
2821
.pdf
ИС, которое принято за 100%. Как видно из рис. 8.1,б, наибольший процент брака готовой продукции (67% всего брака готовой продукции) дают первые три технологические операции (напайка кристалла, герметизация, разводка выводов), которые представляют собой сборочные операции.
а) б)
Рис. 8.1. Гистограмма распределения вклада дефектов различных технологических операций в суммарное количество дефектов готовых ИС (а); накопленная гистограмма дефектов и кривая Парето (пунктир) (б): 1 — напайка (или припайка) — 26%; 2 — герметизация — 22%; 3 — разводка выводов —19%; 4 — фотолитография — 18%; 5 — осаждение диэлектрика — 7%; 6 — диффузия (или ионная имплантация) — 5%; 7 — металлизация — 3%
Среди операций изготовления кристалла первенствующее положение занимает фотолитография (18%), в то время как все остальные технологические операции дают только 15% общего числа брака при изготовлении ИС. Отсюда можно сделать вывод, что необходимо особое внимание обратить на сборочные операции, а среди технологических операций изготовления кристалла следует проанализировать операцию фотолитографии с точки зрения качества ИС.
При использовании диаграммы Парето для контроля важнейших факторов наиболее распространенным методом анализа является так называемый ABC-анализ, сущность которого рассмотрим на следующем примере.
70
Пример. На складе скопилось большое количество готовой продукции, реализация которой задерживается из-за длительного времени их выходного контроля, предшествующего поставке потребителю. В результате изготовитель несет большие убытки в связи с задержкой поставок. Было выяснено, что изготовитель проводит тщательный выходной контроль всех изделий одинаково, без всякого различия в их стоимости.
Разделим все изделия, хранящиеся на складе, по группам в зависимости от стоимости каждого изделия (табл. 8.1).
|
|
|
|
|
|
|
|
|
|
|
Таблица 8.1 |
||
|
|
|
|
Складские запасы изделий |
|
|
|
||||||
Стои- |
90Отдо |
100 |
80Отдо 90 |
70Отдо 80 |
60Отдо 70 |
50Отдо 60 |
40Отдо 50 |
30Отдо 40 |
20Отдо 30 |
10Отдо 20 |
до0От10 |
|
|
мость |
|
||||||||||||
|
|
|
|
|
|
|
|
|
|
|
|
||
изде- |
|
|
|
|
|
|
|
|
|
|
|
Итогo |
|
лия, |
|
|
|
|
|
|
|
|
|
|
|
|
|
руб. |
|
|
|
|
|
|
|
|
|
|
|
|
|
Число |
|
|
|
|
|
|
|
|
|
|
|
|
|
изде- |
0,2 |
0,3 |
0,5 |
0,5 |
0,8 |
1,2 |
1,5 |
2,5 |
5,0 |
12,5 |
25 |
||
лий, |
|||||||||||||
|
|
|
|
|
|
|
|
|
|
|
|
||
тыс. шт. |
|
|
|
|
|
|
|
|
|
|
|
|
Для проведения ABC-анализа построим таблицу с накоплением до 100% (табл. 8.2).
|
|
|
|
|
Таблица 8.2 |
|
|
Таблица накопленных процентов |
|
||||
Стоимость |
Число |
Стоимость изделий, |
Число изделий, хранящих- |
|||
хранящихся на складе |
ся на складе |
|||||
изделия |
изде- |
|
|
|
|
|
накоплен- |
относитель- |
накоплен- |
относительная |
|||
(центр |
лий, |
|||||
класса), |
тыс. |
ная стои- |
ная стои- |
ное число |
частота (час- |
|
мость, |
мость, |
изд., тыс. |
тость) изделий |
|||
руб. |
шт. |
|||||
тыс. руб |
Ст1/Ст% |
шт. |
n1/N% |
|||
|
|
|||||
1 |
2 |
3 |
4 |
5 |
6 |
|
95 |
0,2 |
19,0 |
4,1 |
0,2 |
0,8 |
|
85 |
0,3 |
44,5 |
9,6 |
0,5 |
2,0 |
|
75 |
0,5 |
82,0 |
17,6 |
1,0 |
4,0 |
71
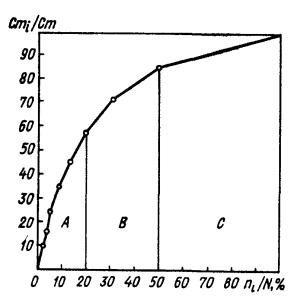
Продолжение табл. 8.2
1 |
2 |
3 |
4 |
5 |
6 |
65 |
0,5 |
114,5 |
24,5 |
1,5 |
6,0 |
55 |
0,8 |
158,5 |
34,0 |
2,3 |
9,2 |
45 |
1,2 |
212,5 |
45,5 |
3,5 |
14,0 |
35 |
1,5 |
265,0 |
56,7 |
5,0 |
20,0 |
25 |
2,5 |
327,5 |
70,2 |
7,5 |
30,0 |
15 |
5,0 |
402,5 |
86,7 |
12,5 |
50,0 |
5 |
12,5 |
465,0 |
100,0 |
25,0 |
100,0 |
Рис. 8.2. Диаграмма Парето для изделий, хранящихся на складе
Построение таблицы накопленных частот осуществляют следующим образом.
