
3688
.pdf
где св и cR – коэффициенты аэродинамического сопротивления при перемещении частицы соответственно в вертикальном и радиальном направлениях.
Отсюда граница разделения δпри заданной вертикальной скорости потока υв составит:
|
3 |
k |
|
|
0 |
|
|
|
|
|
l2v2 |
|
|
|
м. |
(3.43) |
||
|
|
|
|
|
|
в |
|
|
|
|||||||||
4 |
ф м |
|
|
|
|
|
|
2 |
||||||||||
|
|
|
|
|
|
|
|
|
a |
|
|
|
||||||
|
|
|
g |
|
|
|
||||||||||||
|
|
|
|
|
|
|
l |
|
h |
|
ц |
|
|
|
|
|||
|
|
|
|
|
|
c |
c |
|
|
|
||||||||
|
|
|
|
|
|
|
|
|
|
|
|
|
|
|
|
|||
|
|
|
|
|
|
|
|
в |
|
|
|
|
R |
|
|
При преобразованиях этого выражения за относительную скорость υ0 в числе Рейнольдса следует принимать
при определении св – скорость витания υвит принимают по формуле (3.20); при определении cR – радиальную составляющую скорости частицы рассчи-
тывают по формуле (3.38).
Анализ поперечно-поточной центробежной зоны (см. рис. 3.1, з) по четырем условиям разделения показывает, что здесь удовлетворяются первое и четвертое условия, а второе и третье, как и в горизонтально-поточной гравитационной зоне, выполняются лишь частично.
В заключение необходимо отметить, что формулы (3.9), (3.10), (3.11), (3.15), (3.17), (3.18), (3.19), (3.21), (3.22), (3.23) и (3.24) устанавливают связь между границей разделения δ, плотностью сепарируемого материала рм и воздуха (газа) р0 кинематической вязкостью v, схемой и размерами h, l, R,зон разделения, а также скоростью воздуха (газа) υв, υRи ускорением g, ац частицы в сепараторах любых конструкций. Недостатком формул является то, что из-за сложности вопросов физики двухфазного потока в них не учтен ряд факторов, оказывающих существенное влияние на границу разделения и точность сепарации.
Точность разделения
Точность разделения является одним из важнейших показателей, характеризующих работу сепаратора. Она зависит от рода обрабатываемого, материала, его влажности, формы частиц, концентрации, т. е. стесненности потока, непостоянства границы разделения в различных точках объема зоны, местных турбулентных завихрений в потоке и потерь напора при его вращении, требуемой дисперсности выдаваемого продукта, конструктивной схемы, т. е. типа сепаратора и ряда других факторов.
Видеальных условиях сепарируемый материал должен был бы точно разделяться на фракции (классы) по границам разделения. Если, например, фракций две, то тонкая должна состоять только из частиц, размер которых меньше границы разделения, а грубая - из частиц, размер которых больше границы разделения. Частиц же, размер которых равен границе разделения, в обеих фракциях должно быть поровну.
Вреальных условиях такое точное разделение получить невозможно и всегда тонкий продукт оказывается «загрязненным» крупными частицами, что
81
ухудшает его технологические качества, а грубый продукт содержит значительное количество мелких частиц, что отражается на экономичности. Точность разделения в сепараторах может характеризоваться различными показателями. Наиболее употребительны коэффициент полезного действия, эффективность и кривая классификации.
Коэффициент полезного действия – отношение веса одного из продуктов (обычно тонкого) к весу продукта такого же состава, содержащегося в исходном материале:
|
qт |
100 |
c |
|
a b |
100%, |
(3.44) |
qт.н |
|
|
|||||
|
|
a c b |
|
где qт и qт.и – соответственно производительность по тонкому продукту и продукту такого же состава, находящемуся в исходном материале кг/ч;
а, b, с – содержание «минуса»* соответственно в исходном материале, грубом и тонком продуктах, % (по весу).
С помощью КПД легко определить производительность сепаратора. Однако формула КПД не учитывает загрязнения тонкого продукта крупными частицами и может получиться, что сепаратор при высоком к.п.д. будет выдавать продукт непригодный по техническим условиям.
Под «минусом» понимается фракция, размер частиц в которой меньше границы разделения, а под «плюсом» – больше границы разделения.
Эффективность, или степень разделения, определяется по формуле:
q` |
|
G |
|
c a a b |
|
||
|
т |
|
т |
100 10 |
|
% |
(3.45) |
q |
G |
a 100 a c b |
|||||
н |
|
н |
|
|
|
|
где q´т и q´и – производительность по «минусу» соответственно в тонком продукте и исходном материале;
G´ти G´и – производительность по «плюсу» соответственно в тонком продукте и исходном материале.
