
1404
.pdfК а р б о н и з а ц и я рудно-флюсовых окатышей заключается в обработке их газами, содержащими повышенное количество угле кислого газа. Процесс превращения гидрата окиси кальция в кар бонат сопровождается также сушкой окатышей
Са (ОН)2 4“ С02 пН20 = СаСОз -(- (/i 0 Н2Опар.
Интенсивный, ход процесса карбонизации — сушки имеет ме сто только при определенном содержании влаги в шихте.
Применение в шихте мелассы (патоки) в количестве 0,1—0,2% и других материалов, содержащих глюкозу, раздвигает опти мальные пределы влажности обрабатываемого материала и уско ряет процесс карбонизации. Предложено использовать мелассу или глюкозу совместно с хлоридами щелочноземельных металлов. Прочность окатышей при этом повышается в три-четыре раза.
Процесс естественной карбонизации гашеной извести на воз духе протекает медленно и проявляется лишь при длительном вы леживании материала, так как содержание углекислого газа в атмосфере не превышает 0,04%.
А в т о к л а в и р о в а н и е заключается в гидротермальной об работке окатышей. При этом происходит образование гидросили катов или гидроферритов по реакциям:
Si02 + Са (ОН)2 + /гН20 = СаО • Si02 (п -f 1) Н20,
Fe30 4 + СаО (ОН)2 + nH20 = СаО (Fe03-Fe20) (п + 1) Н20.
Предполагается, что в процессе автоклавирования, кроме це ментации структуры окатышей гидросиликатом кальция, возмож но возникновение дополнительных сил сцепления между кристал лами вследствие увеличения содержания химически связанной во ды при перекристаллизации С а(0Н )2-й 1а(0Н )2/гН20.
Автоклавная обработка производится при давлениях 7—8 атм
итемпературе 170—200° С.
Об ж и г сырых окатышей производят в шахтной печи или на подвижной колосниковой решетке обжиговой машины типа агло ленты при температуре 1100—1300° С.
Схема установки для производства обожженных окатышей представлена на рис. 5. Обжиговая машина ОК-Ы08 с непрерыв ным процессом загрузки, обжига и разгрузки окатышей приспо соблена для обжига твердым топливом, накатанным на поверх ность сырых окатышей, и обжига газообразным топливом, сжи гаемым в горне. Производительность машины 100—130 т окаты
шей в час. Тарельчатый окомкователь диаметром 5500 мм имеет производительность 30—40 т/н сырых окатышей, производитель ность барабанного окомкователя диаметром 2,8 м и длиной ба рабана 11 м составляет 40 т/н.
Обожженные окатыши диаметром 12—16 мм выдерживают на грузку на раздавливание до 100 кГ, они сохраняют форму и не разрушаются при перегрузках.
Применение калиброванных и прочных окатышей улучшает га зодинамические свойства доменной шихты, что позволяет автома тизировать процесс, повысить производительность доменных печей и улучшить технико-экономические показатели производства.
Рис. 5. Схема установки для производства обожженных окатышей:
1 — бункера для |
шихты; |
2 — питатели; |
3 — ленточный конвейер; 4 — окомкователь; |
5 — питатель-укладчик; 6 |
— трехкамерная печь для обжига; / — агломерационная ма |
||
шина; |
8, 9 — вибрационные |
грохоты; 10 — шнековый смеситель. |
Офлюсованные окатыши, например, из качканарского концент рата (55,16% Fe; 8,6% СаО; 5,75% Si02; основность 1,5) имеют высокую степень окисленности (94,8—97,0%) и прочность.
Механическая прочность обожженных офлюсованных окаты шей превосходит прочность офлюсованного агломерата, а имен но: выход класса 0—5 мм после разделки барабанной пробы ока тышей составляет 7,6—8,5%; сопротивление раздавливанию на один окатыш достигает 65—75 кГ
Офлюсованные окатыши с основностью 1,2—1,6 имеют пори стость до 40%. Хранить окатыши можно в обычных атмосферных условиях без опасения их разрушения вследствие гидратации из
вести. Они находят все большее применение в практике домен ного производства. Причем, в связи с получением железорудных концентратов более глубокого обогащения и, следовательно, более тонкого измельчения, химические и физические свойства окаты шей улучшаются.
