
741
.pdfТаблица 6.2
Температура плавления и плотность металлов
|
Атомная |
|
20î Ñ , |
tΠΛ , |
ρtΠΛ+100oC, |
|
ρÒÂ − ρ |
Æ |
|
|
Металл |
масса |
tпл, ºC |
ρTB |
ρæ |
æ |
( |
|
)tïë |
100% |
|
ρÒÂ |
|
|||||||||
|
|
кг/м3 |
кг/м3 |
кг/м3 |
|
|
|
|
||
Алюминий |
27 |
660 |
2700 |
2380 |
2350 |
|
|
6,5 |
|
|
Берилий |
9 |
1285 |
1850 |
1690 |
— |
|
|
— |
|
|
Висмут |
209 |
271 |
9800 |
10000 |
9920 |
|
|
–3,3 |
|
|
Вольфрам |
184 |
3400 |
19300 |
16740 |
— |
|
|
3 |
|
|
Галий |
70 |
30 |
5900 |
6100 |
6040 |
|
|
–3,5 |
|
|
Германий |
73 |
937 |
5300 |
5500 |
5440 |
|
|
–5,0 |
|
|
Железо |
56 |
1539 |
7870 |
7000 |
6910 |
|
|
5,0 |
|
|
Золото |
197 |
1063 |
19300 |
17350 |
17025 |
|
|
5,0 |
|
|
Кадмий |
112 |
321 |
8640 |
8020 |
7950 |
|
|
4,3 |
|
|
Кальций |
40 |
840 |
1540 |
— |
— |
|
|
— |
|
|
Кремний |
28 |
1420 |
2350 |
2530 |
2500 |
|
–10,0 |
|
||
Литий |
7 |
181 |
0530 |
500 |
— |
|
|
— |
|
|
Магний |
24 |
650 |
1740 |
1590 |
1550 |
|
|
5 |
|
|
Марганец |
55 |
1240 |
7400 |
6750 |
- |
|
|
— |
|
|
Медь |
64 |
1083 |
8960 |
8000 |
7920 |
|
|
5,5 |
|
|
Молибден |
96 |
2620 |
10200 |
890 |
— |
|
|
4 |
|
|
Натрий |
23 |
98 |
970 |
— |
— |
|
|
— |
|
|
Никель |
59 |
1455 |
8900 |
7900 |
7780 |
|
|
5,3 |
|
|
Ниобий |
93 |
2460 |
8600 |
7850 |
— |
|
|
— |
|
|
Олово |
119 |
232 |
7300 |
7000 |
6900 |
|
|
3,5 |
|
|
Ртуть |
201 |
–39 |
13550*2 |
13700 |
13460 |
|
|
3,7 |
|
|
Свинец |
207 |
327 |
11350 |
10680 |
10550 |
|
|
3,5 |
|
|
Серебро |
108 |
961 |
10500 |
9350 |
9260 |
|
|
4,0 |
|
|
Сурьма |
122 |
630 |
6700 |
6490 |
6430 |
|
|
–1,0 |
|
|
Титан |
48 |
1670 |
4500 |
4100 |
4030 |
|
|
4 |
|
|
Хром |
52 |
1815 |
7150 |
6300 |
— |
|
|
6 |
|
|
Цинк |
65 |
419 |
7140 |
6570 |
6460 |
|
|
4,0 |
|
|
Цирконий |
91 |
1850 |
6500 |
600 |
— |
|
|
5 |
|
По температуре плавления металлы подразделяют на легкоплавкие (температура плавления не выше 600 ºС), среднеплавкие (от 600 ºС до 1600 ºС) и тугоплавкие (более 1600 ºС) — вольфрам, молибден, титан, хром и др.
По плотности металлы делят на легкие (плотность меньше 5 000 кг/м3), тяжелые (плотность от 5 000 до 10 000 кг/м3) и очень тяжелые (плотность более 10 000 кг/м3). Ртуть относится к жидкостям.