Этот показатель хорошо отражает точность разделения, учитывая «загрязнение» тонкого продукта крупными частицами. Однако с помощью эффективности нельзя определить, какое количество тонкого продукта выдает сепаратор.
По промышленным данным КПД сепараторов в среднем составляет 65% (максимум 80%), а эффективность в среднем – 55% (максимум 70%).
Наиболее полно работу сепаратора характеризует кривая классификации, которая строится на основании экспериментального исследования по данным дисперсионного анализа
Конструкции воздушных сепараторов
В технике разделения сыпучих материалов на фракции применяют различные типы гравитационно-центробежных сепараторов, простейшим из кото-
82
рых, как указывалось выше, является циклон. Однако циклон используют чаще не для сепарации, а для отделения частиц из несущего потока. Устройство сепараторов несколько сложнее циклона. Гравитационно-центробежные сепараторы можно условно разделить на два класса: воздушно-проходные и воздуш- но-замкнутые (циркуляционные).
Воздушно-проходные сепараторы
Отличительной особенностью проходных сепараторов является то, что исходный материал в них поступает в виде аэросмеси, а тонкий продукт вместе с воздухом (газом) отводится в автономные пылеосадительные устройства, например циклон и фильтр.
Проходные сепараторы обычно применяются с вентилируемыми мельницами, из которых измельченный материал выносится воздушным потоком, например с шахтными, аэробильными, пневматическими, молотковыми, роли- ко-маятниковыми и струйными, а также с мельницами относительно невысокой производительности, например вибрационными. В цементной промышленности эти сепараторы применяются довольно редко.
Главным недостатком проходных сепараторов является повышенное энергопотребление на пневмотранспорт материала из мельницы в сепаратор.
По принципу действия, т.е. принципиальной схеме основной зоны разделения, проходные сепараторы можно разделить на следующие подгруппы:
1.Сепараторы, в которых разделение материала происходит преимущественно под действием силы тяжести Представителем этой подгруппы является, например, шахтный сепаратор, применяемый в установках с шахтными мельницами.
2.Сепараторы, в которых поток воздуха закручивается с помощью тангенциально установленных направляющих лопаток. Здесь разделение происходит под действием центробежной силы в комбинации с силой тяжести (см. рис. 3.1, е и з).
3.Сепараторы, в которых поток воздуха закручивается с помощью вращающихся крыльчаток (ротора). Здесь разделение происходит главным образом поддействием центробежной силы (см. рис. 3.1, с и з).
Воздушно-проходной сепаратор с неподвижными направляющими лопатками (рис. 3.3). Он состоит из корпуса 2, внутреннего конуса — циклона 3, направляющих поворотных створок 4, механизма управления створками 6, броневого штуцера-наконечника, штуцеров 1, 5, 7 и сборника 9. Пылевоздушная смесь поступает в сепаратор через штуцер 1. В корпусе 2 скорость потока резко уменьшается, и наиболее крупные частицы выпадают в сборник 9. Поднимаясь вверх, поток через створки 4 попадает в циклон 3. Проходя створку, он приобретает вращательное движение. Под действием центробежных сил в циклоне из потока также выделяются более крупные частицы, которые выпадают в вершину конуса и выводятся через штуцер-наконечник 8. Самые мелкие частицы уходят с потоком газа через выводной штуцер 5 на дальнейшую обработку, ча-
83
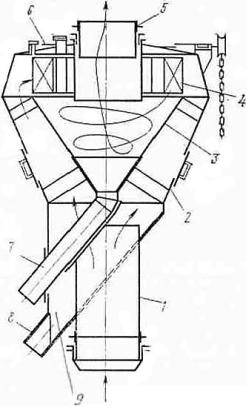
ще всего в циклонах или фильтрах.
В воздушно-проходном сепараторе можно разделить материал на три фракции: крупную, выходящую через штуцер 8, среднюю – через штуцер 7 и мелкую – через штуцер 5. В описанном сепараторе средняя фракция смешивается с крупной, однако при необходимости ее легко собрать отдельно. Для этого штуцер 7 необходимо вывести из корпуса 2. Граница раздела фракции регулируется степенью открытия створок, т. е. входной скоростью потока в циклоп.