§ 3. Доменный процесс
Доменная плавка — это совокупность химических, физических, теплообменных и механических процессов, в результате одновре менного протекания которых из загружаемых в доменную печь исходных материалов — агломерата (рудных окатышей), кокса и флюса — получают продукты плавки — чугун, шлак, колошнико вые газы и пыль. В процессе плавки шихтовые материалы пере
мещаются в печи сверху вниз, а образующиеся |
при горении |
кокса у фурм газы — снизу вверх. Скапливающиеся |
в горне печи |
чугун и шлак периодически выпускаются.
Наиболее важными в доменной печи являются реакции вос становления окислов железа, кремния, марганца и фосфора, про цессы науглероживания металла твердым углеродом кокса и пре вращение его в чугун, а также процессы шлакообразования и реакции, протекающие в системе шлак — металл.
Тепло от горения кокса у фурм должно компенсировать об щее теплопотребление восстановительного процесса, происходя щего в доменной печи, включая стадии нагрева и сушки шихты, газификации топлива и плавления руды.
Горение кокса
Горение кокса происходит возле фурм за счет кислорода вду ваемого воздуха, нагретого до температуры 800—1000° С. Непо средственно у фурм создается окислительная атмосфера, так как углерод кокса сгорает здесь преимущественно по реакции
С + 0 2 = С02 + 94,03 ккал.
По мере продвижения газов к оси печи и уменьшения содер жания в них кислорода углекислый газ реагирует с кусками рас каленного кокса по реакции, протекающей с поглощением тепла
С + С02 = 2СО — 41 ккал.
Суммарная реакция горения углерода в воздухе выражается уравнением
2С + 0 2 + 3,762N2 = 2СО -f 3,762N2.
Таким образом, на уровне фурм к центру печи возрастает со держание СО в газе до ~40% и снижается температура с 1700— 1900° С у фурм до 1450—1600° С на расстоянии 1,5—2 м от фурм.
Окислительная зона в печи простирается от фурм примерно на 1200—1400 мм к вертикальной оси и на 600—1000 мм вверх от
горизонта фурм. В этой зоне концентрация СО2 в газе проходит через максимум (~10% СО2) на расстоянии 500—700 лш-от фурм; соответственно здесь также достигается максимальная тем пература.
При воздушном дутье в горне образуется восстановительный газ следующего состава: 34% СО, 65,3% N2 и менее 1% Н2. Газ распространяется к оси печи и вверх, взаимодействуя с различ ными шихтовыми материалами как восстановитель и теплоноси тель процесса. Колошниковый газ, покидающий доменную печь, имеет следующий состав: 8—12% С02; 39—40% (СО + С 02); 0,2— 0,4% СН4; 2,5—3% Н2 и 57—58% N2; теплота сгорания газа око ло 900—1000 ккал/нм3.
Давление дутья у фурм зависит от объема печи и составляет примерно 2,2—2,5 ата, а над уровнем шихты на колошни ке — 1,1 ата.
Современные доменные печи работают на искусственно по вышенном до 1—1,8 ати давлении газа на колошнике, что спо собствует более равномерному распределению газов по сечению печи, улучшает проникновение его в куски рудной шихты и поз воляет увеличить расход дутья без опасения возрастания выноса
пыли. Это приводит к более ровному |
ходу печи и увеличению |
ее производительности на 10% и более. |
предварительно прошед |
Применение природного газа (СН4), |
шего стадию конверсии (СН4->СО + Н2), позволяет сократить рас ход дорогого и дефицитного кокса, улучшить условия теплооб мена в фурменной зоне, снизить содержание серы в чугуне и уве личить производительность доменных печей за счет улучшения условий восстановления окислов железа водородом. Использова ние природного газа для доменной плавки находит все более ши рокое применение.
