
- •Remote and chemical seals
- •Filled impulse lines
- •Purged impulse lines
- •Water traps and pigtail siphons
- •Mounting brackets
- •Heated enclosures
- •Process/instrument suitability
- •Review of fundamental principles
- •Continuous level measurement
- •Level gauges (sightglasses)
- •Basic concepts of sightglasses
- •Interface problems
- •Temperature problems
- •Float
- •Hydrostatic pressure
- •Bubbler systems
- •Transmitter suppression and elevation
- •Compensated leg systems
- •Tank expert systems
- •Hydrostatic interface level measurement
- •Displacement
- •Torque tubes
- •Displacement interface level measurement
- •Echo
- •Ultrasonic level measurement
- •Radar level measurement
- •Laser level measurement
- •Magnetostrictive level measurement
- •Weight
- •Capacitive
- •Radiation
- •Level sensor accessories
- •Review of fundamental principles
- •Continuous temperature measurement
- •Bi-metal temperature sensors
- •Filled-bulb temperature sensors
- •Thermistors and Resistance Temperature Detectors (RTDs)
- •Proper RTD sensor connections
- •Thermocouples
- •Dissimilar metal junctions
- •Thermocouple types
- •Connector and tip styles
- •Manually interpreting thermocouple voltages
- •Reference junction compensation
- •Law of Intermediate Metals
- •Software compensation
- •Extension wire
- •Burnout detection
- •Non-contact temperature sensors
- •Concentrating pyrometers
- •Distance considerations
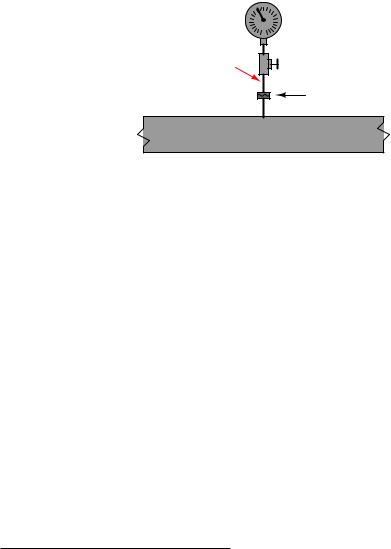
1374 |
CHAPTER 19. CONTINUOUS PRESSURE MEASUREMENT |
A solution to this problem is to fill the pressure sensor mechanism with a clean liquid (called a fill fluid ) and use that fill fluid to transfer pressure from the process fluid to the pressure-sensing element using a slack diaphragm or some other membrane separating the process fluid from the fill fluid:
|
Pressure gauge |
Filled with |
Needle valve |
clean fluid |
(partially open) |
|
Isolating diaphragm |
Pipe |
|
It should be noted that most pressure snubbers utilize a fixed-geometry orifice rather than an adjustable needle valve to dampen pressure pulsations seen at the pressure gauge.
In order for the fill fluid and isolating diaphragm to work e ectively, there cannot be any gas bubbles in the fill fluid – it must be a “solid” hydraulic system from the diaphragm to the sensing element. Gas bubbles present in the filled system would make that volume compressible, which means the isolating diaphragm would have to move more than necessary to transfer pressure to the instrument’s sensing element. This would mean motion at the isolating diaphragm caused by process pressure changes would be “lost” and not fully transferred to the instrument’s sensing element, thereby introducing a pressure measurement error21. For this reason, isolating diaphragm systems for pressure instruments are usually “packed” with fill fluid at the point and time of manufacture, then sealed in such a way that they cannot be opened for any form of maintenance. Consequently, any fill fluid leak in such a system immediately ruins it.
21This concept will be immediately familiar to anyone who has ever had to “bleed” air bubbles out of an automobile brake system. With air bubbles in the system, the brake pedal has a “spongy” feel when depressed, and much pedal motion is required to achieve adequate braking force. After bleeding all air out of the brake fluid tubes, the pedal motion feels much more “solid” than before, with minimal motion required to achieve adequate braking force. Imagine the brake pedal being the isolating diaphragm, and the brake pads being the pressure sensing element inside the instrument. If enough gas bubbles exist in the tubes, the brake pedal might stop against the floor when fully pressed, preventing full force from ever reaching the brake pads. Likewise, if the isolating diaphragm hits a hard motion limit due to gas bubbles in the fill fluid, the sensing element will not experience full process pressure.
