
669
.pdfТаблица 2.1
Статистические характеристики одиночного изъятия термоупрочненных рельсов типа Р65 за 2006 г.
|
Значения характеристик для изъятых рельсов по дефектам |
|
|||||
Характеристики |
|
|
(звеньевой/бесстыковой путь) |
|
|
|
|
11, 21, 30Г |
52.1, 53.1 |
26.3, 46.3, 56.3, 66.3, 86.3 |
10 |
17 |
|
в |
|
|
|
||||||
|
|
среднем |
|||||
|
|
|
|
|
|
|
|
НТМК |
|
|
|
|
|
|
|
Тср, млн т бр. |
553/649 |
543/574 |
467/525 |
499/652 |
627/607 |
|
558/629 |
σТ, млн т бр. |
258/275 |
237/301 |
221/315 |
286/258 |
269/227 |
|
265/270 |
ν, % |
37,7/43,7 |
5,4/5,3 |
1,1/5,4 |
16,2/11,7 |
19,5/11,9 |
|
79,9/78,0 |
НКМК |
|
|
|
|
|
|
|
Тср, млн т бр. |
534/486 |
503/445 |
451/425 |
500/433 |
494/414 |
|
510/455 |
σТ, млн т бр. |
268/208 |
270/246 |
269/217 |
265/238 |
267/221 |
|
253/218 |
ν, % |
27,4/34,3 |
3,1/7,0 |
1,7/15,9 |
15,9/8,1 |
21,7/7,4 |
|
69,8/72,7 |
Примечание: Тср — средний тоннаж одиночного изъятия рельсов; σТ — среднее квадратическое отклонение тоннажа; ν — число рельсов в общем количестве изъятых, %.
На основе данных об изъятии рельсов за 1996–2006 гг. определили Тср в звеньевом и бесстыковом пути по всем одиночным отказам. Результаты показаны на рис. 2.3. Стабильное возрастание Тср за эти годы, пожалуй, главный положительный итог большой работы специалистов, направленной на повышение надежности рельсов. Если в ближайшие годы удастся заметно уменьшить коэффициент вариации VТ в первую очередь за счет снижения доли отказов на ранней стадии эксплуатации, то это и еще большей степени увеличит Тср и в целом улучшит надежность рельсов.
Существуют «Условия гарантии качества новых железнодорожных рельсов и порядок замены рельсов, не выдержавших сроков гарантий», введенные в действие с 01.09.04 г. Согласно этому документу, если в рельсах появились дефекты 10, 17, 20, 21, 30В, 30Г, 50, 52, 53, 60, 70, 79 до достижения гарантийной наработки тоннажа В зависимости от качественной категории рельсов по ГОСТ Р 51685–2000 [37] и плана пути при соблюдении потребителем условии эксплуатации, то предприятие-изготовитель должно возместить ущерб от преждевременного отказа.
Норма гарантийной наработки рельсов наиболее массовой категории Т1 составляет 240 млн т бр. на прямых и в кривых радиусом более 1000 м, 150 — при 650 < R < 1000 м и 120 — при R < 650 м. Результат обработки материалов форм ПУ-4 за 2006 г. позволяют в среднем оценить выход рельсов из строя на ранней стадии их работы и сравнить фактические отказы до гарантийной наработки с числом принятых (или хотя бы предъявленных меткомбинатам) претензий.
43
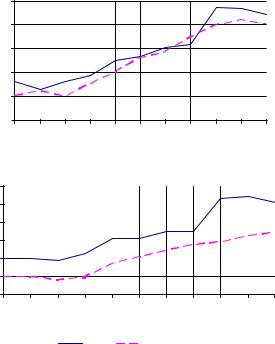
а)
|
|
600 |
|
|
|
|
|
|
|
|
|
|
|
|
|
|
|
500 |
|
|
|
|
|
|
|
|
|
|
|
|
|
|
т |
400 |
|
|
|
|
|
|
|
|
|
|
|
|
|
|
млн |
300 |
|
|
|
|
|
|
|
|
|
|
|
|
|
|
Т ñð, |
|
|
|
|
|
|
|
|
|
|
|
|
|
|
|
200 |
|
|
|
|
|
|
|
|
|
|
|
|
|
|
|
|
|
|
|
|
|
|
|
|
|
|
|
|
|
|
|
|
100 |
|
|
|
|
|
|
|
|
|
|
|
|
|
|
|
1996 |
1997 |
1998 |
1999 |
2000 |
2001 |
2002 |
2003 |
2004 |
2005 |
2006 |
|||
|
|
|
|
|
|
|
|
|
Годы |
|
|
|
|
|
|
б) |
|
|
|
|
|
|
|
|
|
|
|
|
|
|
|
|
700 |
|
|
|
|
|
|
|
|
|
|
|
|
|
|
|
600 |
|
|
|
|
|
|
|
|
|
|
|
|
|
|
т |
500 |
|
|
|
|
|
|
|
|
|
|
|
|
|
|
300 |
|
|
|
|
|
|
|
|
|
|
|
|
|
||
млнñð, |
|
|
|
|
|
|
|
|
|
|
|
|
|
||
|
400 |
|
|
|
|
|
|
|
|
|
|
|
|
|
|
Т |
200 |
|
|
|
|
|
|
|
|
|
|
|
|
|
|
|
|
|
|
|
|
|
|
|
|
|
|
|
|
||
|
100 |
|
|
|
|
|
|
|
|
|
|
|
|
|
|
|
|
1996 |
1997 |
1998 |
1999 |
2000 |
2001 |
2002 |
2003 |
2004 |
2005 |
2006 |
|||
|
|
|
|
|
|
|
|
|
Годы |
|
|
|
|
|
|
|
|
|
|
|
|
|
НТМК |
НКМК |
|
|
|
|
|
||
|
Рис. 2.3. Средний тоннаж одиночных отказов термоупрочненных |
||||||||||||||
|
|
|
рельсов типа Р65 в бесстыковом пути в 2006 г. |
|
|
Результаты соответствующего анализа представлены в табл. 2.1. Он сделан на основе сведений, полученных в 2006 г. с 23955 км звеньевого пути и 19845 км бесстыкового, т.е. всего с 43800 км. Если «распространить» отказы (см. табл. 2.1) на весь полигон главных путей с термоупрочненными рельсами первой укладки типа Р65 (88353 км), то в первом приближении приведенные данные нужно откорректировать, умножив на коэффициент К = 88353/43800 м ≈ 2. Тогда ориентировочно выход рельсов до гарантийной наработки тоннажа в средних условиях эксплуатации следует увеличить в два раза.
