
Сварка и свариваемые материалы. Том 2. Технология и оборудование
.pdf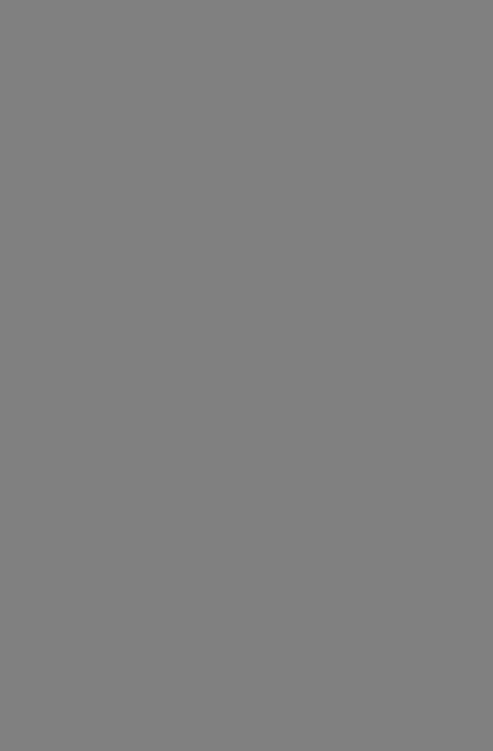
Тепловой |
эффект |
реакции |
горе |
|
|
|
|
|
|
|||||||||||
ния должен быть достаточно боль |
|
|
|
|
|
|
||||||||||||||
шим, чтобы поверхность металла на |
|
|
|
|
|
|
||||||||||||||
лобовой |
кромке |
|
прогревалась |
до |
|
|
|
|
|
|
||||||||||
температуры |
плавления; |
по |
тем |
же |
|
|
|
|
|
|
||||||||||
причинам хуже |
поддаются |
кислород |
|
|
|
|
|
|
||||||||||||
ной резке металлы с высокой тепло |
|
|
|
|
|
|
||||||||||||||
проводностью; вязкость |
расплава |
не |
|
|
|
|
|
|
||||||||||||
должна быть высокой, чтобы обес |
|
|
|
|
|
|
||||||||||||||
печить его турбулизацию в. поверх |
|
|
|
|
|
|
||||||||||||||
ностных слоях и выделение необхо |
|
|
|
|
|
|
||||||||||||||
димого количества тепла на кромке |
|
|
|
|
|
|
||||||||||||||
реза. |
чистых |
металлов |
кислород |
|
|
|
|
|
|
|||||||||||
Из |
|
|
|
|
|
|
||||||||||||||
ной |
резке |
хорошо |
поддаются |
|
же |
|
|
|
|
|
|
|||||||||
лезо, титан, марганец. Так, для же |
|
|
|
|
|
|
||||||||||||||
леза |
Гпл~1800 |
К; |
Твоейл= 1320 К; |
|
|
|
|
|
|
|||||||||||
Гол Рво = 1643 К. |
|
|
реакции |
горе |
|
|
|
|
|
|
||||||||||
Тепловой |
эффект |
|
|
|
|
|
|
|||||||||||||
ния |
железа |
довольно |
высок, |
|
|
|
|
|
|
|
|
|
||||||||
Fe + |
0,5О2 = |
|
|
|
|
|
|
|
|
|
|
|
|
|
|
|
||||
= FeO + |
269 |
МДж/кг • моль. |
|
|
|
|
|
|
|
|||||||||||
|
|
|
|
|
|
|
|
|
|
|
|
(26.3) |
|
|
|
|
|
|
||
Теплопроводность |
железа |
невы |
|
|
|
|
|
|
||||||||||||
сока, |
поэтому |
лобовая |
поверхность |
У |
|
|
|
|
||||||||||||
разогревается |
при |
резке |
до |
|
высоких |
|
|
|
|
|||||||||||
температур |
(1600—2000 °С). |
Кисло |
Рис. 26.1. Схема |
процесса |
кислородной |
|||||||||||||||
родную |
резку |
можно |
успешно |
при |
||||||||||||||||
резки: |
|
|
|
|
|
|||||||||||||||
менять для |
обработки |
малоуглероди |
АА — граница |
раздела |
стоун |
кислорода н |
||||||||||||||
стых, конструкционных, |
низколегиро |
окисленного |
металла; |
ВВ — граница раз |
||||||||||||||||
ванных |
сталей, |
титана. Обычной кис |
дела окисленного и расплавленного ме |
|||||||||||||||||
лородной |
резкой |
|
нельзя |
разрезать |
талла; |
СС — граница |
раздела расплав |
|||||||||||||
|
ленного |
н твердого |
металла |
|
||||||||||||||||
Ni, |
Си, |
Al, |
Mg, |
|
Cr, |
|
Zn, |
|
так |
как |
|
|
|
|
|
|
||||
они |
не |
удовлетворяют |
вышеприве |
|
|
|
|
|
|
|||||||||||
денным условиям резки. |
|
|
в |
стали |
ряда легирующих |
элементов |
и прежде |
|||||||||||||
|
Повышение |
содержания |
всего хрома приводит к тому, что в образующейся жидкой пленке на по верхности реза содержится большое количество тугоплавких оксидов хрома (до 20% ). Температура плавления хромистых железняков с таким содер жанием хрома составляет примерно 2000 °С, что значительно превышает температуру плавления разрезаемой стали. Для кислородной резки высоко легированных сталей необходимо обеспечить расплавление и перевод в шлак образующихся тугоплавких оксидов, что может быть достигнуто путем по вышения температуры в разрезе или переводом шлаков в более легкоплав кие соединения. Для резки высоколегированных хромоникелевых сталей, чу гуна, меди и ее сплавов применяется кислородно-флюсовая резка.
