
645
.pdfОпределение коэффициента трения
В приспособлениях силы трения возникают на поверхностях контактазаготовки с опорными и зажимными элементами. Величина коэффициента трения зависит от многих факторов. При использованииприспособленийегорасчетсвязансопределенными трудностями. В приспособлениях встречается много различных сочетаний контактных поверхностей, отличающихся по форме, состоянию поверхности, твердости и т. д. Значения коэффициента трения для некоторых сочетаний контактных поверхностей приведены в прил. Г.
Расчет коэффициента надежности закрепления
Впроизводственных условияхмогутиметь место отступления от тех условий, применительно к которым рассчитывались по нормативам силы и моменты резания, возможное их увеличение следует учесть путем введения коэффициента надежности (запаса) закрепления K.
Значение коэффициента надежности K следует выбирать дифференцированно в зависимости от конкретных условий выполнения операции и способа закрепления заготовки. Его величинуможно представитькакпроизведениечастныхкоэффициентов, каждый из которых отражает влияние определенного фактора:
K = K0K1K2K3K4K5K6,
где K0 — гарантированный коэффициент запаса надежности закрепления (K0 = 1,5); K1 — коэффициент, учитывающий увеличение силы резания из-за случайных неровностей на заготовках (K1 = 1,2 — для черновой обработки; K1 = 1,0 — для чистовой обработки); K2 — коэффициент, учитывающий увеличение силы резания вследствие затупления инструмента (прил. Д); K3 —коэффициент, учитывающий увеличение силы резания при прерывистом резании (K3 = 1,0 — при работе без удара; K3 = 1,2 — при работе с ударом); K4 — коэффициент, учитывающий непостоянство зажимного усилия (K4 = 1,3 — для ручных зажимов; K4 = 1,0 — для пневматических и гидравлических зажимов); K5 — учитывает степень удобства расположения рукояток в ручных зажимах (K5 = 1,2 — при диапазоне угла отклонения рукоятки 90°; K5 = 1,0 —при удобном расположении
1 1

и малой длине рукоятки); K6 — учитывает неопределенность изза неровностей места контакта заготовки с опорными элементами, имеющими большую опорную поверхность (учитывается только при наличии крутящего момента, стремящегося повернуть заготовку), (K6 = 1,0 — для опорного элемента, имеющего ограниченнуюповерхностьконтактасзаготовкой;K6 =1,5 —для опорного элемента с большой площадью контакта).
Величина K может колебаться в пределах от 1,5 до 8,0. Если K < 2,5, то при расчете надежности закрепления ее следует принять равной K = 2,5 (согласно ГОСТ 12.2.029).
4.8.2. Расчет зажимных устройств приспособлений
Винтовые зажимные устройства
Номинальный (наружный) диаметр винтового зажима определяется по формуле
d W ,
0,5
где W — усилие, действующее на винт при закреплении заготовки, Н; — допускаемое напряжение растяжения (сжатия) материала винта при переменной нагрузке, МПа (прил. Е).
Момент, развиваемый на рукоятке или маховике, для получения заданной силы зажима W определяется по формуле
M 0,001rсрW tg( ) Mтр,
где rср — средний радиус резьбы, мм; W —сила зажима, Н; — угол подъема резьбы, град ( = 2°30 …3°30 ); условие самоторможения: 6°30 ; — угол трения в резьбе, град ( = 6°40 ); Мтр — момент трения на опорном торце гайки или торца винта в контакте с заготовкой, Н∙м.
Величинамоментатрениязависит отхарактерасоприкосновения гайки или торца винта (рис. 1).
Для гаек или звездочек, имеющих кольцеобразную поверхность трения,
M |
|
|
1 |
10 3Wf |
D3 |
d3 |
, |
тр |
|
D2 |
d2 |
||||
|
3 |
|
|
где D — наружный диаметр кольцеобразной поверхности, мм; d — внутренний диаметр, равный диаметру резьбы, мм; f — коэффициент трения на торцевой поверхности (f = 0,15).
