
Системы управления роботами. Литвиненко А.М
.pdfМИНИСТЕРСТВО ОБРАЗОВАНИЯ РОССИЙСКОЙ ФЕДЕРАЦИИ
Воронежский государственный технический Университет
А.М. Литвиненко СИСТЕМЫ УПРАВЛЕНИЯ РОБОТАМИ
УЧЕБНОЕ ПОСОБИЕ
Воронеж 2002

УДК 658.52.011.56.012.3.05
Литвиненко А.М. Системы управления роботами: Учеб. пособие/ Воро-
неж. гос. техн. ун-т. Воронеж, 2002. 140 с.
Учебное пособие посвящено изучению систем управления роботами,
структурно-алгоритмической организации систем управления, основным функ-
циональным модулям систем управления, а также перспективам развития сис-
тем управления промышленными роботами.
Издание предназначено для студентов вузов, обучающихся по направле-
нию 652000 "Механотроника и робототехника", специальности 210100 «Управ-
ление и информатика в ТС», дисциплине "Системы управления роботами".
Учебное пособие подготовлено на магнитном носителе в текстовом ре-
дакторе MS WORD 2000 и содержится в файле «система управления роботами.exe».
Табл. 3. Ил. 43. Библиогр.: 72 назв.
Научный редактор: д-р техн. наук В.Л. Бурковский
Рецензенты: НИИ Механотроника-Альфа;
д-р техн. наук Ю.С. Сербулов.
Издается по решению редакционно-издательского совета Воронежского государственного технического университета.
Литвиненко А.М., 2002.
Оформление. Воронежский государственный технический университет, 2002
1. Основы информатики ГПС
1.1. Ретроспектива развития программного управления станками
История развития станков с числовым программным управлением охватывает около трех десятилетий. Однако именно это направление следует отнести к самому крупному и перспективному достижению XX в. в металлообработке. Интенсивное развитие станков с ЧПУ и расширение области их применения связаны с научно-
технической революцией во всех областях техники.
Создание ГПС с управлением от ЭВМ выдвинуло новые требования не только к станкам, погрузочно-транспортным устройствам, но также привело к коренным измене-
ниям в организации всего технологического процесса. При этом производительность возросла как за счет снижения времени обработки, так и не в меньшей степени благодаря новым фермам организации производства.
Объединение в общую автоматизированную макросистему всего производственно-
го процесса привело к усилению информационных связей между отдельными проектно-
технологическими и производственными службами предприятия, ускорению прохож-
дения потоков информации, объединению различных сведений в банках данных.
Появление гибких производственных систем (ГПС) стало возможным после за-
вершения предшествующих этапов развития оборудования с ЧПУ. Созданию гибких производственных модулей (ГПМ) предшествовала разработка многоцелевых станков с магазинами инструментов, загрузочных роботов-манипуляторов и микропроцессор-
ных систем управления, обеспечивающих развитую диагностику.
Ни одной из индустриально развитых стран не удалось избежать прохождения всех основных этапов в глобальном развитии техники. Эта закономерность проявля-
ется и в машиностроении, прогресс которого зависит от совершенствования других от-
раслей промышленности, и в первую очередь – электроники. При создании ГПС на действующих производствах необходимо принимать во внимание возможности других служб, а также учитывать уже имеющееся оборудование с ЧПУ и целесообразность его модернизации.
На машиностроительных предприятиях эксплуатируют станки с системами про-
граммного управления (ПУ) различных годов выпуска или, как принято говорить, с
системами ПУ различных поколений. Поэтому знание этапов развития устройств ПУ имеет не только познавательное значение, но также позволяет принимать правильное
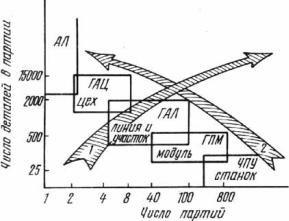
решение по организации эксплуатации и модернизации оборудования. Разнообразие систем ПУ объясняется главным образом быстрым их моральным старением, обу-
словленным бурным развитием электроники.
Рис. 1.1. Области применения различных видов автоматизации обработки металлов резанием:
1 – увеличение производительности; 2 – увеличение гибкости; АЛ – автоматическая линия; ГАЦ – гибкий автоматический цех; ГАЛ – гибкая автоматическая линия.
