
702
.pdfвыбираем в форме «вагонного колеса», высота выступов которого убывает в направлении сопла. Далее идет цилиндрическая часть, которая в дальнейшем переходит в щелевой компенсатор с переменной высотой щели. Все эти элементы имеют примерно постоянную поверхность горения, значит, и весь заряд будет иметь то же свойство. Щели делаем расширяющимися к основанию, при этом радиус при вершине щели будет увеличиваться по мере увеличения перемычки между вершиной щели и корпусом двигателя. Это сделает коэффициенты концентрации напряжений в вершинах щелей примерно одинаковыми по длине заряда. Данный заряд обладает постоянной поверхностью горения, примерно постоянной скоростью газового потока по длине заряда и выровненным напряженно-деформированным состоянием по длине канала заряда, т.е. эта конструкция близка к оптимальной. Здесь сочетаются три типа формы заряда: щелевой, трубчатый и «вагонное колесо». Возможны еще другие варианты сочетаний стандартных форм заряда.
3.2.7. Комбинированные заряды
Комбинированные заряды – это заряды, состоящие из двух или более топлив [2, 5, 10]. Они позволяют решить задачи, которые очень трудно решить, используя заряд из одной марки топлива. Это прежде всего обеспечение более простыми средствами нейтрального закона горения заряда, внесение в продукты сгорания необходимых компонентов, которые являются химически несовместимыми. Кроме того, комбинированные заряды позволяют повысить энергетические характеристики топлив, организовать газовые завесы для защиты некоторых узлов двигателя, обеспечить устойчивую работу медленногорящих топлив и т.д. Эти заряды могут быть как скрепленными, так и вкладными. На рис. 3.18 представлены некоторые прочно скрепленные комбинированные заряды. Один из них обеспечивает двухрежимную работу двигателя: заряд сначала выгорает с ка-
91
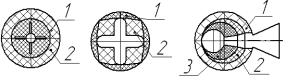
нала, где расположено топливо с малой скоростью горения, потом начинает гореть топливо, расположенное у стенки корпуса, которое имеет гораздо большую скорость горения. В результате получается ступенчатое изменение тяги, которое обеспечить за счет изменения поверхности горения зарядом из одного топлива достаточно трудно. На этом же рисунке приведена схема двигателя с звездообразным каналом. В результате специально спрофилированной границы раздела топлив этот заряд не имеет дегрессивных остатков топлива. Это позволяет повысить величину полного импульса двигателя на 5…9 %. Оба эти заряда обладают нейтральной поверхностью горения. Изготавливают их по обычным технологическим схемам: сначала собирают с оснасткой, которая обеспечивает форму части заряда с большим каналом, проводят заполнение, полимеризацию, а затем собирают с оснасткой, обеспечивающей форму комбинированного заряда, проводят заполнение камеры другим топливом и полимеризуют его.
а |
б |
в |
Рис. 3.18. Схемы комбинированных зарядов, скрепленных с камерой сгорания: а – заряд, обеспечивающий двухрежимную работу двигателя; б – заряд, не имеющий дегрессивных остатков топлива; в – заряд, обеспечивающий работу двигателя на трех режимах; 1, 2, 3 – виды топлив
На этом же рисунке приведена схема двигателя, обеспечивающего работу двигателя на трех режимах. Это достигается тем, что все части заряда имеют внутреннюю поверхность в виде сфер или эллипсоидов, а необходимый закон горения заряда обеспечивается изменением их эксцентриситета.
На рис. 3.19 приведена схема конструкции комбинированного заряда с продольным расположением различных
92

топлив по длине камеры сгорания. Заряд прочно скреплен со стенками камеры сгорания. Основной заряд выполнен из топлива с высоким содержанием металлических добавок, продукты сгорания которого обладают высокой температурой и большим содержанием конденсированной фазы. Перед соплом расположен заряд из топлива, не содержащего металла. Продукты сгорания этого топлива имеют значительно меньшую температуру сгорания. В сопловом блоке происходит двухслойное течение продуктов сгорания – по стенке текут газы с низкой температурой, защищая стенки сопла. Кроме того, от заднего днища осуществляется отбор продуктов сгорания для управления вектором тяги. Эти газы не содержат конденсированной фазы, поэтому не требуются специальные фильтры. Для системы управления вектором тяги не требуется газогенератор, что уменьшает пассивную массу двигателя и повышает эффективность ракеты.