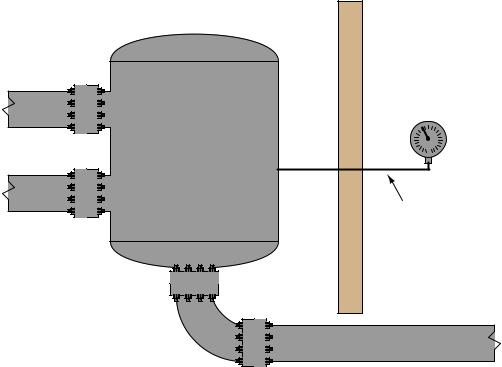
19.6. PRESSURE SENSOR ACCESSORIES |
1375 |
19.6.4Remote and chemical seals
Isolating diaphragms have merit even in scenarios where pressure pulsations are not a problem. Consider the case of a food-processing system where we must remotely measure pressure inside a mixing vessel:
Wall
Pressure gauge
Vessel
Tube
The presence of the tube connecting the vessel to the pressure gauge poses a hygiene problem. Stagnant process fluid (in this case, some liquid food product) inside the tube will encourage microbial growth, which will eventually contaminate the vessel no matter how well or how often the vessel is cleaned. Even automated Clean-In-Place and Steam-In-Place (CIP and SIP, respectively) protocols where the vessel is chemically purged between batches cannot prevent this problem because the cleaning agents never purge the entire length of the tubing (ultimately, to the bourdon tube or other sensing element inside the gauge).
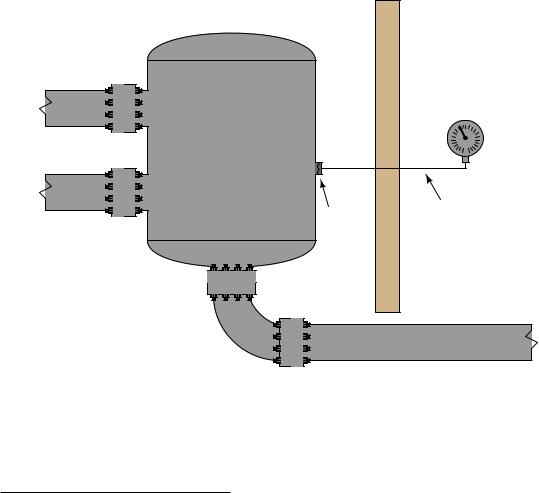
1376 |
CHAPTER 19. CONTINUOUS PRESSURE MEASUREMENT |
A solution to this problem is to install an isolating diaphragm at the vessel, and a liquid-filled capillary tube to transfer sensed pressure to the instrument. Process pressure presses against this diaphragm, which in turn transfers22 pressure to the “fill fluid” inside the capillary tube. This sealed fill fluid then presses against the instrument’s sensing element (diaphragm, bourdon tube, bellows, etc.). Process (food) liquid cannot enter this sealed tube, and the isolating diaphragm will be cleaned with every CIP cycle. Thus, we completely eliminate the problem of microbial contamination:
Vessel
Wall
Pressure gauge
Isolating
Capillary tubing
diaphragm
(with fill fluid)
Such systems are often referred to as remote seals, and they are available on a number of di erent pressure instruments including gauges, transmitters, and switches. If the purpose of an isolating diaphragm and fill fluid is to protect the sensitive instrument from corrosive or otherwise harsh chemicals, it is often referred to as a chemical seal.