Восстановление окислов
Согласно принципу последовательности превращений окислов металлов, сформулированному А. А. Байковым, восстановление высшего окисла железа БегОз при температурах выше 570° С про ходит ряд промежуточных ступеней:
Fe20 3 -» Fe30 4 FeO Fe.
Восстановление окисла металла Л4еО элементом-восстанови телем или его низшим окислом, например С или СО, термоди намически возможно, если сродство к кислороду у С или СО больше, чем у данного металла. Мерой прочности окисла явля ется величина упругости его диссоциации, т. е. равновесного пар циального давления кислорода при данных температуре и давле нии. Если, например, Рмсо>Рсо, то восстановление МеО будет иметь место. При равенстве этих величин устанавливается рав новесие соответствующих систем.
Восстановление окислов железа окисью углерода (косвенное) протекает по следующим реакциям:
3Fe20 3 (ТВ) + СО = 2Fe30 4 (ТВ) + С02+ 15,05 ккал,
Fe30 4 (тв) + СО = 3FeO(TB) + С02 — 5,35 ккал,
FeO(Tn) СО = Fe(XB) -1- С02 -[-3,15 ккал.
Кривые, отвечающие равновесию этих реакций, т. е. опреде ленному (при данной температуре) отношению концентраций
в газовой фазе, приведены на диаграмме рис. 6.
Рис.
Каждое поле диаграммы, ограниченное равновесными линиями,
определяет температуры и составы газа, при |
которых |
устойчива |
|
та или иная твердая фаза — Fe30 4, FeO или |
Fe. Чем |
богаче га |
|
зовая фаза окисью углерода, тем больше удалена |
система оки |
||
сел — газ от равновесия при данных условиях и |
тем |
успешнее |
|
осуществляется восстановление окислов железа. |
|
|
печи ока |
Состав доменного газа на всех горизонтах доменной |
зывается обогащенным окисью углерода по сравнению с соста вом газа, находящегося в равновесном состоянии. Это объясня ется сравнительно большой скоростью движения газа и диффузи онным характером восстановления кусковых рудных материалов, благодаря чему газ покидает печь с недоиспользованной (при
данных температурах) окисью углерода. Отношение — в ко
лошниковом газе обычно равно 2—3.
Основная масса окислов железа рудных материалов восста навливается в доменной печи в зонах нижнего горизонта шахты
///, распара IV и заплечиков V (рис. 7). При высоких темпе ратурах в этих зонах (более 900—1000° С) и при наличии в ших
те кусков кокса получают развитие реакции прямого восстановл ния окислов железа твердым углеродом.
Этот процесс протекает через газовую фазу и характеризуете одновременно происходящими двумя частными реакциями:
FeO(TB) -f СО = FeTB-f С02 -f 3,15 ккал, С -f С02 = 2СО — 41,0 ккал.
FeO(TB) + С = FeTB-f СО — 37,85 ккал.
