
3131
.pdf3.2. Обработка давлением, особенности технологии работы с металлом
Обработка материалов давлением основана на их пластичности. В результате процесса можно получить конечную деталь либо заготовку, близкую по форме к готовому продукту. Различные виды обработки металлов давлением применяются в машиностроении, авиационной промышленности, автомобилестроении и пр.
Физические основы обработки металлов давлением
Обработка материалов давлением основана на механическом свойстве атомов занимать новое устойчивое положение при воздействии на них нагрузки, превышающей предел упругости материала.
Это называется пластической деформации. Помимо механических, изменяются и физико-химические свойства металла.
Существует горячая и холодная обработка металлов давлением.
Горячей называется обработка при температуре заготовки выше температуры рекристаллизации;
Холодная обработка материалов давлением происходит при температуре заготовки ниже температуры рекристаллизации.
Существуют различные виды обработки материалов давлением:
прокатка;
ковка;
прессование;
волочение;
объемная штамповка;
листовая штамповка;
комбинированные методы.
Обработка металлов давлением: прокатка
30
Прокаткой называется вид пластической обработки, в процессе которого исходная заготовка обжимается вращающимися валками стана прокатного. Целью операции является уменьшение поперечного сечения заготовки и придания ей заданного профиля.
Способы прокатки
Существует три способа прокатки металла:
1.продольная: самый распространенный способ прокатки. Суть его заключается в следующем: заготовка пропускается между валками, вращающимися в разные стороны, при этом она обжимается до толщины, равной зазору между валками;
2.поперечная: применяется для обработки тел вращения (шаров, цилиндров, втулок и пр.). Заготовка при этом не имеет поступательного движения;
3.поперечно-винтовая: нечто среднее между двумя предыдущими способами. Применяется для изготовления полых заготовок.
Ковка
Ковка относится к высокотемпературным операциям. Заготовка предварительно нагревается до ковочной температуры, зависящей от конкретной марки металла.
Способы ковки:
1.ковка на молотах (пневматических, гидравлических
ипаровых);
2.штамповка;
3.ручная ковка.
Машинная (на молотах) и ручная ковка является свободной, так как металл при воздействии на него инструмента ничем не ограничен. Штамповка свободной не является, так как заготовка находится в матрице штампа (т. е. ограничена со всех сторон). В результате штамповки металл принимает форму полости матрицы. Ковка применяется в единичном и мелкосерийном производстве. Для получения поковки разогретую заготовку помещают между ударными частями (бой-
31
ками) молота. В качестве подкладных инструментов используются:
1.топор;
2.обжимка;
3.раскатка.
Прессование
Это способ обработки металла, в процессе которого он выдавливается прессом из полости матрицы через ее отверстие. Применяется для обработки хрупких металлов. Прессованием получают полые и сплошные профили из титановых сплавов, алюминия, меди и магния – детали для автомобилей, самолетов, лопатки, подвески, трубы.
Прессование может быть горячим и холодным. Обработка пластичных материалов производится в холодном состоянии (олово, медь, чистый алюминий). Тугоплавкие металлы и сплавы (содержащие никель, титан и др.) прессуются только после предварительного нагрева заготовки и инструмента. С помощью этой операции можно получить детали различной конфигурации, с ребрами (внутренними и наружными), постоянным или периодическим профилем по длине.
Прессование выполняется на прессах со сменной частью (матрицей). Матрицы изготавливаются из жаропрочных штамповых сталей.
Волочение
Волочением называется метод обработки металлов, в процессе которого заготовка круглого (или фасонного) профиля принудительно протягивается через фильеру (волоку). Примером может служить изготовление проволоки, когда заготовка большого диаметра (катанка) протягивается через ряд фильер, на выходе из которых получается проволока гораздо меньшего диаметра.
Операция классифицируется:
1.по типу волочения:
2.сухое (через мыльный порошок);
32
3.мокрое (через эмульсию мыльную).
4.по чистоте обработки поверхности:
5.черновое;
6.чистовое.
7.по кратности переходов:
8.однократное;
9.многократное (с несколькими переходами с по-
степенным уменьшением поперечного сечения заготовки).
по температуре:
1.холодное волочение;
2.горячее волочение.
Объемная штамповка
Метод обработки металла, при котором придание заготовке заданной формы осуществляется с помощью штампа. При этом течение металла ограничивается полостями его частей. Штампованные изделия изготавливают с помощью специальных инструментов - штамповых блоков. Существует две разновидности штампов: открытые и закрытые.
