
3158
.pdf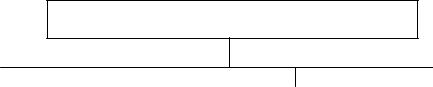
Основные виды термической обработки стали
Термическая обработка
|
|
|
|
|
|
|
|
|
|
Отжиг 1 |
|
Отжиг 2 |
|
Закалка |
|
Отпуск |
|||
рода |
|
рода |
|
|
|
|
|
||
|
|
|
|
|
|
|
|
|
|
Отжиг
Отжиг – термическая обработка, заключающаяся в нагреве стали до
определенной температуры, выдержке и последующем медленном охлаждении (обычно вместе с печью), с целью получения более равновесной структуры. Основные цели отжига: снижение твердости, повышение пластичности и вязкости стали, улучшение обрабатываемости, измельчение зерна.
Различают отжиг 1-го и 2-го рода.
Отжиг 1-го рода частично или полностью устраняет отклонения от равновесного состояния, возникшие при предыдущей обработке, причем его проведение не обусловлено фазовыми превращениями. В зависимости от того, какие отклонения от равновесного устраняются, различают следующие разновид-
ности отжига 1-го рода: диффузионный (гомогенизационный) – для устране-
ния дендритной или внутрикристаллитной ликвации (неоднородности) сталей, рекристаллизационный – термическая обработка деформированного сплава для проведения рекристаллизации с целью снятия наклепа перед последующей деформацией; для снятия внутренних напряжений (табл. 6.1).
Отжиг 2-го рода основан на использовании диффузионных фазовых превращений. Существуют следующие виды отжига 2-го рода: полный, не-
полный, сфероидизирующий, изотермический и нормализация (табл. 6.1). Температуры нагрева и схемы различных видов отжига представлены на рис. 6.6 и 6.7.
61
|
|
|
|
|
|
|
|
|
|
|
|
Таблица. 6.1 |
||
|
|
|
|
|
|
|
Виды отжига |
|
|
|
|
|
||
|
|
|
|
|
|
|
|
|
|
|
|
|
|
|
|
Вид отжига |
|
Характеристика |
|
|
Температура на- |
Структура |
Примечание |
||||||
|
|
|
|
грева |
||||||||||
|
|
|
|
|
|
|
|
|
|
|
|
|
|
|
|
|
|
|
|
|
|
Отжиг 1-го рода |
|
|
|
|
|
||
|
|
|
|
|
|
|
|
|
|
|
|
|
||
|
|
Отжиг |
с |
длительной |
выдержкой |
1000-1100 °С |
Химически однородная |
Подвергают |
отливки |
|||||
|
|
крупнозернистая |
и |
слитки |
из |
|||||||||
|
Диффузионный* |
при температуре выше |
950 °С |
|||||||||||
|
Ас3 + 150¸250 °С |
(видманштеттовая) |
легированной |
стали |
||||||||||
|
с целью выравнивания химического |
|||||||||||||
|
|
состава |
|
|
|
|
|
|
|
структура с игольчатым |
для |
уменьшения |
||
|
|
|
|
|
|
|
|
|
строением феррита |
дендритной ликвации |
||||
|
|
|
|
|
|
|
|
|
|
|||||
|
Рекристаллиза- |
Отжиг деформированной стали при |
680-740 °С |
|
Слитки |
любых |
сталей |
|||||||
|
температуре, |
выше |
температуры |
Превращение текстуры |
после |
холодной де- |
||||||||
|
ционный |
начала |
рекристаллизации |
с целью |
0,5 ¸ 0,6 Тпл |
в равноосные зерна |
формации |
(обработки |
||||||
62 |
|
устранения |
наклепа и получения |
|
|
давлением) |
|
для |
||||||
|
равноосного зерна |
|
|
|
|
|
восстановления |
пла- |
||||||
|
|
|
|
|
|
|
||||||||
|
|
|
