
692
.pdf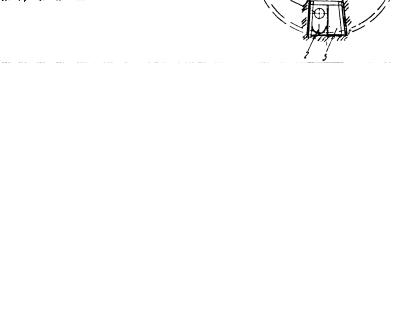
предназначенный для сбрасывания грунта, оснащать деревянным лотком, обшитым листовой сталью, другой — лестницей для прохода людей.
3.2.2. Примеры строительства эскалаторных тоннелей
Оригинальное техническое решение успешно осуществил коллектив СМУ № 6 Мосметростроя при сооружении наклонного тоннеля пересадочного узла между станциями «Марксистская» и «Таганская». Комплекс пересадочного узла состоит из натяжной камеры, наклонного хода и машинного помещения в пересадочном вестибюле.
Особую сложность представляла проходка наклонного хода в условиях сильной обводненности грунтов. Для ускорения проходки инженеры СМУ № 6 предложили соорудить опережающую восстающую штольню из натяжной камеры в нижней части сечения наклонного тоннеля. Штольня обеспечивала спуск грунта (разрабатываемого буровзрывным способом), который затем выдавали на поверхность по подходным выработкам через ствол шахты. Кроме того, опережающая штольня служила для дренирования воды из забоя наклонного хода (рис. 3.8).
Принятые способ проходки и схема транспортирования грунта позволили сократить время проходки эскалаторного тоннеля, приблизить сроки сдачи его под монтаж эскалаторов и начала работ по сооружению вестибюля станции. При строительстве пересадочного узла были совмещены по времени возведение внутритоннельных конструкций в натяжной камере, наклонном ходе и машинном помещении. Параллельно велись работы по возведению перекрытия наклонного хода и оснащению кабельного коллектора станции с работами по устройству водозащитного зонта наклонного хода.
Заслуживает внимания опыт строительства наклонного хода ст. «Исторический музей» Харьковского метрополитена при пересечении им водоносного горизонта. Для дренажа грунтовых вод и откатки грунта институт «Метрогипротранс» запроектировал проходку наклонного хода диаметром 9,5 м на базе опережающей штольни, которую сооружали в два этапа: снизу вверх до водоносного горизонта, а затем сверху вниз. На сопряжении с натяжной камерой трасса наклонного тоннеля пересекала подходную выработку, с использованием которой осуществляли проходку левого станционного тоннеля. Передовая штольня должна была выйти в эту выработку, что препятствовало ведению работ в левом тоннеле и заставило искать иное решение. При этом на момент начала проходки на поверхности уже соорудили часть вестибюля.
Рис. 3.8. Проходка наклонного хода на ст. «Марксистская» с помощью восстающей штольни:
1 — опережающая восстающая штольня; 2 — стальной лист; 3 — тюбингоукладчик; 4 — вентиляционная труба; 5 — людской ходок; 6 — натяжная камера; 7 — передвижной контейнер
Специалисты СМУ № 751 предложили вести проходку на полное сечение сверху вниз, предварительно пробурив дренажные скважины. Для задания оси эскалаторного тоннеля на расстрелах крепления котлована вестибюля оборудовали маркшейдерский столик с теодолитом, снабженным лазерной насадкой, что позволило обойтись без установки направляющих под прорезные кольца.
После монтажа девяти полуколец оголовника эскалаторного тоннеля на них смонтировали буровую установку для наклонного бурения. В лотковой части тоннеля пробурили три дренажные скважины диаметром 219 мм с выходом в подходную выработку, в пределах водоносного горизонта трубы оборудовали фильтрами.
Средняя скважина, пробуренная точно по оси, вышла в подходную выработку с небольшими отклонениями (30 мм в плане и 40 мм в профиле), что облегчило маркшейдерский контроль сооружения наклонного тоннеля. После монтажа укладчика контроль колец за ним вели от луча лазера, забойных колец — от смещенной оси. Ось в забой передавали сканированием луча по вертикали. По окончании проходки укладку бетона опор и монтаж плит перекрытия осуществляли также по лазерному лучу.