Если за средний для сети железных дорог уровень наработки гарантийного тоннажа принять 200 млн т бр., то получим число рельсов, не выдержавших такого тоннажа: NT = 1489·2 = 2978 шт. Эта цифра на два порядка больше реально предъявляемых по рекламации рельсов в течение года. Следовательно, существующая система реализации условий гарантии фактически не работает. В первую очередь подобное происходит из-за сложности доказать правомочность предъявления претензий и слабой заинтересованности в этой процедуре линейных предприятий железных дорог.
Потери ОАО «РЖД» от такого состояния с обеспечением гарантии на рельсы ежегодно могут достигать около 70 млн р. Если же дополнительно включить в расчет ущерб, связанный с заменой преждевременно отказавших рельсов (доставка, сама замена, задержки поездов и т.п.), то потери возрастут не менее чем в два раза, т.е. до 140 млн р. в год.
Немного меньше выход рельсов из строя из-за некачественной сварки (около 400 шт. в год) и нарушений условий взаимодействия колеса и рельса (около 700 шт. в год по пробуксовкам, юзу и т.п.), т.е. всего примерно 1100 шт. в год. Из-за этого ущерб ОАО «РЖД» может достигать 50–70 млн р. в год.
Таким образом, из-за преждевременного изъятия из пути рельсов только по трем группам дефектов до пропуска 200 млн т бр. ежегодные потери могут составить около 200 млн р. Суммарные же отказы рельсов по всем дефектам для такого тоннажа за год превысят 5 тыс. шт. и соответственно возрастут потери.
С целью резкого улучшения ситуации с такими отказами рельсов необходимо изменить процедуру предъявления претензий металлургическим комбинатом, разработать и внедрить систему внутри- и междорожных рекламаций на рельсы, вышедшие из строя на ранней стадии по вине сварочных предприятий, локомотивных и вагонных депо. Без этого потери не уменьшатся. В качестве первого шага в решении поставленной задачи от виновников отказа рельсов на рассматриваемой стадии их работы предлагается все компенсации (потери) получать в денежном исчислении.
Срок службы рельсов определяется пропущенным тоннажом при заданном уровне накопленных одиноч-
ных отказов. Для построения графиков зависимостей вида Σni = f(T) необходимо получить данные о выходе из строя рельсов в расчете на 1 км пути в каждом интервале пропущенного тоннажа. При обработке ведомостей ПУ-4 составление итоговых таблиц для рельсов НТМК и НКМК в звеньевом и бесстыковом пути требует значительных затрат труда и времени. Разделив число отказов ni в каждом интервале тоннажа Ti (0– 50, 51–100, 101–150 и т.д.) на протяжение пути Li, подучим удельные отказы ni = ni/ΔLi. По ним можно
44
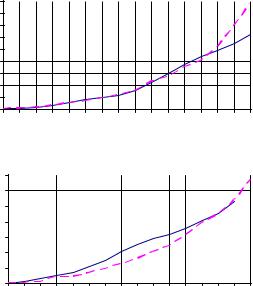
подсчитать накопленные отказы Σni и в итоге построить зависимости, представленные на рис. 2.4. По графикам легко найти средние значения тоннажей при удельном накопленном уровне одиночного изъятия
рельсов 4 шт./км (Т4) и 5 шт./км (Т5).
а)
шт./км |
9 |
|
|
|
|
|
|
|
8 |
|
|
|
|
|
|
|
|
7 |
|
|
|
|
|
|
|
|
отказов, |
6 |
|
|
|
|
|
|
|
5 |
|
|
|
|
|
|
|
|
4 |
|
|
|
|
|
|
|
|
Накопление |
3 |
|
|
|
|
|
|
|
2 |
|
|
|
|
|
|
|
|
1 |
|
|
|
|
|
|
|
|
0 |
|
|
|
|
|
|
|
|
25 |
125 |
225 |
325 |
425 |
525 |
625 |
725 |
|
|
|
|
Пропущенный тоннаж, млн т бр. |
|
б)
шт./км |
14 |
|
|
|
|
|
|
|
12 |
|
|
|
|
|
|
|
|
10 |
|
|
|
|
|
|
|
|
отказов, |
|
|
|
|
|
|
|
|
8 |
|
|
|
|
|
|
|
|
6 |
|
|
|
|
|
|
|
|
Накопление |
4 |
|
|
|
|
|
|
|
2 |
|
|
|
|
|
|
|
|
0 |
|
|
|
|
|
|
|
|
25 |
125 |
225 |
325 |
425 |
525 |
625 |
725 |
|
|
|
|
Пропущенный тоннаж, млн т бр. |
|
–––––––––– НКМК; — – — – — – НТМК
Рис. 2.4. Зависимость накопленного одиночного выхода термоупрочненных рельсов типа Р65 от пропущенного тоннажа в звеньевом (а) и бесстыковом (б) пути в 2006 г.
Итоговые Т4 и Т5 приведены в табл. 2.2. Видно, что в 2006 г. в звеньевом пути эти тоннажи для рельсов НТМК и НКМК находятся на уровне 2004–2005 гг. В бесстыковом пути Т4 и Т5 для рельсов НТМК остались на уровне 2005 г., а НКМК они увеличились на 85 и 115 млн т бр. соответственно.
Если срок службы рельсов НТМК в 2006 г. в звеньевом пути «вышел» на уровень 2000 г., то НКМК после резкого уменьшения в 2002–2003 гг. (из-за значительных поставок на сеть в предыдущие годы низкокачественных рельсов категории СВ) еще не достиг показателей 2000 г. В бесстыковом пути этот срок больше, чем в звеньевом, в 1,2–1,6 раза.