Сущность процесса кислородно-флюсовой резки заключается в том, что в зону реза вводится порошкообразный флюс, который, поступая на кромку разреза, сгорает в струе кислорода и значительно повышает температуру в разрезе. Кроме того, продукты его окисления сплавляются с оксидом по верхностной пленки и образуют шлаки с более низкой температурой плав ления, которые довольно легко удаляются из разреза.
В качестве флюса наиболее широко применяется железный порошок марки ПЖ5М по ГОСТ 9849—86 или его смеси с порошками магния, алю
миния, силикокальция.
Тепловое воздействие на металл при кислородной резке характеризуется быстрым нагревом поверхности разреза и прилегающих к нему слоев и
высокой скоростью их охлаждения (до 2000 °С/с), что при резке конструк ционных, легированных сталей приводит к образованию закалочных струк тур на кромке реза.
Низкая пластичность металла кромки в сочетании с внутренними напря жениями, вызываемыми термическим циклом от источника тепла, могут при вести к потере технологической прочности металла на кромке (образование трещин), а в ряде случаев — к разрушению изделия.
Одним из способов устранения трещин при резке является предвари тельный подогрев заготовок, который снижает скорость охлаждения металла кромки и обеспечивает получение более пластичных структурных составляю щих [1]. Температура предварительного подогрева стали может быть опреде лена из следующей зависимости:
Гп = 500 VCSKB 0 + 1000А6) — 0,45 |
(26.4) |
где б — толщина разрезаемого металла, м; k — коэффициент толщины |
(для |
6<1000 мм, k =0,0002) I Сэкв — эквивалентное содержание углерода: |
|
Сэкв = с + 0,155 (Сг + Мо) + 0,14 (Mn + V) + 0,11 Si + 0,045 (Ni + Си). |
|
|
(26.5) |
При Сакв (1 + 1000 £6)<0,45 сталь при резке не требует подогрева |
и мо |
жет разрезаться в состоянии поставки. В случае невозможности подогрева заготовки должна быть снижена скорость резки:
и = 0опт(1— |
0,8 |
УСэкв“ *М5 )i |
(26.6) |
где Попт — скорость |
резки малоуглеродистой стали, м/с; v — скорость |
резки |
|
закаливающейся |
стали, м/с. В настоящее время кислородная резка |
наряду |
со сваркой является одним из основных технологических процессов в ме таллообрабатывающих отраслях промышленности, металлургии, строитель стве. Она используется для резки заготовок из листа, профильного проката, труб, отрезки прибылей в литейном производстве, резки заготовок под по следующую ковку, штамповку, в ремонтных работах и др.
26.2. Технология резки
При кислородной разделительной резке стали в соответствии с технологиче скими особенностями различают резку металла малых толщин (до 5 мм), средних толщин (5—300 мм) и больших толщин (свыше 300 мм). Такоечде ление довольно условно, однако для каждого диапазона разрезаемых толщин существуют общие закономерности.
26.2.1. Кислородная резка стали средних толщин
Наиболее важными технологическими параметрами кислород ной резки являются расход режущего кислорода, мощность по догревающего пламени, скорость резки.