Рис. 3.19. Схема конструкции двигателя с комбинированным зарядом с продольным расположением различных топлив: 1 – топливо с высокой температурой продуктов сгорания; 2 – топливо с низкой температурой продуктов сгорания; 3 – клапан на линии перепуска газа
Вкладные комбинированные заряды могут выполняться по двум основным схемам: шашки расположены друг за другом по длине камеры сгорания, одна шашка в канале другой шашки. Схема вкладных комбинированных зарядов приведена на рис. 3.20. Схема с последовательным распо-
93
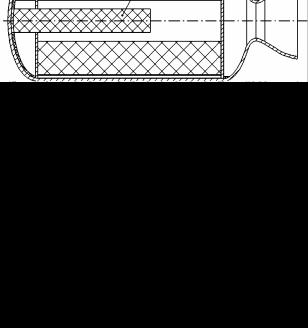
ложением шашек может применяться, например, для создания газовой завесы продуктами сгорания шашки, расположенной у переднего днища. У сопла расположена шашка из топлива с высокой температурой сгорания, которую обтекают низкотемпературные газы от передней шашки, защищающие стенку камеры. Может применяться следующая схема: передняя шашка изготовлена из обычного баллиститного топлива. Известно, что это топливо обладает низким единичным импульсом. С целью улучшения энергетических характеристик в это топливо можно ввести металлические порошки, но их количество должно быть ограничено 8…12 %, хотя оптимальное содержание составляет
Рис. 3.20. Схема конструкций вкладных комбинированных зарядов: 1 – основной заряд; 2 – дополнительный заряд
94
18…20 %. Дело в том, что введение такого количества металлических порошков резко ухудшает технологические и эксплуатационные характеристики топлива. Установив перед соплом шашку из высокометаллизированного топлива (например, гидрореагирующего) можно получить практически любое содержание металлических добавок в топливной паре и увеличить единичный импульс обычного баллиститного топлива на 8…12 %.
При второй схеме, приведенной на рис. 3.20, в канал основной шашки установлена дополнительная шашка, которая обычно называется заряд-сопроводитель. Функция этой шашки – введение необходимых добавок в продукты сгорания основной шашки. Это может производиться с целью ликвидации факела за соплом двигателя, уменьшения температуры продуктов сгорания за соплом, введения специальных противоградовых реагентов и т.д. Таким образом, на базе одного серийно производимого топлива можно получать характеристики продуктов сгорания, которые требуются условиями эксплуатации. Заряды-сопроводители применяются и для зарядов торцевого горения, обычно это бывают газогенераторы, для которых требуется низкая температура продуктов сгорания и небольшая скорость горения топлива. При горении таких топлив в начальный момент времени велики тепловые потери, что ведет к уменьшению давления в камере, изменению расходных характеристик сверх установленных пределов или загасанию заряда. Обычно в торцевую разделку заряда устанавливают небольшой заряд-сопроводитель, который устраняет все недостатки. Данная схема может применяться и для конструкций зарядов для ПТУРСов. В случае многошашечного заряда комбинированная схема изделия получается путем замены одной или нескольких шашек другими шашками, изготовленными из необходимого топлива.
При проектировании двигателей с комбинированным зарядом дополнительно необходимо учитывать процессы смешения и химических реакций между продуктами сгора-
95
ния частей комбинированного заряда. Общий недостаток всех комбинированных зарядов – усложнение технологии изготовления.
3.3. Бронирующие покрытия
Бронирующие покрытия наносятся на поверхности заряда, которые не должны гореть при работе двигателя. Требования к таким покрытиям: хорошая адгезия к топливу, химическая и физическая стабильность в течение срока хранения, низкая теплопроводность, малая плотность, технологичность нанесения, недефицитность сырья [1].
