
- •В зависимости от назначения стального листа и коррозионной реды
- •Общая технологическая схема нанесения защитных покрытий
- •Вторая группа включает собственно операции:
- •Виды и способы нанесения защитных
- •Цинксодержащие композиции
- •Физико-механические характеристики лакокрасочных покрытий
- •Твердость лакокрасочного покрытия - способность пленки противостоять вдавливанию или проникновению в нее твердого
- •Методы нанесения лакокрасочных материалов
- •Распыление:
- •Сушку (отверждение) нанесенных ЛКМ осуществляют при 15-25 °С (холодная, естественная сушка) и при
- •В мировой практике применяют широкую номенклатуру полимерных покрытий,
- •Основное назначение лакового покрытия на белой жести — изоляция ее от соприкосновения с
- •Схема нанесения лака методом наката:
- •Лакирование черной жести
- •В дальнейшем был освоен и коротковолновый диапазон инфракрасного излучения, при котором наблюдается дальнейшее
- •Нанесение пленочных и комбинированных элитных покрытий тонких холоднокатаных полос (в том числе и
- •Жесть — холоднокатаная отожжённая листовая сталь толщиной 0,10 —0,36 мм, с нанесенными защитными
- •В зависимости от состояния луженой поверхности и качества формы листов, белая жесть горячего
- •Техническая характеристика агрегата горячего лужения жести ОАО
- •Окончательное формирование оловянного покрытия осуществляется в жировой ванне с помощью «жировой» машины, помещенной
- •Электролитическое лужение жести
- •Перед лужением черную жесть обрабатывают на АПП. Обработка на АПП включает обрезку утолщенных
- •Далее она поступает на непрерывные агрегаты электролитического лужения
- •На современных агрегатах электролитического лужения применяют химическое и электрохимическое обезжиривание постоянным током.
- •Для лужения применяют щелочные или кислотные электролиты (фенолсульфоновые, галогенидные и щелочные).
- •Для дополнительной защиты жести от коррозии во время транспортировки и хранения на складах,
- •Заключительными операциями являются сортировка и упаковка жести.
- •Алюминирование стальных полос погружением их в расплав появилось в начале 50-х годов прошлого
- •Алюминий на холоднокатаную полосу наносят следующими методами:
- •Мировая практика работы агрегатов горячего алюминирования показала, что для получения качественного алюминиевого покрытия
- •Большинство установок горячего алюминирования листовой стали
- •Расплав в ванне подогревают переменным током и перемешивают. Имеется возможность выводить агрегата и
- •Легирование алюминиевого расплава кремнием (6-8%) и применение отпуска при 400-450°С в течение 1-2
- •Электрофоретическое алюминирование — нанесение алюминиевого порошка на стальную полосу методом электрофореза или в
- •В Японии разработана технология нанесения алюминиевого покрытия на стальную полосу методом порошковой металлургии.
- •В Германии с 1971 г. действует установка для двустороннего напыления алюминия производительностью 15000
- •Гидрографическая печать (аквапринт) («water transfer print», «cubic print», «3D print»).
- •Примеры применения технология гидрографической печати:
- •Технология нанесения пленочного покрытия методом гидрографической печати
- •В практическом применения данная технология выглядит
- •Вкачестве стальной основы для производства хромированной жести используют рулонную черную жесть из низкоуглеродистой
- •Схема расположения основного оборудования реконструированного агрегата подготовки полосы:
- •Созданный и введенный в действие на Лысьвенском металлургическом заводе агрегат предназначен для двустороннего
Окончательное формирование оловянного покрытия осуществляется в жировой ванне с помощью «жировой» машины, помещенной в масляную среду из хлопкового или пальмового масла.
«Жировая» машина состоит из трех пар стальных валков специальной стали и формы. Валки отжимают избыток олова на жести и, кроме того, с помощью специальных щеток из природного талькохлорида с валков снимается накопившееся на их поверхности жидкое олово, что способствует возможности регулировать толщину пократия.
Листы из чистильной машины проходят визуальный осмотр поверхности и поступают в секции укладчиков листов готовой продукции. Каждая секция имеет ленточный транспортер с электромагнитами для удержания листов в подвешенном состоянии при транспортировании.
Электролитическое лужение жести
Примерно 50% всего добываемого олова расходуется на лужение жести.
Оловянные руды найдены во всех частях света, но примерно 60% общих разведанных запасов находится в странах Азии (Малайзия, Таиланд, Индонезия, КНР), 21% в Южной Америке (Бразилия, Боливия), 6% в Африке (Нигерия, Заир), 4% в Австралии и только около 3% в Европе (Великобритания).
Основными потребителями первичного олова являются США, Япония,
Великобритания, Германия, Франция.