При строительстве эскалаторного тоннеля ст. «Дубровка» Люблинской линии бурение вертикальных замораживающих скважин и проходка участка временных колец до «стены в грунте», ограждающей конструкции вестибюля, осуществляли одновременно. Средством для разработки и погрузки грунта на скребковый конвейер служил шахтный манипулятор «Штрек-5» [9, ч. 2, п. 3.7] с навесным оборудованием (ковшовым погрузчиком). Для погрузки грунта в автосамосвалы установили перегружатели — передвижной скребковый ПТК-1 и ленточный прицепной от горно-проходческого комбайна ГПКС: первый — в наклонном ходе под углом 30°, второй — на поверхности стройплощадки (на эстакаде) горизонтально. Монтаж тюбинговой обделки временных колец производили лебедками.
Работы вела одна комплексная бригада в составе 8–10 человек, как правило, в одну, иногда — в две смены. С помощью технологической цепочки «Штрек-5» — ПТК-1 — ленточный перегружатель ГПКС был пройден участок и смонтированы 18 временных полуколец и 7 временных колец эскалаторного тоннеля диаметром 9,5 м. Затем работы были остановлены до завершения процесса замораживания первого контура. Применение данной технологии значительно сократило долю ручного труда и время на погрузку и транспортировку грунта; уменьшило затраты на сооружение тоннеля в результате исключения строительства материальной эстакады и подъемной машины.
Осуществление конструктивной доработки манипулятора «Штрек-5» позволило расширить область его применения и использовать для монтажа обделки. С целью уменьшения трудовых и материальных затрат при производстве работ по креплению лба забоя специалистами СМУ № 7 внедрена технология нанесения набрызг-бетона с помощью машины БМ-67. При применении вышеупомянутой технологии для обеспечения технологической цепочки достаточной является численность звена проходчиков в 5–6 человек.
Заслуживает внимания опыт строительства эскалаторного тоннеля на ст. «Петровско-Разумовская» Тимирязевской линии Московского метрополитена, где впервые был применен проходческий комплекс КП-9,5 (рис. 3.9) с укладчиком тоннельной обделки.
Ножевая часть комплекса снабжена механизмами подъема-опускания; с помощью специальных роликов ее можно сдвигать влево или вправо. Это дает возможность разрабатывать грунт на полное сечение. Обделка монтируется укладчиком, оборудованным грейферным погрузчиком, который прикреплен к раме укладчика. Процесс разработки грунта практически полностью механизирован. Комплекс обслуживает бригада из 6 человек. Даже в процессе его освоения, при проведении дополнительных работ по усилению отдельных узлов, обеспечивались хорошие скоростные показатели проходки.
Определенный интерес представляет технология проходки эскалаторных тоннелей диаметром 10,1 м сплошным забоем, реализованная при строительстве Киевского метрополитена. Она заключается в применении 6-ярусной балочной временной крепи и постоянной сборной железобетонной обделки с резиновым уплотнением (рис. 3.10).
Такая обделка применена для крепления нижнего эскалаторного тоннеля ст. «Печерская» длиной 120 м, эскалаторного тоннеля ст. «Дорогожичи» 124,5 м и проемной части трехсводчатой станции длиной 48 м. Стоимость сооружения эскалаторного тоннеля в сборной железобетонной обделке с резиновым уплотнением стыков снижается в 2,14 раза по сравнению с чугунной тюбинговой обделкой.
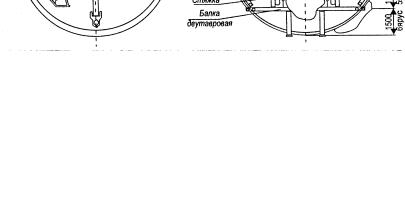
Рис. 3.10. Технологическая схема проходки наклонного хода с использованием сборной железобетонной обделки с резиновым уплотнением
Применение разработанной технологии позволило осуществить быстрый ввод станционных выработок в общестроительные и отделочные процессы при высоком уровне организации труда и безопасности работ.
Практика показывает, что до настоящего времени большинство эскалаторных тоннелей в нашей стране сооружалось с применением закрепления грунтов методом рассольного замораживания. Сущность способа заключается в том, что до вскрытия выработкой неустойчивых, водоносных грунтов их предварительно замораживают, благодаря чему вокруг выработки создается сплошное ледогрунтовое ограждение (ЛГО). Ограждение принимает на себя горное и гидростатическое давление, защищает выработку от затопления, создавая условия для ее проходки по обычной технологии. Разработка грунта ведется отбойными молотками, монтаж обделки — тюбингоукладчиком.
В качестве обделки, как правило, используется сборная обделка круглого очертания из чугунных тюбингов.
