
3375
.pdf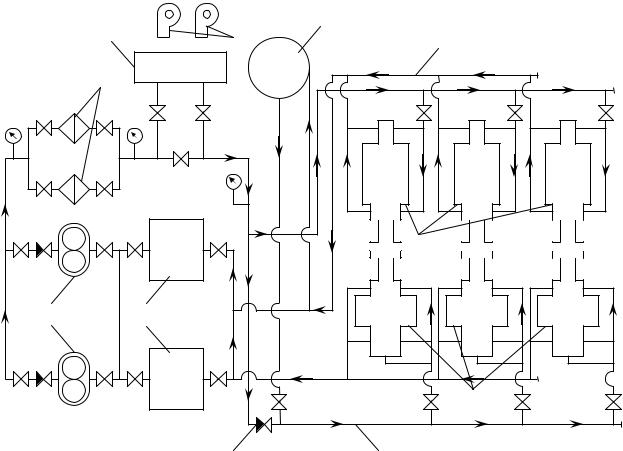
|
3 |
9 |
4 |
|
5 |
||
|
|
||
|
8 |
|
|
|
|
|
10 |
1 |
|
2 |
|
|
|
|
11 |
|
|
7 |
6 |
|
|
Рис. 4.1. Схема системы маслоснабжения НПС: |
|
|
1 – шестеренный насос; 2 – маслобак; 3 – аппарат воздушного охлаждения |
||
масла; 4 – бак аккумулирующий; 5 – трубопровод отводящий; 6 – трубопровод подводящий; |
|||
7 – клапан обратный; 8 – маслофильтры; 9 – вентиляторы; 10 – привод насоса; 11 - насосы |
Таблица 4.1.
Основные показатели турбинного масла ТП-22С
Наименование показателя |
Значение |
|
Кинематическая вязкость, мм2/с, при температурах: |
|
|
50 °С |
20 |
– 23 |
40 °С |
28,8 |
– 35,2 |
Температуры: |
|
|
вспышки в открытом тигле, не ниже |
186 |
|
застывания, не выше |
-15 |
|
Плотность при 20 °С, кг/м3, не более |
900 |
Система смазки магистральных насосных агрегатов состоит из рабочего и резервного масляных насосов, маслопроводов, оборудованных фильтрами очистки масла, рабочего и резервного маслобаков, аккумулирующего маслобака,
30

маслоохладителей и запорной арматуры. Масло с основного маслобака забирается работающим маслонасосом шестеренчатого типа (например, ШФ8-25А), проходит через маслофильтр, подается на маслоохладители, откуда поступает на смазку подшипников магистральных агрегатов и на заполнение аккумулирующего маслобака. В случае отключения маслонасосов масло под действием гидростатического давления из аккумулирующего маслобака подается на смазку подшипников.
Воздух в маслоохладитель подают центробежным нагнетателем 9. Обдувая трубный пучок, воздух охлаждает двигающееся по трубкам масло. Температуру охлаждения масла контролируют и регулируют терморегулятором. Для обеспечения насосного агрегата смазкой во время аварийного отключения электроэнергии предусмотрен маслобак 4 на высоте не менее 3 м от оси насосных агрегатов.
Температура масла в общем коллекторе перед поступлением на магистральные насосные агрегаты должна находиться в интервале от +20ºС до +70ºС, при превышении температуры масла на выходе из маслоохладителя более +70ºС автоматически включаются дополнительные вентиляторы обдува. При низкой температуре масла допускается работа маслосистемы, без маслоохладителей.
Маслоустановки выполняют со 100%-м резервом и предусматривают как параллельную, так и последовательную работу маслоохладителей. Расход и давление масла регулируют путем перепуска части жидкости с нагнетания на всасывание по обводной линии.
4.1. Выбор масляных насосов
Исходными данными являются: плотность масла ρ, кг/м3, при температуре 293 К (принимается по исходным данным прил. 2 равной плотности нефти); температуры масла на входе t1М и выходе t2М из подшипников, ºС (принимаются по выражениям t1М =t+15 ºС, t2М =t+55 ºС, где t – температура нефти); мощность двигателя NДВ - принимается по данным типа двигателя из табл. П.7.1 или П.7.2 прил. 7 для каждого варианта, кВт; КПД подшипников ηП (рекомендуется принять ηП=0,99).
