
2848
.pdf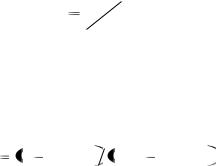
катушках, бумага в рулонах) и т.д. Продукция, расходующая свой ресурс, определяет второй класс промышленной продукции.
В этой среде есть группы для оценки уровня качества. Они сформированы для неремонтируемых изделий. Так, первая группа - это такая продукция, как подшипники, шестерни, конденсаторы, электровакуумные и полупроводниковые приборы и т.д. Вторая – это ремонтируемые изделия, например - транспортные средства, технологическое оборудование, включая автоматические линии, измерительные стенды и комплексы и т.д.
На основании такой классификации и с учетом принятых показателей качества продукции, определяют базовое изделие с набором показателей, отвечающих определенной номенклатуре показателей качества продукции.
Можно сказать следующее. Оценка уровня качества продукции - это совокупность операций, включающая выбор номенклатуры, показателей качества оцениваемой продукции, определение значений этих показателей и сопоставление их с базовыми.
Уровень качества продукции - это относительная характеристика еѐ качества, основанная на сравнении значений показателей качества оцениваемой продукции с базовыми значениями соответствующих показателей. На практике для оценки уровня качества продукции применяют несколько методов. Суть их такова.
Известный дифференциальный метод предполагает, что есть базовый образец, относительно которого рассматриваются остальные. Чтобы определить по каким из единичных показателей достигнут уровень значений базового варианта, рассчитывают относитель-
|
Qотн(1) |
|
|
|
ный показатель качества продукции |
i |
по формуле |
|
|
отн(1) |
P |
|
|
|
Qi |
i |
БАЗ |
|
|
P |
, |
(1) |
||
|
i |
|
||
|
|
|
|
где Pi - значение i-го показателя качества оцениваемого изделия;
PБАЗ
i- значение i-го базового показателя;
i=1..n - количество оцениваемых показателей.
Если задано - нормативное значение i-го показателя ограничивающее диапазон значений показателя качества, то используют следующую формулу:
QОТН (2) |
P |
P НОРМ |
P БАЗ |
P |
НОРМ |
|
i |
i |
i |
i |
i |
. |
(2) |
71

Когда задан, так называемый, главный показатель, которым являются производительность оборудования, годовая выработка электроэнергии и т.д. или какой – то комплексный показатель (а также средневзвешенный или интегральные показатели), то используют комплексный метод оценки уровня качества, который определяют по вышеуказанным формулам.
Если нельзя установить функциональную зависимость главного показателя от исходных показателей качества, но есть информация о параметрах весомости усредненных показателей, то целесообразно использовать средний взвешенный показатель и коэффициенты весомости.
Применяемый смешанный метод оценки уровня качества разнородной продукции основан на одновременном использовании единичных и комплексных показателей. Он применяется в тех ситуациях, когда часть единичных показателей объединяют в группы и для них вводят комплексный показатель, а отдельные главные показатели рассматривают как обобщенные показатели.
Полученные показатели (комплексные и единичные) используют по схеме дифференциальной оценке качества продукции.
Для оценки качества совокупности видов обширной разнородной продукции используют индексы качества (ИК) и дефектности (ИД). Считают, что комплексный показатель качества разнородной продукции, который равен среднему взвешенному относительных значений показателей качества продукции, представляет собой индекс качества, определяемый по формуле
ИК |
В Кi KiБАЗ |
|
|
, |
(3) |
где Вi - коэффициент весомости i - го вида продукции;
Кi и - соответственно комплексный и базовый комплексный показатель i- го вида продукции, причем количество видов продукции равно i=1,…,m.