Для изготовления бронирующих покрытий применяют следующие материалы.
Смолы. Чаще всего эпоксидные с наполнителями или без них. Основное достоинство смол заключается в том, что они очень технологичны при изготовлении. Их наносят заливкой, для чего заряд помещают в форму, которая определяет будущие размеры покрытия, заливают смолу с отвердителем и полимеризуют покрытие. Основным недостатком является большая жесткость бронирующего покрытия (модуль отвержденного покрытия составляет от 1000 до 3000 МПа) по сравнению с твердым топливом. Это ведет к появлению больших температурных напряжений и появлению трещин либо в покрытии, либо в топливе. В настоящее время применяют редко.
Резины. Основным их достоинством является эластичность. Модули упругости резины и топлива примерно одинаковы, поэтому температурные напряжения отсутствуют. Бронирующее покрытие наносят приклейкой пластин резины (на торцевые поверхности заряда) и намоткой резинотканевых лент, пропитанных герметиком (на наружные поверхности заряда). Основной недостаток – трудность контроля адгезии резины к заряду и самих лент между собой. Возможные непроклеи трудно определяются ультразвуковыми методами контроля, так как бронепокрытие представляет собой чередование многих слоев, каждый из которых является поверхностью отражения.
96
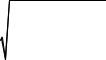
Полимеры. Наносят приклейкой пластин, экструзией или заливкой. Экструдер представляет собой шнековый аппарат, где гранулы полимера плавят и с помощью шнека под давлением выдавливают на поверхность заряда. Для заливки применяют формы, которые полностью повторяют форму заряда. В зазор формы впрыскивается расплавленный полимер, который образует после застывания бронирующее покрытие. Покрытия эластичны, поэтому температурные напряжения практически отсутствуют, технологичны, особенно для массового производства.
В бронирующее покрытие для уменьшения теплопроводности часто вводят наполнители – газовую сажу, хлопчатобумажные или асбестовые нити. Для СТТ в бронепокрытие используют тот же каучук, что и в самом топливе, так как в этом случае лучше адгезия бронирующего покрытия к топливу, выше технологичность изготовления заряда.
Толщина бронепокрытия определяется из условия минимального прогрева слоя топлива, прилегающего к покрытию [1].
δ = |
2 λ τ |
||
Ñ ρ ln |
Tã −Ò0 |
||
|
|||
|
Tã −[T ] |
где λ – коэффициент теплопроводности материала бронепокрытия, τ – время работы двигателя, C – коэффициент теплоемкости бронепокрытия, ρ – плотность бронепокры-
тия, Тг – температура продуктов сгорания (300 −3000 °Ñ) , T0 – начальная температура заряда, [Ò] – допустимая тем-
пература под бронепокрытием.
Допустимая температура под бронепокрытием определяется конкретной конструкцией заряда. В качестве предельного значения брать температуру самовоспламенения топлива нельзя, так как прогрев топлива под бронепокрытием до температуры, например, 150…200 °С приведет к резкому изменению физико-механических характеристик
97
топлива и, самое главное, увеличению скорости горения топлива. Это изменит фронт горения и приведет к аномальному повышению давления в камере сгорания. Двигатель может разрушиться. Особенно это опасно для зарядов торцевого горения, так как даже малые изменения скорости горения в пристеночном слое суммируются и с течением времени могут привести к значительному повышения давления в камере. В качестве первого приближения можно взять следующие допустимые значения повышения температуры под бронирующим покрытием: для зарядов торцевого горения не более 5…10 °С, для трубчатых зарядов не более 15…20 °С. При проектировании необходимо определить температурные поля под бронирующим покрытием, рассчитать внутрибаллистические характеристики при неравномерном прогреве заряда и определить минимально допустимую толщину покрытия. Толщина бронирующих покрытий обычно бывает в пределах от 3 до 8 мм.