Определяем энтальпию масла i1М ,i2М , кДж/кг, до и после подшипников при известных температурах t1М и t2М :
i |
|
0,0536 |
t |
t |
995 , |
(4.1) |
||
|
|
|
||||||
|
||||||||
1М |
|
|
1М |
1М |
|
|
31

i |
М |
|
0,0536 |
t |
2М |
t |
2М |
995 . |
(4.2) |
||
|
|
|
|||||||||
2 |
|
|
|
|
|
|
Подача масла к насосным агрегатам обеспечивает не только смазку подшипников, но и их охлаждение. Необходимый расход масла GМ , кг/с, при этом может быть найден из уравнения теплового баланса по формуле
G |
n |
|
N |
|
1 П |
|
, |
(4.3) |
А |
ДВ |
|
|
|||||
М |
|
|
|
|
|
|||
|
|
|
|
i2М i1М |
|
|
где nА - количество работающих насосных агрегатов, шт. Определяем подачу маслонасоса QМ , м3/ч, по формуле
QМ |
|
3600GМ |
. |
(4.4) |
|
||||
|
|
|
|
По полученному значению подачи маслонасоса QМ и с учетом допустимого давления в маслосистеме (не более 0,4 МПа) по прил. 4 выбираем насос и выписываем его характеристики.
К установке принимаем два насоса, один из которых резервный.
4.2. Пересчет характеристик шестеренного насоса
Шестеренные насосы относятся к роторным насосам объемного типа, в которых жидкая среда перемещается в результате периодического изменения объема занимаемой ею полости, попеременно сообщающейся со входом и выходом насоса.
Характеристика шестеренных насосов описывается уравнениями вида
Q Q |
|
a |
P P |
вш , |
(4.5) |
ш |
ш |
ш |
|
|
|
d0 |
d1P d2P2 , |
(4.6) |
где Qш ,Pш - характерные подача и давление, развиваемые шестеренным насосом; aш ,вш ,d0 ,d1,d2 - эмпирические коэффициенты.
Необходимо иметь в виду, что в области малых давлений Р Pш зави-
симость подачи от Р является линейной вш 1 , а при Р Pш - нелинейной, т.е.
вш 1.
При изменении вязкости перекачиваемой жидкости приближенные значения подачи и мощности шестеренного насоса необходимо подсчитывать по формулам:
32

Q |
Q |
1 1 |
|
|
. |
|
|
|
(4.7) |
||||||||
|
|
|
|
|
|
|
|||||||||||
1 |
|
|
|
|
|
О |
1 |
|
|
|
|
|
|||||
|
|
|
О |
|
|
|
|
|
|
|
|||||||
|
|
|
|
|
|
|
О |
|
|
|
|
|
|
|
|
||
N |
|
N |
|
|
|
|
1 |
|
|
|
|||||||
1 |
1 |
|
|
|
|
|
, |
(4.8) |
|||||||||
|
|
|
|
||||||||||||||
|
|
О |
|
|
|
|
|
|
|
|
|
|
|
||||
|
|
|
|
|
|
|
|
|
|
|
|
|
где Q, N, η, О , - соответственно подача, мощность, общий и объемный КПД, кинематическая вязкость перекачиваемой жидкости.
В тех случаях, когда в комплектацию насоса не входит электродвигатель, последний подбирается по необходимой мощности электродвигателя Nн :
Nн kзN , |
(4.9) |
где kз - коэффициент запаса, величина которого зависит от потребляемой мощности насоса N, определяемой по формуле (3.36): при N<20 кВт kз =1,25; при
20≤N<50 кВт kз =1,2; при 50≤N<300 кВт kз =1,15; при N≥300 кВт kз =1,1.
4.3.Расчет системы охлаждения масла
Внастоящее время на нефтеперекачивающих станциях широко распространены агрегаты воздушного охлаждения масла. На рис. 4.1 представлена схема системы маслоснабжения с воздушным охлаждением.
Находим массовый расход масла G, кг/с, в системе с учетом принятого насоса:
G |
Q |
. |
(4.10) |
|
3600 |
||||
|
|
|
Количество тепла, Q, кВт, которое необходимо отвести от масла, находим по формуле
Q G i2М i1М . |
(4.11) |
Примем давление воздуха, идущего в систему охлаждения, равным нормальному атмосферному (101325 Па). В таком случае плотность воздуха В , кг/м3, используемого для охлаждения, определяется по формуле
|
|
|
|
ТН |
, |
(4.12) |
|
|
|
||||
|
В |
|
Н ТВ |
|
33
где Н - плотность воздуха при нормальных условиях ( Н =1,293 кг/м3); ТН – температура при нормальных условиях (ТН =273 К); ТВ – температура воздуха (принимается на 5ºС меньше температуры масла на входе в систему t1М ), К.