|
|
|
|
|
|
|
|
стичности |
|
|
|
|
|
|
|
|
|
|
|
|
650-680 °С |
|
Детали |
точных |
стан- |
|
|
Для снятия |
Отжиг |
стали |
после |
различных |
Уменьшение |
ков, |
измерительный |
||||||
|
внутренних |
видов металлобработки: сварки, |
Ас1 – (15-30) °С |
внутренних |
инструмент из легиро- |
|||||||||
|
напряжений |
резки, шлифования с целью |
|
напряжений |
ванных и |
углероди- |
||||||||
|
|
уменьшения |
|
внутренних |
|
|
стых сталей с высокой |
|||||||
|
|
напряжений (твердости) |
|
|
|
|
точность размеров |
|||||||
|
|
|
|
|
|
|
Отжиг 2-го рода |
|
|
|
|
|
||
|
|
Отжиг при температуре выше Ас3 с |
|
|
Ликвидация |
пороков |
||||||||
|
|
целью |
получения |
равновесной |
Ас3 + (20¸30) |
|
структуры |
при |
пре- |
|||||
|
Полный |
ненапряженной |
перлитной |
П +Ф(сетка) |
дыдущей |
обработке |
||||||||
|
|
структуры |
|
после |
|
полной |
|
|
доэвтектоидной стали |
|||||
|
|
перекристаллизации |
|
|
|
|
|
|
|
|
|
Окончание табл. 6.1
|
Вид отжига |
Характеристика |
Температура |
Структура |
Примечание |
|
||
|
нагрева |
|
||||||
|
|
|
|
|
|
|
|
|
|
|
Отжиг 2-го рода |
|
|
|
|
|
|
|
|
Отжиг в интервале температур |
|
|
Подвергают |
доэвтек- |
||
|
Неполный |
между Ас1 и Ас3 с целью получения |
Ас1 < Тн < Ас3 |
П + Ф |
тоидные стали с целью |
|||
|
|
перлитной структуры после час- |
|
|
снятия |
внутренних |
||
|
|
тичной перекристаллизации |
|
|
напряжений |
|
|
|
|
|
|
|
(П + Ц2) Пзерн |
Подвергают |
заэвтек- |
||
|
|
Отжиг при температуре несколько |
|
|
тоидные |
стали |
для |
|
|
Сфероидизирущий |
выше Ас1 с целью сфероидизации |
Ас1 < Тн < Асm |
|
устранения |
цемен- |
||
|
|
карбидов |
|
|
титной |
сетки |
и |
|
|
|
|
|
|
уменьшения |
твер- |
||
|
|
|
|
|
дости и хрупкости |
|
||
|
|
Отжиг, заключающийся в нагреве |
|
|
Подвергают |
легиро- |
||
63 |
|
до температуры выше Ас3 (Аcm), |
Ас3 + (40¸50) |
Структуры перлитного |
ванные стали для по- |
|||
|
выдержке, охлаждении до темпера- |
Аcm+ (40¸50) |
превращения: перлит, |
лучения |
однородной |
|||
|
Изотермический |
туры перлитного превращения и |
|
сорбит, троостит |
ферритно- |
|
|
|
|
|
изотермической выдержке до пол- |
|
|
цементитной |
смеси. |
||
|
|
ного распада аустенита |
|
|
Этот вид отжига эко- |
|||
|
|
|
|
|
номичнее обычного |
|||
|
|
Нагрев до температуры выше Ас3 |
Ас3 + (40¸50) |
|
Углеродистые и леги- |
|||
|
|
(Асm) с последующим охлаждением |
|
рованные |
стали |
для |
||
|
Нормализация |
на воздухе с целью получения |
Аcm+ (40¸50) |
Сорбит или троостит |
измельчения |
зерна и |
||
|
|
мелкого зерна и равномерного |
|
|
упрочнения. |
Эконо- |
||
|
|
распределения структурных |
|
|
мичный |
способ |
уп- |
|
|
|
составляющих |
|
|
рочняющей |
термооб- |
||
|
|
|
|
|
работки |
|
|
|
Примечание. Для исправления структуры отливки после диффузионного отжига подвергают полному отжигу
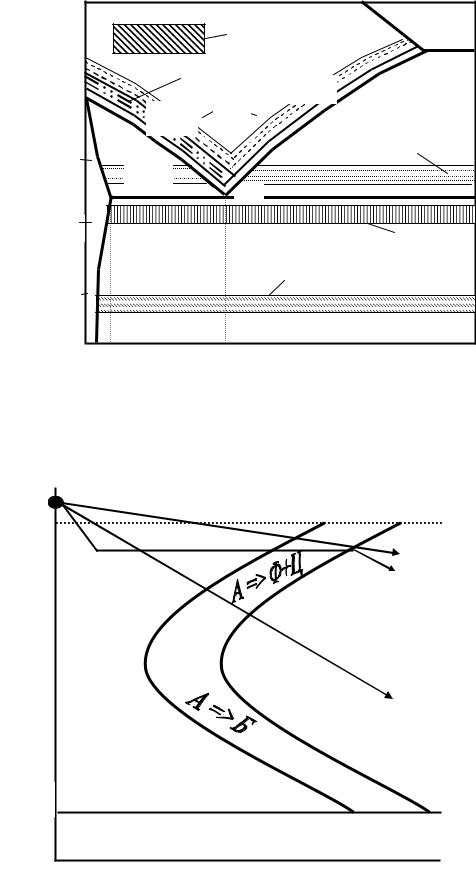
