
Методички / Пособия ОКМ / Конструирование узлов механизмов
.pdf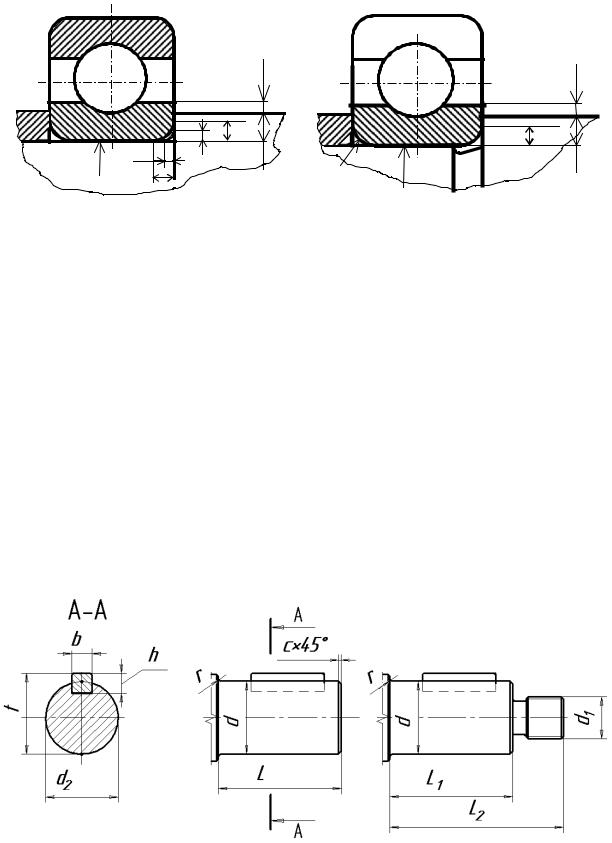
высоты кольца подшипника h, необходимой для демонтажа подшипника съемником, по табл. 3.4.
а)
|
|
h |
|
|
п |
|
r r |
r |
d |
t |
|
|
rп |
|
б)
|
|
h |
|
|
п |
|
|
r |
r |
d |
t |
Рис. 3.4. Уступ (заплечик) вала у подшипника качения:
а – галтель, б – канавка
Таблица 3.3
Размеры галтельных переходов у мест посадки подшипников качения, мм
Радиус фаски подшипника rп |
0.5 |
1.0 |
1.5 |
2.0 |
2.5 |
3.0 |
3.5 |
4.0 |
5.0 |
|
Радиус галтели |
r < rп |
0.3 |
0.6 |
1.0 |
1.0 |
1.5 |
2.0 |
2.0 |
2.5 |
3.0 |
Высота буртика |
t > rп |
1.0 |
2.5 |
3.0 |
3.5 |
4.5 |
5.0 |
6.0 |
7.0 |
9.0 |
|
|
|
|
Таблица 3.4 |
Минимальная свободная высота кольца подшипника качения, мм |
||||
Диаметр вала d |
1 ÷ 15 |
15 ÷ 50 |
50 ÷ 100 |
> 100 |
Свободная высота h |
1,0 |
2,0 |
2,5 |
3,0 |
Концы валов могут быть цилиндрическими или коническими. Первые – более технологичны, но менее удобны при монтаже муфт. Вторые – имеют противоположные качества. Конструктивные исполнения двух вариантов представлены на рис. 3.5 и 3.6, их размеры — в табл. 3.5 и 3.6.
Рис. 3.5. Формы цилиндрических концов валов
21

Тип 1 |
Тип 2 |
Рис. 3.6. Формы конических концов валов
Таблица 3.5
Основные размеры цилиндрических концов валов по ГОСТ 12080-66, мм
|
Диаметр d |
Поле |
Длина l |
r |
С |
|||
|
|
|
Исполнение |
|||||
Ряд 1 |
Ряд 2 |
допуска |
||||||
1 |
2 |
|
|
|||||
|
|
|
|
|
|
|||
10; |
11 |
– |
|
23 |
20 |
0,6 |
0,4 |
|
12; |
14 |
– |
|
30 |
25 |
1,0 |
0,6 |
|
16; |
18 |
19 |
js6 |
40 |
28 |
1,0 |
0,6 |
|
20; |
22 |
24 |
50 |
36 |
1,6 |
1,0 |
||
|
||||||||
25; |
28 |
– |
|
60 |
42 |
1,6 |
1,0 |
|
– |
|
30 |
|
80 |
58 |
2,0 |
1,6 |
|
32; |
36 |
38 |
k6 |
80 |
58 |
2,0 |
1,6 |
|
40; 45; |
42; 48 |
110 |
82 |
2,0 |
1,6 |
|||
50 |
– |
|
|
|
|
|
||
55 |
53 |
|
110 |
82 |
2,5 |
2,0 |
||
60; |
70 |
63; 65; |
|
140 |
105 |
2,5 |
2,0 |
|
– |
|
75 |
m6 |
|
|
2,5 |
2,0 |
|
80; |
90 |
85; 95 |
170 |
130 |
3,0 |
2,5 |
||
|
||||||||
100; |
110 |
105; 120 |
|
3,0 |
2,5 |
|||
|
210 |
165 |
||||||
125 |
– |
|
3,0 |
2,5 |
||||
|
|
|
Примечания: 1. Ряд 1 диаметров является предпочтительным.