В открытых штампах между подвижными частями предусмотрен зазор, в который выдавливается избыток металла – облой.
Его приходится удалять на последующей операции механической обработки. Штамповка в открытых штампах хороша тем, что не требуется предъявлять особых требований к массе заготовки.
Закрытые штампы такого зазора не имеют. Весь металл находится в замкнутом пространстве, облоя не образуется. Но в этом случае заготовка тщательно рассчитывается по объему.
Листовая штамповка
Листовая штамповка заключается в изготовлении детали из листа, полосы или ленты, полученных прокаткой.
Существуют два основных вида операций: 33
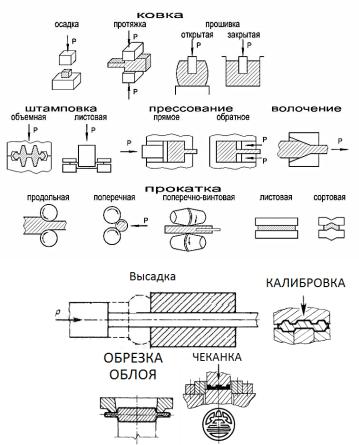
1.разделительные: вырубка, отрезка и пробивка;
2.формообразующие: вытяжка, гибка отбортовка, раздача, чеканка и пр.
Листовая штамповка производится на кривошипных и гидравлических прессах. В качестве инструмента используются штампы, основными деталями которых являются матрицы и пуансоны.
Рис. 6. Схемы напряженно-деформированных состояний основных процессов ОМД
34
В основном штампованная деталь не требует дальнейшей механической обработки. Поэтому матрицы и пуансона должны быть тщательно рассчитаны и изготовлены с соблюдением всех технических требований.
Несмотря на то, что листовая штамповка является в какой-то мере стандартной операцией, конструктора часто сталкиваются с нетипичными проблемами: обработка металлов давлением учебник, как правило, предоставляет множество примеров конструкторских разработок частных случаев.
Листовая штамповка широко применяется практически во всех отраслях промышленности. Детали, полученные этим методом, отличаются высокой точностью.
От мельчайших деталей микроэлектроники до кузовов автомобилей – все это производится методом листовой штамповки. Специальность обработка металлов давлением наряду с обработкой металла резанием является одной из самых востребованных.
Вопросы для самоподготовки
1. Что представляет собой механическая обработка де-
талей?
2.На чем основана обработка металлов давлением?
3.Какие виды обработки металлов давлением сущест-
вуют?
4.Что такое объемная штамповка?
5.В чем заключается листовая штамповка?
35
ЛЕКЦИЯ №4
ТЕОРЕТИЧЕСКИЕ ОСНОВЫ ОБРАБОТКИ МЕТАЛЛОВ ДАВЛЕНИЕМ
Теоретические вопросы:
4.1.Сущность обработки металлов давлением
4.2.Теоретические основы обработки металлов давле-
нием
4.1. Сущность обработки металлов давлением
Обработка металлов давлением основана на исполь-
зовании пластичности металла, т. е. его свойстве изменять первоначальную форму под действием внешних сил или внутренних напряжений без разрушения и сохранять вновь полученную форму после прекращения действия нагрузки. Обработка давлением обычно преследует две основные цели: получение изделий сложной формы из заготовок простой формы и улучшение кристаллической структуры исходного литого металла с повышением его механических свойств.
Получение изделий и полуфабрикатов при обработке давлением осуществляется путем пластического деформирования (перераспределения) металла исходной заготовки или разрезанием его без снятия стружки под давлением рабочего инструмента: бойков, штампов, ножей и др.
Объем металла и плотность его при этом практически не изменяются, поэтому объем исходной заготовки равняется объему полученного изделия плюс объем отходов металла в данном процессе обработки.
В качестве исходных заготовок при обработке давлением используют слитки из стали и цветных сплавов, а также сортовой и листовой прокат.
Обработка давлением является экономичным и прогрессивным технологическим процессом. Отходы металла при этом незначительны и не превышают обычно (за исклю-
36
чением свободной ковки) 20 - 25% от массы получаемого изделия или полуфабриката, а в ряде процессов, например при холодной штамповке, составляют всего 5 - 10%.
В то же время при формообразовании изделий обработкой резанием отходы металла в виде стружки составляют свыше 50% от веса готовой детали; расходуются непроизводительно рабочая сила, энергия, материалы, инструмент. В стружку удаляются наиболее прочные периферийные слои металла прутковых заготовок, имеющие лучшую мелкокристаллическую структуру.