Характерным для общего направления развития машиностроения является со-
кращение сроков внедрения новых разработок и совершенствование технологии. Во второй половине XX в. во всех ведущих отраслях машиностроения массовое произ-
водство все в большей степени заменяется крупно-, средне- и мелкосерийным. Это привело к необходимости частой переналадки производства с одного вида изделия на другое.
Основным фактором, обусловившим необходимость создания и развития стан-
ков с программным управлением, была и остается потребность автоматизации обра-
ботки в средне- и мелкосерийном производствах. Однако создание на основе ЭВМ комплексной информационной системы с автоматическим управлением многоопера-
ционными станками, магазинами инструментов, погрузочно-транспортными устрой-
ствами, складом заготовок и инструмента, т. е. появление ГПС, сделало эффективным применение средств ЧПУ и в крупносерийной производстве.
Одним из главных критериев, определяющих область применения отдельных видов автоматизированного оборудования, является число различных деталей, изго-
товляемых на этом оборудовании, и число деталей в каждой партии. ГПС наиболее эффективны в области производства с числом партии в год от 4 до 100 при числе де-
талей в партии от 150 до 1500 шт. (рис. 1.1), и эта область будет расширяться.
Новым качеством ГПС является интеграция технологического оборудования с микропроцессорной техникой и использование ЭВМ для обработки, хранения и вы-
дачи информации на взаимосвязанное управление оборудованием, входящим в состав ГПС. Создание ГПС стало своеобразным переломным моментом в развитии станко-
строения, ознаменовав начало нового этапа автоматизации средне- н крупно-
серийного производства.
Немаловажным фактором в развитии ЧПУ станками явилась потребность ма-
шиностроения в многокоординатной обработке деталей сложной конфигурации. Из-
готовление таких деталей на станках без ЧПУ практически невозможно. Многокоор-
динатные станки с ЧПУ позволили создать новые конструкции узлов и деталей ма-
шин. Это относится в равной степени к электроэрозионным станкам и высокопроиз-
водительным лазерным машинам.
Следует отметить также, что использование инструмента, оснащенного пла-
стинками из керамического материала на основе нитрида бора и других сплавов, по-
зволило увеличить скорость резания до величин, при которых ручное управление станком становится практически нереализуемым.
Возможность разработки станков с ЧПУ и ГПС была подготовлена развитием электроники и вычислительной техники. Промышленное освоение интегральных схем и микропроцессоров позволило разработать устройства ЧПУ станками высокой на-
дежности при малых габаритных размерах.
Хотя электронные вычислительные машины и числовое программное управле-
ние станками возникли на протяжении «жизни» одного поколения, они имеют свою историю и свои сменяющие друг друга этапы развития. В короткой истории станков с ЧПУ в мировом станкостроении можно выделить четыре основных этапа. Первый – начало промышленного выпуска станков с ЧПУ и опробование принципов ЧПУ в промышленности, неавтоматизированный (ручной) расчет программ; второй – широ-
кое внедрение в промышленность станков с автономными устройствами ЧПУ посто-
янной структуры; освоение систем автоматического программирования на ЭВМ; тре-
тий этап – создание устройств ЧПУ на микроЭВМ и многоцелевых станков; разра-
ботка новых конструктивных компоновок станков. Следующий этап – объединение станков с ЧПУ в общую систему автоматизированного управления технологическим процессом с управлением от ЭВМ (ГПС).
Естественно, что границы начала и конца этапа не могут быть точно определе-
ны, так как указанные направления со сдвигом во времени развивались параллельно.
На первом этапе вели интенсивно разработки систем автоматического програм-
мирования на ЭВМ. Устройства ЧПУ первого поколения выполняли с вводом про-
граммы на магнитной ленте в унитарном коде или фазовом виде.
На втором этапе совершенствуются конструкции и технические показатели от-
дельных узлов станков и систем ЧПУ, хотя большинство станков с ЧПУ в этот период продолжали выпускать без существенных изменений традиционных конструктивных компоновок. В станках применяли быстродействующий привод подач, высокоточные датчики обработки связи, поворотные резцедержатели, револьверные головки и т.д.
Использование интегральных схем в устройствах ЧПУ второго поколения по-
зволяет уменьшить габаритные размеры, расширить их технологические функции и увеличить надежность. Стандартизируют кодирование управляющих программ с вво-
дом их на восьмидорожковой перфоленте. Существенно увеличивается быстродейст-
вие привода подач и соответственно производительность станков.