2.Допуски типа k6 и m6 назначаются при частотах вращения валов n > 700 об/мин.
3.Для тихоходных валов рекомендуются допуски типа h6 или js6.
Таблица 3.6
Основные размеры конических концов валов по ГОСТ 12081-72, мм
Диаметр d |
|
l |
|
l1 |
d1 |
d2 |
l2 |
||
Ряд 1 |
Ряд 2 |
|
Исполнение |
|
|
||||
1 |
2 |
1 |
|
2 |
|
|
|
||
|
|
|
|
|
|
||||
10; 11 |
– |
23 |
– |
15 |
|
– |
М6 |
– |
– |
12; 14 |
– |
30 |
18 |
|
М8×1 |
М4 |
8 |
||
|
|
|
|||||||
16 |
– |
40 |
28 |
28 |
|
16 |
М10×1,25 |
М4 |
8 |
18 |
19 |
|
М5 |
10 |
|||||
|
|
|
|
|
|
||||
20; 22 |
24 |
50 |
36 |
36 |
|
22 |
М12×1,25 |
М6 |
12 |
25; 28 |
– |
60 |
42 |
42 |
|
24 |
М16×1,5 |
М8 |
16 |
30; 32; 35 |
– |
80 |
58 |
58 |
|
36 |
М20×1,5 |
М10 |
20 |
22

Окончание табл. 3.6
36 |
– |
80 |
58 |
58 |
36 |
|
М20×1,5 |
М12 |
24 |
|
||
– |
38 |
80 |
58 |
58 |
36 |
|
М24×2 |
М12 |
24 |
|
||
40 |
42 |
|
|
|
|
|
|
|
М24×2 |
М12 |
24 |
|
45 |
48 |
110 |
82 |
82 |
54 |
|
М30×2 |
М16 |
32 |
|
||
50 |
– |
|
М3×63 |
М16 |
32 |
|
||||||
|
|
|
|
|
|
|
|
|||||
56 |
55 |
|
|
|
|
|
|
|
М3×63 |
М20 |
36 |
|
63 |
60; 65 |
140 |
105 |
105 |
70 |
|
М4×23 |
М20 |
36 |
|
||
71 |
70; 75 |
|
М4×83 |
М24 |
40 |
|
||||||
|
|
|
|
|
|
|
|
|||||
80 |
85 |
|
|
|
|
|
|
|
М56×4 |
М30 |
50 |
|
90 |
- |
170 |
130 |
130 |
90 |
|
М6×44 |
М30 |
50 |
|
||
– |
95 |
|
|
|
|
|
|
|
М6×44 |
М36 |
60 |
|
100 |
– |
|
|
|
|
|
|
|
М7×24 |
М36 |
60 |
|
110 |
– |
210 |
165 |
165 |
120 |
|
М80×4 |
М42 |
65 |
|
||
– |
120 |
|
М90×4 |
М42 |
65 |
|
||||||
|
|
|
|
|
|
|
|
|||||
125 |
– |
|
|
|
|
|
|
|
М90×4 |
М48 |
70 |
|
Примечание: Ряд 1 диаметров является предпочтительным.
Для крепления на валу деталей, передающих момент, используются, шпоночное (рис. 3.7,а) и шлицевое (рис. 3.7,б) соединения. Их размеры, в зависимости от диаметра вала, определяются по ГОСТ 23360-78 (шпоночные) и ГОСТ 1139-80 (шлицевые). Пазы, предназначенные для этих соединений на валах, так же, как канавки и галтели являются концентраторами напряжений, что требует их учета при расчете вала на прочность.