22So long as the isolating diaphragm is “slack” (i.e. has no appreciable tautness or resistance to movement), the pressure of the fill fluid inside the capillary tube will be equal to the pressure of whatever fluid is within the process vessel. If any pressure imbalance were to develop between the process and fill fluids, the isolating diaphragm would immediately shift position away from the higher-pressure fluid and toward the lower-pressure fluid until equal pressures were re-established. In real practice, isolating diaphragms do indeed have some sti ness opposing motion, and therefore do not perfectly transfer pressure from the process fluid to the fill fluid. However, this pressure di erence is usually negligible.
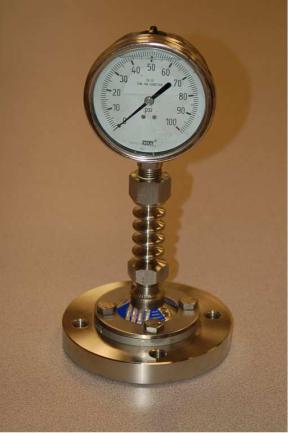
19.6. PRESSURE SENSOR ACCESSORIES |
1377 |
The following photograph shows a pressure gauge equipped with a chemical seal diaphragm. Note that the chemical seal on this particular gauge is close-coupled to the gauge, since the only goal here is protection of the gauge from harsh process fluids, not the ability to remotely mount the gauge:
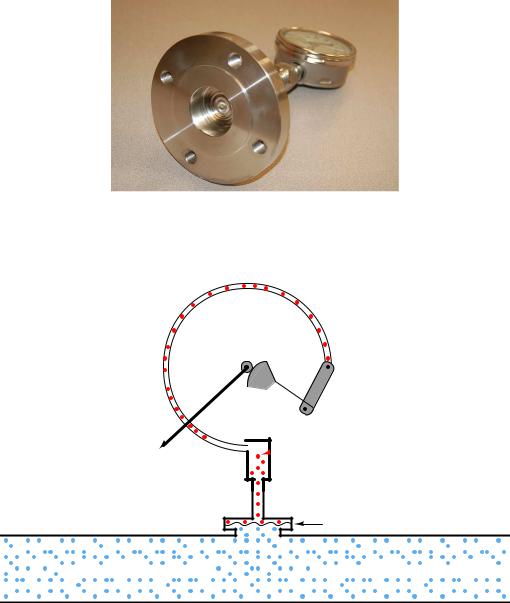
1378 |
CHAPTER 19. CONTINUOUS PRESSURE MEASUREMENT |
A view facing the bottom of the flange reveals the thin metal isolating diaphragm keeping process fluid from entering the gauge mechanism. Only inert fill fluid occupies the space between this diaphragm and the gauge’s bourdon tube:
The following illustration shows how the fill fluid transfers process fluid pressure to the gauge’s bourdon tube element while isolating that bourdon tube from the process fluid (shown here inside a pipe):
Bourdon tube pressure gauge
with isolating diaphragm
Pointer
Bourdon
tube
Pinion gear
Sector gear
Link
Fill fluid
Pipe |
Isolating diaphragm |
(process fluid)
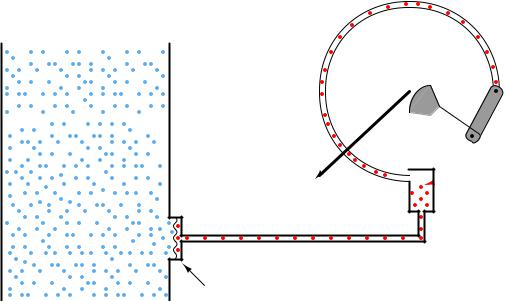
19.6. PRESSURE SENSOR ACCESSORIES |
1379 |
The only di erence between this chemical-seal gauge and a remote-seal gauge is the smalldiameter capillary tubing used to connect the gauge to a remote diaphragm. An illustration showing the internals of a remote seal system appears here:
Bourdon tube
pressure gauge
with remote seal
(process fluid)
Pipe Pointer
Bourdon
tube
Pinion gear
Sector gear
Link
Fill fluid
Capillary tube
Remote isolating diaphragm
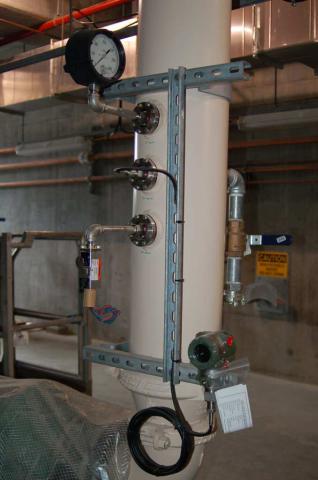
1380 |
CHAPTER 19. CONTINUOUS PRESSURE MEASUREMENT |