Бронепокрытия применяют обычно для вкладных зарядов, для скрепленных зарядов его стараются не применять – нетехнологично. Для скрепленных зарядов используют ЗКС – защитно-крепящий слой, цель которого обеспечить адгезию заряда с корпусом и защитить заряд от внешних тепловых потоков. Требования к ЗКС – хорошая адгезия, высокая стабильность характеристик во времени, низкая плотность и теплопроводность. Применяют, как правило, резины толщиной 1–2 мм.
3.4. Проектирование воспламенителя
Воспламенители служат для зажигания заряда двигателя твердого топлива или газогенератора. Требования, которые предъявляются к узлам воспламенения, делятся на две группы [1, 2, 14]:
1. Баллистические:
- обеспечение заданного времени выхода двигателя на режим;
98
-обеспечение заданной скорости нарастания давления
вкамере сгорания в начальный период работы двигателя;
-отсутствие выбросов давления при воспламенении заряда.
2. Эксплуатационные:
-безопасность обращения с системой воспламенения;
-герметичность узла воспламенения;
-обеспечение заданного времени хранения;
-сохранение эксплуатационных свойств после воздействия нагрузок при транспортировке двигателя.
Воспламенитель разрабатывает конструктор заряда. Воспламенение заряда может быть достигнуто путем
подвода тепла ко всей поверхности заряда или его части и прогрева до температуры воспламенения. Возможны следующие способы воспламенения зарядов:
-воспламенение продуктами сгорания порохов или пиротехнических составов;
-воспламенение самовоспламеняющейся жидкостью;
-нагрев топлива теплом, поступающим от проводника электрического тока;
-индукционный нагрев топлива за счет вихревых токов, образующихся в топливе;
-нагрев лазерным устройством.
Наиболее широко применяется первый способ. Для этого используются дымные ружейные пороха с размером зерна от 1 до 10 мм, имеющие в продуктах сгорания до 40 % конденсированной фазы. От размера зерна зависит градиент нарастания давления в камере сгорания. Применяется в основном для воспламенения зарядов из баллиститного топлива. Воспламенитель помещается в футляр («легкий» корпус), который должен быть герметичным, так как пороха сильно гигроскопичны. Этот футляр при начале работы воспламенителя либо сгорает, либо разрушается. Но этот корпус не должен разрушаться с образованием осколков, которые могут повредить заряд. Изготавливается обычно из тонких листов алюминия или из полимерных пленок. Футляр помещается в прочный корпус, который
99

фиксирует футляр в определенном положении и не допускает возможного разлета его осколков. Прочный корпус, как правило, не герметичен и изготавливается из низколегированных сталей или композитных материалов. Прочный корпус соединяется с полостью, где устанавливается пиропатрон, переходником длиной от 10 до 150 мм и диаметром от 5 до 10 мм. Он нужен для того, чтобы сформировать форс пламени от пиропатрона и подвести его в нужное место. Иногда между переходником и воспламенителем устанавливают рассекатель, который необходим для распределения пламени по поверхности петард или шашек воспламенительного состава. После рассекателя при необходимости устанавливают усилитель, который представляет собой пакет из полимерной пленки, заполненный мелкодисперсным воспламенительным составом. Он нужен для ускорения загорания воспламенительного состава. Пиропатрон обычно устанавливается с помощью резьбового соединения и уплотняется медным кольцом толщиной примерно 1 мм.
Воспламенитель на основе дымного пороха должен создать необходимое давление в камере сгорания и подвести достаточное количество тепла к поверхности заряда. Необходимая масса пороха составляет величину от десятков грамм до нескольких килограмм в зависимости от объема камеры сгорания, требуемого времени выхода на режим и давления в камере сгорания. Массу навески можно определить следующим образом:
ω= q QS0 ,
где q – количество тепла, необходимое для воспламенения единицы поверхности горения заряда, S0 – поверхность горения заряда, Q – теплотворная способность
пороха.
Сейчас широко применяются пиротехнические воспламенители, особенно для зарядов из смесевого твердого
100