45
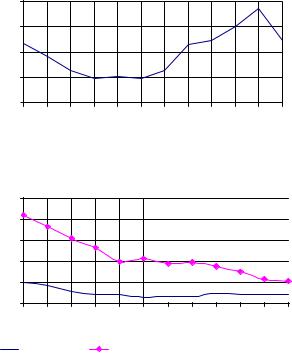
Таблица 2.2
Средние значения тоннажа, при накопленном одиночном изъятии рельсов 4 шт./км (Т4) и 5 шт./км (Т5)
|
|
Звеньевой путь |
|
|
Бесстыковой путь |
|
||
Год |
НТМК |
НКМК |
НТМК |
НКМК |
||||
|
Т4 |
Т5 |
Т4 |
Т5 |
Т4 |
Т5 |
Т4 |
Т5 |
2000 |
420 |
460 |
490 |
575 |
570 |
640 |
585 |
665 |
2001 |
470 |
510 |
575 |
665 |
540 |
640 |
710* |
850* |
2002 |
360 |
425 |
360 |
415 |
485 |
550 |
520 |
570 |
2003 |
415 |
500 |
235 |
270 |
560 |
650 |
700 |
825* |
2004 |
465 |
485 |
410 |
465 |
700 |
760 |
480 |
575 |
2005 |
485 |
515 |
400 |
500 |
630 |
670 |
505 |
570 |
2006 |
475 |
525 |
375 |
425 |
625 |
660 |
590 |
685 |
* — получено экстраполяцией
Для дальнейшего снижения удельных отказов рельсов и повышения их срока службы можно рекомендовать следующие меры:
–разработать и внедрить на меткомбинатах способы снижения отказов рельсов по заводским дефектам, прежде всего по дефекту 17; Департаменту пути и сооружений в свою очередь необходимо принять меры по улучшению работы стыков;
–на НТМК и НКМК активизировать внедрение упрочнения болтовых отверстий, так как выход рельсов по трещинам от них остается значительным (5–7 %);
–уровень отказов рельсов по дефектам сварки (до 16 %) в бесстыковом пути недопустимо высок, поэтому требуется серьезно улучшить технологию сварки, внедрить на всех РСП, во-первых, нормализацию сварных стыков для выравнивания твердости металла в зоне термического влияния сварки, во-вторых, правку стыков и фрезеровку зоны сварки при их отделке для обеспечения требуемой прямолинейности, в-третьих, внеочередные шлифовки головок рельсов в пути с целью уменьшения в сварных стыках вертикальных неровностей и их уклонов;
–быстрее уменьшить количество стыков в бесстыковом пути как за счет увеличения длины плетей, так и своевременным устранением стыков, образовавшихся при вырезке дефектных мест в плетях, обеспечить дороги рельсами длиной 12,5 м для уравнительных пролетов, заказав их на меткомбинатах. Эти меры снизят отказы рельсов уравнительных пролетов в 2–3 раза и в плетях — на 30–40 %.
–необходимо кардинально изменить порядок предъявления рекламаций на рельсы, вышедшие из строя на ранней стадии эксплуатации.
Особое значение для обеспечения безопасности движения поездов имеют отказы рельсов. Изломы рельсов под поездами тесно связаны с одиночным изъятием остродефектных рельсов из пути (рис. 2.5 и 2.6). Одиночное изъятие рельсов, особенно остродефектных, является важным показателем надежности пути и поэтому является основным показателем при планировании капитального ремонта и одиночной смены рельсов [23].
|
60000 |
|
|
|
|
|
|
|
|
|
57167 |
|
||
шт. |
|
|
|
|
|
|
|
|
|
|
|
|
||
50000 |
|
|
|
|
|
|
|
42843 |
49948 |
|
||||
рельсов, |
|
|
43225 |
|
|
|
|
|
|
|||||
40000 |
|
37974 |
|
|
|
32790 |
44377 |
44658 |
||||||
|
|
|
|
32644 |
30327 |
|
|
|
|
|||||
|
|
|
|
|
|
|
|
|
|
|||||
Излом |
30000 |
|
|
|
|
|
|
|
|
|
|
|
|
|
|
|
|
|
29783 |
|
29302 |
|
|
|
|
|
|||
20000 |
|
|
|
|
|
|
|
|
|
|
|
|
||
|
|
|
|
|
|
|
|
|
|
|
|
|
||
|
|
1995 |
1996 |
1997 |
1998 |
1999 |
2000 |
2001 |
2002 |
2003 |
2004 |
2005 |
2006 |
|
|
|
|
|
|
|
|
Годы |
|
|
|
|
|
|
|
|
|
Рис. 2.5. Остродефектные рельсы, выявленные на сети |
|
|||||||||||
|
|
|
|
железных дорог в 1995–2005 гг. |
|
|
|
|
||||||
|
процент |
500 |
|
|
|
|
|
|
|
|
|
|
|
|
|
400 |
420 |
363 |
|
|
|
|
|
|
|
|
|
|
|
|
|
|
|
|
|
|
|
|
|
|
|
|||
|
300 |
|
310 |
265 |
|
|
|
|
|
|
|
|
||
|
|
|
|
|
214 |
|
|
|
|
|
|
|||
|
рельсов, |
|
|
|
|
|
|
|
|
|
|
|||
|
200 |
98 |
83 |
|
197 |
188 |
195 |
176 |
152115 105 |
|||||
|
Излом |
100 |
|
58 |
41 |
39 |
27 |
35 |
30 |
48 |
|
43 44 |
40 |
|
|
|
|
|
|||||||||||
|
|
|
|
|
|
|||||||||
|
0 |
|
|
|
|
|
|
|
|
|
|
|
|
|
|
|
|
|
|
|
|
|
|
|
|
|
|
|
|
|
|
1995 1996 1997 1998 1999 2000 2001 2002 2003 2004 2005 2006 |
||||||||||||
|
|
|
|
|
|
|
|
Годы |
|
|
|
|
|
|
|
|
Всего изломов |
Изломов из-за пропуска дефектов |
|
46
Рис. 2.6. Изломы рельсов на сети железных дорог в 1995-2005 гг.
Изменение показателей выхода рельсов по опасным дефектам происходит пропорционально падению объема перевозок. Так, с 1991 по 1997 г. грузонапряженность дорог России снизилась в 2,13 раза, одиночное изъятие остродефектных рельсов уменьшилось в 1,87 раза, изломы рельсов происходили в 1,89 раза реже, пропуски операторами дефектоскопных тележек опасных дефектов снизились в 1,6 раза [22, 24].
Рост грузонапряженности российских железных дорог начиная с 1998 г. привел к росту числа изъятия из пути остродефектных рельсов (см. рис. 2.5).
