиц прекратится, отсчитывают объемы осадков и определяют коэффициент гидрофильности по формуле:
η=Vв/Vк
Где Vвобъем минерального порошка в воде;
V к - объем минерального порошка в керосине.
Окончательный результат вычисляют как среднее арифметическое из двух определений. Расхождение между двумя определениями объемов в воде и керосине допускается +- 0,2 мл. Оищенный керосин, требуемый для испытания, получают следующим образом. Берут 500см3 обычного осветительного керосина и на приборе фракционной разгонки отгоняют фракции до 2700 С. Отогнанные фракции небольшими порциями профильтровывают через 200 - 500 г суглинистого грунта, находящегося в бумажном фильтре (рис. 1) . Грунт следует прогреть при 2500 С в течении 3 ч и охладить до 18 - 200СС.
Рис. 1 Прибор для получения очищенного керосина.
25
2.6 ВЫВОДЫ
В результате проведения лабораторной работы необходимо сделать выводы о следующем:
-зерновом составе минерального порошка ;
-средней плотности минерального порошка;
-пористости порошка;
-коэффициенте гидрофильности порошка .
2.7 ОФОРМЛЕНИЕ ОТЧЕТА И ЕГО ЗАЩИТА Отчет должен включать краткое описание хода работы, схемы применяемых приборов и оборудования.
2.8 СПИСОК ИСПОЛЬЗОВАННОЙ ЛИТЕРАТУРЫ
1.ГОСТ 16557 Порошок минеральный для асфальтобетонных смесей. Технические условия.
2.ГОСТ 12784-78 Порошок минеральный для асфальтобетонных смесей. Методы испытания .
3.Горчаков Г .И ., Баженов Ю.М. Строительные материалы .-М.: Стройиздат , 1986.-68с.
4.Леонович И.И. Дорожно-строительные материалы .- Минск .: высшая школа., 1983.-399с.
26
3 РАСЧЕТ И ПОДБОР СОСТАВАГОРЯЧЕГО КРУПНО- И МЕЛКОЗЕРНИСТОГО АСФАЛЬТОБЕТОНА
Асфальтобетоном называют уплотненный материал, приготовленный при соответствующей температуре из смеси щебня (дробленого гравия) песка, минерального порошка и битума, взятых в определенных количествах.
Асфальтовые бетоны применяют в горячем, теплом и холодном состояниях. Горячие и теплые асфальтовые бетоны разделяют в зависимости от наибольшего размера зерен щебня (гравия) на крупнозернистые (до 40мм), среднезернистые (до 20мм), мелкозернистые (до15мм), песчаные (до5мм).
Холодные асфальтовые бетоны бывают мелкозернистыми или песчаными . Различают плотные и пористые асфальтовые бетоны. По способу уплотнения асфальтовые бетоны классифицируются на укатываемые, трамбованные, вибрированные и литые.
В зависимости от производственного назначения различают асфальтовые бетоны дорожные, аэродромные, гидротехнические, кислотостойкие и цветные.
Требования предъявляемые к асфальтовым бетонам должны соответствовать
ГОСТ 9128-97 Смеси асфальтобетонные, дорожные, аэродромные и асфальтобетон.
Технические условия.
Цель работы: Изучение методики расчета и подбора состава асфальтового бетона применяемого в горячем состоянии.
3.1 Требования к материалам для приготовления асфальтобетонной смеси
3.1.1 Нефтяные дорожные битумы.
Для приготовления асфальтобетонных смесей применяют нефтяные дорожные битумы, соответствующие требованиям ГОСТ 22245 - 76 «Битумы нефтяные дорожные вязкие» технические условия и ГОСТ 11955 – 74 «Битумы нефтяные дорожные жидкие». Выбор марки битума должен осуществляться с учетом вида асфальтобетона, климатических условий и категории дороги.
27
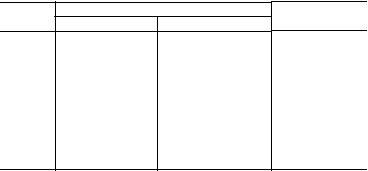
3.1.2. Щебень и гравий.
