
01 POWER ISLAND / 01 CCPP / V. Ganapathy-Industrial Boilers and HRSG-Design (2003)
.pdf
8.42Why water tube boilers are preferred to fire tube boilers for gas turbine applications
8.43Why 10% increase in surface area does not mean 10% more duty in boilers or heat transfer equipment
8.44a Time required to heat up boilers
8.44b Transient heating of a superheater bundle
8.44c Transient response of a water tube evaporator to cutoff in heat input and feedwater supply
8.44d Response of a water tube evaporator when steam demand increases and feedwater supply is cut off
8.45a Parameters to be considered in testing performance of HRSGs 8.45b Evaluating HRSG performance from operating data
8.46Estimating boiling heat transfer coefficient and critical heat flux in water tube boilers
8.47a Relating heat flux, steam pressure, quality, flow in water tube boilers 8.47b Estimating critical heat flux in fire tube boilers
8.47c Estimating critical heat flux in a fire tube boiler; correcting for bundle geometry
8.48Simplified approach to designing fire tube boilers
8.49Simplified approach to designing water tube boilers
8.50Estimating tube bundle size
8.51Estimating thickness of insulation for flat and curved surfaces; effect of wind velocity; estimating thickness to limit surface temperatures
8.52Estimating surface temperature of given thickness of insulation; trial- and-error procedure to determine casing temperature
8.53Sizing insulation to prevent freezing; determining water dew point 8.54a Estimating heat loss from pipes for various insulation thicknesses 8.54b Estimating temperature drop of fluids in insulated piping
8.55Optimum thickness of insulation; life-cycle costing; annual heat loss and capitalized cost; annual heat loss if no insulation is used
8.56Design of hot casing
8.57Temperature of duct or stack wall with and without insulation
8.58Effect of wind velocity, casing emissivity on heat loss
8.59a Checking for noise and vibration problems in heat transfer equipment 8.59b Determining natural frequency of vibration of a tube bundle
8.59c Computing acoustic frequency
8.59d Determining vortex shedding frequency
8.59e Checking for bundle vibrations
8.59f Checks for tube bundle vibration using damping and fluid elastic instability criteria
8.60Estimating specific heat, viscosity, and thermal conductivity for a gas mixture
Copyright © 2003 Marcel Dekker, Inc.

8.61Effect of gas analysis on heat transfer
8.62Effect of gas pressure on heat transfer
8.63Converting gas analysis from weight to volume basis
8.64Effect of gas pressure and analysis on design of fire tube boiler
8.01
Q:
How is the surface area of heat transfer equipment determined? What terms can be neglected while evaluating the overall heat transfer coefficient in boilers, economizers, and superheaters?
A:
The energy transferred in heat transfer equipment, Q, is given by the basic equation
Q ¼ U A DT |
ð1Þ |
Also, |
|
WhDhh ¼ Wc Dhc |
ð2Þ |
where |
|
A ¼ surface area, ft2
W ¼ fluid flow, lb=h
Dh ¼ change in enthalpy (subscripts h and c stand for hot and cold)