Повышение качества рельсов ведет к значительному сокращению ежегодного изъятия дефектных, остродефектных рельсов и изломов их под поездами (рис. 2.6). Однако пока ежегодно на сети дорог ОАО «РЖД» изымается из пути около 120 тыс. дефектных и остродефектных рельсов, из них остродефектных — около 50 тыс. Ежегодно ломается в пути примерно 120 рельсов. Число пропусков остродефектных рельсов при дефектоскопном контроле составляет около 40 шт. в год (табл. 2.3–2.6) [25].
Таблица 2.3
Основные причины изъятия и изломов рельсов в 2005 г.
|
Причины отказа |
|
|
|
|
Общее изъятие |
|
|
|
|
Изломы |
|
|
|||||||||||||
|
|
|
|
|
шт. |
|
|
|
|
|
% |
|
|
|
шт. |
|
|
|
|
% |
|
|
||||
|
|
|
|
|
|
|
|
|
|
|
|
|
|
|
|
|
|
|
|
|||||||
|
Контактная усталость |
|
|
|
77732 |
|
|
|
|
|
65 |
|
|
|
24 |
|
|
|
|
21 |
|
|
||||
|
Износ |
|
|
|
16115 |
|
|
|
|
|
13 |
|
|
|
0 |
|
|
|
|
0 |
|
|
||||
|
Термомеханические повреждения |
12639 |
|
|
|
|
|
11 |
|
|
|
2 |
|
|
|
|
2 |
|
|
|||||||
|
Дефекты сарки |
|
|
|
5170 |
|
|
|
|
|
4 |
|
|
|
33 |
|
|
|
|
29 |
|
|
||||
|
Содержание стыков |
|
|
|
5262 |
|
|
|
|
|
4 |
|
|
|
15 |
|
|
|
|
13 |
|
|
||||
|
Коррозионная усталость |
|
|
|
326 |
|
|
|
|
|
0,3 |
|
|
|
33 |
|
|
|
|
29 |
|
|
||||
|
Всего |
|
|
|
119965 |
|
|
|
100 |
|
|
115 |
|
|
|
|
100 |
|
|
|||||||
|
|
|
|
|
|
|
|
|
|
|
|
|
|
|
|
|
|
|
|
|
|
|
|
|
|
Таблица 2.4 |
|
Изломы, пропуски и сходы по годам |
|
|
|
|
|
|
|
|
|||||||||||||||||
|
|
|
|
|
|
|
|
|
|
|
|
|
|
|
|
|
|
|
|
|||||||
|
Инциденты |
|
|
|
|
Количество инцидентов по годам, шт. |
|
|||||||||||||||||||
|
|
|
|
2002 |
|
|
2003 |
|
|
2004 |
|
2005 |
|
2006 |
|
|
||||||||||
|
|
|
|
|
|
|
|
|
|
|
|
|
||||||||||||||
|
Изломы |
|
|
|
186 |
|
|
176 |
|
|
|
152 |
|
117 |
|
|
105 |
|
|
|||||||
|
в том числе пропуски |
|
|
|
47 |
|
|
45 |
|
|
|
45 |
|
43 |
|
|
40 |
|
|
|||||||
|
Сходы |
|
|
|
2 |
|
|
1 |
|
|
|
|
3 |
|
2 |
|
|
2 |
|
|
||||||
|
|
|
|
|
|
|
|
|
|
|
|
|
|
|
|
|
|
|
|
|
|
|
|
|
|
Таблица 2.5 |
|
Вероятность изломов рельсов в пути за 2005 год |
|
|
|
|
|
|
|
|
|||||||||||||||||
|
|
|
|
|
|
|
|
|
|
|
|
|
|
|
|
|
|
|
|
|
|
|
||||
|
Параметры |
|
|
|
|
|
|
|
Наработка, млн т бр. |
|
|
|
|
|
|
|
|
|||||||||
|
|
менее 250 |
251–350 |
351–500 |
501–600 |
601–750 |
|
более 750 |
|
|||||||||||||||||
|
|
|
|
|
||||||||||||||||||||||
Изъятие N, тыс. шт. |
|
3598 |
|
|
1240 |
|
1375 |
|
|
669 |
|
471 |
|
|
169 |
|
|
|||||||||
Изломы n, шт. |
|
33 |
|
|
13 |
|
18 |
|
|
|
15 |
|
24 |
|
|
14 |
|
|
||||||||
Вероятность излома P, % |
|
9 |
|
|
10 |
|
13 |
|
|
|
22 |
|
51 |
|
|
83 |
|
|
||||||||
|
|
|
|
|
|
|
|
|
|
|
|
|
|
|
|
|
|
|
|
|
|
|
|
|
|
Таблица 2.6 |
|
Основные причины изъятия остродефектных рельсов, |
|
|
|
|
|||||||||||||||||||||
|
|
изломов и пропусков в 2006 г. |
|
|
|
|
|
|
|
|
|
|
|
|||||||||||||
|
|
|
|
|
|
|
|
|
|
|
|
|
|
|
|
|||||||||||
|
Причина отказа |
|
|
|
Общее изъятие |
|
|
|
Изломы |
|
|
Пропуски |
|
|||||||||||||
|
|
|
|
шт. |
|
% |
|
шт. |
|
% |
|
|
шт. |
|
% |
|
|
|||||||||
|
|
|
|
|
|
|
|
|
|
|
|
|
||||||||||||||
|
Контактная усталость |
|
|
|
28235 |
|
67,3 |
|
22 |
|
21 |
|
|
18 |
|
|
51 |
|
|
|||||||
|
Термомеханические повреждения |
|
3305 |
|
7,9 |
|
3 |
|
3 |
|
|
3 |
|
|
9 |
|
|
|||||||||
|
Дефекты сварки |
|
|
|
4535 |
|
10,8 |
|
37 |
|
35 |
|
|
11 |
|
|
31 |
|
|
|||||||
|
Содержание стыков |
|
|
|
5591 |
|
13,3 |
|
12 |
|
11 |
|
|
0 |
|
|
0 |
|
|
|||||||
|
Коррозионная усталость |
|
|
|
282 |
|
0,7 |
|
31 |
|
30 |
|
|
3 |
|
|
9 |
|
|
|||||||
|
Всего |
|
|
|
41948 |
|
100 |
|
105 |
|
100 |
|
35 |
|
|
100 |
|
|
В 2007 г. на Западно-Сибирской железной дороге из пути изъято 3613 остродефектных рельсов, из них 67 % вышли из строя по причине недостаточной контактно-усталостной прочности (дефекты 21 и 30Г). Достаточно высок выход рельсов из-за термических повреждений катания — 6,2 %.