Первый этап. Находят общую стоимость изделий как сумму произведений для значений центров классов и числа изделий, перемножая значения столбцов 1 и 2, т. е.
общая стоимость = 95·200+85·300 + 75·500 + ... + 15·5000 + + 5·12500 = 465,0 тыс. руб.
72
Второй этап. Составляют данные столбца 3. Например, значение из первой строки 19,0 тыс. руб. определяется следующим образом: 95·200 = 19 тыс. руб. Значение из второй строки, равное 44,5 тыс. руб., определяется так: 95·200 + 85·300=44,5 тыс. руб. и т. д.
Затем находят столбец 4, который показывает, сколько процентов от общей стоимости составляют данные каждой строки.
Третий этап. Данные столбца 6 образуются следующим образом. Значение 0,8 из первой строки представляет собой количество процентов, приходящихся на накопленный запас изделий (200), от всего количества изделий (25000). Значение 2,0 из второй строки представляет собой количество процентов, приходящихся на накопленный запас изделий (200+300), от всего количества изделий и т. д
После проведения этой подготовительной работы несложно построить диаграмму Парето.
В прямоугольной системе координат по оси абсцисс отложим относительную частоту изделий ni/N % (данные столбца 6), а по оси ординат — относительную стоимость этих изделий Стi /Ст % (данные столбца 4). Соединив полученные точки прямыми, получим кривую Парето (или диаграмму Парето), как это показано на рис 8.2.
Кривая Парето получилась сравнительно плавной в результате наличия достаточно большого числа классов. При уменьшении числа классов она становится все более ломаной.
Из анализа диаграммы Парето (рис. 8.2) и табл. 8.2 видно, что на долю наиболее дорогих изделий (стоимость от 300. руб. до 1 тыс. руб. за одно изделие), составляющих 20% общего числа хранящихся на складе изделий, приходится более 50% (56,7%) общей стоимости всей готовой продукции, а на долю группы самых дешевых изделий, если сравнивать предпоследнюю и последнюю строки столбцов, 4 и 6 в табл. 8.2, составляющей 50% от всего количества изделий на складе, приходится всего 13,3% от общей стоимости.
Назовем группу, которая включает изделия стоимостью от 30 до 100 руб. (первые семь строк в табл. 8.2), группой А; группу включающую самые дешевые изделия стоимостью до 10 руб. (последняя строка в табл. 8.2),— группой С; промежуточную группу (восьмая и девятая строки в табл. 8.2), стоимость которой составляет 30% (86,7
— 56,7%) от общей стоимости, - группой В (табл. 8.3.).
73
Таблица 8.3 Таблица АВС-анализа складского запаса изделий
|
Относительная частота |
Относительная стои- |
Группа |
(частость) количества |
мость изделий в груп- |
|
изделий в группе, % |
пе, % |
А |
20 |
56,7 |
В |
30 |
30 |
С |
50 |
13,3 |
Теперь ясно, что контроль изделий на складе будет эффективнее в том случае, если контроль изделий группы А будет самым жестким, а контроль деталей группы С — упрощенным.