|
|
|
|
|
|
Суммарный |
|
процесс |
прям ого |
вос |
|||||||
|
|
|
|
|
становления |
с |
|
получением |
м еталличе |
||||||||
|
|
|
|
|
ского |
ж ел еза |
|
возмож ен |
только |
при |
|||||||
|
|
|
=ЩЗ |
условиях, существующих |
в |
заштрихо |
|||||||||||
|
|
|
ванной |
|
области |
|
(см. рис. |
6). П ри |
вы |
||||||||
|
|
|
|
|
|
|
|||||||||||
|
|
|
|
|
соких тем пературах скорость реакции |
||||||||||||
|
|
|
|
|
регенерации СО выше, чем скорость |
||||||||||||
|
|
|
|
|
расхода |
окиси |
|
углерода |
на |
реакции |
|||||||
|
|
|
|
|
косвенного восстановления. |
Поэтому с |
|||||||||||
|
|
|
|
|
повышением |
температуры |
|
получает |
|||||||||
|
|
|
|
|
развитие |
процесс |
прямого |
восстанов |
|||||||||
|
|
|
|
|
ления. |
|
|
|
|
|
|
|
|
|
|
|
|
|
|
|
|
|
При |
выплавке передельного чугуна |
|||||||||||
|
|
|
|
|
около |
40— 60%, |
|
а |
при |
производстве |
|||||||
|
|
|
|
|
ферромарганца до 80% железа руды |
|
|||||||||||
|
|
|
|
|
восстанавливается |
|
прямым |
|
путем. |
|
|||||||
|
|
|
|
|
Кремнезем и закись марганца восста |
|
|||||||||||
|
|
|
|
|
навливаются твердым углеродом, т. е. |
|
|||||||||||
|
|
|
|
|
прямым |
путем, |
только |
при |
высоких |
|
|||||||
|
|
|
|
|
температурах. |
|
|
|
|
|
|
|
|
|
|||
|
|
|
|
|
При восстановлении каждого куска |
|
|||||||||||
|
|
|
|
|
руды (агломерата, окатыша) харак |
|
|||||||||||
|
|
|
|
терным является малая скорость ре |
|
||||||||||||
|
|
|
|
акции |
восстановления |
в |
начальный |
|
|||||||||
|
|
|
|
период из-за трудности формирования |
|
||||||||||||
|
|
|
|
на поверхности куска новой фазы в |
|
||||||||||||
|
|
|
|
результате |
|
кристаллохимического |
пре |
|
|||||||||
|
|
|
|
вращения FemO„—>-Fe. Затем наступает |
|
||||||||||||
|
|
|
|
период |
интенсивного |
|
восстановления, |
|
|||||||||
|
|
|
|
сопровождающегося |
|
ростом |
поверхно |
|
|||||||||
|
|
|
|
сти раздела твердых фаз окисел — ме |
|
||||||||||||
|
|
|
|
талл внутри куска руды. В заключи |
|
||||||||||||
Рис. |
7. |
Процесс восстановле |
тельном |
периоде |
восстановления |
воз |
|
||||||||||
никает усредненный |
фронт реакции |
с |
|
||||||||||||||
ния окислов железа на раз |
|
||||||||||||||||
личных |
горизонтах |
доменной |
относительно |
малой |
удельной |
поверх |
|
||||||||||
I, 11, |
|
лечи: |
|
ностью, подвод к |
ней |
|
восстановителя |
|
|||||||||
111— верхний, средний и ниж |
и отвод |
продуктов |
реакции |
с поверх |
|
||||||||||||
ний |
горизонты шахты |
печи; I V — |
|
||||||||||||||
Цифрами отмечены основные раз |
ности затрудняется. В результате ско |
|
|||||||||||||||
распар; |
V — заплечики; |
VI — гори. |
рость процесса восстановления |
посте |
|
||||||||||||
меры печи и содержание железа в |
|
||||||||||||||||
форме FesOa. FeO и Fe |
на различ |
пенно снижается по мере его развития. |
|
|
|||||||||||||
|
|
ных горизонтах |
|
|
В общем случае скорость и степень восстановления окускованных железных руд зависит от скорости подвода газа — восста новителя и отвода продуктов из зоны реакции, т. е. от размера кусков, их пористости, температуры процесса.
При повышении давления газа улучшаются условия его ад сорбции на поверхности кусков руды и проникновения в поры. Однако увеличение давления газа сверх 4—5 ати приводит к пас сированию (переводу в пассивное состояние) реакционной по верхности газ —твердое тело вследствие накопления здесь га зообразных продуктов, что в итоге приводит к снижению скоро сти процесса восстановления руды.
Увеличение скорости газового потока способствует при прочих равных условиях ускорению процесса восстановления.