Несмотря на определенные достоинства (относительно небольшая стоимость, малая материалоемкость, малый объем подготовительных работ, надежные и простые способы контроля), указанный способ имеет ряд существенных недостатков:
—бурение наклонных скважин длиной более 100 м выполняется обычным станком с использованием буровых штанг. Такой буровой снаряд имеет большую гибкость и при бурении в слабых, неустойчивых грунтах с наличием валунов, в ряде случаев происходит значительный уход скважины от теоретического места размещения. При этом отсутствовал надежный способ определения местоположения скважин. Все это приводит к дополнительному бурению, а это, в свою очередь, вызывает перемораживание грунта в значительно большем объеме, чем это необходимо для работы;
—измерения температур выполнялись гирляндой спиртовых термометров раз в три
дня. Для снятия температур требуется извлечение термометров на поверхность, что не позволяет с достаточной точностью получить реальные температуры грунтов в каждой точке (в процессе извлечения термометров эти данные усредняются);
— режим пассивного замораживания практически не отличается от активного, так как нет возможности плавно регулировать холодопроизводительность машин в соответствии с изменением температур грунта в каждой точке. Это, в конечном счете, также приводит к ненужному наращиванию ледогрунтового массива.
Описанные выше недостатки приводят к сверхпроектному увеличению объема замороженного грунта более чем в два раза. Процесс замораживания вызывает пучение грунта, которое приводит к подъему поверхности в процессе активного замораживания. Параллельно с этим происходит процесс консолидации влаги в замораживаемом грунте, что увеличивает пористость грунта и, при оттаивании, происходят его осадки, значительно превышающие подъем поверхности в процессе активного режима.
В связи с тем, что чугунные тюбинги изолируются жесткой чеканкой, в процессе растепления ледогрунтового массива (которое продолжается много месяцев), происходят значительные деформации обделки и нарушение чеканки. Это вызывает течи в обделке, устранить которые в процессе эксплуатации наклонного хода очень сложно.
Наряду с указанными недостатками, все применявшиеся до настоящего времени способы
строительства эскалаторных тоннелей негативно влияли на окружающую застройку и требовали значительного объема расселения и сноса зданий, попадающих в зону строительства, что зачастую бывает весьма сложно выполнить, особенно при строительстве метро в старой части города в условиях плотной застройки монументальными зданиями и сооружениями.
Так, анализ возможных последствий строительства эскалаторного тоннеля ст. «Адмиралтейская» в Санкт-Петербурге (см. п. 1.3) не позволил завершить строительство станции вместе со строительством всей линии. Была построена только нижняя часть станции, и в настоящее время станция эксплуатируется на проход.
Однако в последнее время в мировой практике появился ряд новых технологий, с помощью которых можно попытаться минимизировать негативное влияние строительства наклонного хода на окружающую застройку, и выполнить достройку ст. «Адмиралтейская». К таким технологиям относятся: направленное бурение, струйная цементация, использование проходческих машин с грунто- и гидропригрузом, замораживание с применением холодильного оборудования с автоматически изменяемыми параметрами и оперативным мониторингом.
Специалистами «Ленметрогипротранса» разработаны новые альтернативные варианты сооружения эскалаторного тоннеля на ст. «Адмиралтейская».
В а р и а н т 1 практически повторяет положения существующей технологии сооружения наклонного хода с применением способа замораживания, однако в него внесены принципиальные изменения, позволяющие резко (в 1,5–2 раза) сократить вредное воздействие строительства на окружающую среду:
1.Бурение замораживающих скважин предлагается выполнять субгоризонтальной буровой установкой типа HD2035_DR с элементами направленного бурения с точностью до 30 см. В результате такого бурения может быть получен контур замораживающих скважин, практически равный расчетному по всей длине замораживания, что позволит довести толщину замораживания до минимальной.
2.Для контроля температур предлагается использовать современную систему термометрического контроля, состоящую из центрального и дополнительных блоков управления, которые способны контролировать до 96 датчиков температур. Датчики смонтированы на проектных отметках в термометрических колонках и фиксируют температуру грунта с заданной дискретностью.
Система многоточечного термометрического контроля с удобным интерфейсом дает возможность получать практически объемную картину состояния ЛГО и оперативно вносить корректировки в технологический режим замораживания. Регулировка режимов работы холодильного оборудования и системы разводки холодоносителя по колонкам, позволит формировать ледогрунтовые цилиндры проектных размеров, не допуская перемораживания грунтового массива.
3.Для реализации технологического процесса рассольного замораживания грунтов предлагается использовать холодильное оборудование на основе винтовых компрессоров фирмы «Bitzer». Такая холодильная машина позволяет осуществлять плавное регулирование холодопроизводительности в зависимости от тепловой нагрузки в пределах 0–100 %. Воздушный конденсатор, укомплектованный приборами автоматики, позволяет поддерживать постоянным давление конденсации и работать при температуре наружного воздуха до –40 °С.