Определяем расход воздуха QВ , м3/ч, необходимого для охлаждения масла
Q |
|
|
3,6 106Q |
|
|
, |
(4.13) |
||||
c |
|
|
|
t |
|
t |
|
|
|||
В |
РВ |
В |
вых |
вх |
|
|
|||||
|
|
|
|
|
|
|
|
||||
где cРВ - массовая теплоемкость воздуха (cРВ =1004 Дж/(кг·К); tвых ,tвх |
- темпера- |
туры воздуха на выходе и входе в калорифер соответственно, ºС (принимаются равными tвых =t2М -30 ºС, tвх =t1М -5 ºС).
По найденному расходу воздуха для охлаждения масла QВ, по прил. 6 подбираем вентилятор центробежный типа Ц4-70 и выписываем его основные параметры.
Определяем необходимую площадь живого сечения калорифера f, м2,
f |
QВ В |
, |
(4.14) |
|
|||
|
w |
|
где w – весовая скорость воздуха в калорифере, принимаемая в интервале 6÷10
кг/(м2·с).
По прил. 6, зная значение f, м2 (живое сечение по воздуху), определяем тип калорифера и выписываем его характеристики.
В случае, когда полученное по формуле (4.14) живое сечение больше табличных значений, необходимо устанавливать несколько одинаковых калориферов.
Находим фактическую весовую скорость воздуха в калорифере wФ ,
кг/(м2·с),
w w |
|
f |
. |
(4.15) |
|
|
|||
Ф |
nК |
fВI |
|
|
|
|
где nК - число калориферов, шт.
Определяем линейную скорость масла в калорифере М , м/с,
|
М |
|
G |
. |
(4.16) |
|
|||||
|
|
nК М fМ |
|
Определяем число Рейнольдса при течении масла в калорифере ReМ
34
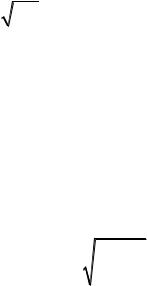
Re |
М |
|
М d |
, |
(4.17) |
|
|
||||||
|
|
|
М |
|
||
|
|
|
|
|
где М - кинематическая вязкость масла (принимаем 20 мм2/с); d – диаметр
трубок для теплоносителя, м.
Определяем коэффициент кинематической вязкости масла по формуле:
М |
|
156,6 |
1 0,00047ТМср , |
||
|
|
М |
|||
|
|
|
|
|
М , Вт/(м·К),
(4.18)
где ТМср – средняя температура масла в калорифере, определяется как среднее
арифметическое температур на входе и выходе из калорифера, К. Определяем теплоемкость масла сРМ , Дж/(кг·К) по формуле
сРМ |
|
31,56 |
|
762 3,39ТМср . |
(4.19) |
|
|
|
|
||||
|
|
|||||
|
|
|
М |
|
Находим число Пекле PeМ при течении масла в трубках калорифера по формуле:
PeМ |
|
МсРМ М d |
. |
(4.20) |
|
||||
|
|
М |
|
Определяем полный коэффициент теплопередачи K, Вт/(м2·К) в калорифере по формуле:
K 1,61 |
М |
3 Pe |
|
d |
. |
(4.21) |
|
|
|||||
|
d |
М l |
|
где l – длина трубок для теплоносителя, м.
Определяем фактическую теплоотдачу в трубках калориферов QФ , кВт, по формуле:
QФ KnК F ТМср ТВср 10 3, |
(4.22) |
где ТВср - средняя температура воздуха в калорифере, определяется как среднее
арифметическое температур на входе и выходе из калорифера, К.
Необходимо сопоставить значения, полученные по формулам (4.11) и (4.22). При выполнении неравенства QФ>Q расчет считается законченным, в противном случае необходимо осуществить перерасчет.
35

К установке принимают два калорифера и вентилятора (один рабочий, другой резервный).
5.Примеры расчетов
5.1. Расчет рабочего колеса
Известны следующие параметры насоса: подача Q=1250 м3/ч (1250/3600=0,347 м3/с), напор Н=260 м, частота вращения n=3000 об/мин
(мин-1), плотность перекачиваемой среды ρ=700 кг/м3.