Плотность всех металлов при нагреве в твердом состоянии до температуры плавления уменьшается. При температуре плавления плотность изменяется скачкообразно. У некоторых металлов и неметаллов она увеличивается: у висмута на 3,3 %, галия на 3,6 %, германия на 5 %, кремния на 10 %, сурьмы на 1 %. У большинства компонентов технических сплавов при нагреве их от комнатной до температуры плавления плотность уменьшается на 3,0–6,5 %. При дальнейшем нагреве металлов в жидком состоянии у всех компонентов, приведенных в табл. 6.2, плотность уменьшается.
Теплота плавления металлов q, кДж/кг у компонентов промышленных сплавов сильно различается. Теплота плавления свинца составляет 25 кДж/кг, а кремния 1700 кДж/кг.
Для основ важнейших литейных сплавов теплота плавления q, кДж/кг, составляет:
Металл |
Zn |
Al |
Cu |
Fe |
q, кДж/кг |
105 |
400 |
205 |
272 |
Удельные теплоемкости С распространенных металлов находятся в пределах 120–1200 Дж/(кг · ºС). При повышении температуры теплоемкость металлов, как правило, растет. Для некоторых основ сплавов значения теплоемкостей при комнатной температуре Ст и вблизи температуры плавления Спл приведены ниже:
Основа сплава |
Zn |
Al |
Cu |
Fe |
Ст, Дж/(кг · ºС) |
419 |
1090 |
440 |
695 |
Спл |
502 |
1290 |
545 |
922 |
Теплопроводность, Вт/(м · ºС) — λ зависит от состава сплава и наличия примесей. Даже небольшое содержание примесей может ее сильно уменьшить.
Теплопроводность основ сплавов при комнатной температуре λт и вблизи температуры плавления λпл имеет следующие значения:
Основа сплава |
Zn |
Al |
Cu |
Fe |
λт при 20 ºС, Вт/(м · ºС) |
102 |
213 |
320 |
87 |
λпл, Вт/(м · ºС) |
58 |
104 |
290 |
23,3 |
Теплофизические свойства литейных сплавов приведены в табл. 6.3.
Таблица 6.3
Теплофизические свойства литейных сплавов
Сплав |
Температура, |
ρ, кг/м3 |
С, Дж/(кг · ºС) |
λ, Вт/(м · ºС) |
|
ºС |
|
|
|
Углеродистая сталь |
1530 |
7200 |
920 |
23 |
|
|
|
|
|
Серый чугун |
800–1200 |
6600–7200 |
750–800 |
38–42 |
|
|
|
|
|
Медные сплавы |
1070 |
8700 |
500 |
42–101 |
|
|
|
|
|
Алюминиевые сплавы |
650 |
2600 |
1200 |
83–102 |
Отношение теплопроводности к электропроводности сплавов для большинства металлов постоянно.
6.3.Строение металлических расплавов
иявление наследственности
Металлические расплавы в интервале температур плавления – кипения имеют различное строение. Вблизи температуры плавления это жидкости, однородные в макрообъеме, но неоднородные в микрообъемах, которые представляют собой микрогетерогенную систему, состоящую из
динамических кластеров, областей с неупорядоченным расположением атомов и статистических кластеров — нерасплавленных долгоживущих остатков твердой породы.
Динамический кластер — это группировки атомов в расплаве, имеющие более или менее упорядоченное строение, схожее со структурой твердого кристалла.
При плавлении происходит дробление кристаллов на группировки, имеющие размеры 16–24 атомных радиусов, окруженные атомами с неупорядоченным строением.
Объемная доля кластеров при температуре плавления составляет 70–90 %. При дальнейшем повышении температуры жидкого металла выше критической происходит полное разрушение кластеров и расплав переходит в бесструктурную жидкость.