Для замораживания грунтов эскалаторного тоннеля ст. «Адмиралтейская» необходимо не менее четырех холодильных машин на основе винтовых компрессоров фирмы «Bitzer»
с холодопроизводительностью 119 кВт каждая. |
|
|
||
Поставка, монтаж, |
наладка |
и гарантийное сервисное |
обслуживание |
данного |
холодильного оборудования осуществляется специалистами Санкт-Петербурга. |
|
|||
4. Применение технологии |
зонального замораживания |
позволяет |
разбить |
технологический процесс замораживания грунтов эскалаторного тоннеля на два примерно равных этапа (по 55 м каждый). На первом этапе производится процесс зонального рассольного замораживания от дневной поверхности до 1-го водоупора геологического
слоя морены (суглинки мягко-тугоплас-тичной и полутвердой консистенции). В процессе проходки замороженного участка выработки, производится второй этап зонального замораживания — от морены до второго водоупора — глины тонкослоистой твердой консистенции. Предлагаемая технология позволяет отключить замораживание от уже построенных участков наклонного хода, оптимизировать проходку и работу холодильного оборудования, минимизировать возможные деформационные явления на дневной поверхности.
Кроме того, оборудовав замораживающие установки нагревателями, можно выполнить искусственное растепление грунта, что позволит резко уменьшить продолжительность послестроительных осадок и их величину. При этом следует растепление от центра скважины к ее периферии с немедленным заполнением растепленного пространства.
Все вышеописанные мероприятия позволят сократить объем замороженного (перемороженного) грунта в 1,5–2 раза, уменьшив при этом осадки дневной поверхности.
Вкачестве обделки для указанного варианта предлагается использовать высокоточную чугунную обделку из тюбингов с дополнительным резиновым уплотнением по периметру, что позволит резко сократить воздействие послеосадочных деформаций на обделку в части ее герметичности.
Ва р и а н т 2 предусматривает сооружение эскалаторного тоннеля с креплением грунтов струйной цементацией.
На сегодняшний день струйное закрепление грунтов широко применяется на объектах с глубиной цементации вертикальными скважинами до 25–30 м. Более глубоко цементацию трудно сделать из-за большого сопротивления изливу отработанного шлама по затрубному пространству. По тем же причинам еще более трудно сделать струйную цементацию в наклонных скважинах глубиной более 100 м. Кроме того, на это накладываются ограничения, вызванные точностью бурения.
Настоящее решение предполагает использовать буровой станок, описанный в варианте 1, для выполнения цементационных работ. Для излива отработанного шлама предлагается использовать двойной буровой инструмент, состоящий из буровой трубы и буровой штанги с монитором.
Закрепление грунтов выполняется следующим образом: первоначально бурится контрольная скважина в центре ствола и производится ее позиционирование. Двойным буровым инструментом (труба и штанга с шарошкой), методом направленного бурения производится бурение цементационной скважины. По достижению проектной отметки шарошка извлекается, на ее место устанавливается монитор, который опускается на 1–15
мниже уровня буровой трубы.
Вмонитор подается цементный раствор с необходимыми добавками под давлением 300–400 бар. Начинается извлечение бурового инструмента одновременно с поднятием вращающегося монитора. При этом сопла монитора должны отставать от обреза буровой трубы не менее чем на 1,5 м. Излив отработанного раствора осуществляется по буровой трубе до устья скважины и далее в специальный отстойник. После извлечения инструмента на поверхность станок переставляется на новую точку и процесс повторяется.
Таким образом, вокруг наклонного хода образуется «система» толщиной около 3 м, состоящая из четырех рядов пересекающихся «кругов» из материала, представляющего собой смесь цемента и вмещающего грунта, имеющая достаточно высокие прочностные и противофильтрационные свойства.
Однако на сегодняшний день нет возможности гарантированно определить качество полученной завесы. В ней могут образоваться участки с нарушенной сплошностью, что может привести к серьезным последствиям при проходке. Для исключения такой возможности предлагается после выполнения цементации и набора грунтоцементным массивом необходимой прочности выполнить контурное замораживание внутри грунтоцементного камня (аналогичное варианту 1), что обеспечит гарантированную водонепроницаемость закрепленного контура. При этом, так как замораживание будет проводиться только внутри цементного камня, практически исключаются такие побочные эффекты замораживания, как пучение грунта и послестроительные
осадки.
Для указанного варианта проходку наклонного хода предлагается выполнить во временной крепи, состоящей из стальных рам и «чернового» бетона. После проходки наклонного хода выполняется изоляция тоннеля полиэтиленом, после чего снизу вверх, с применением скользящей опалубки, бетонируется монолитная железобетонная обделка.