D |
T |
¼ |
|
|
|
|
|
|
|
|
|
|
2 |
|
|
|
|
|
|
|
||||
|
|
¼ |
corrected log-mean temperature difference, F |
|
|
|
|
|
||||||||||||||||
|
U |
overall heat transfer coefficient, Btu=ft |
|
h F |
|
|
|
|
|
|
||||||||||||||
|
|
|
|
|
|
|
|
|
|
|||||||||||||||
For extended surfaces, U can be obtained from [1] |
|
|
|
|
|
|
|
|||||||||||||||||
|
1 |
|
|
¼ |
|
At |
þ ff i |
At |
|
þ ff oþ |
|
|
|
|
|
|
|
|
||||||
U |
hiAi |
Ai |
|
|
|
|
|
|
|
|
|
|||||||||||||
|
|
|
|
At |
|
|
|
d |
|
d |
1 |
|
|
|
|
|
|
|
|
|
||||
|
|
|
|
|
|
|
|
ln |
|
þ |
|
|
|
|
|
|
|
|
|
|
||||
|
|
|
|
Aw |
|
24Km |
di |
Zho |
|
|
|
|
|
|
|
|
||||||||
where |
|
|
|
|
|
|
|
|
|
|
|
|
|
|
|
|
|
|
|
|
|
|
|
|
|
|
|
|
|
At ¼ surface area of finned tube, ft2=ft |
2 |
|
|
|
|
|
|
|
|||||||||||
|
|
|
|
|
Ai ¼ tube inner surface area ¼ pdi=12, ft |
=ft |
|
2 |
|
|
|
|
||||||||||||
|
|
|
|
|
Aw ¼ average wall surface area ¼ pðd þ diÞ=24, ft |
=ft |
|
|
||||||||||||||||
|
|
|
|
|
Km ¼ thermal conductivity of the tube wall, Btu=ft h F |
|
||||||||||||||||||
|
|
|
d; di ¼ tube outer and inner diameter, in. |
|
|
|
|
|
2 |
|
F=Btu |
|||||||||||||
ff |
i |
; ff |
o ¼ |
fouling factors inside and outside the tubes, ft |
|
h |
||||||||||||||||||
|
|
|
|
|
|
|
|
|
|
|
|
|
|
2 |
h |
F |
|
|
||||||
|
hi; ho ¼ tube-side and gas-side coefficients, Btu=ft |
|
|
|
||||||||||||||||||||
|
|
|
|
|
Z ¼ fin effectiveness |
|
|
|
|
|
|
|
|
|||||||||||
If bare tubes are used instead of finned tubes, At |
¼ pd=12. |
|
|
|
Copyright © 2003 Marcel Dekker, Inc.

Equation (3) can be simplified to |
|
||||||||||||
1 |
|
d |
1 |
|
|
d |
|
d |
|
||||
|
|
¼ |
|
þ |
|
|
|
þ |
|
ln |
|
|
|
|
U |
hidi |
ho |
24Km |
di |
ð4Þ |
|||||||
|
|
þ ff i |
d |
þ ffo |
|
|
|
||||||
|
|
|
|
|
|
|
|||||||
|
|
di |
|
|
|
|
where ho is the outside coefficient. Now let us take the various cases.
Water Tube Boilers, Economizers, and Superheaters
The gas-side heat transfer coefficient ho is significant; the other terms can be
neglected. In a typical bare tube economizer, for example, h |
i ¼ |
1500 Btu=ft2 h F, |
|||||||||||||||||||
ff i and ffo |
¼ 0:001 ft |
2 |
h F=Btu, and ho |
¼ 12 Btu=ft |
2 |
h F. d |
|
||||||||||||||
|
|
¼ 2.0 in., di ¼ 1.5 in., |
|||||||||||||||||||
and Km ¼ 25 Btu=ft h F. |
|
|
|
|
|
|
|
|
|
|
|
|
|||||||||
Substituting into Eq. (4) yields |
|
|
|
|
|
|
|
||||||||||||||
1 |
|
2:0 |
|
|
|
|
1 |
|
2:0 |
2 |
|
|
|
|
|
||||||
|
|
¼ |
|
|
|
|
þ |
|
þ |
|
|
|
ln |
|
|
|
|
|
|
||
U |
1500 |
|
1:5 |
12 |
24 |
|
25 |
1:5 |
|
|
|
|
|||||||||
|
|
|
|
|
|
|
2:0 |
|
|
|
|
|
|
|
|
|
|
|
|||
|
|
|
þ 0:001 |
þ 0:001 |
|
|
|
|
|
|
|
|
|
||||||||
|
|
|
|
|
|
|
|
|
|
|
|
|
|||||||||
|
|
|
1:5 |
|
|
|
|
|
|
|
|
|
|||||||||
¼ 0:0874 |
|
|
|
|
|
|
|
|
|
|
|
|
|
|
|
|
Hence,
U ¼ 11:44 Btu=ft2 h F
Thus we see that the overall coefficient is close to the gas-side coefficient, which is the highest thermal resistance. The metal thermal resistance and the tube-side resistance are not high enough to change the resistance distribution much.