За последние 4 года под поездами изломалось 24 рельса, из них — 8 (30 %) вследствие контактной усталости и 7 (29 %) из-за дефектов сварки.
Несмотря на некоторое повышение эффективности работы средств дефектоскопии и снижение процента брака в работе в 2006 г. почти треть изломов рельсов произошла из-за пропусков дефектов по вине операторов дефектоскопов. При этом 18 пропусков составляли дефекты группы контактно-усталостных дефектов и 11 пропусков — дефекты сварки в зоне стыков, т.е. наиболее опасные группы дефектов.
Как показал анализ, основными причинами пропусков дефектов стали низкий уровень профессиональной подготовки операторов дефектоскопов и обслуживающего персонала мобильных средств дефектоскопии, связанный с недостатками процесса обучения, большой текучестью кадров, низким уровнем заработной платы работников дефектоскопии, не соответствующим уровню сложности и ответственности выполняемой работы. Подтверждением этому служит большая текучесть и неукомплектованность кадров специалистов дефектоскопии.
47
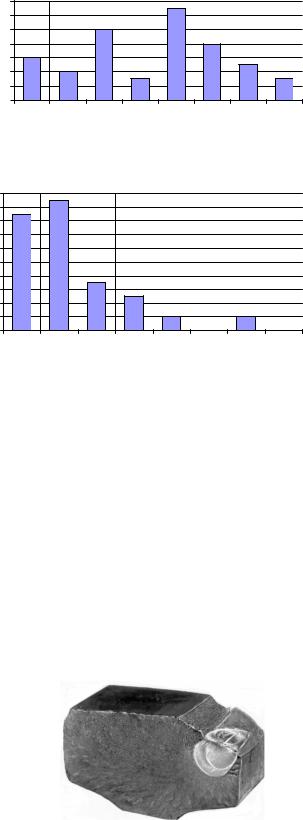
Максимальное число изломов наблюдается в диапазоне наработанного тоннажа 300–600 млн т бр. (рис. 2.7). Однако вероятность изломов резко возрастает после пропуска 600 млн т бр. (табл. 2.5). Отрицательное влияние на количество изломов рельсов оказывают низкие температуры в диапазоне от –20 до –40 ºС (рис. 2.8).
Количество изломов, шт.
14 |
|
|
|
|
|
|
|
12 |
|
|
|
|
|
|
|
10 |
|
|
|
|
|
|
|
8 |
|
|
|
|
|
|
|
6 |
|
|
|
|
|
|
|
4 |
|
|
|
|
|
|
|
2 |
|
|
|
|
|
|
|
0 |
|
|
|
|
|
|
|
101- |
201- |
301- |
401- |
501- |
601- |
701- |
801- |
200 |
300 |
400 |
500 |
600 |
700 |
800 |
900 |
|
Диапазоны пропущенного тоннажа, млн т бр. |
|
|
Рис. 2.7. Распределение изломов по пропущенному тоннажу |
|||||||
|
20 |
|
|
|
|
|
|
|
шт. |
18 |
|
|
|
|
|
|
|
16 |
|
|
|
|
|
|
|
|
изломов, |
14 |
|
|
|
|
|
|
|
12 |
|
|
|
|
|
|
|
|
10 |
|
|
|
|
|
|
|
|
Количество |
8 |
|
|
|
|
|
|
|
6 |
|
|
|
|
|
|
|
|
4 |
|
|
|
|
|
|
|
|
2 |
|
|
|
|
|
|
|
|
|
0 |
|
|
|
|
|
|
|
|
–40 –31 |
–30 –21 |
–20 –11 |
–10 0 |
0 +10 |
+11 +20 |
+21 +30 |
+31 +40 |
|
|
Диапазоны температуры, градусы Цельсия |
|
Рис. 2.8. Распределение изломов по температурам
2.3. Особенности эксплуатационной стойкости отечественных рельсов
Анализирую состояние рельсового производства, известные специалисты В.В. Павлов, Е.А. Шур и Г.Н. Юнин сделали следующие выводы [26] относительно качества современных отечественных рельсов:
–во-первых, по уровню технологии выплавки стали и ее качеству преодолено отставание от таких лидеров, как, к примеру, «Ниппон Стил» (Япония);
–во-вторых, оборудование и технологии прокатки, отделки и контроля готовых рельсов соответствуют лишь 70–80-м годам прошлого века; за последние 25 лет ряд известных передовых технологий, в частности, применение универсальных клетей на стане, а также современного правильного и отрезного оборудования, на меткомбинатах не внедрен.
В настоящее время основными и наиболее опасными дефектами, по которым изымают из пути железнодорожные рельсы, являются дефекты контактно-усталостного происхождения (деф. 11.1-2 и деф. 21.1-2 по классификаций ОАО «РЖД»). Установлено, что такие дефекты развиваются в головке рельсов от внутренних продольных трещин (ВПТ). ВПТ возникают на некоторой глубине (3–14 мм от поверхности катания) на строчечных скоплениях высокотвердых включений. Доказано, что в случае раскисления стали алюминием строчечные скопления глинозема длиной более 8 мм составляют около 5 % количества проконтролированных шлифов. В то же время количество ВПТ, в эпицентре которых находились «строчки» глинозема длиннее 8 мм, характерно для 75 % рельсов, изъятых но контактно-усталостным дефектам (рис. 2.9).
а
)
48
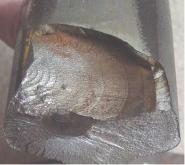
б
)
Рис. 2.9. Контактно-усталостные повреждения рельсов о ВПТ:
а — дефект 11/21; б — поперечная трещина — продольная от поверхности
На первом этапе исследований была ограничена допустимая длина строчек глинозема, на втором — проделана работа по дальнейшему ограничению длины таких строчек, а также внесена в стандарт допустимая длина для хрупкоразрушающих сложных окислов (алюминатов, силикатов, шпинелей и др.) в стали рельсов различных категорий качества [27].