Для асфальтобетонных смесей применяют щебень из естественного камня, полученный дроблением горных пород, а также щебень из гравия, отвечающих требованиям ГОСТ 8267 - 75, ГОСТ 10260 - 74, ГОСТ 3344 - 73, ГОСТ 8268 -74 . Щебень или гравий должен быть рас-
сортирован по фракциям: 20 - 40, 10 - 20,10 - 15, 5 (3) - 25, 5 (3) - 15, 5(3) - 10 мм.
Пластинчатой (лещадной) формы зерен по массе в щебне не должно быть более 15% для асфальтобетонов типа А и 25% типа Б.
3.1.3 Песок.
Песок применяют природный и дробленый, отвечающий требованиям ГОСТ 8736 - 67. Пылеватых и глинистых частиц в природном песке не должно быть более 3%.Применение мелких песков (Мк < 2.0) для асфальтобетонных смесей марок I и II допускается при условии их обогащения добавкой крупного или дробленого песка. Для приготовления горячих и теплых асфальтобетонных смесей марок III и IV допускается применение природного песка с Мк = 1,0 - 2,0 .
3.1.4 Минеральный порошок.
. Минеральный порошок должен быть сухим и рыхлым. Активированный минеральный порошок должен быть однородным по цвету. Материалы, используемые для приготовления минерального порошка, должны быть чистыми, не содержащими загрязняющих и глинистых примесей в количестве более 5% по массе.
Минеральный порошок должен соответствовать требованиям табл. 1.
Таблица 1
казатели |
Нормы по видам порошка |
активированного неактивированного
ерновой |
|
|
остав, % |
|
|
о массе: |
|
|
льче 1,25 |
100 |
100 |
мм |
|
|
мельче |
95 |
90 |
,315, не |
|
|
менее |
80 |
70 |
мельче |
||
071 мм, |
|
|
показатели |
Нормы по видам порошка |
|
Набухание |
активированного |
неактивированног |
1,5 |
2,5 |
|
смеси мине- |
|
|
рального по- |
|
|
рошка с биту- |
|
|
мом, % по объ- |
|
|
ему, не более |
|
|
Показатель |
|
|
битумоемкости, |
|
|
г /100 см3 (аб- |
50 |
65 |
солютного объ- |
|
|
28

Показатели |
Нормы по видам порошка |
показатели |
Нормы по видам порошка |
||
|
активированного |
неактивированного |
|
активированного |
неактивированн |
не менее |
|
|
ема), не более |
|
|
ористость, |
30 |
35 |
Влажность, % |
|
|
% по объе- |
|
|
по массе, не |
|
|
му, не бо- |
|
|
более |
|
|
лее |
|
|
|
|
|
|
|
|
|
0,5 |
1,0 |
|
|
|
|
|
|
3.2 Расчет и подбор состава асфальтобетонной смеси применяемой в горячем состоянии.
3.2.1. Расчет состава смеси.
Расчет состава смеси заключается в том, чтобы определить наилучшее соотношение между составляющими материалами: щебнем, песком, минеральным порошком и битумом.
Последовательность подбора, заключается в следующем: определяют зерновой состав минеральных материалов ( щебня, песка, минерального порошка) выбирают по табл.2 тип асфальтобетона; определяют соотношения между составляющими минеральными материалами; полученный состав (зерновой) сравнивают с пределами зернового состава согласно выбранному типу асфальтобетона. Если подобранный состав будет в пределах, которые приведены в табл.2 данной строки, то расчет минеральных материалов считают правильным. В противном случае изменяют соотношение между составляющими материалами.
3.2.2.Пример подбора асфальтобетонной смеси.
Требуется подобрать мелкозернистую асфальтобетонную смесь III марки, предназначенную для верхнего слоя дорожного покрытия и уплотняемою в горячем состоянии из следующих материалов: щебня, песка, минерального порошка приготовленного из известняка - ракушечника, и нефтяного битума марки БНД 60/90.
Определяем зерновой состав минеральных материалов и результаты записываем в табл.4.
Из табл.2 выписываем рекомендуемый состав минеральных материалов и записываем в табл.5.