При этом, с незначительным увеличением стоимости изоляции, она может быть выполнена в ремонтно-пригодном исполнении, что позволит ликвидировать течи, вызванные некачественным выполнением работ по изоляции.
В а р и а н т 3 предусматривает сооружение эскалаторного тоннеля с применением ТВМ.
В указанном варианте проходку эскалаторного тоннеля предполагается выполнить механизированным щитовым комплексом (ТВМ) с гидравлическим или грунтовым пригрузом забоя, способным вести проходку в различных инженерно-геологических условиях от пылеватых песков до полускальных и скальных грунтов при гидростатическом давлении до 5,5 бар.
Машина с грунтовым пригрузом забоя представляет собой комплекс с системой грунтопригруза, способной поддерживать забой, уравновешивая давление грунта и воды, а также воздействовать на грунт посредством нагнетания химических реагентов.
Удаление разработанной породы осуществляется шнековым конвейером, расположенным в нижней части камеры породоразрушающего органа. Шнековый конвейер сопряжен с рассчитанным на высокую плотность породопогрузочным насосом, который через линию подачи перекачивает породу от выхода шнека к стволу шахты, либо перегружает породу в специальные емкости.
Крепление тоннеля выполняется блочной железобетонной обделкой, из водонепроницаемого бетона с резиновым уплотнением стыков. Кольцевое пространство за бетонными блоками вслед за проходкой заполняется специальным водонепроницаемым раствором, производимым на строительной площадке.
Щит с гидропригрузом отличается от описанного тем, что разработанная порода измельчается режущим органом, перемешивается с бентонитовым раствором, подающимся под давлением в забой, и далее выдается по трубопроводам, непрерывно наращивающимся вслед за проходкой щита, на поверхность в установку для регенерации раствора. Извлеченный из раствора грунт автотранспортом отвозится в отвал, а регенерированный раствор доводится до необходимой консистенции и подается обратно в забой.
Несмотря на то, что до настоящего времени аналогов проходки наклонных тоннелей такого диаметра с применением ТВМ не существует, ряд известных мировых фирм предложили свое участие в создании подобной машины, которая должна отвечать всем необходимым требованиям.
Для монтажа ТВМ потребуется стартовый котлован глубиной около 13 м. Его сооружение предлагается выполнить двухэтапно: сначала соорудить котлован для вестибюля глубиной около 5 м, а затем, внутри котлована, соорудить стартовую камеру. Крепление стен котлована предлагается выполнить ограждающей «стеной в грунте» (для мелкого котлована глубиной 12–15 м, для глубокого — около 30 м).
Так как для старта ТВМ требуется перекрытие кровли над щитом более 4–5 м, а также возможность герметизации задней части оболочки, предлагается осуществить проходку начального участка тоннеля закрытым способом, для чего выполнить укрепление грунтов с поверхности вперед по трассе тоннеля на необходимую длину методом струйной цементации. Крепление начального участка выполняется стальными рамами с черновым бетоном. Внутренний диаметр начального участка должен превышать внешний диаметр ТВМ.
По завершении строительства стартовой камеры и начального участка тоннеля производится монтаж ТВМ и ввод его в начальный участок тоннеля. Монтируются первые два кольца железобетонной обделки, сооружается упорная рама и начинается проходка эскалаторов тоннеля. После завершения проходки ТВМ демонтируется с выдачей узлов на поверхность по построенному тоннелю. При этом внешняя часть оболочки щита не демонтируется, так как

отсутствует возможность строительства демонтажной камеры из за малого перекрытия тоннеля устойчивыми грунтами. После демонтажа ТВМ оболочка бетонируется. Перечень основного строительного оборудования по вариантам и их сравнительные характеристики приведены в табл. 3.4 и табл. 3.5.
Из данных табл. 3.5 следует, что наиболее конкурентоспособным, позволяющим выполнить работы в минимальные сроки, является вариант с рассольным замораживанием (вариант 1). Единственным и основным недостатком этого варианта являются значительные осадки дневной поверхности (200–250 мм), однако при применении современных средств усиления и инъекционного компенсационного уплотнения грунтов под фундаментами зданий, последствия от осадок могут быть сведены к минимальным.
