
Papka_Vz_dlya_bakalavrov_2014g / Анухин В.И. Допуски и посадки 2008
.pdf
вкладышем подшипника, в результате чего возникает гидродинамическое давление, превышающее нагрузку на опору. Цапфа всплывает (рис.1.8). В месте наибольшего сближения цапфы и вкладыша образуется масляный слой толщиной h.
Качество, надежность и долговечность работы подшипника зависят от толщины масляного слоя h, на которую, при прочих равных условиях работы подшипника, будет влиять зазор S (разность между диаметром цапфы и диаметром отверстия вкладыша). Допустим, что зазор S будет очень небольшим, в этом случае величина h также будет маленькой, по ряду причин работа подшипника в таких условиях будет неустойчивой. Теперь пусть зазор S будет достаточно большим, и в этом случае значение h будет маленьким из-за малой подъемной силы гидродинамического клина. Отсюда можно сделать вывод, что для определенных условий работы
|
h |
- |
|
S |
|
h
|
h |
|
|
e |
|
|
|
d |
[hmin ] |
|
|
ω |
|
|
|
|
[Smin ] |
[Smax ] |
S |
имеется некоторый интервал, внутри которого будет существовать надежное всплытие.
Рис. 1.8
Сущность расчета посадки заключается в том, чтобы определить интервал зазоров [ Smin ]...[ Smax ] (см. рис. 1.8), при котором величина всплытия будет не меньше предварительно выбранной допустимо минимальной толщины масляного слоя [ hmin ]. Исходя из сказанного,
найдем величину [ hmin ] и установим зависимость между h и S.
Для обеспечения жидкостного трения необходимо, чтобы микронеровности цапфы и вкладыша не касались при работе подшипника. Это возможно при условии:
[hmin ]≥ RZ1 +RZ2 + ∆ф + ∆P + ∆изг + ∆Д ,
(1.1)
где RZ1, RZ2 - высота неровностей вкладышей подшипника и цапфы вала;
∆ ф, ∆ р - поправки, учитывающие влияние погрешностей формы и расположения цапфы и вкладыша;
∆изг - поправка, учитывающая влияние изгиба вала;
∆Д - добавка, учитывающая разного рода отклонения от принятого режима работы. Для упрощенного расчета можно применять зависимость:
[hmiт ]≥ k (RZ1 + RZ2 + ∆Д ),
(1.2)
где k - коэффициент запаса надежности по толщине масляного слоя (k ≥ 2).
Известна зависимость для среднего удельного давления у гидродинамического подшипника:
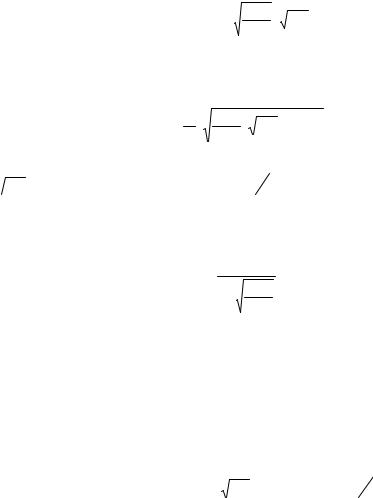
p = |
µ ω D2 |
C |
|
|
|
|
||
|
|
|
|
(1.3) |
||||
|
S2 |
|
|
R , |
|
|
|
|
где µ - динамическая вязкость масла при рабочей температуре подшипника, H c/м2; |
|
|||||||
ω - угловая скорость цапфы рад/c; |
|
|
|
|
|
|
|
|
S - диаметральный зазор, м; |
|
|
|
|
|
|
|
|
D - номинальный диаметр сопряжения, м; |
|
|
|
|
|
|||
CR - безразмерный коэффициент нагруженности подшипника, зависящий от l /D и χ; |
|
|||||||
l - длина подшипника , м; |
|
|
|
|
|
|
|
|
χ - относительный эксцентриситет, который связан зависимостью с h: |
|
|||||||
h = 0.5 S − e = 0.5 S (1 − χ ) |
|
(1.4) |
||||||
Определим из формулы (1.3) значение S: |
|
|
|
|
|
|
|
|
|
S = D |
µ ω |
CR |
. |
|
(1.5) |
||
|
|
|
|
P |
|
|
||
C учетом формулы (1.4) найдем выражение для h: |
|
|
|
|
||||
h = D |
µ ω |
CR |
(1 − χ ) |
. |
(1.6) |
|||
2 |
P |
|
|
|
Значения CR (1 − χ ) = A в зависимости от χ и l D приведены в табл.1.3.