Коэффициент весомости определяют, исходя из Сi - стоимости изделий i-го вида, по формуле
m
Bi Ci Ci
|
i |
1 |
. |
(4) |
|
|
|
||
Индекс дефектности определяют по формуле |
|
|||
m |
Д ikОТН |
|
||
ИД |
Вi |
(5) |
||
i |
1 |
|
, |
|
|
|
|
72

где - относительный коэффициент дефектности продукции i- го вида, являющийся соотношением коэффициента дефектности Д произведенной продукции в рассматриваемом периоде с базовым значением ДБАЗ коэффициента продукции, выпускаемой за базовый период времени, т.е. имеем следующее выражение
ДikОТН Д Д БАЗ |
(6 ) |
. |
Индексы качества и дефектности используют при анализе работы предприятия по совершенствованию выпуска качества продукции.
Воронежский государственный технический университет
УДК 621.09.047
А.М. Семенцев, О.М. Андреева, В.П. Смоленцев
ПОВЫШЕНИЕ КАЧЕСТВА ДЕТАЛИ ЛАЗЕРНЫМ ЛЕГИРОВАНИЕМ
В работе рассмотрена проблема повышения качества детали лазерным легированием. В данной работе приведены физическая и математическая модели с помощью которых можно доказать повышение качества детали лазерным легированием.
Современный этап развития техники предъявляет повышенные требования к эксплуатационным характеристикам деталей. Различные узлы и детали машин, металлорежущие инструменты, металлические элементы конструкций работают в условиях повышенного трения, больших удельных нагрузок, высоких температур, широкого диапазона скоростей, воздействия агрессивных сред и т.д. Зачастую имеет место одновременное воздействие нескольких факторов. Поэтому в настоящее время остро стоит проблема повышения качества рабочих поверхностных слоев изделий.
Повышение свойств изделий в настоящее время достигается за счет использования в качестве материала специальных сталей и сплавов. Большое внимание уделяется сочетанию свойств, присущих сердцевине изделия (ударная вязкость, прочность, пластичность) и поверхностному слою (твердость, износостойкость, теплостойкость, усталостная выносливость и др.). Чаще всего эти свойст-
73
ва достигаются обеспечением химического состава материала изделия, а именно композиционных материалов.
Распространенным способом является поверхностное легирование вообще и лазерное в частности. На обрабатываемый участок поверхности металла наносится (насыпкой, нанесением пасты, диффузионным методом, электроискровым способом, гальваническим или химическим осаждением и др.) слой легирующих элементов, который далее расплавляется вместе со слоем основного металла под действием лазерного излучения. При этом происходит частичное выгорание обмазки, образуется неоднородный по составу и неравномерный по глубине легированный слой. Наиболее изученными в настоящее время являются процессы однокомпонентного легирования неметаллическими материалами – углеродом, азотом, кремнием и бором. В остальных случаях за счет вихревых потоков в кристаллизующемся металле образуется значительная структурная неоднородность, приводящая зачастую к появлению напряженного состояния материала. Глубина легированного слоя не превышает обычно 200 мкм. Появляющаяся после затвердевания поверхностного слоя изделия повышенная шероховатость требует проведения дополнительной механической обработки с удалением части легированного слоя. Это может свести к минимуму положительный эффект от лазерного легирования особенно при эксплуатации детали в условиях динамических нагрузок.
Одним из эффективных путей получения эксплуатационных свойств изделия является возможность изменения химического состава материала изделия путем управляемого легирования поверхностного слоя энергией лазера.
Оптические свойства каждого элемента или соединения определяют характер его взаимодействия с лучом лазера. Считается [1], что существует зависимость поглощательной способности металлов и сплавов от удельного электросопротивления. С ростом электропроводности и уменьшением электросопротивления увеличивается коэффициент отражения металлом лазерного излучения. Коэффициент отражения уменьшают, увеличивая степень черноты материала. Известно [1], что неметаллы имеют высокую степень поглощения лазерного излучения. Поэтому такие соединения как Fe2S, Al2O3, Zn3(PO4)2, Mg3(PO4)2 используют в качестве покрытия обрабатываемых образцов.