|
t, °C |
|
|
|
|
|
|
|
1 |
Е |
|
|
|
|
|
|
|
. |
G |
|
4 |
Аccm |
|
Ас3 |
6 |
5 |
|
||
|
|
|
|
||
|
|
|
|
|
|
|
800 |
Ас1 |
|
|
|
|
Р |
S |
|
К |
|
|
|
|
|||
|
600 |
|
|
2 |
|
|
|
|
|
|
|
|
400 |
|
|
3 |
|
|
|
|
|
|
|
|
Q |
|
|
|
|
|
0,02 |
|
0,8 |
|
C, % |
|
Рис. 6.6. Температура нагрева при отжиге: 1- диффузионный отжиг; |
||||
|
2 – рекристаллизационный отжиг; 3 – отжиг для снятия напряжений; |
||||
|
4 – полный отжиг; 5 – неполный отжиг; 6 - нормализация |
||||
|
t, |
А |
|
|
|
|
°C |
|
|
|
П |
|
|
|
|
V1 |
|
|
|
|
|
А1 V2 |
С |
|
Ап |
|
|
|
|
|
|
|
|
Т |
|
|
|
|
|
|
|
|
|
|
|
V3 |
ВБ |
|
|
|
|
|
|
|
Мн |
|
|
|
НБ |
|
|
|
|
|
|
|
Мк |
|
А ® М |
|
М |
|
|
|
t, с |
|
|
|
|
|
|
|
|
|
Рис. 6.7. Схемы отжига эвтектоидной стали: |
|
|||
|
V1 – обычный отжиг; V2 – изотермический отжиг; V3 - нормализация |
64
Закалка
Закалка – термическая обработка, заключающаяся в нагреве стали
до температуры выше фазовых превращений, выдержке и последующем быстром охлаждении со скоростью, равной или выше критической, с целью получения неравновесной структуры стали - мартенсита.
В результате закалки из аустенита образуется метастабильная структура мартенсита с высокой твердостью.
Результаты закалки во многом зависят от правильного выбора температуры нагрева для закалки. Доэвтектоидные стали для закалки следует нагревать до температуры на 30-50 °С выше Ас3 (рис. 6.8). В этом случае сталь с исходной структурой перлит + феррит нагревается до аустенитного состояния и при охлаждении со скоростью больше критической получается мартенсит. Такая закалка называется полной.
Если доэвтектоидную сталь нагреть выше Ас1, но ниже Ас3, то в ее структуре после закалки, наряду с мартенситом, будут участки феррита. Присутствие феррита как мягкой составляющей снижает твердость стали после закалки. Такая закалка называется неполной. Следовательно, доэвтектоидные стали обычно подвергают полной закалке.
Заэвтектоидные стали нагревают для закалки на 50-70 °С выше Ас1. При этих температурах в стали, наряду с аустенитом, имеется вторичный цементит. Поэтому после закалки в структуре заэвтектоидных сталей присутствуют мартенсит, цементит и небольшое количество остаточного аустенита. Если заэвтектоидную сталь нагреть для закалки выше Асcm, то в ее структуре будет крупноигольчатый мартенсит с повышенным количеством остаточного аустенита. Присутствие остаточного аустенита в структуре стали снижает ее твердость. Все заэвтектоидные стали подвергают неполной закалке (рис. 6.8).
Закалочные среды. Охлаждающая (закалочная) среда должна обеспечить высокую скорость охлаждения при температурах наименьшей устойчивости переохлажденного аустенита (650-550 °С), чтобы предупредить его распад на ферритно-цементитную смесь.
Винтервале температур мартенситного превращения (от Мн до Мк) целесообразно медленное охлаждение с целью уменьшения внутренних напряжений.