Таким образом, определив минимально допустимую величину всплытия - [ hmin ] по формуле (1.2), мы сможем определить величину A:
A = 2 [ hmin ]
D µ ω
P ,
апо табл. 1.3 значения χmin и χmаx. По найденным значениям χmin и χmаx определим по формуле
1.4.соответственно [ Smin ] и [ Smax ].
Таблица 1.3
χ |
|
|
|
Значение |
CR (1 − χ ) = A при |
l D |
|
|
||
0.6 |
0.7 |
0.8 |
|
0.9 |
1.0 |
1.1 |
1.2 |
1.5 |
2.0 |
|
|
|
|||||||||
|
|
|
|
|
|
|
|
|
|
|
0.30 |
0.299 |
0.339 |
0.375 |
|
0.408 |
0.438 |
0.464 |
0.488 |
0.610 |
0.763 |
0.40 |
0.319 |
0.360 |
0.397 |
|
0.431 |
0.461 |
0.487 |
0.510 |
0.891 |
1.091 |
0.50 |
0.327 |
0.367 |
0.402 |
|
0.434 |
0.462 |
0.487 |
0.508 |
1.248 |
1.483 |
0.60 |
0.324 |
0.361 |
0.394 |
|
0.423 |
0.448 |
0.469 |
0.488 |
1.763 |
2.070 |
0.65 |
0.317 |
0.352 |
0.283 |
|
0.410 |
0.433 |
0.452 |
0.469 |
2.099 |
2.446 |
0.70 |
0.310 |
0.344 |
0.372 |
|
0.369 |
0.417 |
0.434 |
0.450 |
2.600 |
2.981 |
0.75 |
0.298 |
0.328 |
0.351 |
|
0.375 |
0.393 |
0.408 |
0.421 |
3.242 |
3.671 |
|
|
|
|
|
|
|
|
|
|
|
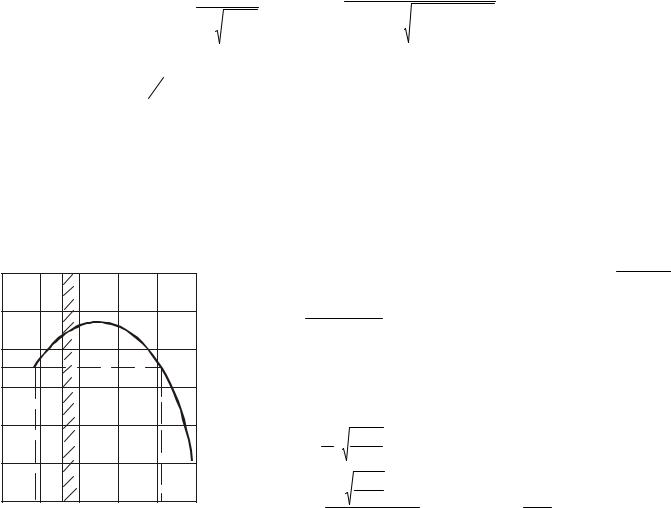
0.80 |
0.283 |
0.310 |
0.332 |
0.350 |
0.367 |
0.378 |
0.389 |
4.266 |
4.778 |
0.85 |
0.261 |
0.284 |
0.302 |
0.317 |
0.329 |
0.339 |
0.341 |
5.947 |
6.545 |
0.90 |
0.228 |
0.246 |
0.245 |
0.210 |
0.279 |
0.286 |
0.292 |
9.304 |
10.09 |
0.95 |
0.178 |
0.188 |
0.196 |
0.202 |
0.207 |
0.211 |
0.215 |
19.68 |
20.97 |
0.99 |
0.091 |
0.095 |
0.096 |
0.098 |
0.100 |
0.101 |
0.101 |
106.8 |
110.8 |
|
|
|
|
|
|
|
|
|
|
Пример
Подобрать посадку для подшипника скольжения, работающего в условиях жидкостного трения при следующих данных: D = 0.075 м, l = 0.075 м, P = 1.47 106 Н/м2, ω = 157 рад/с, масло с динамической вязкостью, при t = 50°С, µ = 19 10-3 Н с/м2. Подшипник половинный.