Необходимо рассчитать основные параметры рабочего колеса насоса. Определяем коэффициент быстроходности nS , об/мин, по формуле (2.1):
nS 3,65 |
n Q |
3,65 3000 |
0,347 |
|
99,7 об/мин. |
|||
3 |
3 |
|
||||||
|
H |
4 |
|
|
260 |
4 |
|
|
Следовательно, по классификации колесо нормальное. Находим объемный КПД по формуле (2.2):
1 |
|
|
|
|
|
2 |
|
1 |
|
|
|
|
|
|
|||||
О |
|
|
|
|
= 1 0,68 99,7 |
3 |
|
0,969. |
|
|
|
2 |
|
||||||
1 0,68n |
|
|
|
|
|
|
|
|
|
3 |
|
|
|
|
|||||
S |
|
|
|
|
|||||
|
|
|
|
|
|
|
|
|
Определяем условный диаметр живого сечения входа в рабочее колесо, называемый приведенным диаметром на входе D1П , м, по формуле (2.3):
|
|
D |
4,253 |
Q |
|
4,253 |
0,347 |
0,207 м. |
|
|||
|
|
|
|
|
||||||||
|
|
1П |
|
n |
|
|
3000 |
|
|
|||
|
|
|
|
|
|
|
|
|||||
Находим гидравлический КПД Г |
по формуле (2.4): |
|
||||||||||
|
|
0,42 |
|
|
|
|
0,42 |
0,909. |
||||
Г |
1 |
|
|
|
1 |
|
||||||
lg 1000D1П 0,172 2 |
|
|
lg 1000 0,207 0,172 2 |
Принимая МЕХ =0,93, находим полный КПД насоса по формуле (2.5):
О Г МЕХ 0,969 0,909 0,93 0,819.
Находим мощность на валу насоса N, кВт, по формуле (2.6):
36
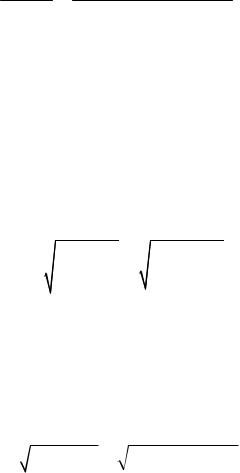
N gHQ 700 9,81 260 0,347 756,8 кВт.
1000 |
1000 0,819 |
Определяем крутящий момент на валу насоса М при рабочем режиме по формуле (2.7):
|
M 9578 |
N |
9578 |
756,8 |
2416,21 Н·м=241621 Н·см. |
|
|||||||||
|
|
|
|
|
|
||||||||||
|
|
n |
3000 |
|
|
|
|
|
|
|
|||||
Принимая |
значение |
|
допустимого |
|
|
напряжения |
кручения |
||||||||
ДОП =1500 Н/см2, находим диаметр вала насоса dВ |
по формуле (2.8): |
|
|||||||||||||
|
|
|
|
|
|
|
|
|
|
|
|
||||
|
dВ 3 |
M |
|
3 |
241621 |
|
|
9,3см. |
|
||||||
|
|
|
|
|
|||||||||||
|
|
|
|
|
0,2 ДОП |
0,2 1500 |
|
Диаметр ступицы колеса dСТ определяем по формуле (2.9):
dСТ (1,2 1,4)dВ 1,3 9,3 12,09см≈12 см.
Диаметр входа в колесо D0 определяем по формуле (2.10):
D0 D12П dВ2
0,2072 0,122 0,239м.
Определяем длину ступицы lСТ по формуле (2.11):
lСТ (1 1,5)dСТ 1,3 12 15,6 см.
Коэффициент быстроходности в рассматриваемом примере nS 180, сле-
довательно, диаметр входа на рабочие лопасти D1 определяем по формуле (2.12):
D1=0,8·0,239=0,1912 м.
Находим окружную скорость на входе в каналы рабочего колеса u1 по
формуле (2.14): |
|
|
|
|
|
u |
D1n |
|
3,14 0,1912 3000 |
30,03м/с. |
|
60 |
60 |
||||
1 |
|
|
Определяем скорость входа в рабочее колесо с1 по формуле (2.15):
37
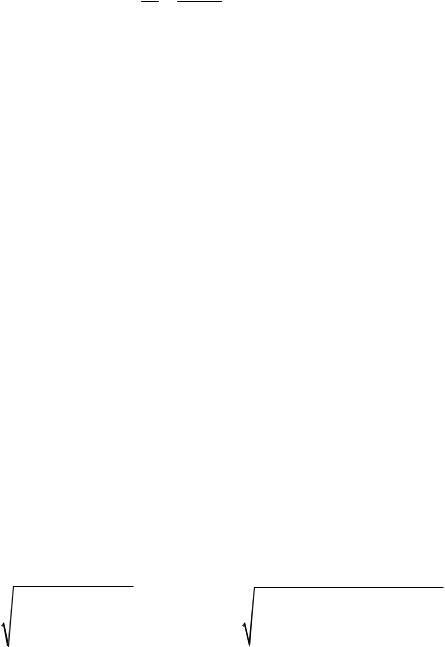
с1 |
4Q |
|
|
4 0,347 |
10,67 |
м/с. |
о D02 dСТ2 |
|
0,969 3,14 0,2392 0,122 |
Находим значение входного угла β1 по формуле (2.16):
tg 1 c1 10,67 0,355, β1=19,5º. u1 30,03
Находим конструктивный угол лопасти β1Л, принимая угол атаки i=4º, по формуле (2.17):
β1Л=β1+i=4+19,5º=23,5º.
