
- •МЕХАНИКА МАШИН
- •1.1. Структура машинного агрегата
- •1.4. Управление движением машинного агрегата
- •СТРОЕНИЕ МЕХАНИЗМОВ
- •2.1. Основные определения
- •2.2. Кинематические пары и соединения
- •2.5. Структурный синтез механизмов
- •2.6. Классификация механизмов
- •КИНЕМАТИЧЕСКИЕ ХАРАКТЕРИСТИКИ МЕХАНИЗМОВ
- •3.1. Основные понятия
- •tgfa
- •3.6. Примеры графического исследования механизмов
- •pc = fivVB\ Р'Ь" = цайв', Ь"Ь'= цаагВ-
- •3.7. Кинематические характеристики плоских механизмов с высшими парами
- •3.8. Кинематические характеристики пространственных механизмов
- •3.9. Метод преобразования декартовых прямоугольных координат
- •4.1. Динамическая модель машинного агрегата
- •4.2. Приведение сил
- •4.3. Приведение масс
- •4.8. Неравномерность движения механизма
- •JTnp,
- •4.10. Динамический анализ и синтез с учетом влияния скорости на действующие силы
- •5.1. Динамическая модель машинного агрегата
- •5.2. Установившееся движение машинного агрегата
- •5.3. Исследование влияния упругости звеньев
- •СИЛОВОЙ РАСЧЕТ МЕХАНИЗМОВ
- •6.1. Основные положения
- •6.4. Силовой расчет механизма с учетом трения
- •6.5. Потери энергии на трение. Механический коэффициент полезного действия
- •ВИБРОАКТИВНОСТЬ И ВИБРОЗАЩИТА МАШИН
- •7.1. Источники колебаний и объекты виброзащиты
- •7.3. Анализ действия вибраций
- •7.6. Статическая и динамическая балансировка изготовленных роторов
- •Щ = у/g sina/<5CT,
- •7.8. Демпфирование колебаний. Диссипативные характеристики механических систем
- •7.9. Динамическое гашение колебаний
- •тт(р - рт) = mjyE.
- •7.11. Ударные гасители колебаний
- •7.12. Основные схемы активных виброзащитных систем
- •ТРЕНИЕ И ИЗНОС ЭЛЕМЕНТОВ КИНЕМАТИЧЕСКИХ ПАР МЕХАНИЗМОВ И МАШИН
- •8.1. Виды и характеристики внешнего трения
- •8.2. Основные понятия и определения, используемые в триботехнике
- •8.3. Механика контакта и основные закономерности изнашивания
- •8.4. Методика расчета износа элементов кинематических пар
- •МЕТОДЫ ПРОЕКТИРОВАНИЯ СХЕМ ОСНОВНЫХ ВИДОВ МЕХАНИЗМОВ
- •МЕТОДЫ СИНТЕЗА МЕХАНИЗМОВ С ВЫСШИМИ ПАРАМИ
- •9.1. Основные понятия и определения
- •9.2. Основная теорема зацепления
- •9.3. Скорость скольжения сопряженных профилей
- •9.4. Угол давления при передаче движения высшей парой
- •9.5. Графические методы синтеза сопряженных профилей
- •9.7. Производящие поверхности
- •МЕХАНИЗМЫ ПРИВОДОВ МАШИН
- •10.1. Основные понятия и определения
- •10.2. Строение и классификация зубчатых механизмов
- •10.4. Планетарные зубчатые механизмы
- •ЦИЛИНДРИЧЕСКАЯ ЗУБЧАТАЯ ПЕРЕДАЧА
- •11.2. Эвольвента, ее свойства и уравнение
- •11.3. Эвольвентное прямозубое колесо
- •11.4. Эвольвентная прямозубая рейка
- •11.5. Эвольвентное зацепление
- •11.8. Подрезание и заострение зуба
- •11.9. Эвольвентная зубчатая передача
- •11.10. Качественные показатели зубчатой передачи
- •11.11. Цилиндрическая передача, составленная из колес с косыми зубьями.