Определяющим фактором в развитии устройства ЧПУ является развитие элек-
троники. Первые устройства ЧПУ выполняли на полупроводниковых элементах. Ши-
рокое развитие системы ЧПУ получили после применения интегральных элементов.
Начиная с этого можно различать поколения систем ЧПУ: на элементах малой в средней степени интеграции, затем с использованием микроЭВМ и далее на микро-
процессорных элементах.
Наряду с элементной базой совершенствовались также привод подач и общая структура устройств ЧПУ. В условиях резкого расширения выпуска станков с ЧПУ первостепенное значение приобрело создание систем автоматического расчета управ-
ляющих программ на ЭВМ.
С программированием связал целый комплекс проблем как чисто технического
(кодирование, математическое обеспечение расчетов и т.д.), так и организационного характера. Программирование – ответственный этап в подготовке производства, так как качество программы не только определяет выходные параметры детали, но и в значительной степени влияет на производительность станка.
Разработка методов автоматического программирования и необходимого мате-
матического обеспечения оказала решающее влияние на темпы развития ЧПУ стан-

ками в целом и подготовила переход к ГПС. Для ускорения решения вопросов про-
граммирования были созданы специальные системы автоматического программиро-
вания и машинные языки, рассчитанные на определенные группы станков (токарные,
фрезерные и т. д.). В СССР значительную роль в ускорении внедрения систем автома-
тического программирования и улучшении вопроса подготовки программ сыграли за-
водские бюро и территориальные центры по программированию.
Моральное старение устройств ЧПУ наступает быстрее, чем станков. Практиче-
ски устройства ЧПУ претерпевают существенные изменения каждые 3-4 года, в то время как конструкции станков за это время лишь незначительно модифицируются, и
сроки их морального старении в 2—2,5 раза больше. Поэтому границы этапов разви-
тия числового программного управления станками в целом в значительной мере ус-
ловны. Каждый последующий этап развития систем управления содержит некоторые элементы предыдущего. Это наблюдается также в этапах развития конструкции стан-
ков с ЧПУ и, в частности, при создании и применении многоцелевых станков и моду-
лей.
Новая концепция автоматизации основана на максимальном приближении ЭВМ к сфере производства как в части управления отдельными станками, так и в части планирования производственного процесса участка, цеха и завода.
Устройства ЧПУ выполняют на элементах большей степени интеграции (БИС),
микропроцессорах ( P) н микроЭВМ ( ЭВМ). Расширяется номенклатура многоце-
левых станков с магазинами инструмента. Появляются гибкие производственные мо-
дули с промышленными роботами (манипуляторами) и магазином заготовок. Станки объединяют в участки с введением элементов централизованного управления от ЭВМ.
При подготовке УП на ЭВМ определяют не только траектории движения инст-
румента, но также технологические параметры (режимы обработки и т.п.).
Усиливается тенденция программирования у станка, особенно при обработке деталей несложной конфигурации, и использование для подготовки управляющей программы автономной микро-ЭВМ, установленной в технологическом отделе. При-
менительно к этим микро-ЭВМ создают специализированные системы автоматиче-
ского программирования, ориентированные на ограниченную номенклатуру деталей
(рис. 1.2).
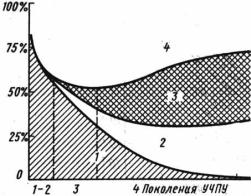
Если в системах ЧПУ первого поколения алгоритмы управлении реализовыва-
лись схемно, то в микропроцессорных УЧПУ второго и третьего поколений функции управления задаются программно-математическим обеспечением. Это создает гиб-
кость систем ЧПУ и позволяет расширить технологические возможности оборудова-
ния.
Рис. 1.2. Соотношение методов подготовки управляющих программ для станков с ЧПУ:
1 – ручная подготовка УП; 2 – подготовка УП на станке; 3 – подготовка УП в технологическом бюро с автономной микроЭВМ; 4 – система автоматического программирования на ЭВМ вычислительного центра завода.
Системы ЧПУ второго и третьего поколений позволили создать гибкие произ-
водственные модули (ГПМ) и гибкие производственные системы на основе включе-
ния ГПМ в общую транспортно-складскую систему автоматизированного управления от ЭВМ.