Однако ABC-анализ не ограничивается только управлением складскими запасами. Такой анализ широко применяется для контроля за производительностью труда и выпускаемой продукции, для контроля денежных сумм, связанных со сбытом, и т. д.
Диаграмма Парето совместно с ABC-анализом эффективно применяется для выявления главных причин брака. Она может в этом случае выражать результаты расслаивания дефектов по причинам, по условиям, по положению и т. д.
Располагая виды брака в порядке убывания суммы потерь так, чтобы в конце стояли виды, которым соответствуют наименьшие суммы потерь (рис. 8.1,а), и виды, входящие в рубрику «прочие», с помощью ABC-анализа диаграмм Парето (рис. 8.2) выявляют причины брака, имеющие наибольшую долю (наибольший процентный вклад), и намечают мероприятия по их устранению. Так, из анализа рис. 8.2 ясно, что группу А будут составлять сборочные операции, группу В — фотолитография, группу С — все прочие технологические операции изготовления ИС.
Поэтому необходимо подвергнуть тщательному анализу все факторы групп А и В, влияющие на качество изделий, и разработать план мероприятий по улучшению технологического процесса. Сравнивая диаграммы Парето, построенные по статистическим данным до и после улучшения технологического процесса, оценивают эффективность принятых мер.
Но в этом случае для анализа факторов, влияющих на показатель качества изделия, диаграмму Парето целесообразно применять вместе с причинно-следственной диаграммой.
74
9. ПРИЧИННО-СЛЕДСТВЕННАЯ ДИАГРАММА
Как уже ранее отмечалось, качество изделий обеспечивается в процессе их изготовления и является результатом действия системы факторов и причин, составляющих процесс. Все многообразие факторов и причин, составляющих технологический процесс, можно расслаивать с помощью 4М (см. § 6). Поэтому процесс изготовления изделий, влияющий на качество изделия, можно рассматривать как взаимодействие 4М. Зависимость между процессом 4М, представляющим собой систему причинных факторов, и качеством, представляющим собой результат действия этих причинных факторов, можно выразить графически, как показано на рис. 3.18.
Если в результате процесса качество изделия оказалось неудовлетворительным, значит в системе причин, т. е. в какой-то точке процесса, произошло отклонение от заданных условий. Если эта причина может быть обнаружена и устранена, то будут производиться изделия только высокого качества. Более того, если постоянно поддерживать заданные условия хода процесса, то можно обеспечить формирование высокого качества выпускаемых изделий. Важно также, что полученный результат — показатели качества (точность размеров, степень чистоты, значение электрических величин и т. д.) — выражается конкретными данными (поз. 10 на рис. 9.1). Используя эти данные, с помощью статистических методов осуществляют контроль процесса, т. е. проверяют систему причинных факторов. Таким образом, процесс контролируется по фактору качества (поз. 11 на рис. 9.1).
Для производства качественных изделий необходимо наиболее важным показателям качества (являющимся следствием) поставить в соответствие различные факторы производства (составляющие систему причинных факторов). Затем через воздействие на отрицательные факторы правильно подобранными мерами процесс вводят в стабильное состояние. Для этого важно хорошо понимать и контролировать зависимость между характеристиками качества (следствием) и параметрами процесса (системой причинных факторов). При этом удобно использовать причинно-следственную диаграмму, приведенную на рис. 9.2, которую из-за своего внешнего вида часто называют «рыбьей костью» или «рыбьим скелетом».
75

Рис. 9.1. Причинно-следственная диаграмма:
1 — система причинных факторов; 2 — основные факторы производства; В — материалы; 4 — оператор; 5 — оборудование, включая инструменты; 6 — методы операций; 7 — процесс 4М; 8 — следствие; 9 — параметры качества; 10 — показатели качества; 11 — процесс контролируется качеством
Рис. 9.2. Причинно-следственная диаграмма («рыбья кость»): 1 — система причинных факторов; 2 - показатель
качества (следствия)
76
Как показано на рис. 9.2, показатели качества (2), являющиеся «хребтом» этого скелета и в то же время следствием (результатом) различных причин (факторов),— причины А, причины В и т. д. На рис. 9.2 они обозначены стрелками, которые называют «большими костями». Эти причины являются, в свою очередь, следствием других причин: A1 ,A2, ... (для следствия А); В1, Вг, ... (для следствия В) и т. д. («средние кости»). Все они также обозначены стрелками, направленными к соответствующим следствиям. Вторичным причинам могут соответствовать третичные причины — G’1 и т. д. («малые кости»).