а) |
d |
б) |
D |
d
Рис. 3.7. Шпоночные (а) и шлицевые (б) соединения
3.3. Материалы валов
В соответствии с рассмотренными условиями работы валов, материалы, применяемые для их изготовления, должны обладать достаточно высокими прочностными характеристиками, малой чувствительностью к концентрации напряжений, способностью подвергаться термической обработке, хорошей обрабатываемостью. Этим требованиям отвечают углеродистые стали 25, 40, 50 и легированные стали 35Х, 40Х, 45Х и др. (табл. 3.7).
23

|
|
|
|
|
|
|
|
Таблица 3.7 |
|
|
Механические характеристики сталей по ГОСТ 12081-72, мм |
|
|||||||
|
|
|
|
|
|
|
|
|
|
|
Углеродистые стали |
|
|
Легированные стали |
|
||||
Марка |
|
Временное |
|
Предел |
Марка |
|
Временное |
|
Предел |
стали |
|
сопротивление |
|
стали |
|
сопротивление |
|
||
|
|
текучести |
|
|
текучести |
||||
(ГОСТ |
|
разрыву |
|
(ГОСТ |
|
разрыву |
|
||
|
|
σт, МПа |
|
|
σт, МПа |
||||
1050-88) |
|
σв, МПа |
|
4543-71) |
|
σв, МПа |
|
||
|
|
|
|
|
|
||||
10 |
|
330 |
|
205 |
35Х |
|
910 |
|
735 |
15 |
|
370 |
|
225 |
40Х |
|
980 |
|
785 |
20 |
|
410 |
|
245 |
45Х |
|
1030 |
|
835 |
25 |
|
450 |
|
275 |
50Х |
|
1080 |
|
885 |
30 |
|
490 |
|
295 |
40ХН |
|
980 |
|
785 |
35 |
|
530 |
|
315 |
45ХН |
|
1030 |
|
835 |
40 |
|
570 |
|
335 |
35ХМ |
|
930 |
|
825 |
45 |
|
600 |
|
355 |
20Х |
|
780 |
|
625 |
50 |
|
630 |
|
375 |
18ХГТ |
|
880 |
|
735 |
55 |
|
650 |
|
380 |
12ХН3А |
|
950 |
|
700 |
60 |
|
680 |
|
400 |
|
|
|
|
|
4. ПРОВЕРКА РАБОТОСПОСОБНОСТИ ВАЛОВ
4.1. Расчеты валов на усталостную выносливость
Основными нагрузками на валах являются передаваемый крутящий момент и силы, возникающие в установленных на них элементах передач.
Под действием этих сил, постоянных во величине и направлению, во вращающихся валах возникают знакопеременные напряжения, которые при наличии концентраторов напряжений, могут быть причиной усталостных повреждений.
Целью расчета в этом случае является оценка коэффициента запаса прочности n и сравнения его с нормативным значением [n]:
n > [n].
Алгоритм расчета вала состоит из следующих этапов:
•определение диаметра вала из расчета на кручение;
•назначение диаметров на остальных участках вала;
•определение длины каждого участка вала и длины вала в целом с учетом осевых размеров деталей, установленных на валу (через выполнение эскизной компоновки);
•составление расчетной схемы вала, построение эпюр моментов и нахождение опасного сечения вала;
•проверка работоспособности вала по опасному сечению.
Оценка диаметра выходного конца вала выполняется по пониженным напряжениям кручения (табл. 4.1):
d1 ≈ 316T / π[τкр ] .
24

Таблица 4.1
Допускаемые касательные напряжения при кручении вала [τкр] в зависимости от частоты вращения вала n для углеродистых сталей
n, об/мин |
3000 |
÷ 1500 |
1000 ÷ 600 |
500 |
÷ 100 |
50 ÷ 10 |
[τкр], МПа |
10 |
÷ 15 |
15 ÷ 20 |
20 |
÷ 25 |
30 ÷ 35 |
Примечания: 1. Проектный расчет ведется по пониженным касательным напряжениям при кручении вала с использованием коэффициента запаса [n] = 10 ÷ 15.
2. Применима эмпирическая зависимость:
[τкр ] = σ[предn] (1,25 −0,25lg n) .
Назначение диаметров валов на других участках выполняется с учетом целесообразного количества ступеней и разумного перепада диаметров между соседними участками.