|
|
|
|
|
Решение |
|
|
|
1. Определение минимально допустимой величины масляного слоя. |
|
|
||||||
|
|
|
|
[ hmin ] = k (RZ1 + RZ2 + ∆Д ) , |
|
|
||
RZ1 = RZ2 |
= 3.2 мкм |
– высоты |
неровностей трущихся поверхностей, выбираются в |
|||||
соответствии с рекомендациями [2]; |
|
|
|
|
||||
∆Д – принимается равной 2…3 мкм: |
|
|
|
|
||||
|
|
[ h |
|
] = 2 (3.2 10−6 + 3.2 10−6 + 3 10−6 ) =18.8 10−6 м |
. |
|||
|
|
min |
|
|
|
|
||
2. Расчет значения А. |
|
|
|
|
|
|
|
|
|
A = |
2 [ hmin ] |
A = |
2 18.8 10−6 |
= 0.352 |
|
||
|
75 10−3 19 10−3 157 |
|
||||||
|
|
µ ω |
|
|
|
|||
|
|
D |
|
|
. |
|||
|
|
|
|
P , |
|
1.47 106 |
|
3. Определение значений χmin и χmаx.
По табл. 1.3 при l D = 1 и А = 0.352 находим: χmin – отсутствует; χmаx = 0.83.
График изменения А от χ приведен на рис. 1.9. Заштрихованная зона - зона надежной работы подшипника, т.е. зона при χmin ≥ 0.3. Поэтому в табл. 1.3 приведены значения только для А при χ ≥ 0.3. В
нашем случае мы должны принять χmin не менее 0.3. Принимаем χmin = 0.3 и соответствующее ему А0.3 = 0.438.
4. Определение [Smin ] и [ Smax ].
|
S = |
2 h |
|
Формулу 1.4 преобразуем для определения зазора: |
1 − χ |
. |
А |
|
|
|
|
|
|
|
|
|
[ Smax ] = |
2 [ hmin ] |
||
|
|
|
|
Максимальный |
зазор: |
1 − χmax ; |
|||||||
|
|
|
|
|
|
|
|
||||||
0.5 |
|
|
|
|
[S |
] = 2 18.8 10−6 |
≈ 221 10−6 |
|
|
|
|
||
|
|
|
|
|
max |
|
1 −0.83 |
м. |
|
|
|
|
|
0.4 |
|
|
|
|
|
|
|
|
|
|
|||
|
|
|
|
|
|
|
|
[Smin ] = |
2 [ hmin ] |
|
|
|
|
0.352 |
|
|
|
|
|
|
|
|
|
|
|
||
|
|
|
|
Минимальный |
1 − χmin |
, |
так |
как был |
|||||
|
|
|
|
зазор: |
|||||||||
0.3 |
|
|
|
|
принят больший относительный эксцентриситет, значение h в |
||||||||
0.2 |
|
|
|
|
данном случае не равно [ hmin ]: |
|
|
|
|
||||
|
|
|
|
|
h = D |
µ ω |
|
|
|
|
|
||
0.1 |
|
|
|
|
|
A |
|
|
|
|
|||
|
|
|
|
|
|
2 |
P |
0.3 ; |
|
|
|
|
|
|
|
|
|
|
|
|
D |
µ ω A |
|
|
|
|
|
0 |
|
|
|
|
|
|
|
P |
0.3 |
] A0.3 |
|
|
|
χ min |
0.3 |
0.6 |
χmax χ |
[Smin ] = |
= 2.857 [ hmin |
|
|
|
|||||
|
|
|
|
1 − χmin |
A |
|
|
|
|||||
|
|
|
|
|
[S |
min |
] = 2.857 18.8 10−6 0.436 ≈ 67 10−6 |
|
|
|
|||
|
|
|
|
|
|
|
|
0.352 |
м. |
|
|
|
|
|
|
|
|
Рис. 1.9 |
|
|
|
|
|
|
|
||
|
|
|
|
|
|
|
|
|
|
|
|
|

5. Выбор посадки.
По [Smin ] = 67 мкм находим, что наиболее близкий вид посадки в системе отверстия : H/e c
минимальным зазором : Smin = 60 мкм.
Допуск посадки с учетом коэффициента запаса точности на износ подшипника скольжения KЗ
= 2 :
TS = |
[Smax ] −Smin |
; |
TS = |
221 −60 |
= 80,5 |
|
|
||||
|
Kз |
|
2 |
мкм. |
6. Определение квалитета.