Структурное состояние металлических расплавов ниже критической температуры можно выразить следующим образом:
Σψклд + Σψклс + ψраз = 1, где Σψклд — объемная доля динамических кластеров; Σψклс — объемная доля статических
кластеров, представляющих собой нерасплавленные тугоплавкие частицы; ψраз — доля межкластерной разупорядоченной зоны.
Модель поликластерного строения металлических расплавов позволяет объяснить явление наследственности свойств — в системе шихта – расплав – отливка.
Замечено, что если шихта имеет мелкокристаллическую (или крупнозернистую структуру), то после расплавления ее без перегрева отливка также имеет мелкокристаллическое (или крупнозернистое) строение.
На основе теории наследственности разработаны многие технологические процессы повышения механических свойств отливок. Например, в составе шихты используют быстрозакаленные мелкокристаллические лигатуры, а если шихта имеет крупнозернистое строение, то расплав нагревают выше критической температуры с целью уничтожения неблагоприятной структуры, а затем модифицируют его.
Такими технологическими приемами получают отливки с мелкозернистой структурой и высокими механическими свойствами.
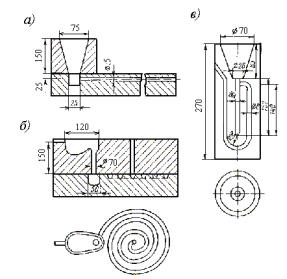
6.4.Литейные свойства сплавов
Клитейным свойствам сплава относятся: жидкотекучесть, усадка, склонность к трещинообразованию, ликвация и другие. Литейные свойства сплава характеризуют его технологичность при формировании отливки требуемого качества.
Жидкотекучесть — это свойства расплава заполнять литейную форму. Жидкотекучесть сплавов определяют путем заливки различных технологических проб. Наибольшее распространение получили пробы, формы для заливки которых показаны на рис. 6.1.
Рис. 6.1. Пробы на жидкотекучесть
О жидкотекучести судят по длине залитой полости пробы. Форма технологической пробы на рис. 6.1, а имеет горизонтальный цилиндрический канал диаметром 5 мм, а на рис. 6.1, б полость в форме выполнена в виде спирали, имеющей в сечении профиль трапеции высотой 8 мм вверху и 7 мм внизу.
На рис. 6.1, в показана комплексная проба Нехендзи – Купцова для определения литейных свойств сплавов: жидкотекучести по длине залитой части U-образной полости диаметром 8 мм; линейной усадки; склонности к трещинообразованию; склонности к образованию усадочных пустот и пористости. После разрезки пробы по ее частям можно определить структуру, содержание газов и неметаллических включений.
Наибольшей жидкотекучестью обладают сплавы эвтектического состава, чистые металлы и интерметаллоиды, кристаллизующиеся при постоянной температуре.
Прямой зависимости жидкотекучести от вязкости и поверхностного натяжения расплава не установлено.
Жидкотекучесть сплавов с большей величиной теплоты кристаллизации выше. Жидкотекучесть резко снижается при окислении сплавов при добавлении к расплаву элементов
с большим сродством к кислороду, в связи с образованием поверхностных окисных пленок. Заполняемость форм — это комплекс технологических факторов, характеризующих условия
заполнения формы. Жидкотекучесть представляет составляющую этого комплекса, определяющую качество сплава как литейного материала.
Заполняемость тонких стенок — наиболее сложная задача практики литья.
Для каждого способа литья существуют ограничения по толщине стенок отливок, получаемых этим методом. Например, при литье по выплавляемым моделям возможно получение отливок с толщиной стенки 1 мм, если ее площадь не превышает 75×75 мм2.
Усадка металла — изменение объема металла при переходе его из жидкого состояния в твердое. Усадка — одно из основных свойств литейных сплавов, определяющих качество отливки.
Коэффициент усадки численно характеризует изменение объемных или линейных размеров тела при охлаждении до комнатной температуры и выражается в долях единицы или в процентах.
Усадка металла или полная объемная усадка складывается из усадки его в жидком состоянии,
усадки в интервале затвердевания и усадки в твердом состоянии.

