
Основные положения теории базирования
.pdf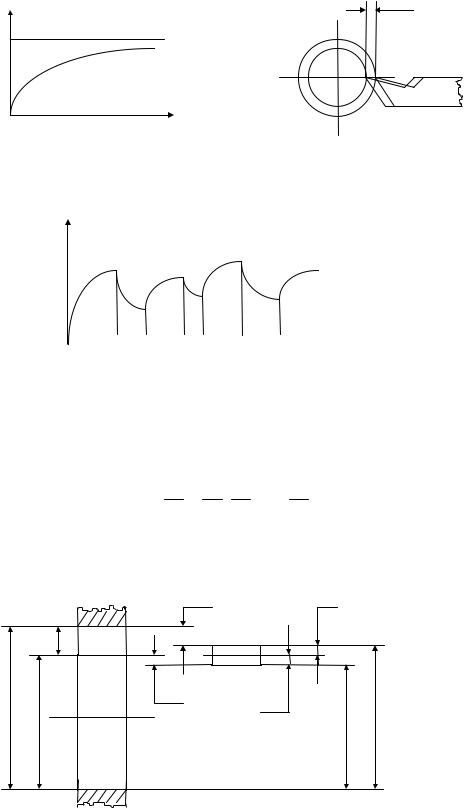
15
Тепловые деформации ξ режущего инструмента могут достигать при
обычных условиях 30 - 50 мкм и вызывают погрешность обработки ∆ Т по следующей схеме:
ξ |
∆ Т |
τ
Изменение длины резца при обработке партии заготовок имеет следующий вид:
ξ
t1 t2 t3
τ
При отсутствии ритмичности ( t1 ≠t2 ,t2 ≠ t3 ) деформации резца различны. В этом случае возникает рассеяние размеров деталей в партии.
ПРАВИЛА СЛОЖЕНИЯ ПОГРЕШНОСТЕЙ
1. Систематические погрешности складываются алгебраически, т.е. с учетом их знака:
∆Σ = ∆1 + ∆2 +...+∆n . |
( 40 ) |
В качестве примера определим суммарную погрешность механической обработки при сверлении отверстия в печатной плате. То же относится и к обработке любым размерным инструментом, т.е. для случаев, когда выдерживаемый размер определяется копированием размера инструмента.
|
|
|
amax |
|
Tи |
|
|
|
|
|
|
|
T |
|
|
|
|
Dmax |
|
аmin |
|
∆и |
|
|
|
|
dmax |
||
|
|
|
|
|
|
|
A |
|
|
|
dmin |
|
|
|
|
|
Здесь обозначено: amax - увеличение диаметра ( разбивка ) отверстия при наибольшем размере инструмента dmax; Ти - допуск на диаметр инструмента, т.е.
погрешность его изготовления, ∆и - допустимый износ при наименьшем предельном
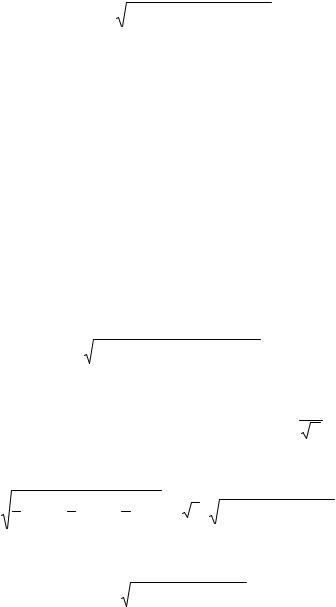
16
размере инструмента, аmin - увеличение диаметра отверстия при допустимом наименьшем диаметре инструмента с учетом его размерного износа. Суммарная погрешность, таким образом, составит:
|
∆Σ = Т = amax+ Ти+ ∆и -аmin . |
( 41 ) |
Пользуясь этой формулой, можно решать и обратную задачу: по величинам Т, |
||
amax, аmin |
находить при заданном ∆и допуск Ти, или при заданном Ти |
допустимое |
значение |
∆и . |
|
2. Случайные погрешности суммируются по правилу квадратного корня. В предположении, что ∆Σ подчиняется нормальному закону распределения, она рассчитывается как:
∆ |
Σ |
= t λ |
1 |
∆2 |
+ λ ∆2 |
+...+λ ∆2 . |
( 42 ) |
|
|
1 |
2 2 |
n n |
|
||
Это обусловлено тем, что дисперсия |
|
|
|||||
|
D{ξ +η }= D{ξ} + D{η} . |
( 43 ) |
В приведенной формуле: t - коэффициент, определяющий процент риска получения брака при обработке: при t=1 процент риска равен 32%, при t=2, он
равен 4,5%, при t=3 он равен 0,27%; λ i - коэффициенты относительного рассеяния характеризующие отклонения действительных кривых нормального распределения.