Втечение ряда лет на рельсопрокатных предприятиях России (ОАО «НТМК» и ОАО «НКМК») проводят работы по изысканию оптимальных вариантов комплексного раскисления рельсовой стали. По наиболее перспективным вариантам прокатаны рельсы, которые испытывали на Экспериментальном кольце.
Впроцессе полигонных испытаний рельсы опытных партий изымали из путей кольца по различным дефектам, в том числе по контактно-усталостным, причем в первую очередь по поперечным усталостным трещинам в головке (деф. 21.1-2). Пробы с дефектами доставляли в лабораторию, где подвергали прецизионному дефектоскопированию. Цель этих мероприятий: во-первых, обнаружить ВПТ, во-вторых, определить их точные геометрические параметры (длину, ширину, глубину залегания), без знания которых вскрыть такие дефекты для дальнейших исследований не представляется возможным. Необходимо это для изучение их фокуса, т.е. исследование строчечных скоплений неметаллических включений путем микрорентгеноспектрального анализа с определением химического состава включений. Этот этап исследований чрезвычайно важен, поскольку позволяет проводить корректировку технологии раскисления рельсовой стали.
Размеры и состав неметаллических включений (НМВ), расположенных в фокусе ВПТ опытных рельсов, отличаются от аналогичных параметров рельсов, изготовленных в 2000–2001 гг. Длина «строчек» НМВ не более 1 мм, диаметр поперечного сечения отдельных включений не превышает 60 мкм. Включения представляют собой сложные силикаты, содержащие алюминий, кремний, кальций и магний, среди них нет алюминатов кальция. Содержание алюминия в силикатах существенно уменьшилось и не превышает 26,7 %. Химический состав практически такой же, как в рельсовой стали японской фирмы «Nippon Steel Corporation», французской «Soqerail».
На сегодняшний день российскими учеными проведены детальные сравнительные исследования металлургического качества рельсов отечественных и иностранных производителей. Общепризнанно, что конструктивную надежность рельсов определяет металлургическая чистота стали, как по общей загрязненности неметаллургическими включениями, так и их морфологией. Важным фактором является и состояние металлической матрицы, параметры ее макро- и микроструктуры.
Эксплуатационная стойкость стали в значительной степени зависит от морфологии включений и объемной доли неблагоприятных включений (оксиды, алюминаты, алюмосиликаты кальция).
Следует обратить внимание на то, что при исключении прямого раскисления стали алюминием в рельсовом металле отечественного производства массовая доля алюминия намного выше, чем в металле Японии и Франции, что возможно только при применении ферросплавов, более загрязненных алюминием, чем за рубежом.
Таким образом, для улучшения качества металла необходимой [28]:
– разработать и внедрить технологию диффузионного раскисления стали на вакууматоре для обеспечения низкого содержания кислорода в расплаве;
– проводить окончательное раскисление кремнием после вакуумирования стали;
– сократить применение силико-кальция для окончательного раскисления стали (возможно совсем исключить его, заменив обработкой расплава барием). Положительное влияние бария на эксплуатационную стойкость рельсов доказано исследованиями, проведенными Уральским институтом металлов совместно с НКМК;
– провести анализ поставщиков ферросплавов на содержание алюминия, что позволит изменить морфологию неметаллических включений в лучшую сторону и повысить эксплуатационный ресурс рельсов.
Еще одной немаловажной проблемой является состояние металлической матрицы. Оценки влияния ее свойств достаточно противоречивы.
49
Макроструктура головки рельсов отечественного производства по сравнению с японскими образцами более грубая и текстурованная. Намного хуже макроструктура шейки рельсов в местах, где проходит ликвационная ось слитка.
Вопросы применения прямых обжатий элементов профиля, особенно головки рельса, могут быть решены с использованием универсальных клетей, предусмотренных в планах реконструкции комбинатов ООО
«ЕвразХолдинг». При этом следует выбирать более мощные чистовые клети, обеспечивающие возможность деформации и формирования профиля при более низких температурах, что обеспечит улучшенные свойства рельсов.
Оснащение машин непрерывного литья электромагнитным перемещением металла в зоне кристаллизации, а также применение мягкого обжатия устья жидкой лунки слитка позволит решить проблемы формирования необходимой структуры слитка.
Исследования влияния параметров микроструктуры на стойкость рельсов, проведенные во ВНИИЖТе, позволили сформулировать принцип однотипной структуры, суть которого заключается в том, что эксплуатационная стойкость рельсов непрерывно повышается с ростом твердости (дисперсности структуры) только у группы рельсов с однотипной структурой. Наиболее конструктивная прочность получается либо при однородной тонкопластичной структуре сорбита максимальной дисперсности с твердостью 331–388 НВ, либо однородной структуре отпущенного мартенсита или бейнита.
К сожалению, Новокузнецкий и Нижнетагильский металлургические комбинаты оснащены оборудованием, не позволяющим регулировать процессы распада аустенита в нижней области диффузного превращения. Это станет возможным при внедрении дифференцированного охлаждения головок рельсов на соответствующем оборудовании, что предусмотрено одним из этапов реконструкции рельсобалочных цехов этих комбинатов.
Необходимо отметить, что при процессах распада аустенита по перлитному механизму, идущему с достаточно большими скоростями, чрезвычайно трудно сконструировать универсальную установку, которая оптимизировала бы скорости охлаждения рельсов в широком диапазоне химического состава. В связи с этим необходимо плавить сталь в достаточно узком диапазоне химического состава и оптимизировать кинетику превращения аустенита соответствующим легированием стали под технические возможности конкретной установки термоупрочнения.
Рельсы, производимые на Новокузнецком и Нижнетагильском металлургических комбинатах (НКМК и НТМК), не полностью отвечают современным и особенно перспективным условиям эксплуатации. Эти комбинаты не могут изготавливать даже рельсы категории «В» длиной 25 м, соответствующие ГОСТ Р 51685– 2000.