а)
б)
Рис. 4.1. Ступенчатый вал с деталями
Длину вала l между опорами определим из рис. 4.1,а:
l = 2l1 + 2l2 + 2l3 +l4 ,
где l1 — половина ширины подшипника 3, выбранного предварительно по диаметру вала d2; l2 — расстояние между торцом подшипника 3 и внутренней стенкой корпуса 1; l3 — зазор безопасности между внутренней стенкой корпуса и торцом колеса 2; l4 — длина ступицы колеса, l4 = (0.8÷1.5) d3; при жидкой смазке подшипника можно принять l2 = 1÷2 мм.
Рассмотренной конструкции соответствует расчетная схема на рис. 4.1,б для построения эпюр Mx, My, Mz.
25

|
|
|
|
|
|
|
|
|
|
|
|
|
|
|
Таблица 4.2 |
||||||
|
Формулы для расчета валов на усталостную выносливость |
||||||||||||||||||||
Наименование параметра |
|
Расчетная формула |
|||||||||||||||||||
|
|
|
|
|
|
|
|
|
|
|
|
|
|
|
|
|
|
||||
Критерий расчета на выносливость |
|
|
|
|
n > [n] |
|
|
|
|
|
|
|
|
|
|
||||||
Коэффициент запаса прочности |
|
n = |
|
|
|
nσ nτ |
|
|
|
|
|
|
|
|
|
|
|||||
|
|
|
|
|
|
|
|
|
|
|
|
|
|
|
|||||||
|
|
|
2 |
|
2 |
|
|
|
|
|
|
|
|
||||||||
|
|
|
|
|
|
|
|
|
|
|
n + n |
τ |
|||||||||
|
|
|
|
|
|
|
|
|
|
|
σ |
|
|||||||||
Коэффициент запаса прочности по нормальным |
nσ = |
|
|
|
|
|
|
σ-1 |
|
|
|
|
|
|
|
|
|
|
|||
напряжениям |
|
|
|
KσΣ σa + |
ψσσm |
||||||||||||||||
|
|
|
|
||||||||||||||||||
Коэффициент запаса прочности по касательным |
nτ = |
|
|
|
|
|
τ-1 |
|
|
|
|
|
|
|
|
|
|
||||
напряжениям |
|
|
|
KτΣ τa + |
ψττm |
||||||||||||||||
|
|
|
|
|
|||||||||||||||||
Суммарный |
коэффициент |
снижения |
предела |
|
|
|
|
|
|
|
|
|
|
|
|||||||
kσ |
|
|
|
|
1 |
||||||||||||||||
выносливости при изгибе |
|
|
KσΣ = |
|
|
|
|
|
+ kF |
−1 |
|
|
|
|
|||||||
|
|
|
|
|
|
|
|
|
|||||||||||||
|
|
kd |
|
|
|
|
|
|
kV |
||||||||||||
Суммарный |
коэффициент |
снижения |
предела |
|
|
|
|
|
|
|
|
|
|
|
|||||||
kτ |
|
|
|
|
|
|
1 |
||||||||||||||
выносливости при кручении |
|
|
K τΣ = |
|
|
|
|
|
+ kF |
−1 |
|
|
|||||||||
|
|
|
|
|
|
|
|
||||||||||||||
|
|
kd |
|
|
|
|
|
|
kV |
||||||||||||
Коэффициенты чувствительности материала к |
ψσ = 2ψτ = 0,1÷0,2 |
||||||||||||||||||||
асимметрии цикла |
|
|
|||||||||||||||||||
|
|
|
|
|
|
|
|
|
|
|
|
|
|
|
|
|
|
|
|
||
Амплитудное значение нормальных напряжений |
σa = Mизг /Wизг |
||||||||||||||||||||
при симметричном цикле |
|
|
|||||||||||||||||||
|
|
|
|
|
|
|
|
|
|
|
|
|
|
|
|
|
|
|
|
||
Среднее значение нормальных напряжений при |
|
|
|
σm = 0 |
|
|
|
|
|
|
|
|
|
|
|||||||
симметричном цикле |
|
|
|
|
|
|
|
|
|
|
|
|
|
|
|
||||||
|
|
|
|
|
|
|
|
|
|
|
|
|
|
|
|
|
|
|
|
||
Амплитудное и среднее значения касательных |
τa = τm |
= 0,5T /Wкр |
|||||||||||||||||||
напряжений при симметричном цикле |
|
|
|
|
|
|
|
|
|
|
|
|
|
|
|
|
|
|
|
||
Примечания: Mизг, Т – изгибающий и крутящий |
моменты; [n] – нормативный коэф- |
||||||||||||||||||||
фициент запаса прочности (табл. 4.3); |
σ-1 и τ-1 |
– пределы выносливости материала |
|||||||||||||||||||
(таб. 4.4); kσ |
и kτ – коэффициенты концентрации напряжений (табл. 4.5); kd, kF и kV – ко- |
эффициенты влияния размеров деталей (табл. 4.6), поверхности (табл. 4.7) и упрочнения (табл. 4.8); Wизг и Wкр – моменты сопротивления изгибу и кручению (табл. 4.9).