However, in a liquid-to-liquid heat exchanger, all the resistances will be of the same order, and hence none of the resistances can be neglected.
Even if finned tubes were used in the case above, with At=Ai ¼ 9 substituted into Eq. (3), U ¼ 9.3 Btu=ft2 h F, which is close to ho. Thus, while trying to figure U for economizers, water tube boilers, or gas-to-liquid heat exchangers, U may be written as
U ¼ 0:8 to 0:9 ho |
ð5Þ |
Copyright © 2003 Marcel Dekker, Inc.
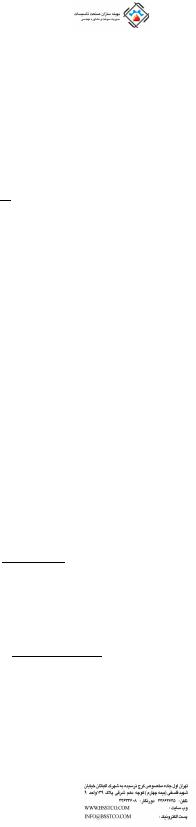
Fire Tube Boilers, Gas Coolers, and Heat Exchangers with Gas Flow Inside Tubes with Liquid or Steam–Water Mixture on the Outside
ho is large, on the order of 1000–1500 Btu=ft2 h F, whereas hi will be about 10– 12 Btu=ft2 h F. Again, using Eq. (4), it can be shown that
di |
ð6Þ |
U hi d |
All the other thermal resistances can be seen to be very small, and U approaches the tube-side coefficient hi.
Gas-to-Gas Heat Exchangers (Example: Air Heater in Boiler
Plant)
In gas-to-gas heat transfer equipment, both hi and ho are small and comparable, while the other coefficients are high.
Assuming that ho ¼ 10 and hi ¼ 15, and using the tube configuration above,
1 |
|
|
2:0 |
|
1 |
|
0:001 |
|
9:6 |
|
10 4 |
||||
|
|
|
|
|
|
|
|
|
|
|
|
||||
U |
¼ 15 |
|
1:5 þ 10 þ |
þ |
|
||||||||||
|
|
|
|||||||||||||
|
|
|
|
|
2 |
|
|
|
|
|
|
||||
|
þ 0:001 |
¼ 0:1922 |
|
|
|
||||||||||
|
|
|
|
|
|
||||||||||
|
1:5 |
|
|
|
or
U ¼ 5:2 Btu=ft2 h F
Simplifying Eq. (4), neglecting the metal resistance term and fouling, we obtain
hidi=d |
ð7Þ |
U ¼ ho ho þ hidi=d |
Thus both ho and hi contribute to U.
DT, the corrected log-mean temperature difference, can be estimated from
DT ¼ FT DTmax DTmin
lnðDTmax=DTminÞ
where FT is the correction factor for flow arrangement. For counterflow cases, FT ¼ 1.0. For other types of flow, textbooks may be referred to for FT. It varies
from 0.6 to 0.95 [2]. DTmax and DTmin are the maximum and minimum terminal differences.
Copyright © 2003 Marcel Dekker, Inc.

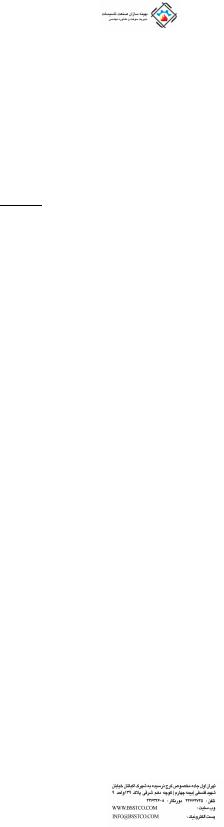
Substituting Eqs. (9)–(11) into Eq. (8) and simplifying, we have
hi ¼ 2:44 |
w0:8k0:6Cp0:4 |
¼ 2:44 |
w0:8C |
ð12Þ |
|
di1:8m0:4 |
|
di1:8 |
where C is a factor given by
C ¼ k0:6Cp0:4 m0:4
C is available in the form of charts for various fluids [1] as a function of temperature. For air and flue gases, C may be taken from Table 8.1.