Direct-reading gauges are not the only type of pressure instruments benefiting from remote seals. Pressure switches and pressure transmitters may also employ remote seals for the same reasons: protection of the transmitter sensor from harsh process fluid, elimination of impulse tube clogging problems, and/or the prevention of “dead-end” tube lengths where organic process fluid would stagnate and harbor microbial growths. In this photograph, you see three pressure sensing devices (gauge, transmitter, and switch, from top to bottom), each one with its own remote seal to sense fluid pressure in a large pipe:
The pressure transmitter (a Yokogawa unit) is the only instrument shown here using a capillary tube. The other two instruments use short lengths of rigid pipe. The capillary is visible in this photograph as a coiled tube covered in black plastic. It is actually a very small-diameter metal tube enclosed in a spiral-metal protective sheath which is in turn covered by black plastic.
This particular application happens to be in wastewater treatment, where sludge has a tendency to clog instrument impulse lines connected to the main piping. With remote seals in place, that problem is completely eliminated.
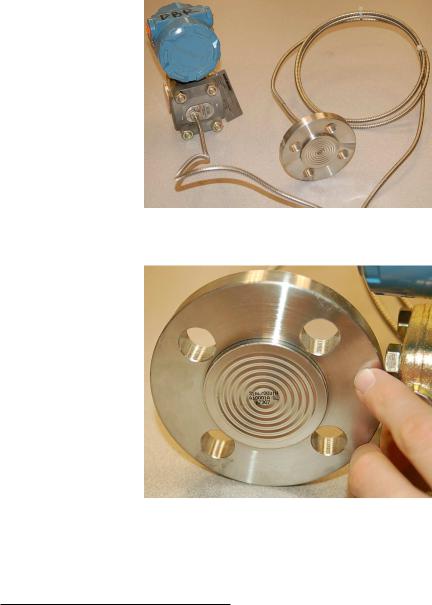
19.6. PRESSURE SENSOR ACCESSORIES |
1381 |
The following photograph shows a Rosemount model 1151 electronic pressure transmitter equipped with a remote sealing diaphragm. Here we may see the coiled metal (“armor”) sheath protecting the capillary tube from damage:
A close-up view of the sealing diaphragm shows its corrugated design, allowing the metal to easily flex and transfer pressure to the fill fluid within the capillary tubing23:
As with the isolating diaphragms of the pressure-sensing capsule, these remote diaphragms need only transfer process fluid pressure to the fill fluid and (ultimately) to the taut sensing element inside the instrument. Therefore, these diaphragms perform their function best if they are designed to easily flex. This allows the sensing diaphragm to provide the vast majority of the opposing force to the fluid pressure, as though it were the only spring element in the fluid system.
23Like all instrument diaphragms, this one is sensitive to damage from contact with sharp objects. If the diaphragm ever becomes nicked, dented, or creased, it will tend to exhibit hysteresis in its motion, causing calibration errors for the instrument. For this reason, isolating diaphragms are often protected from contact by a plastic plug when the instrument is shipped from the manufacturer. This plug must be removed from the instrument before placing it into service.
