
2832.Теория и технология получения наноструктурированных компактных мате
..pdf3.3. Моделирование процесса закалки плоской струи расплава
Получение аморфных сплавов методом закалки плоской струи расплава на сегодняшний день можно считать одним из наиболее перспективных. В связи с этим ученые проводят исследования в направлении развития этого метода. Одним из путей таких исследований является математическое моделирование процессов, происходящих при закалке жидкого металла. Построение адекватных математических моделей должно, в перспективе, уменьшить количество натурных экспериментов, сократить время отработки технологий и снизить стоимость разработки новых материалов и отработки технологии закалки.
Сотрудниками НТЦ «Электронтех» (г. Черноголовка) предложена математическая модель процесса формирования аморфной ленты при закалке плоской струи расплава на поверхности вращающегося бараба- на-холодильника. Модель построена на применении балансового подхода к решению уравнений гидродинамики и теплопроводности. Она позволяет рассчитать динамику геометрических характеристик зоны формирования, включая толщину ленты, среднюю температуру зоны, а также их зависимость от технологических параметров и физических свойств расплава 11 .
Теоретически процесс формирования аморфной ленты можно описать системой уравнений неразрывности, Навье–Стокса и теплопроводности, дополненных начальными и граничными условиями 12 . С учетом сделанных допущений полученная система уравнений ограничивается соплом, барабаном-холодильником, границами расплав – газ и лента – газ (рис. 3.7).
На основе данной системы уравнений построена модель процесса формирования аморфной ленты, описывающая форму жидкой зоны и зависимость толщины ленты от технологических параметров и физических свойств в стационарном и нестационарном режимах. Модель также описывает теплофизические и гидродинамические процессы, протекающие внутри зоны формирования ленты.
Состояние ленты на выходе из зоны формирования определяется выбранным режимом (см. рис. 3.7): при гидродинамическом режиме на выходе из зоны лента «жидкая», при теплофизическом режиме – «твердая». С практической точки зрения гидродинамический режим нереализуем технологически, «жидкая» лента просто не будет держаться на поверхности вращающегося барабана. Теплофизический режим является слишком
41
elib.pstu.ru
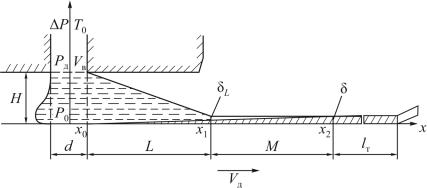
жестким из-за вынужденной синхронизации подачи расплава и процесса затвердевания. В первом случае барабан работает как вентилятор, разбрызгивая расплав, а во втором – из-под сопла будет выходить поток затвердевших чешуек. Оптимальным будет смешанный режим, когда при переносе импульса от барабана в зону формирования теплоперенос и гидродинамика вносят равный вклад, и на выходе из зоны формирования лента будет«твердая», примернонаполовину толщины.
– жидкая форма формирования ленты;
– аморфная лента
Рис. 3.7. Схема зоны формирования ленты: H – зазор между соплом и барабаном-холодильником; d – толщина сопла; T0 – температура разливки; P – приложенное давление; Vв – скорость выхода расплава из сопла; Vд – скорость вращения барабанахолодильника; L – длина зоны формирования ленты; M – длина двухфазного участка ленты толщиной ; lт – длина теплового
контакта ленты с поверхностью барабана-холодильника
Модель позволяет рассчитать временные зависимости всех интересующих характеристик процесса закалки при постоянных параметрах, а также зависимости геометрических характеристик зоны формирования ленты и ее средней температуры от технологических параметров и типа разливаемого расплава (рис. 3.8).
Особое место среди аморфных материалов, получаемых методом закалки плоской струи расплава, занимают сплавы на основе кобальта с близкой к нулю магнитострикцией, имеющие чрезвычайно низкие потери на перемагничивание и высокие значения магнитной проницаемости. Использование этих сплавов в радиоэлектронной промышленности в качестве магнитопроводов обеспечивает создание устройств нового поколения, параметры которых основываются на уникальности свойств кобаль-
42
elib.pstu.ru
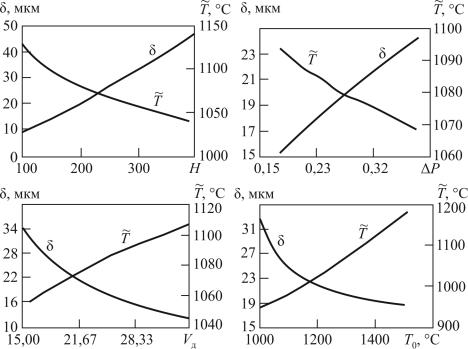
товых аморфных магнитно-мягких сплавов. В связи с этим в производстве аморфных сплавов прослеживается четкая тенденция к расширению выпуска магнитно-мягких высококачественных аморфных лент для изготовления малогабаритных магнитопроводов. Такие ленты при заданной толщине должны иметь высокие магнитные свойства и минимальное количество топологических дефектов поверхности, которые являются характерной особенностьюлент, получаемых закалкойиз расплава.
Рис. 3.8. Зависимость толщины ленты и средней температуры жидкой зоны формирования ленты от технологических параметров процесса закалки
Результаты исследований аморфных металлических лент показывают, что технологические параметры процесса закалки расплава играют определяющую роль в формировании свойств аморфных сплавов.
Целенаправленно изменяя условия охлаждения на стадиях получения аморфных лент, можно управлять уровнем их магнитных свойств. Следовательно, для адекватного описания влияния условий получения и последующей термической обработки на магнитные свойства аморфных сплавов необходимо изучить сам механизм формирования аморфной ленты методом закалки плоской струи расплава.
43
elib.pstu.ru
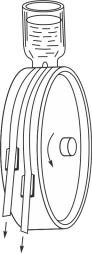
Наиболее эффективно изменять тепловые условия закалки можно путем изменения длины теплового контакта ленты с поверхностью ба- рабана-холодильника и толщины получаемой ленты. Влияние этих параметров на магнитные свойства изучали на аморфных лентах из сплава Co57Fe5Ni10SinB17 с близкой к нулю магнитострикцией [13].
Для получения ленты разной толщины из сплава Co57Fe5Ni10Si11B17 и различной длины теплового контакта использовали специальные «двойные» ампулы (рис. 3.9). Расплав одновременно через оба формирователя струи выдавливали на барабан-холодильник, а принудительный съем осуществляли с помощью специальных ножей при различной длине теплового контакта.
Определяли магнитные свойства лент разной толщины, полученных при различной длине теплового контакта.
В начале процесса лента самопроизвольно сходит с барабана, при этом длина теплового контакта не превышает 3–6 см. Вследствие этого начальные участки всех лент имеют приблизительно одинаковый уровень свойств. Коэффициент прямоугольности петли гистерезиса этих лент Вr/Вs ≈ 0,5, коэрцитивная сила Нс ≈ 0,8–1,2 А/м, начальная магнитная проницаемость 5000–7000. Но уже на пятом обороте лента «залипает» на поверхности
подложки, что дает возможность контроля и поддержания заданной длины теплового контакта.
Было установлено, что для каждой толщины ленты существует некоторая длина контакта, превышение которой приводит к резкому изменению магнитных свойств ленты.
Ленты толщиной 10 < δ < 20 мкм (тонкие ленты), полученные на длине теплового контакта lт = 5 см, обладали следующими свойствами: Br/Bs ≈ 0,5, Hc ≈ 0,8 А/м, е ≈ 7000, которые практически не изменялись по всей длине ленты. В случае получения лент с lт = 24 см наблюдалось
44
elib.pstu.ru
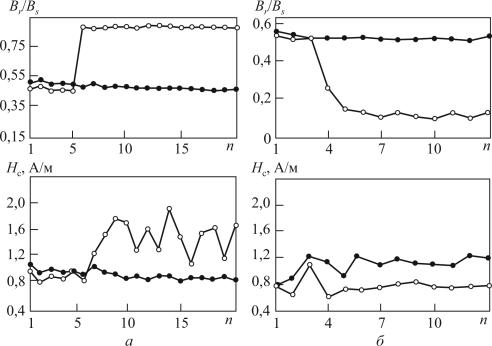
резкое увеличение Br/Bs до значений, близких к 1. При этом увеличивались значения Нc (до 2,0 А/м) и их разброс, а магнитная проницаемость снижалась до е = 400 (рис. 3.10, а).
Рис. 3.10. Зависимость прямоугольности петли гистерезиса Br/Bs и коэрцитивной силы Нc ленты Co57Fe5Ni10Si11B17 от числа оборотов барабана-холодильника 13
Ленты толщиной 25 < < 35 мкм (толстые ленты), полученные с коротким сходом lт = 5 см, имели практически такую же форму петли гистерезиса, что и тонкие ленты, однако наблюдалось увеличение разброса и ухудшение значений Нc и е. У лент с длинным сходом lт = 24 см наблюдались изменения, противоположные изменениям в тонкой ленте. Коэффициент прямоугольности петли гистерезиса снижался до 0,1 (рис. 3.10, б), и петля гистерезиса становилась практически линейной. Значительно повышалась начальная магнитная проницаемость до е = 18 000.
Таким образом, свойства начальных участков лент разных толщины и длины схода приблизительно одинаковы. Это связано с тем, что во всех случаях мы фактически имеем короткий сход. На основе численного моделирования тепловых полей в процессе получения аморфной
45
elib.pstu.ru
ленты было установлено, что температура схода ленты возрастает с уменьшением длины теплового контакта, особенно резко при lт < 3 см. Аморфные ленты при коротком сходе независимо от их толщины сходят с барабана при достаточно высокой температуре, что приводит к развитию процессов структурной релаксации.
Тонкие ленты при большой длине теплового контакта имеют низкую температуру схода, поэтому процесс структурной релаксации в них затруднен. Это подтверждают проведенные калориметрические исследования. В толстых лентах, несмотря на сильный теплоотвод на большой длине lт, температура схода относительно высокая, что приводит к частичному протеканию процессов структурной релаксации. Следовательно, наиболее неравновесное состояние имеют ленты с прямоугольной петлей гистерезиса; наиболее релаксированными являются ленты с петлей гистерезиса, характеризующейся отношением Br/Bs = 0,5. Ленты с линейной петлей гистерезиса соответствуют промежуточному состоянию. Если это так, тогда при получении лент с большой длиной теплового контакта при переходе от состояния Br/Bs ≈ 0,5 (начало ленты) к состоянию Br/Bs ≈ 1 должен быть участок ленты с петлей гистерезиса, приближающейся к линейной. Для подтверждения этого вывода ленту, на которой происходило такое изменение, разрезали на более мелкие образцы, на которых измеряли петлю гистерезиса. Обнаружено, что коэффициент прямоугольности по длине ленты сначала уменьшался от 0,5 до ≈0,2, а затем резко увеличивался до 1,0.
Таким образом, для получения материала с прямоугольной петлей гистерезиса подачу расплава необходимо осуществлять таким образом, чтобы толщина ленты < 20 мкм, а длина теплового контакта lт > 20 см. Для получения ленты с линейной петлей гистерезиса необходимо увеличивать подачу расплава так, чтобы получать ленты с > 25 мкм. Для получения лент с коэффициентом прямоугольности петли гистерезиса ≈0,5 и равномерными по длине свойствами подачу расплава необходимо осуществлять таким образом, чтобы толщина получаемых лент была порядка 20 мкм, а съем ленты с поверхности барабана происходил на расстоянии lт ≈ 5…6 см.
Так как длина теплового контакта lт определяется до начала процесса закалки из расплава, то с практической точки зрения важнейшей задачей является расчет технологических параметров, обеспечивающих получение аморфных лент заданной толщины.
46
elib.pstu.ru
3.4.Влияние деформации и отжига на структуру
исвойства аморфных сплавов
При нагреве аморфных металлов, за счет протекания процессов структурной релаксации, происходит уменьшение свободного объема и возникает топологический и химический ближний порядок. Кроме того, происходит фазовое расслоение и выпадение кристаллов. Структурная релаксация при нагреве до относительно низких температур связана с диффузией на короткие расстояния (кажущаяся энергия активации ≈0,5 эВ). Фазовое расслоение и выделение кристаллов связаны с диффузией на большие расстояния (кажущаяся энергия активации ≈1 эВ). Локальные остаточные напряжения, возникшие в ходе затвердевания расплава, частично устраняются при нагреве до температур ниже температуры кристаллизации.
При термической обработке аморфных сплавов на стадии, предшествующей кристаллизации, наблюдаются изменения физических свойств. Например, хорошо известны соответствующие изменения магнитных свойств и пластичности. При термической обработке с кристаллизацией аморфные металлы практически утрачивают свои отличительные свойства. Это обстоятельство необходимо учитывать при выборе температурных и временных режимов термической обработки с тем, чтобы сохранить присущие аморфным металлам специфические свойства.
Группой исследователей была изучена структура аморфных металлических сплавов на основе железа и кобальта до и после отжига при температурах 573–723 К, а также после деформации прокаткой или одноосным растяжением. Получена температурная зависимость предела прочности и относительного удлинения аморфных сплавов, подвергнутых предварительной термической обработке и без нее. Измерена коэрцитивная сила аморфных металлических сплавов до и после их деформации и отжига 14 .
Тонкие структурные изменения (перераспределение компонентов, вакансий, возникновение неоднородности плотности, выделение фаз) возникают в аморфных металлических сплавах (АМС) в процессе их получения, при последующем отжиге, а также при деформации. Стабильность структуры и свойств АМС, по-видимому, в большой степени зависит от того, насколько существенны эти тонкие изменения структуры в виде образования метастабильных квазикристаллических фаз или изменения морфологии и скорости роста кристаллических фаз при расстекловывании, а также изменения последовательности фазовых превращений, обеспечи-
47
elib.pstu.ru
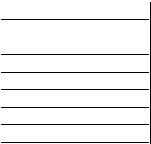
вающего задержку возникновения равновесных кристаллических фаз. Показано 15 , что на стабильность структуры и кристаллизацию АМС влияет предварительная деформация и отжиг. Состав исследованных сплавов приведен в табл. 3.2. Исследования проводили на ленточных образцах (толщиной 25 мкм, шириной 4 мм, длиной 30 мм). Микроструктуру изучали методамисветовойи электронной микроскопии.
Таблица 3 . 2
Состав исследованных сплавов, их температура кристаллизации и температура Кюри
Состав АМС |
Ткрист, К |
Тк, К |
Fe5Co71,8Si15B8.2 |
728 |
691 |
Fe5Co70Si15B10 |
758 |
588 |
Fe5Co68,2Si15B11,8 |
803 |
487 |
Co81,5Mo9,5Zr9 |
823 |
– |
Fe81Si7B12 |
708 |
663 |
Fe60Cr18Ni7Si3B12 |
853 |
– |
Fe81Si4B13C2 |
753 |
– |
Макро- и микроструктура АМС после деформации и отжига.
Висходном состоянии структура аморфных сплавов на основе железа и кобальта, как показали электронно-микроскопические исследования, состоит из плотных и менее плотных областей. Особенности структуры в свежезакаленном состоянии исследованных АМС заключались в различной степени однородности структуры. Это проявилось в различной плотности черно-белого контраста на темнопольных снимках и возникновение областей размером 20–50 нм с более светлым контрастом на светлопольных снимках.
Проведение отжигов в интервале температур 573–723 К практически во всех исследованных сплавах вызывает структурные изменения, сопровождающиеся релаксацией внутренних напряжений. После низкотемпературного отжига структура всех исследованных сплавов остается аморфной, однако картина микродифракции изменяется. Так, в сплавах Fe–Si–В и Со–Mo–Zr микродифракция электронов сопровождается возникновением диффузного гало в малых углах перед основным диффузным гало с присутствием на первом тонких рефлексов, указывающих на выделение в результате низкотемпературного отжига дисперсных кристаллических (возможно, квазикристаллических) фаз.
Всплаве Fe–Сr–Ni–Si–В микродифракция характеризуется расщепле-
48
elib.pstu.ru
нием основного диффузного гало, что, по-видимому, связано с процессами «расслоения» аморфной матрицы сплава. В сплаве Fe–Со–Si–В в аморфной матрице обнаруживаются кристаллы фазы. Отжиг сплавов при 723 К в течение 30 мин приводит к образованию в аморфной матрице дендритных кристаллов и дисперсных кристаллов. При этом на электронограммах присутствуют рефлексы от кристаллической фазы и расшифровываются для сплавов на основе железа, как фаза твердого раствора α-Fe (с В или Si), и для сплавов на основе кобальта, как Со2В. Отжиг при 823 К в течение 30 мин приводит к образованию мелкозеренной кристаллической структуры и появлению кристаллических фаз Fe2B и Fe3Si в сплавах на основе железа. В сплавах на основе кобальта возникают при этом кристаллические зерна размером на два-три порядка больше, чем в сплавах на основе железа, но с очень дисперсной фазой Со2Si и Со2В.
При деформации растяжением АМС сдвиговые полосы обнаруживаются в достаточно малой области деформируемых лент (в месте разрыва). Наблюдается сильная локализация грубых сдвиговых полос. Это косвенно указывает на то, что в сдвиговой полосе идут процессы разупрочнения материала, позволяющие продолжаться деформации в полосе до разрушения.
Эволюция сдвиговых полос при прокатке резко отличается от эволюции сдвиговых полос в аморфном сплаве при деформации растяжением. При прокатке полосы сдвига волнисты, расположены почти перпендикулярно прокатке, обнаруживаются на обеих сторонах ленты по всей поверхности и распределяются неравномерно по ширине и длине ленты [15 . В АМС на основе железа с разным содержанием бора полосы сдвига претерпевают изменения: с увеличением содержания бора наблюдаются более грубые полосы, а их распределение более неравномерное. С ростом степени деформации прерывистые линии сдвига становятся сплошными, между ними возникают новые полосы сдвига. Ранее были изучены методом электронной просвечивающей микроскопии области АМС Fe–Со–Si–В, включающие в себя сдвиговые полосы и микро- и макротрещины, возникшие в результате деформации. Было показано, что в области сжатия сдвиговой полосы происходят структурные перестройки, стимулирующие возникновение зародышей кристаллической фазы. Повышение температуры деформации способствует протеканию этих процессов. Позднее этот факт был подтвержден на деформированных АМС на железной основе, а именно в Fe81Si7B12.
49
elib.pstu.ru
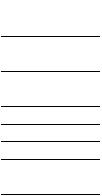
Механические свойства АМС после закалки и отжига. Результа-
ты определения температурной зависимости предела прочности и относительного удлинения свежезакаленных и отожженных при 723 К
втечение 30 мин АМС на железной основе представлены в табл. 3.3, на кобальтовой основе – в табл. 3.4. Как видно из табл. 3.3 и 3.4, механические свойства (предел прочности) достаточно температурно стабильны у сплава Со–Mo–Zr и сплава Fe–Si–В–С, хотя температура кристаллизации у последнего ниже, чем у Со–Mo–Zr. Отжиг при 723 К, 30 мин,
врезультате которого в структуре Со–Mo–Zr сплава выделяются дисперсные кристаллические фазы, приводит к дополнительному повышению прочности сплава (см. табл. 3.4). Подобный отжиг во всех сплавах вызывает немонотонную температурную зависимость предела прочности и в области температур, не превышающих температуру отжига, делает их более температурно стабильными. Повышение предела прочности в некотором узком интервале температур испытания отожженных при 723 К, 30 мин АМС происходит, по-видимому, за счет струкурных превращений (выделяются метастабильные кристаллические и, возможно, квазикристаллические фазы), вызывающих релаксационные процессы и сопровождающихся незначительным увеличением пла-
стичности 14 .
Таблица 3 . 3
Температурная зависимость предела прочности и относительного удлинения АМС на железной основе
Сплав |
Тдеф, К |
Предел прочности, МПа |
Удлинение, % |
||
Закалка |
Отжиг 723 К, |
Закалка |
Отжиг 723 К, |
||
|
|
|
30 мин |
|
30 мин |
Fe81Si7B12 |
293 |
1875 |
1150 |
0,0 |
1,0 |
|
573 |
1507 |
1330 |
1,2 |
3,0 |
|
723 |
952 |
701 |
0,5 |
0,5 |
Fe81Si4B13C2 |
293 |
2078 |
1170 |
0,0 |
0,5 |
|
373 |
1500 |
1190 |
1,0 |
1,0 |
|
473 |
1080 |
1410 |
1,2 |
1,3 |
|
573 |
1080 |
1180 |
1,5 |
2,0 |
Fe60Cr18Ni7Si3B12 |
293 |
3260 |
2860 |
0,0 |
0,5 |
|
573 |
2600 |
2980 |
1,2 |
1,5 |
50
elib.pstu.ru