74
Легирующие элементы, вводимые в стали, могут находиться там либо в виде соединений (интерметаллидных или неметаллических), либо в виде раствора в матрице. Если учесть, что эти соединения имеют разные оптические характеристики, то можно предположить, что различные составляющие, входящие в состав слоя, поглощающего лазерного излучение, подвергаются разной степени воздействия. Естественно, что неметаллические включения, расположенные в этой зоне, поглощают большее количество энергии по сравнению с основным металлом, так как они имеют высокую степень черноты и теплоемкость при низкой электропроводности. В связи с этим неметаллические включения нагреваются до более высоких температур, чем матрица. Этот нагрев осуществляется за короткий промежуток времени в рамках импульса лазерного излучения, что приводит к появлению градиента температуры не только по глубине образца, но и по направлению от неметаллического включения к зернам металла, то есть имеет место сток температуры к включению и локальные флуктуации температуры в пределах самого включения.
Следует отметить, что немаловажную роль играет скорость нагрева материала, от чего зависит возможность фазовых переходов твердая фаза – жидкость или твердая фаза – газ. Для скоростей нагрева, характерных для высококонцентрированных источников энергии наиболее предпочтительным является переход твердая фаза
– газ. Таким образом, при воздействии лазерного излучения на поверхность детали происходит сублимация включений и образование газовой фазы.
Поскольку неметаллические включения располагаются, как правило, по границам зерен (по дефектам структуры), то в этом месте образуются газовые каналы, которые могут превращаться в газожидкостные за счет некоторой потери теплоты. По этим каналам происходит перенос сублимированных неметаллических включений к поверхности образца, причем движение газовой и жидкой фазы подчиняется законам турбулентной диффузии. Коэффициенты диффузии при такой модели переноса на 5…6 порядков выше, чем соответствующие коэффициенты при описании диффузии по гидродинамической, флуктуационной или активационным моделям[1]. При достижении поверхности происходит падение температуры переносимого материала, сопровождаемое диссоциацией неметаллического включения на ионы металла и неметалла. Неметаллическая состав-
75
ляющая удаляется из образца, а большая часть металлической остается в поверхностном слое за счет того, что имеет более высокую температуру возгонки.
Описанный механизм массопереноса характерен для зоны закалки из твердого состояния как для случая обработки без оплавления поверхности, так и для облучения с оплавлением поверхности при проведении высокоскоростного нагрева. При охлаждении стального образца, которое происходит в условиях, отличных от равновесных, перенос элементов осуществляется по механизмам, описанным в работах [1, 2].
Лазерное излучение является электромагнитным, разработана физическая модель массопереноса, учитывающая взаимодействие индуцированного излучением магнитного поля с компонентами сплава. Со стороны этого поля на компоненты сплава (парамагнетики и диамагнетики) в зоне оплавления и зоне термического влияния действуют силы, имеющие различные направления вектора, которые зависят от магнитных свойств компонентов.
На основании предложенных физических моделей массопереноса легирующих элементов и связанного с ним трансформации и перераспределения неметаллических включений разработана математическая модель одномерного распространения температурного поля в зоне лазерного воздействия, в основу которой положена теория релаксационных процессов. Математически доказана гипотеза о более высокой интенсивности нагрева образца лазерным излучением, чем это было принято считать, исходя из известных математических моделей.
Эксперименты подтвердили результаты теоретических исследований, что при лазерной обработке деталей из сталей происходит перераспределение легирующих элементов в зоне лазерного воздействия. На характер перераспределения легирующих элементов в зоне лазерного воздействия большое влияние оказывает длительность импульса излучения. При различных длительностях импульса (при прочих равных условиях) концентрация одного и того же легирующего элемента в определенной области может быть значительно выше или ниже среднего содержания этого элемента в основной массе металла.
Экспериментально доказана модель аномального массопереноса легирующих элементов в железоуглеродистых сплавах, что обеспечивает возможность использования этого явления для повы-
76
шения эффективности лазерной обработки деталей машин и инструментов.