Принимая значение коэффициента стеснения входного сечения кромками лопастей k1=1,15, находим ширину лопасти на входе b1 по формуле (2.18):
b |
Q |
|
|
|
0,347 |
|
0,047 м, |
|
|
|
3,14 0,1912 10,67 1,15 |
||||
1 |
Dc k |
|
|||||
|
1 |
1 |
1 |
|
|
|
|
Проверяем выполнение неравенства (3.19):
0,239 |
|
0,122 |
|
|
b1 |
|
0,239 |
|
0,122 |
|
|
|
|
1 |
|
|
|
2,5 |
|
1 |
|
|
|
, |
|
4 |
0,239 |
2 |
4 |
0,239 |
2 |
|||||||
|
|
|
|
|
|
|
|
|
0,0447 b1 0,1117м.
Таким образом, рассчитанное значение b1=0,047м принадлежит допустимому интервалу. Расчет входных элементов рабочего колеса считается законченным.
Переходим к расчету выходных элементов рабочего колеса.
Задаваясь значением угла потока (лопасти) на выходе из рабочего колеса β2 =18°, определяем окружную скорость u2 по формуле (2.20):
u |
c2r |
|
|
c2r |
2 |
|
gH |
|
1,1 10,67 |
|
1,1 10,67 |
2 |
|
9,81 260 |
74м/с. |
|
|
|
|
|
|
|
|
|
|
|
|||||||
2 |
2tg 2 |
|
2tg 2 |
|
Г |
|
2tg18 |
2tg18 |
0,909 |
|
||||||
|
|
|
|
|
|
|
|
|
Определяем диаметр выхода из рабочего колеса D2 по формуле (2.21):
D |
60u2 |
|
60 74 |
0,471 м. |
|
n |
3,14 3000 |
||||
2 |
|
|
Находим отношение диаметров выхода и входа:
38

D2 0,471 2,46.
D1 0,1912
Определяем ширину лопасти на выходе из рабочего колеса b2 по формуле (2.23)
b b |
D1 |
0,047 |
0,1912 |
0,0191 м. |
|
|
|||
2 1 D |
0,471 |
|
||
|
2 |
|
|
|
Принимая литое рабочее колесо, имеющее значение K = 6,5, определяем количество рабочих лопаток по формуле (2.24)
z K D2 D1 sin 2 1 6,50,471 0,1912sin18 19,5 4,9 шт .
D2 D1 |
2 |
0,471 0,1912 |
2 |
Полученное значение округляем до целых, т.е. z = 5 штук.
Принимая толщину лопастей s = 5 мм, вычисляем коэффициенты стеснения лопастями сечения на входе k1Р в рабочее колесо и выходе k2Р из него по формуле (2.25):
|
|
|
|
|
3,14 0,1912 |
|
|||||||||||
k1Р |
|
|
|
5 |
|
|
|
|
|
|
|
|
|
|
1,142. |
||
|
3,14 0,1912 |
|
0,005 |
|
|||||||||||||
|
|
|
|
|
|
|
|
|
|
|
|
|
|
|
|
|
|
|
|
|
|
5 |
sin19,5 |
||||||||||||
|
|
|
|
|
|
|
|||||||||||
|
|
|
|
|
|
3,14 0,471 |
|||||||||||
k2Р |
|
|
5 |
|
|
|
|
|
|
|
1,058. |
||||||
|
3,14 0,471 |
|
|
0,005 |
|||||||||||||
|
|
|
|
5 |
|
|
|
sin18 |
|
||||||||
|
|
|
|
|
|
|
|
Величина k2Р должна находиться в пределах 1,05÷1,1. В нашем случае это требование выполняется.
Находим отклонение значения k1Р от принятого в расчете k1=1,15 по фор-
муле (2.26):
|
|
|
k1Р k1 |
|
|
100% |
|
1,142 1,15 |
|
100% 0,7 %. |
|
|
|
||||||||
|
|
|
|
|
|
1,142 |
|
|||
|
|
|
k1Р |
|
|
Полученное значение ∆<5 %, следовательно, расчет рабочего колеса окон-
чен.
39