Известно, что TS =Td +TD . Подберем квалитеты так, чтобы сумма допусков была близка к 80 мкм. Наиболее близко соответствует этим условиям предпочтительная посадка:
H7( +0.030 )75 e8 (−−0.1060.060 )
1.7Посадки переходные
1.7.1Особенности посадок
1.7.2 Области применения некоторых рекомендуемых переходных посадок
Посадки H/js; Js/h - «плотные». Вероятность получения натяга P(N) ≈ 0.5...5%, и, следовательно, в сопряжении образуются преимущественно зазоры. Обеспечивают легкую собираемость.
Посадка |
H7/js6 |
применяется для сопряжения стаканов подшипников с корпусами, |
небольших шкивов и ручных маховичков с валами. |
||
Посадки |
H/k; K/h - |
«напряженные». Вероятность получения натяга P(N) ≈ 24...68%. Однако |
из-за влияния отклонений формы, особенно при большой длине соединения, зазоры в большинстве случаев не ощущаются. Обеспечивают хорошее центрирование. Сборка и разборка производится без значительных усилий, например, при помощи ручных молотков.
Посадка |
H7/k6 |
широко применяется для сопряжения зубчатых колес, шкивов, маховиков, |
муфт с валами. |
|
|
Посадки |
H/m; |
M/h - «тугие». Вероятность получения натяга P(N) ≈ 60...99,98% . Обладают |

высокой степенью центрирования. Сборка и разборка осуществляется при значительных усилиях. Разбираются, как правило, только при ремонте.
Посадка H7/m6 применяется для сопряжения зубчатых колес, шкивов, маховиков, муфт с валами; для установки тонкостенных втулок в корпуса, кулачков на распределительном валу.
Посадки H/n ; N/h - «глухие». Вероятность получения натяга P(N) ≈ 88...100%. Обладают высокой степенью центрирования. Сборка и разборка осуществляется при значительных усилиях: применяются прессы. Разбираются, как правило, только при капитальном ремонте.
Посадка H7/n6 применяется для сопряжения тяжело нагруженных зубчатых колес, муфт, кривошипов с валами, для установки постоянных кондукторных втулок в корпусах кондукторов, штифтов и т.п.
1.7.3 Расчет переходных посадок
Расчеты переходных посадок выполняются редко и в основном как проверочные. Расчеты могут включать:
•расчет вероятности получения зазоров и натягов в соединении;
•расчет наибольшего зазора по известному предельно допустимому эксцентриситету соеди-няемых деталей;
•расчет прочности сопрягаемых деталей от действия сил, возникающих при сборке (только для тонкостенных втулок).
1.8Посадки с натягом
1.8.1Особенности посадок
•В сопряжении образуются только натяги. На рис. 1.11 приведена в сокращении схема распо-ложения полей допусков посадок с натягом в системе отверстия для размеров до 500 мм.
•Посадки применяются только в точных квалитетах.
•Они используются для передачи крутящих моментов и осевых сил без дополнительного кре-пления, а иногда для создания предварительно напряженного состояния у сопрягаемых деталей.
•Посадки предназначены для неподвижных и неразъемных соединений. Относительная не-подвижность деталей обеспечивается силами трения, возникающими на контактирующих поверхно-стях вследствие их упругой деформации, создаваемой натягом при сборке соединения.
•Преимущество посадок - отсутствие дополнительного крепления, что упрощает конфигура-цию деталей и их сборку. Посадки обеспечивают высокую нагрузочную способность сопряжения, ко-торая резко возрастает с увеличением диаметра сопряжения.
•В то же время прочность и качество сопряжения зависят от материала сопрягаемых деталей, шероховатостей их поверхностей, формы, способа сборки (сборка под прессом или способ термиче-ских деформаций) и т.п.
Рис. 1.11 1.8.2 Области применения некоторых рекомендуемых посадок с натягом

Посадки H/p; P/h - «легкопрессовые». Имеют минимальный гарантированный натяг. Обладают высокой степенью центрирования. Применяются, как правило, с дополнительным креплением.
Посадка H7/p6 применяется для сопряжения тяжело нагруженных зубчатых колес, втулок, установочных колец с валами, для установки тонкостенных втулок и колец в корпуса.
Посадки H/r; H/s; H/t и R/h; S/h; T/h - «прессовые средние». Имеют умеренный гарантированный натяг в пределах N = (0.0002...0.0006)D. Применяются как с дополнительным креплением, так и без него. При сопряжении возникают, как правило, упругие деформации.
Посадки H7/r6 , H7/s6 применяются для сопряжения зубчатых и червячных колес с валами в условиях тяжелых ударных нагрузок с дополнительным креплением (для стандартных втулок подшипников скольжения предусмотрена посадка H7/r6).
