
2804.Сварка плавлением
..pdf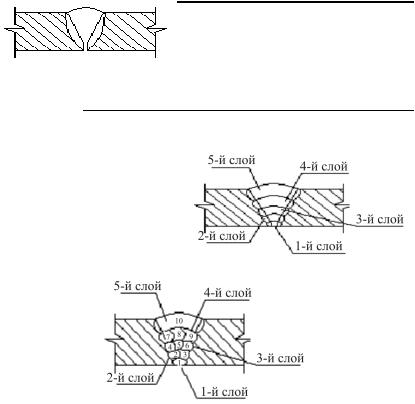
Сварочный материал
Марка электродов |
Режим прокалки |
|
|
УОНИ 13/45 |
350 Св течение 1 ч |
|
|
УОНИ 13/55 |
350 Св течение 1 ч |
|
|
Режим сварки
Диаметр |
Положение шва в пространстве |
|||
электрода |
Горизонтальное |
Вертикальное |
|
Потолочное |
3 |
80–100 |
60–80 |
|
70–90 |
4 |
130–160 |
100–130 |
|
120–140 |
Род тока, |
Постоянный, обратная |
|
||
полярность |
|
|||
|
|
|
|
Последовательность наложения валиков
однопроходный
многослойный
многопроходный
10. Оформить отчет по результатам работы.
61
Лабораторная работа № 6 Условия горения дуги, формирование валика
и производительность при сварке в углекислом газе
Краткие теоретические сведения
Сущность сварки в среде СО2 (рис. 1) состоит в том, что дуга горит в среде защитного газа, оттесняющего воздух от зоны сварки и защищающего наплавленный металл от О2 и N2 воздуха. Особенностью данного способа сварки является сравнительно сильное выгорание элементов, обладающих большим сродством к кислороду (С, Al, Ti, Si, Mn и др.). Окисление происходит за счет как СО2, так и атомарного О, который образуется при диссоциации СО2 под действием тепла дуги. Непрерывный уход окислов С, Si, Mn из ванны приводит к значительному обеднению металла шва раскислителями, что ухудшает механические свойства соединения, поэтому для получения качественных соединений необходимо при сварке в среде СО2 иметь в сварочной ванне достаточное количество раскисляющих элементов, которые обычно вводят за счет проволоки (Св-08Г2С, Св-08ГС).
Химический состав металла шва зависит не только от основного и электродного металлов, но и от параметров режима сварки, особенно от сварочного напряжения и сварочного тока. Повышение силы сварочного тока при том же диаметре сварочной проволоки приводит к уменьшению времени пребывания капли на конце электрода и ее контакта с газами. Вследствие этого уменьшается степень выгорания раскислителей из сварочной проволоки. Повышение напряжения на дуге приводит к значительному обеднению металла шва раскислителями, так как процент выгорания их в столбе дуги повышается за счет увеличения времени контакта капли электродного металла с газом.
Влажность и расход СО2 также влияют на качество шва. С повышением влажности СО2 увеличивается количество растворенного вметаллешваН2, которыйобразуетсяпридиссоциацииН2О:
2Н2О = 2Н2 + О2; Н2 Н + Н.
62
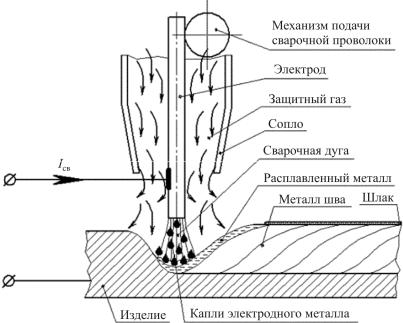
Рис. 1. Схема процесса сварки в углекислом газе
При недостаточном расходе СО2 в зону сварки проникает воздух. Из-за этого в металл шва попадает N2, что приводит к образованию пор, как и при попадании Н2. Расход газа обычно устанавливается по расходомеру.
Преимущество этого вида сварки перед сваркой под флюсом состоит в том, что сварщик может наблюдать за ходом процесса и горением дуги, которая не закрыта флюсом; не нужны приспособления для подачи и отсоса флюса, усложняющие сварочное оборудование; отпадает необходимость в последующей очистке швов от шлака и остатков флюса, что особенно важно при многослойной сварке.
Основными достоинствами способа сварки в углекислом газе являются:
1. Хорошее использование тепла сварочной дуги, вследствие чего обеспечивается высокая производительность сварки.
63
2.Высокое качество сварных швов.
3.Возможность сварки в различных пространственных положениях с применением аппаратуры для полуавтоматической и автоматической сварки.
4.Низкая стоимость защитного газа.
5.Возможность сварки металла малых толщин и сварки электрозаклепками.
6.Возможность сварки на весу без подкладки.
Коэффициент наплавки при сварке в углекислом газе выше, чем при сварке под флюсом. При сварке постоянным током прямой полярности этот коэффициент в 1,5–1,8 раза выше, чем при сварке обратной полярности. Процесс сварки отличается высокой производительностью, достигающей 18 кг/ч наплавленного металла. Скорость сварки достигает 60 м/ч. Производительность сварки в углекислом газе в 1,5–4 раза выше, чем производительность ручной сварки покрытыми электродами, и в 1,5 раза выше, чем при сварке под флюсом.
Стоимость наплавки 1 кг металла при сварке в углекислом газе в 2–2,5 раза меньше, чем при ручной сварке, и на 10–20 % меньше, чем при автоматической сварке под флюсом.
Наибольшее применение сварка в углекислом газе нашла в судостроении, машиностроении, при сварке трубопроводов, в том числе магистральных, при выполнении монтажных работ, изготовлении котлов и аппаратуры из теплоустойчивых и легированных сталей, заварке дефектов стального литья, наплавке и др.
Металлургические процессы при сварке в углекислом газе.
При высокой температуре дуги молекулы углекислого газа расщепляются (диссоциируют) на СО и О по реакции СО2–СО + О. Образующаяся СО, в свою очередь, диссоциирует на С и О по реакции СО–С + О. Атомарный кислород (О) обладает высокой химической активностью и способен окислять все элементы, входящие в состав проволоки и основного металла.
Температура капель жидкого металла в зоне дуги составляет 2150–2350 °С, а температура газа – 2900 °С. Температуры же в
64
сварочнойванненижеисоставляют: металла– 1700 °С, газа– 2300 °С. Как известно, чем выше температура, тем реакции окисления идут интенсивнее, поэтому при сварке в углекислом газе в большей степени происходит выгорание (окисление) элементов, содержащихся
вэлектродной проволоке, и в меньшей степени – элементов основного металла. При таком распределении температур бóльшая часть углекислого газа (60 %) расщепляется на окись углерода и кислород
взонедугиименьшая(15 %) – вместеконтактасванной.
При указанных условиях в зоне сварки протекают следующие реакцииокисленияэлементовивосстановленияихизокислов.
Выделение газообразной окиси углерода (СО) из жидкого металла вызывает «кипение» сварочной ванны и приводит к образованию пор. При сварке в углекислом газе пористость шва может возникнуть в результате: 1) недостатка элементов-раскислителей (кремния, марганца и др.) в проволоке; 2) присутствия ржавчины и окалины, попадающих с кромок металла и проволоки в ванну; 3) повышенного содержания влаги в углекислом газе; 4) попадания в зону сварки азота из воздуха при недостаточной защите дуги углекислым газом.
Для повышения количества марганца и кремния в металле шва, уменьшающихся в результате угара, и подавления реакции окисления углерода при сварке в углекислом газе применяют электродную проволоку с повышенным содержанием марганца и кремния. При сварке низко- и среднеуглеродистых сталей содержание в металле шва кремния более 0,2 % и марганца более 0,4 % предупреждает образование пор.
На степень окисления углерода, кремния и марганца при сварке в углекислом газе влияют напряжение, величина и полярность сварочного тока, а также диаметр электродной проволоки. С повышением напряжения окисление увеличивается, а при возрастании сварочного тока и уменьшении диаметра проволоки (повышении плотности тока) – уменьшается. Сварка на постоянном токе обратной полярности дает меньшее окисление, чем на токе прямой полярности. При сварке проволокой диаметром 0,5–1,2 мм происходит
65
значительно меньшее окисление элементов, чем при сварке проволокой диаметром 1,6–2 мм, поэтому более тонкая проволока, имеющая низкое содержание кремния и марганца, обеспечивает получение плотных беспористых швов. Плотность тока при сварке в углекислом газе должна быть не ниже 80 А/мм2. При этом потери металланаразбрызгиваниенепревышают10–15 %
Сварка в среде СО2 – процесс высокопроизводительный, в настоящее время, как правило, осуществляемый на постоянном токе обратной полярности. Переменный и постоянный токи прямой полярности не применяются из-за недостаточной устойчивости процесса и неудовлетворительного качества и формы шва. Это происходит вследствие того, что наличие в дуговом промежутке О2, имеющего большое сродство с электроном, приводит к образованию большого количества отрицательных ионов, нарушающих нормальные условия горения дуги, питаемой переменным и постоянным токами прямой полярности.
На производительность процесса сварки оказывают влияние коэффициенты плавления и наплавки. При сварке в среде СО2 коэффициент наплавки значительно превышает коэффициент наплавки под слоем флюса. Это объясняется тем, что тепло дуги, горящей в среде СО2, не тратится на плавление флюсов, т.е. эффективная тепловая мощность дуги повышается. С увеличением силы тока и уменьшением диаметра электродной проволоки (повышением плотности тока) значения коэффициентов э и н увеличиваются. Повышение напряжения на дуге и скорости сварки приводит к снижениюзначений коэффициентов э и н. Этообъясняетсяувеличением потерь тепла с ростом длины дуги на излучение в окружающее пространство, атакжеувеличениемпотерьметалланаразбрызгиваниеи угар. Повышение скорости перемещения дуги влечет за собой некоторое снижение значений э и н, потому что с увеличением скоростисваркипогоннаяэнергияуменьшается.
Целесообразность применения сварки в СО2 подтверждается практикой работы многих предприятий.
66

Цель работы – изучить влияние параметров режимов сварки углеродистых сталей в СО2 на качество, форму шва и производительность процесса.
Материалы и оборудование:
1)сварочный пост для сварки в защитных газах;
2)секундомер;
3)пластина из углеродистой стали (100×100×8 мм);
4)сварочная проволока, например марки Св-08Г2С;
5)пресс для излома проб;
6)штангенциркуль;
7)счетчик для определения расхода проволоки.
Задания для лабораторной работы:
1.Собрать пластины, прихватить их по торцам.
2.Подобрать диаметр проволоки по толщине свариваемого металлаисилу сварочного токапо диаметру сварочногоматериала.
3.Назначить режимы сварки в углекислом газе (табл. 1)
Таблица 1
Режим сварки в среде СО2
Толщина |
Вылет |
Диаметр |
Сила |
|
Скорость |
Объемный |
металла, |
электрода, |
электрода, |
свар. |
Напряжение |
подачи |
расход |
мм |
мм |
мм |
тока, А |
на дуге, В |
проволоки, |
СО2, л/мин |
|
15–22 |
|
|
|
м/ч |
|
8–12 |
1,6–2 |
200–500 |
26–32 |
250–300 |
14–24 |
4.На выбранном режиме по нижнему пределу наплавить валик длиной 60–80 мм, перпендикулярно стыку, фиксируя время горения дуги, напряжение, силу сварочного тока и показания счетчика расхода проволоки. Длина расплавленной проволоки определяется как произведение показаний счетчика (оборотов) на длину окружности подающего ролика.
5.Охладить и осушить образец.
6.Увеличивая силу тока примерно на 100–150 А и сохраняя при этом остальные параметры режима по возможности постоянными, наплавить еще два валика на этот же образец.
67
7.Определить размеры валиков h, e, q на образцах.
8.Рассчитать Fн, Fпр, qп, vсв.
9.Составить отчет по работе, оформить таблицы записей и
результаты расчетов (табл. 2).
Таблица 2
Результаты опытов и расчетов
|
|
|
Результаты замеров |
|
|
Ско- |
Погон- |
|||
|
|
|
|
|
|
|
|
|
рость |
ная |
Марка |
|
|
|
|
|
|
|
|
энер- |
|
|
Режим |
|
|
Размеры валика, мм |
сварки, |
|||||
и диа- |
|
|
|
|
|
|
|
|
м/ч |
гия, |
метр |
|
|
|
|
|
|
|
|
Дж/см |
|
прово- |
Сила |
|
Время |
|
|
|
|
Глу- |
|
|
локи |
Напря- |
горе- |
Дли- |
Шири- |
Выпук- |
бина |
|
|
||
|
тока, |
жение, В |
ния |
на |
|
на |
лость |
прова- |
|
|
|
А |
|
дуги, с |
|
|
|
|
ра |
|
|
|
|
|
|
|
|
|
|
|
||
|
|
|
|
|
|
|
|
|
|
|
10. Сформулировать выводы и объяснения полученных результатов.
Лабораторная работа № 7 Изучение влияния различных методов
дуговой сварки чугуна на качество сварного соединения
Краткие теоретические сведения
Чугунами называют железоуглеродистые сплавы с содержанием углерода свыше 2 %. Благодаря хорошим литейным свойствам и сравнительно невысокой стоимости они широко применяются в машиностроении. В зависимости от состояния углерода и скорости охлаждения чугун разделяют на белый и серый.
Твердость является важной характеристикой чугуна; она зависит от структуры, легирующих примесей и размера графитных включений. Наименьшую твердость имеют ферритные чугуны, в которых почти весь углерод находится в свободном состоянии, перлитный чугун с пластинчатым графитом имеет HB 400–500, а струк-
68
тура цементита HB 750. Наибольшее применение находят серые чугуны. Сваркасерыхчугуновпроизводится двумяспособами.
Сварку чугуна применяют в ремонтных целях и для изготовления сварнолитых конструкций. К сварным соединениям чугунных деталей в зависимости от типа и условий эксплуатации предъявляют требования по механической прочности, плотности (водо- и газонепроницаемость) и обрабатываемости режущим инструментом. Обеспечить эти требования при сварке весьма сложно из-за физико-химических особенностей чугуна.
Трудности, возникающие при сварке чугуна, обусловлены, как правило, низкой стойкостью металла сварного соединения к образованию трещин и плохой его обрабатываемостью на механических станках. Указанные особенности чугуна являются следствием нарушения сплошности его металлической основы, включениями графита, а также его склонностью к отбелке и закалке даже при небольших скоростях охлаждения. Эти свойства чугуна определяются высоким содержанием в нем углерода.
Соединение чугунных деталей между собой выполняют газовой, термитной, литейной, дуговой и электрошлаковой сваркой и пайкой. Сварку ведут без подогрева (холодная сварка), с местным и общим подогревом (полугорячая и горячая сварка). Для дуговой сварки используют угольные, графитовые, стальные и легированные электроды, а также электроды из цветных металлов. Поскольку чугун обладает достаточно высокой жидкотекучестью, для удержания расплавленного металла сварочной ванны применяют специальные формовки. Формовочная масса имеет следующий состав: кварцевый песок, замешанный на жидком стекле, – 40 %, формовочная земля – 30 % и белая глина – 30 %.
Подготовленная к сварке деталь подвергается общему или местному нагреву до температуры 350–450 °С, иногда для особо сложных деталей – до 550–600 °С.
Сварку выполняют как на переменном, так и на постоянном токе, величину тока подбирают из расчета 50–90 А на 1 мм диаметра электрода.
69
Горячая сварка – это способ, при котором осуществляются предварительный и сопутствующий нагревы изделия до 600–700 С с последующим медленным охлаждением. Такой процесс уменьшает скорость охлаждения металла сварочной ванны и околошовной зоны, что обеспечивает полную графитизацию металла шва и отсутствие отбела в околошовной зоне, а также исключает возможность появлениясварочныхнапряжений.
Холодная сварка – это сварка без предварительного нагрева изделия. Этот способ требует меньших затрат, при этом имеется возможность варьировать в больших пределах химический состав металла шва. Но при наложении валика на холодную поверхность чугуна вследствие быстрого отвода тепла металл наплавленного валика получится твердым и хрупким. В околошовной зоне на первом участке неполного расплавления, ограниченном температурами 1150–1250 С, при большой скорости охлаждения образуется белый чугун, а на втором участке, где при нагреве от наплавки валика образовался аустенит, большая скорость охлаждения и химический состав чугуна приводят к его переохлаждению с образованием твердой и хрупкой структуры мартенсита.
Уменьшение склонности к образованию структуры мартенсита первого участка околошовной зоны при сварке чугуна может быть достигнуто введением в металл шва таких графитизаторов, как Cu, Ni, т.е. соответствующим изменением химического состава металла шва. Исключить или уменьшить вероятность образования мартенсита на втором участке околошовной зоны можно снижением скорости охлаждения, что достигается увеличением погонной энергии сварки или подогревом изделия.
Сварка стальными электродами. При этом способе сварки для образования прочного наплавленного металла в чугунное изделие завертывают шпильки, которые впоследствии обваривают. Такой способ применяют при ремонте тяжелых и громоздких чугунных деталей. При сварке чугуна стальными электродами металл шва обычно содержит повышенное количество углерода, вследствие чего имеет высокую твердость и подвержен образова-
70