При поиске причин важно помнить, что показатели качества, являющиеся следствием процесса, обязательно испытывают разброс. Поиск факторов, оказывающих особенно большое влияние на разброс показателей качества изделия (т. е. на результат), называют исследованием причин.
Таким образом, причинно-следственная диаграмма позволяет выявить и систематизировать различные факторы и условия (например, исходные материалы, условия операций, станки и оборудование, операторы), оказывающие влияние на рассматриваемую проблему (на показатели качества).
Информация о показателях качества для построения диаграммы собирается из всех доступных источников: используются журнал регистрации операций, журнал регистрации данных текущего контроля, сообщения рабочих производственного участка и т. д. При построении диаграммы выбираются наиболее важные с технической точки зрения факторы. Для этой цели широко используется экспертная оценка. Очень важно проследить корреляционную зависимость между причинными факторами (параметрами процесса) и показателями качества. В этом случае параметры легко поддаются корреляции. Для этого при анализе дефектов изделий их следует разделить на случайные и систематические, обратив особое внимание на возможность выявления и последующего устранения в первую очередь причины систематических дефектов.
77

Рис. 9.3. Причинно-следственная диаграмма для анализа дефектов СБИС: Большие «кости» причинных факторов: I — этап проектирования и изготовления фотошаблонов; II — этап переноса, совмещения и проявления рисунков фотошаблонов на подложки СБИС; III — этап 1-й и 2-й термообработок; IV — этап травления топологии и удаления фоторезиста маски.
78
Средние и малые «кости» причинных факторов:
1 — ошибки в техническом задании ТЗ); 2 — невнимательность проектировщика; 3 — сбои в работе оборудования; 4 — сбои в работе генератора изображения; 5 — искажение объектива; 6 — сбои координатного стола фотоповторителя; 7 — сбои в работе ЭВС; 8 — низкое качество фотопластин; 9 — скрытые дефекты в стекле; 10 — некачественный фотоэмульсионный слой; 11 — несоответствие контрастности, разрешающей способности и т. д. фотопластин техническому условию (ТУ); 12 — нарушение условий хранения, транспортировки и т. д. фото пластин; 13 — недостаточная производственная чистота; 14 — погрешность контрольно-измерительного оборудования; 15 — снижение качества фотошаблонов в процессе эксплуатации; 16 — загрязнение фотошаблонов; 17 — осколки кремниевых пластин; 18 — загрязнение используемыми химическими реактивами; 19 — износ фотошаблонов; 20 — повреждение маскирующего слоя при отмывке фотошаблонов; 21 — проявление заложенных скрытых дефектов фотошаблонов; 22 — погрешности контактной фотолитографии; 23 — недостаточный зазор при совмещении; 24 — слишком плотный контакт; 25 — пропущенный брак фотошаблонов; 26 — нарушение режимов проявления и экспонирования; 27 — переэкспонирование; 28 — перепроявление; 29 — несоблюдение режимов термообработок; 30 — повышенная температура 2-й сушки (расплывание фоторезиста); 31 — превышение времени сушки (растрескивание и т. д.); 32 — загрязнение подложек; 33 — попадание на подложки окалины из оборудования для сушки; 34 — несоблюдение оператором технологических норм; 35 — нарушение технологических режимов травления и удаления фоторезиста, 36 — перетравление; 37 — несоблюдение концентрации травителя; 38 — износ оборудования; 39 — ошибки технологов и операторов; 40 — ошибка в выборе методов травления и удаления фоторезиста; 41 — ошибка в выборе травителя; 42 — ошибка в выборе режимов; 43 — проявление скрытых дефектов, заложенных на предыдущих операциях; 44 — контроль, 45 — погрешности оператора; 46 — погрешности методик контроля; 47 — случайные факторы; 48 — уровень профессионализма обслуживающего персонала; 49 — обучение и практика, 50 — работает постоянно или временно; 51 — уровень мастерства; 52 — стаж работы, 53 - одежда; 54 — личные достижения; 55 — подготов-
79