Наряду с созданием новых структур гибких производственных систем для этого этапа характерным является увеличение объема программного обеспечения (ПрО)
микропроцессорных систем ЧПУ. Грани между аппаратной частью различных испол-
нений устройств ЧПУ стираются. Основное отличие их определяется составом ПрО.
УЧПУ третьего (и частично второго) поколения выполняют функции программиро-
вания работы электроавтоматики станка. Это исключает необходимость релейных схем и повышает надежность.
Возрастают объемы памяти УЧПУ, и быстродействие что позволяет увеличить число управляемых координат и реализовать функции адаптивного управления, авто-
матического измерения на станке, графического отображения информации на дисплее УЧПУ, диалогового задания управляющих программ. УЧПУ имеет интерфейс, позво-
ляющий подсоединить систему к локальной вычислительной сети ГПС.
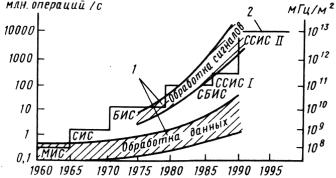
Создание новых поколений УЧПУ базируется на увеличении вычислительной способности микропроцессорных систем, определяемой в первую очередь быстро-
действием интегральных элементов и объемом памяти.
При этом переход на большую степень интеграции сопровождается скачкооб-
разным увеличением удельного быстродействия. Этот показатель равен произведе-
нию числа вентилей в ИС на частоту следования тактовых импульсов, отнесенному на единицу площади кристалла. В то же время быстродействие вычислительной сис-
темы, определенное отношением частоты тактовых импульсов к числу импульсов на операцию, возрастает плавно (рис. 1.3).
Рис. 1.3. Развитие быстродействия интегральных схем:
1- быстродействие млн. операций в секунду; 2 – частота, отнесенная к площади интегральной схемы.
Увеличение мощности микропроцессорных устройств характерно также для систем управления промышленными роботами (ПР) (рис. 1.4). Для наиболее простых видов работ управляющая программа ПР задается детерминировано либо вводится в
режиме обучения с ручным управлением. При более сложных видах работ наряду с этими методами задания УП (В, Г на рис.1.4) используют тактильные датчики, уста-
новленные в схвате, техническое зрение, оптические (лазерные) средства дистанци-
онного контроля положения схвата.
Увеличивается число управляемых координат ГПМ и ПР. Кинематические свя-
зи в оборудовании заменяются взаимосвязанным микропроцессорным управлением приводами. Электронные системы концептуально и конструктивно объединяют с ме-
ханическими узлами машин. Это направление в машиностроении получило название мехатроники.
Наряду с совершенствованием средств микропроцессорных систем ЧПУ, разви-
тие вычислительной техники приводит к созданию интегрированной системы автома-
тизированного конструирования и проектирования технологических процессов, ори-
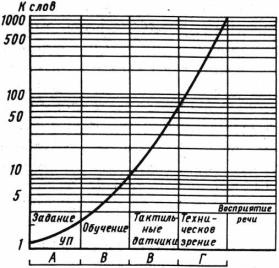
ентированные на применение ГПС и систем автоматической сборки. Этот период за-
вершился к концу XX века появлением полностью автоматизированных цехов и заво-
дов.
Рис. 1.4. Зависимость объема памяти устройства управления промышленным роботом от выполняемых технологических функций:
А – загрузка и выгрузка деталей и инструмента, ориентированных в таре; Б – окраска деталей сложной конфигурации, сварка; В – загрузка и выгрузка неориентированных деталей, контроль деталей; Г – сборочные работы с контролем, статической обработкой информации.
1.2. Основные определения и классификация
Терминология в области ЧПУ станками быстро видоизменяется и расширяется
в соответствии с появлением новых структур систем управления и отмиранием ста-
рых. В табл. 1.2 приведены определения систем и их отдельных узлов (ГОСТ 25686-
85, ГОСТ 26228-85).
Существующие в основной составной части ГПС–гибком производственном
модуле (ГПМ) – функции контроля обеспечивают:
-идентификацию формы и положения загружаемых заготовок;
-слежение за состоянием инструмента, в том числе его поломкой и износом
(последнее путем измерения силы резания или с помощью других методов);
-учет периода стойкости каждого инструмента;
-измерение готовых деталей и при необходимости коррекцию параметров об-
работки.
Буферные накопители заготовок создают па определенный период относитель-
ную автономность функционирования ГМП. Введение диагностики состояния станка