Высшие окислы марганца (МпОг, МщОз и МП3О4) восстанав ливаются окисью углерода до закиси очень легко и процесс со провождается значительным выделением тепла
MnmO„ + СО -►Мп 4- С02+ Q.
В зоне высоких температур протекает суммарный процесс прямого восстановления закиси марганца с затратами тепла вдвое большими, чем на единицу (точнее моль) железа
МпОхв 4- С = Мптв 4- СО — 68,64 ккал.
Этот процесс термодинамически возможен при температурах более 1410° С и давлении 1 ат. Для облегчения восстановления марганца при выплавке марганцовистых чугунов необходимо по вышать температуру процесса (нагрев дутья), увеличивать рас ход топлива, а также работать на основных шлаках, так как вос становление марганца из силикатов затруднено.
Кремнезем является еще более прочным окислом, чем закись марганца. Поэтому восстановление кремния твердым углеродом возможно при давлении 1 ат только при температурах выше 1550° С по реакции
SiC>2(тп> 4- 2С = Si(TD) 4- 2СО — 154 ккал.
Восстановлению кремнезема способствуют высокие темпера туры и наличие кислых шлаков.
Восстановление трудновосстановимых окислов MnO, SiCb и других в условиях доменного процесса облегчается тем,, что про дукты восстановления — марганец и кремний — растворяются в железе. В этих условиях константа равновесия реакции
МпО 4-С = [Mn]Fe 4-СО
выражается уравнением
Кмп = Рсо-амп»
где р'со — равновесное парциальное давление окиси углерода; амп — активность марганца.
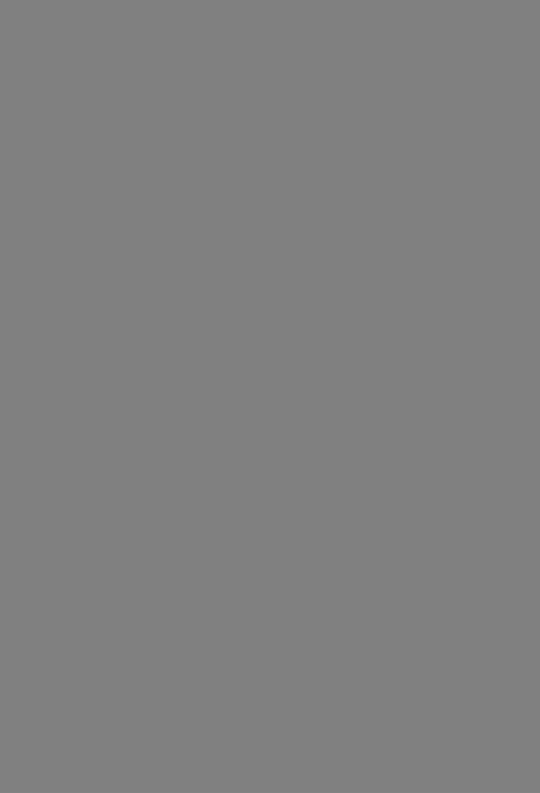
При использовании более богатого железом рудного сырья процесс формирования шлака наступает на более низких гори зонтах доменной печи и при относительно более высокой темпе ратуре. Это улучшает газодинамические условия процесса плав ки, обеспечивая ровный ход печи и увеличивая ее производитель ность.
Химический состав и физическое состояние образующихся шла ков позволяют регулировать температуру в горне печи. Чрезмерно легкоплавкая пустая порода, плавясь при относительно низкой температуре в шахте печи, приходит в горн с малым запасом тепла и понижает температуру горна. Наоборот, расплавы туго плавких пустых пород поступают в горн с большим количеством тепла и температура горна поэтому повышается. Густой и вязкий шлак, кроме того, налипает на поверхность футеровки, образуя настыли, что нарушает нормальный сход шихты и удаление шлака из печи.
Процесс шлакообразования, состав и консистенция образую щихся шлаков оказывают решающее влияние на состав выплав ляемого чугуна, обеспечивая развитие реакций между металлом и шлаком в горне печи в необходимом направлении.