|
|
|
|
|
|
|
|
|
|
|
Таблица 4.3 |
|
|
|
|
|
Рекомендуемые нормативные коэффициенты запаса [n] |
|
|||||||
|
|
|
|
|
|
|
|
|
|
|
||
|
Тип |
|
|
Нормативный коэффициент запаса [n] для сталей |
|
|||||||
|
|
углеродистых |
|
углеродистых |
легированных |
отливок |
|
|||||
|
нагрузки |
|
|
|||||||||
|
(Ст.2 ÷ Ст.6) |
|
(10 ÷ 45) |
(40Х ÷ 35ХМ) |
(45Л ÷ 45ХЛ) |
|
||||||
|
|
|
|
|
|
|||||||
|
1 |
|
|
1,5 ÷ 2,2 |
|
|
1,8 ÷ 2,6 |
1,7 ÷ 3,3 |
2,5 ÷ 4,3 |
|
||
|
2 |
|
|
2,1 ÷ 2,9 |
|
|
2,5 ÷ 3,5 |
2,1 ÷ 4,6 |
3,7 ÷ 6,0 |
|
||
|
3 |
|
|
2,7 ÷ 3,7 |
|
|
3,3 ÷ 4,7 |
2,6 ÷ 5,9 |
5,0 ÷ 7,8 |
|
||
|
Примечание |
:1 – статическая, 2 – переменная |
пульсационная, 3 – знакопеременная |
|
||||||||
|
симметричная нагрузки. |
|
|
|
|
|
Таблица 4.4 |
|
||||
|
|
|
|
|
|
|
|
|
|
|
|
|
|
|
|
Эмпирические зависимости между статическими и усталостными |
|
||||||||
|
|
|
|
|
|
характеристиками металлов |
|
|
||||
|
Вид нагружения |
|
Предел выносливости при цикле переменных напряжений |
|
||||||||
|
|
|
|
симметричный |
|
пульсационный |
|
|||||
|
|
|
|
|
|
|
|
|
|
|||
|
|
|
Изгиб |
|
|
σ-1 = (0,40 ÷ 0,55) σв |
|
σ0 = 0,6 σв |
|
|||
|
Растяжение – сжатие |
|
|
σ-1 = (0,26 ÷ 0,40) σв |
|
σ0 = 0,5 σв |
|
|||||
|
|
Кручение |
|
|
τ-1 = (0,22 ÷ 0,25) σв |
|
τ0 = 0,3 σв |
|
26
Таблица 4.5
Коэффициенты концентрации по нормальным kσ и касательным kτ напряжениям
|
|
|
|
|
|
|
|
|
|
Коэффициенты концентрации |
|
|
|
|
|
|
||||||||||||||||
|
Тип |
|
|
|
|
|
|
|
при пределе прочности σв, МПа |
|
|
|
||||||||||||||||||||
|
концентратора |
|
|
|
|
|
|
kσ |
|
|
|
|
|
|
|
|
|
|
|
|
kτ |
|
|
|
|
|
|
|||||
|
|
|
|
|
500 |
|
|
700 |
|
900 |
|
1200 |
|
500 |
|
|
700 |
|
|
900 |
|
1200 |
|
|||||||||
|
Галтель при t / r = 2: |
|
|
|
|
|
|
|
|
|
|
|
|
|
|
|
|
|
|
|
|
|
|
|
|
|
|
|
|
|
||
|
|
|
r / d = 0,1 |
|
1,55 |
|
1,6 |
|
1,65 |
|
|
1,7 |
|
1,4 |
|
|
1,4 |
|
|
1,45 |
|
1,45 |
|
|||||||||
|
|
|
r / d = 0,2 |
|
1,8 |
|
|
1,9 |
|
2,0 |
|
|
2,15 |
|
1,55 |
|
1,6 |
|
|
1,65 |
|
1,7 |
|
|||||||||
|
Галтель при t / r = 3: |
|
|
|
|
|
|
|
|
|
|
|
|
|
|
|
|
|
|
|
|
|
|
|
|
|
|