Таблица 3.4
Перечень основного строительного оборудования
№ |
Наименование |
Стоимо |
|
Кол-во |
|
Примечание |
|
п/п |
сть, |
|
|
|
|||
оборудования |
|
|
|
|
|||
|
млн р.* |
Вар. 1 |
Вар. 2 |
Вар. 3 |
|
||
|
|
|
|
|
|
|
|
|
Субгоризонтальная |
|
|
|
|
|
|
1 |
буровая установка |
17,0 |
1 |
2 |
— |
|
|
|
HD2035_DR |
|
|
|
|
|
|
|
|
|
|
|
|
|
|
2 |
Буровой инструмент для |
4,5 |
|
Компл. |
— |
|
|
|
струйной цементации |
|
|
|
|
|
|
3 |
Система управления |
8,5 |
1 |
2 |
— |
|
|
|
бурением |
|
|
|
|
|
|
4 |
Система Maxibohr |
4,9 |
1 |
1 |
— |
|
|
|
|
|
|
|
|
|
|
|
Комплектная |
|
|
|
|
Производитс |
|
5 |
замораживающая станция |
2,72 |
4 |
4 |
— |
||
я в СПб. |
|||||||
|
с системой мониторинга |
|
|
|
|
||
|
|
|
|
|
|
||
|
|
|
|
|
|
|
|
|
Комплектный ТВМ с ос- |
|
|
|
|
|
|
6 |
насткой для |
600 |
— |
— |
Компл. |
|
|
|
производства обделки |
|
|
|
|
|
|
|
|
|
|
|
|
|
|
|
Установка для |
|
|
|
|
Имеется в |
|
7 |
сооружения стены в |
— |
— |
— |
1 |
||
Метрострое |
|||||||
|
грунте |
|
|
|
|
||
|
|
|
|
|
|
||
|
|
|
|
|
|
|
|
|
Буровая установка |
|
|
|
|
Имеется в |
|
8 |
С-6 для вертикальной |
— |
— |
— |
1 |
||
Метрострое |
|||||||
|
струйной цементации |
|
|
|
|
||
|
|
|
|
|
|
||
|
|
|
|
|
|
|
|
9 |
Комплект оборудования |
— |
— |
1 |
1 |
Имеется в |
|
для струйной цементации |
Метрострое |
П р и м е ч а н и е. Цены даны без учета НДС и таможенных налогов.
Вариант 2 практически исключает как осадки дневной поверхности, так и послестроительные осадки конструкций эскалаторного тоннеля. Однако к недостаткам указанного варианта следует отнести значительно больший (по сравнению с первым вариантом) срок выполнения работ, для снижения которого потребуется применение двух комплектов бурового оборудования, что увеличит стоимость строительства.
Таблица 3.5
Сравнительные характеристики вариантов строительства
№ |
|
Показатель |
Ед. |
Вар. 1 |
Вар. 2 |
Вар. 3 |
п/п |
|
изм. |
||||
|
|
|
|
|
|
|
1 |
Стоимость |
строительства (без учета |
млн р. |
|
|
|
стоимости приобретения оборудования) |
|
|
|
|||
2 |
Срок строительства |
мес. |
|
|
|
|
|
|
|
|
|
|
|
|
Стоимость |
приобретения |
|
|
|
|
3 |
оборудования (без НДС и таможенных |
млн р. |
45,8 |
71,3 |
600 |
|
|
налогов) |
|
|
|
|
|
4 |
Установленная мощность |
кВт ч |
1100 |
1100 |
4500 |
|
5 |
Потребление воды |
м3/ч |
1 |
10 |
24 |
Вариант 3 также практически исключает осадки дневной поверхности, при этом активная фаза строительства (проходка самого эскалаторного тоннеля) сокращается в несколько раз. Однако этот вариант требует сложных и долгосрочных подготовительных работ (строительство стартового
котлована, проходка стартовой камеры, укрепление грунтов вперед и по трассе). Кроме того, требуется обеспечить проходку необходимыми ресурсами (вода, электроэнергия, канализование), что выполнить в условиях старого города в необходимых для проходки ТВМ объемах крайне трудно. По стоимости указанный вариант самый дорогой, при этом стоимость закупки необходимого для его осуществления оборудования во много раз отличается от других рассматриваемых вариантов.
3.2.3. Сооружение эскалаторных тоннелей способом «горизонтального забоя»
На протяжении всей истории строительства эскалаторных тоннелей конструктивнотехнологические решения варьировались весьма слабо. Разработка и погрузка грунта при производстве работ, хотя и совмещены по времени, однако в основном выполнялись вручную. Темпы сооружения эскалаторных тоннелей в среднем составляют 6,9 м/мес., что в 2,5 раза ниже аналогичного показателя для станционных тоннелей. Временное крепление лба и кровли забоя также выполняется вручную и требует повышения уровня механизации.
