
2742
.pdf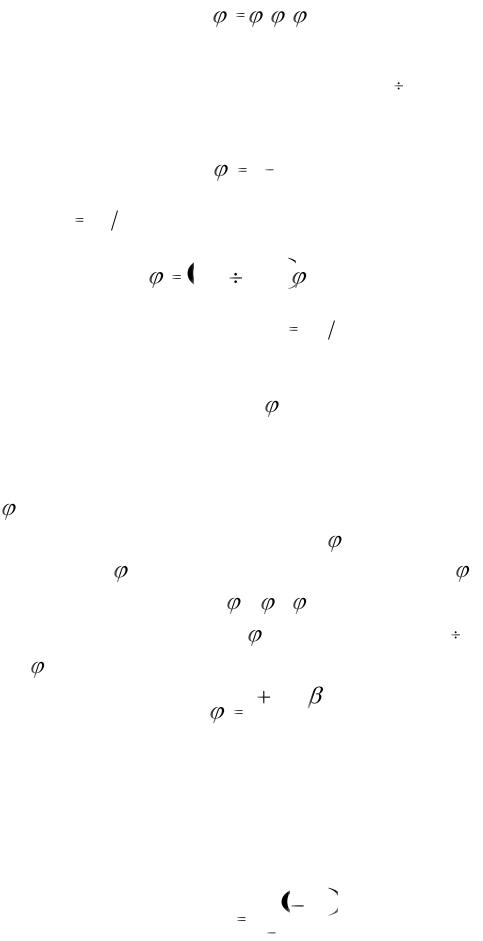
11
k c тепл
На данном этапе проектирования значения отдельных составляющих потерь следует избирать на основании рекомендаций работ [1,2,3]. Несовершенство сгорания оценивается величиной коэффициента 0,96 0,99. Если для камеры сгорания предусматривается внутреннее охлаждение плѐночными завесами, то потери, связанные с этим видом охлаждения, рекомендуется оценивать по формуле:
|
|
|
|
З |
1 0,6g З |
(3.2) |
|
где: |
|
m m |
|
|
|
|
|
|
З |
|
|
|
|
|
|
g |
|
З КС |
- относительный расход охладителя через кольца завесы; |
||||
mЗ - расход охладителя через кольца завесы. |
|
||||||
Таким образом, |
k |
0,96 |
0,99 |
. |
|
||
|
|
|
|
|
З |
|
Тепловые потери определяются в основном величиной безразмерной площа-
ди цилиндрической части камеры: |
f K F K |
F КР . |
|
|
|||||||
FК |
и F КР - площади цилиндрической части и критического сечения камеры |
||||||||||
соответственно. |
|
|
|
|
|
|
|
|
|
||
При |
определении |
величины |
тепл |
следует руководствоваться данными |
|||||||
|
|
|
|
|
|
|
|
|
|
|
|
табл.3.1 |
|
|
|
|
|
|
|
|
|
||
Таблица 3.1 |
|
|
|
|
|
|
|
|
|
||
f K |
|
|
1,5 |
|
|
3,0 |
|
|
5,0 |
|
7,0 |
тепл |
|
|
0,992 |
|
0,9987 |
|
|
0,9996 |
|
0,9998 |
|
|
|
|
|
|
|
|
|
|
|
|
|
|
|
|
|
|
|
||||||
На расчѐтных режимах потери в сопле |
|
складываются в основном из по- |
|||||||||
|
|
|
|
|
|
|
|
c |
|
|
|
терь на трение |
и потерь на непараллельность истечения |
|
, так что: |
||||||||
|
|
|
тр |
|
|
|
|
|
|
a |
|
|
|
|
|
= |
|
|
|
|
|
|
|
|
|
|
|
|
c |
тр |
a |
|
|
|
|
Обычно для сопел величина |
лежит в пределах 0,98 |
0,995, а коэффици- |
|||||||||
|
|
|
|
|
|
тр |
|
|
|
|
|
ент |
рекомендуется рассчитывать по формуле: |
|
|
||||||||
a |
|
|
|
|
|
|
|
|
|
|
|
|
|
|
|
1 |
cos |
a |
|
|
|
|
|
|
|
|
|
|
a |
2 |
|
|
|
|
|
|
|
|
|
|
|
|
|
|
|
|
где:
- угол между образующей сопла и его осью на срезе, обычно pа=150-
a
300.
