
Контроль качества сварных соединений
..pdf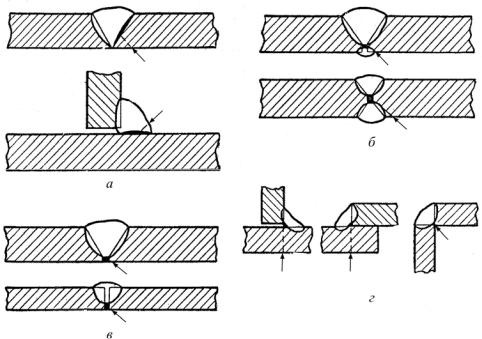
Непровары между отдельными слоями (см. рис. 2.9, б) возникают по следующим причинам:
–не полностью удален шлак, образовавшийся при наложении предыдущего валика, что возможно вследствие трудности его удаления или небрежности сварщика;
–недостаточная тепловая мощность (малый ток, излишне длинная или короткая дуга).
Рис. 2.9. Непровары в стыковых швах: а – по кромке; б – по середине шва; в – в корне шва; г – в угловых швах
Трещины − частичное местное разрушение сварного соединения (рис. 2.10). Образованию трещин способствуют следующие факторы:
–сварка конструкционных легированных сталей в жестко закрепленных конструкциях;
–высокая скорость охлаждения при сварке углеродистых сталей, склонных к закалке на воздухе;
–применение высокоуглеродистой проволоки при автоматической сварке конструкционной легированной стали;
–использование повышенных плотностей сварочного тока при наложении первого слоя многослойного шва толстостенных сосудов
иизделий;
41
Стр. 41 |
ЭБ ПНИПУ (elib.pstu.ru) |
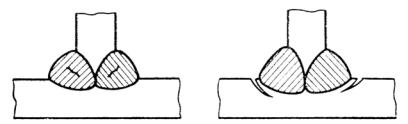
а |
б |
Рис. 2.10. Трещины в сварных швах и соединениях: а – в наплавленном металле; б – в зонах сплавления и термического влияния
–недостаточный зазор между кромками деталей при электрошлаковой сварке;
–слишком глубокие и узкие швы при автоматической сварке под слоем флюса;
–чрезмерное нагромождение швов для «усиления» конструкции (применение наплавок и т.п.), в результате чего возрастают сварочные напряжения, способствующие образованию трещин всварном соединении;
–наличие в сварных соединениях других дефектов, являющихся концентраторами напряжений, под действием которых в области дефектов начинают развиваться трещины.
Трещины и непровары относятся к числу наиболее опасных дефектов и по всем действующим нормативно-техническим документам являются недопустимыми.
2.2. ДЕФЕКТЫ КОНТАКТНОЙ СВАРКИ
Основными наружными дефектами швов сварных соединений, выполненных точечной сваркой, являются:
–наружные трещины (рис. 2.11);
–прожог ;
–наружный выплеск;
–вырыв точек;
–выход на поверхность литой структуры;
–разрыв металла у кромки соединения;
–поверхностное нарушение сплошности металла во вмятине от электродов;
–чрезмерная вмятина инеправильная форма вмятиныотэлектродов;
–темная поверхность сварных точек.
42
Стр. 42 |
ЭБ ПНИПУ (elib.pstu.ru) |
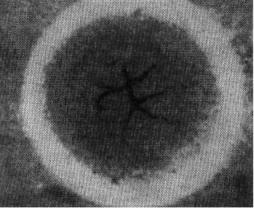
Рис. 2.11. Наружные трещины сварной точки. Увеличение 10х
Причины этихдефектов(способствуют образованию этихдефектов):
–большая величина или длительность импульса сварочного тока;
–малое усилие сжатия электродов или отсутствие его;
–плохая подготовка поверхностей свариваемых деталей;
–загрязнение электродов;
–малое ковочное усилие;
–позднее приложение ковочного усилия;
–недостаточное охлаждение электродов;
–неисправность сварочного оборудования;
–неправильная форма контактных поверхностей электродов;
–большие натяги деталей при сварке и в процессе сварки;
–близость сварочной точки к краю соединения;
–малая величина нахлестки;
–небольшой размер рабочей поверхности электродов;
–перекос детали или электродов;
–неправильная заточка или неравномерный износ рабочих поверхностей электродов.