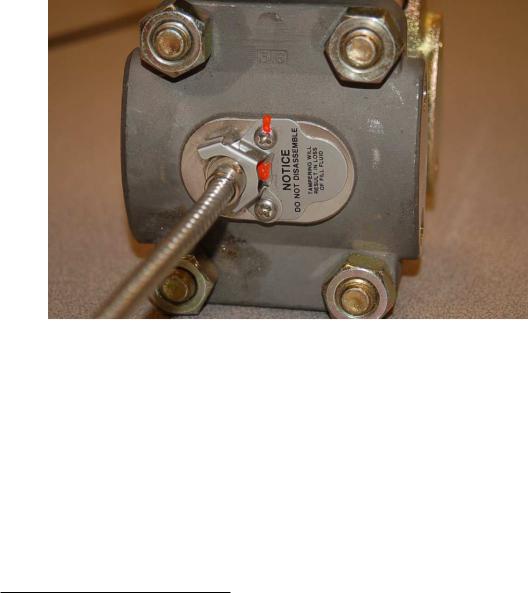
1382 |
CHAPTER 19. CONTINUOUS PRESSURE MEASUREMENT |
The connection point between the capillary tube and the transmitter’s sensor capsule is labeled with a warning never to disassemble, since doing so would allow air to enter the filled system (or fill fluid to escape from the system) and thereby ruin its accuracy:
In order for a remote seal system to work, the hydraulic “connection” between the sealing diaphragm and the pressure-sensing element must be completely gas-free so there will be a “solid” transfer of motion from one end to the other24. The presence of gas bubbles in the filled system will cause some of the isolating diaphragms’ motion to be “lost” rather than be fully transferred to the instrument’s pressure-sensing element. For this reason, the capillary system must remain perfectly sealed at all times! Breaching this seal, even for just a brief moment, will ruin the system.
A protective measure visible in this photograph is the orange compound painted on the screw head and on the capillary tube connector. This is simply a visual indication that the factory seal is still intact, since any motion of the screw or of the tube connector would crack the brittle orange compound and betray the breach.
24Anyone familiar with “bleeding” air bubbles out of automotive hydraulic brake systems will understand this concept. In order for the pedal-operated hydraulic brakes in an automobile to function as designed, the hydraulic system must be gas-free. Incompressible liquid transfers pressure without loss of motion, whereas compressible gas bubbles will “give” in to pressure and result in lost brake pad motion for any given brake pedal motion. Thus, an hydraulic brake system with air bubbles in it will have a “spongy” feel at the brake pedal, and may not give full braking force when needed.
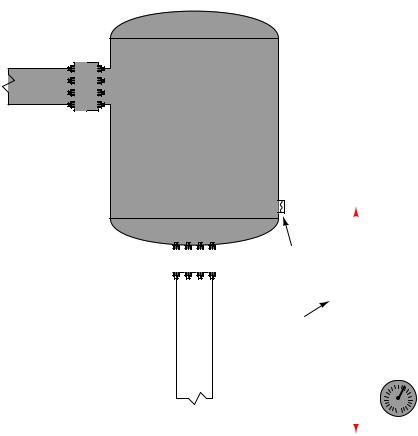
19.6. PRESSURE SENSOR ACCESSORIES |
1383 |
A potential problem with using remote diaphragms is the hydrostatic pressure generated by the fill fluid if the pressure instrument is located far away (vertically) from the process connection point. For example, a pressure gauge located far below the vessel it connects to will register a greater pressure than what is actually inside the vessel, because the vessel’s pressure adds to the hydrostatic pressure caused by the liquid in the tubing:
Vessel
Pressure = Pprocess
0 to 50 PSI
|
|
|
|
|
|
|
|
|
|
|
|
|
|
|
|
|
|
|
|
Isolating |
|
|
|
|
|
|
|
|
|
|
|
|
|
|
|
|
|
|
|
|
|
|
|
|
|
|
|
|
|
|
|
|
|
|
|
|
|
|
|
|
|
|
|
|
|
|
|
|
|
|
|
|
|
|
|
|
|
|
|
|
|
|
|
|
diaphragm |
|
|
|
Pelevation = ρgh = γh |
|
|
|
|
|
|
|
|
|
|
|
|
||
|
|
|
|
|
|
|
|
|
||||
|
|
|
|
|
Tube |
|
|
Elevation = 4.86 PSI |
||||
|
|
|
|
|
(with fill fluid) |
|
|
|
(h) |
|||
|
|
|
|
|
|
|
||||||
|
|
|
|
|
|
|
|
|
|
|
Pressure = Pprocess + Pelevation |
|
|
|
|
|
|
|
|
|
|
|
|
|
Pressure gauge |
|
|
|
|
|
|
|
|
|
|
|
|
|
|
|
|
|
|
|
|
|
|
|
|
|
4.86 to 54.86 PSI |
|
|
|
|
|
|
|
|
|
|
|
|
|
|
|
|
|
|
|
|
|
|
|
|
|
(calibrated range) |
|
|
|
|
|
|
|
|
|
|
|
|
This pressure may be calculated by the formula P = ρgh or P = γh where ρ is the mass density of the fill liquid or γ is the weight density of the fill liquid. For example, a 12 foot capillary tube height filled with a fill liquid having a weight density of 58.3 lb/ft3 will generate an elevation pressure of almost 700 lb/ft2, or 4.86 PSI. If the pressure instrument is located below the process connection point, this 4.86 PSI o set must be incorporated into the instrument’s calibration range. If we desire this pressure instrument to accurately measure a process pressure range of 0 to 50 PSI, we would have to calibrate it for an actual range of 4.86 to 54.86 PSI.
The reverse problem exists where the pressure instrument is located higher than the process connection: here the instrument will register a lower pressure than what is actually inside the vessel, o set by the amount predicted by the hydrostatic pressure formulae ρgh or γh.
In all fairness, this problem is not limited to remote seal systems – even non-isolated systems

1384 |
CHAPTER 19. CONTINUOUS PRESSURE MEASUREMENT |
where the tubing is filled with process liquid will exhibit this o set error. However, in filled-capillary systems a vertical o set is guaranteed to produce a pressure o set because fill fluids are always liquid, and liquids generate pressure in direct proportion to the vertical height of the liquid column and its density. Many common remote seal fill fluids have specific gravity ratings greater than 1 (i.e. they are denser than water) which means the o set error resulting from hydrostatic pressure will be even greater than that of a water-filled tube.
A similar problem unique to isolated-fill pressure instruments is measurement error caused by temperature extremes. Suppose the liquid-filled capillary tube of a remote seal pressure instrument is placed too near a hot steam pipe, furnace, or some other source of high temperature. The expansion of the fill fluid may cause the isolation diaphragm to extend to the point where it begins to tense and add a pressure to the fill fluid above and beyond that of the process fluid. Cold temperatures may wreak havoc with filled capillary tubes as well, if the fill fluid congeals or even freezes such that it no longer flows as it should. Fill fluid expansion/contraction e ects may be mitigated by keeping the volume of the fill fluid to a minimum, which is why capillary (small-diameter) tubes are used to connect remote seals with instruments.
Another problem with remote seal pressure instruments is a time delay caused by the viscosity of the fill fluid as it moves through the small-diameter capillary tubes. This makes the pressure instrument slow to respond to changes in process fluid pressure, as though the pressure instrument were equipped with an (undesired) pressure snubber. While minimal capillary tube diameter reduces the e ects of temperature changes, it increases the e ect of time delay.
Proper mounting of the instrument and proper selection of the fill fluid25 will help to avoid such problems. All in all, the potential for trouble with remoteand chemical-seal pressure instruments is greatly o set by their benefits in the right applications.
Some diaphragm-sealed pressure transmitters are equipped with close-coupled seals rather than remote seals to minimize hydrostatic, temperature, and time delay e ects caused by fill fluid inside a capillary tube. A Rosemount extended-diaphragm pressure transmitter appears in the left-hand photograph, while a Yokogawa transmitter of the same basic design is shown installed in a working process in the right-hand photograph:
25Most pressure instrument manufacturers o er a range of fill fluids for di erent applications. Not only is temperature a consideration in the selection of the right fill fluid, but also potential contamination of or reaction with the process if the isolating diaphragm ever su ers a leak!