Вкачестве закалочных сред для углеродистых сталей, имеющих высокую критическую скорость охлаждения, применяют воду и различные водные растворы, а для легированных сталей, имеющих небольшую критическую скорость закалки, используют масло и воздух.
Способы закалки. Оптимальный способ закалки выбирают в зависимости от состава стали, формы и размеров детали. Различные способы закалки представлены в табл. 6.2 и на рис. 6.9, оптимальные температуры нагрева под закалку на рис. 6.8.
65
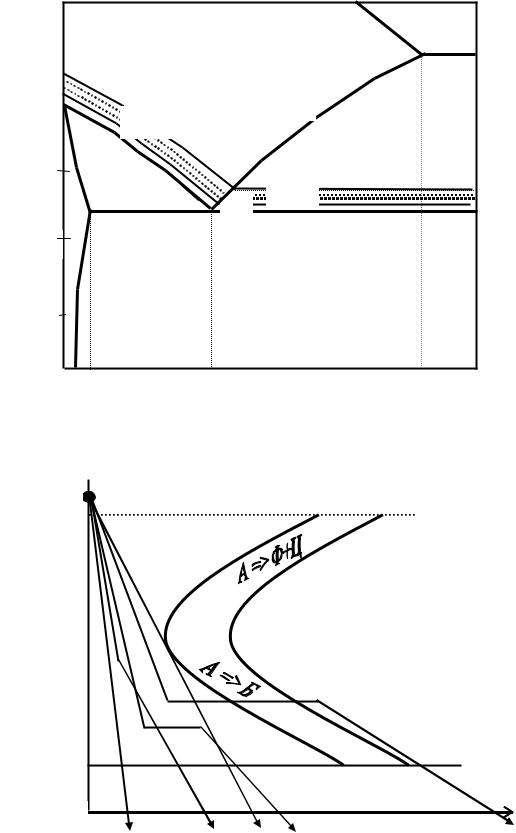
t, °C |
|
|
|
|
|
Аустенит |
|
Е |
|
|
|
|
||
G |
Ас3 |
|
Асcm |
|
|
|
|
|
|
800 |
А + Ф |
|
|
А + Ц2 |
|
Ас1 |
|
||
Р |
|
S |
К |
|
|
|
|||
600 |
|
|
|
|
400 |
Ф + П |
|
|
П + Ц2 |
|
|
|
А1 |
|
|
Q |
|
|
|
|
|
|
|
|
|
0,02 |
0,8 |
|
C, % |
Рис. 6.8. Оптимальные температуры нагрева под закалку углеродистыхсталей |
t, °C |
А |
|
Ап
М
А ® М
М
1 |
2 Vк 3 |
t, с |
4 |
|
Рис. 6.9. Виды закалки сталей: 1 – непрерывная закалка; 2 – прерывистая; 3 – ступенчатая; 4 - изотермическая
66
|
|
|
|
Таблица 6.2. |
|
|
Способы закалки |
|
|
|
|
|
|
|
|
Способ закалки |
Характеристика |
Структура |
Применение |
|
|
Полная закалка (температура нагрева Ас3 + (30 ¸ 50 °) |
||
|
|
|
|
|
|
Непрерывная |
Закалка с непрерывным охлаждением |
|
Применяют для закалки легированных сталей |
|
(в одном |
в одной среде с целью получения |
Мартенсит |
при охлаждении в масле и цементированных |
|
охладителе) |
структуры мартенсита |
|
углеродистых при охлаждении в воде |
|
|
Закалка с охлаждением в среде с |
|
Применяют для деталей из углеродистых ста- |
|
|
температурой несколько выше Мн, |
|
лей диаметром не более 10-12 мм, для легиро- |
|
Ступенчатая |
выдержкой без превращения аусте- |
Мартенсит |
ванных сталей – до 20-30 мм сложной конфи- |
67 |
|
нита и последующим охлаждением |
|
гурации с целью уменьшения остаточных на- |
|
на воздухе для получения структуры |
|
пряжений при сохранении высокой твердости |
|
|
|
|
||
|
|
мартенсита |
|
|
|
|
Закалка с охлаждением в среде с |
|
Применяют для закалки изделий сложной |
|
|
температурой выше Мн, изотерми- |
|
формы из легированных сталей во избежание |
|
Изотермическая |
ческой выдержкой до полного или |
Нижний бейнит |
образования трещин и коробления и для полу- |
|
|
неполного превращения аустенита |
|
чения высокой прочности и вязкости. Закалоч- |
|
|
и последующим охлаждением для |
|
ная среда – расплавы солей или щелочей |
|
|
получения структуры бейнита |
|
|
|
|
Неполная закалка (температура нагрева Ас1 + (30 ¸ 50 °) |
||
|
|
|
|
|
|
|
Закалка с непрерывным охлаждени- |
|
Применяют для закалки изделий из высокоуг- |
|
|
ем в одной среде с целью получения |
|
леродистых сталей несложной формы в воде. |
|
Непрерывная |
структуры мартенсита и цементита |
Мартенсит и це- |
Изделия диаметром до 6-7 мм закаливают в |
|
|
|
ментит |
масле |
|
|
|
|
|
|
|
|
|
|
Окончание табл. 6.2 |
|
|
|
|
|
|
||
|
Способ закалки |
Характеристика |
Структура |
Применение |