Наличие внутреннего охлаждения приводит к тому, что среднекамерное соотношение компонентов Кк отличается от головочного Кг. При использовании на плѐночное охлаждение горючего коэффициент камерного соотношения компонентов равен:
K Г 1 |
gЗ |
(3.3) |
|
Kk 1 g |
З K |
|
|
Г |
|
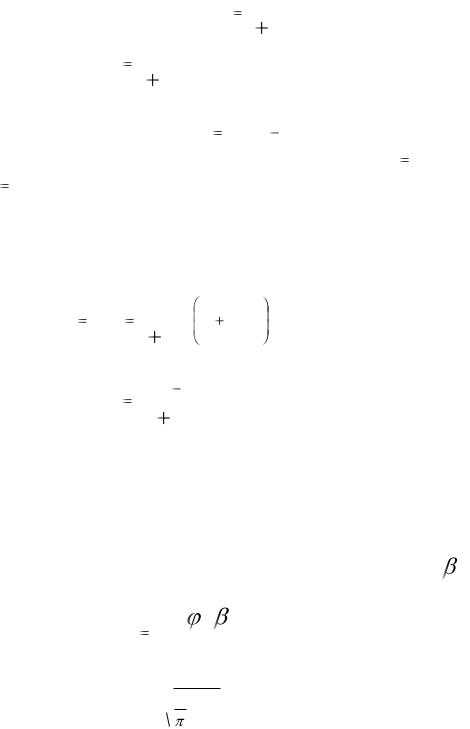
12
Значением g З следует задаваться в пределах 2-4%.
Таким образом, определяют значения расходов компонентов на камеру сго-
рания. |
|
|
|
|
|
|
|
А. Формулы для двигателя открытой схемы: |
|
||||||
- суммарный расход компонентов mКС |
- (3.1); |
|
|||||
- расход окислителя (на головку) mО.КC |
|
K K |
mКС ; |
||||
|
|
||||||
|
|
|
|
|
1 K K |
||
- расход горючего mГ .КC |
|
|
1 |
mКС ; |
|
|
|
1 |
K K |
|
|
|
|||
|
|
|
|
|
- расход горючего на завесу mЗ g З mКС ;
- расход горючего на головку mГ .ГОЛ |
mГ .КС |
mЗ |
|
|
- расход |
горючего на наружное |
охлаждение mОХЛ |
mГ .КС или |
|
mОХЛ |
mГ .ГОЛ |
|
|
|
Б. Формулы для двигателя замкнутой схемы (окислительный газогенератор):
-суммарный расход компонентов mКС - (3.1)
-расход окислителя (газообразного) равен расходу компонентов в газогене- ратор mГГ
ГАЗ |
|
|
K K |
|
1 |
|
|
mО.КС |
mГГ |
|
|
1 |
|
|
mКС , |
1 K K |
K |
|
|||||
|
|
|
ГГ |
( К ГГ - коэффициент соотношения компонентов в газогенераторе);
- расход горючего m |
K ГГ |
K K |
1 |
m ; |
1K K K ГГ КС
-остальные значения расходов mЗ , mГ .ГОЛ , mОХЛ определяются также, как и
для двигателя открытой схемы.
3.2. Определение геометрических параметров камеры
Площадь критического сечения Fкр определяется из известной по результа-
там термодинамического расчѐта величины теоретического комплекса |
(или |
||||
|
|
|
|
|
* |
характеристикой скорости): |
|
|
|
|
|
|
КС |
К t |
|
|
|
FКР |
m |
|
(3.4) |
||
|
PK |
||||
|
|
|
Соответственно диаметр критического сечения DКР равен:
DКР 4 F КР .
Размеры цилиндрической части камеры должны быть минимальными, однако достаточными для того, чтобы энерговыделение прошло по возможности полностью. Поскольку процессы смесеобразования и сгорания сложны и в настоящее время нет их точного аналитического описания, для определения гео-
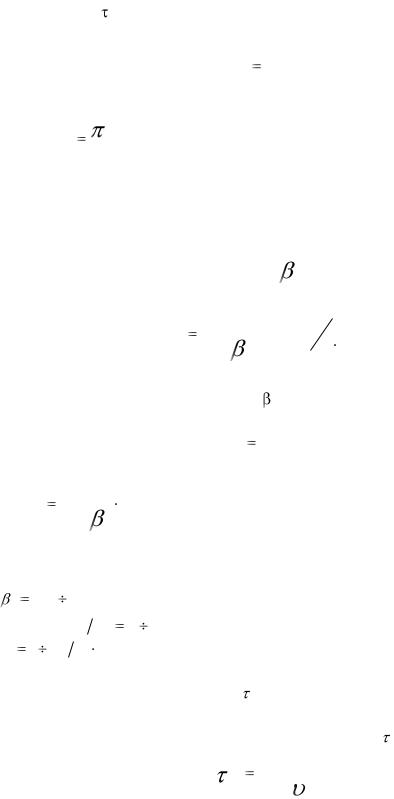
13
метрии цилиндрической части используют некоторые рекомендации, основанные на опыте создания и доводки ряда двигателей.