Усадка металла в жидком состоянии — это изменение объема металла Vз до Vл при его охлаждении от температуры заливки tз до температуры ликвидус tл.
Коэффициент объемной усадки в интервале затвердевания αз выражается в долях единицы. Для металлов он равен:
Металл |
Fe |
Cu |
Al |
Mg |
αз |
0,030 |
0,044 |
0,066 |
0,051 |
Коэффициент усадки в твердом состоянии αт определяется по изменению линейных размеров тела:
αò = |
|
lt − lo |
|
, |
||
l |
|
) |
||||
|
o |
(t − t |
o |
|
||
|
|
|
|
|
где lt и lo —размеры тела при температуреt и to соответственно, м.
Соотношение коэффициентов объемной αVò и линейной усадки αëò принимают:
αVò = 3 αëò .
Коэффициент линейной усадки сплавов αл, выраженный в %, принимают как отношение размеров полости литейной формы lф к размеру отливки при комнатной температуре:
αë = lô − lo 100% . lo
Линейная усадка сплава — свободная усадка и фактическая усадка отливки отличаются из-за термического или механического торможения формы усадкe отливок. Такая усадка носит название
затрудненной или литейной.
Литейная усадка серого чугуна для отливок простой конфигурации составляет 0,9–1,0 %, для средней сложности 0,8–0,9 %, а для сложной 0,7–0,8 %.
К литейным свойствам сплавов относятся также склонность к трещинообразованию, окисляемость, склонность к отбелу, образованию рассеянной пористости, склонность к ликвации, свариваемость и др. Эти свойства определяют по технологическим пробам, конструкции которых и способ изготовления стараются приблизить к реальным условиям изготовления отливки.
Контрольные вопросы
1.Дайте определения сплаву, компонентам сплава, химическому составу сплава и его механическим свойствам.
2.Опишите свойства расплавленных металлов как жидкостей.
3.В чем заключаются теплофизические свойства металлов?
4.От чего зависят строение металлических расплавов и явление наследственности?
5.Перечислите литейные свойства сплавов.
Глава 7. Общая технология плавки литейных сплавов
7.1. Основные положения разработки технологии плавки
Схема технологического процесса плавки литейных сплавов приведена на рис. 7.1.
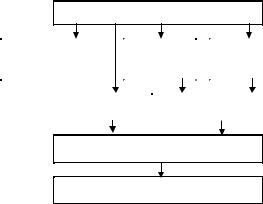
Разработка технологии плавки
|
Приобретение |
|
|
Расчет |
|
Подготовка |
|||
|
|
|
шихты |
|
шихтовых |
||||
|
материалов |
|
|
|
|||||
|
|
|
|
|
|
|
материалов |
||
|
|
|
|
|
|
|
|
||
|
|
|
|
|
|
|
|||
|
Подготовка плавильной |
|
|
|
Навеска шихты |
|
|||
|
печи к плавке |
|
|
|
|
|
|
Загрузка шихты в печь и плавка
Подготовка ковша и выпуск металла из печи в ковш
Рис. 7.1. Схема технологического процесса плавки литейных сплавов
Разработку технологического процесса плавки начинают с анализа его химического состава
и свойств: температуры плавления, химической активности элементов, склонности к
поглощению газов и количественной потребности.
Прежде всего выбирают тип плавильной печи, ее мощность, материал тигля или ванны. Разрабатывается технология футеровки печи и подготовки ее к плавке.
Влитейном производстве применяют следующие плавильные печи: вагранки для плавки чугуна; электрические дуговые и индукционные печи для плавки чугуна, стали и цветных металлов; электрические печи сопротивления для плавки алюминиевых и магниевых сплавов.
Титановые и жаропрочные сплавы плавят и разливают в вакуумных печах.
Вбольшинстве случаев плавку ведут в атмосфере воздуха. Для защиты сплавов от взаимодействия с атмосферой печи их плавки ведут под покровом шлака или флюса. Расход шлакообразующей смеси и флюса обычно составляет 2 % от количества металла в печи.