Посадки H/u; H/x; H/z и U/h - «прессовые тяжелые». Имеют большой гарантированный натяг в пределах N = (0.001...0.002)D. Предназначены для соединений, на которые воздействуют большие, в том числе и динамические нагрузки. Применяются, как правило, без дополнительного крепления соединяемых деталей. В сопряжении возникают упругопластические деформации. Детали должны быть проверены на прочность.
Посадки H7/u7; H8/u8 наиболее распространенные из числа тяжелых посадок. Примеры применения: вагонные колеса на осях, бронзовые венцы червячных колес на стальных ступицах, пальцы эксцентриков и кривошипов с дисками.
1.8.3 Расчет посадок с натягом
У посадок с натягом неподвижность сопрягаемых деталей под действием нагрузок обеспечивается силами трения, возникающими при упругой деформации деталей, создаваемой натягом. Минимальный допускаемый натяг определяется исходя из возможных наибольших сил, действующих на сопряжение, а максимальный натяг рассчитывается из условий прочности деталей.
Разность между диаметром вала и внутренним диаметром втулки до сборки называется натягом N. При запрессовке деталей происходит растяжение втулки на величину ND (рис. 1.12) и
одновременно сжатие вала на величину Nd , при этом:
N = ND+Nd. |
(1.7) |
A-A
A
N d 2
A
ND 2
N 2
d 2
d1 |
D |
Рис. 1.12
Известны зависимости:

ND |
= p |
C1 |
; |
Nd |
= p |
C2 |
, |
|
D |
|
|
|
(1.8) |
||||
|
E1 |
D |
E2 |
где р – давление на поверхности контакта сопрягаемых деталей, Н/м2; D – номинальный диаметр, м;
E1, E2 – модули упругости материала втулки и вала, H/м2; C1, C2 – коэффициенты, определяемые по формулам:
|
|
|
|
D |
2 |
|
|
|
|
|
d1 |
|
2 |
|
|
|
||||
|
|
|
|
|
|
|
|
|
|
|
|
|
|
|||||||
|
1 + |
|
|
|
|
|
1 |
+ |
|
|
|
|
|
|
|
|||||
|
|
|
|
|
|
|
|
|
||||||||||||
|
|
|
|
|
|
|
|
|
|
|
||||||||||
C |
= |
|
d2 |
|
+ µ ; |
C |
2 |
= |
|
D |
|
− µ |
2 |
, |
||||||
|
|
|
|
|
|
|
|
|
|
|
||||||||||
1 |
|
|
D |
2 |
1 |
|
|
|
d |
2 |
|
|||||||||
|
1 |
− |
|
|
|
|
|
1 − |
1 |
|
|
|
|
|
|
|||||
|
|
|
|
|
|
|
|
|
|
|||||||||||
|
|
|
|
|
|
|
|
|
|
|||||||||||
|
|
|
|
|
|
|
|
|
D |
|
|
|
(1.9) |
|||||||
|
|
|
d2 |
|
|
|
|
|
|
|
|
|
где d1, d2 – диаметры (см. рис.1.10), м;
µ1, µ2 – коэффициенты Пуассона (для стали µ ≈ 0.3, для чугуна µ ≈ 0.5). Подставив в выражение (1.7) зависимости (1.8), получим:
C1 |
|
C2 |
|
|
||
N = p D |
|
+ |
|
|
|
|
E |
E |
2 |
(1.10) |
|||
1 |
|
|
. |
Наименьший натяг рассчитывается следующим образом:
C1 |
|
C2 |
|
|
||
Nmin = pmin D |
|
+ |
|
|
|
|
E |
E |
2 |
(1.11) |
|||
1 |
|
|
, |
Минимальное давление на поверхность контакта рmin определяется из условия обеспечения неподвижности сопряжения при действии на него:
•• максимальной осевой силы P :
pmin ≥ |
P |
|
|
π D l f |
, |
(1.12) |
|
|
1 |
где f1 – коэффициент трения при продольном смещении деталей;
l– длина сопряжения;
•• максимального крутящего момента Mкр :
pmin |
≥ |
2 Mкр |
|
|
|
π D2 l f2 , |
(1.13) |
||||
|
|
где f2 – коэффициент трения при относительном вращении деталей;
•• крутящего момента Mкр и осевой силы P :
|
2 M |
кр |
|
2 |
|
|
|
|
|
||
|
|
|
|
|
+ P 2 |
|
|
|
|
||
|
|
|
|
|
|
|
|
||||
|
|
D |
|
|
|
|
|
|
|
|
|
pmin ≥ |
|
|
|
|
|
|
|
|
|
||
|
|
π D l f |
. |
|
|
|
(1.14) |
||||
|
|
|
|
|
|
||||||
Наибольший натяг: |
|
|
|
|
|
|
|
|
|
|
|
|
|
|
|
|
|
|
C1 |
|
C2 |
|
|
Nmax |
|
|
|
|
+ |
|
|||||
|
|
|
E |
|
|||||||
= pmax D |
E |
2 |
|
||||||||
|
|
|
|
|
|
|
1 |
|
|
. |
Максимальное давление рmax определяется из условия прочности сопрягаемых деталей. В качестве pmax берется меньшее из допустимых значений давлений – рдоп, которые рассчитываются по следующим формулам:
|
|
D |
|
|
|
D |
|
|
2 |
||||
|
|
|
|
|
|
|
|||||||
|
|
|
|
|
|
|
|||||||
|
|
|
|
|
|
||||||||
pдоп ≤ 0.58 σT |
1 |
− |
|
|
|
|
|
|
|||||
для втулки |
|
|
|
|
d2 |
|
|
|
|||||
|
|
|
|
|
|
|
|
|
|
|
|
, |
|
|
≤ 0.58 σ |
d |
|
|
|
d1 |
|
|
2 |
|
|||
p |
|
|
|
|
|
|
|||||||
|
|
|
|
||||||||||
доп |
|
T |
|
|
|
D |
|
|
|
|
|||
для вала |
|
|
|
|
|
|
|
|
|
|
|
|
, |
где σTD ; σTd – пределы текучести материала деталей при растяжении, H/м2 .
Пример
Подобрать посадку с натягом для соединения при следующих данных : D = 0.185 м, d1 = 0.110
м, d2 = 0.265 м, l = 0.17 м.
Соединение нагружено осевой силой P = 392 103 H. Детали изготовлены из стали 40,
E1 = E2 = 206 ГПа , σm = 313 МПа, f1 = 0.14, Rz1 = Rz2 = 8 мкм.
Решение
1. 1. Определение коэффициентов C1, C2 .
|
|
|
|
|
D |
|
2 |
|
|
|
|
|
|
0.185 |
2 |
|
|||||
|
|
|
|
|
|
|
|
|
|
|
|
1 + |
|
|
|
||||||
|
|
|
|
|
|
|
|
|
|
|
|||||||||||
|
1 + |
|
|
|
|
|
|
|
|
||||||||||||
C |
= |
|
|
d2 |
|
|
+ µ ; |
C |
= |
|
|
0.265 |
|
|
+ 0.3 ≈ 3.2; |
||||||
|
|
|
|
|
|
|
|
|
|
|
|
|
|
|
|||||||
1 |
|
|
|
|
D |
|
2 |
1 |
1 |
|
|
|
0.185 |
2 |
|
||||||
|
|
|
|
|
|
|
|
|
|
|
1 − |
|
|
|
|||||||
|
|
|
|
|
|
|
|
|
|
|
|||||||||||
|
1 − |
|
|
|
|
|
|
|
|
|
0.265 |
|
|
||||||||
|
|
|
|
d2 |
|
|
|
|
|
|
|
|
|
||||||||
|
1 |
d |
|
2 |
|
|
|
1 |
|
0.110 |
2 |
|
|||||||||
|
+ |
1 |
|
|
|
|
|
+ |
0.185 |
|
|
||||||||||
C |
= |
|
|
|
D |
|
|
|
− µ ; |
C |
= |
|
|
|
|
−0.3 ≈1.8. |
|||||
|
|
|
|
|
|
|
2 |
|
|
|
|
|
|
2 |
|||||||
2 |
|
|
|
d |
|
1 |
2 |
|
|
|
|
0.110 |
|
||||||||
|
1 |
− |
1 |
|
|
|
|
|
|
1 − |
|
|
|
|
|||||||
|
D |
|
|
|
|
|
0.185 |
|
|||||||||||||
|
|
|
|
|
|
|
|
|
|
|
|
|
|
|
|
2. Расчёт наименьшего натяга.