- •11.12. Особенности точечного круговинтового зацепления Новикова
- •ПРОСТРАНСТВЕННЫЕ ЗУБЧАТЫЕ ПЕРЕДАЧИ
- •12.1. Коническая зубчатая передача
- •МЕХАНИЗМЫ С НИЗШИМИ ПАРАМИ
- •13.1. Основные этапы синтеза
- •13.4. Синтез четырехзвенных механизмов по двум положениям звеньев
- •13.5. Синтез четырехзвенных механизмов по трем положениям звеньев
- •13.6. Синтез механизмов по средней скорости звена и по коэффициенту изменения средней скорости выходного звена
- •tijivu) < [tfj]-
- •КУЛАЧКОВЫЕ МЕХАНИЗМЫ
- •14.1. Виды кулачковых механизмов и их особенности
- •14.2. Закон перемещения толкателя и его выбор
- •sinx4
- •sinx2 = [(*2 “ Vj3)/f34]sm03;
- •14.5. Определение габаритных размеров кулачка по условию выпуклости профиля
- •14.6. Определение координат профиля дисковых кулачков
- •14.7. Механизмы с цилиндрическими кулачками
- •МЕХАНИЗМЫ С ПРЕРЫВИСТЫМ ДВИЖЕНИЕМ ВЫХОДНОГО ЗВЕНА
- •15.1. Зубчатые и храповые механизмы
- •15.2. Мальтийские механизмы
- •15.3. Рычажные механизмы с квазиостановками
- •УПРАВЛЕНИЕ ДВИЖЕНИЕМ СИСТЕМЫ МЕХАНИЗМОВ
- •16.2. Циклограмма системы механизмов
- •МАНИПУЛЯЦИОННЫЕ МЕХАНИЗМЫ
- •17.3. Задачи о положениях манипуляторов
- •17.4. Задачи уравновешивания и динамики
- •Glos
в другой плоскости коррекции. Конечно, возможность приме нения такого приема непосредственно определяется конструк цией ротора.
В заключение рассмотрим ротор, размеры которого вдоль оси вращения малы по сравнению с его радиальными размера ми. Это значит, применительно к рис. 7.9, а, что детали 1 , 2, 3 расположены близко друг к другу, так что размеры а2 и аз ма лы. Тогда, согласно формулам (7.10), дисбалансы Б^в и В будут также малыми и ими можно пренебречь. Следователь но, согласно уравнениям (7.11), DB ~ 0, так что вся неурав новешенность ротора будет выражаться практически только одним дисбалансом Б д и поэтому будет статической. Отсюда вытекает, что и балансировка такого ротора с малыми разме рами вдоль оси вращения должна быть статической. Ее можно выполнить одной корректирующей массой, назначив плоскость коррекции так, чтобы она проходила через центр масс ротора. Добавим, что при малости размеров а2 и аз, т.е. координат z центров масс S2 и 5з (см. рис. 7.9, а), центробежные моменты инерции Jxz и Jyz ротора будут также малы. Следователь но,, согласно уравнению (7.9), малым будет и главный момент дисбалансов Мр такого ротора, так что им можно пренебречь. Это еще раз подтверждает, что неуравновешенность ротора, имеющего малые размеры вдоль оси вращения, практически будет только статической.
7.6. Статическая и динамическая балансировка изготовленных роторов
Полностью сбалансированный при проектировании ротор после изготовления обладает тем не менее некоторой неурав новешенностью, вызванной неоднородностью материала и от клонениями фактических размеров ротора от их номинальных значений. Такая неуравновешенность устраняется в процессе изготовления на специальных балансировочных станках. Ба лансировка может быть как автоматической, так и неавтома тической. Сначала рассмотрим статическую и динамическую балансировки, выполняемые в неавтоматическом режиме.
Статическая балансировка. В § 7.5 было показано, что Для роторов с малыми размерами вдоль оси вращения
(шкивы, маховики, диски и т.п.) допустимо ограничиться ста тической балансировкой. При этом определяется только глав ный вектор дисбалансов DCT. Если требуется невысокая точ ность балансировки, то она выполняется в статическом режи ме.