For hot water flowing inside tubes, Eq. (8) has been simplified and, for t < 300 F, can be written as [3]
hi ¼ ð150 þ 1:55tÞ |
V 0:8 |
ð13Þ |
|||
di0:2 |
|
||||
where |
|
|
|
|
|
V ¼ velocity, ft=s |
|
||||
t |
¼ |
water temperature, F |
|
||
|
|
|
|
|
For very viscous fluids, Eq. (8) has to be corrected by the term involving viscosities at tube wall temperature and at bulk temperature [1].
8.03a
Q:
Estimate hi when 200 lb=h of air at 800 F and atmospheric pressure flows in a tube of inner diameter 1.75 in.
TABLE 8.1 |
Factor C for Air |
and Flue Gases |
|
|
|
Temp ( F) |
C |
200 |
0.162 |
400 |
0.172 |
600 |
0.180 |
800 |
0.187 |
1000 |
0.194 |
1200 |
0.205 |
|
|
Copyright © 2003 Marcel Dekker, Inc.
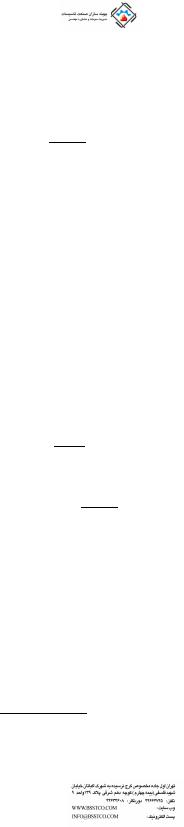
A:
Using Table 8.1 and Eq. (12), we have C ¼ 0.187.
hi ¼ 2:44 2000:8 0::187: ¼ 11:55 Btu=ft2 h F 1 751 8
where
w ¼ flow, lb=h
di ¼ inner diameter, in.
For gases at high pressures, Ref. 1 gives the C values. (See also p. 531.)
8.03b
Q:
In an economizer, 50,000 lb=h of water at an average temperature of 250 F flows in a pipe of inner diameter 2.9 in. Estimate hi.
A:
Let us use Eq. (13). First the velocity has to be calculated. From Q5.07a, V ¼ 0:05ðwv=di2Þ: v, the specific volume of hot water at 250 F, is 0.017 cu ft=lb. Then,
0:017
V ¼ 0:05 50;000 2:92 ¼ 5:05 ft=s Hence, from Eq. (13),
hi ¼ ð150 þ 1:55 250Þ 5:050:8 ¼ 1586 Btu=ft2 h F 2:90:2
8.03c
Q:
Estimate the heat transfer coefficient when 4000 lb=h of superheated steam at
500 psia |
and an average temperature of 750 F flows inside a tube of inner |
|||||||
diameter 1.5 in. |
|
|
|
|
||||
A: |
|
|
|
|
|
|
|
|
Using Table 8.2, we see that C ¼ 0.318. From Eq (12) |
||||||||
h |
i |
¼ |
2:44 |
|
40000:8 0:318 |
¼ |
285 Btu=ft2 h F |
|
1:51:8 |
||||||||
|
|
|
If steam were saturated, C ¼ 0.383 and hi ¼ 343 Btu=ft2 h F.
Copyright © 2003 Marcel Dekker, Inc.