Параметрами, позволяющими оценить степень завершенности процессов в камере являются расходонапряжѐнность r, условное время пребывания рабочего тела в камере усл и приведѐнная длина камеры Lпр.
Расходонапряжѐнность камеры определяется формулой:
r |
mКС |
, |
(3.5) |
|
|||
|
F K |
|
где:
F K |
D2K |
- площадь поперечного сечения цилиндрической части, |
|
4 |
|||
|
|
DK – еѐ диаметр (см. рис. 3.1).
Величина r показывает величину массового расхода топлива через единицу площади цилиндра камеры. Из формулы (3.4) следует:
mКС F КР pК ,
тогда:
r |
F КР |
103 pK |
г |
|
2 , |
(3.5а) |
|
см |
|||||
|
F к |
с |
|
|
||
|
|
|
|
|
В формуле (3.5а) величина давления pk измеряется в кг/см2. Так для данного вида топлива величина комплекса примерно постоянна, то расходонапряжѐнность камеры пропорциональна давлению в камере:
|
|
|
r rР pK , |
(3.5б) |
|
где: |
|
||
rР |
|
F КР |
103 - называется относительной расходонапряжѐнностью. |
|
|
|
|
||
|
|
F К |
|
Величина r Р зависит только от вида топлива и отношения площадей F КР F К . Для применяемых топлив величина комплекса
колеблется в узких пределах:
170 240 сек, а конструкции работающих камер характеризуются отноше-
нием |
FКР |
FК |
2 4 . |
Поэтому |
установлена |
оптимальная |
величина |
rР 1 |
2 г кг |
сек , |
которая может использоваться с учѐтом формул (3.5)-(3.5б) |
||||
определения диаметра камеры. |
|
|
|
||||
Условное время пребывания усл |
определяет величину времени, в течение ко- |
торого рабочее тело находится в камере и которое используется для совершения
процессов смесеобразования и сгорания. Величина |
усл определяется формулой: |
|||
|
V K |
, |
(3.6) |
|
усл mКС К |
||||
|
|
где:
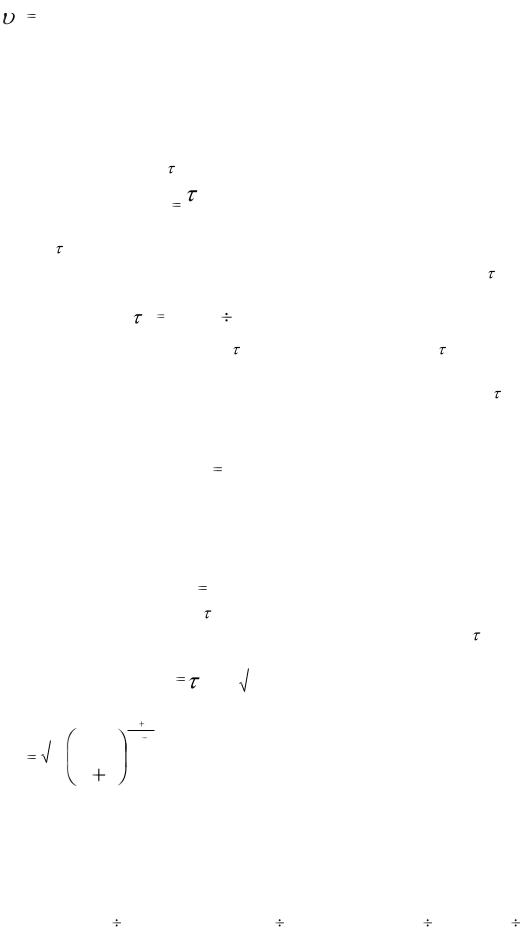
14
К |
RK T K - удельный объѐм рабочего тела в камере при условии его |
pK |
|
|
полного сгорания ( pK ,T K , RK - давление, температура и газовая постоянная рабочего тела);
V K - объѐм камеры, под которым понимается объѐм, ограниченный плоскостью форсуночного днища и плоскостью, проходящей через критическое се-
чение сопла (см. рис.3.1). |
|
|
|
|
При известной величине |
усл легко вычисляется объѐм V K : |
|
||
V K |
|
усл mКС RK T K |
, |
(3.7) |
|
|
|||
|
|
pK |
|
Значение усл зависит от вида применяемого топлива и качества смесеобразования. Для различных типов топлив и конструкций камер величина усл опре-
деляется экспериментально и находится в пределах:
усл 0,0015 0,005сек
Увеличение давления уменьшает усл . При выборе величины усл необходимо также учитывать схему установки. В двигателях с дожиганием часть топлива по-
ступает в камеру в газообразном состоянии, поэтому для таких камер усл |
при- |
мерно в 1,5 раза меньше, чем для двигателей, работающих без дожигания. |
|
Понятие приведѐнной длины камеры Lпр вводится соотношением: |
|
V К , |
(3.8) |
LПР FКР |
|
из которого следует, физически Lпр – длина цилиндрической камеры с объѐмом Vк, равным объѐму действительной камеры, и диаметром Dкр, равным диаметру минимального сечения сопла. Зная величину Lпр, легко определить объѐм
Vк.