Более точным и перспективным в отношении автоматиза ции процесса балансировки является способ определения ста тической неуравновешенности в процессе вращения ротора, т.е. в динамическом режиме* Одним из примеров оборудова ния, работающего по этому принципу, служит балансировоч ный станок, изображенный на рис. 7.10. Неуравновешенный ротор i, закрепленный на шпинделе вращается с постоян ной скоростью cjg в подшипниках, смонтированных в плите 2 . Эта плита опирается на станину посредством упругих элемен тов 3 . С плитой 2 с помощью мягкой пружины 5 связана масса 6 сейсмического датчика. Собственная частота колебаний мас сы датчика должна быть значительно ниже частоты вращения ротора. Массе 6 дана свобода прямолинейного перемещения вдоль оси я, проходящей через центр масс 5о плиты.
При вращении шпинделя вместе с ротором ось z под вли янием неуравновешенности ротора описывает коническую по верхность, а плита совершает пространственное движение. Составляющая этого движения, направленная вдоль оси я, вос принимается массой 6. Вынужденные колебания массы отно сительно плиты 2 преобразуются датчиком в ЭДС, направляе мую в электронное счетно-решающее устройство (на рис. 7.10 не показано), являющееся неотъемлемой частью балансировоч ного станка. Это устройство выдает сведения об искомой не уравновешенности в виде модуля и угловой координаты глав ного вектора DCT дисбалансов ротора. (На рис. 7.10 статиче ская неуравновешенность ротора условно представлена в виде
* Отсюда следует, что термин «статическая неуравновешенность» не только очень неудачен, но и попросту устаревает, поскольку современ ные точные и высокопроизводительные балансировочные станки определя ют так называемую «статическую неуравновешенность» в динамическом режиме.
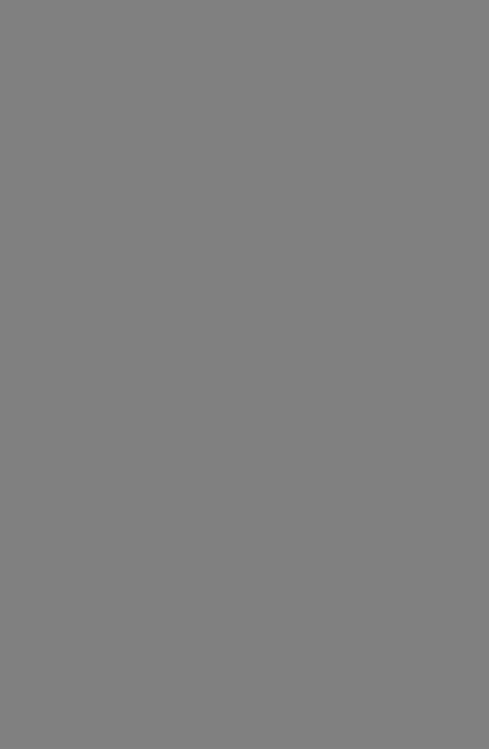
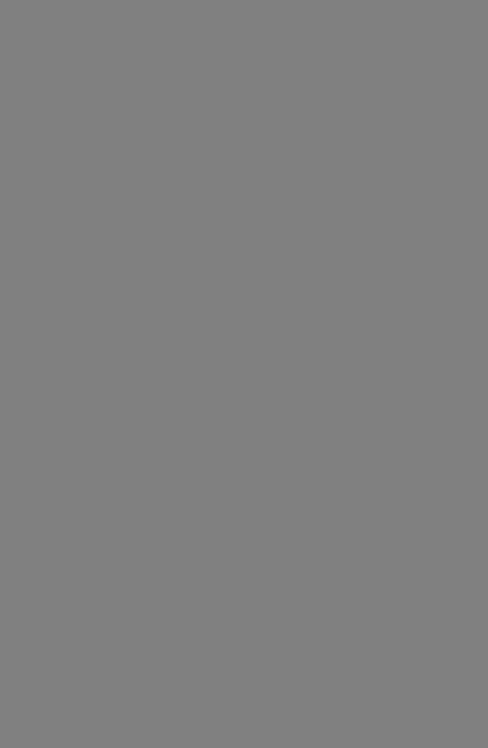
Пример рамного балансировочного станка второй группы, не имеющего электронно-решающих устройств, и описание ра боты на нем имеются в литературе.