Взависимости от выбранного типа печи производят расчет шихты, определяют ее массу, состав, размеры и способы подготовки к плавке. Затем устанавливают температурные режимы плавки и способы обработки расплава перед выпуском жидкого металла из печи в ковш.
Применяют следующие виды обработки жидких расплавов: раскисление, рафинирование и модифицирование.
Раскисление — это удаление из жидкого металла растворенного в нем или связанного в оксиды кислорода путем введения в расплав веществ с бо´льшим сродством к кислороду, чем основа сплава. Сталь раскисляют марганцем, кремнием, алюминием; медь — фосфором, магнием. Количество раскислителя составляет 0,1–0,3 % от массы обрабатываемого сплава.
Алюминиевые и магниевые сплавы не раскисляют.
Рафинирование — это процесс удаления из металлического расплава растворенных газов и неметаллических включений.
Способы рафинирования: фильтрация — процесс разливки металла через тканевые, зернистые и пенокерамические фильтры; продувка расплавов газами — аргоном, хлором; обработка сплавов хлористыми или углекислыми солями; вакуумирование жидкого металла; обработка сплавов вибрацией, ультразвуком, электрическими и магнитными полями, выстаиванием или замораживанием.
Модифицирование — это процесс обработки металлических расплавов с целью получения однородной мелкозернистой структуры сплава после кристаллизации. В результате модифицирования можно изменить форму и размер фазовых составляющих сплава.
Наиболее распространены методы модифицирования, основанные на введении в расплав небольших количеств веществ-модификаторов (0,05–0,7 %).
Модификаторы I рода (Ti, B) измельчают зерно за счет образования в расплаве большого количества центров кристаллизации.
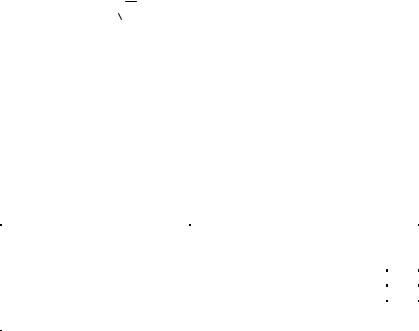
Модификаторы II рода (Na, Mg), являясь поверхностно-активными веществами, препятствуют росту первичного зерна и изменяют формы графита в чугунах и форму эвтектики в алюминиевых сплавах.
Раскисленный, рафинированный и модифицированный сплав сохраняет свои свойства в течение определенного промежутка времени. Поэтому в техпроцессе указывается допустимый срок времени от выпуска металла из печи до конца разливки всей массы расплава в формы.
В технологии на плавку литейных сплавов указываются методы контроля их химического состава, температуры, структуры и механических свойств.
7.2. Взаимодействие металлов при плавке с газами
При загрузке шихты в печь начинаются процессы взаимодействия металлов с атмосферой печи,
окисления поверхности шихты и растворения газов. С повышением температуры увеличиваются
интенсивность окисления и растворимость газов в металлах.
Содержание газов [Г] в металле принято выражать в % или см3/ 100 г. При переходе из
жидкого состояния в твердое растворимость газа в металле изменяется скачкообразно.
При постоянной температуре растворимость газа [Г] в жидком металле зависит от
парциального давления газа над расплавом — p (закон А. Сивертса):
[Г] = Ê ð ,
где К — постоянный коэффициент.
Способность основ промышленных сплавов поглощать газы из атмосферы печи приведена в
табл, 7.1 и отмечена знаком «+», в графе металлов, не растворяющих указанный газ, стоит знак «–».