V К FКР LПР , |
(3.8а) |
Величина Lпр, как и величина усл, зависит от вида топлива, конструкции форсуночной головки и типа схемы двигателя. Между величинами Lпр и усл существует однозначная связь:
|
|
|
|
Lпр усл An Rk T k , |
(3.8б) |
где:
|
|
2 |
||
An |
n |
|||
|
|
|||
|
n 1 |
|||
|
|
|
n 1
2(n 1)
- газодинамическая функция;
n – показатель изоэнтропы.
Рекомендуемая величина Lпр, необходимая для полного сгорания, определяется по результатам испытаний двигателей. Рекомендуемая величина Lпр дана в таблице 3.2
Таблица 3.2
Топливо |
Керосин+кислород |
Водород+кислород |
НДМГ+HNO3 |
NH3+F2 |
Lпр, м |
1,5 2 |
0,25 0,5 |
1,5 2 |
1 1,5 |
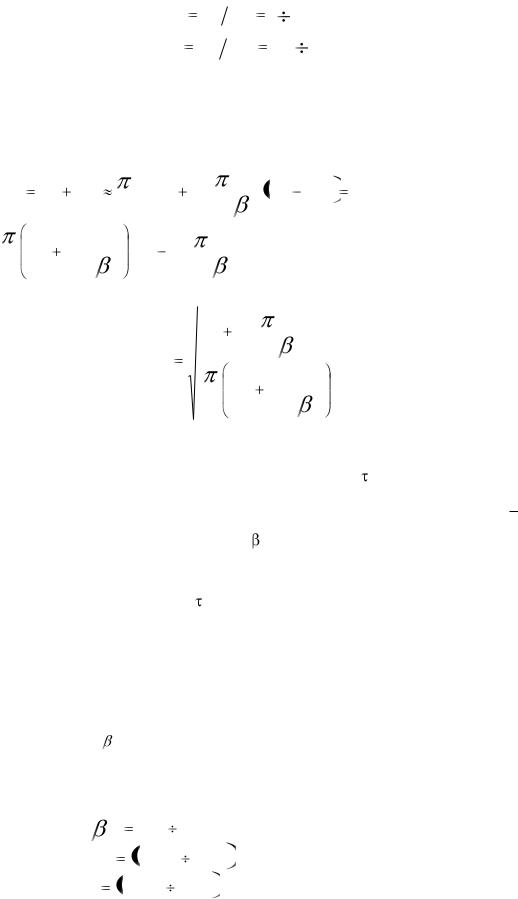
15
Для цилиндрической части камеры геометрические параметры рекомендуется выдерживать в пропорциях:
|
|
|
|
|
1 1,5 , |
Lk |
k |
k |
|||
L D |
|
||||
f k |
Fk |
Fкр |
1,5 4 |
Для удобства расчѐтов удобно иметь зависимость, связывающую объѐм камеры Vк с диаметром цилиндрической части Dк. Схема камеры показана на рис.3.1. Из неѐ следует, что объѐм Vk складывается из объѐма цилиндрической части Lц и объѐма входной части сопла Vвх, которая приближѐнно может быть представлена в виде усечѐнного конуса, т.е:
|
|
|
|
|
|
|
|
2 |
|
|
|
|
|
|
|
|
|
|
|
|
|
|
|
|
|
|
V k V ц |
V вх |
|
|
Dk |
|
|
|
|
|
|
|
|
|
|
|
|
3 |
3 |
|
|
||||||
|
|
|
Lk |
|
|
|
|
|
|
|
|
Dk |
Dкр |
|||||||||||||
|
|
4 |
|
24tg вх |
||||||||||||||||||||||
|
|
|
|
|
1 |
|
|
D3 |
|
|
|
|
|
|
|
|
D3кр , |
|
|
|
|
|
||||
|
|
Lk |
|
|
|
|
|
|
|
|
|
|
|
|
||||||||||||
|
|
|
|
|
|
|
|
|
|
|
|
|
|
|||||||||||||
4 |
6tg |
|
|
24tg |
|
|
|
|
|
|
|
|
||||||||||||||
|
|
|
вх |
|
|
вх |
|
|
|
|
|
|
|
|||||||||||||
или: |
|
|
|
|
|
|
|
|
|
|
|
|
|
|
|
|
|
|
|
|
|
|
||||
|
|
|
|
|
|
|
|
|
|
|
|
|
|
|
|
|
|
|
|
|
|
|
|
|
|
|
|
|
|
|
|
|
|
|
|
|
|
|
V k |
|
|
|
|
|
|
|
|
3 |
|
|
|||
|
|
|
|
|
|
|
|
|
|
|
|
|
|
|
|
|
|
Dкр |
||||||||
|
|
|
|
|
|
|
|
Dk |
|
|
|
24tg |
вх |
|||||||||||||
|
|
|
|
|
|
|
|
|
|
|
|
|
|
|
|
|
|
|
|
|
(3.9) |
|||||
|
|
|
|
|
|
|
|
3 |
|
|
|