1 2
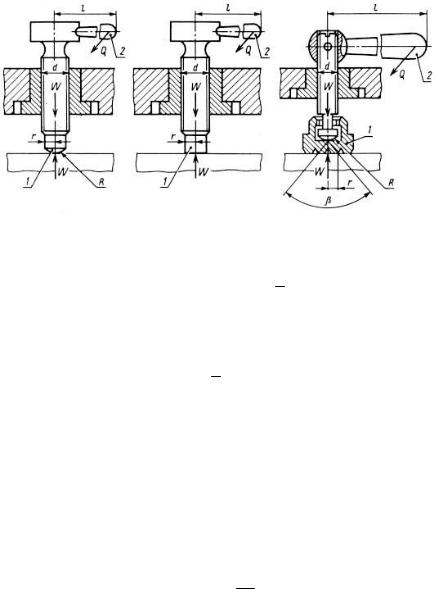
а) |
б) |
в) |
Рис. 1. Винтовые зажимы
Для винтов с башмаком, предупреждающим повреждение поверхности заготовки, момент трения находится по формуле
Mтр 10 3Wfrctg , 2
где r—радиус сферы винта, мм; —уголконусабашмака, град. Для винтов с плоским торцом, имеющим размер d1, момент
трения будет равен:
Mтр 110 3Wfd1. 3
Для винтов со сферическим торцом момент трения мал (менее 3 %) и им можно пренебречь.
Предельные моменты, создаваемые рукой рабочего при различных конструкциях приводного элемента, также приведены в прил. Е в зависимости от размера этого элемента. Пользуясь данной в приложении таблицей, можно обоснованно выбирать конструкциюголовкипонайденномузначениюмоментапривода.
При использовании других приводных элементов (гаечные ключи,маховики,штурвалыи т. д.) размер приводногоэлемента можно определять по формуле
l 103 M ,
PP
где РР — усилие, создаваемое рабочим на рукоятке (РР = = 100…150 Н), Н; l — плечо действия силы на рукоятке, мм.
1 3
Если размеры приводных элементов получаются слишком большими, а сами устройства становятся слишком громоздкими, то необходимо отказаться от зажима вручную или пересмотреть схему закрепления заготовки.
Рычажные зажимные устройства
При точном расчете рычажных зажимов необходим учет сил трения, возникающих на оси, а также в местах контакта с заготовкой и плунжером, передающим исходное усилие на рычаг. В этих случаях получаются довольно громоздкие расчетные формулы.
Если конструктивноеоформление рычагов выполнятьсминимальными плечами сил трения, а ось принимать с учетом допустимых напряжений на смятие и срез, то общие потери на трение составят порядка 8…10 %. Поэтому в целях более быстрогорасчетарычажныхмеханизмовможноприменятьупрощенные формулы, вводя КПД, равный 0,85.
При этом условии основные схемы расчета рычажных устройств и формулы для определения усилия, передаваемого на рычаг, приведены в прил. Ж.
При составлении вышеуказанного приложения сделано допущение, что необходимая для закрепления заготовки сила W известна из ранее выполненных расчетов (п. 4.8.1) и требуется определить усилие на приводе рычажного устройства.
Клиновые зажимные устройства
Соотношения между силой на приводном клине и зажимом плунжера, воздействующего назаготовку, определяются схемой клиноплунжерного устройства, величиной конструктивных параметров и потерями на трение.
Длянаиболеераспространенныхклиноплунжерныхустройств расчетные схемы и формулы для определения усилий даны в прил. И.
Коэффициент полезного действия клиноплунжерных устройств находится по формуле
= itg ,
где i — передаточное отношение сил; — угол наклона клина. Для указанных в приложении случаев и для других клиноплунжерных устройств передаточное отношение сил равно отно-
шению силы зажима и силы, приложенной к клину:
1 4

i W . Q
Передаточное отношение перемещений для всех видов клиновых и клиноплунжерных устройств определяется по формуле
iп S0 tg ,
Sp
где S0 — перемещение плунжера, закрепляющего заготовку, мм; Sp — перемещение приводного клина, мм.
Так, при угле 5° это передаточное отношение будет равно 0,088, т. е. перемещение приводного клина приблизительно в 11 разбольше,чемперемещениеплунжера. Поэтомурекомендуется использовать приводной клин с двойным углом наклона: на участке быстрого подвода клин может иметь угол 25°…45°, а на рабочем участке угол наклона принимается с учетом самоторможения и желательного передаточного отношения сил.
Эксцентриковые зажимные устройства
Если угол поворота эксцентрика не ограничен, то величина эксцентриситета определяется по следующей формуле:
e W S1 S2 , 2 2j 2 2
где — допуск на размер заготовки от ее установочной базы, мм; W — сила зажима заготовки, Н; S1 — зазор, обеспечивающий свободную установку заготовки под эксцентрик, мм (S1 = 0,2…0,4 мм); S2 — запас хода эксцентрика, мм (S2 = = 0,1…0,6 мм); j — жесткость зажимного устройства, Н/мм (в среднем j = 118 МН/м).