Таблица 7.1
Взаимодействие жидких металлов с газами и газообразующими элементами
Газ или газообразующий элемент |
|
|
|
Металл |
|
|
|
||
Mg |
Al |
Cu |
|
Mn |
|
Ni |
Fe |
Cr |
|
|
|
|
|||||||
Кислород |
– |
– |
+ |
|
+ |
|
+ |
+ |
+ |
Водород |
+ |
+ |
+ |
|
+ |
|
+ |
+ |
+ |
Азот |
– |
– |
– |
|
+ |
|
+ |
+ |
+ |
Углерод |
– |
– |
– |
|
+ |
|
+ |
+ |
+ |
Сера |
– |
+ |
+ |
|
_+ |
|
+ |
+ |
+ |
С кислородом большинство металлов активно взаимодействуют как в твердом, так и в
жидком состояниях. Конечным продуктом взаимодействия являются оксиды.
Особенность расплавов чистых металлов состоит в том, что при их охлаждении и
кристаллизации избыточный сверх растворимости кислород не выделяется из раствора в свободном
виде, а переходит в твердые соединения — оксиды. В результате эвтектического превращения (в
системе Сu – О) медь с оксидом меди образует эвтектику (Сu – Сu2О), которая снижает
механические свойства сплава.
Растворившийся в жидком расплаве кислород уже не может покинуть его в чистом виде и не может образовать в отливках кислородной газовой пористости, за исключением серебра, в котором кислород при 940 ºС выделяется по газоэвтектической реакции жидкость – кристалл
– газ, и в результате отливки поражаются кислородной пористостью.
Склонность металлов к окислению характеризуется теплотой образования оксида — ΔН, кДж/моль О2, величина которой отрицательна. Это означает, что реакция происходит с выделением
тепла.
Металл |
Cu |
Fe |
Al |
Mg |
Si |
Оксид |
Cu2O |
FeO |
Al2O3 |
MgO |
SiO2 |
ΔН, кДж/моль О2 |
–405 |
–480 |
–1126 |
–1220 |
–950 |
Водород составляет основную долю газов, растворенных в жидком металле. Растворимость
водорода [Н], выраженная в см3/100 г металла, в жидком металле при температуре (tпл + 100 ºС) и
tпл и в твердом металле при температуре tкр, при этом (tпл = tкр), характеризуется следующими
величинами:
Жидкий металл |
Fe |
Mg |
Al |
Cu |
Ni |
Ti |
tпл + 100 ºС |
30 |
40 |
1 |
7 |
45 |
1200 |
tпл |
24 |
30 |
0,7 |
5 |
40 |
1000 |
Твердый металл |
|
|
при 1000 ºС |
|
|
|
tкр |
12 |
20 |
0,05 |
3 |
20 |
5000 |
Если величина теплоты растворения водорода в металле имеет положительное значение, то в отливках из этих металлов водород образует газовую пористость. К таким металлам относятся Al, Mg, Cu, Ni, Fe.
Молекулярный азот взаимодействует с жидкими металлами с малой интенсивностью.
Атомарный азот либо растворяется в жидком металле, либо образует нитриды. Растворимость азота в марганце, железе, никеле происходит с поглощением тепла, поэтому с понижением температуры растворимость азота снижается, а в отливках возможно образование газовой пористости.
В хроме азот растворяется с выделением тепла, поэтому при кристаллизации азот образует с хромом первичные нитриды хрома Cr2N и эвтектики Cr – Cr2N.
Взаимодействие жидких металлов с парами воды
Легкоплавкие металлы до цинка включительно не растворяют ни кислород, ни водород. Следовательно, эти металлы в жидком состоянии будут окисляться парами воды, а водород будет уходить в атмосферу.
Жидкий магний и алюминий будут окисляться и покрываться слоем оксида, но освободившийся водород будет переходить в расплав, т.е. сплавы магния и алюминия при взаимодействии с парами воды будут интенсивно насыщаться водородом.
Остальные металлы, начиная с меди, будут окисляться на поверхности жидкого металла и одновременно растворять кислород и водород.
Взаимодействие жидких металлов с оксидом углерода СО
Все легкоплавкие металлы, включая алюминий, будут окисляться по реакции
Me + CO = MeO + C.