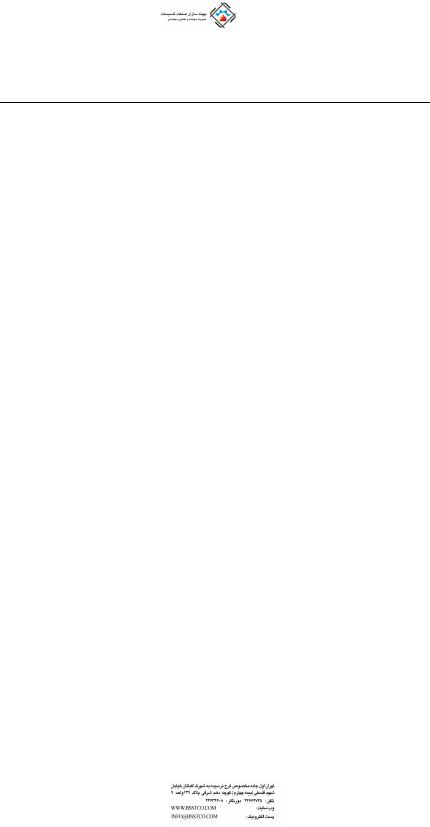
TABLE 8.2 Factor C for Steam
|
|
|
|
Pressure (psia) |
|
|
|
|
|
|
|
|
|
|
100 |
200 |
500 |
1000 |
2000 |
|
|
|
|
|
Saturation |
|
|
Temperature ( F) |
|
|
|
|
|
|
0.282 |
0.310 |
0.383 |
0.498 |
0.8733 |
||
400 |
0.2716 |
0.3059 |
|
|
|
|
500 |
0.2737 |
0.2909 |
0.3595 |
|
|
|
600 |
0.2813 |
0.2896 |
0.3228 |
0.413 |
|
|
700 |
0.2917 |
0.2965 |
0.3161 |
0.3586 |
0.5206 |
|
800 |
0.3050 |
0.3090 |
0.3206 |
0.3453 |
0.4214 |
|
900 |
0.3161 |
0.3197 |
0.3277 |
0.3477 |
0.3946 |
|
1000 |
0.3276 |
0.3302 |
0.3392 |
0.3531 |
0.386 |
|
|
|
|
|
|
|
|
8.04
Q:
How is the outside gas heat transfer coefficient ho in boilers, air heaters, economizers, and superheaters determined?
A:
The outside gas heat transfer coefficient ho is the sum of the convective heat transfer coefficient hc and nonluminous heat transfer coefficient hN .
ho ¼ hc þ hN |
ð14Þ |
For finned tubes, ho should be corrected for fin effectiveness. hN is usually small if the gas temperature is less than 800 F and can be neglected.
Estimating hc for Bare Tubes
A conservative estimate of hc for flow of fluids over bare tubes in in-line and staggered arrangements is given by [1]
Nu ¼ 0:33 Re0:6 Pr0:33 |
ð15Þ |
||||
Substituting, we have the Reynolds, Nusselt, and Prandtl numbers |
|
||||
Re ¼ |
|
Gd |
ð16Þ |
||
|
|
|
|
||
12 m |
|||||
Nu ¼ |
|
hcd |
|
ð17Þ |
|
12k |
Copyright © 2003 Marcel Dekker, Inc.
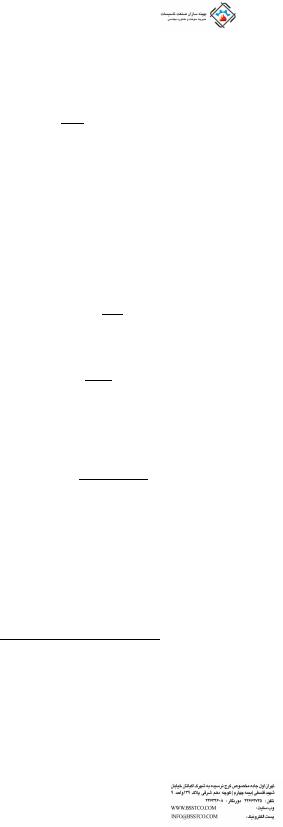
and |
|
|
Pr ¼ |
mCp |
ð18Þ |
k |
where
G ¼ gas mass velocity, lb=ft2 h d ¼ tube outer diameter, in.
m ¼ gas viscosity, lb=ft h
k ¼ gas thermal conductivity, Btu=ft h F Cp ¼ gas specific heat, Btu=lb F
All the gas properties above are to be evaluated at the gas film temperature. Substituting Eqs. (16)–(18) into Eq. (15) and simplifying, we have
F |
ð19Þ |
hc ¼ 0:9G0:6 d0:4 |
where
C0:33
F ¼ k0:67 p ð20Þ
m0:27
Factor F has been computed for air and flue gases, and a good estimate is given in Table 8.3.