Для кривой распределения, близкой с нормальной λ =1/9. Для кривой равной вероятности и в случае, когда о формуле кривой распределения ничего неизвестно,
рекомендуется принимать λ =1/3. Если форма кривой распределения приближается к форме треугольника, то λ =1/6.
В качестве примера рассмотрим, чему равна погрешность настройки, рассматриваемая как случайная погрешность, состоящая, как указывалось выше, для
метода пробных деталей, из |
∆ изм, |
∆ рег и |
∆ рас. |
|
|
|
||||
|
∆н |
= t |
λ1∆2изм + λ 2∆2рег + λ3∆2рас |
|
( |
44 ) |
||||
Принимаем t=3, поскольку обычно так рекомендуется; λ 1= λ 2=1/3 - закон равной |
||||||||||
вероятности, λ 3=1/3 - неизвестный закон, т.к. ∆ расч= ± |
σ |
|
||||||||
n |
|
|||||||||
Если предполагать что |
∆ н |
подчиняется нормальному закону распределения, то |
||||||||
1 |
2 |
1 |
2 |
1 |
2 |
|
2 |
2 |
2 |
|
∆н = 3 3 ∆изм + 3 ∆рег + |
3 |
∆рас = |
3 |
∆изм + ∆рег + ∆рас |
( 45 ) |
|||||
Если предполагать что, ∆ н |
подчиняется закону равной вероятности, то |
|||||||||
|
|
|
∆ н = |
|
∆2изм + ∆2рег + ∆2рас |
|
|
( 46 ) |
||
Другой пример расчета суммарной погрешности установки, состоящей из ε б, ε з |
||||||||||
и ε пр. Составляющая |
ε б |
- случайная погрешность, которая подчиняется закону |
||||||||
нормального распределения. Составляющая |
ε з |
- погрешность закрепления заготовки. |
Величины y1=Cmin(Qnmax-Qnmin) и y2=Cmax(Qnmax-Qnmin)Qnmax - случайные, подчиняющиеся нормальному закону распределения, поэтому
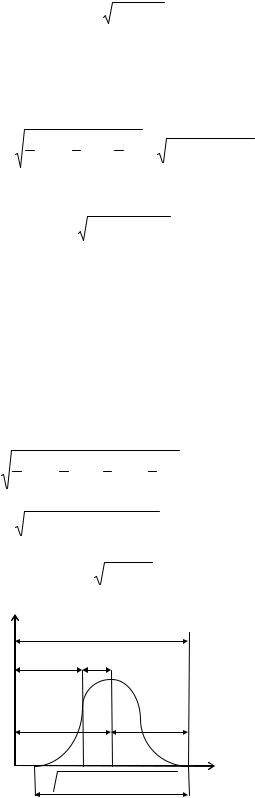
17
εз = y12 + y22 |
( 47 ) |
Составляющая ε пр - погрешность положения заготовки, вызываемая неточностью приспособления, определяется ошибками изготовления и сборки его установочных элементов ε уэ , их прогрессирующим износом ε и , а также ошибками установки и фиксации приспособления на станке ε с. Распределение этих величин можно принять по нормальным законам ( для приспособлений - спутников ):
ε пр=3 91 εуэ2 + 13 εи2 + 91 εс2 = εуэ2 +3εи2 +εс2 |
( 48 ) |
Погрешность установки, как суммарное поле рассеивания выполняемого размера
ε пр= εб2 +εз2 +εп2р |
( 49 ) |
3. Систематические погрешности со случайными складываются арифметически. Поскольку знак случайной погрешности невозможно предвидеть, то нужно считаться с худшим вариантом.
В качестве примера рассмотрим суммарную погрешность, которая возникает при обработке одной партии заготовок в одном приспособлении на одном станке при
одной настройке. В этом случае ∆ у - случайная погрешность, связанная со случайными неравномерностями припуска. ∆ н,
Σ ∆ ф - систематические погрешности, причем постоянные. ∆ и - переменная систематическая погрешность, но она может рассматриваться, как случайная с равномерным законом распределения. Тогда
|
1 |
2 |
1 |
|
2 |
|
1 |
2 |
1 |
2 |
|
|
∆Σ = 3 |
9 |
∆у + |
9 |
ε |
|
+ |
3 |
∆и + |
3 |
∆Т |
+ ∆н + Σ∆ф |
( 50 ) |
Сокращая коэффициенты, получаем:
∆Σ = ∆2у +ε2 +3∆2и +3∆2Т + ∆н + Σ∆ф |
( 51 ) |
ε и ∆ т - случайные погрешности, причем в этом случае
ε = ε пр+ εб2 +εз2 . |
(52) |
∆Σ
∆ н Σ ∆ ф
∆сист ∆сл
∆2у + ε2 + 3∆2и + 3∆2Т
ПРИЛОЖЕНИЕ
Таблица 1. Относительный износ u0 ( мкм/км ) резцов при чистовом точении.
Материал |
Углеродистая |
Легированная |
Серый чугун |
Чугун, НВ |
инструмента |
сталь |
сталь |
|
375-400 |
T60K6 |
0,7-4 |
0,7-4 |
- |
- |
T30K4 |
3-4 |
4-6 |
- |
|
T15K6 |
5-7 |
9-10 |
- |
- |
T5K10 |
8 |
12-13 |
- |
- |
BK9 |
- |
65 |
- |
- |
BK8 |
- |
17-25 |
13-14 |
- |
BK6 |
- |
- |
14 |
- |
BK4 |
- |
15-30 |
- |
- |
BK3 |
- |
9-10 |
6 |
16 |
BK2 |
- |
- |
4-26 |
12 |
|
|
|
|
|
Таблица 2. Станки токарные многорезцовые и многорезцово-копировальные горизонтальные полуавтоматические ( ГОСТ 16472-79 )
|
Класс |
Наибольший диаметр устанавливаемой |
|||||
Параметр |
точности |
|
|
заготовки, мм |
|
||
|
|
160 |
200 |
250 |
320 |
400 |
|
Наибольшее допустимое |
Н |
160 |
220 |
|
320 |
450 |
630 |
перемещение под |
П |
100 |
140 |
|
200 |
280 |
400 |
нагрузкой продольного |
|
||||||
суппорта относительно |
|
|
|
|
|
|
|
оправки, закрепленной в |
|
|
|
|
|
|
|
шпинделе или |
Н |
200 |
300 |
|
450 |
670 |
1000 |
переходной втулке, мкм |
|
||||||
П |
120 |
200 |
|
280 |
400 |
630 |
|
То же, относительно |
|
||||||
|
|
|
|
|
|
|
|
оправки, закрепленной в |
|
|
|
|
|
|
|
пиноли, мкм |
Н |
300 |
450 |
|
670 |
1000 |
1500 |
Наибольшее допустимое |
|
||||||
перемещение под |
П |
200 |
280 |
|
400 |
630 |
1000 |
нагрузкой поперечного |
|
||||||
суппорта относительно |
|
|
|
|
|
|
|
оправки, закрепленной в |
|
|
|
|
|
|
|
шпинделе или |
|
|
|
|
|
|
|
переходной втулке, мкм |
Н |
6 |
10 |
|
16 |
26 |
40 |
Сила, КН |
|
||||||
П |
5 |
8 |
|
12 |
20 |
30 |
|
|
|
Таблица 3. Станки токарные и токарно-винторезные ( ГОСТ 18097-72 )
|
Класс |
Наибольший диаметр обрабатываемой детали, |
||||||
Параметр |
точности |
|
|
|
мм |
|
|
|
|
|
100 |
160 |
250 |
400 |
630 |
1000 |
|
Наибольшее |
|
|
|
|
|
|
|
|
смещение (мкм) |
|
|
|
|
|
|
|
|
резцедержателя |
|
|
|
|
|
|
|
|
и оправки, |
|
|
|
|
|
|
|
|
установленной: |
Н |
40 |
70 |
130 |
|
200 |
350 |
600 |
в шпинделе |
|
|||||||
передней бабки |
П |
25 |
40 |
80 |
|
130 |
220 |
400 |
в пиноли задней |
Н |
50 |
100 |
160 |
|
270 |
470 |
800 |
бабки |
П |
30 |
60 |
100 |
|
170 |
300 |
500 |
|
|
|||||||
Сила, Н |
Н |
686 |
1372 |
2744 |
|
5488 |
10976 |
21952 |
П |
549 |
1098 |
2195 |
|
4390 |
8781 |
17562 |
|
|
|
Таблица 4. Значения коэффициентов и показателей степеней в формулах силы резания.