Таблица 2
29
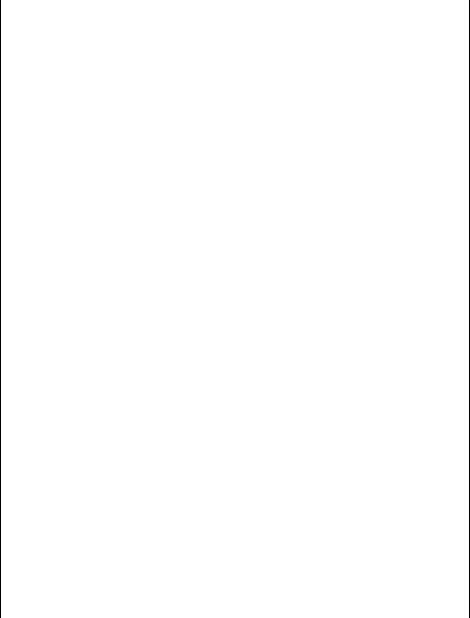
Наименование |
|
Содержание зерен минерального материала, % мельче данного размера, мм |
Примерный |
||||||||||
асфальтобетонных |
40 |
|
20 |
15 |
10 |
5 |
2,5 |
1,25 |
0,63 |
0,315 |
0,14 |
0,071 |
расход |
смесей и тип |
|
|
|
|
|
|
|
|
|
|
|
|
битума, % от |
асфальтобетона |
|
|
|
|
|
|
|
|
|
|
|
|
массы |
|
|
|
|
|
|
|
|
|
|
|
|
|
минеральной |
|
|
|
|
|
|
|
|
|
|
|
|
|
части |
Асфальтобетонные смеси для плотного асфальтобетона, применяемого в верхнем слое покрытия среднезернистые типов:
А |
- |
95- |
78- |
60- |
35- |
24- |
17- |
12- |
9-15 |
6- |
4-10 |
5,0-6,0 |
|
|
100 |
85 |
70 |
50 |
38 |
28 |
20 |
|
11 |
6-12 |
5,0-6,0 |
Б |
- |
95- |
85- |
70- |
50- |
38- |
28- |
20- |
14- |
9- |
||
|
|
100 |
91 |
80 |
65 |
52 |
39 |
29 |
22 |
16 |
8-14 |
6,0-7,0 |
В |
- |
95- |
91- |
80- |
65- |
52- |
39- |
29- |
20- |
12- |
||
|
|
100 |
96 |
90 |
80 |
66 |
53 |
40 |
28 |
20 |
|
|
Мелко зернистые |
|
|
|
|
|
|
|
|
|
|
|
|
типов: |
|
|
|
|
|
|
|
|
|
|
|
|
А |
- |
- |
95- |
63- |
35- |
24- |
17- |
12- |
9-15 |
6- |
4-10 |
5,0-6,0 |
|
|
|
100 |
75 |
50 |
38 |
28 |
20 |
9-15 |
11 |
|
|
А |
- |
- |
- |
95- |
35- |
24- |
17- |
12- |
6- |
4-10 |
5,0-6,0 |
|
|
|
|
|
100 |
50 |
38 |
28 |
20 |
14- |
11 |
|
|
Б |
- |
- |
95- |
75- |
50- |
38- |
28- |
20- |
14- |
9-16 |
5,5-7,0 |
|
|
|
|
100 |
85 |
65 |
52 |
39 |
29 |
22 |
22 |
|
|
Б |
- |
- |
- |
95- |
50- |
38- |
28- |
20- |
14- |
9- |
6-12 |
2,5-7,0 |
|
|
|
|
100 |
65 |
52 |
39 |
29 |
22 |
16 |
|
|
В |
- |
- |
95- |
85- |
65- |
52- |
39- |
29- |
20- |
12- |
8-14 |
6,0-7,0 |
|
|
|
100 |
93 |
80 |
66 |
53 |
40 |
28 |
20 |
|
|
В |
- |
- |
- |
95- |
65- |
52- |
39- |
29- |
20- |
12- |
8-14 |
6,0-7,0 |
|
|
|
|
100 |
80 |
66 |
53 |
40 |
28 |
20 |
|
|
Песчаные типов: |
|
|
|
|
|
|
|
|
|
|
|
|
Г |
- |
- |
- |
- |
95- |
68- |
45- |
28- |
18- |
11- |
8-14 |
7,0-9,0 |
|
|
|
|
|
100 |
83 |
67 |
50 |
35 |
23 |
10- |
7,0-9,0 |
Д |
- |
- |