Наряду с экономным расходованием металла и повышением его механических свойств в готовых изделиях обработка давлением обеспечивает чрезвычайно высокую производительность труда, по сравнению с другими методами обработки, благодаря высоким скоростям обработки и одновременному деформированию всего объема заготовки или значительной его части.
Например, при прокатке скорость выпуска готовой продукции достигает 20-30 м/сек; при горячей штамповке за 1 мин на одном штамповочном молоте или прессе изготовляются две-три поковки сложной формы при массе поковки до 20 - 50 кг; при холодной штамповке производится 1300 - 1500 мелких деталей в минуту на одном прессе-автомате.
Примером рационального изготовления изделия методом обработки давлением может служить изготовление болта М16 х 100 холодной высадкой на кривошипном прессеавтомате из заготовки диаметром 16 мм, длиной 139 мм, массой 0,22 кг.
Масса готового болта равна 0,21 кг; отход металла составляет лишь 4,8%. При изготовлении болта на токарноревольверном полуавтомате из шестигранной заготовки массой 0,57 кг отход металла в стружку составляет 171% от массы готового болта, при этом за 1 ч на станке изготовляется 40 болтов, а при высадке на прессе - 720 болтов, причем штампованные болты имеют лучшую макроструктуру и повышенную прочность.
37
Процессы обработки металлов давлением развиваются
исовершенствуются в направлении приближения формы и размеров заготовки к конфигурации и размерам готовой детали, что обеспечивает снижение трудоемкости последующей их обработки резанием, себестоимости продукции и повышение коэффициента использования металла.
Точность изделий, получаемых обработкой давлением, высока: например, прокаткой получают фольгу толщиной 2 - 3 мкм, с допуском в десятые доли мкм; волочением изготовляют проволоку диаметром 10 - 20 мкм, а холодной объемной
илистовой штамповкой получают готовые детали 3 - За классов точности, поступающие непосредственно на сборку.
При этом чистота поверхности указанных изделий достигает 9 - 10-го классов. В настоящее время в Российской Федерации обработке давлением подвергается около 90% всей выплавляемой стали и 55% цветных металлов и сплавов, или свыше 100 млн. т металла в год.
4.2. Теоретические основы обработки металлов давлением
Теория обработки металлов давлением - это наука о физической сущности и закономерностях процессов пластической деформации металлов в различных технологических условиях.
Основными ее задачами являются определение оптимальных условий для пластического деформирования металлов в холодном и горячем состоянии и расчет необходимых усилий деформации с целью правильного выбора мощности оборудования.
Упругая и пластическая деформация Деформацией называют изменение формы и размеров
тела под действием внешних сил или внутренних напряжений. Деформация называется упругой, или обратимой, если после удаления приложенных к телу сил оно полностью вос38
станавливает свои первоначальные форму и размеры. Если после прекращения действия внешних сил тело сохраняет вновь полученную форму, то такая деформация называется пластической или остаточной.
Упругая деформация предшествует пластической, так как она возникает при меньшей величине деформирующих сил и напряжений. Поэтому полная деформация тела в момент действия нагрузки равна сумме упругой и остаточной (пластической) деформаций.
При упругой деформации происходит искажение кристаллической решетки металла с отклонением групп атомов, расположенных в узлах решетки, от положений их устойчивого равновесия.
При снятии внешней нагрузки форма тела восстанавливается, а атомы кристаллической решетки принимают первоначальное положение, причем изменений в строении и свойствах металла не происходит.
Пластическая деформация металлов, имеющих неоднородное поликристаллическое строение, является сложным механическим и физико-химическим процессом, вызывающим коренные изменения в структуре металла и его свойствах в зависимости от тепловых и механических условий деформации.
Пластическая деформация отдельно взятого металлического кристалла может происходить путем скольжения или двойникования.
Скольжение представляет собой последовательные параллельные перемещения дислокаций вдоль кристаллографических плоскостей, наиболее плотно заполненных атомами. Как указано выше, дислокации представляют собой линейные дефекты кристаллической решетки вдоль прерванных плоскостей кристалла. При деформации кристалла перемещение отдельных объемов его происходит разновременно, а не сразу по всей плоскости скольжения. Дислокации смещаются последовательно микроскачками, и вместе с этим образуются новые дислокации. Таким образом, пластическая де-
39