Электролитически луженую белую жесть выпускают в соответствии с требованиями ГОСТ 13345 таких марок: ЭЖК (консервная), ЭЖР (разная).
Её подразделяют по степеням твердости (А, В, С, Д), измеряемым на приборе типа супер-Роквелла по ГОСТ 13345.
Для лужения применяют олово марки 01 или 01ПЧ (не менее 99,9% Sn).
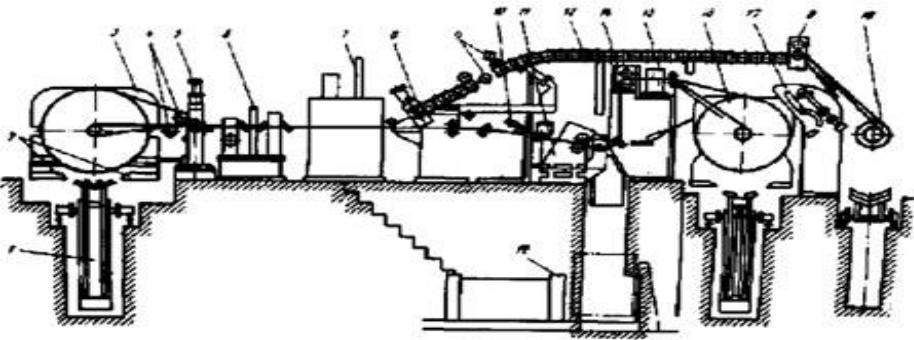
Перед лужением черную жесть обрабатывают на АПП. Обработка на АПП включает обрезку утолщенных и мятых концов полосы, обрезку боковых кромок, вырезку дефектных участков, контроль качества поверхности, трещин жести и наличия проколов, комплектование полновесных рулонов и их взвешивание. Рулоны с большим количеством дефектов возвращают на повторную дрессировку и для удаления дефектов
1— подъемная тележка; 2 — стеллаж; 5 — разматыватель рулонов; 4
— отклоняющие ролики; 5 — подающие ролики; 6—приборный стол; 7 —сварочная машина; 8, 14 — тянущие ролики; 9 — накопитель полосы; 10— натяжное устройство; 11 — дисковые ножницы; 12 — кромкомоталка; 13 — обводной мост; 15 — гильотинные ножницы; 16
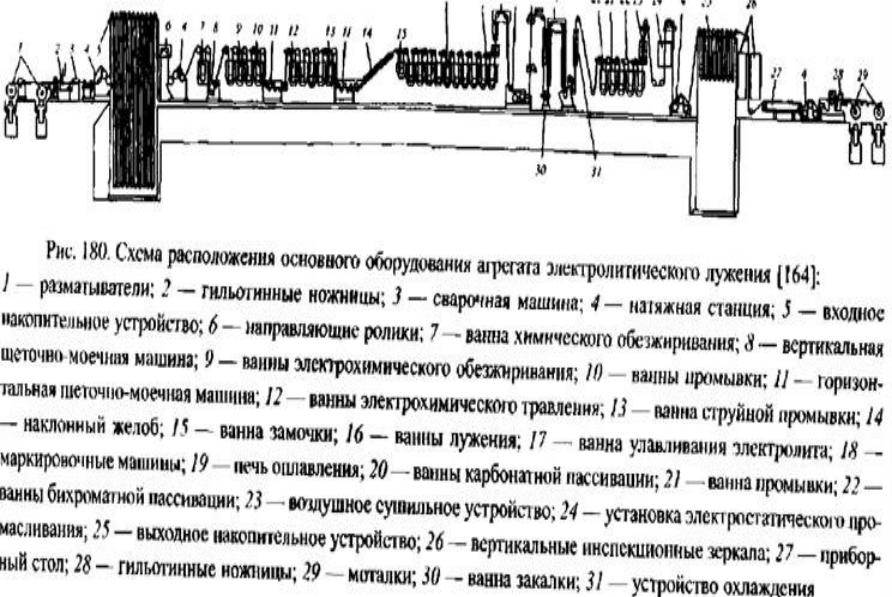
Далее она поступает на непрерывные агрегаты электролитического лужения
На современных агрегатах электролитического лужения применяют химическое и электрохимическое обезжиривание постоянным током.
Химическое обезжиривание производят в щелочном растворе состава, г/л:
Na(OH) —25-30; Na,P04 или Na3P3O10 — 25-30; сульфирол — 1-4. Температура раствора 80—90°С.
После химического обезжиривания полосу подвергают щеточной обработке и промывке холодной водой в щеточно-моечной машине.