|
|
|
|
|
|
1 |
|
|||||||
|
|
|
|
|
|
|
|
|
|
|
|
|
|
|
|
|
|
|
|
|
|
|
|
|
|
|
|
|
|
|
|
|
|
|
|
|
|
|
|
|
|
L k |
|
|
|
|
|
|
|||||
|
|
|
|
|
|
|
|
|
|
|
|
|
|
|
|
|
|
|
|
|
||||||
|
|
|
|
|
|
|
|
|
|
|
|
|
|
4 |
|
6tg |
вх |
Исходя из изложенного, можно использовать следующую последовательность расчѐта по определению размеров цилиндра:
1)Задаться рекомендуемой величиной Lпр (или усл) и определить необходимый объѐм Vk (формулы (37),(37а))
2)По формуле (39) определить диаметр Dk, задавшись величиной L k . Реко-
мендации по определению величины вх см. ниже.
3) Определить площадь цилиндрической части Fk и рассчитать расходонапряжѐнность r.
Если расчѐтные значения усл, Lпр, r и др. не соответствуют рекомендуемым, геометрические размеры скорректировать и расчѐты повторить.
3.3. Профилирование входной (дозвуковой части сопла)
Входная часть сопла проектируется из условия отсутствия входных потерь. Основными геометрическими параметрами входной части являются: угол
входа в сопло - 2 ВХ , радиус скругления критической части сопла – RСКР и ради-
ус скругления входной части сопла – R1 (см. рис.3.1).
Для того, чтобы потери отсутствовали указанные геометрические параметры должны находиться в пределах:
2 ВХ 450 1000
RСКР 0.65 1.0 DКР R1 0.35 0.5 DК
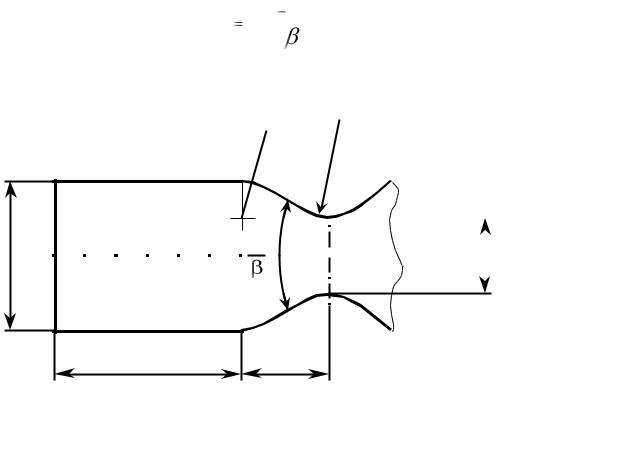
16
Длина входной части сопла: LВХ |
DK DKР |
||||||
2tg ВХ |
|||||||
|
|||||||
|
|
|
|
|
Rскр |
||
|
|
R1 |
|||||
|
|
|
|
|
|
|
|
|
|
|
|
|
|
|
|
|
|
|
|
|
|
|
|
|
|
|
|
|
|
|
|
|
|
|
|
|
|
|
Dк |
|
|
|
|
|
|
Vк |
||||||||
|
|
|
|
|
|
|
|
|
|
|
|
|
2 |
||
|
Lk |
Dкр вх
Lвх
Рис.3.1
4.Смесеобразование и проектирование форсунок
4.1.Общие положения и проектирование системы смесеобразова-
ния
Система смесеобразования в камере сгорания реализуется в виде конструк- ционно-технологического узла, называемого головкой и форсунками.
Качество процессов смесеобразования должно удовлетворять следующим требованиям:
1.Обеспечение возможно равномерного по сечению камеры соотношения компонентов Кг и расходонапряжѐнности r.