Литература 1.Семенцев А. М. Повышение эффективности лазерной об-
работки деталей из железоуглеродистых сплавов, основанное на установленном механизме массопереноса легирующих элементов.
Брянск, 2008, - 231 с.
2.Качество машин: справочник. В 2-х т. Т.2./ А.Г.Суслов, Ю.В.Гуляев, А.М.Дальский и др.- М.: Машиностроение, 1995.- 430с.
3.Суслов А.Г. Технологическое обеспечение параметров состояния поверхностного слоя деталей.- М.: Машиностроение, 1987.-
208 с.
4.Бутенко В.И. Локальная отделочно-упрочняющая обработка поверхностей деталей машин.- Таганрог: Изд-во ТРТУ, 2006.-
126 с.
5.Суслов А.Г., Дальский А.М. Научные основы технологии машиностроения.- М.: Машиностроение, 2002.- 684 с.
Воронежский государственный технический университет
УДК 621.9.047
С. Ю. Жачкин, А.А. Сидоркин, А.А. Живогин, П.В. Цысоренко
АНАЛИЗ ПРИЧИН ВЫСОКОГО ПЕРЕНАПРЯЖЕНИЯ ПРИ ВОССТАНОВЛЕНИИ ИОНОВ ЖЕЛЕЗА
Дан анализ причин эффекта перенапряжения, возникающего при осаждении железных покрытий гальваническим методом. Анализируются различные гипотезы, объясняющие данное явление.
Осаждение металлов является сложным электрохимическим процессом. Кинетика и механизм электроосаждения зависят не только от природы металлов, состава электролита, структуры поверхности металла, степени ее дефектности, но и от электронных свойств, обусловливающих адсорбционные и каталитические характеристики металлов, особенности их поведения на границе раздела с раствором электролита. Не менее важную роль при этом играют структурные, молекулярные и физико-химические свойства элек-
77

тролита, его адсорбционная и комплексообразующая способности, наличие всякого рода взаимодействий в растворе.
Особенностью электроосаждения металлов как любого сложного электрохимического процесса является стадийный механизм разряда, когда переход из начального (иона в растворе) в конечное (металлическое) состояние осуществляется через ряд последовательных (одноэлектронных) электрохимических процессов.
В настоящее время на основе анализа электрохимических и кинетических закономерностей сделаны предположения о механизме процесса осаждения, причинах значительного перенапряжения при протекании электрохимических процессов на металлах группы железа, разработан целый ряд теорий и гипотез. Однако до сих пор нет единого взгляда на указанные явления из-за их сложности и многообразия проявления в различных условиях. С этим в основном связаны эмпирические поиски новых блескообразователей, добавок, а также режимов технологических процессов.
Электролитическое выделение металлов чаще всего осуществляется из простых солей – сульфатов, хлоридов или нитратов. Суммарной катодной реакцией в этом случае будет разряд гидратированных металлических ионов с их последующим переходом в кристаллическую решетку образующегося на катоде осадка:
|
|
|
|
Me nH2O 2e [Me ] xH2O . |
(1) |
Восстановление ионов металла на поверхности катода происходит через ряд последовательных стадий: 1 – перенос ионов посредством диффузии и миграции из объема раствора в слой раствора, прилегающий к электроду; 2 – разряд ионов на электроде с образованием атомов; 3 – формирование и рост осадка вещества. При электроосаждении металлов реализуется стадия образования кристаллических зародышей. В ходе электрохимического процесса может происходить перемещение частиц по поверхности электрода (поверхностная диффузия) от центров, на которых идет разряд до некоторых других, где продуктам реакции находиться энергетически выгодно. Если поверхность электрода несет заряд, одинаковый с зарядами реагирующей частицы, то электрическое поле двойного слоя препятствует адсорбции этой частицы и необходимо учитывать стадии вхождения реагирующей частицы в двойной слой.