|
|
|
|
|
|
|
|
|
P |
|
|
|
|
|
|
C2 |
|
|
|
|
||
|
|
|
|
|
|
|
|
|
|
|
C1 |
|
|
|
|
|
||||||
|
|
|
|
|
Nmin = |
|
|
|
|
|
+ |
|
|
|
|
|
|
|||||
|
|
|
|
|
π |
l f |
E |
E |
2 |
|
|
|
||||||||||
|
|
|
|
|
|
|
|
|
1 |
|
|
1 |
|
|
; |
|
|
|
||||
|
|
|
392 10 |
3 |
|
|
3,2 |
|
|
|
|
|
1,8 |
|
|
|
=127 10−6 |
|
||||
N |
min |
= |
|
|
|
|
|
+ |
|
|
|
|
м |
|||||||||
|
|
|
|
|
11 |
|
|
|
|
|
11 |
|||||||||||
|
|
π 0,17 |
0,14 |
|
2,06 10 |
|
|
2,06 10 |
|
|
. |
|||||||||||
|
|
|
|
|
|
|
|
|
|
|
В процессе запрессовки неровности на поверхностях детали сминаются, и в соединении создается меньший натяг, поэтому следует расчетный Nmin увеличить на значение поправки:
u = 0.8 (Rz1 + Rz2 ),
u = 0.8 (8 + 8)=12.8 мкм.
Наименьший натяг:
Nminр =127 +12.8 ≈140 мкм.
3.Определение допустимых значений давления.
|
|
|
|
|
|
|
|
|
D |
|
2 |
|
|
|
|
|
|
|
|
|
|
|||||
|
|
|
|
|
|
|
|
|
|
|
|
|
|
|
|
|
|
|
||||||||
|
|
pдоп = 0.58σT |
|
|
|
|
|
|
, |
|
|
|
|
|
|
|
|
|||||||||
|
|
|
|
|
|
|
|
|
|
|
|
|
|
|
|
|
||||||||||
|
|
|
1 |
− |
|
|
|
|
|
|
|
|
|
|
|
|
|
|
||||||||
|
|
|
|
|
|
|
|
d2 |
|
|
|
|
|
|
|
|
|
|
|
|||||||
|
|
|
|
|
|
|
|
|
|
|
|
|
|
|
|
|
|
|
|
|
|
|
|
|
|
|
|
|
|
|
|
|
|
|
|
|
|
|
6 |
|
|
|
|
0.185 |
2 |
|
|
||||||
|
|
pдоп = 0.58 313 10 |
|
|
|
|
|
|
= 93.1 МПа; |
|||||||||||||||||
|
|
|
|
1 − |
0.265 |
|
|
|
||||||||||||||||||
для втулки: |
|
|
|
|
|
|
|
|
|
|
|
|
|
|
|
|
|
|
|
|
||||||
|
|
|
|
|
|
|
|
|
|
|
|
|
|
|
|
|
|
|
|
|
|
|
|
|
|
|
|
|
|
|
|
d1 |
|
|
2 |
|
|
|
|
|
|
|
|
|
|
|
|
|
|
|
|||
p |
|
= 0.58σ |
|
|
|
|
|
, |
|
|
|
|
|
|
|
|
|
|
|
|
||||||
|
|
|
|
|
|
|
|
|
|
|
|
|
|
|
|
|
||||||||||
|
доп |
|
T |
|
|
D |
|
|
|
|
|
|
|
|
|
|
|
|
|
|
|
|
|
|
||
|
|
|
|
|
|
|
|
|
|
|
|
|
|
|
|
|
|
|
|
|
|
|
|
|
|
|
|
|
|
|
|
|
6 |
|
|
|
|
0.110 |
2 |
|
|
|
|
|
|
||||||||
pдоп = 0.58 313 10 |
|
|
|
|
|
|
=117.4 МПа. |
|||||||||||||||||||
|
1 − |
0.185 |
|
|
|
|||||||||||||||||||||
для вала: |
|
|
|
|
|
|
|
|
|
|
|
|
|
|
|
|
|
|
||||||||
|
|
|
|
|
|
|
|
|
|
|
|
|
|
|
|
|
|
|
|
|
|
|
|
|
4. Определение максимально допустимого натяга для данного сопряжения.