Доменный шлак состоит в основном из трех окислов, содержажание которых изменяется в следующих пределах: 30—40% Si02; 10—20% А120 3 и 40—50% СаО. Иногда доменный шлак содержит до 10—15% окиси магния, повышающей жидкоподвижность ос
новных шлаков. |
Вязкость доменных |
шлаков с |
основностью |
СаО |
температуре 1500° С |
составляет |
2—5 пз и за- |
----- =1,0—1,2 при |
|||
Si02 |
|
|
|
висит от концентрации в нем окисей кальция и магния, кремнезе ма и глинозема.
Одним из наиболее важных процессов, происходящих между металлом и шлаком в горне печи, является десульфурация чу
гуна. В |
условиях доменной печи сера практически не удаляется |
с газами |
(удаляется не более 5%). Поэтому для получения мало |
сернистого чугуна поступающую с шихтой серу в возможно боль шем количестве переводят в шлак.
Наибольшее количество серы вносится в доменную печь кок сом в виде пирита, при сгорании которого образуется сернистый ангидрид S02, восстанавливаемый затем углеродом. Газообраз ная сера поглощается окислами шлака, флюса, частично губча тым железом и восстановленным марганцем.
Окончательное удаление серы из чугуна происходит во время падения капель металла в слое шлака и на поверхности раздела шлак — металл в горне по следующим реакциям, продуктом кото
рых является прочный сульфид кальция |
|
||
[FeS] + (СаО) = |
(FeO) + (CaS), [MnS] + (СаО) = (MnO) + |
(CaS). |
|
1 Здесь |
и далее |
в квадратных скобках дается содержание того |
или иного |
компонента |
в металле, в круглых скобках — содержание в шлаке. |
|
В присутствии твердого углерода кокса суммарная реакция де сульфурации чугуна имеет вид
[FeS] + (СаО) + CtB = (CaS) + Реж + СО — Q.
Удалению серы из чугуна благоприятствуют повышение основ ности шлака, понижение содержания в шлаке закиси железа и марганца и высокая температура, так как суммарная реакция десульфурации шлаком в присутствии твердого углерода эндотермична. Повышение температуры, кроме того, увеличивает теку честь основных шлаков и, следовательно, улучшает кинетические условия удаления серы.
Коэффициент распределения серы между чугуном и шлаком
/о/S) |
|
-- ; обычно изменяется в пределах 20—40; для высокоосновных |
|
[%S] |
F |
шлаков 60—80. |
газа в доменном процессе взамен ча |
Применение природного |
сти кокса позволяет снизить содержание серы в чугуне. Составы передельного и литейного чугунов приведены в табл. 2. В домен ной печи выплавляют также специальные чугуны — ферромарга нец и ферросилиций.
§ 4. Оборудование доменного цеха
Общий вид доменного цеха в составе рудного двора, бункер ного отделения и собственно доменной печи показан на рис. 8.
Руда и флюс с рудного двора поступают в бункерное отде ление, где дозируются по заданной программе с коксом, и по наклонному подъемнику подаются скипами на колошник домен ной печи. Отсюда шихта через специальное загрузочное устрой ство поступает в печь.
Колошниковые газы проходят сложную систему очистки и ис пользуются для нагрева насадок воздухонагревателей доменной печи и как энергетическое топливо смежных цехов металлурги ческого завода.
Чугун и шлак выпускаются в специальные ковши, установлен ные на железнодорожных платформах, и вывозятся из цеха. Чу гун поступает либо в миксерное отделение сталеплавильного це ха, либо на разливочную машину.
Доменная пень
В практике металлургической промышленности строятся до менные печи только большого полезного объема 1500—2000 м3 и более (табл. 6) *. Производительность таких печей в зависи мости от качества сырой руды составляет 2000—3800 т чугуна в сутки.
* Сооружаются печи объемом до 3000 м3 и проектируются — 5000 м3.