2.Обеспечение достаточной мелкости распыла и перемешивания компонентов с целью получения возможно полного сгорания топлива.
3.Тепловая защита стенок камеры осуществляется в виде периферийного ряда форсунок, подающих избыток горючего (по сравнению с центральными форсунками) и создающими защитный пристеночный слой газа с пониженными соотношениями компонентов Кпс и температурой.
4.Тепловая защита огневого днища и др.
Наибольшее применение для двигателей больших тяг находят плоские форсуночные головки. Такие головки представляют собой систему двух плоских и одного выпуклого днища: плоское днище, обращѐнное к объѐму камеры называют огневым, второе плоское днище называют средним.
В пространство между огневым и средним днищем обычно поступает охладитель (горючее) из регенеративной системы охлаждения и оно является коллек-
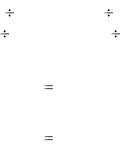
17
тором для раздачи горючего по форсункам. В пространство между средним и выпуклым днищем подаѐтся второй компонент (окислитель) и это пространство является коллектором откуда окислитель поступает на свои форсунки.
В двигателях замкнутых схем выпуклое днище может отсутствовать, его заменяет газовод, подводящий рабочее тело после турбины (газообразный окислитель например).
Впрыск и подготовка топлива к сгоранию осуществляется форсунками, расположенными на головке. В двигателях обычно применяют два типа форсунок: струйные и центробежные. Достоинством струйных форсунок является их конструктивная простота и большая пропускная способность по сравнению с центробежными. Однако центробежные форсунки обеспечивают более качественное смесеобразование (меньшая дальнобойность и более тонкий распыл), поэтому им отдаѐтся предпочтение.
Широко применяют двухкомпонентные форсунки, которые представляют смесительный элемент для обоих компонентов и являются комбинацией двух центробежных или центробежной и струйной форсунок. Двухкомпонентные форсунки применяют также на двигателях замкнутых схем.
Таким образом, проектирование системы смесеобразования следует начинать
собоснованного выбора типа форсунок:
-струйная или центробежная;
-однокомпонентная или двухкомпонентная
Примеры конструкций форсунок различных типов приведены в работах
/1,2,3,4,5/.
Равномерность соотношения компонентов и расходонапряженности по поперечному сечению камеры достигается за счѐт правильного геометрического чередования форсунок на плоскости головки. Для однокомпонентных форсунок применяют шахматное или сотовое расположение их на головке, предпочтение отдаѐтся сотовому расположению.
Для двухкомпонентных форсунок способ их расположения на головке может быть произвольным, но чаще применяют расположение по концентрическим окружностям.
Выбрав способ расположения форсунок, определяют число форсунок окислителя nо горючего nг на головке. Для этого производится предварительная компоновка форсунок на головке (окружность диаметром Dk) с принятым шагом Н (расстояние между форсунами). Величина шага Н определяется габаритными размерами форсунки и прочностью головки. Для однокомпонентных форсунок, габаритный размер которых 8 14мм, Н=12 18 мм; для двухкомпонентных форсунок габаритный диаметр 20 30 мм и Н=30 40 мм.
Расход компонентов через одну форсунку равен:
m |
О. Г |
|
О.Ф |
m |
|
n0 |
||
|
||
mГ .Ф |
mГ .Г |
|
nГ |
||
|
После расчѐта форсунок и определения их размеров шаг и число форсунок могут быть скорректированы.
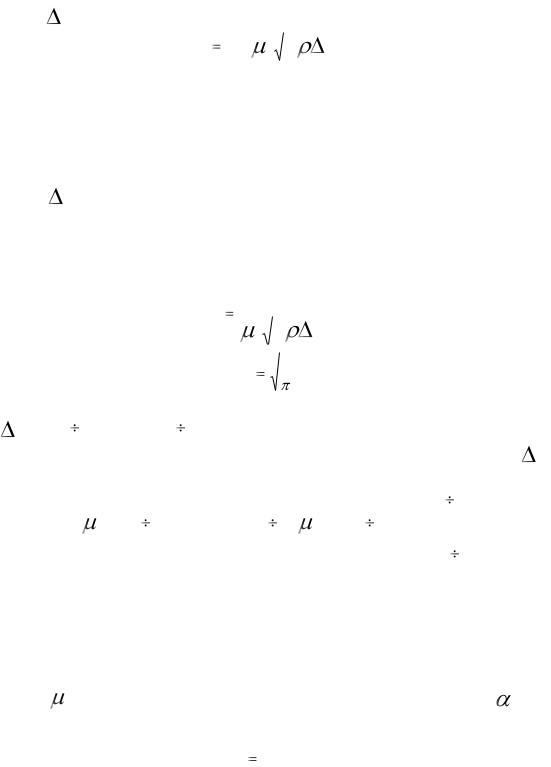
18
Расчѐт форсунки сводится к определению еѐ размеров, обеспечивающих
прохождение заданного расхода |
mФ |
при принятом перепаде давления на фор- |
|||
сунке PФ . Основной расчѐтной формулой является уравнение расхода: |
|
||||
Ф f |
C |
2 |
P |
, |
|
m |
|
Ф |
(4.1) |
||
|
|
|
|
где:
f C - площадь поперечного сечения сопла форсунки, м2;
- коэффициент расхода форсунки, зависит от еѐ типа и геометрии;
- плотность компонента, подаваемого форсункой, кг/м3;
PФ - перепад давления на форсуне.