Эксплуатационная стойкость рельсов определяется структурой стали, неметаллическими включениями, наличием разнообразных внутренних и наружных дефектов металлургического происхождения, химическим составом металла, механическими свойствами, остаточными напряжениями, геометрическим качеством (прямолинейностью), а также качеством обработки болтовых отверстий и торцов. В табл. 2.7 сопоставлены качества отечественных и зарубежных рельсов. Можно видеть, что наши термически упрочненные рельсы уступают лучшим иностранным по следующим параметрам [28]:
–прямолинейность (по всей длине и по концам рельсов);
–качество поверхности и отделки (торцы, болтовые отверстия, фаски);
–чистота стали по неметаллическим включениям и вредным примесям (сера, фосфор, водород, кисло-
род);
–прокаливаемость, обеспечивающая в зарубежных рельсах более высокую твердость и прочность в зоне действия высоких контактных напряжений, а также большую износостойкость;
–остаточные напряжения.
Вместе с тем у иностранных рельсов ниже ударная вязкость по сравнению с российскими, поэтому нужно более тщательно соблюдать технологию сварки. Качество рельсов передовых зарубежных производителей определяется лучшим оборудованием на заводах. Во-первых, это вакууматоры и технические средства для внепечной рафинирующей обработки жидкой рельсовой стали; современные нагревательные, прокатные и правильные агрегаты, а также станки для механической обработки при изготовлении прокатных валкой и отделке рельсов. Вовторых, установки для закалки рельсов из углеродистой и хромистой сталей с дифференцированным охлаждением по сечению сжатым воздухом. В-третьих, комплекс оборудования для сплошного контроля внутренних и поверхностных дефектов и прямолинейности рельсов. В-четвертых, большая степень компьютеризации производства.
Таблица 2.7
Основные показатели, определяющие эксплуатационную стойкость рельсов
Наименование показателя |
Изготовитель рельсов |
||
Россия (НТМК НКМК) |
Япония, Франция и др. |
||
|
|||
Содержание кислорода, ppm |
20–40 |
5–20 |
|
Содержание алюминия, % |
0,005–0,020 |
0,004–0,005 |
|
Чистота стали — максимальная длина строчек |
0,8–1,0 |
0,2–0,3 |
|
неметаллических включений, мм |
|||
|
|
||
Твердость головки в зоне максимальных кон- |
321–363 |
341–388 |
50
тактных напряжений, НВ |
|
|
|
Ударная вязкость в головке, МДж/м2 |
0,25–0,35 |
0,12–0,17 |
|
Остаточные напряжения — расхождение паза, |
2,0–2,5 |
1,0–1,5 |
|
мм |
|||
|
|
||
Вертикальная неровность на длине 1,5 м, мм |
0,3–0,9 |
0,2–0,4 |
|
Кривизна концов вверх/вниз/боковая, мм |
0,7/0,3/0,5 |
0,5/0,0/0,5 |
Улучшение технологической дисциплины на наших металлургических комбинатах и проводимые там незначительные усовершенствования могут лишь немного поднять качество рельсов. Для того чтобы этот показатель приблизился к зарубежному, необходимы большая реконструкция существующих комбинатов или строительство нового с соответствующими инвестициями.
Последние крупные мероприятия по реконструкции рельсового производства были следующими:
–освоение изготовления термоупрочненных рельсов — объемная закалка рельсов в масле на НТМК в 1966 г. и на НКМК в 1979 г.;
–освоение выпуска рельсовой стали без крупных скоплений глинозема (оба меткомбината — 70-е годы);
–внедрение сплошного неразрушающего ультразвукового контроля внутренних дефектов в проекции шейки (оба меткомбината — 70-е годы);
–освоение производства продукции из кислородно-конвертерной стали (НТМК) и электростали (НКМК): рельсы изготавливают из заготовок, полученных непрерывной разливкой (оба меткомбината с 1997 г.); на НТМК сталь подвергается вакуумированию, на НКМК вакуумирования нет; на НКМК внедрена установка для внепечной обработки стали в ковше (2003 г.), на НТМК реконструирована головная часть рельсобалочного цеха.
В ближайшей перспективе все отечественные рельсы должны выпускать из кислородно-конвертерной стали или электростали, подвергнутой внепечной обработке, которая обеспечит однородность химического состава и высокую чистоту стали по неметаллическим включениям, а также отсутствие флокенов. Планируется существенно повысить уровень компьютеризации управления и контроля за всеми операциями выплавки и разливки стали. Прокатка рельсов из непрерывнолитых заготовок будет начинаться с нагрева в методической печи с шагающими балками (уже внедрено на НТМК, а введение в строй на НКМК намечено на 2005 г.).
Ввод в действие печей прецизионного нагрева позволит в дальнейшем применить гидросбив окалины при прокатке, что существенно улучшит чистоту поверхности рельсов, а также даст возможность пересмотреть всю их калибровку. На НКМК начали обновлять вальцетокарные станки для точной калибровки валков обжимных и рельсопрокатных станов. Весьма перспективно использование универсальных клетей на последних стадиях прокатки.
Предстоит разработать более прогрессивную и высокопроизводительную технологию термической обработки рельсов взамен применяемой в настоящее время объемной закалки в масле. При разнообразии существующих за рубежом технических решений наиболее интересна закалка рельсов с прокатного нагрева с двухсторонним дифференцированным охлаждением сжатым воздухом или водой, в результате чего получаются достаточно прямые рельсы перед холодной правкой. Последнюю необходимо выполнять на роликоправильных машинах с большим числом валков, чем на имеющихся в настоящее время на отечественных металлургических комбинатах. После правки рельсы должны быть не только прямыми, но и с благоприятной эпюрой остаточных напряжений. Кроме новых роликоправильных машин, меткомбинаты следует оснастить гидравлическими прессами для правки рельсов в двух плоскостях без кантовки, с лазерным технологическим измерителем величины и профиля местных неровностей.
В кардинальном обновлении нуждается техника для механической обработки и отделки термоупрочненных рельсов. Это и переход от фрезерования торцов к чистовой разрезке на агрегатных сверлильноотрезных станках типа станков фирмы «Вагнер», и внедрение оборудования для упрочнения болтовых отверстий, а также новых технических средств для маркировки рельсов.
На российских меткомбинатах совершенно недостаточен объем сплошного неразрушающего контроля рельсов. Он сводится только к ультразвуковому контролю внутренних дефектов в проекции шейки за исключением концевых зон, и контролю прямолинейности рельсов для скоростного совмещенного движения (СС) с помощью прибора «Элекон». В перспективе так же, как за рубежом, каждый рельс должен быть подвергнут, по крайней мере, трем видам неразрушающего контроля: ультразвуковому на внутренние дефекты по всему поперечному сечению, токовихревому на поверхностные дефекты и контролю на прямолинейность.