Возведение постоянной обделки, хотя и механизировано, требует дополнительных слабомеханизированных работ по сболчиванию, переболчиванию и чеканке швов. В то же время такой прогрессивный вид крепи, как набрызг-бетонная или комбинированная, на ее основе практически не применяется, за исключением случаев крепления лба забоя. И это несмотря на то, что наивысший теоретически достижимый уровень механизации при использовании набрызгбетонных крепей составляет 0,95, арочно-набрызг-бетонных — 0,77, а монолитных бетонных — 0,71.
На основе анализа существующих технологических схем, В.П. Ефремов, автор одноименной статьи, опубликованной в журнале «Метро и тоннели» (№ 3 за 2002 г. С. 39–41), приходит к следующим выводам:
1.Наиболее рациональной и перспективной в широком спектре инженерно-геологических условий является схема с двухслойной обделкой — первичная крепь набрызг-бетонная (арочно- набрызг-бетонная), постоянная обделка из монолитного бетона (железобетона). Такая схема позволит обеспечить наивысший уровень механизации.
2.Наклонное положение тоннеля и забоя выработки существенно снижает производительность труда проходчиков и затрудняет применение высокопроизводительной серийной горно-про- ходческой техники. Поиск новых технологических приемов, исключающих указанные затруднения, поможет существенно повысить скорости проходки наклонных тоннелей и снизить затраты на их сооружение.
Исходными предпосылками для разработки альтернативных вариантов конструктивнотехнологической схемы проходки наклонного тоннеля, по мнению автора, являются следующие: сооружение эскалаторного тоннеля горизонтальным забоем для устранения наклонного положения рабочих механизмов; применение комплекса оборудования, включающего тоннелепроходческий экскаватор с полноповоротной стрелой или агрегат на его основе с рабочим органом избирательного действия и крепеустановщик; использование конструкций с набрызгбетонными временным и монолитными постоянными обделками; применение механизмов непрерывного действия для транспортирования разработанного грунта.
При этом были рассмотрены следующие варианты технологических схем проходки эскалаторных тоннелей.
В а р и а н т 1. Сооружение эскалаторных тоннелей в слабых грунтах крепостью f < 1. Временная крепь эскалаторного тоннеля состоит из решетчатых металлических арок кругового очертания, опережающей крепи из арматурных стержней и набрызг-бетона (рис. 3.11).
Решетчатое кольцо включает 11 элементов, каждый из которых, в свою очередь, состоит из четырех криволинейных арматурных стержней, соединенных в пространственные каркасы арматурной решеткой, — сечение элементов конструкции арки принимается по расчету.
Решетчатые металлические кольца устанавливают поэтапно с расчетным шагом в плоскости, перпендикулярной продольной оси тоннеля. Его сечение круговое, что позволяет унифицировать элементы арки как равные части кольца. Элементы различаются лишь конструкцией узлов соединения. Шаг арок определяется их несущей способностью и несущей способностью стержней забивной опережающей крепи между арками. Узлы соединения элементов арки представляют собой прямоугольные фланцы для сборки на болтах. Узлы соединения проектируют равнопрочными сечениям элементов. В продольном направлении кольца временного крепления соединяют элементами из стали углового или швеллерного профиля для объединения колец в совместную работу и повышения продольной жесткости крепи.
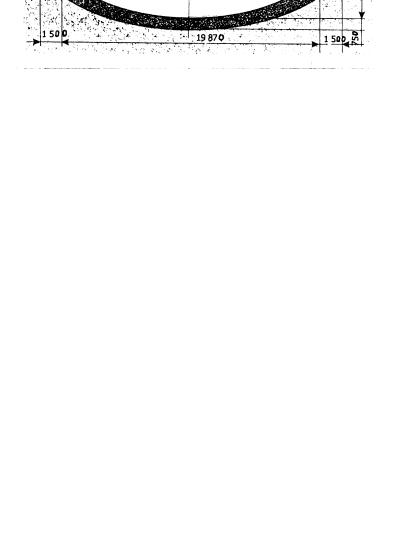
Проходку тоннеля предполагается выполнять по следующей технологической схеме. Разработка и погрузка грунта в горизонтальном забое ведется серийным экскаватором,
модернизированным для подземных работ. Производительность экскаватора назначают по известным техническим характеристикам указанного типа (зона действия, вылет стрелы в горизонтальной и вертикальной плоскостях и т.п.), а также исходя из необходимости размещения в забое других проходческих механизмов и обустройств. По этим параметрам устанавливают марку нужного экскаватора и его эксплуатационную производительность.
а)
б)
Рис. 3.11. Крепление наклонного тоннеля при проходке:
а — временная крепь из решетчатых металлических арок с набрызг-бетоном и монолитным бетонным лотком (вариант 1); б — первичная крепь
из монолитного бетона (вариант 2)
Транспортировка грунта из забоя осуществляется конвейером. Увязка производительности
экскаватора и конвейера производится по формуле |
|
Пк = КрφПэ , |
(3.1) |
где Пк — требуемая эксплуатационная производительность конвейера, м3/с; Кр — коэффициент
разрыхления грунта; φ — коэффициент неравномерности погрузки; Пэ — эксплуатационная производительность экскаватора.
Временное крепление сооружаемого тоннеля принимают арочно-набрызг-бетонным. На этапе I при проходке верхней калотты монтируют три верхних элемента Б-1-1, Б-1, Б-1-1, составляющих арку с центральным углом около 77°. При этом элементы Б-1-1 с каждой стороны имеют специальные дополнительные для опоры на грунт (КР1), направленные тангенциально. Эти опоры служат для обеспечения несущей способности временной крепи при перекреплении элементов кольца на этапе II и в целом для устойчивости верхней сводовой части выработки.
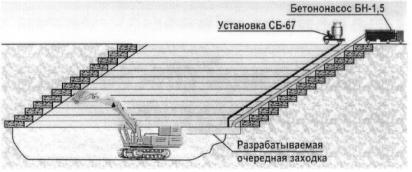
На этапе II при проходке нижней калотты устанавливают еще два элемента Б-1-1. Непосредственно после монтажа элементов арок каждого этапа производят: устройство опережающей крепи из арматурных стержней (шаг стержней определяют расчетом их на прочность как балок на двух опорах); установку арматурных сеток и нанесение набрызг-бетона расчетного класса прочности.
На этапе III при проходке штроссы монтируют нижние элементы арки Б-1-1 и Б-1-2 и, после нанесения набрызг-бетона на сетку, кольцо из 11 элементов замыкают сооружаемым на этом этапе бетонным лотком постоянной обделки.
Возведение постоянной обделки из монолитного бетона с элементами внутритоннельных обустройств (банкетки для опирания плит перекрытия, по которым устраивают фундаменты под эскалаторы) осуществляют после проходки тоннеля во временной крепи на всю длину.
На этапе IV производят бетонирование постоянной обделки в обратном порядке (снизу вверх). Передвижение механизированной опалубки производят по монолитному лотку, сооруженному на этапе III. Внутренний диаметр обделки принимают из условия размещения оборудования эскалаторного комплекса, а толщину рассчитывают в зависимости от нагрузки.
Приведенную технологию характеризуют следующие расчетные показатели, полученные после составления циклограмм проходческих процессов: скорость возведения тоннеля и арочно- набрызг-бетонной временной крепи 45 м/мес.; скорость сооружения постоянной бетонной обделки 60 м/мес.; средняя скорость сооружения готового эскалаторного тоннеля 25,9 м/мес.; трудозатраты на 1 м готового тоннеля 81,6 чел.-ч.
Расчетная средняя скорость сооружения тоннеля по предложенной технологии получилась ниже, чем по традиционной технологии, однако по показателям приведенных затрат, уровню технологии (трудозатратам) существенно ее превосходит.
В а р и а н т 2. Первичная крепь из набрызг-бетона без арматуры, сооружаемая сразу же вслед за разработкой грунта. В горизонтальном сечении крепь представляет собой эллипс, в продольном разрезе — ступенчатая конструкция с высотой ступени, равной заходке (величина заходки должна определяться индивидуально в каждом случае). При высоте вертикальной заходки 0,5 м обеспечивается в нормальном к оси тоннеля сечении средняя толщина временной крепи 0,75 м. Постоянную обделку из монолитного бетона расчетного класса прочности сооружают с применением механизированной опалубки после проходки тоннеля на всю длину (как в варианте 1).
Технологическая схема предусматривает выполнение работ в следующем порядке (рис. 3.12).
Рис. 3.12. Устройство временного крепления эскалаторного тоннеля по варианту 2
1.Разработка и погрузка грунта в горизонтальном забое тоннелепроходческим экскаватором с полноповоротной стрелой, при помощи которой должны нарезаться в грунте щели-заходки в горизонтальной плоскости и отрабатываться по всей плоскости забоя.
2.Временное крепление из набрызг-бетона заполнением горизонтальных прорезей (щелейзаходок) по контуру тоннеля одновременно с их нарезкой.
3.Транспортирование грунта конвейером.
4.Устройство постоянной обделки из монолитного бетона с элементами внутритоннельных обустройств после проходки тоннеля во временной крепи на всю длину.
Состав комплекса оборудования для технологических вариантов 1 и 2 приведен в табл. 3.6.
Таблица 3.6