Рис. 3.3. Воздушно-проходной сепаратор с неподвижными лопатками:
1 – штуцер для отвода крупной фракции; 2 – корпус; 3 – циклон; 4 – створки; 5 – штуцер выводной; 6 – створки; 7 – штуцер; 8 – штуцер-наконечник;
9 – сборник
Такие сепараторы не поддаются строгому расчету. Многолетняя практика эксплуатации и многочисленные исследования этих сепараторов привели к установлению зависимости между размерами отдельных элементов сепаратора (рис. 3.4). Основным конструктивным размером сепаратора, определяющим все остальные, является его диаметр. Последний зависит от производительности сепаратора и размера частиц готового продукта. Выбор диаметра сепаратора производится в зависимости от напряженности его объема, по газу-носителю:
k |
|
V |
, |
(3.46) |
|
||||
0 |
V |
|
||
|
|
c |
|
где V– объем газа, проходящего через сепаратор; Vс– объем сепаратора.
84
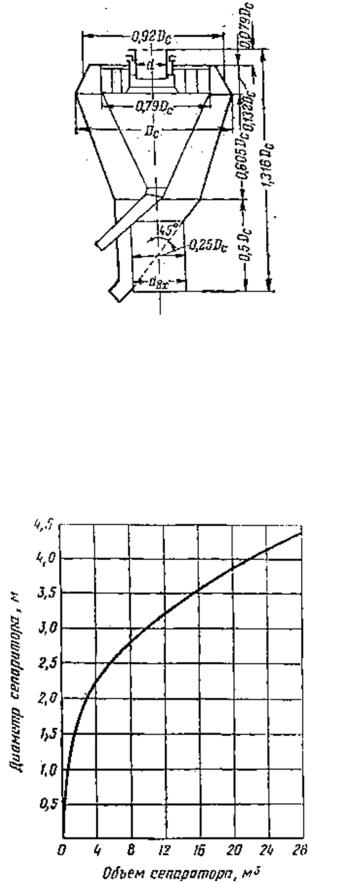
Рис. 3.4. Относительные размеры Воздушно-проходных сепараторов
В зависимости oт границы раздела фракций рекомендуются следующие значения напряженности объема сепаратора:
Объем, сепаратора определяют по формуле Vc=V/k0
Зная объем сепаратора, по графику (рис. 3.5) находят его диаметр, а по диаметру, пользуясь рис. 3.4, все остальные размеры.
Рис. 3.5. График зависимости диаметра воздушно-проходного сепаратора от объема
85
В табл. 3.1 приведены размеры сепараторов, рекомендуемые нормами расчета и проектирования.
|
|
|
|
|
Таблица 3.1. |
|
Размеры рекомендуемых сепараторов |
||||
|
|
|
|
|
|
№ сепаратора |
|
Диаметр, мм |
|
Объем сепаратора, |
|
сепаратора |
|
патрубков |
|
м3 |
|
1 |
1900 |
350 |
400 |
- |
2,4 |
2 |
2250 |
500 |
600 |
- |
4,2 |
3 |
2500 |
600 |
750 |
- |
5,5 |
4 |
2850 |
700 |
850 |
1000 |
8,4 |
5 |
3000 |
800 |
950 |
1150 |
10,0 |
6 |
3420 |
800 |
950 |
1150 |
14,3 |
7 |
4000 |
950 |
1100 |
1140 |
22,0 |
Воздушно-проходной сепаратор с вращающимися отбойными лопатками. Представителем этой группы является, например, отбойно-вихревой сепаратор Специального конструкторского бюро ВНИИ новых строительных материалов (рис. 3.6). Основная зона разделения в этом противоточном сепараторе выполнена по схеме (см. рис. 3.1. е). Воздух с исходным материалом по патрубку 1 поступает в нижнюю часть сепаратора, где поток резко расширяется и из него выпадают наиболее крупные частицы. Далее поток воздуха с материалом поднимается вверх и закручивается вращающимся ротором 2 с прямыми лопатками. Под действием центробежной силы средние частицы отбрасываются.
К периферии и по стенке кожуха 3 сползают вниз, в патрубок 4, где, смешиваясь с крупными частицами, образуют грубый продукт. В верхней части находится основная зона разделения. Здесь окружная скорость лопаток ротора, а, следовательно, и потока наибольшая и поэтому лишь для самых тонких частиц центробежная сила оказывается меньше силы давления потока. Эти частицы выносятся воздухом в улитку 5, а затем в пылеосадитель. Ротор приводится во вращение электродвигателем 6 через клиноременную передачу 7.
Регулирование границы разделения осуществляется за счет изменения скорости вращения ротора или дросселированием воздушного потока на выходе из сепаратора. Последний способ менее выгоден, так как снижает производительность.
Применяется этот сепаратор главным образом с вибрационными и струйными мельницами для выдачи тонкого продукта, характеризуемого остатком от 15 до 0% на сите № 0063, но он может выдавать и более тонкие продукты. Диаметр выпускаемых сепараторов этого типа 0,5–1,2 м, расход воздуха составляет соответственно от 0,8 до 7 тыс. м3/ч.