|
|
|
||
|
|
|
r / d = 0,1 |
|
1,9 |
|
|
2,0 |
|
2,1 |
|
|
2,2 |
|
1,55 |
|
1,6 |
|
|
1,65 |
|
1,75 |
|
|||||||||
|
|
|
r / d = 0,2 |
|
1,95 |
|
2,1 |
|
2,2 |
|
|
2,4 |
|
1,6 |
|
|
1,7 |
|
|
1,75 |
|
1,85 |
|
|||||||||
|
Галтель при t / r = 5: |
|
|
|
|
|
|
|
|
|
|
|
|
|
|
|
|
|
|
|
|
|
|
|
|
|
|
|
|
|
||
|
|
|
r / d = 0,1 |
|
2,1 |
|
|
2,25 |
|
2,35 |
|
|
2,50 |
|
2,2 |
|
|
2,3 |
|
|
2,4 |
|
2,6 |
|
||||||||
|
|
|
r / d = 0,2 |
|
2,15 |
|
2,3 |
|
2,45 |
|
|
2,65 |
|
2,1 |
|
|
2,15 |
|
|
2,25 |
|
2,5 |
|
|||||||||
|
Шпоночный паз |
|
|
1,6 |
|
|
1,9 |
|
2,15 |
|
|
2,5 |
|
1,4 |
|
|
1,7 |
|
|
2,05 |
|
2,4 |
|
|||||||||
|
Для шлицов |
|
|
1,45 |
|
1,6 |
|
1,7 |
|
|
1,75 |
|
2,35 |
|
2,45 |
|
|
2,65 |
|
2,8 |
|
|||||||||||
|
Для резьбы |
|
|
1,8 |
|
|
2,2 |
|
2,45 |
|
|
2,9 |
|
1,8 |
|
|
2,2 |
|
|
2,45 |
|
2,9 |
|
|||||||||
|
Натяг (kσ(τ) / kd) при |
d = 30 мм |
|
2,5 |
|
|
3,0 |
|
3,5 |
|
|
4,25 |
|
1,9 |
|
|
2,2 |
|
|
2,5 |
|
2,95 |
|
|||||||||
|
|
|
|
|
|
|
|
|
|
|
|
|
|
|
|
|||||||||||||||||
|
|
|
d = 50 мм |
|
3,05 |
|
3,65 |
|
4,3 |
|
|
5,2 |
|
2,25 |
|
2,6 |
|
|
3,0 |
|
3,5 |
|
||||||||||
|
|
|
d ≥ 100 мм |
|
3,3 |
|
|
3,95 |
|
4,6 |
|
|
5,6 |
|
2,4 |
|
|
2,8 |
|
|
3,2 |
|
3,8 |
|
||||||||
|
Примечания: t – высота буртика |
, r – радиус галтели, d – диаметр вала. |
|
|
|
|
|
|
||||||||||||||||||||||||
|
|
|
Коэффициент влияния размеров детали kd |
|
|
|
|
Таблица 4.6 |
||||||||||||||||||||||||
|
|
|
|
|
|
|
|
|
|
|
|
|
||||||||||||||||||||
|
|
|
|
|
|
|
|
|
|
|
|
|
|
|
|
|
|
|
|
|
||||||||||||
|
Напряженное |
|
Материал |
|
|
|
|
|
Значения kd при диаметре вала, мм |
|
|
|
||||||||||||||||||||
|
состояние |
|
|
15 |
|
|
20 |
|
30 |
|
|
40 |
|
50 |
|
70 |
|
|
100 |
|
200 |
|
||||||||||
|
|
|
|
|
|
|
|
|
|
|
|
|
|
|
|
|||||||||||||||||
|
Изгиб |
|
Углеродистая |
|
0,95 |
|
0,92 |
|
0,88 |
|
0,85 |
|
0,81 |
|
0,76 |
|
0,70 |
|
0,61 |
|||||||||||||
|
|
сталь |
|
|
|
|
|
|
|
|
||||||||||||||||||||||
|
|
|
|
|
|
|
|
|
|
|
|
|
|
|
|
|
|
|
|
|
|
|
|
|
|
|
|
|
|
|
||
|
Изгиб, круче- |
Высокопрочная |
|
|
|
|
|
|
|
|
|
|
|
|
|
|