Имеются и другие недостатки отечественных рельсов. Назовем шесть из них.
–Максимально возможная длина 25 м, необходимая — до 50 м и более. Длина рельсов ведущих производителей — Фест Альпине, Корус — составляет 100 м и более. У нас она ограничивается планировкой рельсобалочных цехов, построенных еще в 1932 г. и 1947 г.
–Недостаточна твердость головки, что приводит к ее повышенному износу. В кривых участках пути срок службы рельсов не превышает двух-трех лет.
–Велики остаточные внутренние напряжения, которые способствуют возникновению и развитию трещин при эксплуатации, в частности разрушениям вдоль шейки.
51
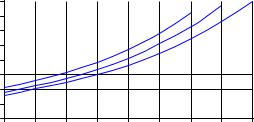
–Механические свойства не соответствуют требованиям национального стандарта (для категории В).
–Существующая технология термообработки не позволяет изготавливать хромистые рельсы, демонстрирующие наиболее высокие потребительские свойства.
–Размер вредных неметаллических включений в зарубежных рельсах не превышает 15 мкм, в отечественных — 1500 мкм.
Все перечисленные факторы сказываются на эксплуатационной стойкости рельсов. Испытания на Экспериментальном кольце ВНИИЖТа, проведенные в последние годы, показали, что стойкость наших рельсов в 2-3 раза ниже японских, французских и др. (300-500 млн т против 1000 млн т и более). На Российских железных дорогах более 10 тыс. чел. занято дефектоскопным контролем рельсов в пути. Тем не менее ежегодно под колесами поездов разрушается около 200 из них, что серьезно ухудшает безопасность движения.
НКМК и НТМК составили и согласовали с железнодорожниками планы коренной реконструкции своих предприятий. Ее стоимость 200–300 млн долларов США. В этой ситуации МПС вынуждено было в 90-е годы закупить на наиболее ответственные участки пути небольшое количество японских и канадских рельсов. Однако проблема обеспечения безаварийной и длительной работы рельсов остается и усугубляется.
2.4. Работоспособность рельсов с трещинами
Основная причина изломов рельсов — дефекты усталостного происхождения. Наиболее опасны поперечные трещины в головке рельсов — дефект 21.1-2. Такие трещины, достигнув критического размера, приводят к хрупкому долому всего сечения рельса пол поездом. В этом случае следует рассматривать две стадии работы рельса: первая — бездефектная, которая заканчивается зарождением контактно-усталостной трещины, вторая — развитие последней до критического размера.
Вторую стадию классифицируют как живучесть рельсов. Следовательно, их надежность в конкретных условиях эксплуатации предопределена продолжительностью этой стадии, которая, в свою очередь, зависит от критического размера трещины и скорости се развития. Для того чтобы немедленно (после обнаружения) не изымать рельс с дефектом 21.1-2 небольшой площади (от 5 до 15 %), необходимо иметь количественную оценку указанных параметров [29].
Сначала рассмотрим скорость развития поперечной трещины в головке рельсов. В немногочисленных публикациях на эту тему выделим сведения об исследованиях В.Л. Порошина [30]. Их проводили на 25 опытных участках пути с незакаленными рельсами при различной грузонапряженности, скорости движения 70–80 и 40–50 км/ч и осевых нагрузках от 125 до 190 кН. Для каждого участка получили зависимость скорости роста трещины от пропущенного тоннажа (рис. 2.10).
|
40 |
|
|
|
|
1 |
|
|
|
é |
35 |
|
|
|
|
|
|
|
|
|
|
|
|
|
|
|
2 |
||
î ò |
|
|
|
|
|
|
|
||
30 |
|
|
|
|
|
|
|
||
еречн ро цен |
|
|
|
|
|
|
|
|
|
25 |
|
|
|
|
|
|
|
|
|
|
|
|
|
|
|
|
|
|
|
î ï , ï |
20 |
|
|
|
|
|
|
|
|
àäü ï èí û |
15 |
|
|
|
|
|
|
|
|
10 |
|
|
|
|
|
|
|
|
|
ëî ù òðåù |
|
|
|
|
|
|
|
|
|
5 |
|
|
|
|
|
|
|
|
|
Ï |
0 |
|
|
|
|
|
|
|
|
|
|
|
|
|
|
|
|
|
|
|
0 |
5 |
10 |
15 |
20 |
25 |
30 |
35 |
40 |
|
|
|
Ï ðî ï óù åí í û é òî í í àæ, ì ëí |
ò áð. |
|
|
|||
Рис. 2.10. Зависимость площади трещины от пропущенного тоннажа: |
|||||||||
1, 2 — соответственно верхняя и нижняя границы доверительной функции |
Как видно из графика, такая зависимость, во-первых, описывается экспоненциальным законом, вовторых, наработка тоннажа при увеличении площади трещин от 10 до 30 % сечения головки рельса составила около 30 млн т бр., что свидетельствует о достаточно высокой живучести рельсов. В то же время приведенная зависимость, видимо, является обобщенной на всех опытных участках пути. В.Л. Порошин приводит также данные о влиянии эксплуатационных факторов на скорость развития трещин. В таблице показан пропущенный тоннаж при развитии трещин от 25 до 30 % сечения головки. Можно видеть, что на интенсивность развития трещин значительное влияние оказывает статическая осевая нагрузка и скорость движения. Усталостные трещины растут быстрее также с уменьшением радиуса кривых.
Анализируя критические размеры поперечных усталостных трещин (в разных странах они различны, к примеру, в Венгрии — 45 %, в Германии 50 %, а во Франции 55 % площади головки рельса), необходимо учитывать один из важнейших факторов — температуру. По данным служб пути, на дорогах, расположенных в районах с холодным и очень холодным климатом (среднесуточная температура от –20 °С и ниже — соответственно 53 и 142 дня) зимой одиночное изъятия рельсов по различным дефектам в 2,0–2,5 раза больше, чем летом. При этом минимальные размеры поперечных усталостных трещин, приведших к излому нетермоупрочненных рельсов Р65 под поездом, в зимний период составили 10 % площади головки, в летний
— 40 %, а объемнозакаленных в зимний период — 20 %, а летом изломов не было.
52