Для расчетов расходов режущего кислорода может быть ре комендована следующая формула, полученная на основании ре зультатов обработки данных ВНИИаатогенмащ и зарубежных
фирм, |
|
|
|
Ккр = 0W kM nku'b™ , |
|
|
(26.7) |
где Уцр— расход «режущего» |
кислорода, |
м3/с; |
k2— коэффи |
циент, учитывающий состояние |
металла |
перед |
резкой (Л2 = |
ЗНАЧЕНИЯ КОЭФФИЦИЕНТОВ ДЛЯ РАСЧЕТА РАСХОДА ГАЗА
И |
СКОРОСТИ |
РЕЗКИ |
Наименование коэффициента |
Обозна |
Величины |
чение |
Коэффициент, |
учитывающий |
|
kp = |
1 + 0,01 (Я -10s — 10), где Я — |
||||
расстояние между |
резаком и |
|
расстояние между резаком и метал |
|||||
металлом |
|
|
|
кг |
лом, |
м. При Я < |
0,01 |
= 1 |
Коэффициент, |
учитывающий |
Лт = |
(1 + 27V 10“3)*(1 — 1,56я), где |
|||||
температуру |
металла |
перед |
|
Ты — температура металла перед рез |
||||
резкой |
|
|
|
ku |
кой, °С (справедлива для |
6 < 0,8 м) |
||
Коэффициент, |
учитывающий |
Для проката ku = |
14-0,75, для литья |
|||||
состояние и состав металла |
|
ku = |
0,85-f-0,5 (первые значения бе |
|||||
|
|
|
|
|
рутся для малоуглеродистых и низко |
|||
|
|
|
|
|
легированных сталей, вторые — для |
|||
Коэффициент, |
учитывающий |
Е |
высоколегированных) |
|
||||
При механизированной резке проката |
||||||||
состояние поверхности |
метал |
|
с чистой поверхностью £ = 0,55-т-1,1; |
|||||
ла |
|
|
|
|
при резке литья и горячего металла |
|||
Коэффициент, |
учитывающий |
kr |
Е = |
1,5ч-2,8 |
|
|
||
Определяется из табл. 26.2 |
||||||||
замену ацетилена |
другими |
|
|
|
|
|
||
горючими |
|
|
|
kn |
При резке вертикальным резаком &п= |
|||
Коэффициент, |
учитывающий |
|||||||
положение резака при резке |
|
= 1,0. При резке |
в горизонтальном |
|||||
|
|
|
|
|
положении kn = 0,8 |
|
||
=0,3 — для |
проката; £2= 0 ,6 — для литья и поковок толщиной |
от 0,3 до 0,6 м), £р, kn, kM— см. табл. 26.1.
Подогревающее пламя нагревает поверхностные слои ме талла до температуры воспламенения в начале резки, а в про цессе резки — фронтальную поверхность металла. Мощность подогревающего пламени возрастет с увеличением толщины раз резаемого металла, расстояния между торцом резака и метал лом. При резке загрязненного металла мощность пламени не обходимо увеличивать. Мощность пламени определяется расхо дом горючего газа, его родом и соотношением расхода горючего газа и подогревающего кислорода. При кислородной резке в ка честве горючего используются газообразные и жидкие углево дороды. При сгорании указанных горючих в смеси с кислоро дом образуется высокотемпературное пламя.
В табл. 26.2 приведены сведения об основных свойствах го рючих газов.
Расходы горючего газа и подогревающего кислорода при
резке могут |
быть определены из нижеследующих зависимостей: |
|
Vr.г = Е |
' (10*6 + 100); |
(26.8) |
VK.„ = $Vr. r, |
(26.9) |
Т А Б Л И Ц А 26.S
КОЭФФИЦИЕНТ СКОРОСТИ РЕЗКИ *к В ЗАВИСИМОСТИ ОТ КЛАССА ТОЧНОСТИ
Класс точности |
*к |
Примеры применения |
1 |
1,0 |
Точная фигурная вырезка деталей с отстава |
|
|
нием до 5 % |
2 |
1.2 |
Прямолинейная резка с отставанием до 1 5 % , |
|
|
фигурная резка с отставанием до 10 % |
3 |
1,4 |
Прямолинейная резка с отставанием до 25 % , |
Не нормируется |
|
фигурная — с отставанием до 15 % |
2 ,0 |
Грубая заготовительная резка |
где Рн — давление |
«режущего» кислорода, |
кПа; кч— коэффи |
циент скорости резки, зависящий от чистоты кислорода, |
||
k " ~ У2 (100 — е) |
’ |
|
где е — чистота кислорода, %; kT, k„, kp выбираются в соответ |
||
ствии с табл. 26.1. |
|
при точной вырезке |
Меньшие скорости резки выбираются |
фигурных деталей, наибольшие при прямолинейной раздели тельной кислородной резке металла в скрап (табл. 26.3).