|
|
|
|
|
|
|
|
|
|
|
|
|
|
||
|
ние для всех |
|
легированная |
|
0,87 |
|
0,83 |
|
0,77 |
|
0,73 |
|
0,70 |
|
0,65 |
|
0,59 |
|
0,52 |
|||||||||||||
|
деталей |
|
сталь |
|
|
|
|
|
|
|
|
|
|
|
|
|
|
|
|
|
|
|
|
|
|
|
|
|
|
|
|
|
|
Коэффициент влияния шероховатости поверхности kF |
Таблица 4.7 |
||||||||||||||||||||||||||||||
|
|
|
|
|
|
|
||||||||||||||||||||||||||
|
|
|
|
|
|
|
|
|
|
|
|
|
|
|
|
|
|
|
|
|
|
|
|
|
|
|
|
|
||||
|
|
|
|
|
|
|
Среднее арифметическое |
|
|
|
Значение |
|
|
|
||||||||||||||||||
|
Механическая |
|
|
|
коэффициента kF |
|||||||||||||||||||||||||||
|
|
|
|
|
|
отклонение |
|
|
|
|
||||||||||||||||||||||
|
обработка поверхности |
|
|
|
|
|
|
|
|
|
|
при σв, МПа |
||||||||||||||||||||
|
|
|
|
|
|
профиля Ra, мкм |
|
|
|
|
|
|||||||||||||||||||||
|
|
|
|
|
|
|
|
|
|
|
|
400 |
|
|
600 |
|
800 |
|
||||||||||||||
|
|
|
|
|
|
|
|
|
|
|
|
|
|
|
|
|
|
|
|
|
|
|
|
|||||||||
|
Шлифование |
|
|
|
|
|
|
0,32 ÷ 0,08 |
|
|
|
|
|
1 |
|
|
|
1 |
|
1 |
|
|||||||||||
|
Обточка |
|
|
|
|
|
|
2,50 ÷ 0,32 |
|
|
|
1,05 |
|
|
1,10 |
|
1,25 |
|
||||||||||||||
|
Обдирка |
|
|
|
|
|
|
|
|
|
20 ÷ 5 |
|
|
|
|
|
1,20 |
|
|
1,25 |
|
1,5 |
|
|||||||||
|
Необработанная поверхность с |
|
|
|
|
|
|
|
|
— |
|
|
|
|
|
|
1,35 |
|
|
1,5 |
|
2,2 |
|
|||||||||
|
окалиной и т.д. |
|
|
|
|
|
|
|
|
|
|
|
|
|
|
|
|
|
|
|
||||||||||||
|
|
|
|
|
|
|
|
|
|
|
|
|
|
|
|
|
|
|
|
|
|
|
|
|
|
|
|
|
|
|
27

|
|
|
Таблица 4.8 |
Коэффициент влияния упрочнения kV при поверхностной обработке |
|||
|
|
Образец |
|
Вид упрочнения |
|
без |
с |
|
концентрации |
концентрацией |
|
|
|
||
|
|
напряжений |
напряжений |
Закалка ТВЧ углеродистых и легированных сталей |
1,2 ÷ 1,5 |
1,5 ÷ 2,5 |
|
Азотирование при глубине слоя |
0,1 ÷ 0,4 мм |
1,1 ÷ 1,15 |
1,3 ÷ 2,0 |
Азотирование при толщине слоя |
0,2 ÷ 0,6 мм |
1,1 ÷ 1,5 |
1,2 ÷ 2,0 |
Обкатка роликами углеродистых и легированных |
|
|
|
сталей |
|
1,1 ÷ 1,25 |
1,3 ÷ 1,8 |
Обдувка дробью углеродистых и легированных
сталей 1,1 ÷ 1,2 1,1 ÷ 1,5
Примечание: большие значения выбирают при большей концентрации напряжений.
Таблица 4.9
Моменты сопротивления некоторых сложных плоских фигур (к расчету валов)
Форма поперечного |
|
Момент сопротивления |
Момент сопротивления |
||||||||||||||||
сечения |
|
|
|
изгибу Wизг |
|
|
|
|
|
кручению Wкр |
|
||||||||
Сечение вала со шпоночным |
|
|
|
|
|
|
|
|
|
|
|
|
|
|
|
|
|
||
пазом |
|
|
|
|
|
|
|
|
|
|
|
|
|
|
|
|
|
|
|
b |
1 |
|
|
|
|
|
|
|
|
|
|
|
|
|
|
|
|
|
|
|
t |
|
|
|
|
|
|
|
|
|
|
|
|
|
|
|
|
|
|
|
|
|
W |
|
= πd3 |
− bt1(d −t1 )2 |
|
W |
= πd3 |
− bt1(d −t1 )2 |
|||||||||
|
|
|
x |
32 |
|
|
2d |
|
|
|
кр |
|
16 |
|
2d |
|
|||
|
|
|
|
|
|
|
|
|
|
|
|
|
|
||||||
d |
|
|
|
|
|
|
|
|
|
|
|
|
|
|
|
|
|
|
|
Сечение червяка |
|
|
|
|
|
|
|
|
|
|
|
|
|
|
|
|
|
|
|
|
y |
|
W |
=W |
|
= |
πd3 |
|
|
|
|
|
|
|
|
|
|
||
|
|
|
y |
|
f 1 × |
|
|
|
|
|
|
|
|
|
|||||
|
|
|
|
x |
|
|
32 |
|
|
|
|
|
|
|
= πd3f 1 |
|
|||
a1 f1 |
|
|
|
|
|
|
|
da1 |
|
|
|
|
|
W |
|
||||
|
1 |
|
|
|
|
|
|
|
|
|
|
кр |
16 |
|
|||||
x |
× |
|
0,375 |
+0,625 |
|
|
|
|
|
|
|
||||||||
d d |
d |
|
|
|
|
|
|
|
|
|
|
|
|||||||
|
|
|
|
|
|
|
|
|
|
d f 1 |
|
|
|
|
|
|
|
|
|
Сечение вала со шлицами |
|
|
|
|
|
|
|
|
|
|
|
|
|
|
|
|
|
||
y |
b |
|
Wx =Wy = |
π d 4 |
× |
|
|
|
|
Wкр |
= |
π d4 |
× |
|
|
||||
|
|
|
|
|
|
|
32D |
|
|
|
|
|
16D |
|
|
||||
|
D |
|
× 1 |
+ bz(D − d )(D + d ) |
2 |
|
|
|
|
|
|
||||||||
|
|
|
bz(D −d )(D +d )2 |
||||||||||||||||
|
|
|
|
|
|
|
|
|
|
|
|
|
|
|
|
|
|
|
|
|
x |
|
|
|
|
|
|
π d 4 |
|
|
|
|
× 1+ |
|
|
4 |
|
||
d |
|
|
|
|
|
|
|
|
|
|
|
|
|
|
|
π d |
|
|
|
|
|
где z – число шлицев |
|
|
|
|
|||||||||||||
|
|
|
|
|
|
|
|
|
|
28

Окончание табл. 4.9
Сечение вала с отверстием под
штифт y dшт
W |
|
|
πd 3 |
|
d |
|
|
W |
|
|
πd 3 |
|
d |
|
|
x |
= |
|
1−1,7 |
|
шт |
x |
= |
|
1− |
|
шт |
||||
|
|
|
|
||||||||||||
|
|
32 |
|
d |
|
|
|
16 |
|
d |
|
||||
|
|
|
|
|
|
x
d
Пример.
Для конического вала (рис. 4.2, а) составить расчетную схему (рис. 4.2, б), построить эпюры моментов (рис. 4.2, в), определить опасное сечение для расчета на усталостную прочность.
а)
б)
в)
Рис. 4.2. Ступенчатый вал с консольным колесом
29

Размеры l1, l2, l3, l4 следует выбирать по рекомендации к рис. 4.1.
Из построенных эпюр следует, что опасное сечение находится под правым подшипником. Используя численные значения сил и расстояний, а также формулы из табл. 4.2, определяем коэффициент запаса прочности.
4.2. Проверка жесткости вала
Проверка жесткости вала имеет целью определение прогибов вала f и углов его поворота θ в опорах. Это позволяет скорректировать, при необходимости, диаметр вала и уточнить выбор подшипников. Расчет актуален для относительно длинных валов, например, для вала червяка.
Для выполнения этих расчетов допускается замена ступенчатого вала эквивалентным постоянного диаметра.
Рис. 4.3. Схема упругих перемещений вала
Рис. 4.4.Прогиб червяка—установка «враспор» (две шарнирные опоры)
Рис. 4.5. Прогиб червяка— установка с плавающей опорой (левая опора—заделка)
30