Преимущество проходных сепараторов 3-й подгруппы по сравнению с сепараторами 2-й подгруппы заключается в том, что точность разделения здесь более высокая, а также они могут выдавать более тонкие продукты. Однако се-
86

параторы 2-й подгруппы более просты по конструкции, и поэтому они получили большее распространение.
Рис. 3.6. Проходной отбойно-вихревой сепаратор:
1, 4 – патрубки; 2 – ротор вращающийся; 3 – кожух; 5 – улитка; 6 – электродвигатель; 7 – передача клиноременная
Циркуляционные сепараторы
Отличительной особенностью циркуляционных сепараторов является то, что в них вентилятор для создания воздушного потока, распылитель для образования пылевоздушной смеси, сепарирующие и пылеосадительные устройства объединены в одном агрегате. Исходный материал в сепараторы этой группы, как правило, подается механическим путем.
Циркуляционные сепараторы по сравнению с проходными имеют в 2–4 раза меньшее энергопотребление, более удобны и точность разделения в них несколько выше. Благодаря этим преимуществам циркуляционные сепараторы получили преимущественное распространение в высокопроизводительных установках промышленности строительных материалов, в частности при производстве цемента, при обогащении полезных ископаемых и др.
По принципу действия, т.е. принципиальной схеме основной зоны разделения, циркуляционные сепараторы можно разделить на следующие подгруппы.
87
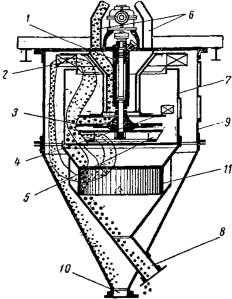
1. Сепараторы с разбрасывающим диском (или дисками) без крыльчатки,
в которых разделение материала происходит в основном под действием силы тяжести и в небольшой степени центробежной силы. Принципиальная схема основной зоны разделения этих сепараторов приведена на рис.3.1 г.
2. Сепараторы с разбрасывающим диском и крыльчаткой, в которых разделение материала происходит под действием центробежной силы, направленной перпендикулярно или под углом к радиальной составляющей скорости потока. Принципиальная схема основной зоны разделения этих сепараторов приведена на рис. 3.1. Представителями этой подгруппы являются, например, сепараторы НИИ Цементного машиностроения, выпускаемые заводом «Волгоцеммаш», отечественный сепаратор «Механобр».
Схема сепаратора НИИ Цементного машиностроения показана на рис.3.7. На вертикальном вращающемся валу 1 укреплены вентиляторное колесо 2, тарельчатый питатель-диск 3, верхняя 4 и нижняя 5 крыльчатки. Исходный материал через загрузочный патрубок 6 подается на диск и веером сбрасывается с него под действием центробежной силы. Происходит первый отбор наиболее крупных частиц, которые под действием силы тяжести выпадают вниз или центробежной силой отбрасываются к стенке внутреннего кожуха 7 и сползают по ней в патрубок выхода грубого продукта 8. Засасываемый вентиляторным колесом 2 и нижней крыльчаткой 5 воздух пересекает веер материала, подхватывает средние и мелкие частицы и увлекает их вверх через основную зону разделения, а, выполненную по схеме рис.3.1з. Здесь под действием центробежной силы проходит отделение средних частиц, которые также отбрасываются к стенке внутреннего кожуха 7 и сползают вниз в патрубок 8 выхода грубого продукта.
Рис. 3.7. Циркуляционный сепаратор НИИ Цементного машиностроения: 1 – вал; 2 – колесо вентиляторное; 3 – питатель-диск тарельчатый;
4,5 – крыльчатка верхняя и нижняя; 6–патрубок загрузочный; 7,9 – кожухи внутренние; 8 – патрубок разгрузочный;10 – патрубок выхода тонкого продукта; 11 – жалюзи
88
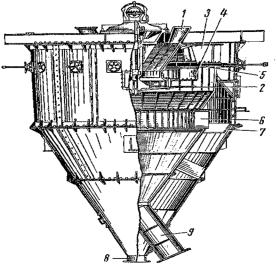
Воздух с мелкими частицами вентиляторным колесом 2 направляется в полость между внутренним 7 и наружным 9 кожухами, которая является зоной осаждения и выполнен по схеме (рис.3.7). Здесь окружная скорость воздушного потока максимальна и поэтому центробежная сила, действующая на частицы, также имеет наибольшее значение. Под ее влиянием частицы отбрасываются к периферии, ударяются о стенку, и, теряя живую силу, по спиральной траектории сползают вниз, в патрубок выхода тонкого продукта 10. Очищенный воздух, замыкая цикл, возвращается между направляющими лопатками жалюзи 11 во внутренний кожух и продувает сползающий вниз-грубый продукт, извлекая из него случайно захваченные тонкие частицы. Таким образом, на выходе из жалюзи имеется вспомогательная зона разделенияb выполненная по схеме рис. 3.1е.