Основные внутренние дефекты точечной сварки:
–непровар – отсутствие взаимной литой зоны соединяемых элементов сварных конструкций (рис. 2.12);
–внутренние трещины, поры и раковины;
–внутренний выплеск металла (рис. 2.13);
–несимметричное расположение ядра точки;
–чрезмерное проплавление (более 80 %) толщины свариваемого листа.
43
Стр. 43 |
ЭБ ПНИПУ (elib.pstu.ru) |
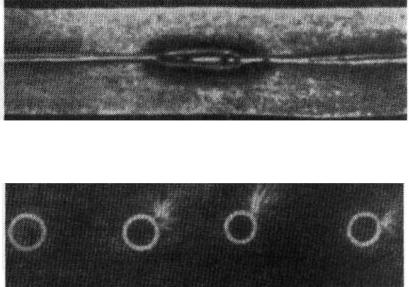
Рис. 2.12. Макроструктура непроваренной сварной точки из сплава Д16Т толщиной 2 + 2 мм
Рис. 2.13. Сварные точки с выплеском
Причины образования внутренних дефектов:
–недостаточная величина или импульс сварочного тока;
–большое усилие сжатия электродов;
–шунтирование сварочного тока;
–увеличение рабочей поверхности электродов;
–нестабильность контактного сопротивления (из-за плохой подготовки поверхности детали);
–раннее приложение ковочного усилия;
–малое усилие сжатия электродов;
–малое ковочное усилие;
–запоздание включения ковочного усилия;
–большой сварочный ток;
–продолжительное время сварки;
–большое контактное сопротивление деталей;
–плохая зачистка электродов;
–загрязнение электродов;
–перенос свариваемых элементов конструкции;
–смещение точек к краю нахлестки;
–малая нахлестка;
–неправильный подбор размеров контактных поверхностей электродов.
44
Стр. 44 |
ЭБ ПНИПУ (elib.pstu.ru) |
Основным дефектом контактной стыковой сварки сопротивлением или оплавлением является «слипание», при котором между свариваемыми элементами имеется механический контакт, но отсутствует взаимное прорастание зерен между соединяемыми границами.
Подобный дефект часто образуется при сварке трением, давлением (холодная сварка), диффузионной и сварке взрывом.
2.3. ВЛИЯНИЕ ДЕФЕКТОВ НА РАБОТОСПОСОБНОСТЬ КОНСТРУКЦИИ И ИХ ИСПРАВЛЕНИЕ
Наличие тех или иных дефектов в сварных соединениях само по себе не определяет потерю работоспособности этих соединений.
Опасность дефектов зависит не только от собственных характеристик (типа дефекта, его размера и т.д.), но и от конструктивных и эксплуатационных факторов.
Наиболее детально влияние дефектов на работоспособность конструкций изучено для изделий, выполненных сваркой. В большинстве случаев степень влияния того или иного дефекта на работоспособность конструкций устанавливают экспериментально – испытаниями образцов с дефектами.
При сдаче конструкции в эксплуатацию прежде всего оценивают допустимость наличия наружных дефектов. Значения их допустимости, как правило, указаны в технических условиях на изготовление конструкции и зависят от условий ее эксплуатации.
Установлено, что выпуклость шва не снижает статической прочности, однако очень влияет на вибрационную прочность. Чем больше выпуклость шва и, следовательно, меньше угол перехода от основного металла к наплавленному, тем сильнее снижается предел выносливости. Таким образом, чрезмерная выпуклость шва может свести к нулю все преимущества, полученные от оптимизации технологического процесса по улучшению качества сварных соединений, работающих при вибрационных динамических и повторно-статических нагрузках.
Значительным (по влиянию на работоспособность) наружным дефектом является подрез. Он недопустим в конструкциях, работающих на выносливость. Небольшой протяженности подрезы, ослабляющие сечение шва не более чем на 5 %, в конструкциях, работающих под действием статических нагрузок, можно считать позволительными.
45
Стр. 45 |
ЭБ ПНИПУ (elib.pstu.ru) |
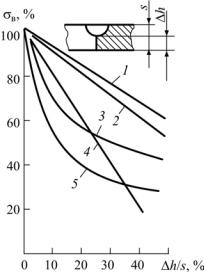
Наплывы, резко изменяя очертания швов, образуют концентраторы напряжений и, тем самым, снижают выносливость конструкции. Наплывы, имеющие большую протяженность, следует считать недопустимыми дефектами, так как они вызывают концентрацию напряжений и нередко сопровождаются непроварами. Небольшие местные наплывы, вызванные случайнымиотклонениямисварочныхрежимов отзаданных, разрешаются.