||
|
|
|
|
|
|
|
|
|
Неполная закалка (температура нагрева Ас1 + (30 ¸ 50 °) |
|
|||
|
|
|
|
|
||
|
|
Закалка с охлаждением в двух сре- |
|
Основной вид закалки углеродистых инстру- |
||
|
Прерывистая |
дах: вначале с большей (вода), затем |
Мартенсит |
ментальных сталей. Применяется для сниже- |
||
|
(в двух средах) |
с меньшей охлаждающей способно- |
и цементит |
ния внутренних напряжений при сохранении |
||
|
|
стью (масло) |
|
высокой твердости |
|
|
|
|
|
|
|
||
|
|
Закалка с продолжением охлажде- |
|
Подвергают измерительные инструменты, де- |
||
68 |
|
ния до температуры ниже + 20 °С, |
Мартенсит |
тали подшипников, |
цементированные детали |
|
С обработкой |
но в интервале Мн-Мк с целью до- |
и цементит |
из легированных сталей с устойчивым аусте- |
|||
|
||||||
|
холодом |
полнительного превращения оста- |
|
нитом. Среда охлаждения – жидкий азот и ки- |
||
|
|
точного аустенита в мартенсит |
|
слород |
|
|
|
|
|
|
|
||
|
|
Закалка с охлаждением в среде с |
|
Применяют для закалки инструментов не- |
||
|
|
температурой несколько выше Мн, |
Мартенсит |
большого сечения |
из низко- и среднелегиро- |
|
|
Ступенчатая |
выдержкой без превращения аусте- |
и цементит |
ванных сталей |
|
|
|
|
нита и последующим охлаждением |
|
|
|
|
|
|
на воздухе для получения структуры |
|
|
|
|
|
|
мартенсита |
|
|
|
|
|
|
|
|
|
|
Отпуск
Отпуск является заключительной операцией термической обработки ста-
лей. Отпуск – это термическая обработка, заключающаяся в нагреве стали,
подвергнутой закалке, до температуры ниже Ас1, выдержке и последующем охлаждении, с целью превращения неравновесной структуры в более равновесную.
Закаленная структура сталей является термодинамически нестабильной, так как имеет искаженную кристаллическую решетку (тетрагональную с отношением осей с/а > 1) и повышенную свободную энергию. Поэтому при последующем нагреве закаленная сталь стремится к более стабильному состоянию, т.е. к превращению мартенсита и остаточного аустенита в ферритоцементитную смесь.
Различают три вида отпуска (табл. 6.3).
Низкотемпературный отпуск (низкий) осуществляется в интервале температур 100-250 °С. При этом отпуске уменьшается степень тетрагональности кристаллической решетки мартенсита вследствие выделения из нее углерода в виде e-карбида. Кристаллическая решетка e-карбида когерентно связана с решеткой мартенсита, т.е. отдельные кристаллографические плоскости у них являются общими. В связи с когерентной связью твердость стали при этом не снижается, а внутренние напряжения уменьшаются. В результате низкотемпературного отпуска мартенсит закалки превращается в мартенсит отпуска, имеющий повышенную ударную вязкость и пластичность по сравнению с мартенситом закалки. При этом сталь сохраняет высокую твердость (рис. 4.10). Поэтому низкотемпературному отпуску подвергают режущий и мерительный инструмент из углеродистых и низколегированных сталей, а также детали после поверхностной закалки, цементации и т.д.