Несмотря на существующее согласие при определении основных стадий разряда остается ряд нерешенных вопросов при определении их последовательности: предшествует ли адсорбция иона
78

акту разряда или последний происходит на некотором расстоянии от электрода в двойном слое, образуются ли атомы металлов на поверхности кристалла или разряд происходит в момент вхождения в кристаллическую решетку и ряд других. Любая из упомянутых стадий может оказаться самой медленной и будет определять скорость данного электродного процесса, состоящего из ряда последовательных стадий.
Таким образом, электрохимическое осаждение металлов является сложным процессом, состоящим из целого ряда независимых реакций, протекающих последовательно или одновременно в электродной системе. Последовательность этих реакций, природа замедленной стадии, установление причины поляризации определяют механизм электрохимических реакций при восстановлении ионов металла.
При исследовании суммарной электродной реакции при осаждении металлов изучается общая поляризация, которую можно разделить на ряд составных частей:
общее |
Ом |
С |
П |
К |
i , |
(2) |
где η – перенапряжение; ηОм – омическое; ηС – концентрационное; ηП
– перехода; ηК – кристаллизационное; ηi – ингибирующее.
Для определения природы катодной поляризации, вида перенапряжения, закономерностей сложного процесса электроосаждения железа, когда в реальных условиях на поверхности электрода протекает несколько процессов, применяют разнообразные современные методы исследования – стационарные (классические) и нестационарные (релаксационные). Электроосаждению железа посвящено большое количество работ [1 – 3].
Многочисленные теории, предложенные для объяснения высокой поляризации при выделении металлов группы железа, обычно основываются на предположении о замедленности какой-то определенной стадии.
Причины высокой поляризации железа многие авторы [1, 2] видят в замедленности процесса дегидратации ионов или в разнице между энергией гидратации и его связи с кристаллической решеткой. Однако эта точка зрения вызвала возражение [3], где была произведена количественная оценка энергии гидратации ионов ряда металлов и показано, что этот взгляд на природу поляризации металлов группы железа не соответствует действительности, так как энергии гидратации, а также энергии отрыва ионов от решетки у метал-
79
лов группы железа мало отличаются от соответствующих энергий других двухвалентных ионов, выделяющихся из водных растворов или совсем без перенапряжения или с очень малым напряжением. Показано [3], что энергия гидратации – величина термодинамическая, а потому необязательно может влиять прямо на кинетику процесса.
Строгая теория механизма электроосаждения металлов не может быть создана без учета поверхностной структуры и свойств электроосаждающего металла, энергетических уровней выделяющихся ионов и образовавшегося металла, возможной адсорбции как ионных, так и молекулярных веществ на обновляющейся поверхности, а также их взаимосвязи с природой выделяющегося иона и других факторов. На основе анализа литературных, экспериментальных данных можно сделать вывод, что большие поляризации, наблюдаемые в процессе выделения железа, обусловливаются вторичными процессами, происходящими как на поверхности катода, так и в ближайшем прикатодном слое. Согласно современным представлениям значительную роль в процессе электроосаждения железа могут иметь коллоидно-химические процессы.
При электроосаждении железа впервые было обращено внимание на вторичные процессы, т.е. на образование щелочных соединений и гидроокисей в приэлектродных слоях [3], которые находятся в коллоидном состоянии, и при их адсорбции на поверхности втода значительно меняются физико-механические свойства получаемых осадков. Однако экспериментальные факты по изменению физико-механических свойств покрытий, полученных в разных условиях электролиза, не могут быть однозначным доказательством влияния на них образующихся в прикатодном слое гидроокисей, так как подобное действие могут оказывать следы органических приме-
сей или включение молекул воды.
На основании изучения катодной поляризации нестационарными гальваническими методами было показано, что первичным электрохимическим процессом при электроосаждении железа вляяется разряд ионов водорода, который быстро приводит к пассивации катодной поверхности. Экспериментальные данные показывают, что при электроосаждении железа из растворов солей независимо от начальной кислотности раствора выделение его начинается лишь после достижения предельного тока разряда ионов водорода. Вследствие этого при электролизе происходит подщелачивание
80