Кратеры, как и прожоги, во всех случаях являются недопустимыми дефектами и подлежат исправлению.
Для окончательной оценки качества сварного соединения контролер должен знать значения допустимости наружных и внутренних дефектов, которые указаны в НДТ. Результаты многочисленных исследований показывают, что для пластичных материалов при статической нагрузке (рис. 2.14, кривые 1, 2, 4) влияние величины непровара на уменьшение их прочности прямо пропорционально относительной глубине непровара.
Для малопластичных и высокопрочных материалов при статической (см. рис. 2.14, кривые 3, 5), а также при динамической или вибрационной нагрузке (рис. 2.15) пропорциональность между потерей работоспособности и величиной дефекта нарушается.
Рис. 2.14. Влияние соотношенияглубины∆ h/s непровара корняшванастатическуюпрочностьстыковых соединений (безвыпуклости): 1 – Ст3; 2 – 12Х 18Н9Т; 3 – 25 ХГФА; 4 – сплав Д16Т; 5 – 30 ХГСНА
46
Стр. 46 |
ЭБ ПНИПУ (elib.pstu.ru) |
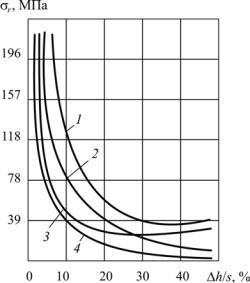
Рис. 2.15. Влияние относительной величины дефектов ∆ h/s на усталостную прочность стыковых соединений из низкоуглеродистых сталей (без выпуклости):
1 – подрезов; 2 – пор; 3 – непроваров; 4 – шлаковых включений
Сравнительно небольшой дефект может существенно влиять на прочность. Например, при статической нагрузке и пластичном материале величина непровара влияет на потерю прочности пропорционально относительной величине этого непровара или его площади.
При малопластичном материале, а также при динамической или вибрационной нагрузке наблюдается непропорциональность между потерей работоспособности и величиной дефекта, сравнительно небольшие дефекты могут существенно влиять на прочность.
При статических нагрузках такие дефекты, как поры, шлаковые включения при их суммарной площади в сечении шва до 5–10 %, прак - тически не влияют на прочность сварной конструкции.
На усталостную прочность влияют дефекты в виде концентраторов напряжений.
Установлено, что поры и шлаковые включения при их относительной суммарной площади в сечении шва до 5–10 % мало влияют на статическую прочность соединения (рис. 2.16). Если швы имеют значительную выпуклость, то поры и шлаковые включения суммарной площадью (размером) 10–15 % от сечения шва слабо сказываются на статической прочности. Для ряда конструкций (закладные детали, стыки арматуры) в зави-
47
Стр. 47 |
ЭБ ПНИПУ (elib.pstu.ru) |

Рис. 2.16. Влияние относительной площади дефектов (пор)
на механические свойства стыковых соединений из легированной стали (σ в = 850 МПа после закалки и отпуска): 1 – σ в; 2 – КС; 3 – ϕ ; 4 – δ 5
симости от места расположения таких дефектов их допустимая величина может составлять 10–25 % от сечения шва.
Такие дефекты, как трещины, оксидные пленки, несплавления, недопустимы.
С учетом всех перечисленных конструктивно-эксплуатационных факторов для альтернативной оценки опасности влияния сварочных дефектов их целесообразно разделить на две группы: объемные и плоскостные. Объемные дефекты не оказывают существенного влияния на работоспособность соединений. Эти дефекты (поры, шлаки, флокены) можно нормировать по размерам или площади ослабления ими сечения изделия. Плоскостные трещиноподобные дефекты (трещины, оксидные пленки, несплавления, раскаты) по НТД, как правило, считаются недопустимыми.