Автоматическая балансировка. Станок для автома тической балансировки называют автоматическим, если обе фазы балансировки — как измерение неуравновешенности, так и ее устранение — осуществляются без участия оператора. Возможны два метода автоматической балансировки: дискрет ный метод, когда обе фазы выполняются последовательно, при чем вторая фаза — на неподвижном роторе, и*непрерывный метод, когда обе фазы совмещены во времени и ротор во всем процессе балансировки не останавливается.
Устранять неуравновешенность можно двумя способами: добавлением или удалением корректирующих масс тк\ и тк2 в плоскостях коррекции. Автоматические балансировочные станки, работающие с добавлением корректирующих масс, не обходимы для уравновешивания тонкостенных роторов.
Наиболее распространен способ удаления материала, осу ществляемый путем сверления углублений или фрезерования пазов на роторе, а также другими средствами. Станки, исполь зующие этот способ, описаны ниже. Ось вращения ротора на этих станках неподвижна, и поэтому они относятся к третьей группе.
Автоматический станок для дискретной балансировки обычно состоит из двух агрегатов: измеряющего И и устра няющего У неуравновешенность (рис. 7.12), связанных между собой электронным устройством ЭУ Сведения о неуравнове шенности ротора Р2 подаются в ЭУ от датчиков а и /3 непо движных чувствительных опор А и В. В решающем блоке РБ эти сведения преобразуются в сигналы, эквивалентные дис балансам D\ и в плоскостях коррекции 1 — 1 и 2 — 2 . Сигналы направляются в блоки УБ1 и УБ2 , которые управля ют инструментами, устраняющими дисбалансы в плоскостях коррекции. Но поступившие сигналы пока сохраняются там в памяти, так как в это время происходит устранение дисбалан сов предыдущего ротора Pi путем удаления материала. При этом никакой обратной связи между балансируемым ротором Pi и ЭУ не существует. По завершении балансировки ротор