4.2. Расчѐт струйных форсунок.
Как следует из формулы (4.1), площадь сечения сопла форсунки равна:
f C |
|
|
mФ |
|
(4.2) |
||||
|
|
|
|
|
|
|
|||
2 |
PФ |
||||||||
|
|
|
|
||||||
|
|
|
|
|
|
|
|
||
А диаметр сопла форсунки dC |
|
4 |
f C |
|
|
||||
|
|
|
|
|
|||||
Перепад давления на струйных |
|
форсунках задаѐтся обычно в пределах |
PФ =0.3 1,5 Мн/м2 (3 15кг/см2). Создавать большой перепад давления невы-
годно, т.к. это потребует увеличения давления подачи, а уменьшение P ниже
Ф
0,3 МН/м2 ухудшает качество распыла и смесеобразования. Компонентом задаются в соответствии с размерами форсунки. При lc/dc=0.5 1 (lc – длина сопла форсунки) = 0.6 0.65; при lc/dc=2 3, = 0.75 0.85.
Диаметр сопла струйных форсунок обычно равен dc = 0.8 2.5мм.
4.3. Расчѐт центробежных форсунок.
Конструктивная схема и основные геометрические размеры центробежной форсунки с тангенциальным подводом жидкости показаны на рис 4.1.
Гидравлические характеристики центробежной форсунки (коэффициент расхода - , коэффициент заполнения сопла - и угол распыла - ) определя-
ются в основном геометрической характеристикой А, которая равна:
|
A |
RВХ rС |
(4.3) |
|
|
2 |
|
||
|
|
irВХ |
|
|
где: |
|
|
|
|
rС - радиус сопла форсунки; |
|
|
|
|
RВХ |
- радиус закручивания или расстояние, |
на котором расположены |
||
входные отверстия от оси форсунки; |
|
|||
rВХ |
- радиус входных отверстий; |
|
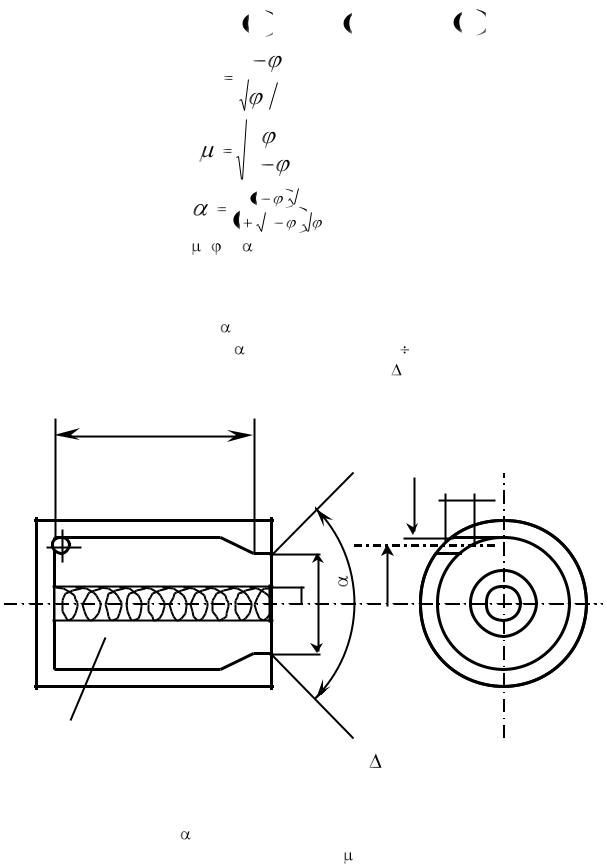
19
i - количество входных отверстий (см. рис 3.1);
Известны зависимости f 1 A ,
f 2 A
и
f 3 A :
|
|
|
|
1 |
|
|
|
, |
|
|
|
|
||||
|
|
|
|
|
|
|
|
|
|
|
|
|
|
|||
|
A |
|
|
|
|
|
|
|
|
|
|
|||||
|
3 |
2 |
|
|
|
|
||||||||||
|
|
|
|
|
|
|
|
|
||||||||
|
|
|
|
|
|
|
|
|
|
|
|
|
|
|
|
|
|
|
|
|
|
|
|
|
3 |
|
|
|
|
|
|
|
|
|
|
|
|
|
|
|
|
|
|
|
, |
(4.5) |
||||
|
|
|
|
2 |
|
|
|
|
|
|
||||||
|
|
|
|
|
|
|
|
|
|
|
|
|
|
|||
|
|
|
|
|
|
|
|
|
|
|
|
|
||||
tg |
|
|
|
1 |
|
8 |
|
|
|
|
||||||
|
|
|
|
|
|
|
|
|
|
|
|
|
|
|
|
|
|
|
|