Материал |
Вид обработки |
Коэффициенты и показатели степеней |
|||
рабочей части |
|
Сру |
x |
y |
n |
Твердый сплав |
Наружное продольное и |
243 |
0,9 |
0,6 |
-0,3 |
поперечное точение и |
|||||
|
растачивание |
|
|
|
|
Твердый сплав |
Наружное продольное |
355 |
0,6 |
0,8 |
-0,3 |
точение резцами с |
|||||
Твердый сплав |
дополнительным лезвием |
173 |
0,73 |
0,67 |
0 |
Отрезание и прорезание |
|||||
Быстрорежущая |
Наружное продольное |
125 |
0,9 |
0,75 |
0 |
сталь |
точение, подрезание и |
||||
Быстрорежущая |
растачивание |
- |
- |
- |
- |
Отрезание и прорезание |
|||||
сталь |
|
|
|
|
|
Таблица 5. Значение поправочного коэффициента kϕp от главного угла в плане.
Материал режущей |
Величина угла, |
Поправочные коэффициенты, |
части |
ϕ0 |
k ϕp |
Твердый сплав |
30 |
1,3 |
Твердый сплав |
45 |
1 |
Твердый сплав |
60 |
0,77 |
Твердый сплав |
90 |
0,5 |
Быстрорежущая сталь |
30 |
1,63 |
Быстрорежущая сталь |
45 |
1 |
Быстрорежущая сталь |
60 |
0,71 |
Быстрорежущая сталь |
90 |
0,44 |
|
|
|
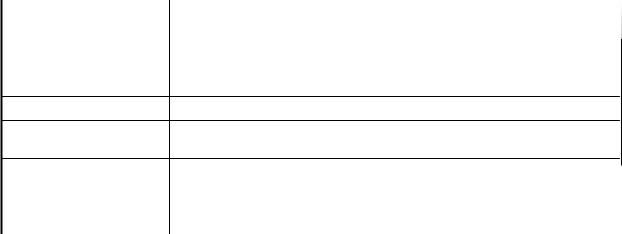
Таблица 6. Полуавтоматы ( станки ) токарные многорезцовые и многорезцовокопировальные горизонтальные ( ГОСТ 16472-79 )
Характер образца |
|
Сталь НВ 161-207 |
|
изделия |
|
|
|
Наибольший диаметр |
|
|
|
обрабатываемой |
до 160 |
160-250 |
свыше 250 |
заготовки, мм |
|
|
|
Длинаλ (обработки lд) |
150 |
300 |
300 |
Постоянство |
|
|
|
Классы точности станков |
|
|
|||||
диаметра, С : |
Н |
П |
В |
|
Н |
П |
В |
|
Н |
П |
В |
в поперечном сечении |
10 |
6 |
4 |
|
12 |
8 |
|
5 |
16 |
10 |
6 |
в продольном сечении |
|
|
|||||||||
16 |
10 |
6 |
|
20 |
12 |
|
8 |
25 |
16 |
10 |
|
|
|
|
Таблица 7. Допустимые погрешности измерения ∆изм ( мкм ) линейных размеров ( длин, диаметров ) в зависимости от допусков и квалитетов точности размеров.
Квали |
Погреш |
|
|
|
Номинальные размеры, мм |
|
|
|
|
|||||||
теты |
ности |
св.3 |
св.6 |
св.10 |
|
св.18 |
св.30 |
св.50 |
св.80 |
св.120 |
св.180 св.250 |
|||||
|
|
до 6 |
до 10 |
до 18 |
|
до 30 |
до 50 |
до 80 |
до 120 |
до 180 |
до 250 |
до 315 |
||||
4 |
IT |
4 |
4 |
5 |
|
6 |
7 |
8 |
|
10 |
|
12 |
|
14 |
|
16 |
|
∆изм |
1,4 |
1,4 |
1,7 |
|
2 |
2,4 |
2,8 |
|
3,5 |
|
4 |
|
4,5 |
|
5,5 |
5 |
IT |
5 |
6 |
8 |
|
9 |
11 |
13 |
|
15 |
|
18 |
|
20 |
|
23 |
|
∆изм |
1,4 |
2 |
2,8 |
|
3 |
4 |
4,5 |
|
5 |
|
6 |
|
7 |
|
8 |
6 |
IT |
8 |
9 |
11 |
|
13 |
16 |
19 |
|
22 |
|
25 |
|
29 |
|
32 |
|
∆изм |
2,5 |
2,5 |
3 |
|
4 |
4,5 |
5,5 |
|
6 |
|
7 |
|
9 |
|
10 |
7 |
IT |
12 |
15 |
18 |
|
21 |
25 |
30 |
|
35 |
|
40 |
|
46 |
|
52 |
|
∆изм |
3,5 |
4,5 |
5,5 |
|
6 |
7 |
9 |
|
10 |
|
12 |
|
13 |
|
15 |
8 |
IT |
18 |
22 |
27 |
|
33 |
39 |
46 |
|
54 |
|
63 |
|
72 |
|
81 |
|
∆изм |
4,5 |
5,5 |
7 |
|
8 |
10 |
12 |
|
13 |
|
16 |
|
18 |
|
20 |
9 |
IT |
30 |
36 |
43 |
|
52 |
62 |
74 |
|
87 |
|
100 |
|
115 |
|
130 |
|
∆изм |
7 |
9 |
10 |
|
13 |
15 |
18 |
|
20 |
|
25 |
|
25 |
|
30 |
10 |
IT |
48 |
58 |
70 |
|
84 |
100 |
120 |
|
140 |
|
160 |
|
185 |
|
210 |
|
∆изм |
10 |
12 |
14 |
|
15 |
20 |
20 |
|
25 |
|
30 |
|
35 |
|
40 |
11 |
IT |
75 |
90 |
110 |
|
130 |
160 |
190 |
|
220 |
|
250 |
|
290 |
|
320 |
|
∆изм |
15 |
18 |
20 |
|
25 |
30 |
40 |
|
40 |
|
50 |
|
60 |
|
60 |
12 |
IT |
120 |
150 |
180 |
|
210 |
250 |
300 |
|
350 |
|
400 |
|
460 |
|
520 |
|
∆изм |
20 |
30 |
35 |
|
40 |
50 |
60 |
|
70 |
|
80 |
|
90 |
|
100 |
13 |
IT |
180 |
220 |
270 |
|
330 |
390 |
460 |
|
540 |
|
630 |
|
720 |
|
810 |
|
∆изм |
35 |
40 |
50 |
|
70 |
80 |
90 |
|
100 |
|
120 |
|
140 |
|
150 |
14 |
IT |
300 |
360 |
430 |
|
520 |
620 |
740 |
|
870 |
|
1000 |
|
1150 |
|
1300 |
|
∆изм |
60 |
70 |
80 |
|
100 |
120 |
150 |
|
170 |
|
200 |
|
200 |
|
250 |
15 |
IT |
480 |
580 |
700 |
|
840 |
1000 |
1200 |
|
1400 |
|
1600 |
|
1850 |
|
2100 |
|
∆изм |
100 |
100 |
150 |
|
150 |
200 |
250 |
|
250 |
|
300 |
|
350 |
|
400 |
16 |
IT |
750 |
900 |
1100 |
|
1300 |
1600 |
1900 |
|
2200 |
|
2500 |
|
2900 |
|
3200 |
|
∆изм |
150 |
200 |
200 |
|
250 |
300 |
400 |
|
400 |
|
500 |
|
600 |
|
600 |
Таблица 8. Погрешность регулирования ( установки ) резца при наладке на размер в поперечном направлении.
Метод регулирования положения резца |
∆р ,мкм |
По лимбу с ценой деления, мм |
|
0,01 |
5-10 |
0,02 |
10-15 |
0,03 |
10-30 |
0,05 |
15-30 |
0,1-0,5 |
30-70 |
По индикаторному упору сценой деления прибора, мм |
|
0,01 |
10-15 |
0,002 |
3-5 |
0,001 |
1-2 |
По жесткому упору |
20-50 ( 10-130 ) |
По эталону: |
|
резец закрепляют винтами резцедержателя после |
100-130 |
касания его с эталоном |
|
резец, закрепленный в резцедержателе, подводят к |
20-30 |
эталону винтом поперечной подачи |
|
то же, но с контролем положения резца с помощью |
10-20 |
бумажного щупа |
|
то же, но с контролем положения резца с помощью |
7-10 |
металлического щупа |
|
Установка взаимозаменяемого режущего инструмента со |
|
сменой: |
|
резца, установленного на размер вне станка с помощью |
20-30 |
индикатора или миниметра |
|
блока с резцами, установленными на размер вне станка |
10-50 |
режущей пластинки ( или путем поворота круглой |
25 |
пластинки ) |
|