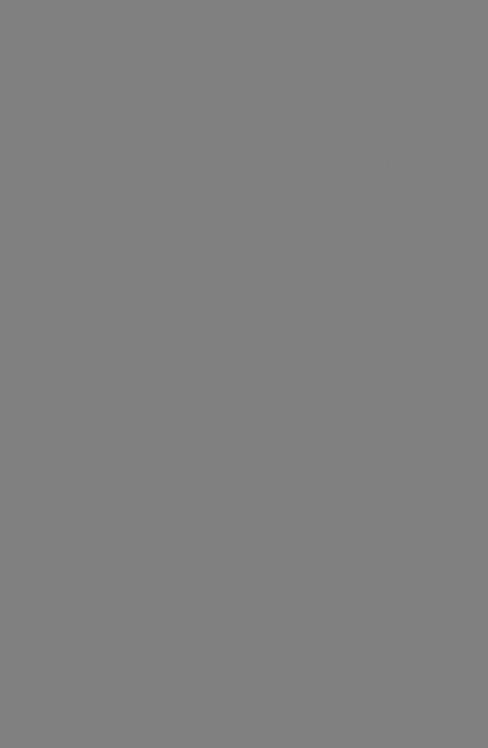
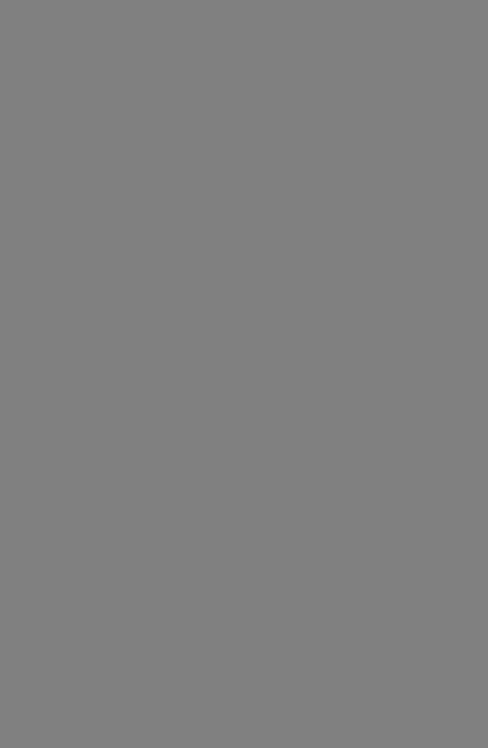
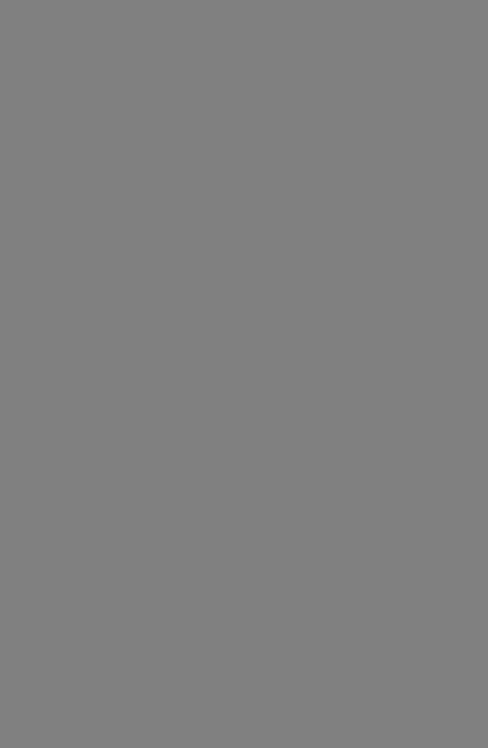
происходит по тем или иным причинам нарушение сбаланси рованности ротора. Например, на вал ротора такой установки жестко закрепляют автоматический компенсатор в виде обой мы со свободно расположенными внутри нее корректирующи ми массами (шары, кольца и др.). Эти массы при вращении ротора (со сверхкритической скоростью) самоустанавливаются относительно обоймы, устойчиво обеспечивая уравновешен ное состояние ротора.
7.7.Виброизоляция. Виброзащитные системы
содной степенью свободы
Виброизоляция — защита сооружений, машин, приборов и людей от вредного воздействия вибрации путем введения демп феров или виброизоляторов между источниками вибрации и за щищаемыми объектами. Этой проблеме посвящены ряд работ отечественных и зарубежных авторов.
Виброизолятор, или амортизатор, — элемент виброзащитной системы, наиболее существенная часть которого — упругий элемент. В результате внутреннего трения в упру гом элементе происходит демпфирование колебаний. Кроме то го, в ряде конструкций амортизаторов применяют специальные демпфирующие устройства для рассеяния энергии колебаний. Динамические характеристики амортизатора существенно за висят от его статических характеристик, причем и те и другие являются нелинейными. Нелинейность характеристик аморти затора определяется рядом причин: нелинейными свойствами упругого элемента (например, резины), внутренним трением в упругом элементе, наличием конструктивных особенностей амортизатора типа ограничительных упоров, демпферов сухо го трения, нелинейных пружин и т.д. На рис. 7.15 изображе ны различные амортизаторы и их силовые характеристики (по оси абсцисс — перемещения, по оси ординат — реакции): а — резинометаллический; б — сетчатый; в — с упругими ограни чителями хода; г — демпферный; д — с конической пружиной.
В любом амортизаторе могут быть определены три взаим но перпендикулярных направления я, j/, г, такие, что переме щение точки крепления амортизатора в одном из этих напра влений вызывает силовую реакцию амортизатора в противопо
Рис. 7.15
ложном направлении. Эти направления называются главны ми. Если через X , Y и Z обозначить проекции реакции амор тизатора на главные направления и учесть упругие и демпфи рующие свойства реальных амортизаторов при малых колеба ниях, то можно предположить следующее: реакции по главным направлениям зависят только от соответствующих перемеще ний и их первых производных по времени. Тогда функции
A' = A’ (z ,i), Y = Y (y,y), Z = Z (z ,z ) |
(7.12) |
называют динамическими характеристиками амортизатора. При анализе малых колебаний амортизируемого объекта
вблизи положения равновесия можно считать перемещения я, у и z малыми и линеаризовать динамические характеристи ки (7 .1 2 ), разлагая их в ряд Маклорена и отбрасывая члены, имеющие порядок выше первого:
A’ (* ,i) « схх + bxx, Y (y,y) « суу + Ьуу,
Z(z, z) = czz + bzz, |
(7-13) |
где «•-$г<0-0* =f1 |
*•=И<м> |
— жесткости амортизатора в главных направлениях, а
61 = Ц (°,0); 6, = § (0 ,0 ); 6, = §(0 ,0 )
— коэффициенты демпфирования.
Рассмотрим малые колебания амортизированного объекта (рис. 7.16, а), имеющего массу га. Для вывода уравнения дви жения амортизированных систем можно использовать принцип Даламбера. В произвольный момент времени t при значении текущей координаты z на массу га действует реакция Z(z, z) амортизатора. Приравнивая нулю сумму сил, приложенных к массе га, и силы инерции mz в соответствии с (7.13), получаем дифференциальное уравнение движения массы га:
mz + bzz + czz —0. |
(7-14) |
|
Соответствующее характеристическое уравнение |
имеет |
|
вид |
|
|
ms2 + bzs + с2 = 0. |
(7-15) |
|
Его корни равны |
|
|
sl,2 = 2~ |
± ф г2~ 4 т с * ) |
|
Общее решение уравнения (7.14) принимает вид |
|
|
г = А |
^ 1+ A2eS2i, |
|
где А\ и А2 — произвольные постоянные, зависящие от на чальных условий; 5^2 — корни характеристического уравне ния (7.15), которые для удобства можно представить так:
51,2 = -fwo ± \J£2 - 1-^ 0,
где czlrn = CJQ; bz/(2^/czm) = £] UQ — собственная частота амортизированной системы; f — безразмерный коэффициент затухания.
На рис. 7.16, б дана схема системы амортизации при изо ляции фундамента от колебаний гф = ZQsmut.
Элементы расчетной модели и их характеристи ка. В расчетной модели виброзащитной системы можно выде лить три основные части: источник возмущения (И), объект виброзащиты (О) и виброизолирующее устройство (ВУ). В простейшем случае источник и объект считаются твердыми телами, движущимися поступательно вдоль некоторой оси х (рис. 7.17, а).
Приложенные к системе внешние силы F (возмущения), а также внутренние силы R и iZ;, с которыми виброизолирую щее устройство, расположенное между источником и объектом, воздействует на них, считаются направленными вдоль оси я, тем самым ось х служит осью рассматриваемого виброизоли рующего устройства.
В большинстве случаев масса одного из тел системы — источника или объекта — существенно превышает массу дру гого тела — соответственно объекта или источника. Тогда
И ВУ О
F
П Rr
1_1 *
а
*П ' г г и *
б
1
1J 1—1я ,
в
Рис. 7.17
движение тела «большой» массы может считаться не за висящим от движения тела
X«малой» массы. Если, в част ности, «больш ую» массу име ет объект, то его обычно счи
тают неподвижным; движение
Xсистемы вызывается в этом случае приложенными к источ нику внешними силами, пред
ставляющими силовое возбуж
X дение |
F = F (t) |
(рис. 7.17, б). |
|
Если |
«больш ую» |
массу име |
|
ет источник, то закон его дви |
|||
жения |
f = |
£(t) |
можно счи |
тать заданным; это движение |
|||
играет роль |
кинематического |