Среднетемпературный отпуск (средний) проводят при температуре
350-500 °С. При температуре свыше 300 °С из мартенсита выделяется цементит. Образование цементита и его коагуляция (укрупнение) сопровождаются снижением твердости и повышением вязкости и пластичности. При среднетемпературном отпуске образуется дисперсная ферритно-цементитная смесь, имеющая зернистое строение цементита. Эта структура называется трооститом отпуска. Средний отпуск средне- и высокоуглеродистых сталей обеспечивает высокие предел упругости, предел выносливости, большую релаксационную стойкость. Поэтому этот вид отпуска используют после закалки рессор, пружин, штампов.
Высокотемпературный отпуск (высокий) осуществляется при темпера-
туре 500-600 °С. При этом происходит полное снятие внутренних напряжений, коагуляция и сфероидизация частиц цементита. Структуру, возникающую после высокого отпуска, называют сорбит отпуска. Сорбит отпуска состоит из ферритной основы, пронизанной сферическими частицами цементита. В результате высокотемпературного отпуска понижается твердость закаленной
69
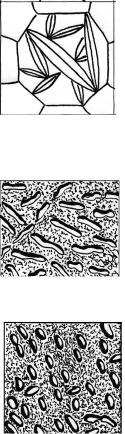
|
|
|
|
|
|
|
|
|
Таблица 6.3 |
||
|
|
|
|
Виды отпуска |
|
|
|
|
|
|
|
|
|
|
|
|
|
|
|
|
|
|
|
|
Вид отпуска |
|
Характеристика |
Температура |
Время вы- |
Структура |
Применение |
||||
|
|
нагрева |
держки |
(схема) |
|||||||
|
|
|
|
|
|
|
|
|
|||
|
|
|
|
|
|
|
Мартенсит |
Режущий и |
|
|
|
|
Низко- |
|
|
|
|
|
отпуска |
мерительный |
|||
|
Отпуск |
при температуре ниже |
|
|
|
инструмент |
|
из |
|||
|
температурный |
250 °С, |
с целью получения мар- |
150-250 °С |
2 часа + 1 мин |
|
высокоуглеро- |
||||
|
(низкий) |
тенсита отпуска и уменьшения ос- |
|
на мм сечения |
|
дистых и легиро- |
|||||
|
|
таточных напряжений |
|
|
|
ванных сталей с |
|||||
|
|
|
|
|
|
|
|
высокой |
твер- |
||
|
|
|
|
|
|
|
|
достью и |
изно- |
||
70 |
|
|
|
|
|
|
|
состойкостью |
|||
|
Отпуск |
в |
интервале температур |
|
|
Троостит |
|
|
|
|
|
|
|
|
|
|
|
|
|
||||
|
Средне- |
350-500 °С, с целью получения |
|
|
отпуска |
Используют |
|
||||
|
дисперсных |
продуктов распада |
350-500 °С |
|
|
для |
пружинно- |
||||
|
температурный |
мартенсита, |
некоторого снижения |
20 мин + 1 мин |
|
рессорных |
ста- |
||||
|
(средний) |
твердости при значительном уве- |
|
на мм сечения |
|
лей |
|
|
|
||
|
|
личении предела упругости и вы- |
|
|
|
|
|
|
|
||
|
|
носливости |
|
|
|
|
|
|
|
|
|
|
|
|
|
|
|
|
|
Используют |
|
||
|
|
Отпуск |
в |
интервале температур |
|
|
Сорбит отпуска |
для |
конструк- |
||
|
Высоко- |
500-680 °С |
|
|
ционных |
|
ста- |
||||
|
500-680 |
°С, с целью получения |
10 мин + 1 мин |
|
лей, |
детали |
из |
||||
|
температурный |
структуры сорбита отпуска, дос- |
|
на мм сечения |
|
которых |
под- |
||||
|
(высокий) |
тижения |
оптимального сочетания |
|
|
|
вергаются |
дей- |
|||
|
|
прочностных, пластических и вяз- |
|
|
|
ствию высоких |
|||||
|
|
ких свойств. |
|
|
|
напряжений |
и |
||||
|
|
|
|
|
|
|
|
ударным |
|
на- |
|
|
|
|
|
|
|
|
|
грузкам |
|
|