|
|
|
|
|
|
|
|
|
|
|
|
|
|
1 |
1 |
|
|
|
|
|
|
|
|
|
||||||
|
|
|
|
|
|
|
|
|
|
|||||||
Результаты вычислений , и |
|
|
по формулам (4.5) представлены на графи- |
ках рис.4.2; они могут быть использованы при проведении расчѐтов форсунок. Расчѐт однокомпонентной центробежной форсунки с тангенциальным под-
водом жидкости осуществляется в следующей последовательности:
1. Задаются углом распыла 2 и перепадом давления на форсунках. Наиболее
распространѐнное значение угла 2 лежит в пределах 90 |
1200. Перепад давления |
на центробежных форсунках может достигать величин |
P =2,5 Мн/м2. |
|
ф |
|
h |
|
|
|
rвх |
|
|
Rвх |
|
|
2 |
|
|
rm |
|
|
dc |
|
|
Pk |
жидкость |
газовый |
|
|
|
|
|
вихрь |
Pф |
|
|
|
|
|
Рис. 4.1. |
lвх
= Pвх – Pk
2. Зная значение угла 2 по графикам рис.4.2 находят величины геометрической характеристики А и коэффициента расхода .
3. По уравнению расхода (4.2) определяется площадь fc и диаметр сопла форсунки.
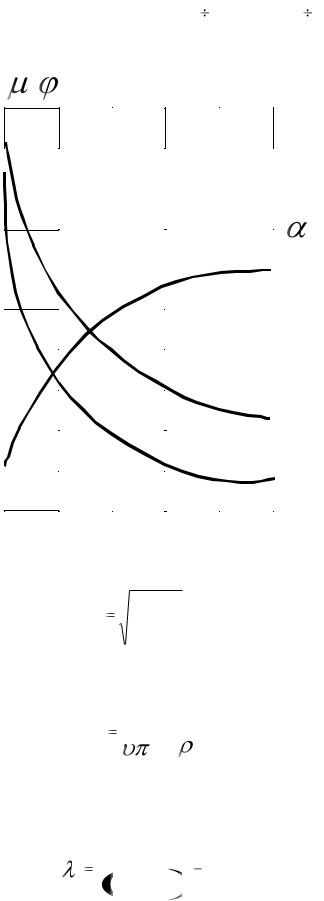
20
4. Из конструктивных соображений задаются количеством входных отвер-
стий i и «плечом» закрутки Rвх/rc. Обычно i = 2 4 и Rвх/rc = 2 3. Тогда из формулы (4.3) для геометрической характеристики легко определить значение радиуса
входных отверстий:
|
, |
|
|
|
|
1.0 |
|
|
|
|
|
0.9 |
|
|
|
|
|
0.8 |
|
|
|
|
|
0.7 |
|
|
|
|
2 |
0.6 |
|
|
|
|
120 |
0.5 |
|
|
|
|
100 |
0.4 |
|
|
|
|
80 |
0.3 |
|
|
|
|
60 |
0.2 |
|
|
|
|
40 |
0.1 |
|
|
|
|
20 |
0.0 0 |
2 |
4 |
6 |
8 |
A |
|
|
|
Рис. 4.2 |
|
|
|
|
rВХ |
RВХ rС |
|
|
|
|
|
|
|
|
|
|
|
iA |
|
|
На этом заканчивается расчѐт форсунки первого приближения. Далее учитывается слияние трения на процессы в форсунке.
5. Определяется число Рейнольдса во входных отверстиях форсунки
ReВХ |
4mФ |
|
d ВХ |
||
|
где:
- коэффициент кинематической вязкости компонента, м2/с; и коэффициент трения
для условий входа в форсунку
lg |
25.8 |
2 |
2.58 |
||
|
lg Reвх |
|
6. Вычисляется эквивалентная характеристика форсунки А по формуле: