
на мобилу / Б7
.pdfБилет №7
1. вопрос. Клапаны ТНВД. Они также относятся к прецизионным деталям. В судовых насосах применялись всасывающие и отсечные клапаны, однако механические управляемые регулирующие клапаны ныне - устаревшие. В большинстве ТНВД всех типов - автоматические нагнетательные клапаны, разъединяющие линию высокого давления и надплунжерную полость (рис. 2.10, 2.14). Это: улучшение наполнения над плунжерной полости; создание в нагнетательном трубопроводе в период между впрыскиваниями заданного остаточного давления; корректирование скоростной характеристики топлива. Встречаются без нагнетательных клапанов. Проще, в них нет подвпрыскивания, но помимо прочего, повышаются требования к надежности запирающего элемента форсунки.
Наиболее распространены грибковые клапаны (рис. 2.24, а-г, з). Под действием давления топлива клапан, сжимая пружину, перемещается в осевом направлении. Для исключения радиального биения разгружающего пояска 2 при входе в канал и конической поверхности клапана при посадке на седло 3 эти поверхности так же, как и крестообразные направляющие (перья) 1 клапана, изготовляют с высокой точностью. Прецизионной является также нижняя торцовая поверхность корпуса клапана. Как правило, она образует с верхним торцом втулки плунжера беспрокладочное герметичное соединение, при этом корпус клапана притягивают к втулке штуцером.
Цилиндрические клапаны (рис. 2.24, ж) отличаются такой же надежностью, как грибковые, но компактнее их, поэтому применяются на крупных дизелях. Плоские (рис. 2.24, е, и) и шариковые (рис. 2.24, д) имеют малую массу, т.е. высокое быстродействие, однако их надежная работа обеспечивается при соблюдении ряда конструктивных и технологических условий, другими словами, их простота обманчива.
После закрытия клапана остановка столба топлива обусловливает гидроудар, образование волны давления, вызывающей повторное открытие форсунки - подвпрыскивание. Все изображенные на рис. 2.24 клапаны различными способами противодействуют ему. Популярнейшее решение - разгружающий поясок 2 при закрытии клапана входит в седло 3. С этого момента надплунжерная полость и нагнетательный трубопровод разобщаются, так как разгружающий поясок образует с каналом зазор 8...15 мкм, и дальнейшее опускание клапана приводит к увеличению объема полостей, образующих ЛВД. Увеличение объема сопровождается уменьшением давления в нагнетательном трубопроводе, так называемой разгрузкой. Таким образом, выбором размеров нагнетательного клапана обеспечивают оптимальное значение остаточного давления, исключающее подвпрыскивание, но сохраняющее возможность впрыскивания в следующий цикл с большими давлениями.
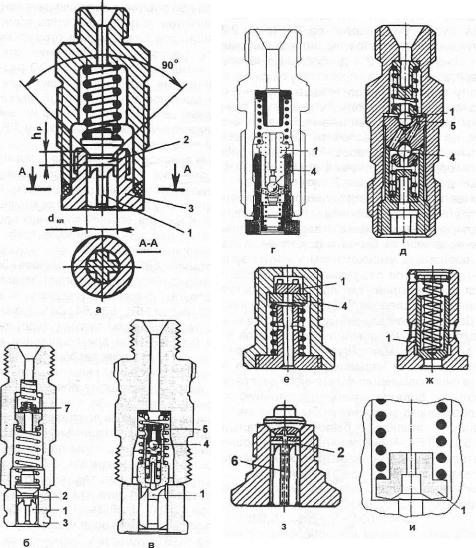
РИС. 2.24. Нагнетательные клапаны ТНВД:
1 - нагнетательный клапан;
2 - разгружающий поясок;
3 - седло клапана;
4 - реверсивный клапан для подавления волны давления; 5 - жиклер; 6 - каналы клапана-корректора; 7 - последовательный клапан.
Простейшее решение - жиклер в клапане (рис. 2.24, и) не может обеспечить повышенного остаточного давления. Последовательный нагнетательному клапан 7 (рис. 2.24, б) не мешает впрыскиванию, но, закрываясь, тормозит посадку нагнетательного и таким образом демпфирует гидроудар и уменьшает остаточное давление за
счет роста вытекающего из трубопровода топлива при отсечке. Применяются и другие замедлители посадки клапана, например, гидроподушка под его седлом. Радикальное решение в борьбе с подвпрыскиванием - установка реверсивного,, клапана 4 параллельно нагнетательному, но направленного в противоположную сторону (рис. 2.24, в-е). Реверсивные клапаны ослабляют гидроудар перепуском топлива в ппунжерную полость и обеспечивают стабильное начальное давление. Управление этим процессом осуществляют тщательным подбором последовательного с реверсивным клапаном жиклера 5.
2. вопрос. Испытания форсунок
ведут на одноплунжерных опрессовочных стендах, а в условиях производства или крупного сервиса - на полуавтоматизированных высокопроизводительных стендах типа.
Визуальный контроль качества впрыскивания. При впрыскивании с частотой 60...80 раз в минуту топливо должно образовывать туман без видимых сгущений, струй, капель. Струи должны быть симметричными и не отклоняться от заданного направления. Нужно обязательно сосчитать количество струй, при необходимости используя бумажный экран. В связи с увеличением числа и уменьшением диаметра сопловых отверстий растет вероятность засорения сопел и возможность этого не заметить при испытаниях форсунки. Если из сопел выходят вялые струи ("усы"), значит, напора нет.
Проверка подвижности иглы. Помимо сказанного, о затрудненном движении иглы свидетельствует отсутствие дробящего впрыскивания новой форсунки. При этом форсунка должна "звенеть" (точнее - скрипеть). Однако поработавшие форсунки с частично смятыми конусами, оставаясь еще работоспособными, не "звенят" (в этом -
ошибочность требований ГОСТ). Другой признак малоподвижности - увлажнение носика распылителя после впрыскивания (он должен оставаться сухим, но может увлажняться также и из-за негерметичности запорного конуса). Наконец, рекомендован прямой контроль подвижности: игла, вынутая на 1/3 из распылителя, промытого в топливе и наклоненного по 45° к горизонту, должна свободно опускаться под действием тяжести. Проверка герметичности (по запорному конусу иглы) производится при выдерживании форсунки в течение 20 с под давлением Р=Рфо— (1...1.5 МПа), т.е. с максимальной разгрузкой конуса от запирающей силы. Перед испытанием нужно сделать несколько энергичных впрыскиваний. При этом допустимо "потение", незначительное увлажнение носика, но не образование капли. Это испытание работавшие форсунки часто не выдерживают, что приводит к закоксо-выванию внешних поверхностей распылителей. Проверка гидроплотности (по прецизионной цилиндрической поверхности иглы). Регламентируется минимальное время падения давления. Обычно при использовании дизельного топлива в интервале 20... 18 МПа гидроплотность не менее 5 с. Однако, условия строго регламентируются ТУ на испытания (интервал давлений, вязкость топлива или смеси, объем ЛВД, герметичность испытательного стенда).
Давление начала впрыскивания Рфо контролируется при медленном опускании рычага привода стенда. С учетом естественного падения Рфо в эксплуатации, встречаются две его нормы, например, для КамАЗ у новой форсунки модели "33" - Рфо=22...22,7 МПа, но исправной в эксплуатации считается Рф0 20 МПа. Чем выше Рфо, тем качественнее впрыскивание, при регулировке целесообразно ориентироваться на верхнюю границу интервала. Однако нельзя сильно завышать Рфо во избежание ухудшения пуска и холостого хода.
Проверка пропускной способности распылителя правильно осуществляется методом статической проливки топливом при напоре не менее 5 МПа. При этом обычно форсунка
собрана игла вставлена, но удалена пружина. Обычно в процессе эксплуатации F сопел растет в результате износа кромок и ствола отверстий, а с ним уменьшается давление и качество впрыскивания. Прочистку сопловых отверстий ведут проволочками и специнструментом (выпускаются в наборах). Важно не обломить инструмент, поэтому работают сидя, на чистом столе, при хорошем освещении (на всех заводах сопла сверлят только женщины). Используют также измерение мгновенного расхода воздуха, обеспечиваемого форсункой при статической продувке. Применяют также сортировку по группам, каждую топливную систему укомплектовывают в этом случае из одной группы.
Иные проверки. Охлаждаемые форсунки проверяют на герметичность полости охлаждения. Распылители могут подвергаться контролю точности соблюдения направления струй и равномерности или заданного соотношения топлива, подаваемого через отверстия.