26.2.2. Кислородная резка стали малых толщин
Своеобразие кислородной резки листового проката малых тол
щин |
(до 5 мм) |
состоит в том, что подогревающее пламя разо |
|||||||||||||
гревает весь лист по толщине до высоких температур |
(порядка |
||||||||||||||
800 °С) |
с |
образованием |
до |
|
|
|
Т А Б Л И Ц А |
26.4 |
|||||||
вольно |
|
большого |
|
пятна. |
|
|
|
||||||||
|
|
РЕЖИМЫ |
МЕХАНИЗИРОВАННОЙ |
||||||||||||
Вследствие |
этого |
шлаки, |
вы |
||||||||||||
|
КИСЛОРОДНОЙ РЕЗКИ |
|
|||||||||||||
дуваемые |
струей |
|
кислорода |
|
|
||||||||||
|
|
ТОНКОЛИСТОВОЙ СТАЛИ |
|
||||||||||||
из разреза, смачивают |
ниж |
|
|
|
|
|
|
||||||||
нюю нагретую кромку с обра |
Толщина метал ла, мм |
Расход газа, 10“4 ма/с |
|
||||||||||||
зованием |
трудноотделимого |
|
|
|
|
|
|||||||||
грата. Поэтому |
меры, |
направ |
кислорода «режущего» |
кислорода подогрева ющего |
ацетилена |
|
0 |
||||||||
ленные |
на |
достижение хоро |
воздуха |
*Я |
|||||||||||
шего |
качества |
при |
кислород |
1 |
|||||||||||
ной |
резке |
тонкого |
|
металла, |
|
||||||||||
предусматривают |
уменьшение |
|
|
|
|
|
|
||||||||
высокотемпературного |
пятна |
2 |
2,8 |
0,46 |
0,42 |
5 ,6 |
142 |
||||||||
нагрева |
на нижней |
поверхно |
3 |
3,1 |
0,55 |
0,50 |
7 ,0 |
130 |
|||||||
сти листа. Для резки тонкого |
4 |
3,4 |
0,66 |
0,60 |
8,4 |
125 |
|||||||||
металла |
применяют специаль |
5 |
3,6 |
0,77 |
0,70 |
11,2 |
120 |
||||||||
ные |
мундштуки с максималь |
П р и м е ч а н и е , |
v — скорость резки. |
||||||||||||
ным |
приближением |
каналов |
|||||||||||||
|
|
|
|
|
|
подогревающего пламени к режущему кислороду и охлажде нием металла за счет дополнительной подачи воздуха или воды в зону резки. Режимы резки тонколистовой стали приведены в табл. 26.4.
26.2.3. Кислородная резка стали больших толщин
Толщины стали более 300 мм принято называть большими. Ос новная особенность резки стали больших толщин состоит в том, что необходимо сформировать фронт окисления металла боль шой протяженности. Поэтому при резке металла большой тол щины требуется специальная режущая аппаратура и особые приемы резки. Для достижения стабильных показателей произ водительности, качества резки струя режущего кислорода должна сохранять окислительную способность и кинетическую энергию на возможно большой длине по толщине разрезаемого металла, а мощность подогревающего пламени должна быть такой, чтобы обеспечить подогрев шлаков в нижней части раз реза и защиту режущей струи от подсоса воздуха. Поэтому рас ход режущего кислорода и горючего газа предусматриваются намного большими, чем при кислородной резке стали обычных толщин. Резка выполняется, как правило, с использованием кислорода низкого давления, не более 392 кПа, мундштуки ре заков имеют обычные цилиндрические сопла большого диа метра. Скорость истечения струи невысока (близка к звуковой). Струя большого диаметра обеспечивает окисление соответст венно большего количества металла в верхней части разреза, чем улучшается прогрев металла в нижней части реза. Обра зующийся шлак заполняет раковины и пустоты, располагаю щиеся довольно часто в прибылях, в связи с чем кислородная струя не теряет устойчивости и не меняет направления при резке металла с внутренними дефектами [3].
Особое внимание рекомендуется уделять операциям, пред шествующим резке. Место начала резки следует хорошо подо греть, причем нагреваемая зона должна простираться ближе к низу торцовой поверхности, чем к верху вдоль линии предпо лагаемого разреза. При резке металла больших толщин боль шое значение имеет момент врезания струи кислорода в металл. Начало резки значительно облегчается, если угол атаки будет на 2—3° больше прямого (рис. 26.2). В конце резки необходимо снизить скорость тележки и наклонить резак в противоположную сторону, что обеспечивает прорезание нижнего угла заготовки.
Большое значение при резке металла больших толщин имеет подогревающее пламя. Для обеспечения прогрева шлаков в нижней части разреза и защиты струи кислорода от переме
шивания с |
воздухом при резке стали толщиной более 1000 мм |
в резаках |
за режущим соплом располагают дополнительно |