При обнаружении недопустимых наружных или внутренних дефектов их обязательно удаляют. Удаление наружных дефектов следует проводить вышлифовкой с обеспечением плавных переходов в местах выборок. Места выборок можно не заваривать, если сохранилась минимальная допустимая толщина стенки детали в месте максимальной глубины выборки. Дефекты с корня шва удаляют по всей длине заподлицо с основным металлом. Если в процессе механической обработки (вышлифовки) не удалось полностью исправить наружные дефекты, то их как недопустимые внутренние дефекты необходимо полностью удалить.
48
Стр. 48 |
ЭБ ПНИПУ (elib.pstu.ru) |
Заглубленные наружные и внутренние дефекты (дефектные участки)
всоединениях из алюминия, титана и их сплавов следует удалять только механическим способом: вышлифовкой абразивным инструментом или резанием, а также вырубкой с последующей зашлифовкой. В ряде случаев
вконструкциях из стали допустимо удалять дефектные участки воздушнодуговой или плазменной строжкой с последующей обработкой поверхности выборки абразивными инструментами. При этом поверхности изделий из углеродистых и кремнемарганцовистых сталей должны быть зачищены (зашлифованы) дополногоудаления следоврезки.
Исправление дефектов с заваркой выборок в сварных соединениях, подлежащих обязательной термической обработке и выполненных из легированных и хромистых сталей, нужно проводить после высокого
(450–650 °С) отпуска сварного соединения (промежуточного, окончательного или предварительного), за исключением отдельных случаев, оговоренных технологическими инструкциями.
При удалении дефектных мест целесообразно соблюдать определенные условия. Длина удаляемого участка должна быть равна длине дефектного места плюс 10–20 мм с каждой стороны, а ширина разделки выборки должна быть такой, чтобы ширина шва после заварки не превышала двойной ширины до заварки. Форма и размеры подготовленных под заварку выборок должны обеспечивать возможность надежного провара в любом месте. Поверхность каждой выборки должна иметь плавные очертания без резких выступов, острых углублений и заусенцев. При заварке дефектного участка необходимо перекрыть прилегающие участки основного металла.
После заварки участок надо зачистить до полного удаления раковин и рыхлости в кратере, выполнить на нем плавные переходы к основному металлу. В сварных швах со сквозными трещинами перед заваркой требуется засверлить их концы, чтобы предотвратить распространение трещин. Дефектный участок в этом случае проваривают на полную глубину. Заварку дефектного участка проводят одним из способов сварки плавлением (ручной дуговой, дуговой в инертных газах и т.д.). Исправленные швы сварных соединений должны быть повторно проконтролированы в соответствии с требованиями, предъявляемыми к качеству изделия. Если при этом вновь будут обнаружены дефекты, то их исправляют снова
ссоблюдением необходимых требований. Число исправлений одного
итого же дефектного участка зависит от категории ответственности конструкции и, как правило, не превышает трех.
49
Стр. 49 |
ЭБ ПНИПУ (elib.pstu.ru) |
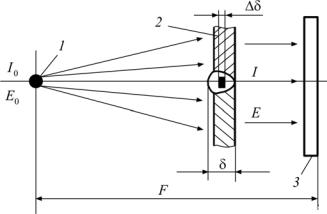
3.РАДИАЦИОННЫЕ МЕТОДЫ КОНТРОЛЯ
3.1.ФИЗИЧЕСКИЕ ОСНОВЫ РАДИАЦИОННОЙ
ДЕФЕКТОСКОПИИ
В основе этих методов лежит регистрация и анализ прошедшего через изделие проникающего ионизирующего излучения.
При прохождении через изделие ионизирующее излучение ослабляется (поглощается и рассеивается). Степень ослабления зависит от самого изделия (толщины и плотности), а также и от интенсивности М и энергии Е самого изделия.
Для выявления дефектов любым из методов радиационного контроля необходимо иметь как минимум три основных элемента (рис. 3.1): источник ионизирующего излучения; контролируемый объект; детектор, регистрирующий дефектоскопическую информацию.
Рассмотрим, что из себя представляют источники ионизирующего излучения.
Рентгеновское излучение и γ -излучение, как и световые, ультрафиолетовые и радиоволны, имеет электромагнитную природу (разновидность электромагнитных колебаний).
Рис. 3.1. Схемаконтролярадиоционными методами:
1 – источник ионизирующегоизлучения; 2 – контролируемый объект; 3 – детектор, регистрирующийдефектоскопическую информацию
50
Стр. 50 |
ЭБ ПНИПУ (elib.pstu.ru) |