Если угол поворота ограничен и равен (рис. 2), то величину эксцентриситета определяют по формуле
W S1 j
e . 1 cos
Радиус цапфы эксцентрика можно определить, задаваясь ее
шириной:
r W ,
2b см
где b — ширина цапфы, мм; см — допускаемое напряжение на смятие, МПа ( см = 15…20 МПа).
1 5

Наружный диаметр эксцентрика можетбытьопределенизусловиясамоторможения.Приближенноонрассчитывается по формуле
D = (14…20)e.
Ширина рабочей части эксцентрика может быть определена из формулы
B 0,0175 WE ,
R 2см
где R—наружныйрадиусэксцентрика,
мм; E — модуль упругости материала эксцентрика, МН/м2 (Е = 1,96∙105 МН/м2).
Полученные размеры дискового экс- Рис. 2. Эксцентриковый центрика e, R, D, B необходимо согла-
зажим совать с ГОСТ 9061.
Величина усилия зажима, создаваемая непосредственно эксцентриком, определяется по формуле
W |
|
|
|
|
|
|
Qlcos 1 |
, |
||
|
D |
tg |
|
|
d |
tg |
|
esin( ) |
||
|
|
|
|
|
||||||
2 |
|
1 |
2 |
|
2 |
1 |
|
где Q — сила, приложенная к рукоятке эксцентрика, Н; l — плечо приложения силы, мм; 1 — угол трения эксцентрика с заготовкой, град ( 1 = 6…8°); 2 — угол трения в цапфе эксцентрика.
Наибольшее усилие зажима эксцентрик развивает при малых углах поворота, а наименьшее — при повороте на 90°. Это обстоятельство нужно учитывать в расчетах, беря наихудшие условия работы эксцентрика.
Цанговые зажимные устройства
Цанги представляют собой разрезные пружинящие гильзы, материал которых работает либо на растяжение, либо на сжатие. Угол конуса цанги 30…40°. Цанги обеспечивают концентричность установки в пределах 0,02…0,05 мм.
При закреплении заготовки в цанговом устройстве усилие затяжки расходуется на создание усилий зажима и упругую деформацию лепестков цанги.
1 6

Величина усилия зажима, необходимого для надежного закрепления в цанге, может быть рассчитана по формуле
Wk M2 P2 , f r2
где k — коэффициент запаса; f — коэффициент трения между заготовкой и цангой; M—моментсил резания, воспринимаемый цанговым устройством, Н∙мм; r — радиус базовой поверхности заготовки, мм; P — осевая сила, сдвигающая заготовку, Н.
При выполнении поверочного расчета для универсального цангового зажима, зная величину силы затяжки цанги, можно определить создаваемую силу закрепления заготовки по следующим формулам:
— без осевого упора
W |
Q |
, |
|
tg( )
где Q — сила затяжки цанги, Н; 2 — угол при вершине конуса цанги; — угол трения между цангой по конической поверхности и корпусом;
— при наличии осевого упора
W |
Q |
, |
|
tg( ) tg 1
где 1 — угол трения между губками цанги и заготовкой. Найденное значение должно быть сопоставлено с потребным
усилием зажима при заданных режимах резания.
На практике большое распространение имеют комбинированные зажимы, включающие в свой состав винтовые зажимы, прихватные планки, рычаги и рычажные системы, а также клиновые и эксцентриковые элементы с гидравлическим и пневматическим приводами. Наиболее распространенные схемы и формулы для расчета комбинированных зажимных устройств представлены в прил. К.
4.8.3. Расчет приводов зажимных устройств приспособлений
Пневматический, гидравлический и пневмогидравлический привод
Схемы устройств приводов и расчетные формулы для определения усилия на штоке приведены в прил. Л. В указанных формулах приняты следующие обозначения:
1 7
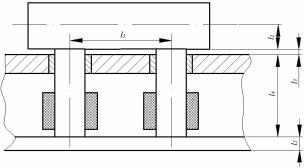
Рш, Р1ш — усилие на штоке, Н; D — диаметр цилиндра, мм;
Dв, Dж —диаметры соответственно пневматическогоигидравлического цилиндров в пневмогидравлическом приводе, мм;
N — сопротивление пружины возврата при крайнем рабочем положении, Н;
p — удельное давление сжатого воздуха или гидравлической жидкости в зависимости от привода, МПа;
pв, pж —удельное давление сжатоговоздухаигидравлической жидкости в пневмогидравлическом приводе, МПа;
— КПД;
d — диаметр штока, мм;
d0 —диаметропорнойшайбывдиафрагменном цилиндре,мм; d2 — диаметр штока пневмоцилиндра в пневмогидравличес-
ком приводе, мм.
Указанныев прил.Л формулы используются дляповерочных расчетов. При проектных расчетах находят необходимые размеры, по которымподбирают по [3, 5]ближайший больший размер привода. Для встроенных приводов размеры должны быть округлены по нормальному ряду диаметров. Усилие на штоке привода определяется по схеме закрепления с учетом влияния передаточных устройств и величины усилия зажима заготовки
(пп. 4.8.1 и 4.8.2).
Электромагнитные приводы
Расчет электромагнитных устройств ведется по схеме, представленной на рис. 3. При расчете учитываются геометрические размеры и электротехнические формулы.
Рис. 3. Схема магнитопровода электромагнитной плиты
1 8

Участками магнитопровода являются: l1, l2 — обрабатываемая заготовка;
l3 — зазор между заготовкой и магнитной плитой; l4 — высота сердечников плиты;
l5 — соединительная планка.
Расчет производится в следующей последовательности: 1. Определяется необходимая удерживающая сила Q:
Q Pрез ,
f
где Ррез — усилие резания, вызывающее сдвиг заготовки, кг; f — коэффициент трения между заготовкой и плитой (f = 0,1…0,15).
2.Определяется число пар полюсов перекрываемых заготовкой, исходя из ее размеров и конфигурации.
3.Определяется удерживающая сила, создаваемая одним полюсом в магнитной системе:
Q Q1 2n,
где n — число пар полюсов.
4. Подсчитываетсяплощадьпоперечногосечениясердечника.
25 106 Q1
Fc B2 ,
где В — магнитная индукция для материала, из которого изготовлен сердечник, гс.
5. Определяется общее сопротивление магнитопровода.
R |
l1 |
|
l2 |
... |
ln |
, |
|
|
|
||||
|
m1F1 |
|
m2F2 |
|
mnFn |
где l1, l2, …, ln —длина каждого участка магнитопровода, см; m1, m2, …, mn — магнитная проницаемость материала каждого участка; F1, F2, …, Fn — площадь поперечного сечения каждого участка, см2.
6.Определяетсяобщиймагнитныйпотоксучетом30%потерь.
Ф0,7BFc.
7.Рассчитывается количество ампервитков катушки.
IW ФR , 0,4
где I — сила тока, А; W — количество витков катушки.
1 9
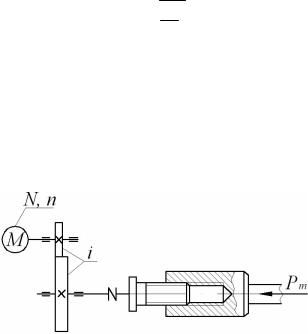
8. Определяется диаметр провода катушки.
d 4I ,
q
где q — допустимая плотность тока, А/мм2 (q = 3…5 А/мм2). Для стандартных магнитных плит, используемых на плоскошлифовальных станках, производится поверочный расчет, на основании которого решается вопрос о возможности вести обработку заготовок при заданных режимах резания. Если усилия магнитной плитынедостаточны, то уменьшаютрежимы резания.
Электромоторные приводы
Однаиз схемэлектромоторногоприводапредставленанарис. 4.
Рис. 4. Схема электромоторного привода
Величина усилия, создаваемого тягой электромоторного привода, определяется в зависимости от характера используемого приспособления.
При расчете электромоторного привода необходимо знать и учитыватьвлияние конструкции,передающейусилие отпривода к обрабатываемой заготовке.
Усилие тяги для указанной выше схемы определяется по формуле
Pт |
71620 |
|
N i |
, |
|
nrср |
tg( ) |
||||
|
|
|
где N—мощность электродвигателя,кВт;n—частотавращения двигателя, об./мин; rср — средний радиус резьбы, см; — КПД редуктора; i — передаточное отношение редуктора; — угол подъема резьбы винта, град; — угол трения в резьбе, град.
2 0