- |
- |
95- |
74- |
53- |
37- |
27- |
17- |
||
|
|
|
|
|
100 |
93 |
86 |
75 |
55 |
33 |
16 |
|
Среднезернистые |
|
|
|
|
|
|
|
|
|
|
|
|
типов: |
|
|
|
|
|
|
|
|
|
|
|
|
А |
- |
95- |
78- |
60- |
35- |
35- |
35- |
35- |
17- |
8- |
4-10 |
5,0-6,5 |
|
|
100 |
85 |
70 |
50 |
50 |
50 |
50 |
28 |
15 |
6-12 |
5,0-6,5 |
Б |
- |
95- |
85- |
70- |
50- |
50- |
50- |
50- |
28- |
14- |
||
|
|
100 |
91 |
80 |
65 |
65 |
65 |
65 |
40 |
23 |
|
|
Мелкозернистые |
|
|
|
|
|
|
|
|
|
|
|
|
типов: |
|
|
|
|
|
|
|
|
|
|
|
|
А |
- |
- |
95- |
63- |
35- |
35- |
35- |
35- |
17- |
8- |
4-10 |
5,0-6,5 |
|
|
|
100 |
75 |
50 |
50 |
50 |
50 |
28 |
15 |
4-10 |
5,0-6,5 |
А |
- |
- |
- |
95- |
35- |
35- |
35- |
35- |
17- |
8- |
||
|
|
|
|
100 |
50 |
50 |
50 |
50 |
28 |
15 |
6-12 |
5,5-7,0 |
Б |
- |
- |
95- |
75- |
50- |
50- |
50- |
50- |
28- |
14- |
||
|
|
|
100 |
80 |
65 |
65 |
65 |
65 |
40 |
23 |
6-12 |
5,5-7,0 |
Б |
- |
- |
- |
95- |
50- |
50- |
50- |
50- |
28- |
14- |
||
|
|
|
|
100 |
65 |
65 |
65 |
65 |
40 |
23 |
|
|
Асфальтобетонные смеси для пористого асфальтобетона, применяемого в нижних слоях покрытий и в основаниях
Крупнозернистые |
95- |
- |
57- |
45- |
27- |
18- |
10- |
7- |
4-19 |
2- |
0-4 |
4-6 |
|
100 |
|
80 |
73 |
60 |
48 |
37 |
26 |
|
12 |
0-4 |
4-6 |
Среднезернистые |
- |
95- |
68- |
52- |
27- |
18- |
10- |
7- |
4-19 |
2- |
||
|
|
100 |
85 |
76 |
60 |
48 |
37 |
26 |
|
12 |
0-6 |
4-6,5 |
Мелкозернистые |
- |
- |
95- |
67- |
35- |
27- |
18- |
12- |
6-18 |
2- |
||
|
|
|
100 |
85 |
65 |
50 |
38 |
27 |
|
13 |
|
|
Крупнозернистые |
95- |
72- |
60- |
147- |
30- |
30- |
30- |
30- |
30- |
14- |
0-4 |
4-6 |
|
100 |
82 |
72 |
60 |
40 |
40 |
40 |
40 |
40 |
22 |
0-4 |
4-6 |
Среднезернистые |
- |
95- |
72- |
60- |
35- |
35- |
35- |
35- |
22- |
10- |
||
|
|
100 |
88 |
80 |
65 |
65 |
65 |
65 |
44 |
25 |
0-6 |
4-6,5 |
Мелкозернистые |
- |
- |
95- |
70- |
35- |
35- |
35- |
35- |
22- |
10- |
||
|
|
|
100 |
88 |
65 |
65 |
65 |
65 |
44 |
25 |
|
|
30