р |
|
|
C2 |
|
||
C1 |
|
|
||||
Nmax = pmax D |
|
+ |
|
|
|
|
E |
E |
2 |
||||
|
1 |
|
|
; |
p |
|
6 |
|
|
|
3,2 |
|
|
1,8 |
|
|
|
|
−6 |
|
|
|
|
|
|
|
|
|
|
|
|
|
|
|
||||
Nmax = 93,1 10 |
|
|
0,185 |
|
|
2,06 10 |
11 + |
2,06 10 |
11 |
|
= 418 10 |
|
м |
|||
|
|
|
|
|
|
|
|
|
|
|
|
|
|
. |
||
5. Выбор посадки. |
|
|
|
|
|
|
|
|
|
|
|
|
|
|
|
|
По ГОСТ 25347-82 выбираем посадку: |
|
|
|
|
|
|
|
|
|
|
|
|
||||
185 H8 ( |
+0.072 |
) ; |
|
|
Nmax = 308 мкм < Nmaxр |
= 418 мкм; |
||||||||||
|
|
|
|
Nmin =164 мкм > Nminр |
|
|
|
|||||||||
u8 (++0.2360.308 ) |
|
|
|
=140 мкм. |
1.9 Рекомендации по выбору посадок гладких соединений
1. В первую очередь следует выбирать посадки для наиболее ответственных и точных сопряжений, определяющих качество работы узла.
Например, на узле (см. рис. П.8.2) вначале выбираются посадки подшипников качения, затем посадка зубчатого колеса на вал и посадка стакана в корпусе, а уже затем посадка, связанная с установкой уплотнения, посадка проставочного кольца и крышки подшипника.
2. При назначении посадок необходимо применять соответствующие стандарты и нормативно-технические документы, устанавливающие виды посадок, предельные отклонения и порядок их выбора.
Например, выбор посадок подшипников качения, посадок типовых соединений (шпоночных, шлицевых, резьбовых и т.д.), назначение предельных отклонений для деталей уплотнительных элементов, сопрягаемых со стандартной манжетой и т.п.
3. Перед выбором посадки необходимо определить:
o характер сопряжения (подвижное или неподвижное);
o основные конструктивные требования, предъявляемые к сопряжению (скорость относительного перемещения деталей, компенсация погрешностей монтажа, необходимость центрирования сопрягаемых деталей или величина и характер нагрузок, передаваемых сопряжением).
4. После выбора вида посадки необходимо решить вопрос о точности выполнения сопряжения. При этом не следует забывать, что излишне высокая точность выполнения деталей ведет к значительным и неоправданным затратам при их изготовлении.
Выбор квалитета зависит:
o от точностных требований непосредственно к сопряжению;
o от типа выбранной посадки, например, при применении переходных посадок изменение квалитета незначительно;
o от точности, обусловленной эксплуатационным назначением механизма или машины в целом, особенно это относится к ответственным сопряжениям, например, точность сопряжения деталей в коробке скоростей прецизионного станка может значительно отличаться от точности посадок аналогичных деталей в коробке скоростей трактора.
В общих чертах можно указать на следующее применение квалитетов.
Квалитеты 4-й и 5-й применяются сравнительно редко, в особо точных соединениях, требующих высокой однородности зазора или натяга (приборные подшипники в корпусах и на валах, высокоточные зубчатые колеса на валах и оправках в измерительных приборах).
Квалитеты 6-й и 7-й применяются для ответственных соединений в механизмах, где к посадкам предъявляются высокие требования в отношении определенности зазоров и натягов для обеспечения точности перемещений, плавного хода, герметичности соединения, механической прочности сопрягаемых деталей, а также для обеспечения точной сборки деталей (подшипники качения нормальной точности в корпусах и на валах, зубчатые колеса высокой и средней точности на валах, подшипники скольжения и т.п.).
Квалитеты 8-й и 9-й применяются для посадок при относительно меньших требованиях к однородности зазоров или натягов и для посадок, обеспечивающих среднюю точность сборки (посадки с зазором для компенсации погрешностей формы и расположения сопрягаемых поверхностей, опоры скольжения средней точности, посадки с большими натягами).
Квалитет 10-й применяется в посадках с зазором и в тех же случаях, что и 9-й, если условия эксплуатации допускают некоторое увеличение колебания зазоров в соединениях.
Квалитеты 11-й и 12-й применяются в соединениях, где необходимы большие зазоры и допустимы их значительные колебания (грубая сборка). Эти квалитеты распространены в неответственных соединениях машин (крышки, фланцы, дистанционные кольца и т.п.).
2.ДОПУСКИ И ПОСАДКИ ТИПОВЫХ СОЕДИНЕНИЙ
2.1Шпоночные соединения
Шпоночные соединения предназначены для соединения с валами зубчатых колес, шкивов, махо-виков, муфт и других деталей и служат для передачи крутящих моментов. Наиболее часто применяются соединения с призматическими шпонками. Размеры, допуски, посадки и предельные отклонения соединений с призматическими шпонками установлены ГОСТ 23360-78*.
2.1.1 Основные размеры соединений с призматическими шпонками