Медь и серебро не взаимодействуют с оксидом углерода. Поэтому данный газ является для них защитной средой при плавке и позволяет получать чистые металлы. Все остальные металлы, представленные в табл. 7.1, способны поглощать углерод и кислород, поэтому их взаимодействие будет определяться температурой, концентрацией [С] и [О] в расплаве и парциальным давлением СО над расплавом.
Взаимодействие жидких металлов с СО2
Для серебра и меди СО2 является защитной средой. Для остальных металлов он является
окислительным газом.
Взаимодействие жидких металлов с сернистым газом
Жидкие металлы окисляются и растворяют серу или кислород и серу без образования оксидов.
Насыщение меди и серебра серой может привести при их кристаллизации к появлению в отливках газовой пористости.
Плавка остальных металлов (см. табл. 7.1) в присутствии сернистого газа приводит к загрязнению их оксидами и сульфидами.
Взаимодействие жидких металлов с метаном СН4
Взаимодействие жидких металлов с метаном СН4 в атмосфере пламенных печей происходит
в результате разложения его на углерод и водород. Атомарный водород активно растворяется в жидких металлах, а также может происходить насыщение сплавов углеродом (см. табл. 7.1).
7.3. Взаимодействие жидких металлов с материалами тиглей и футеровки плавильных печей
Взаимодействие с оксидными материалами: динасом SiO2, шамотом Al2O3·SiO2, магнезитом
MgO, корундом Al2O3, цирконом ZrO2 · SiO2, — проявляется, если в составе сплава
присутствуют элементы, имеющие большее сродство к кислороду, чем элемент, образующий оксид футеровки.
Например, магний взаимодействует с динасом по реакции
SiO2 + 2Mg = 2MgO + Si.
Оксид магния и кремний переходят в металл и загрязняют его. Поэтому чистый магний не плавят в печах с кислой футеровкой.
При плавке алюминия в печах с шамотной футеровкой из-за его взаимодействия с оксидом кремния происходит разрушение футеровки и загрязнение сплавов кремнием и оксидами алюминия.
При чисто механическом разрушении футеровки печей сплавы загрязняются материалом футеровки. При плавке сталей в индукционных печах происходит разъедание футеровки из-за интенсивного движения расплава.
Металлизация футеровки происходит при химическом взаимодействии расплава с
материалом футеровки или при условии смачивания, когда краевой угол ϑ < 90 ºС. В этом случае металл проникает в поры футеровки. Металлизированный слой футеровки разъедается расплавом. Происходит интенсивный износ футеровки и загрязнение металла.
Образование настылей. При соприкосновении оксидов, содержащихся в расплаве, с оксидом футеровки образуются соединения оксидов, которые спекаются в зоне высоких температур. Их называют настылями. Настыли часто образуются при плавке алюминиевых сплавов в печах с шамотной футеровкой.
Оксидно-графитовые материалы не смачиваются расплавом, но из-за выгорания углерода поверхностный слой тигля будет состоять из шамота. Их можно применять до температуры не выше 1400 ºС. Поэтому шамотно-графитные тигли применяют для плавки цинка, алюминия, меди, серебра, золота.
Карборундовые материалы (80 % SiC + 20 % связка из тугоплавких оксидов) применяют для плавки цветных металлов до меди включительно.
Стальные тигли применяют для плавки магния.
Чугунные тигли применяют для плавки алюминия. При этом необходима хорошая защита тигля от взаимодействия с алюминием, который активно растворяет железо. При некачественной окраске тиглей алюминиевые сплавы насыщаются железом.
Тугоплавкие металлы активно взаимодействуют с оксидами и графитом, поэтому для их плавки применяют медные водоохлаждаемые тигли — кристаллизаторы.
7.4. Контроль температуры жидкого металла и его качества
Контроль температуры жидкого металла производят пирометрами или термопарами погружения (табл. 7.2, 7.3).
Таблица 7.2