Затем полоса поступает в ванны электролитического обезжиривания, которое производят в растворе того же состава, что и при химическом обезжиривании. Механизм процесса сводится к эмульгированию жиров с полосы выделяющимися
на поверхности полосы пузырьками водорода.
После обезжиривания жесть проходит струйную промывку умягченной холодной водой. Промытую полосу подвергают дополнительной щеточной обработке и промывке холодной водой в следующей щеточно-моечной машине, после чего полоса поступает в ванны травления.
Травление осуществляют в электролите состава; H,S04 — 50-100, Fe до 20 г/л при нормальной температуре. Полоса является
катодом, в качестве анода применяются свинцовые пластины.
Для лужения применяют щелочные или кислотные электролиты (фенолсульфоновые, галогенидные и щелочные).
Фенолсульфоновые электролиты агрессивны, ванны и коммуникации требуют защитных покрытий. Состав электролита: олово Sn 25-40 г/л, фенолсульфоновая кислота 50-70 г/л.
Электроосаждение ведется при температуре 35-55С. Анодный процесс сводится к растворению олова, а катодный к электроосаждению его на поверхности стальной полосы. В электролите допускается содержание железа до 15 г/л.
Электролит непрерывно циркулирует между баком и ваннами через теплообменники.
Скорость полосы в технологической части агрегатов составляет 5-9 м/с.
С целью уплотнения оловянных осадков в электролизных ваннах, их подвергают оплавлению при температурах, превышающих температуру плавления олова (232°С), Оплавление осуществляется контактным или индукционным методами. После оплавления луженую ленту подвергают пассивации, в результате которой образуется искусственная окисная пленка (1-5 им), В современных агрегатах электролужения осуществляется катодная пассивация в растворе бихромата натрия, концентрация 20-30 г/л, температура раствора 40-50°С, рН — 4-6. Плотность тока 5-20 А/дм1, время
пассивации 1,5-2 с.
Для дополнительной защиты жести от коррозии во время транспортировки и хранения на складах, а также для предохранения оловянного покрытия от истирания при штабелировке листов, смотке полосы в рулоны и переработке жести у потребителя на поверхность наносят тончайшую пленку масла (5 мг/мг).
До последнего времени для промасливания электролитически луженой жести применяли хлопковое масло, представляющее собой смесь ненасыщенных жирных кислот: линолевой, олеиновой
ипальмитиновой. В процессе работы эти кислоты легко окисляются
иполимеризуются. в результате чего значительно изменяются свойства хлопкового масла. В некоторых случаях свойства масла настолько изменяются, что оно препятствует покрытию жести пищевыми лаками. Состав и свойства хлопкового масла нестабильны; они обусловлены климатом, составом почвы, на которой произрастает хлопок, и наконец, неизбежными отклонениями технологии переработки от установленной.
В связи с этим были подобраны синтетические масла: диоктилсебацинатта и дибутилсебацината. Они состоят из насыщенных двухосновных кислот и поэтому стабильны. Эти масла хорошо совмещаются с лаками и красками.
Заключительными операциями являются сортировка и упаковка жести.
Сортировку белой жести производят в соответствии с требованиями ГОСТа и осуществляют в потоке агрегатов при помощи микрометра, замеряющего толщину жести, и дефектоскопа, определяющего наличие проколов.
Оценку качества поверхности жести осуществляют визуальным осмотром.
Жесть поставляют либо в карточках, либо в рулонах.
Алюминирование стальных полос погружением их в расплав появилось в начале 50-х годов прошлого века в США.
Алюминирование позволяет получить холоднокатаную полосу с более стойким защитным покрытием, чем
цинкование, особенно при температуре вплоть до 800°С и в
атмосфере, содержащей сернистые соединения.
Такая полоса также обладает окалиностойкостью и отражающей способностью.
Такое сочетание защитных свойств позволяет использовать алюминированный прокат в конструкциях, работающих при повышенной температуре, в емкостях для транспортирования агрессивных газов, для изготовления
глушителей и выхлопных устройств двигателей внутреннего
сгорания и т.п..
Алюминий на холоднокатаную полосу наносят следующими методами:
методами погружения в расплав алюминия (горячий способ),
металлизацией — напылением мелких оплавленных частиц алюминия, плакированием — совместной прокаткой листового алюминия и стали,
электрофореза — осаждением алюминиевого порошка на полосу с последующим уплотнением полученного слоя покрытия и т.д.
Достоинства — высокая производительность (продолжительность выдержки в расплаве измеряется секундами-минутами), простота, малые затраты на
организацию производства.
Существенным недостатком нанесения алюминиевого покрытия горячим способом на листовой прокат является ухудшение пластичности стали после алюминирования,
поэтому при совершенствовании технологии основное
внимание уделяется получению металла с достаточной