The gas mass velocity G is given by
Wg |
ð21Þ |
G ¼ 12 NwLðST dÞ |
where
Nw ¼ number of tubes wide
ST ¼ transverse pitch, in.
L ¼ tube length, ft
Wg ¼ gas flow, lb=h
TABLE 8.3 F Factor for Air and Flue Gases
Temp ( F) |
F |
200 |
0.094 |
400 |
0.103 |
600 |
0.110 |
800 |
0.116 |
1000 |
0.123 |
1200 |
0.130 |
|
|
Copyright © 2003 Marcel Dekker, Inc.
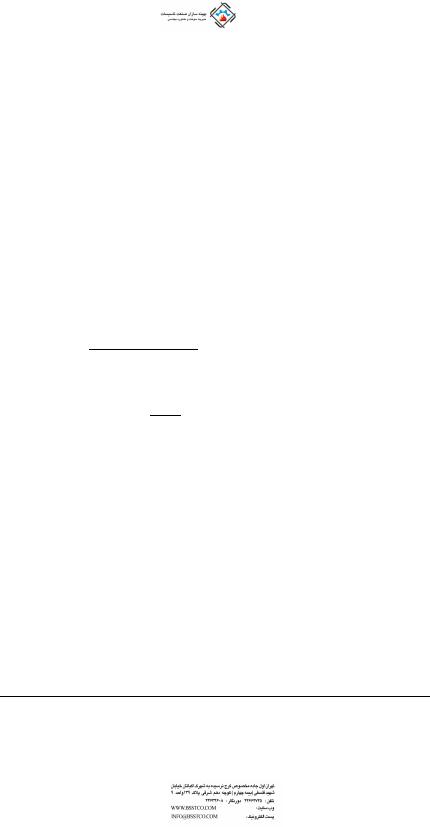
For quick estimates, gas film temperature tf can be taken as the average of gas and fluid temperature inside the tubes.
Example
Determine the gas-side convective heat transfer coefficient for a bare tube superheater tube of diameter 2.0 in. with the following parameters:
Gas flow ¼ 150,000 lb=h
Gas temperature ¼ 900 F
Average steam temperature ¼ 500 F
Number of tubes wide ¼ 12
Length of the tubes ¼ 10.5 ft
Transverse pitch ¼ 4.0 in.
Longitudinal pitch ¼ 3.5 in. (staggered)
Solution. Estimate G. From Eq. (21),
G ¼ 12 |
150;000 |
¼ 7142 lb=ft2 h |
12 10:5 ð4 2Þ |
Using Table 8.3, at a film temperature of 700 F, F ¼ 0.113. Hence,
hc ¼ 0:9 71420:6 0:113: ¼ 15:8 Btu=ft2 h F
20 4
Because the gas temperature is not high, the hN value will be low, so
U ho hc ¼ 15:8 Btu=ft2 h F
(Film temperature may be taken as the average of gas and steam temperatures, for preliminary estimates. If an accurate estimate is required, temperature drops across the various thermal resistances as discussed in Q8.16a must be determined.)
The convective heat transfer coefficient obtained by the above method or Grimson’s method can be modified to include the effect of angle of attack a of the gas flow over the tubes. The correction factor Fn is 1 for perpendicular flow and decreases as shown in Table 8.4 for other angles [1].
If, for example, hc ¼ 15 and the angle of attack is 60 , then hc ¼ 0:94 15 ¼ 14:1 Btu=ft2 h F:
TABLE 8.4 Correction Factor for Angle of Attack
a, deg |
90 |
80 |
70 |
60 |
50 |
40 |
30 |
20 |
10 |
|
|
|
|
|
|
|
|
|
|
Fn |
1.0 |
1.0 |
0.98 |
0.94 |
0.88 |
0.78 |
0.67 |
0.52 |
0.42 |
Copyright © 2003 Marcel Dekker, Inc.