Регулирование границы разделения осуществляется за счет изменения радиального положения лопастей крыльчатки 4 (выдвигание их повышает дисперсность тонкого продукта) либо за счет уменьшения количества лопастей, что загрубляет продукт.
Диаметр сепараторов, выпускаемых «Волгоцеммашем», 2,8; 3,2; 4 и 5 м. Удельное энергопотребление находится в пределах 1,35– 9 кВт, а удельная нагрузка составляет 1,2– 1,5 т/·м2
2. В сепараторах с разбрасывающим диском и крыльчаткой разделение материала происходит под действием центробежной силы, направленной навстречу радиальной составляющей скорости потока. Принципиальная схема основной зоны разделения этих сепараторов приведена на рис.3.1, е.
Представителями этой подгруппы являются, например, сепаратор КЦ5000, разработанный специальным конструкторским бюро ВНИИ новых строительных материалов (рис 3.8). Исходный материал из загрузочного патрубка 1 поступает на разбрасывающий диск 2, который находится на одном валу с вентиляторным колесом 3 и сепарирующей крыльчаткой 4.
Рис. 3.8. Циркуляционный противоточный сепаратор КЦ-5000:
1 – патрубок загрузочный; 2 – диск-разбрасывающий; 3 – колесо вентиляторное; 4 – крыльчатка сепарируящая; 5 – заслонка шиберная; 6 – жалюзи;
7 – щиток кольцевой; 8,9 – патрубки
89
Последовательность разделения и осаждения материала в циркулирующем воздушном потоке здесь такая же, как в описанном ранее сепараторе НИИЦементного машиностроения. Принципиальное отличие заключается в том, что основная зона разделения, а выполнена по противоточной схеме (см. рис.3.1, ё). С этой целью сепарирующая крыльчатка 4 сделана высокой, так что поток воздуха с материалом может пройти через нее только в горизонтальном направлении. Регулирование границы разделения осуществляется на ходу за счет дросселирования воздушного потока на входе в вентилятор с помощью шиберных заслонок 5.
В сепараторе для повышения эффективности вспомогательной зоны разделения в направляющие лопатки жалюзи 6 сделаны подвижными и могут быть установлены на требуемый угол с помощью механизма поворота. Кроме того, напротив жалюзи поставлен кольцевой щиток 7, предохраняющий опускающийся по стенке тонкий продукт отвлекающего воздействия воздушного потока. В сепараторе тонкий продукт выходит через патрубок 8, а грубый – через патрубок 9. Удельное энергопотребление в сепараторе находится на уровне 1.45 кВт/ч (при получении продукта), характеризуемого остатком 5% на сите № 0075 удельная нагрузка – до 2,6 т/ч· м2.
Главным преимуществом циркуляционных сепараторов 3-й подгруппы является то, что эффективность разделения здесь более высокая, так как наиболее полно удовлетворяются четыре условия разделения.
Конструктивно циркуляционные сепараторы различных подгрупп и типов отличаются дуг от друга соотношением основных размеров в зонах разделения и осаждения, дополнительными устройствами в виде различных крыльчаток, отражателей, стабилизаторов и завихрителей потока, устройствами для регулирования границы разделения, центральной или боковой загрузкой исходного материала на вращающийся диск.
Большие отличия имеют конструкции механизмов привода. В качестве двигателей применяют электродвигатели постоянного тока с изменяемым для регулирования границы разделения числом оборотов, или, если электродвигатели асинхронные, то устанавливают многоступенчатые коробки скоростей, а в последнее время – механические вариаторы скорости. При небольшой установочной мощности применяют клиноременные передачи со ступенчатыми шкивами.
Теоретически и экспериментально показано, что для регулирования границы разделения полезно иметь постоянное число оборотов вентиляторного колеса и изменяемое число оборотов сепарирующей крыльчатки с разбрасывающим диском. Это влечет за собой повышение точности разделения и снижение общей установочной мощности и удельных энергозатрат. С этой целью некоторые типы сепараторов выполнены с двумя различными приводами и автономными электродвигателями на вентиляторном колесе и сепарирующей крыльчатке, например, сепаратор «Фив-Лиль» (Франция), установленный на одном из наших цементных заводов.
90